Технологический процесс механической обработки детали - кольцо подшипника внутреннее 53516.02 с экономическим обоснованием технологического процесса




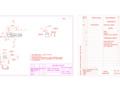
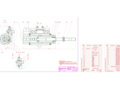
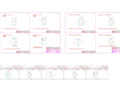
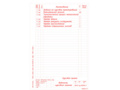
- Добавлен: 24.01.2023
- Размер: 2 MB
- Закачек: 1
Описание
Состав проекта
![]() |
![]() |
![]() ![]() ![]() |
![]() ![]() ![]() ![]() |
![]() ![]() ![]() ![]() |
![]() |
![]() ![]() ![]() |
![]() ![]() |
![]() ![]() ![]() |
![]() ![]() ![]() ![]() |
![]() ![]() ![]() ![]() |
![]() ![]() ![]() ![]() |
![]() ![]() ![]() ![]() |
![]() ![]() ![]() ![]() |
![]() ![]() ![]() ![]() |
![]() ![]() ![]() |
![]() ![]() ![]() ![]() |
![]() ![]() ![]() |
![]() ![]() ![]() ![]() |
![]() |
![]() ![]() ![]() ![]() |
![]() ![]() ![]() ![]() |
Дополнительная информация
КУРСАЧ.doc
БЕЛОРУССКИЙ НАЦИОНАЛЬНЫЙ ТЕХНИЧЕСКИЙ УНИВЕРСИТЕТ
Кафедра «Технология машиностроения»
на тему «Технологический процесс механической обработки детали – кольцо подшипника внутреннее 53516.02 с экономическим обоснованием технологического процесса»
Исполнитель: Михаленя П.В.
Руководитель: Бохан С.Г.
НАЗНАЧЕНИЕ И УСЛОВИЯ РАБОТЫ ДЕТАЛИ В УЗЛЕ8
АНАЛИЗ ТЕХНОЛОГИЧНОСТИ КОНСТРУКЦИИ ДЕТАЛИ11
ВЫБОР ТИПА И ФОРМЫ ОРГАНИЗАЦИИ ПРОИЗВОДСТВА13
АНАЛИЗ СУЩЕСТВУЮЩЕГО ТЕХНОЛОГИЧЕСКОГО ПРОЦЕССА16
ВЫБОР СПОСОБА ПОЛУЧЕНИЯ ЗАГОТОВКИ С ЭКОНОМИЧЕСКИМ ОБОСНОВАНИЕМ20
ПРОЕКТИРОВАНИЕ ТЕХНОЛОГИЧЕСКОГО ПРОЦЕССА23
ОПРЕДЕЛЕНИЕ РЕЖИМОВ РЕЗАНИЯ28
ОПРЕДЕЛЕНИЕ НОРМЫ ВРЕМЕНИ ДЛЯ ОПЕРАЦИЙ34
ОПРЕДЕЛЕНИЕ НЕОБХОДИМОГО КОЛИЧЕСТВА ОБОРУДОВАНИЯ И ПОСТРОЕНИЕ ГРАФИКОВ ЗАГРУЗКИ36
РАСЧЕТ И ПРОЕКТИРОВАНИЕ ИНСТРУМЕНТА39
РАСЧЁТ И ПРОЕКТИРОВАНИЕ ПРИСПОСОБЛЕНИЯ41
ТЕХНИКО-ЭКОНОМИЧЕСКИЕ РАСЧЁТЫ44
Минский подшипниковый завод – крупнейшее машиностроительное предприятие Республики Беларусь специализирующееся на выпуске подшипников. Приказ о строительстве ГПЗ №11 в Минске был подписан в 1948 году и уже в 1951 году был собран первый белорусский подшипник. В 1991 году по решению коллектива предприятие было преобразовано из государственного в арендное.
В рамках союзной кооперации АП "МПЗ" был ориентирован на обеспечение подшипниками качения крупных конвейерных заводов и в первую очередь автомобильного и сельскохозяйственного машиностроения имея устойчивые рынки сбыта во всех регионах бывшего СССР. При этом его доля в поставках подшипников в БССР равнялась 75 % в целом по союзу – 15 % и в мире 1 %.
Традиционно завод являлся поставщиком подшипников шариковой и роликово-сферической группы. Однако после развала союза для выживания в новых условиях понадобилось расширять номенклатуру выпускаемой продукции. Так с 1993 года начался выпуск игольчатых подшипников. В последние годы значительно сократилась номенклатура подшипников роликово-сферической группы не находящей спроса зато резко увеличился ассортимент подшипников шариковой группы. Так за период 1997-1998 гг. было освоено более чем сто типоразмеров этих подшипников. Следуя потребностям рынка завод в 1994 году освоил и начал производство уникальных шариковых многорядных радиально-упорных подшипников которые используются в опорах турбобуров. Такие подшипники не имеют аналогов в мире.
Теперь следует сказать о структуре продаж. Большая часть продукции продается в Республике Беларусь. Она является приоритетным рынком для завода. Продажа подшипников в Россию невыгодна потому что заводы конкуренты находящиеся там продают продукцию дешевле чем может МПЗ. Экспорт подшипников в дальнее зарубежье не выгоден для завода ибо продукция поставляется туда по ценам ниже себестоимости. Однако это единственный способ добыть валюту которая необходима заводу для различных целей.
В связи с увеличением конкуренции заводу необходимо увеличивать эффективность производства. Именно с этой целью на заводе цеха в которых станки с ЧПУ экономически выгодней и эффективней использовать чем универсальные и агрегатные станки переводят на станки с ЧПУ. В доказательство этому можно перевести следующие примеры: практически все универсальные шлифовальные станки заменены станками с программным управлением; в цех по производству шарниров равных угловых скоростей (ШРУС) закуплены специальные станки со стойкой ЧПУ "SINUMERIK"; установлены новые фрезерные пяти-координатные станки с вводом программы с ЭВМ и т.д.
Основной вид деятельности – производство подшипников качения. АП "МПЗ" выпускает подшипники различных конструктивных групп (шариковые роликовые ролико-сферические игольчатые карданные шарнирные) диаметром от 12 до 840 мм. и массой от 2 граммов до 640 килограммов. Всего более 300 типоразмеров и модификаций. Мощность предприятия – 364 млн. штук в год.
В настоящее время МПЗ успешно пользуется последними достижениями мировой промышленности (установлена одна из трёх закупленных в США графических станций Silicon Graphics оснащённых программным комплексом "ProEngineer" готовится к запуску автоматическая линия предназначенная для изготовления колец подшипников и т.д.)
Кроме того АП "МПЗ" выпускает специальное техническое оборудование и станки для собственных нужд и сторонних потребителей товары народного потребления выполняет работы промышленного характера имеет подсобное хозяйство оказывает платные услуги населению.
ПРОДУКЦИЯ ВЫПУСКАЕМАЯ НА МПЗ
АП "МПЗ" выпускает широчайший спектр подшипников качения. В номенклатуру продукции предлагаемой предприятием входят следующие группы подшипников:
1 Радиальные – предназначены для восприятия тяжёлой радиальной нагрузки но могут воспринимать и осевую нагрузку определённой величины;
2 Упорно-радиальные – предназначены для восприятия осевой и радиальной нагрузки;
3 Игольчатые – обладают высокой грузоподъёмностью при значительно меньшем сечении;
1 Радиальные однорядные – предназначены для восприятия радиальных нагрузок но могут воспринимать и значительные осевые нагрузки в двух направлениях;
2 Радиально-упорные – предназначены для восприятия радиальной и осевой нагрузки;
3 Упорно-радиальные многорядные – предназначены для передачи больших осевых нагрузок;
Тела качения – шарики и ролики различных типов и размеров.
За последние годы на МПЗ освоено большое количество продукции. Освоено производство подшипников-гигантов (их вес 648 кг наружный диаметр 820 мм) которые используются в горнодобывающей промышленности. Шариковые упорно-радиальные многорядные подшипники для опор турбобуров (применяемых для бурения глубинных скважин) не имеют аналогов в мировом подшипникостроении; освоено более десяти видов конических подшипников; и т.д.
Необходимо отметить возросший выпуск нетрадиционной продукции. К нетрадиционной продукции относятся:
Шарниры равных угловых скоростей (ШРУС) применяющиеся в ходовой части переднеприводных автомобилей.
Комплект деталей для крепления рельс по европейскому стандарту состоящий из анкера и клеммы.
Гильза блока цилиндра (для трактора "Беларус").
Роликовые цепи использующиеся в сельском хозяйстве.
