Full Hotel Project
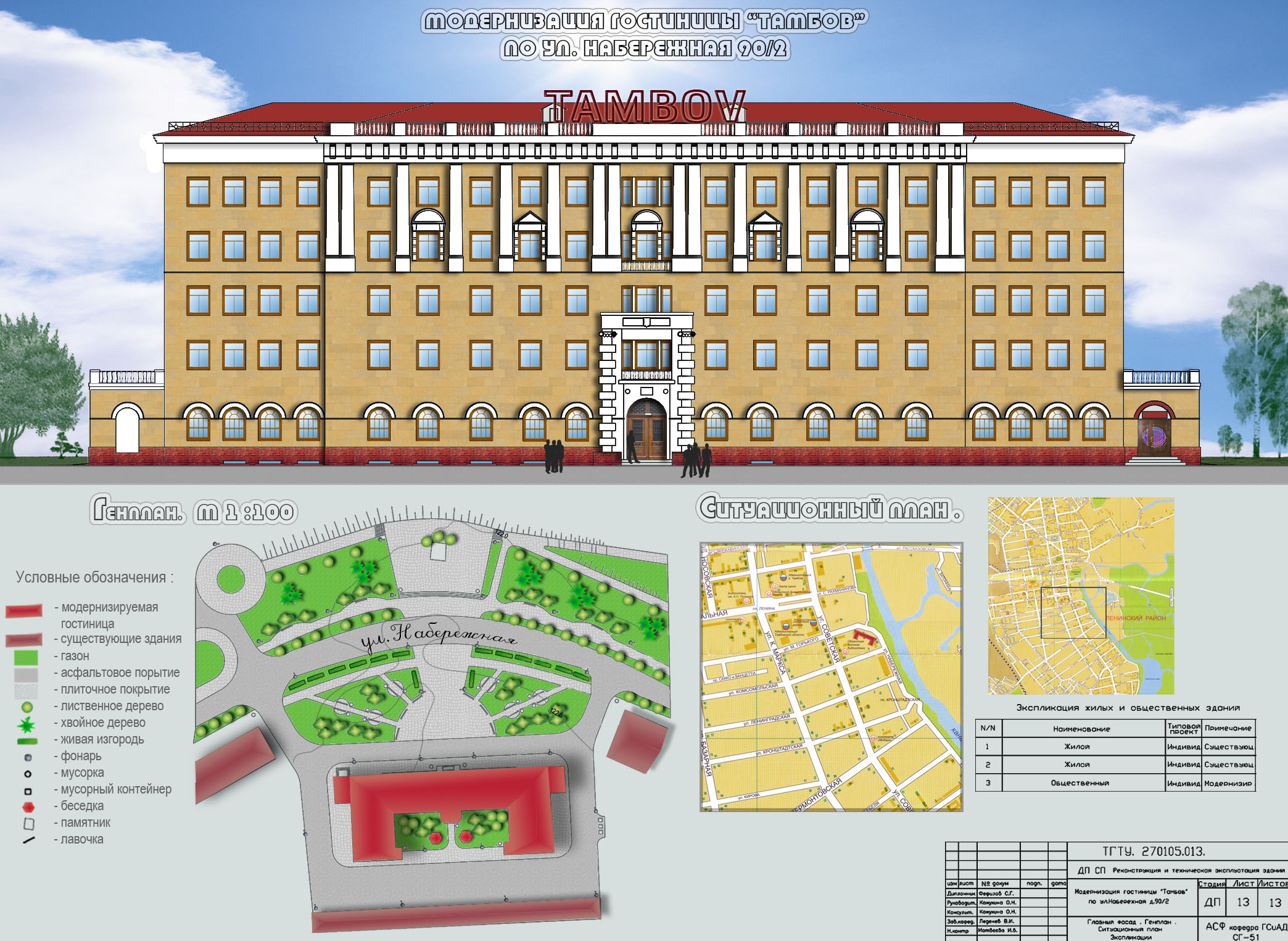
- Added: 27.12.2016
- Size: 9 MB
- Downloads: 4
Description
the entire project
Project's Content
![]() |
![]() |
![]() ![]() ![]() |
![]() ![]() ![]() |
![]() ![]() ![]() |
![]() ![]() ![]() |
![]() |
![]() ![]() ![]() |
![]() ![]() ![]() |
![]() ![]() ![]() |
![]() ![]() ![]() |
![]() ![]() ![]() |
![]() |
![]() ![]() ![]() |
![]() ![]() ![]() ![]() |
![]() |
![]() ![]() ![]() |
![]() ![]() ![]() ![]() |
![]() |
![]() ![]() ![]() |
![]() ![]() ![]() ![]() |
![]() ![]() ![]() |
![]() |
![]() ![]() ![]() |
![]() ![]() ![]() |
![]() |
![]() |
Additional information
Contents
Introduction
1. Architectural and construction section
1.1. Study of technical condition of buildings
1.1.1. General characteristics of space-planning and structural solutions of the building
1.1.2. Characteristics of building operating conditions during the survey period
1.1.3. Characteristics of the building by degree of capital
1.1.4. Technical condition of structural and enclosing structures of the building
1.1.5. Technical condition of building engineering systems
1.2. Volume-planning, structural and architectural-artistic solution of the building after reconstruction
1.2.1. Space-planning solution of the building after reconstruction
1.2.2. Structural solution of the building after reconstruction
1.2.3. Architectural and artistic solution of the building after reconstruction
1.3. Justification for selection of building enclosures
1.3.1. Thermal design of the outer wall and structural design of the thermal protection
1.3.2. Selection of window infills according to the required heat protection conditions
1.3.3. Calculation of thermal insulation of attic floor
1.4. Calculation and design of intermediate floors according to soundproofing conditions
2. Design section
2.1. Calculation of Interstage Floor
2.1.1. Calculation of metal beams
2.1.2. Calculation of monolithic slab
2.1.3. Calculation of Floor Beam Baseplate
2.2. Calculation of building coverage
2.2.1. Grid Calculation
2.2.2. Calculation of rafter structure
3. Process Section
3.1. Process instruction for disassembly of roof with wooden rafters and roof made of sheet steel using crane on chassis of automobile type
3.1.1. Scope of Application
3.1.2. Procedure and organization of works performance
3.1.3. Quality and Acceptance Requirements
3.1.4. Calculation of labor, machine time and wages
3.1.5. Work Schedule
3.1.6. Logistical resources
3.1.7. Safety precautions
3.1.8. Technical and economic indicators
3.2. Job Instruction for Wooden Roof Arrangement
rafters and sheet steel roofs
3.2.1. Procedure and organization of works performance
3.2.2. Quality and Acceptance Requirements
3.2.3. Calculation of labor, machine time and wages
3.2.4. Work Schedule for Final Product Meter
3.3. Logistical resources
3.4. Safety precautions
3.5. Technical and economic indicators
4. Organizational and Economic Division
4.1. Organizational and technical preparation of the facility construction
4.1.1. Selection and description of work methods
4.1.2. Technical and economic selection of lifting mechanism
4.1.3.Determination of nomenclature and scope of work
4.2.1. Determination of duration of works on the determiner card
4.2.2. Network Model Design and Calculation
4.2.3. Calculation of network parameters and key figures
4.2.4. Calculation of network parameters and indicators
4.2.5. Building a Time-Based Network
4.2.6. Definition of manpower and logistics requirements
4.2.7. Schedule and adjust the workforce
4.2.8. Identification of logistical requirements
4.3. Construction plan design and calculation
4.3.1. Calculation of storage rooms and sites
4.3.3. Calculation of requirements for temporary buildings and structures
4.3.4. Calculation of construction demand for water
4.3.5. Calculation of construction demand for electricity
5. Building engineering equipment
5.1. Technical condition of the building water supply system prior to modernization
5.1.1. Technical condition of the building water supply system
5.1.2. Technical condition of the building water disposal system
5.1.3. Technical condition of the building heating system
5.1.4. Technical condition of building ventilation system
5.1.5. Technical condition of building power supply system
5.1.6. Technical condition of vertical transport
5.2. Design of modernization of domestic water supply system
5.2.1.Recipitation of cold water supply system modernization works
5.2.2. Determination of estimated costs of the upgraded cold water supply system
5.2.3. Hydraulic calculation of the upgraded cold water supply system
5.3. Building drainage
5.4. Building heating
5.5. Building ventilation
5.6. Building power supply
5.7. Vertical transport
6. Technical operation of the building
6.1. Contents of roofs and attic rooms
6.2. Structural repair
6.3. Metal roof repair and sealing
6.4. Improvement of temperature and humidity conditions and elimination
