Development of the technological process of casting the hub







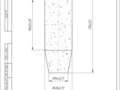

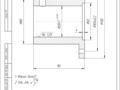
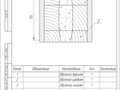

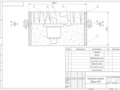
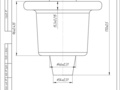
- Added: 03.02.2022
- Size: 684 KB
- Downloads: 1
Description
Developed a technological process of casting the hub
Project's Content
![]() |
![]() ![]() ![]() |
![]() ![]() |
![]() ![]() |
![]() ![]() ![]() ![]() |
![]() ![]() ![]() ![]() |
![]() ![]() ![]() ![]() |
![]() ![]() ![]() ![]() |
![]() ![]() ![]() ![]() |
![]() ![]() ![]() ![]() |
Additional information
Contents
Introduction
1 Sand-clay casting. Process Features
2 Chemical composition, physical-mechanical and technological properties of the material
3 Determination of part weight
4 Workpiece type and machining allowance
4.1 Development of casting drawing, definition of tolerances, dimensions and allowances for machining
4.2 Calculation of runner system elements
Conclusion
List of literature
Introduction
Essence of foundry consists in production of billets or parts by pouring of molten metal of specified chemical composition into casting mould, cavity of which has configuration of billet or part. Upon cooling, the poured metal solidifies and retains the shape of the mold cavity. The cast blanks are further machined. Castings of both simple and complex configuration with internal cavities are obtained by casting. The most important task of foundry production is to obtain castings in shape and size approaching the finished part, which significantly reduces cutting treatment.
Casting in sandy-clay forms. Process Features
Sand-clay casting is a common and relatively simple method of casting. Single sand-clay forms can be prepared either directly in the soil (in the floor of the foundry) according to templates, or in special support boxes according to models.
Casting into sandy-clay molds has its advantages. These include:
- casting mass can reach the value of hundreds of tons (machine bed),
- sizes from several millimeters to tens of meters,
- can be made of any configuration and of any casting alloys. This method produces the vast majority of castings in machine building.
Moulding mixture is used to produce mold, which is multicomponent system, composition of which is determined by type and mass of casting, and nature of metal. The main components of the moulding mixture are quartz sand and moulding clay. The clay is a binder and at an optimal water content (45%) gives the molding mixture the necessary strength and ductility. The sand increases the porosity and hence the gas permeability of the molding mixture. In addition, anti-stick additives (coal-tar dust, graphite), protective additives (boric acid) and other ingredients are added to the molding mixture. For the production of rods, rod mixtures consisting of quartz sand and self-solidifying inorganic (liquid glass with an addition of 10% solution of NaOH) or organic binders are used.
Casting molds - the process of filling the cavity of the mold with molten metal from a ladle. Ladle with molten metal is transported from smelting furnaces to casting place by means of bridge crane or via monorail track.
It is important to select the casting temperature of the molten metal when casting molds. At an increased pouring temperature, the fluid flow of the metal increases, the nutrition of the castings improves, but the hot metal is more gas-saturated, oxidizes more, causes burning on the surface of the casting. At that
while the low filling temperature increases the risk of the mold cavity not filling, air gripping, the casting power is deteriorated. The casting temperature of the alloys is suitably set to 100150 ° C above the liquidus temperature.
Cooling of castings in moulds after pouring continues to knock-out temperature. Small thin-walled casts cool in shape for several minutes, and thick-walled (weighing 5060 tons) - for several days and even weeks.
To reduce the cooling time: the molds are blown with air; coils or pipes are laid into moulds during moulding, through which air or water and others are passed. At the same time, the quality of castings does not deteriorate.
Casting is the process of removing solidified and cooled castings from a mold to a certain temperature, while the mold is destroyed. Castings are knocked out at various knock-out units.
Cleaning of castings - the process of removing tart, residues of the molding and rod mixture from the external and internal surfaces of the castings.
First of all, castings are monitored visually to identify defects or castings to be corrected. The correct configuration and dimensions are checked by marking, the density of the casting metal is checked by hydraulic tests under water pressure up to 200 MPa. Internal defects are detected in specialized laboratories.
Conclusion
In this work theoretical foundations of metal processing by casting are considered, analysis of material is carried out, mass of part is determined, calculation of allowances for mechanical processing of workpiece is carried out, drawing of workpiece is built and its mass is calculated.
The high material utilization rate indicates that the correct method of obtaining blanks is chosen, which provides minimum allowances, maximum approximation of the shape of the blank to the shape of the part. The analysis of the shape of the workpiece also indicates that the shape is not complex, which makes it economically feasible to produce the workpieces according to the proposed technology.
Деталь.m3d

отливка ступицы.m3d

литейная форма.cdw

Модель _ РГР1.ПиПЗ.МО41.2019.06.04.00.00.cdw

Стержень _ РГР1.ПиПЗ.МО41.2019.06.03.00.00.cdw

Ступица (отливка) _ РГР.ПиПЗ.МО-41.2020.15.00.00.00.02.00.cdw

Ступица _ РГР.ПиПЗ.МО-41.2020.15.00.00.00.01.00.cdw

Ящик стержневой.cdw

Similar materials
- 25.01.2023
- 25.01.2023
- 25.01.2023
- 25.01.2023
- 13.05.2022
- 25.01.2023
- 25.01.2023