Абразивный инструмент
В связи с увеличением номенклатуры выпускаемых изделий начал работу участок по изготовлению пластмассовых и резинотехнических изделий.
НАЗНАЧЕНИЕ И УСЛОВИЯ РАБОТЫ ДЕТАЛИ В УЗЛЕ
1 Назначение сборочной единицы
Подшипники предназначены для восприятия тяжелой нагрузки главным образом радиальной но могут воспринимать и осевые нагрузки определенной величины. Подшипники фиксируют вал в осевом направлении в обе стороны в пределах имеющихся осевых зазорах и могут работать при угле перекоса оси внутреннего кольца до 2 градусов относительно оси нагруженного образующегося в результате прогиба вала под действием нагрузки или вследствие технологических неточностей обработки и сборки узла.
Внутреннее кольцо подшипника имеет в качестве исполнительной поверхности сферическую дорожку качения 1. Эта же поверхность является вспомогательной конструкторской базой так как на неё опираются ролики подшипника. Основной конструкторской базой внутреннего кольца является внутренняя цилиндрическая поверхность 2 так как она служит для посадки подшипника на сопрягаемую поверхность вала. Торцовые поверхности 3 при работе подшипника выполняют вспомогательные функции. Они могут использоваться для ориентирования подшипника на валу в осевом направлении и следовательно также являются основными конструкторскими базами.
Рисунок 1 - Эскиз сборочной единицы.
1.2 Описание и назначение внутреннего (наружного) кольца
Внутреннее кольцо и наружное кольцо подшипника изготавливается из стали ШХ15 и имеет в качестве исполнительных поверхностей дорожки качения. Эти же поверхности являются вспомогательными конструкторскими базами так как на них опираются шарики подшипника . Основной конструкторской базой внутреннего кольца является коническая поверхность так как она служит для посадки подшипника на сопрягаемую поверхность вала. Торцевые поверхности при работе подшипника выполняют вспомогательные функции. Они могут использоваться для ориентирования подшипника на валу в осевом направлении и следовательно также являются основными конструкторскими базами.
Дорожки качения колец подшипника работают при больших контактных напряжениях достигающих 6000 МПа и являются лимитирующими с точки зрения его долговечности. Поверхности дорожек качения в зависимости от условий эксплуатации подшипника могут быть подвержены различным видам разрушений вследствие контактной усталости абразивного коррозионного и других видов изнашивания. При работе подшипника каждый элемент поверхности дорожек качения работает при циклических переменных нагрузках в результате чего на рабочих поверхностях возникают усталостные трещинки приводящие к хрупкому разрушению материала в зоне контакта. На основании выше изложенного можно сделать вывод что внутреннее и наружные кольца подшипника является ответственными тяжело нагруженной деталями.
Специфика нагрузок и условия работы подшипников качения обусловили применение для их изготовления специальных подшипниковых сталей таких как ШХ15 и ШХ15СГ. В последние время для производства подшипников начали использовать конструкционную легированную сталь 20Х так как после цементации и закалки механические параметры поверхностей не уступают специальным подшипниковым сталям а стоимость её гораздо ниже.
Внутреннее кольцо подшипника 53516 изготавливается из стали ШХ15 ГОСТ 801-78. Химический состав стали приведен в таблице 1.1 а механические свойства в таблице 1.2.
Таблица 1.1 – Химический состав стали ШХ15.
Таблица 1.2 – Механические свойства стали ШХ15.
Технологические свойства стали ШХ15: в горячем состоянии (1150-800°С) сталь легко куётся поддаётся деформированию прокаткой и высадкой. При комнатной температуре деформируемость рассматриваемой стали ограничена вследствие малой пластичности и резкого возрастания усилия деформации. Обрабатываемость резанием хорошая.
Поверхность дорожки качения во время эксплуатации подшипника может подвергаться различным видам разрушения вследствие контактной усталости абразивного коррозийного и других видов изнашивания. Преобладающим видом разрушения вызываемого контактной усталостью рабочей поверхности является выкрашивание материала в виде мелких раковин или отслаивание элементов материала.
На основании изложенного можно сделать вывод что внутреннее кольцо подшипника является ответственной тяжело нагруженной деталью. Основные задачи по его обработке состоят в обеспечении размерной точности высокой твердости и усталостной износостойкости дорожки качения.
АНАЛИЗ ТЕХНОЛОГИЧНОСТИ КОНСТРУКЦИИ ДЕТАЛИ
Отработка детали на технологичность—комплекс мероприятий по обеспечению необходимого уровня технологичности конструкции изделия по установленным показателям. Она направлена на повышение производительности труда снижение затрат сокращение времени на изготовление изделия при обеспечении необходимого качества. Оценка технологичности конструкции может быть двух видов: качественной и количественной.
1 Качественная оценка технологичности конструкции
Проанализируем технологичность конструкции с точки зрения применяемого материала. Производство внутреннего кольца подшипника 53.516.02 возможно из сталей 20Х ШХ15 ШХ15СГ. Сталь 20Х для изготовления данной детали не пригодна так как она цементируется только на 3-4 мм а подшипник работает при высоких нагрузках которых данная сталь может не выдержать. Сталь ШХ15 хорошо прокаливается и обеспечивает хорошие прочностные и эксплуатационные свойства. Отрицательной стороной стали ШХ15 является то что при использовании её в качестве материала для толстостенных подшипников ШХ15 не полностью прокаливается. У стали ШХ15СГ лучшая прокаливаемость так как в ней увеличено содержание Мn однако она дороже стали ШХ15. Исходя из выше приведённых факторов можно сделать вывод что сталь ШХ15 наиболее подходит для изготавления внутреннего кольца роликового радиального подшипника 53.516.
Обрабатываемые поверхности внутреннего кольца за исключением дорожки качения являются простыми что позволяет выполнить точную и стабильную обработку данной детали. Ко всем поверхностям возможен свободный подход инструмента.
В процессе обработки детали технологические базы совпадают с измерительными т.е. соблюдается принцип совмещения баз что также свидетельсвует о технологичности конструкции.
Требования к точности и шероховатости предъявляются обоснованно. На рабочие поверхности такие как дорожка качения и внутренний диаметр установлены более жёсткие требования чем для нерабочих поверхностей.
2 Количественная оценка технологичности конструкции
Трудоемкость изготовления детали Ти = 1303 нормо-час.
Технологическая себестоимость детали Ст = 2097 руб.
Коэффициент унификации конструктивных элементов:
где (Qу.е - число унифицированных конструктивных элементов детали; Qэ - общее число конструктивных элементов детали.
Всего деталь содержит 9 конструктивных элементов: наружных фасок - 2; внутренних фасок - 2; внутренних цилиндрических поверхностей - 1; дорожек качения - 2; наружных цилиндрических поверхностей - 2; канавок - 1. Из них 6 унифицированных. Неунифицированные элементы: отверстие внутреннее 2 дорожки качения канавка. Ку.э = 610 = 06
Коэффициент применяемости стандартизованных обрабатываемых поверхностей:
где Dо.сDм.о - соответственно число поверхностей детали обрабатываемых стандартным инструментом и всех подвергаемых механической обработке поверхностей шт.
Всего обрабатывается 13 поверхностей: фасок - 4; наружных цилиндрических поверхностей - 2; дорожек качения - 2; канавок - 1; внутренних цилиндрических поверхностей - 2; торцев - 2. Из них обработке стандартным инструментом подвергается 6. Специальным инструментом обрабатываются: фаски и 2 дорожки качения.
Коэффициент обработки поверхностей:
где Dэ - общее количество поверхностей.
Так как обработке подвергаются все 13 поверхностей то получим:
Максимальное значение параметров шероховатости обрабатываемых поверх ностей 016 мкм
Максимальное значение квалитета обработки IТ6.
ВЫБОР ТИПА И ФОРМЫ ОРГАНИЗАЦИИ ПРОИЗВОДСТВА
Тип производства характеризуется коэффициентом закрепления операций: Кз.о 1- массовое; 1 Кз.о10 – крупносерийное; 10 Кз.о 20 – среднесерийное; 20 Кз.о 40 – мелкосерийное производство; Кз.о> 40 – единичное производство.
Коэффициент закрепления операций равен:
S Рi – явочное число рабочих участка выполняющих различные операции при работе в одну смену.
где hн – планируемый нормативный коэффициент загрузки станка всеми закрепленными за ним однотипными операциями принимаемый для крупно- средне- и мелкосерийного производства соответственно равным 075; 08; 09;
hз – коэффициент загрузки станка проектируемой (заданной) операцией:
Nг – годовая программа выпуска заданной детали шт.; Nг = 50000 шт.
