Технологический процесс обработки шестерни 3 передачи промежуточного вала коробки передач автомобиля ЗИЛ-4342




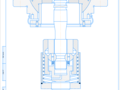
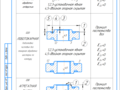
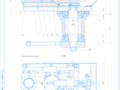
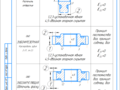
- Добавлен: 24.01.2023
- Размер: 6 MB
- Закачек: 1
Описание
Состав проекта
![]() |
![]() |
![]() |
![]() |
![]() |
![]() |
![]() |
![]() ![]() ![]() |
![]() ![]() ![]() ![]() |
![]() ![]() ![]() ![]() |
![]() ![]() ![]() ![]() |
![]() ![]() ![]() ![]() |
![]() ![]() ![]() ![]() |
![]() ![]() ![]() ![]() |
![]() ![]() ![]() ![]() |
![]() ![]() ![]() ![]() |
![]() |
![]() ![]() ![]() ![]() |
![]() |
![]() ![]() ![]() ![]() |
![]() |
![]() |
![]() |
![]() ![]() ![]() ![]() |
![]() ![]() ![]() |
![]() |
![]() ![]() ![]() ![]() |
![]() ![]() ![]() |
![]() |
Дополнительная информация
технологическая карта.doc
Кафедра «Технология машиностроения»
ТЕХНОЛОГИЧЕСКАЯ КАРТА
МЕХАНИЧЕСКОЙ ОБРАБОТКИ И СБОРКИ
Шестерня 3-й передачи
Наименование и содержание операции с указанием номера размеров и допусков обрабатываемых поверхностей
Рабочее приспособление
Наименование инструмента и материал режущей части
Протянуть отверстие до
Протянуть шпоночную канав-
ку в размер 5720-5700*
Подрезать торец обода выдер-
Станок токарный 8-ми
жав перепад 9 между торцем
обода и торцем ступицы.
Обточить обод до 126 мм
Обточить фаску 18×45º
Расточить фаску 2×30º
Расточить фаску 1×45º
Зенковать фаску 07×30º по
периметру шпоночного паза
Расточить отверстие до
Подрезать торец в размер
жав перепад 63-60 между
Торцем обода и торцем ступи-
Расточить отверстие 5427-
Подрезать торец обода в раз-
Выдержать размер 5756-5715
Произвести контроль по пред-
Фрезеровать зубья z=31 m=35
Направление винтовой линии
Угол наклона 24º40’15”
Острые кромки зубьев z=31
затупить фаской 1×45º
Очистить деталь от стружки.
Шевинговать зубья z=31
Промыть деталь в моющем
Контролировать предшевст-
Транспортировать детали в
Зубья упрочнить наклёпом.
Обкатать зубья z=31 m=35
Шлифовать отверстие 5453-
Шлифовать торец ступицы в
Хонинговать зубья z=31
Шлифовать торец ступицы
Промыть деталь в моющем
Проверить предшествующие
Приёмочный контроль.
контрольное приспособление2.cdw

остальные для справок.
Допуск перпендикулярности образующей оправки поз.8 к
поверхности не более 0.01 мм.
Люфт каретки поз.3 не допускается.
Станция для контроля
межосевого расстояния
Технологический процесс обработки
шестери III передачи
промежуточного вала коробки передач автомолбиля ЗИЛ-4342
На виде сверху деталь непоказана
Токарная наладка.cdw

Расточить фаску 1х45
внутри диаметра обода
Расточить фаску 2х30
Обточить фаску 1.8х45
Расточить диаметр ступицы в диаметр 126 мм
Материал режущей части
Технологический процесс обработки
шестери III передачи
промежуточного вала коробки передач автомолбиля ЗИЛ-4342
Операция 020 Токарная
Таблица баз 4.cdw

Проверка шестерни на зацепление.cdw

расстояния за один оборот шестерни -
Допуск параллельности оси пальцев
Предельные отклонения размеров с
неуказанными допусками
Усилие пружины на длине 65 мм - 14
Технологический процесс обработки
шестери III передачи
промежуточного вала коробки передач автомолбиля ЗИЛ-4342
Приспособление для проверки
шестерни на зацепление
Шестерня.cdw

