Технологический процесс механической обработки детали колесо зубчатое 05-1701216 с экономическим обоснованием технологического процесса




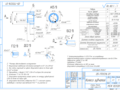
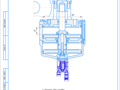
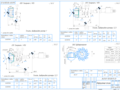
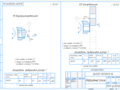
- Добавлен: 24.01.2023
- Размер: 6 MB
- Закачек: 2
Описание
Состав проекта
![]() |
![]() |
![]() ![]() ![]() |
![]() ![]() ![]() |
![]() ![]() ![]() ![]() |
![]() ![]() ![]() ![]() |
![]() ![]() ![]() ![]() |
![]() |
![]() ![]() ![]() |
![]() ![]() ![]() |
![]() ![]() ![]() |
![]() ![]() ![]() |
![]() ![]() ![]() |
![]() ![]() ![]() |
![]() ![]() ![]() |
![]() ![]() ![]() |
![]() ![]() ![]() |
![]() ![]() ![]() |
![]() ![]() ![]() |
![]() ![]() ![]() |
![]() ![]() ![]() |
![]() ![]() ![]() |
![]() ![]() ![]() ![]() |
![]() ![]() ![]() ![]() |
![]() ![]() ![]() ![]() |
Дополнительная информация
титульник.doc
Белорусский национальный технический университет
МАШИНОСТРОИТЕЛЬНЫЙ ФАКУЛЬТЕТ
Кафедра "Технология машиностроения
Проектирование технологических процессов механической обработки
на тему: «Технологический процесс механической обработки детали – колесо зубчатое -1701216 с экономическим обоснованием технологического процесса»
студент гр. 103128 Севбо А.Е.
Руководитель проекта Беляев Г.Я.
HoLdeN(готово).docx
Выбор типа и формы организации производства7
Анализ технологичности конструкции детали11
Выбор способа получения заготовки с экономическим обоснованием13
Анализ заводского техпроцесса составление маршрута обработки14
Размерный анализ техпроцессов25
Расчет режимов резания32
Нормирование техпроцессов38
Определение потребного количества станков и построение графиков загрузки39
Расчет и проектирование приспособления41
Техникоэкономические расчеты44
Составление карты кодирования информации (фрагмент)47
В данном курсовом проекте мы рассмотрим технологический процесс изготовления детали «Зубчатое колесо 05-1701216». Анализируем заводской технологический процесс выберем способ получения заготовки детали «Зубчатое колесо 05-1701216». Также мы рассчитаем силу зажима и точность зубофрезерного приспособления. Определим потребное количество станков и составим график их загрузки.
Прохождение практики на заводе является важным этапом изучения технологии машиностроительных производств а также различных методов получения заготовок и обработки деталей так как позволяет воочию увидеть уже внедрённое оборудование и убедиться в соответствии изученных в теории методов и приёмов обработки применяемым на практике. Практика даёт возможность расширить и закрепить полученные в учебном заведении знания об организации различных типов производств о расчётах проектировании и методах внедрения всевозможных типов оборудования приспособлений и инструмента. Целью практики является также изучение конкретного технологического процесса и нахождение возможностей его усовершенствования с точки зрения экономии времени энергии оборудования и материалов с экономическим обоснованием. Это позволяет повышать эффективность производства и обуславливает его технический прогресс .
Основными задачами и перспективами развития машиностроительной отрасли является уменьшение времени на изготовление деталей изделий сборочных единиц и повышение производительности труда. Это достигается путём сокращения номенклатуры применяемого универсального оборудования путем внедрения различных высокопроизводительных автоматизированных и автоматических в основном многошпиндельных станков и как следствие уменьшения количества операций обработки. Преимущество должно отдаваться совмещению различных переходов на одном станке что также позволит сократить время на обработку.
Минский завод шестерен одно из крупнейших предприятий по производству шестерен в Республике Беларусь и странах СНГ. Основным направлением деятельности предприятия является производство шестерен для промышленных предприятий РБ производство запасных частей к тракторам «Беларус» Минского тракторного завода ЮМЗ САЗ К-700 ДТ-75 и др. На предприятии освоен полный технологический цикл производства шестерен на предприятии имеется собственное заготовительное кузнечно-штамповое инструментальное химико-термическое и обрабатывающее производства.
ПРУП «Минский завод шестерен» входит в производственное объединение «Минский тракторный завод» и является одним из крупнейших поставщиков комплектующих запасных частей для тракторов на конвейер МТЗ. В условиях роста спроса на белорусские трактора важно обеспечить качественное техническое обслуживание и ремонт поэтому большинство организаций эксплуатирующих отечественную технику приобретают оригинальные запасные части производства Минского завода шестерен.
Благодаря огромному инженерно-техническому потенциалу на предприятии освоен выпуск тракторных плугов. Модельный ряд тракторных плугов включает пропашные плуги оборотные навесные и полунавесные плуги для гладкой пахоты плуги с рессорной защитой для каменистых почв. Вся гамма тракторных плугов производства Минского завода шестерен положительно зарекомендовала себя на полях Республики Беларусь странах СНГ и дальнего зарубежья
Назначение детали и принцип работы в узле
Колесо зубчатое 05-1701216 входит в коробку передач мотоблока Беларус-09Н09Н-02. Мотоблок предназначен для выполнения пахоты легких почв боронования культивации междурядной обработки картофеля и свеклы кошения трав в садах и огородах на пришкольных и приусадебных участках а также для транспортирования грузов стационарных работ с приводом от вала отбора мощности.
Рисунок 1.1 – Коробка передач мотоблока Беларус-09Н09Н-02
Муфта сцепления – многодисковая работающая в масле с ручным управлением.
Коробка перемены передач – ступенчатая механическая с постоянным зацеплением шестерен. Главная передача – конические шестерни со спиральным зубом.
Дифференциал – шестеренчатый конический с принудительной блокировкой.
Конечные передачи – одноступенчатые с цилиндрическими шестернями.
Ходовая система – колесная формула 2х2. Колеса мотоблока с пневматическими шинами 6L-12 Давление воздуха в шинах в зависимости от нагрузки 0.08-0.12 МПа.
Управление подачей топлива – рычагом с тросовым приводом.
Управление валом отбора мощности – рычагом на корпусе трансмиссии.
Управление блокировкой дифференциала – рычагом через систему тяг.
Рулевое управление – штанговое регулируемое по высоте и в горизонтальной плоскости с возможностью переналадки на реверсивное положение влево или вправо на угол 150.
Тормозная система – агрегат из мотоблока и прицепа( тормоза установлены на прицепе) оборудован тормозами с возможностью торможения агрегата в движении и на стоянке.
Вал отбора мощности с частотой вращения( при номинальной частоте вращения коленчатого вала) – 1200 обмин.
Прицепное устройство – скоба со шкворнем сцепка трубчатой формы.
Высота присоединительного места – 3695мм.