Fг – годовой действительный фонд времени работы оборудования 4055 ч;
kв – коэффициент выполнения норм принимается равным 13.
Необходимое число рабочих для обслуживания в течение одной смены одного станка загруженного по плановому нормативному коэффициенту
Ф – месячный фонд времени рабочего занятого в течение 22 рабочих дней в месяц ч: Ф = 22 × 8 = 176 ч.
Для расчетов примем значение hн = 08.
Результаты расчетов сведем в таблицу 3.1.
Наименование операции
Таким образом коэффициент закрепления операций равен:
Следовательно принимаем тип производства – среднесерийное.
Формы организации технологических процессов в соответствии с ГОСТ 14.312-74 зависят от установленного порядка выполнения операций расположения оборудования количества изделий и направления их движения при изготовлении. Существуют две формы организации технологических процессов: групповая и поточная.
Рассмотрим целесообразность организации поточной формы производства. Это решение обычно принимается на основании сравнения заданного суточного выпуска изделий и расчетной суточной производительности поточной линии при двухсменном режиме работы и ее загрузке на 65 75%.
Заданный суточный выпуск изделий определяется по формуле:
Суточная производительность поточной линии определяется по формуле:
где Fc – суточный фонд времени работы оборудования (при двухсменном режиме работы – 960 мин);
Тср – средняя станкоемкость основных операций мин;
hз – коэффициент загрузки оборудования.
Средняя станкоемкость операций (станко-мин)
kв – средний коэффициент выполнения норм времени принимается равным 13;
n – количество основных операций.
Коэффициент загрузки оборудования:
Суточная производительность поточной линии
Заданный суточный выпуск изделий больше суточной производительности поточной линии значит делаем вывод о групповой форме организации производства.
Такт производства равен:
При групповой форме организации запуск изделий в производство осуществляется партиями с определенной периодичностью что является признаком серийного производства.
Рассчитываем предельно допустимые параметры партии n1 и n2:
где FЭ.М – эффективный месячный фонд времени участка равный 10560 мин;
no – число операций механической обработки по технологическому процессу; kмо – коэффициент учитывающий затраты межоперационного времени принимаем равным 15.
Параметр n1 отражает производительность и уровень специализации рабочих мест на участке. С помощью параметра n2 учитывается и ограничивается объем незавершенного производства и связывания оборотных средств. Меньший из двух параметров обозначают nmin а больший – nmax.
Расчетная периодичность повторения партий деталей (дн.):
Ближайшее большее нормативное значение равно Iн = 11 дней.
Рассчитаем размер партии согласно условию:
при условии nmin n nmax.
Так как условие выполняется значит размер партии определен верно.
АНАЛИЗ СУЩЕСТВУЮЩЕГО ТЕХНОЛОГИЧЕСКОГО ПРОЦЕССА
Предметом анализа является технологический процесс изготовления внутреннего кольца роликового подшипника. Производство среднесерийное. Годовой объем выпуска – 50000Технологический процесс механической обработки детали "Кольцо внутреннее" применяемый на производстве достаточно сложен. Это объясняется сложностью конструкции детали и повышенными требованиями к её основным рабочим поверхностям.
Для данного масштаба производства метод получения заготовки является рациональным. Реальная заготовка соответствует чертежу в отношении фактических припусков на обработку и выполнение прочих технологических требований. Для достижения заданной точности детали последовательность операций техпроцесса выбрана верно. В таблице 4.1 приведены основные технологические возможности применяемого оборудования для внутреннего кольца.
Таблица 4.1 - Внутреннее кольцо.
Предельные или наибольшие размеры обрабатываемой заготовки мм
Технологические возможности метода обработки
шероховатость обрабатываемой поверхности
Проведённый анализ показал что оборудование находится в приемлемом техническом состоянии однако оно морально устарело и нуждается в замене на более современное. При этом следует отметить что коэффициенты загрузки оборудования достаточно высоки что оправдывает создание из них автоматических линий.
При изготовлении детали в условиях крупносерийного производства большую роль играет метод базирования и точность которую он позволяет получить. В условиях крупносерийного производства применяют специальные и специализированные приспособления которые позволяют за короткий промежуток времени точно и надежно закрепить деталь. В этих приспособлениях наиболее правильно можно следовать законам единства и баз что ведёт к достижению более жестких требований при тех же затратах.
Рисунок 4.1 – Эскиз внутреннего кольца.
На участке применяют высокопроизводительное оборудование. Участок оснащен сложными специальным токарным автоматам высокопроизводительными шлифовальными станками. Все эти станки обладают достаточной жесткостью и точностью что позволяет обеспечить заданные чертежом детали технологические требования.
Приспособления применяемые на участке все специальные с пневматическими зажимами они соответствуют современным требованиям: позволяют добиться нужных параметров по качеству и точности предъявляемых к детали обеспечивают точное базирование и надежное закрепление а также повышает производительность труда.
СОЖ применяемая на участке соответствует санитарно-гигиеническим нормам. Для защиты окружающей среды от выбросов на участке предусмотрены устройства отсасывающие пыль с подключением их к заводской сети вентиляции и пылеулавливания.
Проверка настройка и профилактика оборудования осуществляется слесарями-ремонтниками и наладчиками в неосновное рабочее время что позволяет вести беспростойный процесс обработки детали.
Разряды рабочих вполне соответствуют характеру работы и для изготовления детали по данному техпроцессу не требуется рабочих более высокой квалификации .
В целом организационные вопросы на участке решены без особых нарушений. Межоперационный транспорт на участке современен что позволяет избегать простоев из-за отсутствия заготовок.
Недостатки данного техпроцесса:
Оборудование на участке установлено с отклонением от норм технического проектирования участков механических цехов. Это является недостатком с точки зрения охраны труда и ТБ так как может стать причиной травматизма.
Условия складирования деталей и хранения заготовок так же не соответствуют требованиям охраны труда и ТБ так как контейнеры в которых они хранятся расположены прямо на участке что мешает проходу .
Документация устарела и не соответствует требованиям ЕСТД. Технологическая документация выполнена на бланках старого образца.
Организационно-технических мероприятий по совершенствованию существующего варианта техпроцесса:
- производить инструктаж по технике безопасности регулярно и своевременно;
- для создания оптимальных условий с точки зрения эстетических условий труда произвести профилактику и покраску всего оборудования;
- для создания необходимых условий труда установить современные осветительные приборы;
- уделить особое внимание утилизации и дальнейшего использования не только стружки но и других отходов производства;
- оснастить участок наглядными пособиями по технике безопасности и поведению в случае получения травм и увечий;
- в результате применения централизованной системы управления появляется возможность ориентации на безлюдную технологию то есть работы в течении нескольких смен без оператора а также повысить коэффициент загрузки оборудования.
При получении заготовки из поковки на токарнй операции задействованы два токарных полуавтомата.Расчитаем себестоимость обработки при получении детали из трубы по сравнению с поковкой.
Часовые приведенные затраты определяем по формуле:
Сп.з=Сз+Сч.з+Ен(Кс+Кз)
где Сз – основная и дополнительная зарплата с начислениями Сз = 423 руб.
Сч.з – часовые затраты на эксплуатацию рабочего места Сч.з = 420 руб;
Ен – нормативный коэффициент экономической эффективности капитальных вложений Ен = 015;
Кс и Кз – удельные часовые капитальные вложения соответственно в станок и здание Кс = 717 руб Кз = 470 руб.
Сп.з = 423+420+015(717+470)=102105 руб.
Определяем технологическую себестоимость детали:
где Кв - коэффициент выполнения норм Кв = 13;
Со =102105157(6013) = 206 рубч.
ВЫБОР СПОСОБА ПОЛУЧЕНИЯ ЗАГОТОВКИ С ЭКОНОМИЧЕСКИМ ОБОСНОВАНИЕМ
Огромную роль в производстве играет метод получения исходной заготовки под механическую обработку наружных и внутренних колец подшипников. Наиболее распространёнными методами получения заготовок из колец подшипников на Минском подшипниковом заводе являются:
точение из труб изготовленных горячей или холодной прокаткой;
изготовление заготовок кузнечным способом из горячекатаного прутка (штамповка на ГКМ штамповочных молотах и свободная ковка на молотах с последующей раскаткой на раскаточных машинах).
Методом вытачивания колец подшипников из трубной заготовки изготавливаются до 50% всех выпускаемых подшипников размерной группы наружного диаметра до180мм. Данный метод в сравнении с кузнечным способом производства заготовок колец подшипников до180 мм диаметром на ГКМ имеет более высокий коэффициент использования металла требует меньших трудовых затрат.
