Проектирование конструкций металлорежущих инструментов



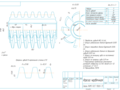
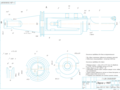
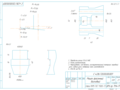
- Добавлен: 12.05.2021
- Размер: 548 KB
- Закачек: 0
Описание
Проектирование фрезы червячной для нарезания цилиндрических колес
Проектирование резца фасонного дискового
Проектирование сверла с механическим креплением МНП
Состав проекта
![]() ![]() ![]() ![]() |
![]() ![]() ![]() ![]() |
![]() ![]() ![]() ![]() |
![]() ![]() ![]() |
![]() ![]() ![]() ![]() |
![]() ![]() ![]() |
Дополнительная информация
Содержание
Содержание
Введение
1. Проектирование фрезы червячной для нарезания цилиндрических колес
1.1 Исходные данные
1.2 Дополнительные технологические данные
1.3 Проектный расчет
1.4 Термическая обработка инструментального материала
1.5 Расход инструментального материала
1.6 Технические требования на изготовление и контроль
2. Проектирование резца фасонного дискового
2.1 Исходные данные
2.2 Определение расхода инструментального материала и его стоимости
2.3 Термическая обработка
2.4 Технические требования
3. Проектирование сверла с механическим креплением МНП
3.1 Исходные данные
3.2 Проектный расчет
3.3 Экономическая скорость резания и срок службы инструмента
3.4 Технические требования
3.5 Расчет инструментального блока на точность позиционирования и податливость
Список использованной литературы
Приложение А
Введение
В современном машиностроении обработка резанием является главным технологическим методом, обеспечивающим высокое качество и точность обрабатываемых поверхностей деталей. Основными направлениями экономического развития является широкое применение высоко производящих, гибких ресурсосберегающих технологий. Важнейшей задачей является ускорение научно-технического прогресса путем комплексной механизации и автоматизации производства. Эффективность машиностроения должна повышаться за счет изменения структуры парка металлообрабатывающего оборудования. Это достигается путем увеличения удельного веса автоматизированного оборудования, в том числе автоматических линий, станков с ЧПУ, роботизированных, оснащенных микропроцессорной и вычислительной техникой гибких автоматизированных комплексов (ГАК) и гибких производственных систем (ГПС), позволяющих быстро и эффективно перестраивать производство на выпуск новых изделий.
Эффективная эксплуатация указанного оборудования невозможна без создания совершенной инструментальной оснастки, обладающей повышенной надежностью, обеспечивающей экономичное, трудосберегающее использование прогрессивной дорогостоящей техники, что обуславливает все более возрастающую роль металлообрабатывающего инструмента. Поэтому специалисты, которым предстоит работать в металлообрабатывающих отраслях промышленности, должны уметь грамотно проектировать различные виды инструментов.
Таким образом, генеральная линия развития машиностроения – комплексная автоматизация проектирования и производства – требует знания и совершенного владения методами проектирования, обеспечивающими создание высокоэффективных конструкций режущих инструментов.
Проектирование фрезы червячной для нарезания цилиндрических колес
Червячные фрезы применяют для черновой и чистовой обработки цилиндрических зубчатых колес наружного зацепления с прямым, винтовым и шевронным зубьями, червячных колес и колес внутреннего зацепления. Червячными фрезами обрабатывают колеса 711й степеней точности. Эти фрезы могут работать с осевой, радиальной и тангенциальной подачами. По способу крепления фрезы делятся на насадные и хвостовые.
1.1 Исходные данные
Обрабатываемый материал – Сталь 40Х.
Модуль нормальный – mn = 7,0 мм.
Число зубьев колеса – Zк=56.
Угол наклона зубьев колеса – = 4˚.
Степень точности колеса – 6.
Проектирование резца фасонного дискового
Фасонные резцы применяются для обработки поверхностей сложного профиля на станках токарной группы и реже на строгальных или долбежных станках в условиях серийного и массового производства. Как правило, они являются специальными инструментами, предназначенными для обработки одной детали. Фасонные резцы обеспечивают строгую идентичность обработанных деталей, большое количество переточек, высокие общую и размерную стойкость, совмещение предварительной и окончательной обработки, простоту установки и наладки на станке, что делает их незаменимыми в автоматизированном производстве, особенно на токарных автоматах. Фасонные резцы классифицируют по нескольким признакам:
по типу станка — токарные, автоматные, строгальные, долбежные;
по форме тела резца — круглые или дисковые, призматические, стержневые. Реже применяются винтовые резцы;
по виду обрабатываемой поверхности — наружные, внутренние, торцовые. Последние представляют собой наружные с базой, развернутой на угол 90°;
по направлению подачи — с радиальной, осевой и тангенциальной подачей (соответственно радиальные, торцовые и тангенциальные резцы
по конструкции, способу соединения режущей части и корпуса, мате
риалу режущей части: насадные и хвостовые (круглые); цельные, сварные, паяные; быстрорежущие и твердосплавные.
2.3 Термическая обработка
Закалка является основной и важнейшей операцией термической обработки инструмента, определяющей в значительной мере вместе с последующим отпуском его стойкость в процессе эксплуатации. Закалка должна обеспечивать высокую твердость, износоустойчивость, теплостойкость и высокую механическую прочность инструмента. Этим требованиям удовлетворяет наличие мартенсита в закаленной стали. Мартенсит углеродистой стали представляет собой твердый раствор углерода в αжелезе, который обладает низкой теплостойкостью.
Нагрев фрезы проводим в хлоробаривой ванне (ВаС12).
Фрезу подвергаем двум подогревам:
– первый подогрев до температуры 800 - 840 °С с выдержкой 1 час;
– второй подогрев до температуры 1210 - 1235 °С с изотермической выдержкой 1,52 минуты (6 - 7 с на каждый миллиметр сечения инструмента).
Охлаждение производится в масле до температуры 300 °С , далее охлаждение ведется сжатым воздухом для избежание появления трещин в интервале мартенситного превращения.
Структура быстрорежущей стали после закалки, состоит из мартенсита, остаточного аустенита и карбидов. Отпуск быстрорежущей стали необходим для превращения остаточного аустенита, а также для отпуска первичного и вторичного мартенсита и снятия при этом внутренних напряжений. Превращение остаточного аустенита в мартенсите в быстрорежущей стали достигается длительным отпуском при температуре 550 - 580 °С в течение 3-4 часов.
Отпуск производим в электровоздушной печи, с последующей очисткой окалины.
Технические требования
Резцы изготавливаемые из быстрорежущей стали по ГОСТ 19265—73 должны иметь твердость HRC 59...63;
Параметры шероховатости поверхностей резцов не должны быть более ,мкм:
а) передней поверхности режущей части Ra 0,4;
б) задней поверхности режущей части Ra 3,2.
Резцы должны быть остро заточены. Завалы и выкрошенные места на режущих кромках не допускаются.
Резцы должны быть размагничены.
Проектирование сверла с механическим креплением МНП
Сверла – один из наиболее широко используемых типов режущих инструментов, предназначенный для сверления отверстий в сплошном металле, рассверливания, получения центровочных отверстий, подразделяющийся на множество разновидностей: центровочные, перовые, спиральные, для глубокого сверления и др. Наиболее распространены среди них спиральные сверла, которые можно эксплуатировать в самых разнообразных условиях. Сверла обеспечивают обработку отверстий по 1112 квалитетам точности и шероховатость Ra=10...3,2.
Для обработки коротких (до 2d) отверстий на автоматизированном оборудовании широко используются сверла с МНП. Такие сверла обладают высокой жесткостью и могут работать не только как непосредственно сверла, но и растачивать отверстия, фрезеровать бобышки, подрезать торцы.
В отличие от сверла с двумя симметричными и идентичными режущими кромками сверла с МНП в зависимости от диаметра имеют две или три отличающиеся по форме, несимметрично расположенные режущие пластины со стружкодробящими канавками. Одна из пластин с углом в плане близким к 180, работает у периферии, другая – у центра, а третья, для больших диаметров, заполняет промежуток между ними. Таким образом, сверло работает как односторонний расточной резец с прерывистой режущей кромкой.
3.1 Исходные данные
Обрабатываемый материал – Чугун КЧ403.
Диаметр отверстия Dотв – 63H12.
Длина отверстия – Lотв=80 мм.
Вид отверстия – глухое.
Хвостовик – конический.
3.4 Технические требования
Материал твердосплавных пластин ВК8 ГОСТ 388274, так как обрабатывается твердая сталь и снимается стружка большого сечения, следуя рекомендации [4].
Твердость 8691 HRA.
Материал тела сверла сталь 40Х ГОСТ 454371, так как является наиболее характерной для корпусов металлорежущих инструментов, следуя условию [7].
Твердость 44…52 HRC.
Биение режущих кромок – 0,018 мм.
Сверла с механическим креплением многогранных сменных пластин должны изготовляться в соответствии с требованиями ГОСТ 2772488.
Фреза.cdw

