Технологический процесс изготовления вала-шестерни




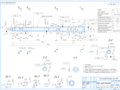
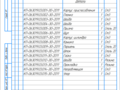
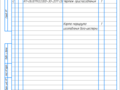
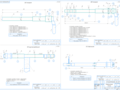
- Добавлен: 24.01.2023
- Размер: 1 MB
- Закачек: 1
Описание
Технологический процесс изготовления вала-шестерни
Состав проекта
![]() |
![]() |
![]() |
![]() |
![]() ![]() ![]() |
![]() ![]() ![]() ![]() |
![]() ![]() ![]() |
![]() |
![]() |
![]() |
![]() |
![]() |
![]() ![]() ![]() ![]() |
![]() ![]() ![]() ![]() |
![]() ![]() ![]() ![]() |
![]() ![]() ![]() ![]() |
![]() |
![]() ![]() ![]() ![]() |
![]() ![]() ![]() ![]() |
![]() |
![]() ![]() ![]() |
![]() ![]() ![]() |
![]() |
![]() |
![]() ![]() ![]() |
![]() ![]() ![]() |
![]() ![]() ![]() |
![]() ![]() ![]() |
![]() ![]() ![]() |
![]() ![]() ![]() |
![]() ![]() ![]() ![]() |
Дополнительная информация
Содержание.docx
Анализ технологичности конструкции изделия9
Выбор заготовки и его экономическое обоснование 10
Анализ существующего технологического процесса 12
Выбор варианта технологического маршрута и его
технико-экономическое обоснование 16
Расчет режимов резания 19
Нормирование технологического процесса 23
Расчет и проектирование приспособления 25
Список литературы 33
Ведомость.spw

Пояснительная записка
КП-063019.01.000-ЗО-2011.
КП-063019.02.000-ЗО-2011
Чертеж приспособления
изготовления вала-шестерни
Реферат.docx
Руководитель работы – Лысов А.А.
Курсовая работа состоит из расчетно-пояснительной записки объемом 46 страниц; использовано 9 литературных источников. Графическая часть объемом 5 листов формата А1 включает чертеж детали узла приспособления и чертеж операционных эскизов. Приложение составляют маршрутные карты обработки детали.
Последовательность операций техпроцесса обеспечивает получение заданной точности и качества поверхностей.
Простая конфигурация детали позволила применить достаточно прогрессивные режимы резания простые и удобные приспособления высокопроизводительный в основном стандартный режущий инструмент.
В ходе курсовой работы применялась ЭВМ. В частности использовалось программное обеспечение:
Microsoft Word 2007 – пояснительная записка.
КОМПАС 3D V9 – графическая часть.
эскизы_лист_2.cdw

Фрезеровать на поверхности В паз
выдерживая размеры 1 и 4
выдерживая размеры 2
А. Установить заготовку в призматических тисках
Фрезеровать шпоночный паз на поверхности В
Фрезеровать шпоночный паз на поверхности Г
Вертикально-фрезерный
Фрезерный штрокоунивер.
А. Установить заготовку в центрах с переустановкой
Шлифовать поверхности А
Круг шлифовальный ПП250
Шлифовать поверхность Г окончательно с подшлифовкой
Шлифовать поверхность В окончательно
Шлифовать поверхность Б окончательно
Шлифовать поверхность А окончательно
Шлифовать поверхность Д окончательно
Сталь 40Х ГОСТ 4543-71
КП-063019.00.005-ЗО-2011
1 шпоночно-фрезерная
0 круглошлифовальная
Каретка.cdw

Спецификация.spw

Чертеж приспособления
КП-063019.03.001-ЗО-2011
Корпус приспособления
КП-063019.03.002-ЗО-2011
КП-063019.03.003-ЗО-2011
КП-063019.03.004-ЗО-2011
КП-063019.03.005-ЗО-2011
КП-063019.03.006-ЗО-2011
КП-063019.03.007-ЗО-2011
КП-063019.03.008-ЗО-2011
КП-063019.03.009-ЗО-2011
КП-063019.03.010-ЗО-2011
КП-063019.03.011-ЗО-2011
КП-063019.03.012-ЗО-2011
КП-063019.03.013-ЗО-2011
КП-063019.03.014-ЗО-2011
КП-063019.03.015-ЗО-2011
Винт М6х25 ГОСТ 1491-80
Винт М6х20 ГОСТ 1491-80
Винт М6х85 ГОСТ 1491-80
Гайка М8 ГОСТ 2524-70
Винт М6х16 ГОСТ 1478-75
Манжета 1-15х25 ГОСТ 8752-79
Шайба 6 65Г ГОСТ 6402-70
Шайба 8 65Г ГОСТ 6402-70
Шпилька М20 ГОСТ 22034
Штифт 6 m6х75 ГОСТ 3128
Штифт 6 m6х85 ГОСТ 3128-70
эскизы_лист_1.cdw

Вертикально-сверлильный
А. Установить заготовку
Точить поверхность В
Точить поверхность Б
выдерживая размеры 3 и 4
Точить поверхность А
выдерживая размеры 1 и 2
Б. Переустановить заготовку
Точить поверхность В на остаток
Точить поверхность Г
выдерживая размеры 6 и 7
А. Установить заготовку в центрах.