Однако применение дорогостоящих труб с ценой в 16 – 18 раза превышающей цену горячекатаного круглого проката не позволяет увеличение коэффициента использования металла (КИМ) более чем на 05 при производстве шариковых и роликосферических подшипников а при производстве конических подшипников до 03. Низкий КИМ объясняется тем что только при отрезании кольца из трубы особенно при изготовлении колец шариковых подшипников малой ширины до 20% металла превращается в стружку. Кроме этого процесс резания отрезным резцом из стали Р6М5 малопроизводительный.
Для вытачивания колец применяют дорогие многошпиндельные трубные автоматы с низкой производительностью из-за наличия в многоинструментальной наладке отрезного резца.
Вышеуказанные недостатки методов производства заготовок колец подшипников создали предпосылки для разработки и внедрения более прогрессивных способов высокопроизводительного автоматизированного труда металлосберегающих технологий с одновременным улучшением экологических условий.
Углубленный анализ состояния затрат на производство подшипников показал что необходим переход от трубной заготовки колец подшипников на заготовку полученную методом горячего деформирования с увеличением КИМ до 065 за счёт использования образующихся отходов снижением размерности используемого проката а именно из прутка одного диаметра изготавливать поковки различных размеров.
Заготовку детали "Кольцо внутреннее” по существующему техпроцессу получают из трубы. В таблице 5.1 приведены основные экономические показатели для колец.
Таблица 5.1 - Экономические показатели.
Стоимость заготовки руб.
Стоимость 1т стружки руб.
Стоимость заготовки (расчёт выполнен в ценах на 2005г.) из проката определяется по формуле:
где М - затраты на материал заготовки;
SСо.з – технологическая себестоимость операций правки калибровки резки.
где S - базовая стоимость одной тонны заготовок S = 2200700 руб;
Q - масса заготовки кг; Q=068 кг;
q - масса детали кг q=0555 кг;
Sотх - стоимость одной тонны отходов руб.
М=06822007001000-(068-0555)454131000=14908 руб.
Sзаг = 14908+717 = 22078 руб.
Заготовку детали "Кольцо внутреннее" можно получить штамповкой на ГКМ1200 с последующей раскаткой на РМ-300. При этом заготовка приближенна по своим габаритам и форме к готовой детали. После раскатки заготовку подвергают отжигу до твердости ТШ-2М ГОСТ23677-79 производят очистку и снятие заусенцев. В таблице 2.2 приведены основные экономические показатели.
Таблица 5.2 - Экономические показатели
Стоимость заготовки (расчёт выполнен в ценах на 2005г.) получаемых на ГКМ определяется по формуле:
Sзаг = (Ci1000Qk)-(Q-q)-Sотх1000]
Q - масса заготовки кг; Q=076 кг;
k - коэффициент зависящий от точности группы сложности массы марки материала и объема производства заготовок k = 162 [1с.33-34].
Sqtx -стоимость одной тонны отходов руб.
Sзаг=07616188891000162-(076-0555)424131000=19845 руб.
ВЫВОД: Так как экономический эффект от внедрения нового метода получения заготовки не перекроет затрат на внедрение метода рациональнее оставить базовый вариант производства заготовок.
ПРОЕКТИРОВАНИЕ ТЕХНОЛОГИЧЕСКОГО ПРОЦЕССА
Технологический процесс получения детали «Кольцо подшипника внутреннее 53520.02» используемый на заводе является оптимальным в данных условиях производства т.к. рассматривается специализированное подшипниковое предприятие на котором используется автоматическое оборудование что полностью соответствует организации производства на заводе. Станки достаточно новые удовлетворяют требованиям по точности и жесткости в полной мере. Применительно к этой детали станки имеют низкий коэффициент загрузки но на практике они догружаются аналогичными деталями другого типоразмера. Станки способны к переналадке у них автоматизирована погрузка и выгрузка заготовок. Практически по всем показателям можно говорить об оптимальности производства.
Определим для размеров мм и 46-006 мм припуски на механическую обработку расчетно-аналитическим способом согласно [1] а на остальные поверхности назначим по ГОСТ7505-89.
Заготовкой является трубный прокат 130 мм.
Расчёт припусков на обработку отверстия мм ведём в форме табл.7.1 в которую последовательно записываем технологический маршрут обработки отверстия и все значения элементов припуска. Методика расчета изложена в [1].
Расчетная формула для определения припуска для i – перехода:
где Rz – высота неровностей профиля мкм;
h – глубина дефектного слоя мкм;
ρ – суммарное значение пространственных отклонений мкм;
e – погрешность установки мкм.
Суммарное пространственное отклонений заготовки находим по формуле
где ρсм – погрешность смещения ρсм = 400 мкм;
ρэксц – погрешность эксцентричности ρэксц = 600 мкм;
Остаточные пространственные отклонения
где n – количество переходов механической обработки;
ρзаг – исходное отклонение заготовки;
kyi – коэффициент уменьшения погрешности.
Остаточное пространственное отклонение для каждого перехода
Погрешность установки заготовки на выполняемой операции или переходе
где e з e б e пр – погрешность соответственно базирования закрепления положения заготовки мм.
При черновом растачивании
eб=0;[1 с.106 табл.4.33];
eз=440 так как нет никаких зажимающих сил;
Таким образом на первом переходе
При чистовом растачивании
eз=90;[1 с.110 табл.4.35];
На втором же переходе
eз=45 так как нет никаких зажимающих сил;
Таким образом на третьем переходе
Таблица 7.1 - Расчет припусков и предельных размеров по технологическим переходам на обработку отверстия
Расчетный размер dp мм
Предельное значение припуска мм
Условие zmax-zmin= max- min выполняется следовательно расчет припусков произведен верно.
В завершение расчёта строим схему расположения припусков и допусков на обработку отверстия мм ( рис.6.1 ).
Рис. 6.1 - Схема расположения припусков и допусков на обработку отверстия
При расчёте припуска на торец (размер 46-0062) составляем расчётную табл.7.2 в которую последовательно записываем значения элементов припуска.
где ρкор – погрешность по несоосности мкм;[1табл.5];
Остаточное пространственное отклонение для последующего перехода
При следующих переходах погрешность установки равна 0.
Расчет припусков и предельных размеров по технологическим переходам на обработку торца 46-0062 мм
Расчетный размер Lp мм
max- min=062-0062=0558 мм.
В завершение расчёта строим схему расположения припусков и допусков на обработку торца 46-0062 мм ( рис.6.2 ).
Рис. 6.2 - Схема расположения припусков и допусков на обработку торца 46-0062.
ОПРЕДЕЛЕНИЕ РЕЖИМОВ РЕЗАНИЯ
Рассчитаем режимы резания для перехода операции 010 – токарной расчетно-аналитическим методом изложенным в [4]. На данной операции растачивается отверстие 996-02 . Обработка ведется резцом с материалом режущей части Т15К6. Обработка ведется по сплошному металлу.
Глубина резания t=2 мм
Подача S = 02 ммоб. [4 табл. 12 стр. 267]
где Сv = 420; х = 015; y = 020; m = 020 [4 табл. 17 стр. 269];
Т – период стойкости Т = 50 мин.
Kv – поправочный коэффициент
где Kмv – коэффициент учитывающий обрабатываемый материал Kмv = 13;
Kuv – коэффициент учитывающий инструментальный материал Kuv = 10;
По паспорту станка принимаем n = 500 мин-1 тогда скорость резания
В связи с тем что в нашем случае растачивание принимаем скорость на 10% меньше полученной:
где Ср =204; х = 10; y = 075; n=0.
kp – коэффициент учитывающий влияние качества обрабатываемого материала на силовые зависимости.
где Lp.x – длина рабочего хода
Lр.х. = Lрез. + y + Lдоп.
где Lрез. – длина обработки Lрез. = 47 мм;
у – длина подвода перебега врезания инструмента у = 5 мм [5];
Рассчитаем режимы резания для операции 015 – круглошлифовальная согласно методики изложенной в литературном источнике [5]. На данной операции производится шлифование шеек вала под подшипник.
Обработка ведется шлифовальным кругом ПП 600×80×305 23 АНС27К1 ГОСТ 4785-80.
Расчет скорости шлифовального круга:
где D=600 мм – диаметр круга;
nкр – число оборотов круга по станку. Принимаем nкр=1000 обмин;
Выбираем характеристики шлифовального круга учитывая класс точности – 7 точность обработки =005 мм обрабатываемый материал – сталь ШХ15СГ скорость шлифовального круга кр=314 мс а также твердость поверхности шейки – 56 62 HRC: Э5 40 СМ2 6-7 Б.
