Проектирование конструкций металлорежущих инструментов




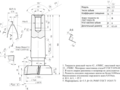
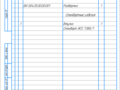
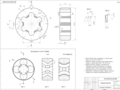
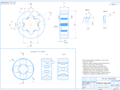
- Добавлен: 24.01.2023
- Размер: 1 MB
- Закачек: 0
Описание
Проектирование конструкций металлорежущих инструментов
Состав проекта
![]() |
![]() |
![]() ![]() ![]() ![]() |
![]() |
![]() ![]() |
![]() |
![]() ![]() ![]() |
![]() ![]() ![]() ![]() |
![]() ![]() ![]() ![]() |
![]() ![]() ![]() ![]() |
![]() |
![]() |
![]() ![]() ![]() ![]() |
![]() |
![]() |
![]() ![]() ![]() ![]() |
![]() ![]() ![]() ![]() |
![]() ![]() ![]() ![]() |
![]() |
![]() ![]() ![]() |
![]() ![]() ![]() ![]() |
![]() ![]() ![]() ![]() |
![]() |
![]() |
![]() ![]() ![]() ![]() |
![]() ![]() ![]() ![]() |
![]() |
![]() ![]() ![]() |
![]() ![]() ![]() ![]() |
![]() ![]() ![]() ![]() |
![]() ![]() ![]() ![]() |
![]() ![]() ![]() ![]() |
![]() |
![]() |
![]() |
![]() |
![]() ![]() ![]() |
Дополнительная информация
Чертеж развертка.cdw

Развертки должны удовлетворять техническим требованиям
Заточка режущей части производится алмазными кругами АС01061
доводка-алмазными кругами АСМ3Б1 или пастами АП28 АП17.
Обратная конусность по наружному диаметру развертки 0
Маркировать: диаметр развертки
режущей части и товарный знак завода-изготовителя
Белорусско-Российский университет
Титульник.doc
Министерство образования и науки Российской Федерации
Учреждение высшего профессионального образования
БЕЛОРУССКО-РОССИЙСКИЙ УНИВЕРСИТЕТ
по дисциплине «Режущий инструмент»
на тему: «Проектирование конструкций металлорежущих инструментов»
Пояснительная записка 31411.00.00.000 ПЗ
Чертеж развертка модифмкация.cdw

Развертки должны удовлетворять техническим требованиям
Заточка режущей части производится алмазными кругами АС01061
доводка-алмазными кругами АСМ3Б1 или пастами АП28 АП17.
Обратная конусность по наружному диаметру развертки 0
Маркировать: диаметр развертки
режущей части и товарный знак завода-изготовителя
Блок инструментальный
Белорусско-Российский университет
Чертеж долбяк окончательно.cdw

хвостовой части 32 35HRC.
Материал хвостовика сталь45 ГОСТ1050-88
В месте сварки раковины и непровар не допускаются
Разность соседних окружных шагов не более 0
Накопленное отклонение окружного шага 0
Маркировать: m=3.5; b=10; Р6М5 ГОСТ 19265-73
Толщина зуба по делительной
Белорусско-Российский университет
Коэффициент смещения
Чертеж плашка.cdw

Твердость зубьев у режущих кромок должна быть у
плашек из стали марки 9ХС HRC 58 62
Радиальное биение наружной цилиндрической
поверхности плашек относительно оси резьбы и
торцевое биение плашек относительно наиболее
удоленной точки от оси для диаметра >26-0.1мм
Маркировать: обозначение резьбы
товарный знак завода изготовителя(М33х2-Н8- )
Сталь9ХС ГОСТ5950-73
Белорусско-Российский университет
Исполнение 2 по АС 1106601
Чертеж развертка.cdw

Развертки должны удовлетворять техническим требованиям
Заточка режущей части производится алмазными кругами АС01061
доводка-алмазными кругами АСМ3Б1 или пастами АП28 АП17.
Обратная конусность по наружному диаметру развертки 0
Маркировать: диаметр развертки
режущей части и товарный знак завода-изготовителя
Блок инструментальный
Чертеж развертка модифмкация.cdw

Развертки должны удовлетворять техническим требованиям
Заточка режущей части производится алмазными кругами АС01061
доводка-алмазными кругами АСМ3Б1 или пастами АП28 АП17.
Обратная конусность по наружному диаметру развертки 0
Маркировать: диаметр развертки
режущей части и товарный знак завода-изготовителя
Блок инструментальный
Чертеж долбяк окончательно.cdw

хвостовой части 32 35HRC.
Материал хвостовика сталь45 ГОСТ1050-88
В месте сварки раковины и непровар не допускаются
Разность соседних окружных шагов не более 0
Накопленное отклонение окружного шага 0
Маркировать: m=3.5; b=10; Р6М5 ГОСТ 19265-73
Толщина зуба по делительной
Коэффициент смещения
Чертеж плашка.cdw