Точить поверхность А выдерживая размер 1 на проход
Точить поверхность Б выдерживая размеры 2 и 3
Точить поверхность В выдерживая размеры 4 и 5
Точить поверхность Г выдерживая размеры 6 и 7
Точить поверхность Д выдерживая размеры 8 и 9
Точить поверхность Е выдерживая размеры 10 и 11
Точить поверхность Ж выдерживая размер 12
Отступить от торца на размер 13
врезаться на размер 14 и точить
выдерживая размер 15
Резец упорный Т15К6 ГОСТ 18879-73
А. Установить заготовку в УСП
с коническим ховставиком по ГОСТ 10903-77
А. Установить заготовку в центрах с переустановкой
Шлифовать поверхности А
Круг шлифовальный ПП250
Сталь 40Х ГОСТ 4543-71
КП-063019.00.004-ЗО-2011
0 круглошлифовальная
16BT20.42.209.cdw

Степень точности по ГОСТ 1643-81
Средняя длина общей нормали
Радиус кривизны активного профиля
Обозначение чертежа сопряженного
КП-063019.01.000-ЗО-2011
Сталь 40Х ГОСТ 4543-71
Допуск непостоянства диаметра в поперечном и продольном
сечениях поверхности М 0
поверхностей Л и П - 0
по наружному диаметру обнизить на 0
Приспособление.cdw

Допустимое значение давления воздуха в магистрали 1 МПа
Утечка воздуха в местах стыка не допускается.
Движение штока должно осуществляться плавно
Чертеж приспособления
КП-063019.03.000-ЗО-2011
КП_ТМ.docx
Цель курсовой работы – привить навыки практического применения теоретических знаний для решения прикладных инженерных задач связанных с разработкой технологических процессов изготовления машиностроительных изделий включая выбор заготовки расчет припусков и межоперационных размеров выбор маршрутной и операционной технологии техническое нормирование выбор оборудования инструмента станочных приспособлений и технологической оснастки.
В процессе технологического проектирования приобретаются навыки обосновано принимать технические решения пользоваться справочной и нормативной литературой.
Анализ служебного назначения детали
Деталь 16ВТ20.42.209 представляет собой вал-шестерню входящий в сборочный узел «каретка» (рис.1.1). По технологическому признаку эта деталь относится к классам ступеньчатые валы и валы-шестерни. По длине деталь относится ко II группе (l=150 500 мм). По соотношению длинны и среднего диаметра – нежесткий вал (ld>12).
Рис.1.1 Узел в сборе.
Вал-шестерня устанавливается в корпус и служит для перемещения каретки. Деталь средних размеров и имеет следующие габаритные размеры: длинна – 339 мм наибольший диаметр – 36мм.детали - 07 кг.
Рис. 1.2 Обозначение позиций поверхностей детали
Поверхности 1 и 2 – торцы вала-шестерни; поверхности 3 4 5 6 26 – наружные цилиндрические поверхности вала-шестерни; поверхности 7 8 9 – внутренние цилиндрические поверхности вала-шестерни; 10 11 12 13 – фаски поверхностей 3 5 6 9 соответственно; 14 – наружная резьба; 15 – внутренняя резьба; 16 17 – шпоночные пазы на цилиндрических поверхностях 26 и 4 соответственно; 18 19 – канавки на поверхностях 6 и 5 соответственно; 20 21 – пазы; 22 23 24 – канавки; 25 – шестерня вала; 27 – отверстие 48 мм.
Поверхности 4 и 5 являются основными конструкторскими базами определяющими положение вала-шестерни в сборочном узле. К этим поверхности назначаются повышенные требования по точности и соответственно и шероховатости Ra125.
К поверхности 3 так же предъявляются повешенные требования по точности . Это обусловлено посадкой подшипника на эту поверхность.
Наружная резьба 14 (M20x15 – 8g) предназначена для закрепления вала-шестерни в узле.
Внутренняя резьба 15 (M12x125 – 7H) предназначена для вкручивания пробки в вал-шестерню.
В шпоночные пазы 16 17 устанавливаются шпонки 4х4х16. В шпоночный паз 16 устанавливается шпонка с помощью которой на вале закрепляется втулка со шлицами предназначенная для включения-отключения рукоятки поперечного перемещения суппорта. С помощью шпоночного паза 17 соединяются вал-шестерня и одна из составляющих лимба.
Пазы 20 21 служат для ограничения перемещения штока выключающего рукоятку поперечного перемещения суппорта.
Внутренней поверхностью 9 вал-шестерня соединяется с валом который непосредственно перемещает суппорт. Следовательно к этой поверхности предъявляются повешенные требования по точности . В отверстие 27 устанавливается шплинт для предотвращения проворачивания деталей относительно друг друга в соединении.
Во внутренней поверхности 8 устанавливается пружина. Повышенных требований к обработке этой поверхности не предъявляется.
Фаски 10 11 12 и 13 предназначены для облегчения сборки узла и предотвращения порезов рабочих об острые кромки.
Шестерня 25 служит для автоматического перемещения суппорта. Степень точность шестерни 25 8-В и твердость 45 54 HRC достигаемая закалкой ТВЧ обусловлены техническими требованиями предъявляемыми к работе данной детали в узле.