Расчет скорости в ммин и числа оборотов детали в минуту:
а) определение рекомендуемой нормативами скорости вращения детали
з=35 40 ммин. Принимаем з=35 ммин;
б) расчет числа оборотов шпинделя соответствующего рекомендуемой скорости и уточнение его паспорту станка:
где d – диаметр детали;
Принимаем по паспорту станка np=90 обмин;
в) уточнение скорости вращения детали по принятым оборотам шпинделя:
Выбор минутной поперечной подачи Sм в мммин учитывая диаметр детали d=12227 мм ширину шлифования b=46 мм скорость круга кр=314 мс припуск на сторону a=04 мм точность обработки =005 мм диаметр круга D=600 мм количество одновременно работающих кругов q=1 характер поверхности (гладкая шлицевая) расстояние от шлифуемой шейки до опоры lоп=86 мм а также то что шлифование происходит в ручном режиме:
К1 – коэффициент зависящий от обрабатываемого материала и от скорости круга К1=1;
К2 – коэффициент зависящий от припуска и точности К1=12;
К3 – коэффициент зависящий от диаметра круга количества кругов и характера поверхности К1=11;
Определение времени выхаживания tвых в мин учитывая чистоту обработки Ra=063 мкм точность обработки =005 мм ширину шлифования b=46 мм диаметр детали d=122 мм а также наличие на поверхности шпоночных канавок срезов и т.д.:
Определение величины слоя снимаемого при выхаживании авых в мм учитывая минутную поперечную подачу Sм=066 мммин а также время выхаживания tвых=0195 мин:
Определение машинного времени tм в мин учитывая все вышеперечисленные параметры.
Для остальных операций расчёт производим аналогично и результаты сводим в таблицу 8.1.
Наименова-ние операции
Скорость резания и число оборотов шпинделя
Точить наружный диаметр
Расточить внутренний диаметр
Точить внутреннюю фаску предварительно
Точить дорожку качения
Точить канавку на наружном диаметре
Таблица 8.1 - Сводные данные по режимам резания
Продолжение таблицы 8.1
Точить внутреннюю фаску
Точить наружную фаску в размер
Точить внутреннюю противобаз. фаску
Пила дисковая ГОСТ 4047-82
Шлифовать одновременно 2 торца
0 Круглошлифовальная
Шлифовать роликовые дорожки
5 Внутришлифовальная
Шлифовать внутренний диаметр
Шлифовать роликовые дорожки оконч.
Суперфинишировать роликовые дорожки оконч.
ОПРЕДЕЛЕНИЕ НОРМЫ ВРЕМЕНИ ДЛЯ ОПЕРАЦИЙ
Технические нормы времени в условиях массового и серийного производств устанавливаются расчетно-аналитическим методом.
В серийном производстве норма штучно-калькуляционного времени определяется по формуле:
где Тшт – норма штучного времени:
Тшт = То + Тв + Тоб + Тот;
где То –основное время мин; Тв – вспомогательное время мин. Вспомогательное время состоит из затрат времени на отдельные приемы: Тв = Тус + Тзо + Туп + Тиз; Тус – время на установку и снятие детали мин; Тзо – время на закрепление и открепление детали мин; Туп – время на приемы управления мин; Тиз – время на измерение детали мин; Тоб – время на обслуживание рабочего места мин. Складывается из времени на организационное и времени на техническое обслуживание рабочего места; Тот – время перерывов на отдых и личные надобности.
Рассчитаем норму штучно-калькуляционного времени для торцешлифовальной операции 010 выполняемой на шлифовальном автомате 3344АЕ. Производство среднесерийное размер партии деталей равен 50000 шт.детали равна 085 кг. Деталь устанавливается в установочно-зажимное приспособление. Основное время равно 005 мин.
Нормативы времени принимаются по [6 прил. 5].
Определяем состав подготовительно-заключительного времени: установка детали на станок – 8 мин; на получение инструмента и приспособлений до начала и сдачу после окончания обработки – 7 мин.
Время на установку и снятие детали закрепление ее и открепление: Тус + Тзо = 008 мин.
Время затраченное на приемы управления: включить и выключить станок кнопкой – 001 мин; подвести шлифовальный круг к детали до появления искры – 002 мин.
Тогда Туп = 001+002 = 003 мин.
Время затраченное на измерение детали равно 011 мин. При 100% контролируемых деталей получим Тиз = 011 мин.
Вспомогательное время Тв = 003 + 008 + 011= 022 мин.
Оперативное время Топ = 022+091 =113 мин.
Время на обслуживание рабочего места и отдых составляет: затраты времени на техническое обслуживание рабочего места – 3% от основного времени; на организационное обслуживание рабочего места – 2% от оперативного времени.
Тоб.от = 091×003+113×002=005 мин.
Штучно-калькуляционное время:
Тш-к = 152084 + 091 + 022+ 003 =078 мин.
Таблица 9.1 - Сводная таблица технических норм времени по операциям мин
ОПРЕДЕЛЕНИЕ НЕОБХОДИМОГО КОЛИЧЕСТВА ОБОРУДОВАНИЯ И ПОСТРОЕНИЕ ГРАФИКОВ ЗАГРУЗКИ
Потребное количество единиц оборудования для данной операции определяется по формуле:
Fэ – эффективный годовой фонд времени работы единицы оборудования ч.
Расчетное количество единиц оборудования mp округляется в большую сторону до величины mпр.
Коэффициент загрузки станка определяется:
Коэффициент использования оборудования по основному (технологическому) времени определяется для серийного производства как отношение основного времени к штучно-калькуляционному времени:
Этот коэффициент характеризует уровень механизации технологической операции. Коэффициент использования станков по мощности привода представляет собой отношение необходимой мощности привода станка к фактической мощности установленного на станке привода главного движения:
Результаты расчетов сведем в табл. 10.1.
Таблица 10.1. - Расчет коэффициентов использования оборудования
В строке «Итого» записана математическая сумма значений колонки для Т0 Тшт-к mпр и среднее арифметическое для колонок з о м.
Для наглядности построим диаграммы загрузки оборудования загрузки оборудования по основному времени по мощности по стойкости режущего инструмента (рис. 7.4.1 – 7.4.4).
Рис. 10.1 – График загрузки оборудования
Рис. 10.2 – График загрузки оборудования по основному времени
е Рис. 10.3 – График загрузки оборудования по мощности
Рис. 10.4 – График загрузки по стойкости инструмента
РАСЧЕТ И ПРОЕКТИРОВАНИЕ ИНСТРУМЕНТА
В данном курсовом проекте необходимо спроектировать фасочный резец используемый на 005 токарной операции. Резец является наиболее распространенным инструментом в металлообрабатывающей промышленности. Он применяется при работе на токарных револьверных карусельных расточных строгальных долбежных станках токарных автоматах полуавтоматах и на многих других станках специального назначения. Многообразие применения резцов породило множество форм конструкций и геометрических параметров их которые меняются в зависимости от вида станка и рода выполняемой работы.
Резцы разделяются на следующие типы:
) по виду станков: а) токарные; б) строгальные; в) долбежные; г) резцы для автоматов и полуавтоматов; д) расточные для горизонтально-расточных станков; е) специальные для специальных станков; ж) фасонные;
) по виду обработки: а) проходные; б) подрезные; в) отрезные; г) прорезные; д) расточные; е) фасонные; ж) резьбонарезные; з) фасонные;
) по установке относительно детали: а) радиальные б) тангенциальные;
) по характеру обработки: а) обдирочные (черновые); б) чистовые; в) для тонкого точения;
) по сечению стержня: а) прямоугольные; б) квадратные; в) круглые;
) по конструкции г о л о в к и: а) прямые; б) отогнутые в) изогнутые; г) оттянутые;
) по направлению подачи: а) правые; б) левые;
) по способу изготовления: а) с головкой сделанной заодно целое со стержнем; б) с приваренной в стык головкой; в) с приваренной или припаянной пластинкой; г) с приваренной полоской; д) с наплавленной головкой; е) с головкой в виде сменной вставки снабженной пластинкой режущего материала.
) по роду материала: а) с пластинками из твердого сплава; б) из быстрорежущей стали; в) с пластинками из минералокерамики.
Все углы данного резца исполнены для обработки фаски внутреннего кольца подшипника. Напайная пластина резца выполнена со следующей геометрией:
Рис. 11.1 – Геометрия резца (разрез перпендикулярный к режущей кромке).
