Coursework 3-storey brick cottage



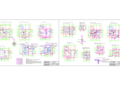
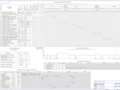
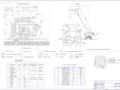
- Added: 31.03.2021
- Size: 5 MB
- Downloads: 0
Description
Cottage 3-storey, brick, floor height 3.1 m. Borovsk construction district, Kaluga region Climatic district: Borovsk III B Temperature characteristics: January − 6.9 ° С; July + 17.8 ° C Prevailing winds: West and South Freezing Depth: m = 1.7 m Materials: Foundation - strip of prefabricated concrete blocks and railway cushions External walls - porous brick of CJSC "Victory/Knauf" Internal walls - from brick KRPU 75/1450/15 GOST 530-80 on cement-sand mortar of grade M50 Jumpers - precast reinforced concrete according to the series 1.038.1-1, in 4 Floors - prefabricated railway slabs according to the series 1.141-1, 60.64 Staircase - in the basement from prefabricated individual railway stages Partitions - from a profile metal frame, covered on both sides with gypsum cardboard sheets Roof - gable of wooden rafters Roof - metal staple Floors - laminated panels Windows - plastic Doors - entrance metal, interior wooden
Contents
1. Engineering assignment for design.................................................................................................................
2. Introduction …………………… …………………… …………………… ………….
3. Initial data...........................................................................................................................................................................................................................................................................................................................................................................................................................................
4. Construction and installation works.........................................................................................................................
5. Safety.............................................................................
6. Engineering equipment...................................................
7. Calendar plan.........................................................................................
8. Construction Plot Plan.............................................................................................................
9. Production control................................................................................................................................................................................................................................................................................................................................................................................................................................................................
10. Occupational safety and fire safety measures..............
11. Environmental Conditions..............................
12. Process map.........................................................................................................................
13. Conclusion …………………… …………………… …………………… …… …
14. List of used sources......................................................
15. Applications …………………… …………………… …………………… …….
16. Specifications …………………… …………………… …………………… ….
Project's Content
![]() ![]() ![]() ![]() |
![]() ![]() |
![]() ![]() ![]() |
![]() ![]() ![]() ![]() |
![]() ![]() ![]() ![]() |
![]() ![]() ![]() ![]() |
![]() ![]() ![]() ![]() |
![]() ![]() ![]() ![]() |
![]() ![]() ![]() ![]() |
![]() ![]() ![]() ![]() |
Additional information
Contents
Contents
1. Engineering Assignment for Design
2. Introduction
3. Initial data
4. Construction and installation works
5. Safety precautions
6. Engineering equipment
7. Calendar Plan
8. Construction Master Plan
9.Productive control
10. Occupational Safety and Fire Safety Measures
11. Environmental conditions
12. Technology Map
13. Conclusion
14. List of used sources
15. Applications
16. Specifications
Introduction
Modern individual construction and design allows you to more fully satisfy the needs of each family member according to the age limit, according to what place in society is assigned to the inhabitants of the house. A deep study of the life of the family allows you to solve the functional zoning of the apartment, successfully organize life, study, work, rest of the family as a whole and each of its members individually. Modern projects with their diverse form, the use of new finishing materials, structural solutions allow you to create individual urban planning complexes in combination with public buildings. Important in individual construction is the widespread use of local building materials and products, which allows to significantly reduce the cost of their transportation and installation.
Construction and installation works
Engineering and preparatory works.
Engineering support of the construction site provides for the encirclement of the territory with a fence from 2 meters high with protective caps, the construction of temporary roads from reinforced concrete slabs, the supply of water supply networks with connection to the existing network, as well as power supply and sewerage.
The construction site is cleaned of garbage, the trees that are on it are uprooted and transplanted to a specially brought place.
The construction site will be equipped with locker rooms, a dining room, showers, a work manufacturer's office, warehouses and temporary workshops, as well as the organization of lighting of the construction site;
All domestic and temporary premises are outside the crane radius for greater safety.
Earthworks.