Проанализировав предъявляемые требования к точности размеров шероховатости поверхностей точности их взаимного расположения можно сделать вывод что все требования обусловлены служебным назначением конструктивных элементов вала-шестерни.
Материал заготовки Сталь 40Х. Твердость вала-шестерни 223 285 НВ обусловлена условиями работы детали в условиях постоянных либо периодически изменяющихся нагрузок. Так как заготовка не обладает требуемой твердостью то требуется ее улучшение.
Однако эту сталь может заменить Сталь 45Х либо Сталь 40Г2 которые так же применяются для изготовления валов и соответствуют предъявляемым требованиям.
Ниже приведены таблицы отражающие химический состав и механические свойства рассматриваемых материалов.
Табл. 1.1 Химический состав сталей 40Х 45Х 40Г2
Табл. 1.2 Механические свойства Стали 40Х
Предел прочности (закалка 860°С (масло) + отпуск 500°С (вода)) Мпа
Предел текучести (закалка 860°С (масло) + отпуск 500°С (вода)) Мпа
Твердость по Бринеллю (закалка 860°С (масло) + отпуск 500°С (вода)) НВ
Твердость по Бринеллю (отжиг) НВ
Температура ковки °С
Табл. 1.3 Механические свойства Стали 45Х
Предел прочности при растяжении (закалка 830°С (масло) + отпуск 300°С (вода)) Мпа
Предел прочности при растяжении (закалка 820°С (масло) + отпуск 600°С (вода)) Мпа
Предел текучести (закалка 830°С (масло) + отпуск 300°С (вода)) Мпа
Предел текучести (закалка 820°С (масло) + отпуск 600°С (вода)) Мпа
Твердость по Бринеллю (закалка 830°С (масло) + отпуск 300°С (вода)) НВ
Твердость по Бринеллю (закалка 820°С (масло) + отпуск 600°С (вода)) НВ
Табл. 1.4 Механические свойства Стали 40Г2
Предел прочности при растяжении (закалка 860°С (масло) + отпуск 650°С (возд.)) Мпа
Предел прочности при растяжении (закалка 850-870°С (масло) Мпа
Предел текучести (закалка 860°С (масло) + отпуск 650°С (возд.)) Мпа
Предел текучести (закалка 850-870°С (масло) Мпа
Твердость по Бринеллю (закалка 850-870°С (масло) НВ
Проанализировав свойства материалов и предъявляемые требования к твердости детали можно сделать вывод что выбранная сталь 40Х вполне удовлетворяет всем требованиям.
Анализ технологичности конструкции изделия
Проведем анализ технологичности конструкции детали по двум направлениям: технологическому контролю чертежей и технологическому анализу конструкции.
Изучив рабочий чертеж вала-шестерни можно сказать что в нем содержатся все необходимые сведения дающие полное представление о детали. Т. к. деталь является телом вращения то достаточно представить две проекции: вид слева и разрез а так же местные разрезы поверхностей имеющих шпоночные пазы и отверстия. Чертеж четко и однозначно объясняет конструкцию и конфигурацию детали. На чертеже указаны все размеры с отклонениями требуемая шероховатость обрабатываемых поверхностей а также допускаемые отклонения от правильности взаимного расположения поверхностей необходимые для изготовления вала-шестерни. Однако так как в 2002 году Международным советом по стандартизации метрологии и сертификации приняты изменения в обозначение шероховатости то обозначение шероховатости на рабочем чертеже выполненные по ГОСТ 2.789-73 необходимо заменить новыми обозначениями. Чертеж содержит данные о массе детали материале и виде заготовки.
Деталь имеет вид вала изготовленного из стали 40Х. Заготовка требует большого объёма механической обработки. Деталь не имеет труднодоступных мест для обработки и все поверхности могут быть получены производительными методами.
Таким образом проанализировав конструкцию детали на технологичность можно сделать вывод что в целом деталь является технологичной конструкция и материал дают возможность использовать производительные методы обработки.
Выбор заготовки и его экономическое обоснование
Показатели технологичности заготовок различают двух видов: качественные и количественные. Качественную оценку («хорошо – плохо» допустимо – недопустимо») получают сравнением двух и более вариантов заготовок. Критерием в этом случаи являются справочные данные и опыт технолога и конструктора. Количественные показатели дают возможность объективно и достаточно точно оценить технологичность сравниваемых заготовок.
Проведем анализ двух вариантов получения заготовок: из проката и методом ковки на молотах.
Деталь имеет вид вала изготовленного из стали 40Х. В предложенном предприятием технологическом процессе заготовку получают из проката (Рис. 3.1). Заготовка имеет длину 344 мм и диаметр 40 мм.заготовки – 34 кг.
Рис. 3.1 Заготовка из проката
Рассчитаем коэффициент использования металла:
где GД – масса готовой детали
GР – масса всего израсходованного металла.
Полученный низкий коэффициент использования металла обусловлен тем что заготовка требует большого объёма механической обработки.
Выбор такого вида заготовки можно аргументировать тем что такая заготовка может быть достаточно экономичной из-за низкой стоимости проката почти полного отсутствия подготовительных операций и возможности автоматизации процесса обработки.