Допуск радиального биения буртиков 0
Допуск торцевого биения буртиков 0.004
Допуск радиального биения по вершинам
Допуск на толщину зуба по постоянной
Допуск на профиль зуба 0
Неуказанные предельные отклонения
размеров: отверстий по Н12
Сталь Р6М5 ГОСТ 19265-73
Профиль зубьев в нормальном сечении (2:1)
Класс точности фрезы
Направление витков фрезы
Направление струж. канавок
Шаг зубьев в нормальном сечении
Сверло спец.spw

Хвостовик конический
Шпонка ГОСТ 23360-78
Сверло.cdw

При сборке сопрягаемые поверхности протереть керосином.
Обеспечить позиционирование с точностью 0
Технические требования для сверла.
Материал корпуса - сталь 40Х по ГОСТ 4543-71
в местах установки пластин 50 55 HRC.
Общие допуски по ГОСТ 30893.2 - mK.
Маркировать: диаметр сверла
материал режущей части
Нижнее опорные поверхности пластин не должны выступать за
пределы корпуса более чем на 0.2 мм.
*Смещение осей необходимо для плотного прижима платины.
Сталь Р6М5 ГОСТ 19265-73
Резец.cdw

инструментальный материал
товарный знак изготовителя.
Сталь Р6М5 ГОСТ 19265-73