Твердость зубьев у режущих кромок должна быть у
плашек из стали марки 9ХС HRC 58 62
Радиальное биение наружной цилиндрической
поверхности плашек относительно оси резьбы и
торцевое биение плашек относительно наиболее
удоленной точки от оси для диаметра >26-0.1мм
Маркировать: обозначение резьбы
товарный знак завода изготовителя(М33х2-Н8- )
Сталь9ХС ГОСТ5950-73
Исполнение 2 по АС 1106601
Моя записка.doc
Министерство образования и науки Российской Федерации
БЕЛОРУССКО-РОССИЙСКИЙ УНИВЕРСИТЕТ
Кафедра «Металлорежущие станки и инструмент»
По дисциплине: «Металлорежущий инструмент»
на тему: «Проектирование режущего инструмента»
Руководитель проекта:
Проектирование долбяка хвостового
1 Введение к инструменту
2 Проектный расчет .
3 Проверочный расчет .
4 Технические требования на изготовление долбяка хвостового
5 Термическая обработка инструментального материала
Проектирование плашки круглой
2 Проектный расчет ..
4 Технические требования на изготовление плашки круглой .
Проектирование развертки хвостовой
3 Технические требования на изготовление развертки хвостовой ..
4 Термическая обработка инструментального материала
развертки хвостовой .
5 Расчет инструментального блока на точность позиционирования
6 Схема сборки инструментального блока .
Раздел стандартизации .
Список использованной литературы ..
Курсовой проект предусматривает конструирование следующих типов ме-
таллорежущих инструментов: долбяк хвостовой плашка круглая и развертка
хвостовая (блочного исполнения).
Зуборезные долбяки применяют для нарезания зубчатых колес. Они рабо-
тают по методу обкатки. В зависимости от характера обрабатываемых деталей
долбяки бывают: прямозубые косозубые и специальные.
По точности долбяки бывают классов АА А и В. Для обеспечения резания
долбяку придают измененный вид по сравнению с обычным зубчатым колесом.
По конструкции долбяки классифицируются на: дисковые чашечные вту-
лочные сборные хвостовые и комбинированные.
Для нарезания наружных резьб диаметром от 1 до 52 мм(иногда до 135мм)
предназначены плашки круглые.
По форме плашки подразделяются на трубчатые круглые квадратные и
другие. Основные размеры плашек стандартизованы.
Конструктивные элементы плашек следующие: корпус со стружечными от-
верстиями и крепежными элементами режущая и калибрующая часть.
Калибрующая часть плашек осуществляет калибровку резьбы служит нап-
равляющей при продольном перемещении плашки во время резьбонарезания и
свинчивания выполняется с полным профилем резьбы.
Развертки цилиндрические предназначены для чистовой обработки отвер-
стий 6 – 10-го квалитетов точности с параметром шероховатости обработанной
поверхности Ra ≤ 25 мкм при обработке стальными и Ra ≤ 063 мкм при обработке
твердосплавными развертками.
По способу применения развертки подразделяют на машинные и ручные а
по принципу регулирования размера: постоянные и регулируемые.
Рабочая часть имеет стружечные канавки – прямые ( = 0) или винтовые
( = ± 25°) разделяющие зубья разверток.
Проектирование долбяка хвостового
1 Введение к инструменту
Зуборезные долбяки работают по методу обкатки. В основу изготовления
долбяка положена не прямозубая рейка а шестерня с соответствующими углами.
Производительность обработки долбяками несколько ниже чем червячными фре-
зами но они позволяют нарезать такие колеса как например блоки колес шев- ронные колеса внутреннего зацепления и другие которые нельзя нарезать чер-
вячными фрезами. Точность же по профилю зубчатых колес нарезанных долбяка-
ми выше чем при зубофрезеровании.
В зависимости от характера обрабатываемых деталей долбяки делятся на
) прямозубые – для нарезания прямозубых колес;
) косозубые – для нарезания колес с винтовым зубом и шевронных колес;
) специальные – для нарезания зубчатых деталей неэвольвентного зацепле-
ния (шлицевые валы звездочки и т. д.) .
По конструкции долбяки классифицируются на: дисковые чашечныевту-
лочные сборные хвостовые комбинированные.
Косозубый долбяк представляет собой косозубое зубчатое колесоснабжен-
ное режущими кромками. Для нарезания пары сцепляющихся колес применяются
два долбяка: правый – для нарезания колес с левым направлением зуба и левый -
для колес с правым направлением. У таких долбяков стандартный модуль и ос-
тальные расчетные данные задаются в нормальном сечении. Углы заточки долбя-
ка на обеих сторонах профиля получаются одинаковыми причем передняя повер-
хность зубьев наклонена от перефирии к центру и образует передний угол.
Боковые поверхности каждого зуба шлифуются по винтовым эвольвентам
в связи с чем при переточках долбяка по передней поверхности форма зуба прак-
тически не изменяется. При этом на одной стороне зуба винтовая эвольвентная поверхность делается правой а на другой – левой за счет чего на обеих сторонах зуба обеспечиваются боковые задние углы
обрабатываемый материал – СЧ 35;
модуль нормальный - 25;
число зубьев шестерни – 32;
число зубьев колеса -66;
угол наклона зуба – 10º;
степень точности колес – 7.
Расчет начинается с определения основных элементов в торцовом сечении.
Определяем торцовый модуль с точностью до 00001 мм.:
Определяем угол зацепления с точностью до 0000001:
Определяем коэффициент высоты зуба с точностью до 00001:
Определяем коэффициент высоты головки зуба с точностью до 0001
необходимой для получения радиального зазора:
Переходим к определению расчетных элементов долбяка.
С учетом принятых делительных диаметров 38; 75; 100; 150; 170; 360мм
(по ГОСТ 9323 - 60) принимаем dd = 75мм с числом зубьев z = 30.
Определяем диаметр делительной окружности:
Определяем величину смещения исходного сечения:
где a’ – величина смещения исходного сечения вдоль зуба долбяка мм;
Принимаем величину переднего угла γ = 10°.
Выбираем величину заднего угла αв на вершине зуба вдоль винтовой ли-
нии принимаемая равной 6° (при угле зацепления α = 20°).
Определяем величину заднего угла на вершине зуба долбяка вдоль оси
где u – угол наклона винтовой линии на делительном цилиндре u = 15°.
Определяем величину расчетного бокового заднего угла:
Определяем угол наклона винтовой линии на делительном цилиндре:
для позитивной стороны (боковая сторона зуба с острым углом)
для негативной стороны (боковая сторона зуба с тупым углом)
Определяем угол давления в торцовом сечении:
для позитивной стороны
для негативной стороны
Определяем диаметр основной окружности:
для негативной сторны
Определяем угол наклона винтовой линии на основном цилиндре:
Углы 0’’ и 0’ являются одновременно и углами поворота шлифовального
Определяем задний угол на боковой поверхности зуба в точках распо-
ложенных на основном цилиндре:
где 0 – угол наклона винтовой линии на основном цилиндре;
Производим определение размеров зуба долбяка в исходном сечении.
Определяем высоту головки зуба:
Определяем высоту ножки зуба:
Определяем толщину зуба по дуге делительной окружности:
Определяем диаметр вершин:
Определяем диаметр впадин:
Определяем размеры зуба долбяка в сечении переднего торца.
где Su – величина учитывающая искажения по толщине зуба долбяка вследствие
Определяем высоту головки зуба по передней поверхности:
Определяем диаметр окружности выступов:
Определяем диаметр окружности впадин:
Определяем толщину зуба по хорде:
Определяем высоту головки зуба до хорды:
3 Проверочный расчет
Конструкцию долбяка подвергаем проверке на отсутствие:
)подрезания зуба ножки зубчатой пары;
)срезания головки зуба зубчатой пары.
Подрезание отсутствует при условии что
где Au12 – среднее расстояние между осью долбяка и осями зубчатых колес мм;
r0 – радиус основной окружности долбяка r0 = 38.07 мм;
Откуда следует что подрезание зуба ножки зубчатой пары отсутствует.
Срезании отсутствует при условии что:
где Re2 – радиус окружности выступов большого зубчатого колеса
Au2 – расстояние между осями долбяка и большого зубчатого колеса мм;
r02 - радиус основной окружности большого зубчатого колеса r02 = 83.77 мм;
Откуда следует что срезание головки зуба зубчатой пары отсутствует.
4 Технические требования на изготовление долбяка хвостового
В целях повышения срока службы долбяка целесообразно увеличить ис-
ходные расстояния однако данное обстоятельство ограничивается опасностью за-
острения зубьев или неполной обработкой рабочего участка профиля. Долбяки
как с положительным так и с отрицательным смещением исходного контура т. е.
при любой степени сточенности должны обеспечивать требуемую точность обра-
Класс точности долбяка - В.
Долбяк должен удовлетворять техническим требованиям ГОСТ 9323 – 79.
Биение окружности вершин зубьев 001мм.
Радиальное биение хвостовика долбяка 0005мм.
Твердость режущей части 62 65 HRC .
Материал хвостовика сталь 45.
Разность соседних окружных шагов не более 0006мм.
Накопленное отклонение окружного шага 0018мм.
В месте сварки раковины и непровар не допускаются.
Маркировать: m = 25; = 10°; Р6М5 ГОСТ 19265 – 73.
5 Термическая обработка инструментального материала долбяка
Инструментальный материал долбяка хвостового – Сталь Р6М5.
По рекомендации стр. 311[5] для корпуса долбяка хвостового выполнить:
Для снижения твердости улучшения обработки резанием и подготовки
структуры стали к закалке сталь подвергают отжигу при 800 830°С.
Нагрев под закалку – в расплаве солей при 800 850°С 10 15мин.
Для придания стали теплостойкости инструмент подвергаем закалке
Отпуск закаленного инструмента производится в жидкой или воздуш-
ной среде(для увеличения твердости):
первый отпуск при 350°С 1час;
второй отпуск при 560 570°С 1час;
третий отпуск при 560 570°С
Для нарезания наружных резьбы диаметром от 1 до 52 мм(иногда до 135мм)
другие. Основные размеры плашек стандартизованы. Внешние размеры плашки зависят от диаметра нарезаемой резьбы диаметра стружечных отверстий прочности и жесткости перемычек.
верстиями и крепежными элементами режущая и калибрующая часть. Корпус
служит для базирования и крепления плашки во время нарезания резьбы при за-
точках и переточках. Корпус может быть выполнен заодно с режущей и калиб-
рующей частями или соединяться с ними сваркой пайкой и механическими спо-
свинчивания.Выполняется с полным профилем резьбы исполнительные размеры
которой обеспечивают получение резьбы требуемой точности.Стандартные
плашки нарезают резьбы с посадками скольжения квалитетов 6h; 8h и с посадка-
ми с зазором квалитетов 6g; 6e; 6d а трубные резьбы – классов А или Б.
Резьба режущей (как и калибрующей) части плашки не затылуется и зад-
ние углы на калибрующей части равны нулю. Накопленная ошибка шага резьбы
составляет 0008 – 001 мм на 25 мм длины.
Резьба калибрующей части может иметь доводку по профилю или быть без
доводки (в зависимости от шероховатости).
Плашки стандартного типа работают с самозатягиванием в связи с чем
при закреплении их на станках необходимо использовать “ плавающие ” патроны
дающие возможность плашке самоустановиться на обрабатываемой заготовке.
обрабатываемый материал – сталь 20;
разновидность – двухсторонняя;
степень точности – 8.
Наружный диаметр плашки D выбираем в зависимости от номинального
размера резьбы и принятого количества стружечных отверстий n: D=65мм и n=6
Угол заборной части φ =25°(для лучшего использования плашки делает-
Определяем длину заборной части:
где t2 – высота резьбы t2 = 173 мм;
a1 – величина превышения заборной части над высотой резьбы обеспечивающая захват заготовки a1 = 025 мм.
Определяем диаметр заборной части:
где do – наружный диаметр резьбы do = 33 мм.
Длину калибрующей части lz устанавливаем в пределах пяти шагов наре- заемой резьбы т. е. lz = 10 мм.
Определяем ширину плашки:
Ширина круглых плашек для стандартных резьб стандартизована. Принимаем h = 20 мм.
Величина переднего угла γ у круглых плашек назначается в зависимости от свойств обрабатываемого материала. Принимаем γ = 20°. Величина угла γ не является постоянной величиной для данной плашки и уменьшается по направле- нию к наружному диаметру резьбы.
Задний угол α принимаем равным 8° (задний угол создается только на заборной части).
Определяем величину затылования необходимую для образования уг-
где dвн – внутренний диаметр резьбы dвн = 313 мм;
z – число перьев плашки z = 6.
Определяем ширину пера:
Угол наклона режущей кромки λ принимаем равным 0°.
Определяем радиус стружечных отверстий r при криволинейной форме передней поверхности:
где k – коэффициент зависящий от принятой величины h k = 115.
Определяем радиус окружности расположения центров стружечных отверcтий:
Толщину перемычки l2 принимаем равной 2мм угол регулировочного паза 60° а его ширину b = 3 мм [3].
Производим проверку толщины тела плашки L по формуле:
Рекомендуется чтобы величина L была в пределах:
(009 010)D при z = 6 8
В нашем случае L = 009D.Условие прочности выполняется.
После аналитического расчета вычерчиваем плашку и проверяем все ее
элементы графическим способом.
4 Технические требования на изготовление плашки круглой
Материал корпуса плашки – инструментальная легированная сталь 9ХС
Твердость зубьев у режущих кромок HRC 58 62.
Радиальное биение наружной цилиндрической поверхности плашки относительно оси резьбы и торцевое биение плашек относительно наиболее удаленной
точки от оси – 01мм.
Параметр шероховатости передней поверхности плашки Ra ≤ 125мкм.
Маркировать: обозначение резьбы степень точности товарный знак завода изготовителя (M33 × 2 – H8 - ).
5 Термическая обработка инструментального материала плашки круглой
По рекомендации стр. 309[5] для корпуса плашки круглой изготовленной
из стали 9ХС выполнить:
При нагреве под закалку предварительно нагреть до температуры
Нагрев под закалку – в расплаве солей при 810°С.
Закалка при 160 180°С (в масле или горячих средах).