Max возможное закругление у корня зуба с
шероховатостью Rz 20 min обеспечить инструментом
Направление линии зуба
Смещение исходного контура
Предельные отклонения
Допуск на колебание длины общей нрмали
с зубьями эталонного
Межосевое расстояние пары
по нормали расчетная
Толщина по хорде зуба и высота
до хорды делительной окр. в нормальном сечении
при номин. наружном диаметре
Ход зуба делительный
Коэф. высоты головки
Коэф. граничной высоты
Коэф. радиального зазора
За оборот зубч. колеса
Нитроцементировать h 0
Сердцевина 37 46 HRC
Штаповочные уклоны 7
Неуказанные предельные откления
Зубья упрочнить наклёпом стальной дробью
Действительного коэффициент радиального зазора
необходимый для нормальной работы инструмента
Технологический процесс изготовления шестерни
III передачи промежуточного вала КП автомобиля ЗиЛ-4342
Шестерня III передачи промежуточного
вала КП автомобиля ЗиЛ-4342
Заготовка.cdw

Термообработка - нормализация d отл 4
Обработка поверхности - дробью
Неуказанные радиусы 0-3 мм
Торцевой заусенец не более 2 мм
Внешние дефекты - допускается глубиной не более 0
Особые требования - разностенность не более 1 мм
Технологический процесс изготовления шестерни
III передачи промежуточного вала КП автомобиля ЗиЛ-4342
Заготовка шестерни III передачи
КП автомобиля ЗиЛ - 4342
Протяжная наладка.cdw

Материал режущей части
Протянуть отверстие в размер
Технологический процесс обработки
шестери III передачи
промежуточного вала коробки передач автомолбиля ЗИЛ-4342
Операция 010 Протяжная
Таблица баз.cdw

Таблица баз 2.cdw

Спецификация мембранный патрон.cdw

Технологический процесс обработки
шестери III передачи
промежуточного вала коробки передач автомолбиля ЗИЛ-4342
Болт М8 х 32 ГОСТ 7798-70
Болт М12 х 25 ГОСТ 7798-70
Винт М10 х 30 ГОСТ 11738-84
Винт М8 х 20 ГОСТ 11738-84
Таблица баз 3.cdw

