Проектирование конструкции металлорежущих инструментов



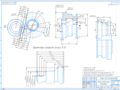
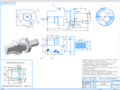
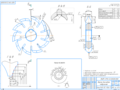
- Добавлен: 15.11.2022
- Размер: 946 KB
- Закачек: 0
Описание
Курсовой проект по режущим инструментам. Представляет собой записку из расчетов размеров и режимов резания и чертежей этих инструментов. Включает 3 чертежа и записку.
Состав проекта
![]() ![]() ![]() |
![]() ![]() ![]() ![]() |
![]() ![]() ![]() ![]() |
![]() |
Дополнительная информация
rezh_instr_KR (3),.docx
2 Дополнительные технологические (конструктивные) данные5
3 Определение параметров нарезаемого колеса5
4 Расчет координат профиля эвольвентного участка зуба5
4 Технические требования7
Проектирование резца фасонного дискового8
3 Коррекционный расчет профиля резца9
Проектирование зенкера11
2 Проектный расчет12
3 Определение геометрических и конструктивных параметров режущей части.13
4 Технические требования на изготовление зенкера13
5 Расчет инструментального блока на точность позиционирования и податливость14
6 Расчет инструментального блока на податливость15
7 Термическая обработка корпуса зенкера16
Проектирование комбинированного инструмента17
2 Проектирование и расчет сверла17
3 Проектирование и расчет зенковки20
4 Проектирование и расчет развертки21
Режущий инструмент является основным исполнительным органом станка без которого невозможно полностью реализовать заложенные в станках технологические возможности. Таким образом режущий инструмент – это главный элемент обрабатывающей системы непосредственно связанный с заготовкой либо деталью и в результате чего изменяется ее размер форма либо свойства.
Режущий инструмент – это геометрическое тело обладающее соответствующими конструктивными и геометрическими параметрами которые непосредственно изменяют форму обрабатывающей детали. По типу режущий инструмент классифицируется следующим образом: резцы общего назначения; сверла чаще двухлезвийные; зенкеры; развертки; напильники; протяжки и прошивки; фрезы; метчики.
Расчет и проектирование фрезы дисковой модульной
Обрабатываемый материал – Сталь 12 модуль нормальный mn = 575; угол профиля ; число зубьев колеса ; степень точности колеса – 10.
2 Дополнительные технологические (конструктивные) данные
Для проектирования фрезы дисковой модульной применяем сталь Р6М5 ГОСТ 19265 – 73.
3 Определение параметров нарезаемого колеса
Для определения параметров фрезы необходимо произвести расчет нарезного колеса в частности определить его диаметры.
Диаметр делительной окружности колеса определяется по формуле:
Диаметр вершины колеса определяется по формуле:
Диаметр основной окружности впадин колеса определяется по формуле:
4 Расчет координат профиля эвольвентного участка зуба
Угол давления в любой точке X профиля определяем по формуле:
Половину угловой ширины впадины на основной окружности определяем по формуле:
- гарантированный боковой зазор в передаче
Половину угловой ширины впадины на окружностях радиуса rx определяем по формуле:
Координаты точек X профиля определяем по формуле:
Для построения эвольвенты определяем координаты точек :
Максимальная ширина профиля впадины зуба определяется по формуле:
Высота профиля фрезы определяем по формуле:
Диаметр фрезы определяем по формуле:
По ГОСТ 10996-64 принимаем диаметр фрезы z = 10 j = 5
Величину затылования определяем по формуле:
ko =15·k=15·75=1125мм (1.36)
Рассчитаем расход материала:
4 Технические требования
Проектируемую дисковую модульную фрезу изготавливают из стали 25Н ГОСТ 19265-73 твердостью 63 65 HRC.
На всех поверхностях фрезы не должно быть трещин выкрошенных мест заусенцев и следов коррозии. Отклонение от радиальной передней поверхности - . Допуск радиального биения по наружному диаметру относительно оси отверстия – 0.04 мм. Допуск торцевого биения в точках наиболее удаленного от оси отверстия фрезы (торцовые плоскости должны быть взаимно параллельны и перпендикулярны к оси отверстия фрезы) – 0.04 мм. Допуск биения боковых режущих кромок зубьев в направлении нормали к профилю – 0.08 мм. Погрешность профиля на участке эвольвенты – 0.063 мм. Погрешность профиля на вершине зуба и на закруглениях – 0.125 мм.
