Технологический процесс механической обработки детали Штуцер




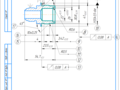
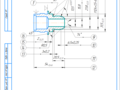
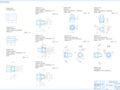
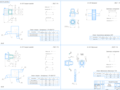
- Добавлен: 24.01.2023
- Размер: 5 MB
- Закачек: 3
Описание
Состав проекта
![]() |
![]() |
![]() ![]() ![]() ![]() |
![]() ![]() ![]() ![]() |
![]() ![]() ![]() ![]() |
![]() |
![]() |
![]() |
![]() |
![]() |
![]() |
![]() |
![]() |
![]() |
![]() |
![]() |
![]() |
![]() |
![]() |
![]() |
![]() |
![]() |
![]() |
![]() |
![]() |
![]() |
![]() |
![]() |
![]() |
![]() |
![]() |
![]() |
![]() |
![]() |
![]() |
![]() |
![]() |
![]() |
![]() |
![]() |
![]() ![]() ![]() ![]() |
![]() ![]() ![]() ![]() |
![]() ![]() ![]() ![]() |
![]() ![]() ![]() ![]() |
![]() ![]() ![]() ![]() |
![]() ![]() ![]() ![]() |
![]() ![]() ![]() ![]() |
![]() ![]() ![]() ![]() |
![]() ![]() ![]() ![]() |
![]() ![]() ![]() ![]() |
![]() ![]() ![]() ![]() |
![]() |
![]() ![]() ![]() ![]() |
![]() |
![]() ![]() ![]() |
Дополнительная информация
Раб.чертеж..cdw

План операций.cdw

Эскиз наладок.cdw

Карта заготовки.cdw

030.cdw

045.cdw

005.cdw

040.cdw

010.cdw

025.cdw

Карта контроля.cdw

015.cdw

035.cdw

020.cdw

ЭСП.размерные цепи0.cdw

Рекомендуемые чертежи
- 07.09.2016
- 02.05.2022
- 04.11.2022