Деталь «зубчатое колесо 05-1701216» изготавливается из стали марки 18ХГТ ГОСТ 4543-71. Это конструкционная легированная сталь. Применяется в улучшаемых или цементуемых деталях ответственного назначения от которых требуется повышенная прочность и вязкость сердцевины а также высокая поверхностная твердость работающие под действием ударных нагрузок.
Таблица 1.1 - Химический состав стали 18ХГТ
Никель (Ni) не более
Таблица 1.2 – механические свойства стали 18ХГТ при Т=200С
Закалка 8500С масло отпуск 2000С воздух
Твердость 18ХГТ после отжига ГОСТ 4543-71 - HB 10-1 = 217 МПа;
Твердость 18ХГТ нагартованного ГОСТ 4543-71 HB 10-1 = 229 МПа;
Sв - Предел кратковременной прочности [МПа];
ST - Предел пропорциональности (предел текучести для остаточной деформации) [МПа];
d5 - Относительное удлинение при разрыве [ % ];
y - Относительное сужение [ % ] ;
KCU - Ударная вязкость [ кДж м2] ;
HB - Твердость по Бринеллю [МПа];
Технологические свойства стали 18ХГТ:
-Свариваемость: без ограничений т.е. сварка производится без подогрева и без последующей термообработки;
-Флокеночувствительность: не чувствительная;
-Склонность к отпускной хрупкости: малосклонна.
Таблица 1.3. – Характеристика сталей 18ХГТ и 25ХГТ
ХГТ 25ХГТ 12ХН3А 12Х2Н4А 20ХН2М 14ХГСН2МА 20ХГР
Сталь конструкционная легированная
Сталь хромомарганцовая
Продукция предлагаемая предприятиями-рекламодателями: Нет данных.
Улучшаемые или цементуемые детали ответственного назначения от которых требуется повышенная прочность и вязкость сердцевины а также высокая поверхностная твердость работающие под действием ударных нагрузок.
нагруженные зубчатые колеса и другие детали твердость которых более НRСэ 59. (Круг квадрат шестигранник полоса поковки и кованые заготовки)
Таблица 1.4 - Механические свойства при Т=20oС материала сталь 25ХГТ.
Нормализация 880-895oC воздух Закалка 850oC масло Отпуск 200oC вода
Твердость материала 25ХГТ после отжига
Таблица 1.5. - Технологические свойства материала сталь 25ХГТ.
Флокеночувствительность:
Склонность к отпускной хрупкости:
Механические свойства:
- Предел кратковременной прочности [МПа]
- Предел пропорциональности (предел текучести для остаточной деформации) [МПа]
- Относительное удлинение при разрыве [ % ]
- Относительное сужение [ % ]
- Ударная вязкость [ кДж м2]
- Твердость по Бринеллю
- сварка производится без подогрева и без последующей термообработки
ограниченно свариваемая
- сварка возможна при подогреве до 100-120 град. и последующей термообработке
- для получения качественных сварных соединений требуются дополнительные операции: подогрев до 200-300 град. при сварке термообработка после сварки - отжиг
Т.к. сталь 18ХГТ и 25ХГТ схожи по своим свойствам и 25ХГТ является одним из заменителей стали 18ХГТ то для изготовления «зубчатого колеса 05-1701216» выбираем сталь 25ХГТ.
Выбор типа и формы организации производства
Тип производства – классификационная категория производства выделяемая по признакам широты номенклатуры регулярности стабильности и объема выпуска изделий. В машиностроении различают 5 типов производства: массовые крупносерийные среднесерийные мелкосерийные и единичные в зависимости от Кз.о.(коэффициент закрепления операций)
ΣРi – явочное число рабочих участка выполняющих различные операции при работе в одну смену.
Таблица 1.3 – Тип производства
Таблица 1.4 – Тип производства
Количество обрабатываемых деталей одного наименования и типоразмера
Крупных тяжелых большой трудоемкости массой св. 30кг
Средних размеров и трудоемкости массой 8-30 кг
Небольших легких малотрудоемких массой до 8кг
Исходя из таблицы 1.4 колесо зубчатое 05-1701216 относится к крупносерийному производству.
н – планируемый нормативный коэффициент загрузки станка всеми закрепленными за ним однотипными операциями. (н = 0.7 для крупносерийного производства).
з – коэффициент загрузки станка проектируемой операцией.
Nм=Nг24=3000024=1250 шт.
ΣПоi=13182*071250(108+1253+1143+1072+1409+112+1061+1333+1027+1441+1152)= 738*(125+0395+0699+1389+0244+083+1639+0300+073+0227+0658)=617
ΣРi=11*(096* н)=11*096*07=7392
Т.к. 1Кз.о.10 значит производство крупносерийное.
Методы упрочняющей технологии
Поверхность зубчатого колеса 05-1701216 улучшается с помощью химико-термической обработки.
Химико-термическая обработка (ХТО) стали - совокупность операций термической обработки с насыщением поверхности изделия различными элементами (углерод азот алюминий кремний хром и др.) при высоких температурах.
Поверхностное насыщение стали металлами (хром алюминий кремний и др.) образующими с железом твердые растворы замещения более энергоемко и длительнее чем насыщение азотом и углеродом образующими с железом твердые растворы внедрения. При этом диффузия элементов легче протекает в решетке альфа-железо чем в более плотноупакованной решетке гамма-железо.
Химико-термическая обработка повышает твердость износостойкость кавитационную коррозионную стойкость. Химико-термическая обработка создавая на поверхности изделий благоприятные остаточные напряжения сжатия увеличивает надежность долговечность.
Цементация стали - химико-термическая обработка поверхностным насыщением малоуглеродистой (С02%) или легированных сталей при температурах 900 950°С - твердым (цементация твердым карбюризатором) а при 850 900°С - газообразным (газовая цементация) углеродом с последующей закалкой и отпуском. Цель цементации и последующей термической обработки - повышение твердости износостойкости также повышением пределов контактной выносливости поверхности изделия при вязкой сердцевине что обеспечивает выносливость изделия в целом при изгибе и кручении.
Детали предназначенные для цементации сначала очищают. Поверхности не подлежащие науглероживанию покрывают специальными предохранительными противоцементными обмазками.
-ый состав простейшей обмазки: огнеупорная глина с добавлением 10% асбестового порошка вода. Смесь разводят до консистенции густой сметаны и наносят на нужные участки поверхности изделия. После высыхания обмазки можно производить дальнейшую цементацию изделия.
-ой состав применяемой обмазки: каолин - 25% тальк - 50%: вода - 25%. Разводят эту смесь жидким стеклом или силикатным клеем.
Цементацию делают после полного высыхания обмазки.
Вещества которые входят в состав обмазки называют карбюризаторами. Они бывают твердые жидкие и газообразные.