Производим отпуск закаленного инструмента в жидкой или воздушной
по принципу регулирования размера постоянные и регулируемые.
Развертки конические служат для образования конических отверстий под
штифты конусы и т.д.
Развертки состоят из рабочей части и корпуса (хвостовика).
( = ± 25°) разделяющие зубья разверток. Число зубьев (канавок) разверток зави-
сит от их конструкции.
Расположение зубьев по окружности может быть равномерным или не-
равномерным различие значений центральных углов ограничивающих зубья мо-
жет достигать 30° (у стандартных разверток 05 - 5°).
Передняя поверхность обычно прямолинейна ( = 0; γ = 0). Ленточка вы-
полнена по цилиндру (f = 005 04мм).
Режущая часть разверток имеет форму зависящую от условий обработки.
задняя поверхность затачивается наостро или с оставлением ленточки. Получают распространение развертки с ломанной режущей кромкой или с криволинейной кромкой. При обработке вязких материалов в том числе коррозионно-стойких и жаропрочных сталей применяют кольцевую форму режущей части.
Процесс развертывания отличается рядом особенностей:
уменьшенными припусками на обработку;
малой толщиной и большой шириной стружки пониженными в этой связи
нагрузками на каждую кромку;
ориентацией развертки по отверстию при врезании режущей части (приме-
няют “плавающие” патроны удлиненные оправки и т.д.);
увеличенным числом зубьев участвующих одновременно в работе;
надежным направлением развертки по отверстию за счет цилиндрической
обрабатываемый материал – сталь 5;
диаметр отверстия – 56Н6;
длина отверстия – 45-сквозное;
хвостовик – конический;
инструментальный материал – твёрдый сплав.
Составим технологический маршрут обработки детали [2]. Для обработ-
ки отверстия диаметром 56Н6 необходимо выполнить сверление рассверливание
предварительное зенкерование предварительное и окончательное развертывание.
Назначаем межоперационные припуски [2]: под окончательное развер-
тывание 008 мм предварительное развертывание 021 мм предварительное зен-
керование 271 мм и рассверливание 22 мм.
Поле допуска для отверстия диаметром 56Н6 по СТ СЭВ 144-75: верхнее
отклонение 0019 мм нижнее отклонение 0 мм поле допуска 0 019 мм.
Поле допуск на изготовление развертки принимают равным 025 04 от допуска на изготовление отверстия: Н=0005 мм; верхнее отклонение
08 мм нижнее отклонение 0003 мм поле допуска 0 005 мм.
Определяем число зубьев развертки:
где d – диаметр развертки d = 56 мм.
Число зубьев принимаем четным т.е. z = 14 чтобы измерение развертки
можно было проводить микрометром.
Принимаем передний угол γ = 10°.
Задний угол α принимаем равным 7°.
На калибрующей части развертки выполняем цилиндрическую фаску
Определяем длину заборной части развертки:
где t – припуск под развертывание на сторону;
φ – угол при вершине φ = 15°.
Калибрующая часть развертки состоит из конической и цилиндрической
частей. Коническую часть выполняют для уменьшения трения и предотвращения
разбивки отверстия. Разность диаметров на этом участке составляет 003 005мм
Определяем длину цилиндрической части вместе с заборным конусом:
Определяем длину рабочей части:
Определяем общую длину развертки:
lхв – длина хвостовика lхв = 124мм.
Конструктивные элементы развертки для обработки сталей принимаем
по ГОСТ 1672-80 11172-80 16086-7016087-70.
Размеры профиля стружечных канавок развертки: ff =05 мм;
R0 = 20мм; r = 1мм [2].
3 Технические требования на изготовление развертки хвостовой
Твердость рабочей части развертки из твердого сплава Т15К6 – 65 67 HRC.
Твердость лапки 35 55 HRCэ.
Параметры шероховатости:
передняя поверхность развертки
задняя поверхность режущей части и ленточка на калибрующей части
задняя поверхность калибрующей части
Обратная конусность по наружному диаметру развертки 001мм.
Заточка режущей производится алмазными кругами АСО1061 доводка – ал-
мазными кругами АСМ361 или пастами АП17 АП28.
Развертка должна удовлетворять техническим требованиям ГОСТ 1672-80
Маркировать: диаметр развертки марку режущей части и товарный
знак завода изготовителя (56 – Т15К6 - ).
4 Термическая обработка инструментального материала развертки
По рекомендации стр. 311[5] для рабочей части развертки хвостовой
третий отпуск при 560 570°С
5 Расчет инструментального блока на точность позиционирования и
Определяем величины отклонения вершины инструмента от номинального положения при сборке и деформации под действием силы резания для инструментального блока.
Найдем для нашего случая величины биений.
Биение конического отверстия шпинделя станка: l1 = 0008 мм.
Допускаемый перекос: l2 = 0001 мм.
Биение базового агрегата от перехода в соединении конусности 7:24
Биение оправки от зазора в цилиндрическом соединении: 2l4 = 00011 мм.
Биение посадочного отверстия базисного агрегата: 2l5 = 002 мм.
Биение втулки от перекоса в цилиндрическом соединении: l6 = 00016 мм. Биение цилиндрической поверхности: 2l7 = 002мм.
Биение цилиндрического отверстия во втулке переходной: 2l8 = 001 мм.
Биение режущего инструмента от перекоса в коническом соединении:
Величина первичного отклонения вершины инструмента от номинального положения:
где K - коэффициент относительного рассеивания величины замыкающего
lнi - вылет на котором нормируется величина перекоса в i – ом соединении.
Коэффициент рассеивания ki:
для цилиндрических поверхностей - k
для конической поверхности 1:30 - ki = 137.
Передаточные отношения:
Допускаемое биение развертки диаметром 56 мм – 008 мм по табл. 8[4]
Расчет инструментального блока на податливость.
Согласно схеме сборки перемещения крепления оправки определим как
суммарное смещение режущей кромки в точке приложения нагружающей силы
(P = 1kH) с учетом контактной податливости в соединениях инструмента:
- модуль продольной упругости ();
- осевой момент инерции сечения
di - диаметр i - го элемента.
Qi M - податливость в конусе с конусностью 7:24 по табл. 10[4].
Qi M - податливость в цилиндрическом соединении с боковым зажимным
Qi M - податливость в конусе 1:30 по табл. 12[4] = 00014
Податливость инструментального блока: 1641 мкм кН.
Для разверток диаметром до 120 мм допускается податливость :
Жесткость инструментального блока:
6 Схема сборки инструментального блока
В этом разделе указываем перечень использованных ГОСТов:
ГОСТ 9323 – 79; ГОСТ 5953 – 70; ГОСТ 1672 – 80; ГОСТ 13777 – 79;
ГОСТ 9740 – 71; ГОСТ 1672 – 71.
Список использованной литературы
Иноземцев Г. Г. Проектирование металлорежущих инструментов – М.:
Машиностроение 1984 – 272с.
Фельдштейн Е.Э. Курсовое и дипломное проектирование – Мн:
Дизайн ПРО 1997 - 384 с.
Климов В. И. Справочник инструментальщика – конструктора – М.:
Машгиз 1958 - 608 с.
Фельдштейн Е. Э. Режущий инструмент и оснастка для станков с ЧПУ –
Мн.: Высшая школа 1988 - 336с.
Лахтин Ю. М. Материаловедение – М.: Машиностроение 1980 - 493c.
Чертеж долбяк.cdw