Записка.docx
1 Краткая характеристика завода и его продукции .4
2 Краткая характеристика цеха .9
3 КПП автомобиля ЗИЛ 130 .10
4 Служебное назначение и технические характеристики 12
II. Технологическая часть 13
1 Анализ технических условий на деталь 13
2 Расчет годового фонда времени .16
3 Типовой технологический процесс обработки одновенцовых цилиндрических шестерен 18
4 Выбор и обоснование технологических баз .21
5 Изготовление заготовок зубчатых колес ..28
6 Расчет припусков . 31
7 Расчет режимов резания ..35
III. Мероприятия по усовершенствованию технологических процессов . 39
1 Описание конструкции контрольного приспособления 42
2 Описание конструкции рабочего приспособления 46
3 Подборка материалов по инструментальному обеспечению 49
4 Система активного обслуживания инструментом автоматических и поточных линий .. 51
IV. Аналитическое исследование .52
Список использованной литературы ..63
В условиях современного производства необходим рост производительности и надежности машин снижение их массы на единицу мощности повышение точности изделий.
Так же остро стоит и проблема улучшения качества агрегатов автомобилей увеличения их надежности работоспособности.
Для достижения поставленных задач необходимо внедрение высокоэффективных технологических процессов коллективной механизации и последовательное проведение автоматизации производства.
Особенно важно осуществление этих мероприятий в тех производственных процессах в которых в настоящее время еще затрачивается ручной труд недостаточная автоматизация и механизация. К числу таких производственных процессов относится и механическая обработка.
В данной работе разработан новый технологический процесс обработки шестерни третьей передачи промежуточного вала КПП автомобиля ЗиЛ-130.
Для выполнения работы необходимо решить следующие задачи:
-обосновать выбор вида заготовки;
-проанализировать схемы базирования;
-разработать маршрут обработки детали;
-рассчитать припуски на обработку;
-рассчитать режимы резания и нормы времени с составлением маршрутной и операционной карт;
-разработать приспособления.
I Общие вопросы проекта
1 Краткая характеристика завода и его продукции
Московский автозавод имени И.А. Лихачева (производственное объединение ЗиЛ).
августа (20 июля по старому стилю) 1916 г. в Тюфелевой роще состоялись торжественный молебен и закладка автомобильного завода (АМО) который к марту 1917 г. должен был выпустить 150 полуторатонных грузовиков «Ф-15» по лицензии итальянской фирмы "ФИАТ". Завод основан торговым домом «Кузнецов Рябушинские и К?». Трудности военного времени и слабость станкоинструментальной базы страны сорвали планы строительства завода в намеченные сроки. Тем не менее Рябушинские закупили в Италии комплекты автомобилей «Ф-15 » что обеспечило сборку 432 грузовиков в 1917 г. 779 - в 1918 г. и 108 автомобилей - в 1919 г. Однако завод для изготовления и сборки собственных автомобилей достроен не был. Виною тому стали Октябрьская революция и гражданская война. Национализация недостроенного завода (15 августа 1918 г.) зафиксировала экспроприацию собственности акционеров АМО. Недостроенное предприятие по существу превратилось в крупные мастерские где ремонтировались автомобили и другая техника.
апреля 1923 г. заводу АМО было присвоено имя итальянского коммуниста Ферреро убитого фашистами. В июне 1923 г. Госплан СССР утвердил производственное задание заводу на 1923-1927 гг. Однако только в марте 1924 г. на завод поступило конкретное правительственное задание на изготовление первых советских грузовиков.
ноября 1924 г. был собран первый полуторатонный грузовик АМО-Ф-15 а 7ноября десять машин приняли участие в параде. Эту дату принято считать днем рождения советского автомобилестроения.
В 1925 году завод был переименован в 1-й Государственный автомобильный завод (бывший АМО).
В 1927 году завод возглавил И.А.Лихачев с именем которого связано интенсивное развитие предприятия.
В 1964г. начато массовое производство ЗИЛ-130. Совершенствование конструкции грузовиков ЗИЛ-130 продолжалось до конца 1970 г. и пополнилось такими модификациями как северные экспортные тропические газобаллонные и т.д.
К категории полноприводных автомобилей к третьему поколению относится 35-тонный грузовик ЗИЛ-131 (6х6) унифицированный с серией "130" и выпускавшийся с 1967 г. В связи с изменениями в двигателе и ходовой части в 1987 году автомобилю присвоен индекс ЗИЛ-131Н.
В 1967г. были спроектированы и производились (штучно) поисково-эвакуационные установки (ПЭУ-1) для поиска и эвакуации спускаемых космических объектов и космонавтов.
В 1967 г. СССР впервые принял участие в 8 Международной "Неделе автобусов" в г. Ницце где комфортабельный автобус малого класса «Юность» ЗИЛ-118 завоевал 12 призов. Автобус изготавливался штучно по отдельным заказам. Серийного производства автобуса организовать не удалось.
