Development of an automatic line for zinc coating









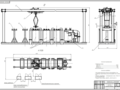
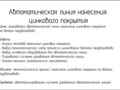
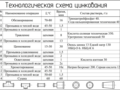
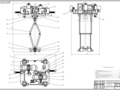
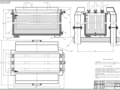
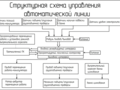
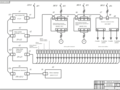
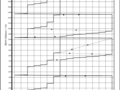
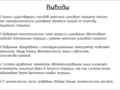
- Added: 01.05.2022
- Size: 7 MB
- Downloads: 4
Description
Graduation qualification project in the specialty 15.03.04. Includes: Explanatory note, graphic part.
Composition of the explanatory note:
Introduction
1 Technological section. Area of application of zinc coatings. Methods of applying zinc coatings. Technological schemes of the galvanizing process. Description of the technological process of galvanizing. Rationale for the automation of the zinc coating line. Comparison of domestic and advanced foreign technologies and solutions. Findings.
2 Design section. Layout of the automatic line for zinc coating. Selection of the main equipment for coating. Selection and justification of the manipulator of the automatic line for applying zinc coating. Findings.
3 Project section. Development of a manipulator control system. Development of an automatic line control system for zinc coating. Selection of technical means of controlling the automatic line for applying zinc coating. Development of a cyclogram of the automated line for applying zinc coating Conclusions.
4 Life safety.
5 Organizational and economic section.
Project's Content
![]() ![]() ![]() ![]() |
![]() ![]() ![]() ![]() |
![]() ![]() ![]() ![]() |
![]() ![]() ![]() ![]() |
![]() ![]() ![]() ![]() |
![]() ![]() ![]() ![]() |
![]() ![]() ![]() ![]() |
![]() ![]() ![]() ![]() |
![]() ![]() ![]() ![]() |
![]() ![]() ![]() ![]() |
![]() ![]() ![]() ![]() |
![]() ![]() ![]() ![]() |
![]() ![]() ![]() |
Additional information
Contents
INTRODUCTION
1 COMPARISON OF DOMESTIC AND ADVANCED FOREIGN TECHNOLOGIES AND SOLUTIONS
1.1 Analysis of existing zinc application methods
coverings
1.2 Overview of manipulator designs for galvanic processing
1.3 Types of planning solutions when designing automated lines for electroplating
2 PROCESS SECTION
2.1 Zinc Coating Technology
2.2 Description of zinc coating process
2.3 Overview of products subject to zinc coating
2.4 Description of the automated zinc coating line
3 DESIGN SECTION
3.1 Development of manipulator design
3.2 Calculation and selection of manipulator actuators
3.3 Calculation of manipulator control system
3.4 Development of a bath for zinc coating
3.5 Structural diagram of automated line control
3.6 Development of connection diagram of the automated line control system
3.7 Cyclograms of automated line operation
4 Life safety
4.1 Ensuring safe working conditions at the automated site
4.2 Calculation of general lighting
4.3 Measures to reduce the effects of earthquakes
5 Organizational and Economic Section
5.1 Capital Cost Calculation (Base Case)
5.2 Calculation of operating costs (base case)
5.3 Capital Cost Calculation (Projected Version)
5.4 Calculation of operating costs (design version)
5.5 Calculation of economic efficiency of the project
CONCLUSION
BIBLIOGRAPHIC LIST
Introduction
Galvanic production is unusually widespread and is available in almost any enterprise related to the manufacture of metal parts and products.
The wide use of galvanic coatings leads to a wide variety of galvanic workshops, both in the types of processing of parts and in the performance of equipment.
One of the main functions of galvanic production is anti-corrosion protection of parts. There are quite a number of methods of anticorrosive treatment of parts, for example, the application of a coating that prevents the formation of a corrosion element (passive method) can be used as a corrosion protection.
One of the cheapest and most economical methods of corrosion protection is galvanic galvanizing, that is, coating steel with a thin layer of zinc. It provides durable and reliable corrosion protection.
However, there are problems of imperfect production of zinc coatings.
Currently, galvanic galvanizing lines are dominated by the so-called manual galvanic production, which has a lot of shortcomings, the main of which is the harmful effect on the human body.
The uncontrolled action of metal ions poses a danger not only to the health of the current generation, but also to subsequent ones, and every year this threat to humanity is increasing. Heavy metal ions, penetrating with water and food into living organisms, are able to accumulate in them, causing pathogenesis of the heart, brain, liver and other important organs in humans. According to the scale of stress factors for the effects on the human body, heavy metal ions are put first (135 points), leaving factors such as noise effects (15 points), radioactive waste (40 points), chemical fertilizers (63 points), oil spills (72 points) far behind.
Manual galvanic production of anti-corrosion processing of parts is an "effective" brake on the implementation of low-waste and non-waste production, since the movement of parts by hand or telfer does not guarantee compliance with technological discipline. In fact, the absence of a certain rate of lifting of parts from the baths, non-compliance with the time spent in the washing baths, as well as the time to drain, only contributes to an increase in electrolyte removal.
Currently, many enterprises need to introduce automatic and automated lines for electroplating parts in order to reduce industrial diseases, as well as reduce costs, chemicals; washing water; sewage water; recovery of electrolytes and non-ferrous metals; for effluent treatment; for sludge disposal.
Comparison of domestic and advanced foreign technologies and solutions
1.1 Analysis of existing zinc coating methods
Zinc protective coatings are applied by the following methods:
a) hot galvanizing of steel structures;
b) cold galvanizing (colouring);
c) thermodiffusion galvanizing;
d) electroplating (galvanizing).
Description of the automated zinc coating line
The automatic line shown in Figure 2.3 consists of baths 5 arranged in one row. Between baths there installed are side suckers and visors (6). Along the baths along the guides 2, a robot manipulator 1 moves on the columns, transferring parts from one bath to another.
The manipulator operates according to the specified program, moving the parts in accordance with the process.
There are working and idling robotic ampanipulators, as well as forced outages. The traffic pattern is "shuttle" in nature.
The robot manipulator is fixed above the automatic line and has two drives of horizontal and vertical movement. Such drives consist of a worm reduction gear, an electric motor and a disc brake controlled by an electromagnet. Load-gripping devices are installed on load-lifting cross-arm. They serve to center and hold the load carried by the car operator.
03.cdw

05 Спецификация.spw

03 Спецификация.spw

01.cdw

06.frw

04 Спецификация.spw

07.cdw

05.cdw

02.cdw

08.frw

09.cdw

04.cdw