icing attic roofs
7. Improvement of the territory
7.1. Territory Engineering Training
7.1.1. Vertical layout of adjacent area
hotels
7.1.2. Territory Relief Organization
7.2. Improvement
7.2.1. Sites of various purposes, their dimensions and placement principles, characteristics of small architectural forms
7.2.2. External landscaping and landscaping
7.2.3. Designing pedestrian links
7.2.4. Selection and justification of types of pavements of streets, tracks, sites
7.2.5. Territory lighting design
7.2.6. Sanitary cleanup activities
7.2.7. Small architectural forms on the territory of development
8. Environmental section
8.1. Brief description of the location of the object
8.2. Restoration and improvement of the territory after the completion of the modernization of the building
8.3. Characteristics of the object according to the degree of environmental pollution and drainage from the building
8.4. Activities for the protection and management of water resources
8.5. Measures to protect the environment during waste disposal of the modernized facility
8.6. Measures to ensure noise and solar conditions of the building area
8.7. Environmental protection during modernization
8.8. Noise protection measures during modernization
8.9. Measures for disposal and disposal of waste generated during modernization
8.10. Measures to protect territory and surface and groundwater during modernization
9. Occupational safety and civil defence
9.1. Equipment grounding calculation
9.2. Calculation of illumination by utilization factor
9.3. Hotel basement shelter calculation
9.4. Protection against radioactive fallout
9.5. Sealing of doors of external plugs and emergency exits
9.6. Ventilation
9.7. Measures for installation of protective structure
9.8. Schematic symbols for the protective structure plan
Literature
Application
Application
Application
Conclusion
Project Description
For the diploma project "Modernization of the Hotel" Tambov "
on the street. Embankment 90/2.
author: student gr. SG51 Fefilov S.G.
specialty 270105 "Urban construction and agriculture."
Head: Kozhukhina O.N.
Year of Diploma Protection 2008.
During the execution of the diploma project, it is planned to develop
project for the modernization of the hotel "Tambov" on the street. Embankment 90/2.
The hotel is located at the intersection of Naberezhnaya and M. Gorky streets ,
located in the city recreation area.
In the diploma project it is necessary to perform:
- new layout of the existing building;
- calculation of new structures of building elements;
- technology of erection of wooden roof;
- time-scale network;
- calculation of local and object estimates;
- engineering systems for the new building;
- calculation of sound and heat insulation of enclosing structures;
- improvement of the adjacent area of the hotel;
- Environmental protection measures
the surrounding area;
- calculation of measures for civil defense and labor protection.
Introduction
In recent years, investment in the hospitality business, which is one of the leading sectors of the economy of many countries of the world, has been increasing worldwide.
For economic reasons, the reconstruction of existing hotel buildings is preferable to the construction of new ones. Moreover, hotels built in the 19th and early 20th centuries are unique architectural objects that largely form the appearance of cities. In addition, in the region there are a large number of hotel buildings built in the second half of the 20th century, with little physical wear, but whose architectural solutions do not meet modern requirements for the level of comfort and aesthetics.
Currently, the volume of construction of commercial and residential real estate is increasing, the process of reconstruction and modernization of old hotels is accelerating mainly due to the increased flow of city guests. Accordingly, in the central part of the city there is a shortage of seats in middle-class hotels, in this regard, the choice of an object for modernization stopped at the Tambov Hotel. The hotel is located in the recreation area, has convenient pedestrian and transport accessibility.
In the diploma project, it is planned to eliminate the moral and physical wear of the building, bring the hotel into proper condition, guided by the modern requirements of the State Standard of the Russian Federation for hotels of the * * * category.
The diploma project was completed in accordance with the requirements of the regulatory documentation. The project consists of a graphic part including a 75x55cm subframe and 12 A-I sheets, and an explanatory note on 192 A-IV sheets.
Process section.
Process sheet for disassembly of the roof with wooden rafters and sheet steel roofs using a crane on an automobile type chassis.
3.1.1. The scope of the map.
The process sheet was developed for disassembly of the roof with log-mounted rafters and a coating of roofing sheet steel on an area of 1673.3 m2.