Вид сверху резца представлен на следующем рисунке:
Рис. 11.2 – Схема резца (вид сверху).
Геометрия резца выполнена для формирования фаски внутреннего кольца подшипника все углы являются обоснованными и обеспечивают нужные параметры фаски у кольца и наиболее благоприятные в данных условиях режимы резания.
РАСЧЁТ И ПРОЕКТИРОВАНИЕ ПРИСПОСОБЛЕНИЯ
В данном курсовом проекте необходимо спроектировать приспособление используемое на 010 операции – торцешлифовальной. Данное приспособление – плунжерный патрон - используется для зажима заготовки в нашем случае для зажима кольца подшипника. Эти устройства просты в изготовлении компактны позволяют изменять значение и направление зажимных сил обладают свойством самоторможения.
Расчет клиновых устройств сводится к определению соотношения сил привода Pпр и зажима W. При известном значении Pпр обеспечиваемая клиновым зажимом сила может определятся графически аналитически и расчетом по коэффициенту усиления [5].
Составляем схему к расчету приспособления:
Рис. 12.1 – Схема к расчету приспособления: 1 – заготовка; 2 – плунжер; 3 – клин.
Самоторможение клина обеспечивается при условии
где α – угол клина φ – угол трения; φ=arcctg () где – коэффициент трения.
При условии смазки и стальных плунжера и клина =004.
Сила привода Pпр определяется по формуле:
где Рz – сила резания Рz=700Н k – коэффициент запаса k=25.
По выбранной силе привода определяем параметры пневмоцилиндра: принимаем поршневой пневмоцилиндр двустороннего действия с односторонним штоком по ГОСТ15608-81: диаметр цилиндра 80 мм сила на штоке 63 кН скорость перемещения не более 05 мс.
Производим расчет приспособления на точность по методике изложенной в литературе [6].
При расчете приспособлений на точность суммарная погрешность при обработке детали не должна превышать величину допуска Т размера Т.
Суммарная погрешность зависит от ряда факторов и в общем случае может быть представлена выражением:
где yc- погрешность установки детали в приспособлении;
обР - погрешность обработки детали;
пр- расчетная погрешность приспособления.
Погрешность установки представляет собой отклонение фактического положения закрепленной детали в приспособлении от требуемого теоретического. Погрешность установки yc включает погрешности: базирования б закрепления 3 и положения детали в приспособлении п:
Погрешность положения n детали в приспособлении состоит из погрешностей: изготовления приспособления по выбранному параметру "np установки приспособления на станке у и положения детали из-за износа элементов приспособления и:
В результате для расчета точности приспособления пр можно использовать упрощенную формулу:
где Т — допуск выполняемого размера;
3 у к— соответственно погрешности: базирования закрепления установки приспособления на станке положения детали из-за износа установочных элементов приспособления и от перекоса (смещения) инструмента;
кт=1 12 - коэффициент учитывающий отклонение рассеяния значений составляющих величин от закона нормального распределения;
кт1 = 08 085 - коэффициент учитывающий уменьшение предельного значения погрешности базирования при работе на настроенных станках;
На основе полученного значения пр производится расчет размерной цепи приспособления. За замыкающее ее звено принимается погрешность по принятому параметру Т.
В каждом конкретном случае рекомендуется выполнять расчет погрешности установки приспособления на станке в зависимости от ее схемы и заданной точности изготовления посадочных элементов.
Таблица 11.1 - Точностной расчет приспособления
Шлифовальное приспособление
Установки приспособления
Допустимая погрешность изготовления приспособления
Точность обеспечивается.
ТЕХНИКО-ЭКОНОМИЧЕСКИЕ РАСЧЁТЫ
Рассчитаем стоимость операций механической обработки по методике изложенной в литературе [1]. Часовые приведенные затраты рассчитываются по формуле:
где Sз - основная и дополнительная зарплата с начислениями коп. ч; Sч.з - часовые затраты на эксплуатацию рабочего места коп.ч; Ен – нормативный коэффициент эффективности капитальных вложений равный в машиностроении 015; Кс Кз – удельные часовые капитальные вложения соответственно в станок и здание.
Основная и дополнительная зарплата с начислениями равна:
где e - коэффициент к часовой тарифной ставке равный 271. Он учитывает следующие виды выплат: за переработку норм – 8% за работу по технически обоснованным нормам – 20% премию станочника – 30% дополнительную зарплату – 11% налоги и отчисления на фонд заработной платы – 45%;
Стф – часовая тарифная ставка станочника соответствующего разряда тыс. руб.ч [1 табл. 8.8]; k – коэффициент учитывающий зарплату наладчика (если наладка станка в серийном производстве ведется без участия наладчика самим рабочим k принимается равным 1; в условиях массового производства – 11 115);×y – коэффициент штучного времени учитывающий оплату труда рабочего при многостаночном обслуживании при одном обслуживаемом станке равен 1.
Часовые затраты на эксплуатацию рабочего места равны:
где – практические часовые затраты на рабочем месте равны 446 копч [3 стр. 81]; kм – коэффициент показывающий во сколько раз затраты связанные с работой данного станка больше чем аналогичные расходы связанные с работой базового станка [4 прил. 4].
Удельные часовые капитальные вложения соответственно в станок и здание определяются:
где А – производственная площадь занимаемая станком с учетом проходов А = а× kа где а – площадь станка в плане м2; kа – коэффициент учитывающий дополнительную производственную площадь [4 с.84].
Технологическая себестоимость операции механической обработки равна:
где kв – коэффициент выполнения норм принимаемый равным 13.
Рассчитаем стоимость операций механической обработки и результаты сведем в табл. 12.1.
Таблица 12.1. - Определение стоимости операций механической обработки
Со руб. в ценах 1985 г
C0 руб.в ценах 2005 г.
Итого себестоимость механической обработки:
Технологическая себестоимость равна:
Ст = Sзаг + SСо = 2172+ 22265 = 244 тыс. руб.
Общее количество рабочих- станочников определяется по формуле:
R = SТш-к Nг (60×1816) = 583× 50000 (60×1816) =3 чел.
с учетом двухсменного режима работы R=6 человека.
Число наладчиков на проектируемом участке может быть принято из условия что один наладчик обслуживает 8 10 станков в смену:
Н = 016S mпi = 016 × 6 = 1 чел.
Годовой фонд заработной платы рабочих-станочников и наладчиков на одну операцию определяется:
Фзi = SзiТш-кi Nг 60.
Используя данные из табл. 12.1 рассчитаем по этой формуле фонд заработной платы. Получим годовой фонд заработной платы в размере 18 млн. руб.
Основные показатели сведем в табл. 12.2.
Таблица 12.2. - Основные технико-экономические показатели разработанного
технологического процесса
Наименование показателя
Наименование и номер детали
Годовой объем выпуска деталей шт.
Эффективный годовой фонд времени работы оборудования ч
Эффективный годовой фонд времени рабочего ч
Масса готовой детали кг
Коэффициент использования материала заготовки
Стоимость заготовки тыс. руб.
Себестоимость механической обработки детали тыс. руб.
Технологическая себестоимость детали тыс. руб.
Основное время по операциям мин
Штучно-калькуляционное время по операциям мин
Трудоемкость годовой программы выпуска деталей ч
Количество единиц производственного оборудования шт.
Средний коэффициент загрузки станков
Средний коэффициент использования оборудования по основному времени
Средний коэффициент использования оборудования по мощности
Число рабочих-станочников на две смены
Число наладчиков на две смены
Годовой фонд заработной платы станочников и наладчиков млн. руб.
Среднемесячная заработная плата рабочих тыс. руб.
В результате выполнения данного курсового проекта был разработан технологический процесс изготовления кольца подшипника.
В базовом проекте на операции 005 для токарной обработки колец на одной из позиций используется отрезной резец для отрезания заготовки от трубы. Это является нецелеособразным поэтому производим отрезание кольца дисковой пилой на станке с помощью специального приспособления.
В проекте просчитан вариант замены способа получения заготовки но расчеты показали нецелеособразность замены.
Таким образом годовой экономический эффект составил 75 млн. руб.
Проектирование технологических процессов механической обработки в машиностроении. Под ред. В.В.Бабука. – Мн.: “Вышэйшая школа” 1987. –256с.
Горбацевич А. Ф. Шкред В. А. Курсовое проектирование по технологии машиностроения. – Мн.: Выш. школа 1983. –256с.
Режимы резания металлов: Справочник. Ю.В.Бараноский и др.- М.: НИИТавтопром 1995. –406с.