Проектирование резца фасонного дискового
Фасонные резцы применяют для обработки деталей с различной формой образующей. По сравнению с обычными резцами они обеспечивают идентичность формы точность размеров детали которая зависит в основном от точности изготовления резца высокую производительность благодаря одновременной обработке всех участков фасонного профиля детали и большую экономию машинного времени. Резцы удобны в эксплуатации благодаря простоте переточки по передней поверхности.
Фасонные резцы используют на токарных револьверных станках автоматах и полуавтоматах. Резцы проектируют для обработки конкретной детали и их применение экономически оправдано при крупносерийном и массовом производстве.
Круглые фасонные резцы применяют для обработки как наружных так и внутренних поверхностей. Они более технологичны чем призматические так как представляют собой тела вращения и допускают большее число переточек и стачиваются до остаточной по условию прочности величины.
Задние углы у круглых резцов получают установкой их оси выше осевой плоскости заготовки в специальных резцедержателях.
Исходные данные заносим в таблицу 2.1
Таблица 2.1 – исходные данные
Обрабатываемый материал
Рисунок 2.1 – Эскиз заготовки
Определяем передний и задний углы по табл.3.32 [1] исходя из обрабатываемого материала: γ = 12° α = 10°.
Определяем габаритные и присоединительные размеры резца.
Наибольшая глубина профиля детали:
Габаритный радиус определяется по формуле:
где е – глубина заточки по передней поверхности необходимая для размещения стружки выбирается из таб. 3.33 [1] е = 4 мм
k – толщина тела резца необходимая для обеспечения его прочности k = 9 мм стр. 205 [3]
- диаметр посадочного отверстия выбирается из табл. 3.33 [1]
Наибольший диаметр резца принимаем исходя из стр. 206 [1].
Размеры рифлений выбираем исходя из табл. 3.34 [1]: r = 2 мм d1 = 32 мм l1 = 16 мм.
Определяем дополнительные конструктивные размеры резца:
Высота установки резца:
Высота заточки резца:
Разбиваем профиль детали на условные точки и покажем их радиусы (рис.2.3)
Рисунок 2.2 – Профиль детали
3 Коррекционный расчет профиля резца
Исходя из условия получим значения радиусов:
Численные значения параметров
Построение шаблона и контршаблона для контроля фасонного профиля сводится для круглых резцов к определению разности радиусов всех узловых точек рассчитанного фасонного профиля относительно узловой контурной точки:
Проектирование зенкера
Зенкеры в отличие от сверл имеют большее количество режущих зубьев и направляющих ленточек (обычно 3-4) обладают большей жесткостью и не имеют перемычки что позволяет уменьшить разбивку обработанного отверстия и угол наклона оси. Различают хвостовые и насадные цельные и сборные зенкеры.
Последовательность проектирования зенкеров и сверл в целом аналогична.
Стандартные зенкеры изготавливают в двух исполнениях: зенкер №1 – для промежуточной обработки отверстий под последующее развертывание и зенкер; №2 – для окончательной обработки отверстий. В обоих случаях допуск на диаметр зенкера рассчитывают из условия обработки отверстия по 11-му квалитету.
Исходные данные заносим в таблицу 3.1
Таблица 3.1 – исходные данные
Диаметр отверстия мм
Схема расчета полей допусков и диаметров зенкера и отверстия
Рис.3.1 Поля допусков и диаметров зенкера и отверстия
Pmax = 025 022 = 0055 (3.1)
d3max = Dmax – Pmax = 9022 – 0055 = 90165 мм (3.2)
IT3 = 03 IT = 03 022 = 0066 (3.3)
D3min = Dmax – IT3 = 9022 – 0066 = 90154 мм (3.4)
Выбор числа зубьев: по рекомендации стр. 118 [2] принимаем количество 4 ножа.
Выбор материала режущей части и корпуса зенкера: в зависимости от обрабатываемого материала выбираем ножи для зенкера из быстрорежущей стали. По ГОСТу 16858-71 выбираем нож 0-44-16. Для корпуса зенкера принимаем Сталь 40Х.
Для крепления ножей на корпусе делают косые пазы наклоненные к оси под углом =10 (по рекомендации стр.120 [2]). Ножи имеют клиновидную форму с углом клина 5 их крепят в корпусе при помощи клина.
3 Определение геометрических и конструктивных параметров режущей
Определение углов заточки:
по рекомендации стр. 45 [3] главный задний угол . Главный угол в плане Передний угол .
По рекомендации стр. 45 [3] находим ширину цилиндрической ленточки по следующей формуле:
f = 003 D = 003 90 = 27 мм (3.5)
где D – диаметр зенкера.
Все виды насадных зенкеров имеют обратную конусность 004-01 мм на длине зуба. Обратную конусность по длине ножа принимаем равным 005 мм.
