Станок вертикально-сверлильный с максимальным диаметром сверления 35 мм




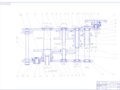
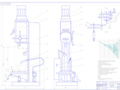
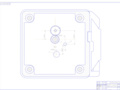
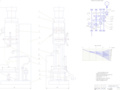
- Добавлен: 25.10.2022
- Размер: 764 KB
- Закачек: 1
Описание
Состав проекта
![]() |
![]() |
![]() ![]() ![]() |
![]() ![]() ![]() ![]() |
![]() ![]() ![]() |
![]() ![]() ![]() |
![]() ![]() ![]() ![]() |
![]() ![]() ![]() ![]() |
![]() ![]() ![]() ![]() |
![]() ![]() ![]() |
![]() |
![]() ![]() ![]() |
Дополнительная информация
ЛИСТ2H135!!!.cdw

Чертеж 1 лист.cdw

Лист 1 - Общий вид станка!!!!!!!!.frw

моя коробка.cdw
