Технологический процесс механической обработки детали Переходник




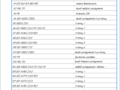
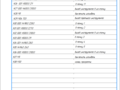
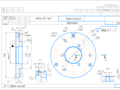
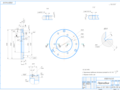
- Добавлен: 24.01.2023
- Размер: 1 MB
- Закачек: 0
Описание
Состав проекта
![]() |
![]() |
![]() |
![]() ![]() ![]() ![]() |
![]() ![]() ![]() ![]() |
![]() |
![]() ![]() ![]() |
![]() |
![]() |
![]() ![]() ![]() ![]() |
![]() |
![]() |
![]() ![]() ![]() ![]() |
![]() ![]() ![]() ![]() |
![]() |
![]() |
![]() ![]() ![]() ![]() |
![]() ![]() ![]() ![]() |
![]() ![]() ![]() ![]() |
![]() |
![]() ![]() ![]() ![]() |
![]() ![]() ![]() ![]() |
![]() |
![]() ![]() ![]() ![]() |
![]() ![]() ![]() ![]() |
![]() ![]() ![]() ![]() |
![]() ![]() ![]() ![]() |
![]() ![]() ![]() ![]() |
![]() |
![]() |
![]() |
![]() |
![]() |
![]() |
![]() |
![]() |
![]() |
![]() |
![]() |
![]() |
![]() |
![]() |
![]() |
![]() |
![]() |
![]() |
![]() ![]() ![]() ![]() |
![]() ![]() ![]() |
![]() |
![]() ![]() ![]() |
![]() ![]() ![]() |
![]() ![]() ![]() |
![]() |
![]() |
![]() ![]() ![]() |
![]() ![]() ![]() |
Дополнительная информация
Чертёж детали..cdw

Чертёж заготовки..cdw

РТК 4.cdw

РТК 3.cdw

картак кодирования стр1.cdw

РТК 2.cdw

картак кодирования стр2.cdw

РТК 1.cdw

040_Карта_Эскизов.cdw

030_Карта_Эскизов.cdw

010_Карта_Эскизов.cdw

015_Карта_Эскизов.cdw

045_Карта_Эскизов.cdw

020_Карта_Эскизов.cdw

025_Карта_Эскизов.cdw

065_Карта_Контроля.cdw

Рекомендуемые чертежи
- 07.09.2016
- 02.05.2022
- 04.11.2022
Свободное скачивание на сегодня
- 06.06.2020
Другие проекты
- 25.01.2023