В условиях домашней небольшой мастерской удобнее осуществлять цементацию с помощью пасты. Это цементация в твердом карбюризаторе. В состав пасты входят: сажа - 55% кальцинированная сода - 30% щавелевокислый натрий - 15% вода для образования сметанообразной массы. Пасту наносят на нужные участки изделия дают высохнуть. Затем изделие помещают в печь выдерживая при температуре 900-920°С в течение 2-25 часов. При использовании такой пасты цементация обеспечивает толщину науглероженного слоя 07-08 мм.
Жидкостная цементация также возможна в небольшой мастерской при наличии печи-ванной в которой и происходит науглероживание инструментов и других изделий. В состав жидкости входят: сода - 75-85% 10-15% хлористого натрия 6-10% карбида кремния. Печь-ванну наполняют этим составом и погружают изделие или инструмент. Процесс протекает при температуре 850-860°С в течение 15-2 часов; толщина науглероженного слоя достигает при этом 03-04 мм.
Газовую цементацию производят в смеси раскаленных газов содержащих метан окись углерода в специальных камерах при температуре 900-950°С и только в производственных условиях. После цементации детали охлаждают вместе с печью затем закаляют при 760-780°С е окончательным охлаждением в масле.
Азотирование стали - химико-термическая обработка поверхностным насыщением стали азотом путем длительной выдержки ее при нагреве до б00 650°С в атмосфере аммиака NН3. Азотированные стали обладают очень высокой твердостью (азот образует различные соединения с железом алюминием хромом и другими элементами обладающие большей твердостью чем карбиды). Азотированные стали обладают повышенной сопротивляемостью коррозии в таких средах как атмосфера вода пар.
Азотированные стали сохраняют высокую твердость в отличие от цементованных до сравнительно высоких температур (500 520°С). Азотированные изделия не коробятся при охлаждении так как температура азотирования ниже чем цементации. Азотирование сталей широко применяют в машиностроении для повышения твердости износостойкости предела выносливости и коррозионной стойкости ответственных деталей например зубчатых колес валов гильз цилиндров.
Нитроцементация (цианирование) стали - химико-термическая обработка с одновременным поверхностным насыщением изделий азотом и углеродом при повышенных температурах с последующими закалкой и отпуском для повышения износо- и коррозионной устойчивости а также усталостной прочности. Нитроцементация может проводиться в газовой среде при температуре 840..860°С - нитроцианирование в жидкой среде - при температуре 820 950°С - жидкостное цианирование в расплавленных солях содержащих группу NaCN.
Нитроцементация эффективна для инструментальных (в частности быстрорежущих) сталей; она используется для деталей сложной конфигурации склонных к короблению. Однако поскольку этот процесс связан с использованием токсичных цианистых солей он не нашел широкого распространения.
Борирование стали - химико-термическая обработка насыщением поверхностных слоев стальных изделий бором при температурах 900 950°С. Цель борирования - повышение твердости износостойкости и некоторых других свойств стальных изделий. Диффузионный слой толщиной 005 015 мм состоящий из боридов FeB и Fе2В обладает весьма высокой твердостью стойкостью к абразивному изнашиванию и коррозионной стойкостью. Борирование особенно эффективно для повышения стойкости (в 2 10 раз) бурового и штампового инструментов.
Цинкование (Zn) алюминирование (Аl) хромирование (Сr) силицирование (Si) сталей выполняются аналогично цементации с целью придания изделиям из стали некоторых ценных свойств: жаростойкости износостойкости коррозионной устойчивости. В настоящее время все большее распространение получают процессы многокомпонентного диффузионного насыщения.
Характеристики зубчатого колеса 05-1701216 до и после ХТО:
Твердость детали до ХТО – НВ156..225
Предельные отклонения ИМР:а)до ХТО Ea’’s=-0.01;Ea’’б)после ХТО Ea’’s=+0.036; Ea’’i=-0.2.
Допуск на колебание ИМР за оборот зколеса Fi’’ и на одном зубе fi’’:
а) до ХТО F f б) после ХТО F fi’’=0.036
Диаметр отверстия: а) до ХТО d=23.6+0.033; б)после ХТО d=23.6±0.05.
Наружный диаметр и расположение выкружек по комплексному калибру:
а) до ХТО d=27.07+0.052; б) после ХТО d=27+0.21.
Анализ технологичности конструкции детали
Технологический анализ конструкции обеспечивает улучшение технико-экономических показателей разрабатываемого технологического процесса. Поэтому технологический анализ – один из важнейших этапов технологической обработки. Основные задачи решаемые при анализе технологичности конструкции обрабатываемой детали сводятся к возможному улучшению трудоемкости и металлоемкости возможности обработки детали высокопроизводительными методами. Таким образом улучшение технологичности конструкции позволяет снизить себестоимость ее изготовления повысить производительность труда и сократить время на изготовление изделия при обеспечении необходимого его качества.
Оценка технологичности конструкции может быть двух видов:
Качественная оценка характеризует технологичность конструкции обобщенно на основании опыта исполнителя и допускается на всех стадиях проектирования как предварительная.
Количественная оценка технологичности изделия выражается числовыми показателями и оправдана в том случае если они существенно влияют на технологичность рассматриваемой конструкции.
Качественная оценка технологичности
Сталь 18ХГТ обладает хорошей обрабатываемостью резанием и имеет не высокую себестоимость.
Деталь имеет поверхности обработку которых можно производить стандартным инструментом присутствуют не обрабатываемые резанием поверхности. Обрабатываемые поверхности простой формы. Но присутствуют поверхности требующие применения сложного и специального инструмента.
Анализируя простановку размеров на чертеже необходимо заметить что предельные отклонения размеров определяющих нерабочие поверхности имеют более широкие поля допусков и большую шероховатость чем размеры рабочих поверхностей что не требует увеличения трудоемкости при изготовлении данной детали.
К положительным моментам можно отнести наличие не обрабатываемых поверхностей невысокие показатели шероховатости не высокую себестоимость материала и простоту формы большинства элементов детали. Это хорошо влияет на процесс получения детали.
Количественная оценка технологичности
Она может быть осуществлена только при использовании соответствующих базовых показателей технологичности. Поэтому необходимо определить основные и дополнительные показатели.
При оценке технологичности используются следующие показатели:
Основные показатели: 1) Технологическая себестоимость детали: Ст=78747 руб.; 2) Трудоемкость изготовления детали: Ти=4160=07 ч.
Дополнительные показатели:
)Коэффициент унификации конструктивных элементов:
где Q у э и Q э - соответственно число унифицированных конструктивных элементов детали и общее шт;
)Коэффициент применяемости стандартизованных обрабатываемых поверхностей:
где Do.c Dм.о - соответственно число поверхностей детали обрабатываемых стандартным инструментом и всех подвергаемых механической обработке поверхностей шт.
)Коэффициент обработки поверхностей: Кп.о= 1 – Dм.о Dэ ;
где DЭ – общее число поверхностей детали шт.
Кп.о= 1 – 1214 = 0143;
)Коэффициент использования материала:
где q Q – масса детали и заготовки соответственно кг.