В 1971 году завод награжден третьим орденом Ленина за успешное выполнение восьмого пятилетнего плана.
июля 1971 года ЗИЛ стал Производственным Объединением (ПО ЗИЛ) в состав которого вошли 17 заводов.
В 1974 году на главном конвейере был собран миллионный ЗИЛ-130.
В 1975 году завод награжден Орденом Октябрьской революции за успешное завершение работ по созданию мощностей на выпуск 200 тысяч автомобилей в год.
В 1975 г. на ЗИЛе наладили производство нового поколения 3-х осных автомобилей ЗИЛ-133Г1 (6x4) грузоподъемностью 8 т к которым с 1977 г. добавилась 10-тонная модель ЗИЛ-133Г2 полной массой 172 т. Их оборудовали стандартным 150-сильным двигателем V8 5-ступенчатой коробкой передач гипоидной главной передачей и балансирной подвеской задних колес на полуэллиптических рессорах.
С 1979 г. взамен ЗИЛ-133Г2 выпускались грузовики ЗИЛ-133ГЯ на которых устанавливались дизельный двигатель КамАЗ-740 Камского автозавода ( 210 л.с) 10-ступенчатая коробка передач усиленные передние рессоры.
Большую роль завод сыграл в судьбе КАМАЗа. На ЗИЛе были спроектированы литейный и автосборочный корпуса а созданные образцы грузовиков легли в основу модельного ряда автомобилей из Набережных Челнов.
Начавшаяся в 1982 году последняя и самая крупная реконструкция завода совпала с кардинальными изменениями в экономике страны.
В 1984г. выпущены первые автомобили ЗИЛ-130 с модернизированным передним приводом. Им был присвоен индекс ЗИЛ-431410.
В1990-е годы производство грузовиков ЗИЛ-130 (ЗИЛ-431410) и ЗИЛ-131Н было переведено на Уральский автомоторный завод (УАМЗ) в Новоуральске под Екатеринбургом.
В декабре 1991 г. распался СССР и порвались многолетние внутрисоюзные связи. Новые условия периода перестройки потеря важных рынков сбои в кооперационных связях и фактическое прекращение поступления военных заказов заставили ЗИЛ в корне пересмотреть свою политику и начать приспосабливаться к рыночным принципам ведения хозяйства. В первое время это привело к резкому падению спроса на все серийные грузовые автомобили и поставило завод на грань банкротства. Одновременно начались активные поиски выхода из создавшегося положения в результате которых вся производственная программа была пересмотрена и расширена. Этому способствовала и конкуренция со стороны иностранных фирм которую ранее ЗИЛ никогда не испытывал.
сентября 1992 г. ПО ЗИЛ было приватизировано первым в отрасли и одним из первых из числа крупнейших предприятий России и преобразовано в Открытое Акционерное Московское Общество "Завод имени И. А. Лихачева" (АМО ЗИЛ) с сохранением торговой марки "ЗИЛ". Общее собрание акционеров избрало новый в истории завода орган управления - Совет директоров. Кроме головного завода оно включало 30 дочерних предприятий. Одним из его акционеров стало правительство Москвы которому в настоящее время принадлежит контрольный пакет акций.
С момента начала своей деятельности на предприятии в период с 1924 по 2000 годыпроизведено: грузовых автомобилей 7769 902 шт.; автобусов 38988 шт; легковых автомобилей высшего класса 11515 шт.
В 2000 году три полноприводных автомобиля ЗИЛ-433420 совершили уникальный автопробег по маршруту Москва-Якутск-Уэлен-Северная Америка-Западная Европа-Калининград-Москва. Первый этап кругосветной экспедиции длиной 13500 км был пройден за 62 дня и завершился в поселке Уэлен на берегу Берингова пролива (Чукотка). Всего экспедиция преодолела 45000 км. Автопробег проводился клубом «Приключение» совместно с АМЛ ЗИЛ и правительством Москвы.
В декабре 2002 года произошла смена руководства АМО ЗИЛ. Был назначен новый генеральный директор Константин Викторович Лаптев который до этого работал в команде "Руспромавто" на посту исполнительного директора ГАЗа. На завод была привлечена группа менеджеров имеющих практический опыт работы в условиях антикризисного управления. Была разработана программа реструктуризации завода направленная на работу с дочерними предприятиями по возвращению утерянных ранее активов АМО ЗИЛ восстановление хозяйственно-производственных связей с сохранившими и возвращаемыми дочерними предприятиями расширение гаммы выпускаемой продукции и услуг освоение новых рынков сбыта.
Сегодня завод на базе шасси ЗИЛ совместно с другими заводами выпускает большую гамму специальной техники: коммунальную дорожно- строительную мусоровозы вакуумные илососные каналопромывочные аварийно-ремонтные машины автоцистерны автоподъемники.
В 2003 году освоено производство автомобилей ЗИЛ-433180 и ЗИЛ-432930 с дизельными двигателями с повышенными мощностными показателями Минского моторного завода Д-260.11Е2 (180 л.с.) и Д-245.9Е2 (136 л.с.) которые имеют сертификаты соответствия норм Евро-2.