Usually, the process of compaction of soil in the planning embankment is preceded by leveling, which is carried out by bulldozers and less often graders. Leveling is carried out in horizontal layers at longitudinal course of bulldozer. Thickness of layers is 0.20.4m in loose state. The sequence and number of passes of the bulldozer depends on the width of the embankment. Leveling is carried out from the edges of the fill to its middle with overlapping of the previous passage by 0.3 m.
For soil compaction, trailed rollers are most often used, the most effective of which are rinks on a pneumatic passage. Soil is compacted in the same sequence as its filling. The soil is compacted by successive circular penetrations of the roller over the entire area of the embankment, each penetration must cover the previous one by 0.20.3 m. Having finished rolling the entire area in one pass, they begin a second penetration.
So that the soil does not collapse near the embankment, the first two penetrations along the slope lead at a distance of at least 1.5 m from the brow. Subsequent penetrations are shifted by 0.5 m to the side of the brow, and thus the edges of the embankment are rolled. Since the rolling is carried out in several penetrations along one trace, the first half of the penetrations is carried out at a low speed, and the second half is carried out at a higher speed, since as the fill density increases, the resistance to the motion of the roller decreases significantly.
The most difficult is soil compaction when backfilling the sinuses of foundations or trenches, since the work is carried out in cramped conditions. In these cases, the soil is compacted 0.8 m wide from the foundation with 1520 cm layers of pneumatic or electric ramming, and the upper layers are compacted with more productive small-sized rollers, self-transmitting vibration plates, etc.
An installation for translucent of soil by gammaluchs is also used: at a certain distance two pipes are immersed in the soil, in one of which any radioactive isotope is laid, and in the other - a quantum radiation counter measuring the intensity of radiation, which depends on the density of the soil separating both pipes .
Soil is also compacted with the help of various rollers operating in coupling with tractor. Vibration tamping machines are also used to transmit frequent oscillatory movements to the compacted soil, and tamping machines with a working element in the form of a plate periodically falling on the soil from various heights.
Earth-moving and earth-moving vehicles are used in earthworks. The planning of the territory of the construction site and the cutting of the vegetation layer are carried out using the bulldozer DZ329, which works in a layer-by-layer manner with the movement of soil at a distance of up to 100 m. Also, with the help of the bulldozer, backfilling of the soil is carried out.
Installation of tape foundations.
Designed foundations - prefabricated tape. Foundation depth -1.500m. Bottom elevation -2.650 m.
The width of the tape foundations is assigned to:
for bearing internal walls along axes - 1600 mm
for bearing external walls along axes - 1400 mm.
The basement walls for the internal walls are designed with a width of 400 mm, for the external walls of 600 mm.
Waterproofing of the underground part of the building:
horizontal is made along the cut of the foundation from two layers of hydroisol on bitumen mastic.
vertical is performed by coating with hot bitumen in 2 times of the surface contacting the soil.
To protect the foundations from surface water along the perimeter of the building, asphalt concrete paving is made with a width of 1000 mm along a crushed stone base with a thickness of 120 mm with a slope of 3% from the building.
Tape foundations are usually made of reinforced concrete blocks - pillows and several rows of wall beams laid along them, which can also be blocks of basement walls.
The installation of blocks is preceded by a breakdown of the foundation axes, which begins with the transfer of the building axes to the base. For this purpose, axial strings are pulled on the shoe and points of their intersection are transferred to the bottom of pits and trenches with the help of plumbs. The design dimensions of the foundations are measured from these points and fixed with metal pins so that the wire berth stretched between them is 2-3 mm further than the side face of the tape foundation.
Installation of cushion blocks is started by laying corner cushions, which are lighthouses, as well as intermediate lighthouses at a distance of about 20 m between them, mainly at the junction of transverse walls with longitudinal ones. Intermediate units are placed successively of lighthouse corner unit to lighthouse intermediate unit, determining their position in plan by berth and by mounting gap between installed and previously installed units .
Installation of blocks-cushions of tape foundations is carried out by "on weight" method of tower crane moving along rail tracks and located on surface of section outside upper edge of pit.
After laying of whole row of blocks-cushions of tape foundations, correctness of their position relative to laying axes is checked with the help of theodolite or plumb from laying axes stretched on cover, applying hairlines corresponding to axes to lighthouse corner and intermediate blocks.
Subsequent rows of tape foundations or basement walls are mounted from wall blocks on mortar with careful filling of horizontal and vertical seams. Vertical seams in rows of blocks adjacent in height are tied to not less than height of block at weak soils and to not less than 0.4 height of block at low compressible soils. At points of adjoining transverse steps to longitudinal steps, adjoining seams are tied to each row with welding reinforcement walls laid in horizontal seams.