Второй вариант заготовки – поковка (Рис 3.2). Заготовка имеет длину 345±2 мм и три ступени диаметрами 25±2 30±2 42±2 мм.заготовки – 184 кг.
Заготовка полученная ковкой имеет более высокий коэффициент использования металла по сравнению с заготовкой из проката. Это объясняется тем что форма данной заготовки больше приближена к форме готовой детали чем заготовка из проката. Такая заготовка уменьшает припуски на механическую обработку что в свою очередь уменьшает количество проходов и переходов механической обработки и тем снижает её стоимость.
Однако заготовка полученная ковкой будет иметь более высокую себестоимость чем заготовка из проката.
Анализ существующего технологического процесса
Технологический процесс рассматриваемой детали представляет собой совокупность операций направленных на получение детали в соответствии с требованиями размеров допусков параметров шероховатости точности формы и взаимного расположения поверхностей а также технических требований и других условий. Технологический процесс вала-шестерни составлен в соответствии с такими производственными условиями завода как тип производства метод получения заготовки наличие необходимого оборудования обеспечивающего получение требуемого качества обработки замена недостающего оборудования наиболее подходящим для получения детали без ухудшения параметров качества возможность изготовления оригинальных инструментов и приспособлений организация производства сроки изготовления и другие факторы. Проведем анализ технологического процесса.
Базовый технологический маршрут обработки данной детали представляет собой последовательность следующих операций обработки:
0 Фрезерно-центровальная
0 Технический контроль
0 Круглошлифовальная
1 Шпоночно-фрезерная
0 Центрошлифовальная
0 Внутришлифовальная
Это последовательность обеспечивает необходимую точность получаемых размеров и качество поверхностей. Сначала обрабатываются чистовые базы и снимается основная часть припуска. Затем идет точная обработка. Принятую в данном варианте техпроцесса общую последовательность обработки логически следует считать целесообразной так как при этом соблюдаются принципы постепенности формирования свойств обрабатываемой детали.
Проанализируем технологические возможности оборудования используемого на участке (табл. 4.1):
Табл. 4.1 Анализ технологических возможностей применяемого оборудования.
ленточно-отрезной 8544
токарно-револьверный 1365
токарно-винторезный 16К40П
круглошлифовальный 3М153
фрезерный широкоуниверс. 6Б75В
вертикально-сверлильный 2Н125
вертикально-фрезерный 6540
зубофрезерный полуавтомат 5К301П
внутрищлифовальный 3К227В
(* - оборудование предположительно используемое на предприятии)
Исходя из анализа технологических возможностей применяемого оборудования можно сделать следующие выводы: оборудование по базовому технологическому процессу выбрано рационально.
Для эффективного изменения технологического процесса необходимо проанализировать степень его автоматизации. Характеристика автоматизации технологического процесса показана в таблице 4.2
Табл. 4.2 Анализ механизации и автоматизации технологического процесса.
Анализ механизации и автоматизации технологического процесса выявил низкий уровень управления циклом обработки и степени автоматизации.
Производительность операций зависит от используемых приспособлений. Основные характеристики станочных приспособлений приведены в таблице 4.3
Табл. 4.3 Установочно-зажимные приспособления
Наименование приспособления
Тиски призматические
Патрон 3-х кулачковый
Патрон 3-х кулачковый люнет
Большинство приспособлений – специальные. За счет этого минимизировано время на установку и снятие заготовки.
Проанализировав установочно-зажимные приспособления можно предложить на токарных и шлифовальных операциях ручной зажим заменить на пневмо- гидроприводы что сократит вспомогательное время на зажим детали. Проектирование приспособления для фрезерования (операция 111) представлено в п. 10.
В технологическом процессе применяется стандартный покупной режущий инструмент за исключением инструмента для обработки отверстия 107 мм на длину l=200 225 мм. Для этой операции применяется специальное удлиненное сверло (107х500). Для сокращения времени на получение данного отверстия предложенный инструмент можно заменить на сверло одностороннего резания с внутренним подводом СОЖ (ТУ 2-035-655-79). Применение этого инструмента позволит увеличить скорость резания и улучшит отвод стружки.
Режимы резания достаточно высокие стоимость эксплуатации инструмента средняя. Обработка ведется с применением СОЖ что позволяет вести ее с высокими скоростями резания и сохранением оптимальных периодов стойкости инструмента.
Для контроля размерных и точностных параметров используется как универсальный так и специальный мерительный инструмент. Точность измерения достаточно высокая; годовые затраты на измерительный инструмент не большие; оснащенность измерительными средствами достаточная. Для контроля отклонений геометрического и позиционного характера используются специальные приспособления с индикаторами часового типа. Специальный мерительный инструмент позволяет уменьшить время на измерение.
Проанализировав данный технологический процесс сведя в таблицы наиболее значимые данные можно сделать следующие выводы:
Межоперационные размеры и допуски на эти размеры подобраны рационально.
Применяемые в основном универсальные установочно-зажимные приспособления обеспечивают механизацию операций однако вместо ручного зажима для уменьшения времени на установку и закрепление желательно использовать пневмо- или гидроприводы.