The process sheet provides for the production of modernization of the building with a complete change of roof and the use of a crane on a chassis of the automobile type.
The building is five-story, the height from the pavement level to the cornice is 18.70 m. The length of the building in the axes is 117-66.40 m. The width in the axes A-Z is 25.20 m.
The roof of the building is attic unheated, with layered rafters. The roof is steel.
3.1.3. Quality and acceptance requirements:
Quality Requirements:
- at removal of roofing; suitable for further use, maximum preservation of roofing steel shall be ensured;
- The components of the rafter system to be re-used in the case shall be understood without damage in the support areas and in the joints.
3.1.5. Work Schedule for Final Product Meter.
The work schedule is drawn up on the accepted final product meter using labor costing data. Schedule items are formed by combining labor cost items.
The duration of the enlarged processes is determined by dividing the total labor costs by the accepted composition of the link (people).
The duration of the process is determined in shifts based on an 8-hour working day. The work schedule is presented in the graphic part.
3.1.7. Safety technique.
The following basic safety rules shall be observed during the works:
a) workers must be given soft non-slipping shoes, safety belts with their places. attachments;.
b) to pass through the roof with a slope of more than 15 °, it is necessary to lay portable ladders with a width of at least 30 cm with sewn bars on the roofs;
c) cut sheets of roofing iron shall not be left on the roof;
d) it is forbidden to disassemble the roof with wind of more than 12 m/s (6 points), thick fog, rain, heavy snowfall and ice;
e) for passage along attic floors it is necessary to lay panel flooring with width of at least 0.5 m along beams.
Technical and economic indicators.
Composition of technical and economic indicators:
- Standard labor costs of workers (in human parts) – 326,03;
- Wages of construction workers in 1984 prices (in p.) - 170.64;
- Production per worker per shift in natural meters - 35.9 m2/cm.
Duration of works (see) -21.5.
3.2. Process map for the construction of a roof with wooden rafters and roof made of sheet steel with the use of.
The scope of the map.
The process map was developed for the construction of a roof with wooden rafters and a roof made of sheet steel.
The process sheet provides for the production of modernization of the building with a complete change of roof and the use of a crane on a chassis of the automobile type.
The building is five-story with a basement. The height of the building from the pavement level to the cornice is 18.70 m. The length of the building in the axes is 117-66.40 m. The width in the axes A-Z is 25.20 m.
The roof of the building is attic unheated. Rafter roof system with hanging rafters. Roof is made of steel.
3.2.4. Work Schedule for Final Product Meter.
The work schedule is drawn up on the accepted final product meter using labor costing data. Schedule items are formed by combining labor cost items. The duration of the enlarged processes is determined by dividing the total labor costs by the accepted composition of the link (people). The duration of the process is determined in shifts based on an 8-hour working day. The work schedule is presented in the graphic part.
3.5. Technical and economic indicators.
Composition of technical and economic indicators:
Standard labor costs of workers (in human parts) – 630,69;
Wages of construction workers (in p.) - 266.37;
Production per worker per shift in natural meters, determined by dividing the numerical value of the final product indicators by the standard labor costs of workers and multiplying by the working shift duration (in natural meters/human days) - 7,83 .
Duration of works (see) 21.5.
Organizational and Economic Division
The diploma project has developed an in-line construction organization. The design object is a public three-story building.
The initial data for the design are: the structural diagram of the object, the architectural and planning solution, the characteristics of the structural and enclosing structures.
Dimensions of the building in plan: - length 67.4 m.
- width 25.2 m
- height 1 floor 4.3, typical 2.9 m.
During the design process, optimization was carried out - in some cases, different numbers of people were accepted on different grips for some processes.
4.1. Organizational and technical training
construction of the facility
4.1.1 Selection and description of work methods
The selection of the method implies the purpose of the main technological reception of the erection and technical means for the performance of the work.
For installation works, the following shall be defined:
a) method of building installation.
b) installation flows that combine groups of mounted elements according to the installation sequence within the framework of the general organizational scheme of building erection.
c) process equipment for installation of elements.
d) devices for adjustment and temporary fixation of elements during installation.
e) installation method.
The work begins with the study of methods for the construction of buildings similar to the one being designed, described in the educational and reference literature.
Then they begin to determine the necessary equipment that ensures the performance of work according to the selected method. When designing installation works with the help of cranes, the crane is selected or checked for the possibility of performing the processes of installation of structural elements taking into account their specific weight, dimensions, schemes for installation of cranes on the object. The selection of load-gripping devices and lifting equipment is made using reference literature and is drawn up in the form of a table. At the same time, each of the selected load gripping devices should be as universal as possible, so that the total number of devices on the construction site is the smallest.
a) Method of building installation.
Since the direction of development of the installation process is vertical, carried out by building up structures, it is advisable to use free lifting of structures.
A distinctive feature is that the installed structures experience the same loads as during operation.
The maximum values of these loads are reached when the installation is completed. The disadvantage of the method is the increased complexity and labor intensity of the work, as well as the need to perform verification, fastening and other operations at height.
b) Installation flows
After installation and reconciliation of the foundations, they begin to masonry the walls, masonry is carried out within one floor at the same time as insulation of the walls.
Floor slabs begin to be laid from the staircase, which allows immediately after laying the first slab along the mounted stairways and platforms to rise to the floor and continue masonry work on the second and third floors.
c) Process equipment for installation of elements
Coating slabs are mounted using multi-branch slings, (Sling 4SK104 for multi-pillar slabs, Sling 4SK104 + PKCH-3.4 for 2T type slabs).
d) Installation method
Elements and structures are delivered to construction sites from manufacturers by road. During warehousing (installation with preliminary unloading), it is necessary to place the heavy elements closer to the installation crane, and the light elements further, laying in the same position in which they were during transportation.
Structures that allow laying in horizontal rows on wooden gaskets are stored in multi-tier stacks.
4.2. Definition of Nomenclature and Quantities of Work
Based on the analysis of the architectural and planning solution of the building, the calculation of the volumes of installation work in tabular form was carried out (see Table 22, Section 6). To do this, the types of structural elements have been installed, the required number of them has been determined, both on a separate typical floor and in the building as a whole.