Расстояние от оси зенкера до дна паза под нож:
H = r – в + p = 45 – 8 – 01 = 369 мм (3.6)
- припуск на полирование
Размеры профиля винтовых канавок:
h = (025 01) D = 01 90 = 9 мм (3.7)
Для крепления насадного зенкера в хвостовике инструмента выбираем для него оправку по ГОСТ 13044-85.
Цилиндрический хвостовик оправки выбираем в соответствии с ГОСТ 26540-85.
Хвостовик инструмента конусностью 7:24 выбираем по ГОСТ 25827-83.
4 Технические требования на изготовление зенкера
Материал корпуса зенкера – сталь 40Х. Твёрдость 61-63 HRC.
Ножи из быстрорежущей стали по ГОСТ 16858-71.
Маркировать: диаметр номер зенкера по точности материал режущей части товарный знак завода изготовителя.
5 Расчет инструментального блока на точность позиционирования и податливость
Согласно схеме сборки можно выделить следующие составляющие погрешности:
Биение конического отверстия шпинделя станка:
Допускаемый перекос:
Биение базового агрегата от перехода в соединении конусности 7:24
Биение оправки от зазора в цилиндрическом соединении:
Биение посадочного отверстия базисного агрегата относительно конуса
Биение оправки от перекоса в цилиндрическом соединении:
Биение цилиндрической поверхности:
Биение конической поверхности конусности 1:30 относительно наружной цилиндрической поверхности:
Величина первичного отклонения вершины инструмента от номинального положения
где - передаточное отношение
- коэффициент относительного рассеивания
- перенос или параллельное смещение оси;
- вылет на котором нормируется величина перекоса;
- коэффициент относительного рассеивания замыкающего звена ;
Коэффициент рассеивания :
для цилиндрических поверхностей -;
для конической поверхности 1:30 - ;
Передаточные отношения:
Допускаемое биение зенкера диаметром 90 мм – 0071 мм по стр.37 [4]
6 Расчет инструментального блока на податливость
Согласно схеме сборки перемещения крепления оправки определим как суммарное смещение режущей кромки в точке приложения нагружающей силы (P = 1 kH) с учетом контактной податливости в соединениях инструмента:
где - длинна i - го элемента вспомогательного инструмента
- осевой момент инерции сечения i - го элемента
- модуль продольной упругости ()
- податливость i - го элемента
- диаметр i - го элемента
- податливость в конусе с конусностью 7:24
- податливость в цилиндрическом соединении с боковым зажимным винтом
- податливость в конусе 1:30 = 00014
Жесткость инструментального блока:
Податливость инструментального блока:
Для зенкеров-разверток диаметром до 90 мм допускается податливость 0115 = 115 .
7 Термическая обработка корпуса зенкера
По рекомендации стр. 126 [5] для корпуса зенкера-развертки изготовленного из стали 40Х выполнить:
При нагреве под закалку предварительно нагреть до температуры 300 – 500 ºС.
Нагрев под закалку – в расплаве солей пр.
Закалка: основная производится в закалочной среде
заменяющая закалка производится в закалочной среде
Отпуск закаленного инструмента производится в жидкой среде или воздушной среде.
Проектирование комбинированного инструмента
Рисунок 4.1 Эскиз детали № 6
Материал – Сталь 20.
2 Проектирование и расчет сверла
Для экономии быстрорежущей стали все сверла с цилиндрическим хвостовиком диаметром более 8 мм и сверла с коническим хвостовиком более 6 мм изготовляются сварными.
В основном сверла делают из быстрорежущих сталей. Твердосплавные сверла делают для обработки конструкционных сталей высокой твердости (45 56HRC) обработке чугуна и пластмасс. Исходя из твердости обрабатываемого материала – 207 НВ принимаем решение об изготовлении сверла из быстрорежущей стали Р6М5 ГОСТ 19265-73.
Величина заднего угла на сверле зависит от положения рассматриваемой точки режущего лезвия. Задний угол имеет наибольшую величину у сердцевины сверла и наименьшую - на наружном диаметре. Рекомендуемые величины заднего угла на наружном диаметре приведены в [4 табл.44] a.= 8°.
Передний угол также является величиной переменной вдоль режущего лезвия и зависит кроме того от угла наклона винтовых канавок w и угла при вершине 2j. Передняя поверхность на сверле не затачивается и величина переднего угла на чертеже не проставляется.
Угол при вершине сверла. Значение углов 2 φ для свёрл используемых для различных обрабатываемых материалов приведены в [4 стр.152 табл.46]. По этим рекомендациям принимаем: 2 φ = 119°.