хвостовой части 32 35HRC.
Материал хвостовика сталь45 ГОСТ1050-88
В месте сварки раковины и непровар не допускаются
Разность соседних окружных шагов не более 0
Накопленное отклонение окружного шага 0
Маркировать: m=3.5; b=10; Р6М5 ГОСТ 19265-73
Коэффициент смещения
Развертка А.frw

Развертки должны удовлетворять техническим
требованиям ГОСТ1672-80
Заточка режущей части производится алмазными
доводка-алмазными кругами
АСМ3Б1 или пастами АП28 АП17.
Обратная конусность по наружному диаметру
Маркировать: диаметр развертки
режущей части и товарный знак завода-изгото-
БИ 05403.03.00.000. СБ
Сталь Р6М5 ГОСТ19265-73
Разраб. Чумаков А.А.
плашка.frw

ХВСГ или 9ХС по ГОСТ 5950-73
Твердость зубьев у режущих кромок должна быть у
плашек из сталей марок ХВСГ
Радиальное биение наружной цилиндрической
поверхности плашек относительно оси резьбы и
торцевое биение плашек относительно наиболее
удоленной точки от оси для диаметра >26-0.1мм
Маркировать: обозначение резьбы
товарный знак завода изготовителя(М36х2-Н6- )
Разраб. Чумаков А.А.
Исполнение 2 по АС 1106601
Сталь9ХС ГОСТ5950-73
Чертеж долбяк12.cdw