) Коэффициент применения типовых технологических процессов при изготовлении данной детали : Kт.п.=Qт.п.Qп;
где Qт.п. и Qн – соответственно число типовых техпроцессов для изготовления детали и общее шт.;
) Максимальное значение квалитета обработки IT - 9;
)Максимальное значение параметра шероховатости обрабатываемых поверхностей Rz -80(Ra 20).
Масса детали равна 01 кг;
) Уровень технологичности конструкции по технологической себестоимости:
Кус = СтСб.т. где Ст. Сб.т. – соответственно достигнутая и базовая себестоимость изделия.
Кус = 7874779300=099
Проанализировав количественные показатели технологичности для данной детали следует сказать что к отрицательным показателям характеризующим деталь относятся: коэффициент унификации конструктивных элементов – деталь в основном технологична
Выбор способа получения заготовки с экономическим обоснованием
В настоящее время на заводе в виде заготовки для детали «Колесо зубчатое» 05-1701216 используется поковка на ГКМ. Материал заготовки сталь 18ХГТ.
Сравним два метода получения заготовок:
Таблица 2.1 – сравнительный анализ двух методов получения заготовок
Стоимость 1кг заготовок принятых за базу Si
Стоимость 1кг стружки Sотх
Vзаг=(314*46524) *175+(314*35524)*85=29704+8290=37994 мм3
Sзаг=(Qkтkckвkмkп)-(Q-q)
Q – масса заготовки кг; Q1=0.3кг Q2=0.258кг;
q – масса детали кг; q=0.1 кг;
Sотх – стоимость 1кг отходов руб.; Sотх=300руб.;
kт – коэффициент зависящий от класса точности заготовок (IV); kт=1;
kc – коэффициент зависящий от группы сложности заготовки (2й); kc=084;
kв – коэффициент зависящий от массы заготовки; kв=087;
kм – коэффициент зависящий от марки материала заготовки; kм=1;
kп – коэффициент зависящий от объема производства заготовок; kп=1;
Sзаг1=(300003108408711)-(0.3-0.1)300 =5977руб;
Sзаг2 =(30000.258108508711)-(0.258-0.1)300=524.9руб.;
Экономический эффект от внедрения нового метода получения заготовки:
Эз=(5977 -5249)30000=2184000руб.
Это говорит о том что выбранный метод более эффективен.
Анализ заводского техпроцесса составление маршрута обработки
Анализ техпроцесса проводится с точки обеспечения заданного качества изделия и производительности обработки. Содержание и степень углубленности анализа зависят от различных факторов: конструкции изделия применяемых методов его обработки реальных производственных условий. В общем случае анализ техпроцесса должен включать в себя следующие основные вопросы:
) Рациональность метода получения заготовки для данного масштаба производства метод получения заготовки;
) Метод упрочнения детали и соответствие их ее функциональному назначению и условиям эксплуатации машин;
) Станочное оборудование и рациональность его использования;
) Концентрация и дифференциация обработки как средство повышения производительности;
) Автоматизация техпроцесса;
) Базирование заготовок при обработке и определение погрешностей базирования;
) Брак при обработке и причины его возникновения;
) Степень оснащенности операций и др.
Технологический процесс Зубчатого Колеса 05-1701216 состоит из следующих операций:
5 Токарная на станке модели 16К20;
0 Токарная с ЧПУ на станке модели 16А20Ф3;
5 Токарная с ЧПУ на станке модели 16А20Ф3;
0 Вертикальнопротяжная на станке модели МП141Н15;
0 Зубофрезерная на станке модели BO-07;
5 Зубозакругляющая на станке модели 5Н580;
0 Зубофасочная на станке модели 5525;
0 Зубошевинговальная на станке модели 5702B;
5 Внутришлифовальная на станке модели 3К228;
0 Шлифовальная на станке модели 3Б1531;
Годовая программа выпуска Зубчатых Колес 05-1701216 30000в год. Производство – массовое.
Предметом анализа является технологический процесс изготовления Колеса Зубчатого 05-1701216.
Таблица 5.1 – Технологические возможности применяемого оборудования.
Предельные или наибольшие размеры обрабатываемой зоготовки мм
Технологические возможности метода обработки
Шереховатость обрабатываемой поверхности
Операции 005-015 заменим на многооперационный станок 16А90МФ4.
Рисунок 5.1. - Токарный многооперационный станок 16А90МФ4
На станке можно выполнять токарную обработку заготовок типа валов устанавливаемых в патроне с опорой на задний центр 5 или в центрах. В этом случае с помощью инструментов закрепляемых в шпинделе 4 возможно обрабатывать шпоночные канавки пазы отверстия и другие элементы расположенные вдоль вала или на его образующей.
И для удаления стружки служат скребковый конвейер 7 и тележка 6. Токарный многооперационный станок 16А90МФ4 по компоновке близок к МС для корпусных заготовок. Заготовки типа тел вращения диаметром до 250 мм и длиной до 100 мм массой до 200 к г . устанавливают в четырехкулачковый патрон 3 получающий вращение от шпинделя смонтированного в бабке 2. Бабка установлена на салазках 1. Кроме непрерывного вращения шпиндель заготовки может совершать медленную круговую подачу нужную при обработке например криволинейных пазов.
Инструментальный шпиндель Ш куда автоматически подаются инструменты из магазина емкостью 32смонтирован в корпусе шпиндельной бабки ШБ перемещающемся вместе с салазками 5 вверх- вниз по стойке 4 (ось Y ) горизонтально вместе со стойкой (ось Z ) и дополнительно на салазках (ось W ). Благодаря наличию еще одного инструментального шпинделя и достаточно широкому диапазону частоты вращения инструментальных (10 — 2000 обмин) шпинделей и шпинделя заготовки (63- 3800 обмин) на станке можно выполнить все виды токарной обработки включая резьбонарезание сверлильные фрезерные работы для поверхностей соосных параллельных и перпендикулярных оси заготовки. Существуют многооперационные специализированные станки предназначенные для обработки заготовок каких-либо типичных по конфигурации и размерам деталей в авиастроении турбостроении и других отраслях производства.