В 2004 году произошла передача функций исполнительного единоличного органа предприятия управляющей компании (МАК). В связи с этим изменилась должность руководителя завода: К.В.Лаптев стал генеральным директором управляющей организации АМО ЗИЛ.
С 2004 года с конвейера стали сходить автомобили ЗИЛ-43272Т (4х4) с дизельным двигателем ММЗ Д-245.9Е2 Евро-2; ЗИЛ-4334В1 (6Х6) с дизельным двигателем ММЗ Д-245.30Е2.
С целью наращивания темпов роста продаж новой техники ЗИЛа на предприятии впервые среди отечественных производителей грузовой и спецтехники организована Акция стартовавшая 15 марта 2004 года предназначенная для владельцев отечественных грузовых автомобилей. Суть акции в том что каждый желающий мог сдать свой подержанный грузовой отечественный автомобиль в зачет стоимости любой новой машины ЗИЛ при ее покупке. При этом старые машины принимались по цене выше рыночной.
2 Краткая характеристика цеха
Характеристика цеха и технологического производства МСЦ-2.
Механосборочный цех № 2 состоит из 3-х производственных участков: "Гидроруль" "Гидронасос" участка "КП" : службы механика энергетика и РХЗ
На производственном участке изготавливаются следующие узлы автомобиля: гидроусилитель рулевого управления гидронасос и колонка систем рулевого управления детали коробки перемены передач.
Технология производства указанных узлов требует изготовления сборочных деталей из стали чугуна и алюминия на металлорежущих станках с применением СОЖ и эмульсий. Из изготовленных деталей и комплектующих (сальники манжеты метизы подшипники) поставляемых другими подразделениями производится сборка узлов с последующей покраской.
При изготовлении деталей и узлов используются металлорежущие станки токарные фрезерные сверлильные шлифовальные хонинговальные; моечные окрасочные и сушильные камеры.
При обработке деталей образуются отходы: стальная чугунная и алюминиевая стружка. При эксплуатации станков используются масла. Отработанное масло сдается на регенерацию. При шлифовании образуется шлам состоящий из абразивного порошка и мелкой металлической стружки.
При сборке и ремонте гидрорулей происходит отход резиновых манжет прокладок сальников (вторичное использование запрещено).
При окраске узлов в окрасочных камерах остаются отходы краски.
При использовании вспомогательных материалов: салфеток древесных опилок образуются отходы замасленной ветоши и замасленные опилки.
При замене перегоревших ламп образуются отходы люминесцентных ламп и ДРА.
В корпусе 2 механосборочные цеха: «задний мост» и «полуось» 1 механообрабатываюший цех 1 вспомогательный цех ремонта оборудования. В МСК 45 поточных линий 52 поточно-механизированных линий 11 автоматических линий 7 поточно-механизированных сборочных линий. Межоперационная передача деталей и узлов производится с помощью подвесных и толкающих конвейеров.
3 Коробка передач автомобиля ЗИЛ-130.
Передней опорой ведущего вала 1 (рис.) служит шарикоподшипник установленный в выточке фланца коленчатого вала задней - шарикоподшипник 2 размещенный в стенке картера коробки передач. Шарикоподшипник 2 закрыт крышкой и фиксируется стопорным кольцом 3 и гайкой Ведомый вал опирается на шарикоподшипник 17 и роликоподшипник 37. На задний конец этого вала надеты червяк привода спидометра и шлицевая втулка с фланцем 19 карданного шарнира закрепленная гайкой с шайбой. Крышка шарикоподшипника 17 одновременно служит кронштейном стояночного тормозного механизма. Промежуточный вал 33 опирается на шарикоподшипник 22 и роликоподшипник 35. Зубчатое колесо 25 изготовлено как одно целое с промежуточным валом а зубчатые колеса 26 28. 29 31 и 34 установлены на валу на шпонках. Наружные кольца шарикоподшипников 17 22 и роликоподшипника 35 фиксируются стопорными кольцами.
зубчатые колеса 4 и 34 соединяющие ведущий и промежуточный валы зубчатые колеса 7 и 31 четвертой 8 и 29 третьей. 14. 26 второй передач имеют косые зубья и находятся в постоянном зацеплении. Зубчатые колеса 7 8 и 14 свободно вращаются на ведомом валу на котором имеются также синхронизаторы 5 и 13 а на шлицах установлено зубчатое колесо 16 первой передачи и передачи заднего хода
Первая передача включается при перемещении зубчатого колеса 16 вперед до зацепления его с колесом 25 на промежуточном валу: при этом вращение через зубчатые колеса 25 и 16 передается ведомому валу. Вторая и третья передачи включаются при перемещении синхронизатора 13 соответственно назад и вперед. Для включения четвертой и пятой передач перемешают назад или вперед синхронизатор 5. При включении пятой передачи (прямой) между собой соединяются ведущий и ведомый валы.