Выбор варианта технологического маршрута и его технико-экономическое обоснование
Технологический процесс вала-шестерни составлен в соответствии с такими производственными условиями завода как тип производства метод получения заготовки наличие необходимого оборудования обеспечивающего получение требуемого качества обработки замена недостающего оборудования наиболее подходящим для получения детали без ухудшения параметров качества возможность изготовления оригинальных инструментов и приспособлений организация производства сроки изготовления и другие факторы.
Рассмотрим некоторые операции механической обработки:
Деталь крепится в центрах с переустановкой.
Рис. 5.1 Эскиз обработки поверхностей на токарной операции (080)
Токарная операция 080 состоит из следующих переходов:
Крепить деталь в центра
Точить поверхность А выдерживая размер 1 на проход
Точить поверхность Б выдерживая размеры 2 и 3
Точить поверхность В выдерживая размеры 4 и 5
Точить поверхность Г выдерживая размеры 6 и 7
Точить поверхность Д выдерживая размеры 8 и 9
Точить поверхность Е выдерживая размеры 10 и 11
Переустановить деталь
Точить поверхность Б выдерживая размер 12
Отстунить от торца на размер 13 врезаться на размер 14 и точить
поверхность З выдерживая размер 15.
Рис. 5.1 Эскиз обработки поверхностей на круглошлифовальной операции (100)
Круглошлифовальная операция 100 состоит из следующих переходов:
Крепить деталь в центра с переустановкой
Шлифовать поверхности А Б В Г Д выдерживая размеры 1 2 3 4 и
Расчет режимов резания
Рассчитаем режимы резания для сверления отверстия 107 мм на l=225 230 мм на 070 операции данного технологического процесса.
Согласно технологическому процессу необходимо сверлить отверстия диаметром 107 мм обрабатываемый материал 40Х по ГОСТ 4543-71. Обработку будем вести на токарно-винторезном станке модели 16К40П. На нем осуществляется автоматическая подача. Принимаем удлиненное сверло спиральное из быстрорежущей стали с цилиндрическим хвостовиком по ГОСТ 886-77. Материал режущей части – быстрорежущая сталь Р6М5.
Параметры сверла: диаметр сверла d=107 мм длина сверла L=550 мм длина рабочей части l=175 мм.
Глубина резания. При сверлении глубина резания . Получаем .
Определение рациональной подачи. При сверлении отверстий без ограничивающих факторов выбираем максимально допустимую по прочности сверла подачу. При рассверливании отверстий подача рекомендованная для сверления может быть увеличена до 2 раз. При наличии ограничивающих факторов подачи при сверлении и рассверливании равны. Их определяют умножением табличного значения подачи на соответствующий поправочный коэффициент приведенный в примечании к таблице.
Выбираем из таблицы для диаметра 107 мм и твердости НВ=160-240 подачу S=017 ммоб.
Скорость резания при сверлении
Значения коэффициентов и показателей степени приводятся в [1 с. 279 табл. 29] а значения периода стойкости Т – в [1 с. 279 табл. 30].
Принимаем следующие значения коэффициентов показателей степени и периода стойкости:
Сv=70; q=040; y=070; m=020;Т=25 мин.
Общий поправочный коэффициент на скорость резания учитывающий фактические условия резания
- поправочный коэффициент учитывающий влияние физико-механических свойств обрабатываемого материала на скорость резания;
= 980 МПа (для стали 40Х);
= 1 - поправочный коэффициент учитывающий влияние инструментального материала на скорость резания;
= 1 - коэффициент учитывающий глубину резания.
Подставим численные значения в формулу для определения скорости резания:
Тогда частота вращения определится как:
После согласования с паспортом станка принимаем частоту вращения n=1250 обмин.
Тогда скорость резания определится как:
Рассчитаем мощность резания осевую силу.
Мощность резания кВт определяется по формуле: [1 с. 280]
где Мкр – крутящий момент Н·м.
Значения коэффициента и показателей степени в формуле приведены в [1 с. 281 табл. 32].
Подставим численные значения:
Таким образом мощность резания определится:
Осевая сила рассчитывается по формуле: [1 с. 277]
Подставим численные значения:
Рассчитаем режимы резания для сверления отверстия 15 мм на l=115 мм на 070 операции данного технологического процесса.
Согласно технологическому процессу необходимо сверлить отверстия диаметром 15 мм обрабатываемый материал 40Х по ГОСТ 4543-71. Обработку будем вести на токарно-винторезном станке модели 16К40П. На нем осуществляется автоматическая подача. Принимаем сверло спиральное из быстрорежущей стали с цилиндрическим хвостовиком по ГОСТ 886-77. Материал режущей части – быстрорежущая сталь Р6М5.
Параметры сверла: диаметр сверла d=15 мм длина сверла L=220 мм длина рабочей части l=144 мм.
Выбираем из таблицы для диаметра 107 мм и твердости НВ=160-240 подачу S=02 ммоб.
После согласования с паспортом станка принимаем частоту вращения n=650 обмин.
Нормирование технологического процесса
Технические нормы времени в условиях серийного производства устанавливаются расчетно-аналитическим методом.