Угол наклона винтовых канавок. Угол наклона винтовых канавок определяет жесткость сверла величину переднего угла свободу выхода стружки и др. Он выбирается в зависимости от обрабатываемого материала и диаметра сверла. По (6 табл.5) назначаем = 30°.
Угол наклона поперечной кромки. При одном и том же угле φ определенному положению задних поверхностей соответствует вполне определенная величина угла y и длина поперечной кромки и поэтому угол y служит до известной степени критерием правильности заточки сверла. По рекомендациям [4 табл.46] назначаем: = 55°.
Расчет назначение конструктивных размеров сверла.
Длина сверла характеризуется его серией. В связи с тем что длина рабочей части сверла определяет его стойкость жесткость прочность и виброустойчивость желательно во всех случаях выбирать сверло минимальной длины. Серия сверла должна быть выбрана таким образом чтобы
Расчетная длина рабочей части сверла lо равна расстоянию от вершины сверла до конца стружечной канавки может быть определена по формуле:
lо = lр + lвых + lд + lв + lк + lф (4.1)
lф - величина характеризующая уменьшение глубины канавки полученной при работе канавочной фрезы
lк + lф = 15·dсв = 15·20 = 30 мм (4.2)
l0 = 6 + 3 +12 + 30 = 51 мм. (4.3)
Определение количества переточек.
Общая длина стачивания:
lо = lk - lвых - Δ - lр (4.4)
lо = 30-12-6=12 мм. (4.5)
Число переточек: n = loDl = 1206 = 20 переточки.
Dl – величина стачивания за одну переточку.
Выбор числа зубьев: по рекомендации стр. 435 [4] принимаем Z=4.
Выбор материала режущей части и корпуса зенкера: по рекомендации стр. 116 [7] для зенкеров предназначенных для обработки Сталь 20 применяют быстрорежущую сталь Р6М5 ГОСТ 19265-73. Для корпуса зенкера принимаем Сталь 45 ГОСТ 1050-2013.
Определение геометрических и конструктивных параметров режущей части Определение углов заточки:
по рекомендации стр. 437 [4] главный задний угол 8° на толщине пластины по торцевой заточке - 1 12°. Главный угол в плане 60°(т.к. отверстие сквозное). Передний угол 6 10°. Угол наклона главной режущей кромки 10°.
Ширина ленточки f 08.
Для выхода стружки зенкер необходимо снабдить винтовыми канавками с углом наклона 10° по пластине и 15° за пластиной. Шаг винтовой канавки:
H D ctg 314 28 ctg10 4747 мм (4.6)
Угол врезания пластины
tg tg 2 cos 1 0995 0105 01045 5967(4.7)
где 1 - передний угол лежащий в сечении перпендикулярном оси зенкера
cos 1 cos cos 6° 0995
- передний угол лежащий в сечении параллельном оси зенкера
tg 2 tg sin tg cos tg tg6° 1105 (4.8)
Расстояние от оси зенкера до дна паза под пластину:
где в - ширина пластины
p 01 02 мм - припуск на полирование
Так как толщина пластины должна быть больше
a r sin 1 05 tg 21sin 6 05 tg5967 197(4.10)
то принимаем пластинку 21290 ГОСТ 25400-92 ( 27 мм s 2 мм в 5 мм )
h (025 01) D0 01 38 38 мм(4.19)
f (001 003) D0 002 38 076 мм(4.20)
fk (01 002) D0 00375 38 1425 мм(4.21)
3 Проектирование и расчет зенковки
Одной из разновидностей операции зенкерования является операция образования цилиндрических ступенчатых конических и торцевых поверхностей выполняемых специальным осевым инструментом – зенковками.
Зенковка коническая предназначена для изготовления фаски 22х40° в отверстии.
Обоснование выбора геометрических параметров зенковки:
Геометрические параметры режущей части заданы в сечении перпендикулярном режущей кромке величиною заднего угла α шириной фаски f и углом заострения зуба . По рекомендациям [8 стр.30] выбираем:
α = 12°; f = 1.2; = 40°.
Исходя из назначения зенковки угол при вершине 2φ = 80°.
Число зубьев зенковки [8 стр.22] z = 8.
Принимаем зенковку типа № 9 ГОСТ 14253-80 с углом при вершине 80°.
При обработке сталей экономически выгодно использовать зенковки из быстрорежущей стали Р6М5 ГОСТ 19256-73. [4 таб.2]
Изготовление хвостовика для сверла-зенковки:
Для экономии быстрорежущей стали сверло-зенковку сделаем составным неразъемным сваренным с помощью контактной сварки оплавлением. Хвостовик изготавливают из стали 40Х ГОСТ454-74.