Таблица 5.2 – Технологическая характеристика применяемого оборудования
Год изготовления станка
Категория ремонтной сложности
Количество станков на операции
Коэффициент загрузки станка
Таблица 5.3 – режущие инструменты
название инструмента
Материал режущей части
Метод настройки на размер
Таблица 5.4 – Характеристика вспомогательных инструментов
Наименование инструмента
Установка режущего инструмента во вспомогательный
Время на смену одного инструмента
Пневмомашина ИП 2014
Оправка для фрезы 6224-5074
Приспособление для замены фрез 8539-5033
Цанга для фрезы 6112-5045
Продолжение таблицы 5.4
Оправка для круга 6284-5015
Приспособление для зачистки заусенцев 7569-5160
Оправка для круга при станке
Оправка для правки круга 6289-5040
Пневмомашина НП 2014
Тиски 7827-0254 ГОСТ 4045-75
Таблица 5.5 – Установочно-зажимные приспособления
Название приспособления
Привод приспособления
Количество приспособлений
Время на установку и снятие заготовки мин
патрон вспомогательный
пневмоцилиндр ЦВ-150
пневмомашина НП 2014
Управление циклом обработки
Способ загрузки заготовок
Вид межоперационного транспорта
Комплексная неполная
Таблица 5.6 – Характеристика механизации и автоматизации технологического процесса
Таблица 5.7 – Средства технического контроля зубчатого колеса 05-1701216
Наименование инструмента
Точность измерениямм
Допуск на измеремый размермм
Время на измерение мин
штангенциркуль ШЦЦ-I-200 0.01 цифровой
ШЦ-2-250-005 ГОСТ 166
Плита 2-2-250х250 ГОСТ 10905
калибр комплексный 8311-5208-01
оправка контрольная 8031-5310-01
втулка для контролир. колеса
ШЦ-1-125-0.1 ГОСТ 166
ШЦ-1-125-01 ГОСТ 166
Контрольный прибор МЦ-400Б
Втулка для контрольного колеса 8029-5528-01
контрольный прибор МЦ-400Б
Базирование заготовок при обработке
Рисунок 5.1 – эскиз детали зубчатого колеса
Таблица 5.8 – Базирование заготовок при обработке
№ и назначение операции
Выдерживание размеров
Номера поверхностей баз
0 Вертикальнопротяжная
0 Зубошевинговальная
5 Внутришлифовальная
На всех операциях механической обработки схемы базирования выбраны так что измерительные базы совпадают с технологическими поэтому погрешность базирования на всех операциях равна нулю.
Суммарное значение пространственных отклонений поверхности заготовки:
где - погрешность смещения штампованных заготовок;
– погрешность штампованных заготовок по эксцентричности
Погрешность установки заготовки на выполняемой операции
где - погрешность соответственно базирования закрепления положения заготовки.
Табл. 6.1 – расчет припусков и предельных размеров по технологическим переходам на обработку вала (-0.16 ) в зубчатом колесе
Проверка: (1800-160)=(4200+700+1400)-(4000+400+260)=1640
Рисунок 6.1 - Схема графического изображения припусков (-0.16 )
Табл. 6.2 – расчет припусков и предельных размеров по технологическим переходам на обработку вала 155±035 в зубчатом колесе
Проверка: (1600-700)=(2510+670+760)-(2410+370+260)=900
Размерный анализ техпроцессов
Рисунок 7.1 – Размерная схема техпроцесса по линейным размерам
Рисунок 7.2 – Граф производного дерева
Рисунок 7.3 – Граф исходного дерева
Рисунок 7.4 – Граф совмещенного дерева
Выявление технологических размерных цепей:
Z2m Z8m Z5m Z3m Z7m Z6m
)S6=L1=13.5±0.35 мм;
)S5min=S6ma Z6min=S5min-S6max=14.45-13.85=0.6
Допуск по 13 квалитету по посадке h
S5ном=1445+027=1472-027=S5max
Z6=S5-S6=14.72-0.27-13.5±0.35=
)S4min=S5ma Z6min=S4min-S5max=16.22-14.72=1.5
S4ном=S4max=16.22+0.27=16.59-0.27
Z5=S4-S5=16.59-0.27-14.72-0.27=1.87±0.27;
)S3min=S4max+Z7=16.59+0.6=17.19.
Z7=S3-S4=17.79-0.27-16.59-0.27=1.2±0.27;
)З2min=S3ma Z8min=19.29-17.79=1.5
Z8=З2-S3=20.79+0.9-0.5-17.79-0.27=1.5+1.17-0.5;
)S2=L2-S4=22.5-0.21-15.6-0.27=6.9+0.27-0.21;
Z3=S1-S2=7.77-0.22-6.9+0.27-0.21=0.87+0.21-0.49;
TЗ1=14 ; e esЗ1=+09;
Z2=З1-S1=10.77+0.9-0.5-7.77-0.22=3+1.12-0.5;
Расчет режимов резания
02-0305-резец проходной СТП 930-1010
WNMG 080412-PR GC4225-пластина МКТС-Sandvik
WNMG 080408-WMX GC4215-пластина МКТС-Sandvik
S16R-резец расточной (2) ZCC-CT (Черновая и чистовая обработка)
CNMG 090308 – PM YBC351 – пластина ZCC-CT(Черновая обработка)
CNMG 090304 – PM YBC251 – пластина ZCC-CT(Чистовая обработка)
5 Черновая обработка
Нормирование техпроцессов
Технические нормы времени в условиях массового и серийного производств устанавливаются расчетно-аналитическим методом.
В серийном производстве норма штучно-калькуляционного времени определяется по формуле:
где Тшт – норма штучного времени:
Тшт = То + Тв + Тоб + Тот;
где То – основное время мин; Тв – вспомогательное время мин. Вспомогательное время состоит из затрат времени на отдельные приемы: Тв = 185(Тус + Тм.в. + Туп + Тиз); Тус – время на установку и снятие детали мин; Тм.в. – машинное вспомогательное время мин; Туп – время на приемы управления мин; Тиз – время на измерение детали мин; Тоб – время на обслуживание рабочего места мин. Складывается из времени на организационное и времени на техническое обслуживание рабочего места; Тот – время перерывов на отдых и личные надобности.
Таблица 9.1. - Сводная таблица технических норм времени по операциям мин
Наименование операции
Вертикально-протяжная
Определение потребного количества станков и построение графиков загрузки
Таблица 10.1 - Результаты расчёта коэффициентов использования оборудования
Фо=Фн(1-)=4060(1-003)=3938ч;
Количество единиц оборудования для поточного производства на годовую программу выпуска изделий определяется в соответствии с ГОСТом. Однако в целях унификации расчётов при курсовом проектировании допускается определять количество единиц оборудования по общей зависимости
где – годовой объём выпуска заданной детали ;
– эффективный годовой фонд времени работы единицы оборудования
Т.к. Ки=1то Спр=СРокр; КЗфакт=КЗрасч;
Рисунок 10.1 - Диаграмма загрузки оборудования
Расчет и проектирование приспособления
Приспособление для зубофрезерования предназначено для закрепления заготовки 05-1701216 на фрезерном станке на 060 операции.
Рисунок 11.1 – цилиндрическая оправка
Номинальный диаметр базовой поверхности оправки:
dоп=d-=24-002=2398мм (=002мм – гарантированный зазор для установки заготовки на оправке);
Длина базовой поверхности оправки:
L=nlз-(1-5)=1*22.5-1=21.5мм (n-чило одновременно обрабатываемых заготовок lз-длина заготовки)
Наружные диаметры опорного буртика нажимной шайбы:
D1=D-(3..5)=42.8-3=39.8мм
Ширина нажимной шайбы:
Гарантированный крутящий момент передаваемый оправкой:
Мкр.гаркМкр25*22=55Нм
Требуемое усилие зажима заготовки:
Точностной расчёт приспособления
Точности приспособления можно определить по формуле:
где - допуск выполняемого размера; - коэффициент учитывающий отклонение рассеяния значений составляющих величины от закона нормального распределения; - коэффициент учитывающий уменьшение предельного значения погрешности базирования при работе на настроенных станках; - коэффициент учитывающий долю погрешности обработки в суммарной погрешности вызываемой фактами не зависящими от приспособлений.