В серийном производстве определяется норма штучно-калькуляционного времени:
Где – подготовительно-заключительное время мин; – количество деталей в настроечной партии шт;
Где - основное время мин; - вспомогательное время которое состоит из затрат времени на отдельные приемы: ; - время на установку и снятие детали мин; – время на закрепление и открепление детали мин; - время на приемы управления мин; - время на измерение детали мин; - время на обслуживание рабочего места мин; - время перерывов на отдых и личные надобности мин.
Рассчитаем техническую норму времени на шпоночно-фрезерной операции 111.
Основное время при фрезеровании вычисляется по формуле:
Где - длина обрабатываемой поверхности в мм; - длина врезания и подход инструмента; - длина пробега; - число ходов; - подача в мммин.
Время на установку и снятие детали закрепление её и открепления:
Время на приемы управления: Включить и выключить станок кнопкой – 001 мин; подвести деталь к фрезе в продольном направлении – 003 мин; переместить стол в обратном направлении – 011 мин; тогда
Время затраченное на измерение детали:
Вспомогательное время: =118 мин.
Время на обслуживание рабочего места и отдых составляет 6% оперативного времени:
Таким образом штучное время:
Определим состав подготовительно-заключительного времени: установка приспособления с креплением четырьмя болтами – 14 мин; установка фрезы - 2 мин; получение инструмента и приспособлений до начала работы и сдачи их после завершения работы – 7 мин:
Размер партии деталей n=80 шт.
Штучно-колькуляционное время:
Рассчитаем техническую норму времени на токарную операцию 070.
Основное время при сверлении вычисляется по формуле:
мм - размер обрабатываемой поверхности в направлении подачи;
мм – величина врезания и перебега;
мм – дополнительная длина на взятие пробной стружки.
Вспомогательное время: =061 мин.
Расчет и проектирование приспособления
Техническое задание на проектирование приспособления
Спроектировать приспособление к вертикально-фрезерному станку модели 6Б75В для фрезерования в детали (вал-шестерня) шпоночного паза длинной 16 мм шириной 4 мм и глубиной 25 мм.
Годовая программа выпуска - 3000 шт.
Материал детали - Сталь 40Х.
Инструмент - фреза концевая твердосплавная (по ГОСТ 18372-73)
Материал режущей части инструмента – Т15К6.
Определение режимов резания
Рис. 9.1 Схема резания при фрезеровании концевой фрезой
При фрезеровании глубина резания t = 4 мм.
При фрезеровании паза принимаем подачу SZ = 03 ммзуб.
Скорость резания при фрезеровании
Т = 80 мин - период стойкости фрезы;
D = 4 мм - диаметр фрезы;
Тогда частота вращения:
После согласования с паспортом станка принимаем n=2240 обмин.
Тогда скорость резания:
Принимаем v = 2813ммин.
Величины остальных составляющих силы резания находим из следующих соотношений:
Составляющая по которой рассчитывают оправку на изгиб:
Разработка схемы установки заготовки
Для обеспечения точности расположения обрабатываемого отверстия применяем схему базирования представленную на рис. 9.2
Рис. 9.2 Схема базирования заготовки
Разработка эскизного варианта приспособления
Эскизный вариант приспособления представлен на рис. 9.3
Рис. 9.3 Вариант приспособления с пневмоцилиндром
Описание работы приспособления
Рис.9.6 Эскиз приспособления
Принцип работы и конструкция приспособления показаны на рис.9.6
Корпус приспособления представляет собой открытую плиту 1. На плиту при помощи штифтов и винтов установлена призма 2 для обеспечения положения заготовки. На плите также закреплён пневмоцилиндр 9. Рычаг 4 удерживается на опоре шпильке 6 которая в свою очередь крепится к плите приспособления. Высота шпильки регулируется гайкой 5.
Заготовка 3 устанавливается на призму 2. Сверху заготовка прижимается рычагом 4 через шпильку 6 а на рычаг с другой стороны действует шпилька штока 7 через поршень 8 на который в свою очередь действует давление воздуха находящегося в полости пневмоцилиндра 9.
В ходе курсовой работы был разработан конкретный вариант технологического маршрута обработки детали. В результате этого получен вал-щестерня с технологическими и конструктивными характеристиками которые были заданы изначально. Курсовая работа содержит рассчитанные и назначенные величины режимов резания. Процесс изготовления вала четко нормирован. Для каждой операции выбран обрабатывающий станок режущий и измерительный инструмент технологическая оснастка.
Таким образом в результате проведенной работы были окончательно закреплены навыки практического применения теоретических знаний для решения прикладных инженерных задач связанных с разработкой технологических процессов изготовления машиностроительных изделий.
Справочник технолога-машиностроителя. Том 2. Под редакцией А.Г.Косиловой и Р.К.Мещерякова. Москва «Машиностроение» 1986.
Проектирование и расчет приспособлений. В.А.Горохов. Минск «Вышэйшая школа» 1986.
Курсовое проектирование по технологии машиностроения. А.Ф.Горбоцевич В.А.Шкред. Минск «Вышэйшая школа» 1983.
Методические указания к курсовому проектированию по дисциплине «Технология оборудование и автоматизация машиностроения» для студентов специальности Т.03.01. Б.П.Чемисов. Новополоцк 1996.
Проектирование станочных приспособлений. А.П.Белоусов. Минск «Вышэйшая школа» 1980.
