Boom lifting winch drive


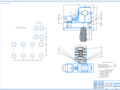
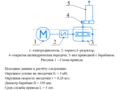
- Added: 23.11.2021
- Size: 1 MB
- Downloads: 0
Description
Course work on the topic: Drive of the boom lifting winch.
Project's Content
![]() ![]() ![]() ![]() |
![]() ![]() ![]() ![]() |
![]() ![]() ![]() ![]() |
![]() ![]() ![]() ![]() |
![]() ![]() ![]() ![]() |
![]() ![]() ![]() |
![]() ![]() ![]() ![]() |
![]() ![]() ![]() |
![]() ![]() ![]() ![]() |
![]() |
Additional information
Contents
1 Energy-kinematic calculation of the drive
2 Worm Gear Calculation
2.1 Transmission Design Calculation
2.2 Check calculation of worm gear
2.3 Thermal calculation of reduction gear box
3 Design calculation of open transmission
3.1 Selection of materials, heat treatment and determination of permissible stresses for gears
3.2 Design calculation of open transmission
3.3 Transmission check calculation
4 Calculation of drive shafts
4.1 Design calculation of all drive shafts
4.2 Check calculation of low-speed shaft for fatigue endurance
5 Selection and calculation of drive bearings
5.1 Preliminary selection of bearings for all shafts and their justification
5.2 Check calculation of low-speed shaft rolling bearings for static and dynamic lifting capacity
Conclusion
List of literature
Conclusion
The purpose of the course design is to design the drive of the boom lifting winch, which consists of both standard parts and parts, the shape and dimensions of which are determined on the basis of design, technological and other standards.
During the course project on "Machine Parts," the knowledge gained over the past period of training in such disciplines as: theory of mechanisms and machines, theoretical mechanics, materials science was fixed. Gearbox and frame were designed and designed.
During the design, special attention was paid to the development of the gearbox and frame.
During the course project, it was clarified:
- electric motor power of not less than 2.2 kW and rotation speed of 590 min-1 is required to obtain the required values on the working tool. On the required power and frequency of rotation electric motor 4A112MA8U3 with a nominal frequency of rotation of 710 min.-1 and 2200 kW was chosen;
- when determining rotation speeds and torques on the drive shafts, it was calculated that the total gear ratio of the reduction gear should be 32 .
- when calculating slow-moving and high-speed transmission, materials for the manufacture of the wheel and gear SCH 20 were selected, as well as heat treatment - improvement;
- number of low-speed gear teeth: on gear z1 = 4, on wheel z2 = 8.
- keys were selected that satisfy all requirements. The main requirement was the strength calculation of the key connection for crushing stress;
- industrial oil I20A, plastic lubricant VNIINP235 for bearing lubrication;
- an explanatory note and design documentation has been developed, including a general view drawing, assembly drawings of drive elements and working drawings of parts according to the task for the course design.
Сборочный чертеж.cdw

Отдушина.cdw

Общий вид (2).cdw

Вал.cdw

Компановка редуктора.cdw

Червяк.cdw

Червячное колесо.cdw
