Вертикально-сверлильный станок на базе станка V7 фирмы WEBO с возможностью агрегатной обработки




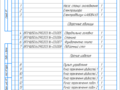
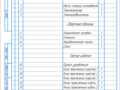
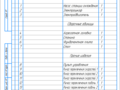
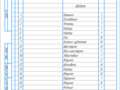
- Добавлен: 25.01.2023
- Размер: 2 MB
- Закачек: 0
Описание
Состав проекта
![]() |
![]() |
![]() ![]() ![]() ![]() |
![]() |
![]() |
![]() ![]() ![]() ![]() |
![]() ![]() ![]() ![]() |
![]() |
![]() ![]() ![]() |
![]() |
![]() ![]() ![]() ![]() |
![]() ![]() ![]() ![]() |
![]() ![]() ![]() ![]() |
![]() |
![]() |
![]() ![]() ![]() ![]() |
![]() |
![]() ![]() ![]() ![]() |
![]() |
![]() ![]() ![]() |
![]() ![]() ![]() ![]() |
![]() ![]() ![]() ![]() |
![]() ![]() ![]() ![]() |
![]() |
![]() |
Дополнительная информация
Общий вид.cdw

Общий вид.cdw

Головка.cdw

Спациф. гл. вид.cdw

Кинематика.cdw

Спецификация на головку.spw

главнай вид.spw

Головка.cdw

Спациф. гл. вид.cdw

Кинематика.cdw

Спецификация на головку.spw

Рекомендуемые чертежи
- 25.01.2023