4.2.5. Creates a time-based network.
When building a network on a time scale, work lying on a critical path is tied to calendar and ordinal days and highlighted by a double line. All other works are plotted according to the parameters of early beginnings. The graph shows the private time reserves of each process.
The time scale network is shown on sheet 10 of the graphic portion.
4.2.6. Definition of Labour Demand and
logistical resources.
In order to determine the need for labor and material resources, it is necessary to draw up a schedule for the movement of labor, a schedule for the receipt of basic structures and materials to the site and a schedule for the operation of main construction machines (see sheet 10 of the graphic part).
4.3. Design and calculation of the construction plan.
In this section a site-wide construction plot plan is developed for the main construction period (installation of the above-ground part).
The construction master plan (SGP) is designed to determine the composition and location of construction facilities in order to maximize the efficiency of their use, taking into account compliance with labor protection requirements.
SGP establishes the boundaries of the construction site and the types of its fences; location of existing and temporary underground, ground and air networks and communications, permanent and temporary roads; traffic patterns and mechanization; place of installation of construction and lifting machines with indication of ways of their movement and zones of action.
4.3.2 Design of construction roads
In the diploma project, the roads are designed with one-way traffic and accordingly have a width of 4 meters. The radius of the rounding of the road is 15 m. The coverage of temporary roads is accepted as improved dirt. The design took into account the following requirements: the distance between the road and the fence is more than 1.5 m, between the road and the warehouse is more than 0.5 m.
Technical condition of vertical transport
The modernized hotel has an iron elevator, in an inactive state. During the modernization of the building, it is planned to completely dismantle it.
Cold Water System Upgrade Design
5.2.1 Description of Cold System Modernization Works
water supply
As a result of the survey, the estimated physical wear of the cold water supply system amounted to 60%, the drainage system - 35%.
Due to the fact that the percentage of physical wear of the cold water supply system is very high and during modernization it is supposed to be completely replaced.
Modernization of the cold water supply system is carried out in two stages:
1) dismantling of old pipelines;
2) installation of a new pipeline.
When installing a new pipeline, consider the following points:
When laying a pipeline passing through floors, walls, partitions, sleeves should be made. The sleeves are a piece of pipe whose inner diameter is 810mm more than the outer diameter of the laid pipe, and protrudes 1015mm on both sides of the floor (a diagram of the intersection of the floor with the pipeline is shown on the graphic part sheet). After the sleeve is installed and a pipe passes through it, the annular space is filled with hemp, and the upper part of the sleeve is poured with bitumen. Installation of the sleeve in the floor eliminates the appearance of wet spots at the location of the pipe on the plaster and prevents the appearance of cracks on it.
To supply cold pipeline to sanitary devices, metal plastic pipelines are used.
The water metering unit is located in a warm and dry non-residential room in a place easily accessible for inspection near the outer wall at the entrance to the building (the diagram of the water metering unit is given on the graphic part sheet).
Booster pump unit is installed after water metering unit located in basement on foundation, which rises above floor level by 20 cm, with sound insulation device.
The inlet is arranged with a slope of 0.005 towards the external network to allow its emptying.
After the completion of the installation of the new pipeline, the internal water supply networks are tested at a pressure of 0.30.6 MPa, exceeding the operating one by 0.2MPa. The pressure drop during the test for 5 minutes shall not exceed 0.05MPa.
Building drainage
Due to the coordination changes in the hotel design and modern requirements for hotel rooms, the water disposal system will be completely replaced during the modernization process. Internal sewerage is designed as household. Sewage receptacles in buildings are sanitary units in rooms and farm rooms. appointments on the ground floor. All receivers are equipped with flushing devices from the water supply line. Waste water flows into the sewer network through a hydraulic gate - a siphon, which is a U-shaped pipe filled with water. The hydraulic gate prevents the passage of gases from the sewer network into the room. The siphon is usually combined with a revision - a hole with a removable cover for cleaning pipes during clogging. All receivers are connected using various shaped parts (taps, elbows, tees, crosses, etc.) to risers. Sewage risers are installed from bell pipes, which are made of plastic. When docking, the straight end of the pipe is inserted into the bell, and the joint is sealed. Above the attic floor, the sewer riser continues as an exhaust pipe exiting above
coating and excluding ingress of gases into rooms. The diameter of the exhaust pipe is assigned more than the diameter of the riser. Drainage of sewage water from the riser outside the building (outlet) is designed from cast iron pipes. Outlet is connected to inspection sewer pit
Waste water is discharged by gravity to the existing yard well and to the existing well along Naberezhnay.
Waste water is discharged from sanitary devices by gravity to the existing courtyard network.
Sewer network is installed from polyvinyl chloride sewer pipes as per specification 61930786
Building heating
Heating is designed central (with heat generation outside the heated building and its transportation via pipelines to the building). Water is used as coolant. Hot water enters the building and is supplied to its heating system by natural circulation. Two-tube schemes with lower wiring are used. Proposed system comprises risers, distribution line, devices with adjusting valves and backflow line. To distribute the pressure in the system, an expansion vessel is installed at the highest point. It receives an excess volume of water formed due to its expansion during heating. To remove air from the system, all non-vertical pipes and supplies to the instruments are installed with a slope that ensures the movement of air from the system to the air collector. Air collector is arranged at top point of dilution hot pipeline but below expansion vessel.
Heating devices serve directly for heating the rooms by transferring heat from the air circulating in the heat carrier devices to the room. Radiators are used as heating devices
Heat carrier parameters in a heating system of 9570 wasps.
Cast iron radiators are used as heating devices
MS-140. Heating devices are located in the sill area
external walls, where it neutralizes descending flows of cold air from the opening.
Main pipelines and riser pipes located in the technical underground of the building are insulated and covered with aluminum foil. "Comfort" temperature controllers are installed on the inputs to the heating devices.
Air descent from the system is carried out through the radiator cranes STD 7073 V, on the upper floor.
Pipelines passing in the basement shall be insulated by HPST5 Cover layer - rolled fiberglass RSTAV GOST 611 145-80.
Heating devices and non-isolated pipelines are painted with oil paint in 2 times.
Building power supply
Power supply of the building is provided from the existing input. As a backup power supply, power supply is provided from the existing diesel plant in the RCC.
Power supply voltage 380V, working and emergency lighting - 220 V, evacuation lighting - 36 V.
Luminaires with fluorescent lamps and filament lamps are provided for lighting.