хвостовой части 32 35HRC.
Материал хвостовика сталь45 ГОСТ1050-88
В месте сварки раковины и непровар не допускаются
Разность соседних окружных шагов не более 0
Накопленное отклонение окружного шага 0
Маркировать: m=3.5; b=10; Р6М5 ГОСТ 19265-73
Коэффициент смещения
Спецификация.spw

Чертеж развертка модифмкация.cdw

Развертки должны удовлетворять техническим требованиям
Заточка режущей части производится алмазными кругами АС01061
доводка-алмазными кругами АСМ3Б1 или пастами АП28 АП17.
Обратная конусность по наружному диаметру развертки 0
Маркировать: диаметр развертки
режущей части и товарный знак завода-изготовителя
Блок инструментальный
долбяк хвостовой.frw

35HRC. Материал хвостовика сталь45 ГОСТ1050-88
В месте сварки раковины и непровар не допускаются
Разность соседних окружных шагов не более 0
Накопленное отклонение окружного шага 0
Маркировать: m=3.5;
=10; Р6М5 ГОСТ 19265-73
Коэффициент смещения
Чертеж долбяк окончательно.cdw

хвостовой части 32 35HRC.
Материал хвостовика сталь45 ГОСТ1050-88
В месте сварки раковины и непровар не допускаются
Разность соседних окружных шагов не более 0
Накопленное отклонение окружного шага 0
Маркировать: m=3.5; b=10; Р6М5 ГОСТ 19265-73
Толщина зуба по делительной
Коэффициент смещения
Чертеж плашка.cdw