Погрешность базирования определим исходя из схемы базирования (рис. 10.3).
Рисунок 10.3 – Схема базирования (по внутреннему диаметру на оправке)
Погрешность базирования:
где Td=0.033мм TD=0.16мм - допуски по диаметру; - минимальный диаметральный зазор между базой и жесткими цилиндрическими пальцами.
Погрешность закрепления .
Погрешность установки приспособления устанавливают в соответствии со схемой установки приспособления (рис. 10.4).
Рисунок 10.4 – Схема определения погрешности приспособления
Погрешность в направлении:
где - торцовое биение опорной поверхности приспособления принимается в пределах 001 004 мм принимаем ; - максимальный зазор в сопряжениях базирующих поверхностей принимаем ; - диаметр центрирующего пояска принимаем D=32мм
Погрешность положения детали из-за износа элементов приспособления [4;с.169]:
где - средний при базовом числе установок ; - соответственно коэффициенты учитывающие влияние материала заготовки оборудования условий обработки и числа установок заготовки отличающиеся от принятых при определении : ; - число установок заготовкиN=30000.
Погрешность от перекоса или смещения инструмента:
где - погрешность установки инструмента по щупу зависящая от точности механизма перемещения инструмента; - допуск на изготовление щупа.
Экономическая точность обработки .
Допустимая погрешность изготовления приспособления равна:
Техникоэкономические расчеты
Определим себестоимость обработки по сравниваемым вариантам. Критерием оптимальности является минимум приведенных затрат на единицу продукции . Расчет ведется в ценах 1985 с учетом коэффициента инфляции равного 1600.
Часовые приведенные затраты можно определить по формуле:
где Sз- основная и дополнительная зарплаты с начислениями руб.;
Sч.з.- часовые затраты на эксплуатацию рабочего места руб.час;
Ен- нормативный коэффициент экономической эффективности капитальных вложений (в машиностроении Ен=015);
Кс Кз- удельные часовые капитальные вложения соответственно в станок и здание руб.час.
Основная и дополнительная зарплата с начислениями и учетом многостаночного обслуживания (руб.час)
где - коэффициент к часовой тарифной ставке равный 266;
Sтф- часовая тарифная ставка станочника-сдельщика соответствующего разряда руб.час;
k - коэффициент учитывающий зарплату наладчика;
y - коэффициент штучного времени учитывающий оплату труда рабочего при многостаночном обслуживании.
Часовые затраты на эксплуатацию рабочего места:
где - практические часовые затраты на базовом рабочем месте руб.час;
км- коэффициент показывающий во сколько раз затраты связанные с работой данного станка больше чем аналогичные расходы связанные с работой базового станка определяется по формулам.
Часовые затраты на базовом рабочем месте в условиях серийного производства при двусменном режиме работы по рекомендациям принимаем равными 9801 руб.час.
Капитальные вложения в станок и здание (руб.час) определяются по формулам:
где Fэ- эффективный годовой фонд времени станка ч;
з- коэффициент загрузки станка.
Цпл.зд- стоимость 1 м2 площади механического цеха.
А- производственная площадь занимаемая станком с учетом проходов;
где а- площадь станка в плане;
Ка- коэффициент учитывающий дополнительную производственную площадь
Таким образом используя приведенные выше формулы и нормативные данные рассчитываются приведенные затраты (руб.час).Для выявления более экономичного варианта необходимо рассчитать технологическую себестоимость операций:
где Тшт.- штучное время на операцию мин;
кв- коэффициент выполнения норм принимается обычно равным 13.
Таблица 12.1.- Определение стоимости операций механической обработки
Итого себестоимость механической обработки:
Технологическая себестоимость равна:
Ст = Sзаг + Со = 24483 + 3457= 4926 руб.
Число полных ставок заработной платы необходимых для изготовления деталей одного наименования в обьеме их годового выпуска.
R = Тшт Nг (601820) = 3633 30000 (601820) = 998
Число наладчиков на проектируемом участке может быть принято из условия что один наладчик обслуживает 8-10 станков в смену:
Н = 016 mпi = 016 10 =16 чел.
Годовой фонд заработной платы рабочих-станочников и наладчиков на одну операцию определяется:
Используя данные из табл. 12.1 рассчитаем по этой формуле фонд заработной платы.
Тогда получим годовой фонд заработной платы в размере 236655917 руб.
Среднемесячная зарплата рабочих:
Зм = Фз ((R +Н)·12);
Зм = 236655917((13+16)·12) =6800457 руб.
Годовой выпуск продукции по технологической себестоимости:
В = 4926·30000 = 14778 млн. руб.
Определим трудоемкость годовой программы:
Тг = 3633·30000 60 = 18165 ч.
Годовой выпуск продукции на одного рабочего:
bр = 14778 млн руб.998 = 1481 млн. руб.
Основные показатели сведем в таблицу 13.2.
Таблица 13.2.-Основные технико-экономические показатели разработанного технологического процесса
Наименование показателя
Наименование детали.
Годовой объем выпуска деталей шт.
Эффективный годовой фонд времени работы оборудованияч.
Эффективный годовой фонд времени рабочего ч.
Коэффициент использования материала заготовки.
Стоимость заготовки руб.
Себестоимость механической обработки детали руб.
Технологическая себестоимость детали руб.
Годовой выпуск продукции по технологической себестоимости млн. руб.
Основное время по операциям мин.
Штучное время по операциям мин.
Трудоемкость годовой программы выпуска ч.
Количество единиц оборудования шт.
Средний коэффициент загрузки станков.
Средний коэффициент использования оборудования по времени
Средний коэффициент использования оборудования по мощности
Число рабочих станочников на две смены чел.
Число наладчиков на две смены чел.
Годовой фонд заработной платы млн. руб.
Среднемесячная зарплата рабочих млн.руб.
Годовой выпуск на одного рабочего млн.руб.
Составление карты кодирования информации (фрагмент)
Всю информацию управляющей программы вносимую в карту программирования записывают в кодированном виде. Кодирование производят в соответствии с ГОСТ 13052-74 и рекомендациям международной организации по стандартизации двоичным кодом ISO-7bit. В этом коде с буквами латинского алфавита и знаками связаны определенные необходимые для программирования понятия а при перфорировании за каждой буквой цифрой и знаком (в дальнейшем будем называть их символами) закреплены комбинации расположения отверстий на восьмидорожковой ленте.