Evacuation lighting is made by lamps with built-in storage battery, which are not switched off during the operation of the building.
Lighting and socket networks are made by wire of PUNP grade and laid in flexible corrugated pipes.
The lighting network is hidden in the rooms.
Power distribution networks are made by wire
PV-8660.
Accounting of electric power consumption is performed by BRU meters.
At the input, all non-current-carrying parts that may be energized when the insulation is damaged are connected to the dead-ground neutral of the power supply with a zero wire.
Vertical transport
Passenger elevators with a carrying capacity of 350 kg with a counterweight at the rear, in axes 78, G-V and 1112, G-V are provided. The position of the elevator shafts is shown on the sheets of the graphics part (see sheets 2,3). The size of the cabin is 2.1x1.1. The mine size is 2.5x1.7. Nominal speed is 0.63 m/s. Dimensions are taken in accordance with GOST 574683: Electric passenger elevators. Basic parameters and dimensions.
Technical operation of the building
6.1. Contents of roofs and attic rooms
The technical content of roof structures and attic rooms consists of periodic inspections, cleaning and ongoing repairs related to the elimination of certain faults in structures and engineering equipment located within the attic room, and the implementation of measures aimed at improving the temperature and humidity conditions of rooms and structures.
Surveys are carried out by engineering and technical workers of operating organizations at least 2 times a year - in early spring and autumn. Extraordinary inspections are carried out after heavy rains.
During inspection of roofs and attic rooms it is necessary to:
Pay attention to the condition and integrity of the roofing material, the joints of the roofing elements, the condition of the screen, the rafters and the places of their conjugations; detecting the presence and quality of roofing fixtures to the base; determine the condition of supports, eaves, backfilling and load-bearing structures of attic floors, ventilation holes and auditory windows, places of conjugations of structures passing through roofing, engineering equipment located within attic rooms, wiring of central heating, expansion tanks, ventilation ducts and shafts, sewage risers, smoke channels, water pumping equipment and ventilation devices.
The technical condition of roofs (steel and piece products) must be checked both from the outside and from the side of the attic "on the light." In some cases, the looseness of the roof is established by the presence of wet spots or snow on the grate and insulation of the attic floor. Before inspection, the roof is cleaned of debris, leaves and dust.
Main defects of roof load-bearing structures that may occur during their operation and require elimination:
wooden - violations of joints in the conjugations of rafters, destruction of waterproofing separating mauerlat from stone structures, bending of rafters' legs, rotting of mauerlats, rafters' legs, lattice and other elements;
reinforced concrete - destruction of concrete on the surface of articles, absence of protective layer of reinforcement, corrosion of reinforcement, breakage of corners, cracks, potholes, stratification, etc.
Main roofing defects:
steel - weakening of the connection of ridges and folds, the presence of single folds in drainage devices, corrosion, holes and fistula, destruction of the color or protective zinc layer;
roofs from piece elements (from asbestos-cement tiles, sheets, tiles, etc.) - damage and displacement of individual elements, lack of proper overlapping of conjugated elements, looseness in places of conjugation with structures and equipment protruding above the roof, weakening of roofing elements attachment to the screen .
It is necessary to regularly clean roofs from garbage (sand, dirt, etc.), as well as from snow and ice during external drainage. When cleaning the roof, you cannot sweep leaves and needles into the funnels of gutters, since, getting there, they adhere to the walls of pipes and, rotting, contribute to the development of corrosion. Gutters are cleaned in the spring. Structural structures
roofs (rafters, grids) are designed for a certain snow load. Exceeding it causes deflection of the bearing elements, as a result of which the connections of the roof cover are broken and leaks are formed. In winter and especially during thaws, to protect the roof with an external drainage from the prolonged impact of meltwater, it must be periodically cleaned of snow, preventing an increase in snow cover by more than 30 cm. Special attention should be paid to clearing gutters, stands, trays and funnels. To avoid one-sided overload of the roof with wooden rafters, snow should be removed evenly from both of its slopes. Asbestos cement roofs should be cleaned of snow from mobile ladders. It is forbidden to walk on the roof. The current "Rules and Standards for the Technical Operation of the Housing Stock" states that protective painting of black steel roofs should be carried out once every 6 years with oil paint on natural olive oil (twice) or other anti-corrosion protective paints at least once every 3-4 years. Before painting, the roof must be repaired. During operation, areas of roof with disturbed paint layer shall be painted immediately.
When corrosion occurs, galvanized steel roofs and gutters pre-cleaned from rust are also painted with oil paints and other anticorrosive compositions. It is advisable to paint roofs made of black steel and on the side of the attic, especially when corrosive lesions are found on the internal surface during inspection.
The domestic chemical industry produces a large range of paints and enamels that can be used for high-quality painting of roofs. The AKH LINE has developed technical guidelines for the use of these materials. For the painting of metal roofs, soils and enamels based on synthetic resins are recommended. LNII AKH together with the Leningrad Polytechnic Institute named after M.I. Kalinin developed coatings for metal roofs with which ice has a weak adhesion - these are complex coatings consisting of an epoxy layer and an organosilicon polymer layer. The coating compositions and technology are described in the Recommendations for the Use of Chemicals to Facilitate the Removal of Ice from Pitched Roofs.
Anti-icing compositions are applied only on a dry surface, previously cleaned of rust, fragile old color, dust and dirt. The first layer of coating consists of epoxy enamel EP5162 and soil-flooring EP-00-10. The composition is applied to the main surface of the sheets with a roller. Falcons are painted with brushes with a particularly careful color of bends. The drying time of the composition is 24 hours.
Organosilicon liquid GKZh94 is applied with tissue rags, which are soaked in the composition and squeezed out, after which it rubs the surface. The results of the adhesion strength tests of ice to the surface of the roof treated with anti-icing compositions showed that the adhesion strength of ice to the surface of such roof is 5-10 times less than with the surface of the roof painted with oil paint.
6. 3. Repair and sealing of metal roof.
Roofing maintenance includes:
repair of individual sections of steel coating with change of up to 10% of the entire roof, fixation of torn steel paintings;
repair of cornice overhangs, overwall and suspended gutters, gutters with partial addition of new material;
repair of the coating of firewalls, parapet walls, collars and heads of smoke and ventilation pipes, strengthening of parapets, antenna fasteners and other protruding elements and closing of the roof adjoins to the latter (blasting);
mandrel of folds (ridges) in the roof made of steel sheets with thiocol mastic, and in its absence - with suric putty;
periodic painting of roof and drainage devices.
