Станок вертикально-сверлильный 2А125




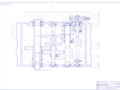
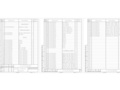
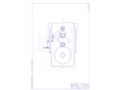
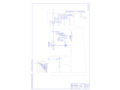
- Добавлен: 25.10.2022
- Размер: 1 MB
- Закачек: 1
Описание
Состав проекта
![]() |
![]() |
![]() ![]() ![]() ![]() |
![]() ![]() ![]() ![]() |
![]() ![]() ![]() ![]() |
![]() ![]() ![]() ![]() |
![]() ![]() |
![]() ![]() |
![]() ![]() |
![]() ![]() |
![]() ![]() ![]() |
Дополнительная информация
1_лист.dwg

3_лист.dwg

2_лист.dwg

31232.dwg

Рекомендуемые чертежи
Свободное скачивание на сегодня
Другие проекты
- 04.11.2022