Heat supply of an urban-type settlement in the Tambov region








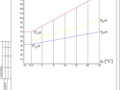
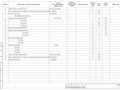

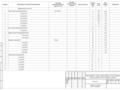
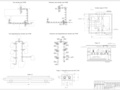
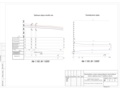
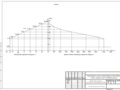
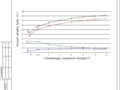
- Added: 21.04.2022
- Size: 3 MB
- Downloads: 2
Description
Characteristics of the construction area
The village is located among the Russian Plain in the Central Black Earth District, 500 kilometers from Moscow.
The temperate continental climate of Tambov is largely determined by its position. In this climate, all seasons are pronounced. 21 days in July and 20 days in January, it is the continentally temperate air that determines the weather. So, the average temperature in January is about -10 degrees Celsius, in July - about 25. The average annual air temperature in the region is 5.3 degrees Celsius, the annual rainfall ranges from 350 to 700 mm, more than half of them (about 300 mm) falls in the warm period of the year. The duration of the growing season is 178 days in the north and 185 days in the south.
Graphic part: Heat network plan; installation diagram of the heat network; plan of the intra-quarter heating network; wiring diagram of the intra-quarter heating network; Incision 1-1; Incision 2-2; Incision 3-3; Thermal chamber UT1
Longitudinal profile of the heat network; Piezometric graph
Schematic diagram of ITP; Schematic diagram of the CTP; Bellows axial compensator; Thermal insulation design
Specification
Annual heat load duration graph
Temperature graph São Paulo
Schedule of expenses
Explanatory note:
CONTENTS
1. Analysis of the design object and determination of the attached thermal loads
1.1. Characteristics of the construction area
1.2. Determination of attached thermal loads
1.2.1. Maximum heat flow for heating microdistricts
1.2.2. Maximum heat flow for ventilation of microdistricts
1.2.3. Maximum and average hourly heat flows for hot water supply of microdistricts
1.2.4. Maximum heat flow for heating of the selected microdistrict
1.2.6. Maximum and average hourly heat flows for hot water supply of the selected microdistrict
1.3. Annual graph of duration and recurrence of heat load
2. Regulation of heat energy release
2.1. Choosing the method of regulating the release of heat for heating, ventilation and hot water supply
2.2. Qualitative regulation of heat supply for heating
2.3. Qualitative regulation of heat supply to ventilation
2.4. Qualitative regulation of heat supply to hot water supply
3. Hydraulic calculation of heating network pipelines
3.1. The main tasks of hydraulic calculation
3.2. Determination of the calculated costs of the coolant
3.3. Hydraulic calculation of main heat pipelines
3.4 Hydraulic calculation of thermal distribution ducts
4. Construction of the longitudinal profile of the heat network of the microdistrict
5. Construction of piezometric graph of the heat network of the microdistrict
6. Thermal calculation of the heat network
6.1. Thermal calculation of the thermal insulation structure.
6.2. Calculation of thermal insulation of pipelines of heat networks with two-pipe laying in an impassable channel
6.3 Determination of the temperature drop of the coolant along the length of the pipeline
7. Mechanical calculation of the heat network
7.1 Determination of distances between fixed supports
7.2 Determination of the mounting length of the gland compensator.
7.3 Verification of the possibility of using the angle of rotation of the track for self-compensation
7.4 Determination of support forces
8. Central heating station equipment
8.1. Selection of the strapping scheme of the heat exchange equipment of the TSP
8.2. Calculation of heat exchangers installed on the TSP
8.3. Selection of network and make-up pumps at the CTP
9. Equipment of an individual heating unit
9.1. Selection of the strapping scheme of itP thermal equipment
Bibliography
Appendix 1 – Graph of the annual duration of the heat load
Annex 2 – Temperature graph
Annex 3 – Schedule of expenses.
Annex 4 – Characteristics of pumps
Project's Content
![]() ![]() ![]() |
![]() ![]() ![]() |
![]() ![]() ![]() |
Additional information
Contents
PAPER
INTRODUCTION
1. Analyze the design object and define the heat loads to attach
1.1. Characteristics of the construction area
1.2. Define heat loads to attach
1.2.1. Maximum heat flow to the heating of microdistricts
1.2.2. Maximum heat flow to microdistrict ventilation
1.2.3. Maximum and average hourly heat flows to the hot water supply of microdistricts
1.2.4. Maximum heat flow to the heating of the selected microdistrict
1.2.6. Maximum and average hourly heat flows to the hot water supply of the selected microdistrict
1.3. Annual schedule of heat load duration and recurrence
2. Regulation of heat energy release
2.1. Choice of heat release control method for heating, ventilation and hot water supply
2.2. Quality control of heat release for heating
2.3. Quality control of heat release for ventilation
2.4. Quality control of heat release to hot water supply
3. Hydraulic calculation of heat network pipelines
3.1. Main tasks of hydraulic calculation
3.2. Determination of design coolant flow rates
3.3. Hydraulic calculation of main heat lines
3.4 Hydraulic calculation of heat distribution lines
4. Construction of the longitudinal profile of the thermal network of the microdistrict
5. Construction of a piezometric plot of the thermal network of the microdistrict
6. Thermal calculation of the heat network
6.1. Thermal calculation of thermal insulation structure
6.2. Calculation of thermal insulation of pipelines of heat networks during double-tube laying in the impassable channel
6.3 Determination of coolant temperature drop along the pipeline length
7. Mechanical calculation of the heat network
7.1 Determination of distances between fixed supports
7.2 Determination of mounting length of gland compensator
7.3 Check whether the route angle can be used for self-compensation
7.4 Determination of forces on supports
8. Central Heat Station Equipment
8.1. Selection of TTC heat exchange equipment piping diagram
8.2. Calculation of heat exchangers installed on CTP
8.3. Selection of mains and makeup pumps at CTP
9. Equipment of individual heat station
9.1. Selection of thermal equipment piping diagram
List of literature used
Annex 1 - Schedule of annual heat load duration
Appendix 2 - Temperature Schedule
Appendix 3 - Expenditure Schedule
Appendix 4 - Pump Specifications
Paper
The explanatory note contains 84 pages, 14 tables, 3 figures, 19 sources of used literature.
