Designing Metal Cutting Tool Designs



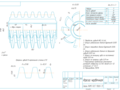
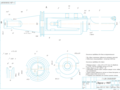
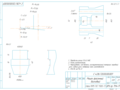
- Added: 12.05.2021
- Size: 548 KB
- Downloads: 0
Description
Design of worm cutter for cutting cylindrical wheels
Design of shaped disk cutter
Design of drill with mechanical attachment of MNP
Project's Content
![]() ![]() ![]() ![]() |
![]() ![]() ![]() ![]() |
![]() ![]() ![]() ![]() |
![]() ![]() ![]() |
![]() ![]() ![]() ![]() |
![]() ![]() ![]() |
Additional information
Contents
Contents
Introduction
1. Design of worm cutter for cutting cylindrical wheels
1.1 Initial data
1.2 Additional Process Data
1.3 Design calculation
1.4 Thermal treatment of tool material
1.5 Instrument material consumption
1.6 Technical Requirements for Fabrication and Inspection
2. Design of shaped disk cutter
2.1 Initial data
2.2 Determination of tool material consumption and cost
2.3 Heat Treatment
2.4 Technical requirements
3. Design of drill with mechanical attachment of MNP
3.1 Initial data
3.2 Design calculation
3.3 Economic cutting speed and tool life
3.4 Technical requirements
3.5 Calculation of tool unit for accuracy of positioning and compliance
List of literature used
Appendix A
Introduction
In modern mechanical engineering, cutting is the main technological method that ensures high quality and accuracy of machined surfaces of parts. The main areas of economic development are the widespread use of highly productive, flexible resource-saving technologies. The most important task is to accelerate scientific and technological progress through integrated mechanization and automation of production. The efficiency of mechanical engineering should be increased by changing the structure of the metalworking equipment fleet. This is achieved by increasing the specific weight of automated equipment, including automatic lines, CNC machines, robotic, microprocessor and computer-equipped flexible automated systems (GAC) and flexible production systems (GPS), which allow quick and efficient reconfiguration of production for the production of new products.
The effective operation of said equipment is impossible without the creation of perfect tooling, which has increased reliability, ensuring the economical, labor-saving use of progressive expensive equipment, which leads to the increasing role of the metal working tool. Therefore, specialists who have to work in metalworking industries should be able to competently design various types of tools.
Thus, the general line of development of mechanical engineering - comprehensive automation of design and production - requires knowledge and perfect knowledge of design methods that ensure the creation of highly efficient designs of cutting tools.
Design of worm cutter for cutting cylindrical wheels
Worm mills are used for rough and finishing of cylindrical gears of external engagement with straight, screw and chevron teeth, worm wheels and wheels of internal engagement. Worm cutters process wheels of 711th degree of accuracy. These cutters can operate with axial, radial and tangential feeds. According to the method of attachment, cutters are divided into nozzle and tail.
1.1 Initial data
Treated Material - 40X Steel.
Normal modulus - mn = 7.0 mm.
Number of wheel teeth - Zc = 56.
Angle of wheel teeth inclination - = 4˚.
The degree of accuracy of the wheel is 6.
Design of shaped disk cutter
Shaped cutters are used to treat surfaces of a complex profile on lathe machines and less often on strict or continuous machines in conditions of mass production and mass production. Typically, they are special tools designed to handle a single part. Shaped cutters ensure a strict identity of the processed parts, a large number of crossings, high general and dimensional resistance, combining preliminary and final processing, easy installation and adjustment on the machine, which makes them indispensable in automated production, especially on lathe machines. Shaped cutters are classified according to several features:
by machine type - lathe, automatic, strict, long;
according to the shape of the cutter body - round or disk, prismatic, rod. Screw cutters are less commonly used;
in terms of the surface to be treated - external, internal, end faces. The latter are external with the base turned through an angle of 90 °;
in the feed direction - with radial, axial and tangential feed (radial, end and tangential cutters, respectively
according to design, method of cutting part and housing connection, mat
cutting part rial: nozzle and tail (round); solid, welded, soldered; fast-cutting and hard-alloy.
2.3 Heat Treatment
Quenching is the main and most important operation of heat treatment of the tool, which determines to a large extent together with its subsequent release resistance during operation. Quenching shall provide high hardness, wear resistance, heat resistance and high mechanical strength of the tool. These requirements are met by the presence of martensite in tempered steel. Carbon steel martensite is a solid solution of carbon in αgland, which has low heat resistance.
The cutter is heated in a chlorobaric bath (BaC12).
The cutter is subjected to two heats:
- first heating to temperature of 800 - 840 ° С with exposure to 1 hour;
- second heating to the temperature of 1210 - 1235 ° С with isothermal holding of 1.52 minutes (6 - 7 s for each millimeter of the tool section).
Cooling is carried out in oil to a temperature of 300 ° C, then cooling is carried out with compressed air to avoid cracks in the martensitic conversion interval.
Structure of fast-cutting steel after hardening consists of martensite, residual austenite and carbides. The tempering of fast-cutting steel is necessary for the conversion of residual austenite, as well as for the tempering of primary and secondary martensite and the removal of internal stresses. Conversion of residual austenite into martensite in fast-cutting steel is achieved by prolonged tempering at temperature of 550 - 580 ° C for 3-4 hours.
Tempering is carried out in an electric-air furnace, with subsequent cleaning of the scale.
Technical requirements
Cutters made of quick-cutting steel according to GOST 19265 - 73 must have a hardness of HRC 59... 63;
Surface roughness parameters of cutters shall not be more than, μm:
a) the front surface of the cutting portion Ra 0.4;
and b ) the rear surface of the cutting portion Ra 3.2.
The cutters must be sharpened acutely. Rubble and crushed places on cutting edges are not allowed.
Cutters must be demagnetized.
Design of drill with mechanical attachment of MNP
Drills are one of the most widely used types of cutting tools, designed for drilling holes in solid metal, drilling, obtaining centering holes, divided into many varieties: centering, feather, spiral, for deep drilling, etc. The most common among them are spiral drills, which can be operated in a wide variety of conditions. Drills provide processing of holes according to 1112 accuracy and roughness Ra = 10... 3.2.
Drills with MNPs are widely used for processing short (up to 2d) holes on automated equipment. Such drills have high rigidity and can work not only as directly drills, but also stretch holes, mill bosses, trim ends.
Unlike a drill with two symmetrical and identical cutting edges, two or three different shape, asymmetrically arranged cutting inserts with chip-breaking grooves have two or three different shape depending on the diameter. One of the plates with an angle in plan close to 180, works at the periphery, the other at the center, and the third, for large diameters, fills the gap between them. Thus, the drill acts as a one-sided boring cutter with an intermittent cutting edge.
3.1 Initial data
Treated material - Cast iron KCh403.
The diameter of the hole Dot is 63H12.
Hole length - Lots = 80 mm.
The view of the hole is blind.
The shank is conical.
3.4 Technical requirements
Material of hard alloy plates VK8 GOST 388274, since hard steel is treated and large-section chips are removed, following the recommendation [4].
Hardness 8691 HRA.
The material of the drill body is 40X steel GOST 454371, since it is the most characteristic for metal cutting tool bodies, following the condition [7].
Hardness 44... 52 HRC.
Cutting edges run-out - 0.018 mm.
Drills with mechanical attachment of multifaceted replaceable plates shall be manufactured in accordance with the requirements of GOST 2772488.
Фреза.cdw

Сверло спец.spw

Сверло.cdw

Резец.cdw

Similar materials
- 17.03.2024