Хвостовик выполнен в форме конуса Морзе №3 [8 Табл.5] его размер выбирается по АТ8 ГОСТ 2848-75.
Допуск на изготовление конических базовых поверхностей сверла- зенковки выбираются по ГОСТ 2848-75.
4 Проектирование и расчет развертки
Исполнительный диаметр развертки D устанавливается в зависимости от диаметра обрабатываемого отверстия D0 допуска на изготовление отверстия величины разбивки отверстия Pmax .
Наибольший исполнительный диаметр развертки:
D D0 Pmax 38 0021 0014 38007мм(4.22)
=0021 мм; Pmax=0014 мм (по табл. 41 [1])
Диаметр заборной части определяется по формуле:
Dz D 1.3 1.4 2t 38007 13 2 09 35667мм(4.23)
где tприпуск под развертывание на сторону t=09 мм
На переднем торце развертки снимается направляющая фаска под углом 45° предохраняющая развертку от повреждения.
Величина угла при вершине непосредственно влияет на стойкость развертки чистоту обрабатываемой поверхности и усилие нужное для развертывания примем 15°.
Длина заборной части:
Число зубьев развертки:
Z 15 √D0 4 15 √38 4 15(4.25)
Задний угол на заборной и калибровочной части примем равным 6
Длина рабочей части развертки:
Lp 06 08D0 07 38 266мм(4.26)
Длина цилиндрической части развертки в месте с заборным конусом:
Lцил 05 07D0 06 38 228мм(4.27)
Общая длина развертки:
Lo Lp Lh 266 10 366мм(4.28)
где Lhдлина шейки развертки Lh=812 мм
Ширину ленточки на режущих кромках калибрующей части назначим по табл. 42
Для получения высокого класса чистоты поверхности обработанного отверстия угловой шаг развертки зубьев делается не равномерным. Неравномерное распределение шага возьмём из таблицы 43 [1]:
По табл. 23 [1] выбираем размеры элементов профиля канавок:
длина задней грани 18 мм
В ходе выполнения курсового проекта были приобретены навыки самостоятельной работы навыки работы со справочными материалами и стандартами. Так же приобретены общие представления о развитии технологии производства металлорежущих инструментов и их возможностях.
В курсовом проекте были рассчитаны следующие инструменты:
- Фреза дисковая модульная;
- Резец фасонный дисковый;
- Зенкер насадной сборный.
Были разработаны их рабочие чертежи приведенные в приложении с указанием предельных отклонений размеров деталей и шероховатостей на поверхности инструмента.
Режущий инструмент. Курсовое и дипломное проектирование. Учебное пособие. Под ред. Е. Э. Фельдштейна-Мн.: ДизайнПРО 1997.-384 с:
Сахаров Г.Н. Металлорежущие инструменты - М: Машиностроение 1989. – 328 с.
Иноземцев Г.Г. Проектирование металлорежущих инструментов – М: Машиностроение 1984. – 272 с.
Кирсанов Г.Н. Руководство по курсовому проектированию металлорежущих инструментов – М.: Машиностроение 1986. – 288с.
Кузнецов Ю.И. Оснастка для станков с ЧПУ. Справочник . – М: Машиностроение 1990. – 510 с.
Оснастка для станков с ЧПУ: Справочник. - 2-е изд. перераб. и доп. М.
«Машиностроение» 1990 -512
Общемашиностроительные нормативы режимы резания для техническо- го нормирования работ на металлорежущих станках. Часть1. Издание 2-е. М. «Машиностроение» 1974 416 с.
Прогрессивные режущие инструменты и режимы резания металлов: Справочник В. И. Баранчиков А. В. Жаринов. Н. Д. Юдина А. И. Садыхов.; Под общ. ред. В. И. Баранчикова. -М.: Машиностроение 1990. - 400 с
Фреза дисковая модульная
Зенкер насадной сборный
Freza Disk. Mod. 1 KR.cdw

марка инструментального
товарный знак изготовителя.
Радиальное биение вершин зубьев
Коэффициент замещения
Число зубьев нарезаемого кодеса
Сталь Р6М5 ГОСТ 19265-73
disk. rezets KR.cdw

Неуказанные предельные отклонения размеров
Маркировать: код детали
инструментальный материал
высоту установки резца
товарный знак изготовителя.
Сталь Р6М5К5 ГОСТ 19265-73
Параметры профиля резца (4:1)