Организация технологического процесса и разработка электротехнического участка с внедрением работ по установке и ТО car distance detection system на базе СТО



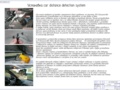
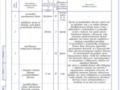
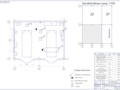
- Добавлен: 10.06.2022
- Размер: 3 MB
- Закачек: 4
Описание
«Организация технологического процесса и разработка электротехнического
участка с внедрением работ по установке и ТО car distancedetection system
на базе СТО»
I. Исходные данные для проектирования СТОА
- Численность населения обслуживаемого района (чел.) ______________14 000__________________
- Среднее число автомобилей на 1000 жителей _______________________520___________________
- Среднегодовой пробег одного автомобиля, км ______________________________16 500____________________
- % владельцев пользующихся услугами СТОА города, % __________________79______________________
- % владельцев пользующихся услугами данного СТОА города, % __________31______________________
- % владельцев автомобилей по маркам, % _________________________________29______________________
- Режим работы СТОА, дней _______________________________5 дн, 8 час., 1 смена____________
- Модификация подвижного состава, модель __________________ Mitsubishi Galant 1,8 GDI AT_________
СОДЕРЖАНИЕ ДИПЛОМНОГО ПРОЕКТА
Пояснительная записка
Введение
1. Исследовательская часть
2. Расчетно-технологическая часть
3. Организационная часть
4. Техника безопасности и охрана окружающей среды
5. Инновационная технология проекта
6. Оценка экономической эффективности проекта
7. Конструкторская часть
8. Заключение
9. Список использованной литературы
II. Конструкторская часть
__ Демонстрационный стенд устройство и работа car distance detection system __________
III. Графическая часть
1 лист ____Планировка участка__________________________________________________
2 лист ____Технологическая карта (схема) производственного процесса________________
3 лист ____Инновационные технологии в проекте___________________________________
Состав проекта
![]() ![]() ![]() ![]() |
![]() ![]() ![]() ![]() |
![]() ![]() ![]() |
![]() ![]() ![]() ![]() |
![]() |
Дополнительная информация
Инновац.cdw

Тех карта.cdw

Круч -план.cdw

Рекомендуемые чертежи
- 13.05.2023
- 01.04.2015
- 24.01.2023
- 22.07.2023
- 29.07.2014