In preparation for the repair of the steel roof in the workshop, the necessary number of paintings, their shares, aprons, drainage pipe links, etc. is harvested. In dry weather, the roof is swept and repair begins, which should be carried out by the links of the roofers (two people each). The work is carried out in the following order: eliminate damage in the glasses, above-the-wall troughs, on cornice overhangs; repair all damaged areas in the row roof of the slopes, starting from the lower part of the roof, and then moving towards the skate; in the last place, front overhangs, places of abutment to walls, collars of dormer windows, smoke and ventilation pipes and other protruding roof elements are repaired.
Repair often requires a partial or continuous change of the above-walled troughs and troughs. These roof elements are laid with significantly smaller slopes than the ordinary coating, so they
more are exposed to corrosion.
Starting to repair the gutters, you need to carefully inspect the state of coverage of the cornice overhang. If the latter is in unsatisfactory condition, it should first be repaired, and then the above-walled troughs. Damage usually occurs both on the cornice overhang itself and in water intake funnels. In the cornice coating, all bent places of the overlaps of the paintings are corrected, as well as the overhang line and its attachment places on crutches are leveled. Damaged places are cut and replaced with new ones. All funnels fixed on the cornice with wire are redone, removing them and cutting special pins (stirrups) into the board flooring.
In the above-walled troughs, the transverse folds of the paintings also rust, and the trays and folds connecting the trough with the row coating are deformed. In such cases, all defective areas in the troughs are cut and replaced with new ones.
When changing troughs and troughs, it is necessary to make extensions to the ordinary cover, since it is impossible to use old lying falcons of the ordinary cover to connect them with new or with cut troughs or troughs; ends of paintings in row strips for extensions are cut necessarily along the line of the next lattice bar.
In ordinary stripes, whole sheets or paintings are replaced if the damage on them (holes, fistula) is distributed evenly throughout the sheet, painting. If the holes or fistula are on a part of the sheet, and the rest of the surface is in a satisfactory state, then only the damaged part is replaced by the entire width of the strip. For this purpose ridges are opened and damaged section is cut out of strip. Then on upper and lower ends of strip edges are bent under recumbent folds along water flow and on place of removed part of strip there laid is patch of normal width, which is first connected with upper and lower parts of row strip, and then - with ridges. In the same way, a whole sheet or picture is replaced in an ordinary strip. All transverse joints of patches and sheets in strips should be made on the bars of the grid.
The necessary clammers are installed in the old places. Sometimes they are displaced up or down by one gap between the bars of the lattice.
Falcons and ridges broken during operation should be straightened, soaked and sealed, and the repaired roof painted with one of the compositions recommended above. If the existing painting is in satisfactory condition, only patches or new sheets shall be painted.
More elastic materials such as thiokol sealants should be used instead of the usually used suric grease on the olife to mash the folded joints in the most critical areas of the roof where water, snow and ice accumulate (folds of the trough, flutes, folds of the joint of the ordinary coating with the trough). Opened folds, places of attachment of fences, antennas, telephone and television racks and abutments of the roof to the structures crossing it can also be sealed with thiokol mastics.
Recommended for metal roofs thiokol mastic grades TM05 and AM05 consist of two components: thiokol paste (T05 for sealant TM05 and A05 for sealant AM05) and curing paste No. 30 (hardener). The hardener is introduced into the thiocol paste strictly by weight 17. h. Hardener on
100 h paste. With a smaller amount of hardener, the paste does not harden completely, and exceeding the required amount of hardener degrades the performance of the sealant.
After mixing the paste with the hardener, the viability of the sealant is 50-60 minutes, so it should be prepared in such an amount that it can be consumed during this time.
Roof areas to be sealed shall be previously cleaned with steel scrapers and brushes from rust, dust and dirt; the old suric putty is removed. The sealant is applied manually by a steel spatula with strong pressure on the surface. The duration of drying of the sealant layer is 24 hours. Existing folding joints, abutments and fixtures are washed from the outside. When setting up new false connections
the edges of the folds must be pre-soaked with a thiokol sealant.
To seal fistula and holes in the metal roof, the use of thiokol mastics is also recommended. Small fistula and holes are completely washed with sealant. If the holes are more than 10 mm, their edges are coated with mastic, and a cotton cloth patch is applied on top, which is pressed to the edges of the holes, after which it is washed with sealant again on top. On the side of the attic, the patch is also washed.
Using sealant, holes can also be sealed with roofing steel. In this case, the patch is strongly pressed to the edges of the hole, washed with thiocolic mastic, after which it is re-washed along the perimeter with sealant.
Sealants TM05 and AM05 are recommended to be used only at positive temperature, however, if necessary, it is allowed to perform the described works in a small amount and in winter at temperature up to - 15 ° C. Surfaces under sealant should be thoroughly cleaned from snow and ice and wiped dry.
Areas covered with thiokol sealant are not subject to additional painting. Domestic industry does not produce paint compositions for thiokol herme.tikov. In this regard, it is desirable to use lighter tones and be careful in the performance of work in order to avoid flows that worsen the appearance of the roof.
6. 4 . Improve temperature and humidity conditions and eliminate icing of attic roofs.
General provisions. The temperature-moisture mode of the attic room is crucial for ice formation. When creating a temperature regime in the attic room, at which the difference in the temperature of the outside air and the air of the attic room is 2-4 ° C, snow thawing does not occur, which means that ice and icicles are not formed.
Inspection of attic rooms, especially houses subject to intense icing, begins with measuring the air temperature of the attic room with an outdoor thermometer or a psychrometer. If the outside air temperature and the air temperature in the attic are higher than 4 ° С, the sources of heat supply to the attic room should be established, which may be: insufficient or poor-quality heat insulation of the attic room; unsatisfactory insulation of pipelines, air collectors, expansion units, ventilation and sewage risers, etc., located in the attic room. In addition, insufficient ventilation of the attic room is possible. To improve the temperature and humidity conditions of attic rooms and roofs, it is necessary first of all to bring their enclosing structures into a technically serviceable state and, if possible, to arrange a special natural ventilation system, placing ventilation holes under the roof overhang and in the building skate. In this case, the prompting forces of air exchange, the heat and wind head, are most used.
