Development of a general purpose with detailed calculation of a single-stage conical gearbox, chain transmission



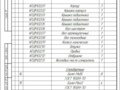
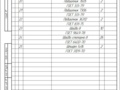
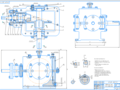
- Added: 23.10.2021
- Size: 5 MB
- Downloads: 1
Description
Calculation of conical gearbox and chain transmission
Project's Content
![]() ![]() ![]() ![]() |
![]() ![]() ![]() ![]() |
![]() |
![]() ![]() ![]() |
![]() ![]() ![]() ![]() |
![]() ![]() ![]() ![]() |
![]() ![]() ![]() |
![]() |
![]() ![]() ![]() |
![]() |
![]() ![]() ![]() |
![]() |
Additional information
Contents
Literature Review and Patent Analysis
Motor selection and motor kinematic calculation
Electric motor selection
Kinematic calculation of the drive
Power calculation
Calculation of chain transmission
Geometric parameters of chain transmission
Check calculation of chain transmission
Calculation of closed bevel gear train
Select Wheel Material
Definition of allowable contact stresses
Defining Allowable Bend Stresses
Design calculation
Check calculation
Gear shaft loads
Determination of forces in closed gear engagement
Definition of cantilever forces
Design calculation of shafts. Gearbox Sketch Layout
Select Shaft Material
Selection of allowable torsional stresses
Defining the Geometric Parameters of Shaft Steps
Calculation of shafts for static strength
Definition of reactions in bearing supports and construction of curves and torques of the 1st shaft
Defining Reactions in Bearing Supports and Constructing Symbols
bending and torques of the 2nd shaft
Second stage of gearbox arrangement
Test of key joints strength
Drive shaft
Driven shaft
Refining calculation of shafts
Drive shaft
Driven shaft
Coupling selection
Selection of lubricant in gearbox
List of standards used
Conclusion
List of literature
Paper
This calculation and explanatory note contains all information about the work done on the implementation of the course project.
The course design consists in the design of a general-purpose drive according to the specified output parameters and according to the specified drive scheme. This drive consists of an electric motor, a single-stage conical reduction gear, and a chain transmission.
Serviceability of the designed drive is confirmed by check calculations. Part handling and actuator assembly are shown in the graphic part of the course design.
The calculation and explanatory note contains:
sheets - 42
Figures - 8
tables -2.
There are 3 working drawings on A1 sheets:
1 sheet - working drawing of general view of the drive
2 sheet - working drawing of reduction gear box in section
3 sheet - working drawing of parts
All drawings are in accordance with ESKD codes and regulations.
Literature Review and Patent Analysis
Single-stage wheel reduction gear
Patent number: 143667
Author: Steshenko
The known single-stage internal engagement wheel reducers have large dimensions and high weight, so that they cannot be placed inside the hub of the automobile wheel. When the gearboxes are located outside the wheel hub, next to the brake drum, there is an uneven load on the support bearings, which causes increased wear of the latter, which leads to a violation of the correct engagement of the gears.
To eliminate these disadvantages, the drive gear of the described reduction gear is symmetrically located between the supports of the drive shaft, which is eccentrically mounted in a journal equipped with a cylindrical open recess. The gear rim of the driving gear protruding from the trunnion recess is in internal engagement with the gear rim of the wheel hub, also symmetrically located between the bearing supports of the trunnion. Thanks to this embodiment, the design is compact, easy and rigid. This allows you to place the reduction gear inside the hub of the car wheel, without practically increasing the size and weight of the latter. Symmetrical arrangement of gears relative to bearing supports and brake drum ensures uniform load on bearings and correct engagement of gear rims.
The figure shows a single-stage wheel reduction gear assembly with a brake drum in a longitudinal section.
Drive gear 1 of reduction gear is fitted on splines of shaft 2, which is mounted on needle bearings and located in trunnion 3. The latter is rigidly bolted to wheel suspension lever 4. Hub 5 is mounted concentrically to trunnion 3 on conical bearings and provided with gear ring of internal engagement in the middle.
Due to the eccentric arrangement of the shaft 2, the toothed rim of the driving gear 1 protrudes through an open annular recess in the trunnion 3 and is in engagement with the toothed rim of the hub 4.
Brake drum 6 is bolted to flange of hub 4.
Gears and bearings of reduction gear are protected by covers (7) and (8) attached to hub (5). Shaft 2 and journal 3 are provided with gland seals 9 and 10 for retention of lubricant. Clearance in conical roller bearings is adjusted by means of adjusting gaskets and tension nuts 11.
The single-stage wheel reduction gear is operated as follows.
Rotation from the power unit half-axle is transmitted to the reduction gear 1 by means of a cardan joint (not shown) connected to the shaft 2. Gear 1, being in constant engagement with toothed rim of hub 5, rotates the latter. Brake drum 6 rigidly secured to hub 5 and wheel disk attached thereto are rotated. At that direction of rotation of power unit half-axle and driven wheel coincide, and speed of wheel rotation decreases in proportion to gear ratio of gear pair of reduction gear.
The prototype of the described gearbox is currently undergoing industrial tests on a microlithrage truck of the Zaporizhzhya automobile plant Kommunar. Drive wheel of car with built-in wheel reduction gear of internal engagement by its weight, compactness of balance practically does not differ from wheel without reduction gear.
Conclusion
During the course project, the skills of phased design of machine parts and their implementation in drawings were acquired. With independent work on the project, the ability to choose the optimal design solution was developed. Knowledge of the subjects of previous courses has expanded and deepened.
During the course design, the general principles of calculation and design of typical parts (shaft, gear wheel, bearing cover) were learned taking into account the technical requirements for them.
Skills have been acquired in the use of standards and other regulatory materials.
Standards provide huge cost savings, interchangeability of general-purpose parts, assemblies and assemblies, reduce the range of cutting and measuring tools
Привод.cdw

дм деталировка.cdw

Лист №2(4).cdw

Редуктор Шляховский Ю.В..cdw

Similar materials
- 09.05.2024
- 15.02.2021
- 06.04.2022
- 04.11.2022
- 24.01.2023