В соответствии с международными стандартами и ГОСТ 20999-83 структура управляющей программы в общем случае подчиняется следующим правилам:
- в тексте управляющей программы должна содержаться геометрическая технологическая и вспомогательная информация которая необходима для проведения заданной обработки. В каждом кадре программы записывается только та информация которая изменяется по отношению к предыдущему кадру. При этом выполнение системой ЧПУ оставшейся неизменной информации прекращается только после поступления команды на ее отмену (вид этой команды и способ отмены определяется особенностями конкретной системы ЧПУ).
- каждая управляющая программа начинается символом «начало программы» подающим системе управления сигнал о начале выполнения программы. Вид символа «начало программы» зависит от особенностей применяемой системы ЧПУ. Наиболее часто в отечественных и зарубежных системах ЧПУ используется символ %. При этом кадр с символом «начало программы» не нумеруется. Нумерация кадров начинается с последующего кадра.
- если управляющей программе необходимо присвоить обозначение то его располагают в кадре с символом «начало программы» непосредственно за символом.
- если текст управляющей программы необходимо сопроводить комментарием например сведениями об особенностях наладки станка то его размещают перед символом «начало программы».
- управляющая программа должна заканчиваться символом «конец программы» подающим системе управления сигнал на прекращение выполнения управляющей программы останов шпинделя приводов подач и выключение охлаждения. Информация помещенная в тексте управляющей программы после этого символа не должна восприниматься системой ЧПУ.
- информация расположенная в тексте управляющей программы между символами «начало программы» и «конец программы» и заключенная в круглые скобки не должна приниматься системой ЧПУ к исполнению. При этом в тексте внутри скобок не должны применяться символы «начало программы» и «главный кадр».
Рисунок 13.1 – Эскиз перехода детали
Эскиз перехода детали на которой сделана карта кодирования (рисунок13.1). Ниже представлена программа на токарную операцию с ЧПУ.
Таблица 13.1 – Программа кодирования
Koleso Zubchatoe 05-1701216
Колесо зубачатое – 05-1701216
Команда на начало выполнения программы с указанием названия программы
N5G27G95T1111M12M41 LF
Последовательность кадров содержащих информацию по обработке детали «Колесо зубчатое 05-1701216»
N150G0X41Z91.25M8 LF
N160X58Z73.5F.3M9 LF
N175G0X43.75Z75.25M8 LF
Команда на окончание выполнения программы
В данном курсовом проекте мы разработали технологический процесс изготовления детали «Зубчатое колесо 05-1701216». Анализировали заводской технологический процесс выбрали способ получения заготовки детали «Зубчатое колесо 05-1701216». Также мы рассчитали силу зажима и точность зубофрезерного приспособления. Определили потребное количество станков и составили график их загрузки.
Технология машиностроения: учебно-методическое пособие по выполнению курсового проекта и курсовой работы для студентов дневной и заочном форм обученияГ.Я. Беляев МА1 Кане А.И- Медведев; под ред. М.М. Кане-Мн.: БНТУ 2006-88 с.
Проектирование технологических процессов механической обработки в машиностроении. Под ред. В.В.Бабука. – Мн.: “Вышэйшая школа” 1987. –256с.
Горбацевич А. Ф. Шкред В. А. Курсовое проектирование по технологии машиностроения. – Мн.: Выш. школа 1983. –256с.
ГОСТ 7505-89 Штамповки. Припуски и допуски.
Справочник технолога машиностроителя. В двух томах.Т1. Под ред. А.Г.Косиловой и Р.К.Мещерякова. М.: Машиностроение 1985. –656с
Справочник технолога машиностроителя. В двух томах.Т2. Под ред. А.Г.Косиловой и Р.К.Мещерякова. М.: Машиностроение 1985. –496с.
(А3)Чертеж заготовки.cdw

Термообработка - нормализация(диаметр отпечатка 4.8-4.2 мкм)
степень сложности С1 по ГОСТ 7505-74
Класс точности II по ГОСТ 7505-74
Неуказанные радиусы закруглений 2.5мм
Неуказанные штамповочные уклоны 7
Допускается заусенец по контуру обрезки до 1.0мм
В месте "А" допускается след от толкателя
мм или глубиной до 1.0мм
Смещение штампов допускается до 0.8мм
Внешние дефекты допускаются до 12 фактического
одностороннего припуска на механическую обработку
Поковку очистить от окалины
Остальные технические требования по ГОСТ 8479-70
Направление заусенца по стрелке "Б
Допускается коробление до 0.4мм
(А3)Карта кодирования.cdw

Зубачатое колесо 05-1701216
Операция 015 Установ 1
(А3)Операционные эскизы.cdw

Для справок: W=15.566
Допуск на колебание ИМР
за оборот зколеса F''i=0.105мм
5 Внутришлифовальная
* - размер для справок
010t.docx
КТМ 3.13 Кафедра”Технология машиностроения ”
Колесо зубчатое 05-1701216
См. карту эскизов №2
Наименование операции
Сталь 25ХГТ ГОСТ4543-71
Оборудование устройство ЧПУ
Обозначение программы
Установить и закрепить деталь
Точить поверхность выдерживая размер 12
02-0305 Резеце проходной СТП 930-1010
WNMG 080412-PR GC4225 – пластина МКТС-Sandvik
WNMG 080408-WM GC4215 – пластина МКТС-Sandvik
Штангенциркуль ШЦ-II-250-005 ГОСТ166
Расточить отверстие выдерживая размер 3
S16R-PCLNR09-резец расточной ZCC-CT
CNMG 0903008-PM YBC351-пластина ZCC-CT
CNMG 090304-PM YBC251-пластина ZCC-CT
Штангенглубиномер ШГ-160-005 ГОСТ162
005t.docx
КТМ 3.13 Кафедра”Технология машиностроения ”
Колесо зубчатое 05-1701216
См. карту эскизов №1
Наименование операции
Сталь 25ХГТ ГОСТ4543-71
Оборудование устройство ЧПУ
Обозначение программы
Установить и закрепить деталь