Справочник технолога машиностроителя. В двух томах.Т1. Под ред. А.Г.Косиловой и Р.К.Мещерякова. М.: Машиностроение 1985. –656с.
Станочные приспособления: Справочник. В 2-х т. Ред. Совет: Б.Н. Вардашкин (пред.) и др.- М.: Машиностроение 1984-Т.1 Под ред. Б.Н. Вардашкина А.А. Шатилова 1984. 656с. ил.
Горохов В.А. Проектирование и расчет приспособлений. – Мн.: Выш. школа 1986. –238 с.
Ведомость курсового проекта.dwg

Задание на курсовое проектирование
Пояснительная записка
Технологический процесс механической
Чертёж приспособления
Чертежи операционных искизов
Чертёж режущего инструмента
Резец прорезной.dwg

мм. 2. Покрытие-lG*p. 3. Поверхности ø30k6 от покрытия предохранить.
БНТУ 05.221.06.01.01.000
не подвергающихся термо- обработке
допускаются следы омеднения. 14. Допускается верхнюю головку по размеру П не обрабатывать. 15. Допускается точеный слой цементации на стебле шатуна с последующим высоким отпуском стебля на ТВЧ участка стебля на длине Р
включающим пере- ходные зоны
образующиеся у головок шатуна.
Неуказанные пред. откл. по ОСТ.37.001. 246-82 2. Сортировать на группы селективности согласно таблицам 1 и 2. Допускаются размеры согласно таблице 1а и 2а до 01.01.88 г. 3. При наличие отклонения от круглости цилиндричности по размерам И и К на границе селективных группдеталь от- носить к группе по наименьшему диаметру. Замеры произво- дить при температуре t=20°±3°C 4. Поверхности канавок Л и М допускается не цементировать. 5. Штамповать уклоны
допуски на размеры неабработанных поверхностей и остатки облоя после обрезки по классу точ- ности Т3 ГОСТ 7505-89. 6. Технические требования на паковку по ГОСТ 8479-70.груп- па II. 7.Наличие трещин не допускается. 8. Маркировать группу селективности кркской согласно таб- лице 1 и 1а. 9. Маркировать группу селективности краской согласно таб- лице 2 и 2а. 10. Чеканить стебель
верхнюю и нижнюю головки шатуна в пределах допуска ±0
мм. 11. Допуск соосности наружной поверхности верхней головки относительно отв.6 указан для стороны противоположной технологической метке Н. 12. При непараллельности осей отв А и Б до 0
мм на длине 100мм допускается рихтовка с последующим отпуском.
Резец прорезной Сборочный чертёж
Пр. МНМЦ 68-4-2 ТУ48-21-674-80 2. H14
IT142 3. Маркировать обозначение и марку твёрдого сплава 4. Остальные технические требования по ГОСТ5688-61 5. Тип 53614К.02
Сталь45 ГОСТ 1050-88
Пластинка 001391-15К10
К1.doc
Наименование операции
Наименование марка материала
Сталь ШХ15 ГОСТ 801-78
Наименование оборудования
Контролируемые параметры
Наименование средств в ТО
Диаметр внутренний 3 непостоянство диаметра и средняя Прибор 299М 100
конусообразность не более 015 мм Эталон 8193-6024
Ширину 4 непостоянство ширины не более 015 мм Прибор В-902М 100
Эталон 10ИГП; 8190-5065-02
Непрямолинейность торца не более 007 мм Линейка ЛД-0-200 100
Диаметр дорожки качения 1 непостоянство диаметра не более Прибор Д-312М; 10ИГП; 100
6 мм Эталон 8190-5065-02
Операционная карта технического контроля
ГОСТ 3.1502-85 Форма 2а
Размеры 2 10 Шаблон 8354-4151
Диаметр наружный 6 непостоянство диаметра не более 016 мм Прибор Д-312М; 10ИГП; 100
Радиальное биение поверхности А относительно поверхности Б Прибор 299 М; 10ИГП 100
Биение поверхности Б относительно базового торца не более 100
Кольцо 125 8125-7186
Нутромер НИ 100-160 ГОСТ 862-82
Координаты фасок 5 7 8 9 Приспособление 8166-4006 100
Шероховатость обработанных поверхностей Образец шероховатости 100
Глубина отводных рисок не более 005 мм Прибор В-902М; ИЧ-10 100
Наконечник 8071-4001
Наконечник 8071-7088
М1.doc
Сталь ШХ15 ГОСТ 801-78
Код наименование операции
Обозначение документа
Код наименование оборудования
005 4110 Транспортная
010 4110 Токарная СТИ по ОТ №63
Токарный авт. КСА4-125-245 19149 4 1р 1 1 1 1 39 102
Установить и закрепить трубу в шпинделе станка
Точить наружный диаметр выдерживая размер 1
Цанга подающая 9000-9510-11; Цанга зажимная 9000-6013-04; Кольцо направляющее 9001-7951-03; Кольцо направляющее 9001-7950-03;
Державка 6720-4023; Резец Т15К6 035-2100-1311 СТП 930-1182-80
Расточить внутренний диаметр выдерживая размеры 78
Державка 6720-4087; Резец Т15К6 035-2100-1312 СТП 930-1182-80
Точить внутреннюю фаску предварительно выдерживая размеры 25; 150
ГОСТ 3.1404-86 Форма 1б
Наименование детали сб. единицы или материала
Державка 6720-4054; Резец Т15К6 035-2100-1312 СТП 980-1182-80
Точить дорожку качения выдерживая размеры 12276+02; 125
Приспособление 7910-41110; Резец Т15К6 035-2100-1484 СТП 980-1182-80
Расточить внутренний диаметр выдерживая размер 796-02
Державка 6720-4088; Резец Т15К6 035-2100-1311 СТП 980-1182-80
Точить канавку на наружном диаметре
Державка 6720-4081; Резец Т15К6 154-4069 СТП 980-1182-80
Державка 6702-4074; Резец Т15К6 035-2100-1311 СТП 980-1184-80
Точить внутреннюю фаску выдерживая размеры 29+19; 21+44 150
Державка 6702-4059; Резец 2136-6061; Пластина И07 R56 Т14К6
Точить наружную фаску выдерживая размеры R28
Державка 6702-4057; Резец 2136-6058; Пластина И07 R56 Т14К6
Точить дорожку качения
Державка 6702-4113; Резец Т15К6 2154-4103 СТП 980-1184-80
Точить внутреннюю противобазовую фаску выдерживая размеры 21+44; 22030’
Приспособление 7910-4066; Державка 7910-40661-01; Толкатель 7910-4077; Плита 7910-4076; Резец 2154-4011
Отрезать кольцо выдерживая размер 333+02
Державка 6705-4113; Резец 2130-4008
015 4130 Торцешлифовальная КТМ6014100001 КТМ2014100001 СТИ по ОТ №76
Торцешлифовальный авт. 3344АЕ 19630 4 1р 1 1 1 1
020 4131 Круглошлифовальная КТМ6014100002 КТМ2014100002 СТИ по ОТ №76
Круглошлифовальный авт. SVAAGL 1255 РС 19630 4 1р 1 1 1 1
025 4132 Внутришлифовальная КТМ6014100004 КТМ2014100004 СТИ по ОТ №76
Внутришлифовальный авт. SIV 41 САС 19630 4 1р 1 1 1 1
030 4131 Круглошлифовальная КТМ6014100003 КТМ2014100003 СТИ по ОТ №76
035 4132 Внутришлифовальная КТМ6014100004 КТМ2014100004 СТИ по ОТ №76
040 4135 Суперфинишная КТМ6014100005 КТМ2014100005 СТИ по ОТ №76
Суперфинишный авт. SF-L-21B 19630 4 1р 1 1 1 1
5 0130 Промывка СТИ по ОТ №105
6 0210 Контрольная КТМ6010200001 КТМ2010200001 СТИ по ОТ №46
037 4110 Транспортная
030.frw

025.frw

контроль.frw

020.frw

015.frw

010.frw

Титульник.doc
МИНИСТЕРСТВО ОБРАЗОВАНИЯ РЕСПУБЛИКИ БЕЛАРУСЬ
Руководитель: Бохан С.Г.