Design position of these units is determined by risks applied on lighthouse corner and intermediate pillow blocks. After determining the position of the lighthouse wall blocks, they are fixed by hairlines on the pillow blocks and from these hairlines with the help of roulette, the position of the intermediate blocks is divided along all foundation blades (by vertical seams), performing this breakdown according to the working drawings of the foundation blocks layout.
After splitting, beacon blocks are carefully laid on the mortar layer. Then, on these blocks, the berth is reinforced along it and all intermediate wall blocks are laid along the laying risks applied on the pillow blocks.
After laying of the last row of blocks, correctness of their position relative to laying axes is checked with the help of theodolite or plumb, as well as leveling of the surface of the upper row of blocks is performed. Installation of tape foundations is carried out as follows: the foundation axes are divided by transferring the axes of the building to the base.
The construction of the monolithic foundation begins with the installation of the formwork (it must be rigid and stable). Then prepared concrete is poured into formwork and held until design strength is set, then formwork is disassembled. The monolithic foundation is widely used in low-rise construction. Installation is carried out by means of the MKA16 crane.
Above ground cycle
Wall masonry
External walls of brick buildings 640 mm thick. Bricks are laid in a certain order, which constitutes a certain stitching system. The dressing system is multi-row.
In the designed building, the internal and external walls are made of brick with dimensions of 250x120x65 mm. Thickness of internal walls 380 mm, external 640mm.
In the internal walls separating kitchens and living rooms, as well as in sanitary units, ventilation channels measuring 140x140 mm are provided. Reinforce wall sections in places of ventilation channels with two longitudinal rods Ø5 Bp I with welding of transverse rods with spacing of 100 mm, bypassing holes of ventilation channels.
How walls are anchored to coordination axes:
internal walls - the central 190х190 mm;
external walls - modular 200x440 mm.
Above the openings in the walls are lintels. Lintels shall be laid on brick walls along the layer of M50 cement mortar.
Partitions.
Partitions are vertical elements that separate adjacent spaces.
Partitions are designed from ceramic bricks 120 mm thick.
Brick partition is fixed in 1.5 m along the length, plugs are installed into seats pre-drilled in the floor, to which mounting elements are fixed by means of nails. Mounting elements are fixed by anchor bolts passed through drilled holes in floor slabs or into seams between them. The last three rows of masonry of the top of the partition are reinforced along the entire length. Places of conjugation of partitions with overlaps after seaming are glued with fabric strip.
The brick partition adjoins the wall with the help of horns clogged in antiseptic wooden plugs or masonry seams.
Vertically, the partitions are fixed in three levels at a distance of 750 mm from the floor to the ceiling.
Inter-apartment partition is made of two-layer panels of gypsum board with thickness of 80mm with clearance of 50mm.
Installation of slabs and coverings.
Prefabricated reinforced concrete slabs of 220 mm thick multi-pillar slabs are designed in the building.
Seams between slabs and walls shall be sealed with concrete of class B15 on fine aggregate.
Slabs are supported on bearing walls by layer of M100 cement mortar. Holes for passage of plumbing pipes can be drilled in place in slab slabs; holes must fall into the voids of the slabs without rear reinforcement; the dimensions of the holes are not more than 150x150 mm.
Anchor connections shall be made of round reinforcement steel. Before sealing in brickwork, tighten the anchors to the lifting loops and weld them to them. After installation, bend the mounting loops and cover with a 30 mm thick layer of cement sand to protect against corrosion. Anchors shall be installed in a chain through the entire building in each third plate.
All types of prefabricated flat floor elements and coatings are mounted in a "canopy" manner. When installing floors and coatings of multi-storey buildings, special layout of elements is not required. The elements are stacked in the warehouse in the crane area. Depending on the size of the slab elements and the number of places where they are captured, a four-branch sling is used as sling devices. Following laying of slab elements of coating floors, all support fixtures are set and welded, followed by their sealing with concrete or solution mixture. The first slabs of the interstage floor panels are laid from floor scaffolding. Subsequent plate elements are laid directly from previously laid elements. In the covers of multi-storey buildings, one of the extreme slabs is laid first, for which scaffolding is used. Subsequent slabs are laid with previously laid one. Extreme plates of coatings are laid with fencing structures attached to them.
Installation of stair elements.
The staircase is a structural device for communication between floors, consisting of marches and platforms.
Stairs from prefabricated reinforced concrete staircases are designed in the building. Width of steps 300mm, height - 150 mm
The entrance porch is made of monolithic concrete with a size of 4200x2000 mm.
The designed exit to the roof is carried out by a metal staircase 600 mm wide.
Stairways are mounted similar to slab elements of floors of multi-storey buildings. They are stroked with a four-branch sling. Stairways are also mounted in a similar manner to plate elements. The difference is that they are raised in a flat position and the slope is slightly higher than their slope in the design position. This is necessary in order to first rest them on the landing of the lower end of the march, and then lower the upper end on the support. Before laying the march with a template, the correct laying of the site is checked.