Точить поверхность выдерживая размер 1
02-0305 Резеце проходной СТП 930-1010
WNMG 080412-PR GC4225 – пластина МКТС-Sandvik
Штангенциркуль ШЦ-II-250-005 ГОСТ166
115t.docx
КТМ 3.13 Кафедра”Технология машиностроения ”
Колесо зубчатое 05-1701216
См. карту эскизов №5
Наименование операции
Сталь 25ХГТ ГОСТ4543-71
Оборудование устройство ЧПУ
Обозначение программы
Установить и закрепить деталь
Шлифовать отверстие выдерживая размер 1
Круг шлифовальный 120х20х6 25А 25С-СМ1 7к5 50мс Акл1 ГОСТ 2424
Карандаш алмазный 3908-0055-01 ГОСТ607
Контрольный прибор МЦ-400Б
060t.docx
КТМ 3.13 Кафедра”Технология машиностроения ”
Колесо зубчатое 05-1701216
См. карту эскизов №4
Наименование операции
Сталь 25ХГТ ГОСТ4543-71
Оборудование устройство ЧПУ
Обозначение программы
Установить и закрепить деталь
Фрезеровать зубья колеса Z=19 m=2
Фреза червячная 2510-5052(Zф=12 dф=63)
Скоба шаговая L=15.534-0.06
120t.docx
КТМ 3.13 Кафедра”Технология машиностроения ”
Колесо зубчатое 05-1701216
См. карту эскизов №5
Наименование операции
Сталь 25ХГТ ГОСТ4543-71
Оборудование устройство ЧПУ
Обозначение программы
Установить и закрепить деталь
Шлифовать торец выдерживая размер 1
Круг шлифовальный 500х63х203 25А 40 ПМ1-СМ150мс А1клА ГОСТ 2424
Круг для правки ПП150х32х51 55С50-40ВТ SK 50мс А1клА ГОСТ 2424
Скоба 227min 8150-5133
015t.docx
КТМ 3.13 Кафедра”Технология машиностроения ”
Колесо зубчатое 05-1701216
См. карту эскизов №3
Наименование операции
Сталь 25ХГТ ГОСТ4543-71
Оборудование устройство ЧПУ
Обозначение программы
Установить и закрепить деталь
Точить поверхность выдерживая размеры 123
02-0305 Резеце проходной СТП 930-1010
WNMG 080412-PR GC4225 – пластина МКТС-Sandvik
WNMG 080408-WM GC4215 – пластина МКТС-Sandvik
45-5001-резец расточной
Штангенциркуль ШЦ-II-250-005 ГОСТ166
Штангенглубиномер ШГ-160-005 ГОСТ162
KK.docx
Наименование операции
Наименование марка материала
Наименование оборудования
Контролируемые параметры
Наименование средств ТО
Проверить отсутствие
Образцы шероховатости ГОСТ 9378-93
Штангенциркуль ШЦ- I -125-01 ГОСТ 166-80
Нормалемер БВ-5045 М1-В ГОСТ 7760-81
Шагомеры OMRON HJ-005-E
Контактомер ГОСТ 25513-82
Биениемер ГОСТ 25513-82
МК.docx
МИНИСТЕРСТВО ОБРАЗОВАНИЯ РЕСПУБЛИКИ БЕЛАРУСЬ
Утвердил: Беляев Г.Я.
НА ТЕХНОЛОГИЧЕСКИЙ ПРОЦЕСС МЕХАНИЧЕСКОЙ ОБРАБОТКИ
Шестерня ведомая 50-1701314
ГОСТ 3.1404-86 Форма 1
Кафедра”Технология машиностроения”
Сталь 25ХГТ ГОСТ4543-71
Код наименование операции
Обозначение документа
Код наименование оборудования
1 Транспортирование из кузнечного цеха КТМ 60140.00001 КТМ 20140.00001 СТИ по ИОТ113
11 11 005 Токарная с ЧПУ∅448-03 КТМ 60140.00002 КТМ 20140.00002 СТИ по ИОТ10 343
11 11 010 Токарная с ЧПУ ∅428-016 КТМ 60140.00003 КТМ 20140.00003 СТИ по ИОТ45 343
11 11 015 Токарная с ЧПУ ∅428-016 КТМ 60140.00004 КТМ 20140.00004 СТИ по ИОТ45 343
12 16 020 Вертикальнопротяжная ∅27Н12(+021) КТМ 60140.00014 КТМ 20140.00014 СТИ по ИОТ189 353
ГОСТ 3.1404-86 Форма 1б
Наименование детали сб. единицы или материала
0 Слесарная КТМ 60140.00005 КТМ 20140.00005 СТИ по ИОТ43 030
5 Контрольная КТМ 60140.00012 КТМ 20140.00012 СТИ по ИОТ89 026
22 68 060 Зубофрезерная Z=19 m=2 КТМ 60140.00005 КТМ 20140.00005 СТИ по ИОТ160 4.06
23 69 065 Зубозакругляющая 150±20 R2±0.3 КТМ 60140.00013 КТМ 20140.00013 СТИ по ИОТ160 406
24 70 070 Зубофасочная 0.4maxx450 КТМ 60140.00006 КТМ 20140.00006 СТИ по ИОТ142 406
5 Промывка КТМ 60140.00014 КТМ 20140.00014 СТИ по ИОТ196 017
0 Зубошевинговальная Z=19 m=2 КТМ 60140.00015 КТМ 20140.00015 СТИ по ИОТ161 333
5 Промывка КТМ 60140.00014 КТМ 20140.00014 СТИ по ИОТ196 017
0 Слесарная КТМ 60140.00015 КТМ 20140.00015 СТИ по ИОТ64 095
5 Контрольная КТМ 60140.00015 КТМ 20140.00015 СТИ по ИОТ187 040
5 Зубообкатывающая Z=19 m=2 КТМ 60140.00018 КТМ 20140.00018 СТИ по ИОТ48 406
5 Внутришлифовальная ∅24+0033 КТМ 60140.00012 КТМ 20140.00012 СТИ по ИОТ164 443
0 Шлифовальная 225-021 КТМ 60140.00013 КТМ 20140.00013 СТИ по ИОТ164 284
0 Слесарная КТМ 60140.00022 КТМ 20140.00022 СТИ по ИОТ64 12
5 Промывка КТМ 60140.00012 КТМ 20140.00012 СТИ по ИОТ196 017
0 Контрольная КТМ 60140.00013 КТМ 20140.00013 СТИ по ИОТ187 062
(А3)Приспособа.cdw

Массу определить взвешиванием
Проверку приспособления осуществлять под давлением 0.5МПа в
течении 30 мин на технологическу точность 1 раз в 6 месяцев
Зубофрезерное приспособление
(А2)Операционные эскизы.cdw

Степень точности по ГОСТ 1643-81
* - размер для справок
выдерживая размеры 1
(А3)Чертеж детали.cdw

Предельные отклонения
измерительного межосе-
Наименьшее дополнительное
отклонение исходного контура
измерительного межосевого
Суммарное пятно контакта
Диаметр основной окружности
Диаметр делительной окружности
Толщина зуба по дуге
делительной окружности
Нитроцементироватьм h 0.25..0.7мм
поверхностяхдопускается снижение нитроцементированного слоя до 0
Поверхности зубьев 57 64 HRC
Сердцевины 27..46HRC
Остальные поверхности 46 HRC не менее
Допускается цианирование h 0.25 0.4мм 59..63HRC
*Размеры обеспечиваются инструментом
Некуказанные предельные отклонения размеров по ОСТ 23.4.209-82
При снятии заусенцев на зубьях допускается фаска по длине зуба
Маркировать 4. Шрифт 5 ГОСТ 2.304-81 на бирке для запчастей
Остальные ТТ по СТБ 1024-96
Допускается притупление острой кромки по контуру зубьев фаской
мм не более от торца зуба
Допускается выполнять отверстие
приводящей к местным прослаблениям
Рекомендуемые чертежи
- 24.01.2023
- 24.01.2023
- 24.01.2023
- 13.05.2022
- 25.01.2023
- 24.01.2023
- 13.12.2022