Справочник технолога-машиностроителя. Том 2. Под редакцией А.Г.Косиловой и Р.К.Мещерякова. Москва «Машиностроение» 1985.
Проектирование и производство заготовок в машиностроении. П.А.Руденко. Киев 1991
Общемашиностроительные нормативы времени. Москва «Машиностроение» 1974.
Общемашиностроительные нормативы времени и режимов резания. Москва экономика 1990
Титульники.docx
УО «Полоцкий Государственный Университет»
Кафедра «Технология и оборудование машиностроительного производства »
по курсу: «Технология машиностроения»
на тему : «Технологический процесс изготовления вала-шестерни»
Пояснительная записка
к курсовому проекту
Титульник.DOC
Кафедра Технология машиностроения’
Министерство образования Республики Беларусь
Руководитель Лысов А.А.
технологический процесс
механической обработки детали “Вал-шестерня ”
ОК.doc
Кафедра Технология машиностроения’
Наименование операции
Сталь 40Х ГОСТ 4543-71
Оборудование устройства ЧПУ
Обозначение программы
Отрезать заготовку 40х344
ОПЕРАЦИОННАЯ КАРТА МЕХАНИЧЕСКОЙ ОБРАБОТКИ
Фрезерно-центровальная
Фрезеровать торцы. выдерживая размер 339-08 до 340-01
Центровать торцы по ГОСТ 14034-74
Крепить деталь в 3-х кулачковом патроне поджать центром
Точить поверхность 36 до 38-01
Точить поверхность 25f7 до 28-01 выдерживая размеры 287 до 286
Точить поверхность 20f7 до 23-01 на l=202 до 201
Притупить острые кромки
Точить поверхность 36 до 38-01 на остаток
Точить поверхность 25f7 до 28-01 на l=14
Крепить деталь в 3-х кулачковом патроне и люнете за поверхность 25f7
Сверлить отверстие 107 на l=225 230 мм
Расточить выточку 12 на l=4 мм снять фаску под 60° выдерживая 13
Нарезать резьбу М12х125-7Н выдерживая размер 14 мм
Подрезать торец выдерживая размер 339-01
Сверлить отверстие 15 на l=52 мм
Расточить фаску 2х60°
Крепить деталь в центра с переустановкой
Точить поверхность 36 на проход
Точить поверхность 25f7 до 257-01 на l=287 до 2868±01
Точить поверхность 20f7 до 207-01 на l=202
Точить поверхность под М20х15-8g до 1985-026 на l=74
Точить поверхность 18h6 до 187-01 на l=54
Точить поверхность 17h6 до 177-01 на l=30
Точить поверхность 25 до 256-01 на l=54
Отступить от торца 24 мм врезаться до 26 и точить выдерживая размер 7 до 72
Крепить деталь в 3-х кулачковом патроне поджать центром с переустановкой
на поверхности 25f7 вид «З» b=20245 05
на поверхности 20f7 вид «Ж» b=25177 1
на поверхности 18h6 вид «Е» b=3175 1
на поверхности 17h6 вид «Д» b=3165 1
Нарезать резьбу М20х15-8g
Точить 3 фаски 1х45°
Точить канавку b=1215 выдерживая размер 8 (вид «Н»)
Точить фаску 05х45 на поверхности 36
поверхность 25f7 до 255-002 Ra 125
поверхность 20f7 до 205-002 Ra 125
поверхность 18h6 до 185-002 Ra 125
поверхность 17h6 до 175-002 Ra 125
поверхность 25 до 253-002
Крепить деталь в приспособлении
Фрезеровать 2 шп. паза b=4P9 выдерживая размеры:
для разреза В-В 32; 2; 16;
для разреза Б-Б 74; 05; 16;
Крепить деталь в УСП с переустановкой
Сверлить 2 отв. 4 мм под пазы вид А-А и В-В насквозь
Притупить острые кромки
Сверлить отв. 48 на поверхности 25
Крепить деталь в УСП с поворотом
Фрезеровать 2 паза выдерживая размеры 14 133 и 171±02
Крепить деталь в центрах
Фрезеровать зубья m=2 z=16 окончательно по 7-й степени точности
поверхность 25f7 до 252-002 Ra 125
поверхность 20f7 до 202-002 Ra 125
поверхность 18h6 до 182-002 Ra 125
поверхность 17h6 до 172-002 Ra 125
поверхность 25 до 251-002 Ra 125
Поверхность М20х15-8g обнизить на 02
Шлифовать фаски под 60° Ra 125
поверхность 25f7 в р-р окончательно Ra 125 с подшлифовкой торца 3625f7 выдерживая р-р 287-08
поверхность 20f7 в р-р окончательно Ra 125
поверхность 18h6 в р-р окончательно Ra 125
поверхность 17h6 в р-р окончательно Ra 125
поверхность 25 в р-р окончательно Ra 125
Крепить деталь в 3-х кулачковом патроне и люнете
Шлифовать поверхность 16Н7 в р-р окончательно Ra 125
МК.DOC
Сталь 40Х ГОСТ 4543-71
Код наименование операции
Обозначение документа