Твердость зубьев у режущих кромок должна быть у
плашек из стали марки 9ХС HRC 58 62
Радиальное биение наружной цилиндрической
поверхности плашек относительно оси резьбы и
торцевое биение плашек относительно наиболее
удоленной точки от оси для диаметра >26-0.1мм
Маркировать: обозначение резьбы
товарный знак завода изготовителя(М33х2-Н8- )
Сталь9ХС ГОСТ5950-73
Исполнение 2 по АС 1106601
Моя записка11.doc
Министерство образования и науки Российской Федерации
Учреждение высшего профессионального образования
БЕЛОРУССКО-РОССИЙСКИЙ УНИВЕРСИТЕТ
по дисциплине «Режущий инструмент»
на тему: «Проектирование конструкций металлорежущих инструментов»
Пояснительная записка 31406.00.00.000 ПЗ
Проектирование первого инструмента 1
1 Введение к долбяку хвостовому 3
2 Проектный расчет долбяка хвостового
3 Проверочный расчет 9
Проектирование второго инструмента 11
1 Введение к плашке круглой
2 Проектный расчет плашки 11
3 Проверочный расчет 11
Проектирование третьего инструмента 15
1 Введение к развёртке 15
2 Проектный расчет развёртки 16
3 Схема расчета полей допусков и диаметров развертки 18
4 Технические требования на изготовление и контроль 19
5 Расчет инструментального блока на точность и податливость 19
6 Термическая обработка корпуса развертки 21
7 Оптимизация режимов резания 22
8 Схема сборки инструментального блока 23
Список использованной литературыВведение
Проектирование долбяка хвостового
1 Введение к инструменту
Зуборезные долбяки работают по методу обкатки. В основу изготовления
долбяка положена не прямозубая рейка а шестерня с соответствующими углами.
Производительность обработки долбяками несколько ниже чем червячными фре-
зами но они позволяют нарезать такие колеса как например блоки колес шев- ронные колеса внутреннего зацепления и другие которые нельзя нарезать чер-
вячными фрезами. Точность же по профилю зубчатых колес нарезанных долбяка-
ми выше чем при зубофрезеровании.
В зависимости от характера обрабатываемых деталей долбяки делятся на
) прямозубые – для нарезания прямозубых колес;
) косозубые – для нарезания колес с винтовым зубом и шевронных колес;
) специальные – для нарезания зубчатых деталей неэвольвентного зацепле-
ния (шлицевые валы звездочки и т. д.) .
По конструкции долбяки классифицируются на: дисковые чашечныевту-
лочные сборные хвостовые комбинированные.
По точности долбяки бывают классов АА А и В. Для обеспечения резания
долбяку придают измененный вид по сравнению с обычным зубчатым колесом.
Косозубый долбяк представляет собой косозубое зубчатое колесоснабжен-
ное режущими кромками. Для нарезания пары сцепляющихся колес применяются
два долбяка: правый – для нарезания колес с левым направлением зуба и левый -
для колес с правым направлением. У таких долбяков стандартный модуль и ос-
тальные расчетные данные задаются в нормальном сечении. Углы заточки долбя-
ка на обеих сторонах профиля получаются одинаковыми причем передняя повер-
хность зубьев наклонена от перефирии к центру и образует передний угол.
Боковые поверхности каждого зуба шлифуются по винтовым эвольвентам
в связи с чем при переточках долбяка по передней поверхности форма зуба прак-
тически не изменяется. При этом на одной стороне зуба винтовая эвольвентная поверхность делается правой а на другой – левой за счет чего на обеих сторонах зуба обеспечиваются боковые задние углы
обрабатываемый материал – СЧ 35;
модуль нормальный - 25;
число зубьев шестерни – 32;
число зубьев колеса -66;
угол наклона зуба – 10º;
степень точности колес – 7.
Расчет начинается с определения основных элементов в торцовом сечении.
Определяем торцовый модуль с точностью до 00001 мм.:
Определяем угол зацепления с точностью до 0000001:
Определяем коэффициент высоты зуба с точностью до 00001:
Определяем коэффициент высоты головки зуба с точностью до 0001
необходимой для получения радиального зазора:
Переходим к определению расчетных элементов долбяка.
С учетом принятых делительных диаметров 38; 75; 100; 150; 170; 360мм
(по ГОСТ 9323 - 60) принимаем dd = 75мм с числом зубьев z = 30.
Определяем диаметр делительной окружности:
Определяем величину смещения исходного сечения:
где a’ – величина смещения исходного сечения вдоль зуба долбяка мм;
Принимаем величину переднего угла γ = 10°.
Выбираем величину заднего угла αв на вершине зуба вдоль винтовой ли-
нии принимаемая равной 6° (при угле зацепления α = 20°).
Определяем величину заднего угла на вершине зуба долбяка вдоль оси
где u – угол наклона винтовой линии на делительном цилиндре u = 15°.
Определяем величину расчетного бокового заднего угла:
Определяем угол наклона винтовой линии на делительном цилиндре:
для позитивной стороны (боковая сторона зуба с острым углом)
для негативной стороны (боковая сторона зуба с тупым углом)
Определяем угол давления в торцовом сечении:
для позитивной стороны
для негативной стороны
Определяем диаметр основной окружности:
для негативной сторны
Определяем угол наклона винтовой линии на основном цилиндре:
Углы 0’’ и 0’ являются одновременно и углами поворота шлифовального
Определяем задний угол на боковой поверхности зуба в точках распо-
ложенных на основном цилиндре:
где 0 – угол наклона винтовой линии на основном цилиндре;
Производим определение размеров зуба долбяка в исходном сечении.
Определяем высоту головки зуба:
Определяем высоту ножки зуба:
Определяем толщину зуба по дуге делительной окружности:
Определяем диаметр вершин:
Определяем диаметр впадин:
Определяем размеры зуба долбяка в сечении переднего торца.
где Su – величина учитывающая искажения по толщине зуба долбяка вследствие
Определяем высоту головки зуба по передней поверхности:
Определяем диаметр окружности выступов:
Определяем диаметр окружности впадин:
Определяем толщину зуба по хорде:
Определяем высоту головки зуба до хорды:
3 Проверочный расчет
Конструкцию долбяка подвергаем проверке на отсутствие:
)подрезания зуба ножки зубчатой пары;
)срезания головки зуба зубчатой пары.
Подрезание отсутствует при условии что
где Au12 – среднее расстояние между осью долбяка и осями зубчатых колес мм;
r0 – радиус основной окружности долбяка r0 = 38.07 мм;
Откуда следует что подрезание зуба ножки зубчатой пары отсутствует.
Срезании отсутствует при условии что:
где Re2 – радиус окружности выступов большого зубчатого колеса
Au2 – расстояние между осями долбяка и большого зубчатого колеса мм;
r02 - радиус основной окружности большого зубчатого колеса r02 = 83.77 мм;
Откуда следует что срезание головки зуба зубчатой пары отсутствует.
Проектирование плашки круглой
1 Введение к инструменту
Для нарезания наружных резьбы диаметром от 1 до 52 мм(иногда до 135мм)
предназначены плашки круглые.
По форме плашки подразделяются на трубчатые круглые квадратные и
другие. Основные размеры плашек стандартизованы. Внешние размеры плашки зависят от диаметра нарезаемой резьбы диаметра стружечных отверстий прочности и жесткости перемычек.
Конструктивные элементы плашек следующие: корпус со стружечными от-
верстиями и крепежными элементами режущая и калибрующая часть. Корпус