HEAT FLOW, HEAT RELEASE CONTROL, MICRODISTRICT, HYDRAULIC CALCULATION, HEAT NETWORKS, MECHANICAL CALCULATION, HEAT STATION, BOILER HOUSE, HEAT POWER EQUIPMENT, PUMP
The design object is a microdistrict for 13,400 people in Orenburg.
Purpose of work:
determination of required coolant flow rate to maintain permissible microclimate parameters by building heating and ventilation systems;
determination of the required coolant flow rate to satisfy the sanitary and hygienic needs of the population by hot water supply systems;
design and calculation of pipelines of main and distribution networks of district heat supply from the district boiler house;
selection of equipment for central and individual heat stations;
calculation of heat scheme of the hot water boiler house.
During operation, the following are calculated: thermal loads of consumers, heat release control mode, temperature and hydraulic mode, determination of optimal insulation thickness and thermal calculation of heat networks, as well as construction and installation elements of heat networks and energy-saving measures.
Introduction
Heat supply means a system for providing heat to buildings and structures. Centralized heat supply systems, which ensure the most economical use of fuel, have the highest economic indicators, and are characterized by lower specific fuel consumption for the generation of thermal energy.
Centralized heat supply is based on the use of large district boiler houses, characterized by significantly higher efficiency than small heating plants.
Heating, i.e. centralized heat supply based on combined heat and power generation, is the highest form of district heat supply. It reduces fuel consumption by 2025%.
The centralized heat supply system consists of the following main elements: a heat source, heating networks and local consumption systems - heating, ventilation and hot water supply systems.
The design object is a working village in the Tambov region.
Hydraulic calculation is performed to determine pressure losses in heat networks and heat pipeline diameters. After calculation of systems equipment is selected. Part of equipment selection calculations is performed on the computer.
Equipment of individual heat station
9.1. Selection of thermal equipment piping diagram
In the heating system with temperature controllers, it is recommended to use:
-from the thermal power of the system 25 kW and more - a pump with a controlled number of revolutions taking into account the pressure difference in the supply and return pipelines;
-from thermal power of the system up to 25 kW - pump with controlled number of revolutions; for a pump with a constant number of revolutions, it is necessary to provide a jumper between the supply and return pipelines with an automatic bypass valve.
The Power Value Quoted is an En EV Directive on Power Saving effective from 01.02.2002 (adopted in final version in November 2001). This directive aims to reduce CO2 emissions to the atmosphere from electricity generation. According to the directive, pumps installed in the circulation circuits of heating systems with boilers with a capacity of more than 25 kW must have at least three stages of rotation speed control and ensure electricity consumption in exact accordance with the heat losses of the building due to external air temperature. Heating systems shall have at least two circulation pumps connected in parallel or one dual pump. One of these pumps is standby. At the same time design parameters
pumps are determined in two ways:
-100% reservation;
-peak load.
The first method: one working pump, the second - standby. Switching from one to the second for uniform wear is carried out automatically after 24 hours. Each pump at this operating mode is selected to supply the entire design coolant flow rate. It is recommended that both pumps be equipped with automatic engine speed change devices to ensure that the hydraulic performance of the system is best met in the partial load mode.
The second method: twin pumps are selected for the 50% design load of the system for each pump. With low heat loads, one pump operates in a 24-hour shift mode with another pump. The pump is controlled by an automatic speed changeover and control device. In peak mode, both pumps operate in parallel.
Two large pumps consider the expediency of replacing them with three smaller ones. From an operational and economic point of view, such a replacement has its advantages.
In small heating systems (for example, cottages), it is not necessary to reserve the pump.
The use of an automatically adjustable pump does not replace its correct selection. The following must be taken into account:
- design point of the automatically controlled pump must not be lower than the operating point (indicated by a bold point) by more than 25% (by coolant flow rate); for a non-adjustable pump - not lower than by 10%;
-The calculation point can be no more than 10% higher than the operating point for automatically adjustable and non-adjustable pumps;
-The operating point shall be in the maximum pump efficiency area;
-operational increase of coolant flow caused by opening of heating system temperature controllers shall be located in the working zone of pump characteristic;
if several pumps meet the design characteristics of the system, it is necessary to select a pump of lower capacity.
The allowable decrease in the hydraulic parameters of the pump is determined taking into account that a decrease in the coolant flow rate by 25% in heating systems leads to a slight decrease in the heat flow of the heating device (by about 7%). This shortfall is fully compensated by the overstated heating capacity of the heating device by 10% and the ability of the temperature controller to open, passing a larger coolant flow rate.
Чертеж2.dwg
Чертеж1.dwg
Similar materials
- 09.07.2014