Код наименование оборудования
5 800 Пилоотрезная КТМ 60 140.00001 КТМ 201400001 ИОТ 117
44 18632 3 1Р 1 1 1 - - - 085
0 009 Маркировочная КТМ 60 146.00002 КТМ 201460002 ИОТ 163
217 3 1Р 1 1 1 - - 002
5 607 Фрезерно-центровальная КТМ60 146.00003 КТМ 201460003 ИОТ 50
217 3 1Р 1 1 1 - - 07
0 029 Технический контроль КТМ60 140.00004 КТМ 201400004 ИОТ 285
217 3 1Р 1 1 1 - - - 09
5 039 Улучшение КТМ 60 140.00005 КТМ 201400005 ИОТ 145
217 3 1Р 1 1 1 - - -
Наименование детали сб. единицы или материала
0 100 Токарная КТМ 60 140.00006 КТМ 201400006 ИОТ 40
65 18217 3 1Р 1 1 1 - - - 565
5 100 Токарная КТМ 60 140.00007 КТМ 201400007 ИОТ 40
К40П 18217 3 1Р 1 1 1 - - - 417
0 100 Токарная КТМ60 1 46.00008 КТМ201460008 ИОТ 40
65 18632 3 1Р 1 1 1 - - - 506
5 100 Токарная КТМ60 1 46.00009 КТМ201460009 ИОТ 40
65 18632 3 1Р 1 1 1 - - - 915
0 300 Круглошлифовальная КТМ 60 140.00010 КТМ 201400010 ИОТ 166
М153 18632 3 1Р 1 1 1 - - - 106
5 014 Разметочная ИОТ 171
Верстак 17474 2 1Р 1 1 1 - - -
0 602 Шпоночно-фрезерная ИОТ 50 095
5 001 Слесарная ИОТ 163
Верстак 12913 1 1Р 1 1 1 - - - -
ГОСТ 3.1404-86 Форма 1б
0 200 Сверлильная ИОТ 71
Н125 18176 3 1Р 1 1 - - - - -
5 600 Фрезерная КТМ 60 140.00011 КТМ 201400011 ИОТ 50
40 18873 4 1Р 1 1 1 - - - 1
0 001 Слесарная КТМ 60 140.00012 КТМ 201400012 ИОТ 163
Верстак 18873 4 1Р 1 1 1 - - - 14
5 502 Зубофрезерная КТМ 60 140.00013 КТМ 201400013 ИОТ 150
К301П 18873 4 1Р 1 1 1 - - - 11
0 001 Слесарная ИОТ 163
5 031 Термическая ИОТ 123
5 100 031 Термическая ИОТ 123
474 3 1Р 1 1 1 - - -
5 011 Промывка КТМ 20103.00001 КТМ 601030001 ИОТ 46
Моечная машина 16572 4 1Р 1 1 1 - - - -
0 034 Термическая ИОТ 70
176 3 1Р 1 1 - - - - -
5 030 Рихтовка КТМ 60 140.00011 КТМ 201400011 ИОТ 50
873 4 1Р 1 1 1 - - - 1
0 300 Круглошлифовальная ИОТ 166
М153 17474 2 1Р 1 1 1 - - -
5 312 Центрошлифовальная ИОТ 166
М153 17474 3 1Р 1 1 1 - - -
5 334 Внутришлифовальная КТМ 20103.00001 КТМ 601030001 ИОТ 166
К227В 16572 4 1Р 1 1 1 - - - -
0 029 Тенический контроль ИОТ 285
5 019 Маркировачная КТМ 60 140.00011 КТМ 201400011 ИОТ 153
0 008 Консервация КТМ 60 140.00012 КТМ 201400012 ИОТ 82
Заключение.docx
Таким образом в результате проведенной работы были окончательно закреплены навыки практического применения теоретических знаний для решения прикладных инженерных задач связанных с разработкой технологических процессов изготовления машиностроительных изделий.
Рассмотрено два варианта получения заготовки – прокат (базовый вариант) и поковка. По рассчитанным коэффициентам использования металл сделан вывод о выборе способа ковкой.
Выбрана оптимальная схема базирования для каждой операции что позволило свести погрешность закрепления заготовки (детали) а выбор наилучшего варианта обработки основных поверхностей позволил достичь заданной точности при оптимальных затратах на производство.
При выборе металлорежущего оборудования учитывались геометрические размеры заготовки что позволило рационально использовать выбранные станки обеспечивающие необходимую мощность резания.
Для шпоночно-фрезерной операции было разработано приспособление использование которого позволит уменьшить вспомогательное время а следовательно и штучное время. Приспособление обеспечивает требуемую точность и простое в обращении.
При курсовом проектировании особое внимание уделяется самостоятельному творчеству студента с целью развития его инициативы в решении технологических задач а также детального и творческого анализа существующих технологических процессов.
Табл.docx
Табл. 7.1 Режимы резания
16BT20.42.209.cdw

Степень точности по ГОСТ 1643-81
Средняя длина общей нормали
Радиус кривизны активного профиля
Обозначение чертежа сопряженного
КП-063019.01.000-ЗО-2011
Сталь 40Х ГОСТ 4543-71
Допуск непостоянства диаметра в поперечном и продольном
сечениях поверхности М 0
поверхностей Л и П - 0
по наружному диаметру обнизить на 0
Рекомендуемые чертежи
- 24.01.2023
- 24.01.2023