Roof.
The building has a gable roof with wooden rafters. The ventilation blocks of the underlying floors are completed with caps in the roof space and intersect the coating.
Coating composition:
Water from the roof is drained by four water intake funnels of the internal drainage.
The roof has a lattice fence 60cm high
Roofing works.
Installation of the metal mill begins with careful preparation for work. First of all, the exact need for material is calculated and, of course, they are based on the size of the roof. They need to be measured as carefully as possible. Cutting the material into the necessary fragments is done by an angular grinding machine, but without an abrasive wheel - it damage the tiles too easily. The former roofing cake is supposed to be removed without residue, because the rafters are not designed for two coatings at once; in this, preparation for laying as a whole ends, except for tools and materials.
Filling openings.
Window and door blocks in buildings are installed before the start of finishing work. But for the period of finishing work, door webs are removed. Window and door blocks are installed in openings during the construction of walls, using installation mechanisms available on the object for this purpose. Work on filling the openings is carried out by a team of working carpenters. Glazing of window and door openings is also carried out before the start of finishing work inside the buildings. Window glass with a thickness of 3 mm is used, glass is cut in workshops (i.e. in any room of the building) equipped with special tables, template rulers, glass is cut with glass cuts. Doorways are glazed by fixing glass with staples on a putty. Before putting in place, the glass is coated with putty, inserted into the binding folds and pressed. The inserted glass is soaked on the folds, after which it is fixed with screws or wire studs. A gap of 1.5-2 mm is left between the edge of the glass and the flange side. Studs are clogged manually or with a special device .
Windows and doors.
Window - Translucent fence used for natural lighting and ventilation.
Doors-A guardrail used to communicate between spaces.
The size of the windows is 1/8 - 1/5 of the floor area of the room.
Windows designed with double glazing with separate binding
In total, there are 3 types of windows and 7 types of doors.
Dimensions of windows and doors are specified in the opening list.
Finishing cycle
Plaster works.
Plastering of surfaces during the construction of an object is carried out by a flow-dissected method, which is based on the breakdown of processes into separate operations performed by specialized units that make up a complex team. The links, their number, composition and scope of work are selected so that the rhythmic transition of workers from one grip to another is ensured and all work is carried out in a continuous flow. At the same time, plaster work in the building is carried out "from top to bottom," since plaster work begins after the construction of the building is completed .
When erecting the volume for plastering, a team of plastering workers consisting of 5 people is occupied, which are distributed according to the work being performed, as follows: 1 worker applies spray, 2 workers apply cover with rubbing of the surface with a half-cloth, 1 worker performs surface rubbing, 1 person ensures continuous operation of the plaster station. In total, five teams of five people work.
Floor arrangement.
The building has 2 types of floors: ceramic tiles (in bathrooms), linoleum (in kitchens and in corridors. Before arrangement of ceramic tile floors, base is cleaned from building debris and washed with water. Cement sand mortar 20 mm is used as bracing. After preparation of the base, lighthouse tiles are laid, then frieze rows. Then the background is laid, i.e. the tiles of the inner frieze and the last wall rows, the level surface of the floor is marked from the door. The construction of floors from ceramic tiles is carried out by a team of 4 people, linoleum - of 10 people. Work should begin after the completion of work on previous grips when preparing the floors during the course of work.
Painting works.
For painting work, a painting station is used. Before starting painting work in the premises, it is necessary to complete all construction work (except for the installation of clean floors), electrical work, sanitary and technical. Before painting, the humidity of plastered and concrete surfaces shall not exceed 8%. Wooden structures, as a rule, come to objects painted at one time. In order to increase the industrialization of finishing work, concrete, railway and other structures should be supplied for construction prepared for painting, for example, paved. To perform painting work at the facility, teams of painter workers consisting of five people were accepted. The organization of the brigade's work was built in-line, i.e. the entire scope of work is divided into grips and molar works are carried out on the grips and on the campaign of the main works, while the brigade is distributed as follows: one person performs crack processing (grinding) and primary priming; two people perform grinding, trellising; two people perform cutting, painting; and termination.
Плита.frw

График.frw

ТЭП.frw

Стройгенплан (курсовой).cdw

Архитектурная часть(2 листа).frw

Стройгенплан.frw

Календарный план(курсовой).cdw

Технология.frw

Similar materials
- 04.11.2022
- 20.08.2014
- 20.08.2014
Free downloading for today
Other materials
- 22.08.2014