Thermal insulation of the attic room. First of all, it is necessary to establish the actual thickness of the bulk insulation. Measurement is carried out with a probe, which is easy to produce under the conditions of the operating organization. It is a steel pin with a centimeter calibration. The thickness of the bulk insulation must be at least 16-22 cm when filled with expanded clay gravel (^ = 500 kg/m3) or slag. Measurements are made at least at five points in different places of the floor. At the outer walls, the thickness of the insulation by a width of 30-50 s should be 2 times more than on the surface of the attic floor. Backfilling shall be in dry loose state With a device on the surface of protective lime-cement brace. If the attic floor is insulated with a slab insulator (for example, mineral wool, cement fibrolite, etc.), | "it is necessary to check the density of their laying (absence of gaps) and the presence of a safety brace. The effectiveness of the insulation can also be checked by measuring its temperature using a thermometer immersed in a 2 cm depth insulation.
Insulation temperature (in degrees) must also be dependent on ambient air temperature, but not less than
for example, at ambient temperature minus 30 ° С -
minus 21 ° С; and accordingly minus 20 ° С - minus 12 ° С;
minus 10 ° С - minus 1 ° С? 0 ° - plus 2 ° С. If the outside air temperature is between the specified values, for example minus 15 ° C, then the air temperature inside the insulation is determined by interpolation and is equal to minus 7.5 ° C.
To improve the thermal insulation of the attic floor, it is recommended to one of the following methods: a) increase the thickness of the insulation to the norm; b) it is recommended to add a lightweight insulation: expanded clay, mineral wool, mineral felt, polymeric insulation, etc. It is not recommended to add heavy insulation, such as slag, without first calculating the load capacity of the attic floor approved by the design organization; when changing the insulation, clay grease cannot be replaced by roll waterproofing, since the ventilation of the floor will be disturbed; c) when loose insulation is observed, perform loosening, which, according to operating rules, must be performed once every 5 years. Doors and hatches of attic rooms shall be covered with roofing steel according to asbestos or felt wetted in clay. For a dense narthex are necessarily needed: sealing gaskets made of rubber, polyurethane foam or other elastic materials.
Doors of hatches for the entrance to the attic must be kept closed in locks, and the keys should be stored in the nearest apartment or at the technician, as well as in the ODS control room.
Heat insulation of pipelines and ventilation shafts. Heat insulation check of central heating pipelines of hot water supply passing in attic room is performed by inspection. Bare participants and thermal insulation cracks are not allowed. It is checked whether the insulation thickness, which should be depending on the diameter | | > b, is sufficient, approximately at L pipes, mm: up to 40-4 cm; up to 150 - 5; YPL1H: 150-6.5 cm. You can measure the temperature of the outer layer of insulation by leaning against the surface of the thermometer through a plasticine patch. Temperature may be higher than ambient air temperature by not more than 4 ° С.
If thermal insulation is disturbed, it is necessary to repair it and insulate the bare areas. In case of insufficient insulation | add another layer of white clay with clays or wrap the pipeline with mineral felt, which is attached with metal or wire. It is also necessary to isolate the expansion tanks, air collectors, heat valves, etc., are made in the form of wooden boxes with backfilling or lining with mineral wool .
Section. Improvement of the territory
The basis of the formation of the improvement system.
The general principle of the formation of urban territories is to provide maximum amenities to the population in ensuring their socio-cultural and household needs with the rational use of resources and urban land.
The specifics of the functional and planning organization of various types of territories predefine a different approach in the organization of the external improvement system, the maintenance and operation of its individual elements. At the same time, there are a number of general provisions that form the basis for the formation, maintenance and operation of the system of improvement of residential complexes of the city.
In the current conditions of intensive socio-economic development of cities, the transformation of their planning structure, mass reconstruction of buildings, the formation of the housing market, the problems of external improvement should be solved at a high artistic and scientific and technical level.
The improvement of urban areas is a complex, multidimensional task. The concept of "improvement" includes a set of measures:
- on engineering improvement (engineering training and engineering equipment, artificial lighting), social and household improvement (improvement of the system of social and consumer services of the population);
- external landscaping (landscaping, organization of traffic and pedestrians, equipping the territory with small architectural forms and improvement elements).
The complex of improvement measures also includes works related to environmental improvement, improvement of sanitary and hygienic conditions of residential buildings, which provide environmental improvement of the territory.
The improvement process of the facility includes, first of all, the design of the improvement system, the implementation of the landscaping project, the maintenance and technical operation, repair and reconstruction of the improvement system of the facility and its elements.
The composition, content and scope of work in certain areas of improvement of urban areas depend on many factors. First of all, from the period of construction of residential buildings, the quality of maintenance of the existing housing stock, the state of engineering infrastructures, the saturation and level of provision of territories with social services institutions, urban planning, engineering, transport and environmental situation in the territories of residential development and adjacent areas, etc.
The comfort criterion of the made decisions on improvement should be considered their compliance with regulatory indicators, ensuring:
- full provision of services in the sphere of social and domestic improvement;
- nomenclature of small architectural forms and layout elements, size and availability of planning elements of improvement;
- required sanitary, hygienic and environmental conditions.
1. Territory Engineering Training
1.1. Vertical layout of the adjacent area of the hotel.
The adjacent territory is planned to be gable, providing natural drainage of surface water. Design elevations are accepted so that the slope is at least 0.005. The planning of the territory is carried out based on the proposal of the smallest mass haul movement.
1.2. Organization of the terrain.
Relief is organized in such a way as to ensure natural removal of surface water from the territory of a residential group. Water is drained along the surface and with the help of open trays. Water is drained along the surface due to the natural (existing) slope of the relief or in the absence of a sufficient slope of the territory due to an artificially created slope (by filling or cutting off soil sections).
As open trays, trays of the carriageways of highways, main and secondary passages are used.
The organization of drainage from the territory should be linked to the drainage system of the microdistrict, that is, it should be resolved comprehensively with mandatory compliance with the condition for its passage through narrow streets and roads, thereby ensuring the removal of most storm drains.
Inner-district driveways and an open network of trays along which water is drained must be coordinated with each other in height and with the marks of city streets.
The design of the vertical layout of the residential group begins with
determining the elevations of the intersection of main streets. All points of the territory of the residential group should be located above the elevations of the adjacent street trays at the exit points.