служит для базирования и крепления плашки во время нарезания резьбы при за-
точках и переточках. Корпус может быть выполнен заодно с режущей и калиб-
рующей частями или соединяться с ними сваркой пайкой и механическими спо-
Калибрующая часть плашек осуществляет калибровку резьбы служит нап-
равляющей при продольном перемещении плашки во время резьбонарезания и
свинчивания.Выполняется с полным профилем резьбы исполнительные размеры
которой обеспечивают получение резьбы требуемой точности.Стандартные
плашки нарезают резьбы с посадками скольжения квалитетов 6h; 8h и с посадка-
ми с зазором квалитетов 6g; 6e; 6d а трубные резьбы – классов А или Б.
Резьба режущей (как и калибрующей) части плашки не затылуется и зад-
ние углы на калибрующей части равны нулю. Накопленная ошибка шага резьбы
составляет 0008 – 001 мм на 25 мм длины.
Резьба калибрующей части может иметь доводку по профилю или быть без
доводки (в зависимости от шероховатости).
Плашки стандартного типа работают с самозатягиванием в связи с чем
при закреплении их на станках необходимо использовать “ плавающие ” патроны
дающие возможность плашке самоустановиться на обрабатываемой заготовке.
обрабатываемый материал – сталь 20;
разновидность – двухсторонняя;
степень точности – 8.
Наружный диаметр плашки D выбираем в зависимости от номинального
размера резьбы и принятого количества стружечных отверстий n: D=65мм и n=6
Угол заборной части φ =25°(для лучшего использования плашки делает-
Определяем длину заборной части:
где t2 – высота резьбы t2 = 173 мм;
a1 – величина превышения заборной части над высотой резьбы обеспечивающая захват заготовки a1 = 025 мм.
Определяем диаметр заборной части:
где do – наружный диаметр резьбы do = 33 мм.
Длину калибрующей части lz устанавливаем в пределах пяти шагов наре- заемой резьбы т. е. lz = 10 мм.
Определяем ширину плашки:
Ширина круглых плашек для стандартных резьб стандартизована. Принимаем h = 20 мм.
Величина переднего угла γ у круглых плашек назначается в зависимости от свойств обрабатываемого материала. Принимаем γ = 20°. Величина угла γ не является постоянной величиной для данной плашки и уменьшается по направле- нию к наружному диаметру резьбы.
Задний угол α принимаем равным 8° (задний угол создается только на заборной части).
Определяем величину затылования необходимую для образования уг-
где dвн – внутренний диаметр резьбы dвн = 313 мм;
z – число перьев плашки z = 6.
Определяем ширину пера:
Угол наклона режущей кромки λ принимаем равным 0°.
Определяем радиус стружечных отверстий r при криволинейной форме передней поверхности:
где k – коэффициент зависящий от принятой величины h k = 115.
Определяем радиус окружности расположения центров стружечных отверcтий:
Толщину перемычки l2 принимаем равной 2мм угол регулировочного паза 60° а его ширину b = 3 мм [3].
Производим проверку толщины тела плашки L по формуле:
Рекомендуется чтобы величина L была в пределах:
(009 010)D при z = 6 8
В нашем случае L = 009D.Условие прочности выполняется.
После аналитического расчета вычерчиваем плашку и проверяем все ее
элементы графическим способом.
Проектирование развертки хвостовой
Развертки цилиндрические предназначены для чистовой обработки отвер-
стий 6 – 10-го квалитетов точности с параметром шероховатости обработанной
поверхности Ra ≤ 25 мкм при обработке стальными и Ra ≤ 063 мкм при обработке
твердосплавными развертками.
По способу применения развертки подразделяют на машинные и ручные а
по принципу регулирования размера постоянные и регулируемые.
Развертки конические служат для образования конических отверстий под
штифты конусы и т.д.
Развертки состоят из рабочей части и корпуса (хвостовика).
Рабочая часть имеет стружечные канавки – прямые ( = 0) или винтовые
( = ± 25°) разделяющие зубья разверток. Число зубьев (канавок) разверток зави-
сит от их конструкции.
Расположение зубьев по окружности может быть равномерным или не-
равномерным различие значений центральных углов ограничивающих зубья мо-
жет достигать 30° (у стандартных разверток 05 - 5°).
Передняя поверхность обычно прямолинейна ( = 0; γ = 0). Ленточка вы-
полнена по цилиндру (f = 005 04мм).
Режущая часть разверток имеет форму зависящую от условий обработки.
задняя поверхность затачивается наостро или с оставлением ленточки. Развертки с углом φ 45° имеют дополнительную фаску с × 45°. Получают распространение
развертки с ломанной режущей кромкой или с криволинейной кромкой. При обра-
ботке вязких материалов в том числе коррозионно-стойких и жаропрочных ста-
лей применяют кольцевую форму режущей части.
Процесс развертывания отличается рядом особенностей:
уменьшенными припусками на обработку;
малой толщиной и большой шириной стружки пониженными в этой связи
нагрузками на каждую кромку;
ориентацией развертки по отверстию при врезании режущей части (приме-
няют “плавающие” патроны удлиненные оправки и т.д.);
увеличенным числом зубьев участвующих одновременно в работе;
надежным направлением развертки по отверстию за счет цилиндрической
обрабатываемый материал – сталь 5;
диаметр отверстия – 56Н6;
длина отверстия – 45-сквозное;
хвостовик – конический;
инструментальный материал – твёрдый сплав.
Составим технологический маршрут обработки детали [2]. Для обработ-
ки отверстия диаметром 56Н6 необходимо выполнить сверление рассверливание
предварительное зенкерование предварительное и окончательное развертывание.
Назначаем межоперационные припуски [2]: под окончательное развер-
тывание 008 мм предварительное развертывание 021 мм предварительное зен-
керование 271 мм и рассверливание 22 мм.
Поле допуска для отверстия диаметром 56Н6 по СТ СЭВ 144-75: верхнее
отклонение 0019 мм нижнее отклонение 0 мм поле допуска 0 019 мм.
Поле допуск на изготовление развертки принимают равным 025 04 от допуска на изготовление отверстия: Н=0005 мм; верхнее отклонение
08 мм нижнее отклонение 0003 мм поле допуска 0 005 мм.
Определяем число зубьев развертки:
где d – диаметр развертки d = 56 мм.
Число зубьев принимаем четным т.е. z = 14 чтобы измерение развертки
можно было проводить микрометром.
Принимаем передний угол γ = 10°.
Задний угол α принимаем равным 7°.
На калибрующей части развертки выполняем цилиндрическую фаску
Определяем длину заборной части развертки:
где t – припуск под развертывание на сторону;
φ – угол при вершине φ = 15°.
Калибрующая часть развертки состоит из конической и цилиндрической
частей. Коническую часть выполняют для уменьшения трения и предотвращения
разбивки отверстия. Разность диаметров на этом участке составляет 003 005мм
Определяем длину цилиндрической части вместе с заборным конусом:
Определяем длину рабочей части:
Определяем общую длину развертки:
lхв – длина хвостовика lхв = 124мм.
Конструктивные элементы развертки для обработки сталей принимаем
по ГОСТ 1672-80 11172-80 16086-7016087-70.
Размеры профиля стружечных канавок развертки: ff =05 мм;
R0 = 20мм; r = 1мм [2].
Список использованной литературы
Романов В.Ф. Расчеты зуборезных инструментов – М: Машиностроение 1969 – 255 с.
Фельдштейн Е.Э. Курсовое и дипломное проектирование – Мн: Дизайн ПРО 1997 - 384 с.