НА ТЕХНОЛОГИЧЕСКИЙ ПРОЦЕСС МЕХАНИЧЕСКОЙ ОБРАБОТКИ ДЕТАЛИ
КОЛЬЦО ПОДШИПНИКА ВНУТРЕННЕЕ 53516.02
ГОСТ 3.1117-81 Форма 2
КИ.dwg

О1.doc
Наименование операции
Сталь ШХ15 ГОСТ 801-78
Оборудование устройство ЧПУ
Обозначение программы
Загрузить детали в лоток
Шлифовать одновременно 2 торца выдерживая размер 1
Линейка верхняя; Линейка нижняя; Карандаш; Звездочка; Круг шлифовальный ПП 600×80×305 23 АНС27К1 ГОСТ 4785-80
Мера установочная 10ИГП 1ИГП ГОСТ 520-89;
Образец шероховатости РД 37.006.106-90
Контроль размеров – 100%
Снять деталь и уложить в тару
Операционная карта механической обработки
Загрузить детали в лоток
Шлифовать роликовые дорожки выдерживая размер 1 предварительно
Устройство башмачное; Башмак; Насадка; Круг шлифовальный ПП 160×60×80 23 АНС27К1 ГОСТ 4785-80
Шаблон КИП Д312М РД 37.006.100-90
Снять детали с лотка уложить в тару
Шлифовать внутренний диаметр выдерживая размер 1 предварительно
Опора; Башмак; Насадка; Круг шлифовальный ПП 60×20×25 23 25А16СМ2К ГОСТ 4785-80
Прибор Сутроник РД 37.006.106-90
Шлифовать роликовые дорожки выдерживая размер 1 окончательно
Суперфинишировать дорожки качения выдерживая размер 1 окончательно
Эскизы.dwg

мм. 2. Покрытие-lG*p. 3. Поверхности ø30k6 от покрытия предохранить.
БНТУ 05.221.06.01.01.000
не подвергающихся термо- обработке
допускаются следы омеднения. 14. Допускается верхнюю головку по размеру П не обрабатывать. 15. Допускается точеный слой цементации на стебле шатуна с последующим высоким отпуском стебля на ТВЧ участка стебля на длине Р
включающим пере- ходные зоны
образующиеся у головок шатуна.
Неуказанные пред. откл. по ОСТ.37.001. 246-82 2. Сортировать на группы селективности согласно таблицам 1 и 2. Допускаются размеры согласно таблице 1а и 2а до 01.01.88 г. 3. При наличие отклонения от круглости цилиндричности по размерам И и К на границе селективных группдеталь от- носить к группе по наименьшему диаметру. Замеры произво- дить при температуре t=20°±3°C 4. Поверхности канавок Л и М допускается не цементировать. 5. Штамповать уклоны
допуски на размеры неабработанных поверхностей и остатки облоя после обрезки по классу точ- ности Т3 ГОСТ 7505-89. 6. Технические требования на паковку по ГОСТ 8479-70.груп- па II. 7.Наличие трещин не допускается. 8. Маркировать группу селективности кркской согласно таб- лице 1 и 1а. 9. Маркировать группу селективности краской согласно таб- лице 2 и 2а. 10. Чеканить стебель
верхнюю и нижнюю головки шатуна в пределах допуска ±0
мм. 11. Допуск соосности наружной поверхности верхней головки относительно отв.6 указан для стороны противоположной технологической метке Н. 12. При непараллельности осей отв А и Б до 0
мм на длине 100мм допускается рихтовка с последующим отпуском.
Операция 010 - Токарная Позиция I Переход 2
Операция 010 - Токарная Позиция I Переход 3
Операция 010 - Токарная Позиция II Переход 7
Точить наружный профиль
Точить внутренний профиль
выдерживая размеры 2
Операция 010 - Токарная Позиция III Переход 8
Токарный автомат КСА4-125-245
Наименование и модель станка
Операция 025 - Внутришлифовальная
Операция 020 - Круглошлифовальная
Шлифовать роликовые дорожки
Шлифовать поверхность
Операция 015 - Торцешлифовальная
Операция 030 - Круглошлифовальная
Кафедра "Технология машиностроения
ГОСТ 3.1105-84 Форма 7
Приспособление.dwg

мм. 2. Покрытие-lG*p. 3. Поверхности ø30k6 от покрытия предохранить.
БНТУ 05.221.06.01.01.000
не подвергающихся термо- обработке
допускаются следы омеднения. 14. Допускается верхнюю головку по размеру П не обрабатывать. 15. Допускается точеный слой цементации на стебле шатуна с последующим высоким отпуском стебля на ТВЧ участка стебля на длине Р
включающим пере- ходные зоны
образующиеся у головок шатуна.
Неуказанные пред. откл. по ОСТ.37.001. 246-82 2. Сортировать на группы селективности согласно таблицам 1 и 2. Допускаются размеры согласно таблице 1а и 2а до 01.01.88 г. 3. При наличие отклонения от круглости цилиндричности по размерам И и К на границе селективных группдеталь от- носить к группе по наименьшему диаметру. Замеры произво- дить при температуре t=20°±3°C 4. Поверхности канавок Л и М допускается не цементировать. 5. Штамповать уклоны
допуски на размеры неабработанных поверхностей и остатки облоя после обрезки по классу точ- ности Т3 ГОСТ 7505-89. 6. Технические требования на паковку по ГОСТ 8479-70.груп- па II. 7.Наличие трещин не допускается. 8. Маркировать группу селективности кркской согласно таб- лице 1 и 1а. 9. Маркировать группу селективности краской согласно таб- лице 2 и 2а. 10. Чеканить стебель
верхнюю и нижнюю головки шатуна в пределах допуска ±0
мм. 11. Допуск соосности наружной поверхности верхней головки относительно отв.6 указан для стороны противоположной технологической метке Н. 12. При непараллельности осей отв А и Б до 0
мм на длине 100мм допускается рихтовка с последующим отпуском.
Устройство для обработки внутренних фасонных поверхностей Сборочный чертёж
Сталь45 ГОСТ 1050-88
Прокладка 45h14*40h14
Болт М10-6gx20.56.05
Винт М16-6gx60.56.05
Винт В М6-6gx6.56.05
Винт В М6-6gx12.56.05
Винт В М3-6gx12.56.05
Винт В М6-6gx16.56.05
Подшипник упорный 8105
Переменные данные для исполнения
Размеры для справок. 2. Обеспечить размер Д в конце рабочего хода. 3. При регулировке устройства выход выход канавки Г за торец Е не допускается. 4. Перед эксплуатацией устройство наполнить смазкой ЦИАТИМ 201 ГОСТ6267-74. В процессе эксплуатации смазывать не реже 1 раза в месяц.
Кольцо.dwg

мм. 2. Покрытие-lG*p. 3. Поверхности ø30k6 от покрытия предохранить.
БНТУ 05.221.06.01.01.000
не подвергающихся термо- обработке
допускаются следы омеднения. 14. Допускается верхнюю головку по размеру П не обрабатывать. 15. Допускается точеный слой цементации на стебле шатуна с последующим высоким отпуском стебля на ТВЧ участка стебля на длине Р
включающим пере- ходные зоны
образующиеся у головок шатуна.
Неуказанные пред. откл. по ОСТ.37.001. 246-82 2. Сортировать на группы селективности согласно таблицам 1 и 2. Допускаются размеры согласно таблице 1а и 2а до 01.01.88 г. 3. При наличие отклонения от круглости цилиндричности по размерам И и К на границе селективных группдеталь от- носить к группе по наименьшему диаметру. Замеры произво- дить при температуре t=20°±3°C 4. Поверхности канавок Л и М допускается не цементировать. 5. Штамповать уклоны
допуски на размеры неабработанных поверхностей и остатки облоя после обрезки по классу точ- ности Т3 ГОСТ 7505-89. 6. Технические требования на паковку по ГОСТ 8479-70.груп- па II. 7.Наличие трещин не допускается. 8. Маркировать группу селективности кркской согласно таб- лице 1 и 1а. 9. Маркировать группу селективности краской согласно таб- лице 2 и 2а. 10. Чеканить стебель
верхнюю и нижнюю головки шатуна в пределах допуска ±0
мм. 11. Допуск соосности наружной поверхности верхней головки относительно отв.6 указан для стороны противоположной технологической метке Н. 12. При непараллельности осей отв А и Б до 0
мм на длине 100мм допускается рихтовка с последующим отпуском.
Твёрдость 62 65 HRCэ. i0
Радиальное биение дорожек качения относительно друг друга 13мкм. 4. Биение базового торца относительно отверстия не более 0
2мм. 5. Маркировать: 53516.
Сталь ШХ15 ГОСТ801-78
Рекомендуемые чертежи
- 24.01.2023
- 24.01.2023
- 24.01.2023
- 13.05.2022
- 25.01.2023
- 25.05.2024
- 24.01.2023