Minimum slope of landscaping areas directed towards adjacent internal passages shall be at least 0.005. It can approach the natural terrain and can fall into slopes if this is consistent with the requirements of the architectural solution of this residential group. To protect the foundations from damp, a pavement with a width of 1 m and a slope of 0.05 is arranged along the building.
The main passage is arranged gable with a transverse slope of 0.02. The driveways to the buildings are taken as single-pitched with a slope of 0.02 from the building. At the point of abutment, the transverse slope of the secondary passage is taken equal to the longitudinal slope of the main passage.
2. Improvement of the residential group.
2.1. Sites of various purposes, their sizes and placement principles, characteristics of small architectural forms.
Placement of sites in relation to the development and other planning elements is carried out taking into account their accessibility, safety of operation. Noise characteristics created by these sites are also taken into account.
The terrain of the sites should meet the requirements of rainwater discharge, the surfaces of the sites should be floodless, and after rain or watering, quickly dry out.
Lighting of recreation areas should operate in one mode during the evening. It is designed, as a rule, built into the equipment elements of the sites.
When maintaining adult recreation grounds, it is necessary to make increased requirements for their artistic and coloristic design, using atypical solutions of small architectural forms (benches, fences, decorative sculptures), various coatings, flower beds for improvement.
In the adjacent territory it is necessary to provide for the presence of sites of various purposes. Sites will be provided:
- adult recreation grounds;
- site for waste collectors;
The adult recreation area is removed from the building as much as possible, a gazebo or benches are placed on it. Shading of such a site shall not exceed 60%.
- parking of cars;
Sites for garbage collectors should have an entrance for transport. For masking the site, reinforced concrete or brick walls 1.21.8 m high are also used. Containers are installed at a distance of no closer than 1 m from the fence .
Garages and open parking spaces for car storage should be provided in the territory. Parking will be located on the courtyard of the hotel. Open parking should be provided at the rate of at least 70% of the estimated fleet of individual cars. Including allowed all-season storage of 25% of the number of cars in the garage. The garage is designed with a car wash and repair shop.
A complete list of small architectural forms is provided in the small architectural form list in sheet drawing 12.
2.3. Designing pedestrian links.
The network of footpaths should be rationally organized in order to provide convenient shortest possible approaches from any exit to public transport stops, parking lots, gardens, shops and other buildings of cultural and consumer services, that is, in the direction of the main pedestrian routes. They should also provide approaches to recreation areas. Walkways should also provide recreational opportunities, bringing pedestrians to the most landscape-winning elements of the territory. In the case when a pedestrian network is formed within a residential development irrationally, residents of microdistricts and neighborhoods spontaneously determine more rational routes of pedestrian communications. In this case, it is more advisable for operating organizations to consolidate the current situation by arranging footpaths, paved sidewalks or special pavements along these directions.
The width of the main walking routes is calculated based on the intensity of walking, and is 2.25-3.0 m. The width of one lane is assigned 0.75 m. Secondary paths are usually arranged with a width of 0.75-1.5 m. Pedestrian alleys, paths and paths, as a rule, should be the same width throughout.
It is allowed to expand them, mainly to install leisure benches on them.
Operating organizations should take into account that pedestrian routes within the territories should be adapted for the movement of disabled people and people with diseases of the musculoskeletal system. For the convenience of residents using wheelchairs for their movements, pedestrian paths must be laid with slopes from 4 to 50% 0, equipped not only with stairs, but also with ramps that soften
significant slope by horizontal sections.
2.4. Selection and justification of types of pavements of streets, tracks, sites.
The types of pavement of tracks and platforms may vary. For sidewalks, footpaths, sites (on which systematic traffic is not provided, but vehicles with a standard axle load of up to 6 tons can enter), the use of artificial prefabricated coatings, as well as natural coatings, is rational. When selecting coatings, you should be guided by the purpose of the footpath or platform, the intensity of its use, the color-facture characteristics of the coatings, and the capabilities of mechanized cleaning using sidewalk harvesting equipment.
Adult recreation grounds are covered with tiles laid throughout the site. Driveways must be adjacent to the carriageways of residential streets and highways of the district value of regulated traffic or to local driveways of highways of the citywide value of continuous traffic.
In the reconstructed areas, in order to ensure normal conditions for traffic and the separation of transport and pedestrian traffic, it is necessary to streamline the arrangement of transport passes and reduce the number of departures to adjacent streets. Such a solution is necessary to reduce or eliminate conflict points that complicate traffic on adjacent highways of the city.
Roadwear structures of driveways are of an improved capital type, for fire driveways - improved lightweight, provided that the design load from fire engines is 20 tons per axle.
Waste container sites shall have asphalt or concrete paving with a slope of 0.02 towards the roadway.
Parking lots are arranged with asphalt pavement.
The coating designs are shown in sheet 12.
Conclusion
During the thesis project on:
"Modernization of the hotel" Tambov "on the street. Embankment 90/2 "
was performed in the following sections:
- Architectural: redevelopment of existing hotel buildings in accordance with modern requirements for * * * class hotels, insulation was performed and the historical facade, longitudinal and transverse sections were preserved, heat engineering calculations of fences were made;
- Design design: calculation of a monolithic slab of the floor by metal beams, calculation of a new wooden covering of the building;
- Technological: Process instruction for removal and development of roof has been developed;
- Organizational and economic: the network schedule was developed and calculated, its binding to the time scale was carried out, the scope of work was determined, local and object estimates were calculated;
- Engineering equipment of the building: calculation of the domestic water supply system of the building; designed water supply, heating, ventilation, vertical transport, garbage removal systems;
- Maintenance: maintenance of roofs and attic rooms, improvement of temperature and humidity conditions of attic roofs;
- Landscaping of the territory: landscaping of the adjacent territory of the hotel, arrangement of driveways, paths, sites, equipment of the territory with small architectural forms;
- Ecological: study of the residential quarter on the degree of environmental pollution, rational use of water resources, waste disposal, provision of noise and solar conditions of the built-up area, environmental protection, noise protection and waste disposal during the reconstruction of the quarter;
- Occupational Safety and Civil Defense: earthing device was calculated, illumination was calculated by the use factor method and a shelter was designed in the hotel basement.
Монолитка.dwg

ОРГ.dwg

ТЕХНОЛОГИЯ.dwg