В передачу заднего хода входит зубчатое колесо 28 установленное на промежуточном валу. При движении зубчатого колеса 16 назад и его зацеплении с малым зубчатым колесом блока 41 включается задний ход. В этом случае крутящий момент от коленчатого вала двигателя через зубчатые колеса 4. 34 и 28 блок 41. зубчатое колесо 16 передается ведомому валу который будет вращаться в обратную сторону по сравнению с направлением его вращения при включении других передач. В картере коробки передач с обеих сторон есть люки с фланцами для крепления коробки отбора мощности. Пробка 43 закрывает контрольно-заливное отверстие для заливки и контроля уровня масла.
4 Служебное назначение и техническая характеристика изделия.
Шестерня 3-ей передачи промежуточного вала КП предназначена для передачи крутящего момента на ведущие колеса. Она находится в постоянном зацеплении с шестерней 3-ей передачи третичного вала.
Условия работы шестерни (работа при знакопеременных нагрузках). На нее накладывают ряд жестких требований что в свою очередь определяет технологию изготовления детали которая должна обладать высокими механическими свойствами.
Технические требования к изготовлению
Колебание межцентрового расстояния:
За оборот колеса max – 0071
Зубья венца должны быть бочкообразные. При проверке поверхности на краску пятно контакта должно быть не менее 75% поверхности конуса.
Для повышения твердости и износостойкости шестерни её подвергают химико-термической обработке со следующими требованиями:
Глубина нитроцементированного слоя – 06-08 мм
Твердость поверхности – HRCэ 58 61
Твердость сердцевины - HRCэ 37 46
Зубья венца упрочнять наклепом стальной дробью 08 12 мм
В результате нитроцементации повышается прочность и износостойкость поверхностного слоя определенной глубины.
II Технологическая часть
1 Анализ технических условий на деталь
Зубчатые колеса изготавливают из сталей: сталь 40Х сталь 40ХН 25ХГТ 25ХГН и т.д.
В интересах достижения технико-экономических показателей разрабатываемой конструкции необходимо чтобы материал детали позволял применять заготовительные технологии обеспечивающие максимальную приближенную форму размеры и качество поверхности.
Требования предъявляемые к материалу:
Хорошая обрабатываемость
Простота и дешевизна термообработки
Невысокая стоимость стали
Нагрузка допускаемая на контактную прочность зубьев определяется твердостью материала. Наибольшую твердость а следовательно и наименьшие габариты и массу можно получить при изготовлении из стали подвергнутой термообработке. Одной из сталей соответствующей всем выше указанным условиям в большей степени соответствует сталь 25ХГМ. Это хромо-марганцевая конструкторская сталь с присадкой молибдена.
Она не склонна к отпускной хрупкости обладает мелкими зернами повышенной вязкостью и может быть применена для изготовления ответственных деталей работающих при больших окружных скоростях средних и высоких давлениях и больших ударных нагрузках.
Углерод (( C ) -У)находится в стали обычно в виде химического соединения Fe3C называемогоцементитом.
С увеличением содержания углерода до 12%увеличиваетсятвердость прочность и упругость сталипонижается пластичность и сопротивление ударуухудшаетсяобрабатываемость и свариваемость.
Кремний (( Si ) -C) если он содержится в стали в небольшом количестве особого влияния на ее свойства не оказывает.
При повышении содержания кремния значительноулучшаютсяупругие свойства магнитопроницаемость сопротивление коррозии и стойкость против окисления при высоких температурах.
Марганец (( Mn ) -Г) как и кремний содержится в обыкновенной углеродистой стали в небольшом количестве и особого влияния на ее свойства также не оказывает. Однако марганец образует с железом твердый раствор и несколько повышаеттвердость и прочность сталинезначительно уменьшаяее пластичность. Марганец связывает серу в соединение MnS препятствуя образованию вредного соединения FeS. Кроме того марганец раскисляет сталь.При высоком содержании марганцасталь приобретает исключительно большую твердость и сопротивление износу.
Сера ((S))являетсявреднойпримесью. Она находится в стали главным образом в виде FeS. Это соединение придает стали хрупкость при высоких температурах например при ковке - свойство которое называется красноломкостью. Сера увеличивает истираемость стали понижает сопротивление усталости и уменьшает коррозионную стойкость.
В углеродистой стали допускается серыне более 006-007%.
Увеличение хрупкости стали при повышенном содержании серы используется иногда для улучшения обрабатываемости на станках благодаря чему повышается производительность при обработке.
Фосфор (( P ) -П)также являетсявреднойпримесью. Он образует с железом соединение Fe3P которое растворяется в железе. Кристаллы этого химического соединения очень хрупки. Обычно они располагаются по границам зерен стали резко ослабляя связь между ними вследствие чего сталь приобретает очень высокую хрупкость в холодном состоянии (хладноломкость). Особенно сказывается отрицательное влияние фосфора при высоком содержании углерода. Обрабатываемость стали фосфор несколько улучшает так как способствует отделению стружки
Хром (( Cr ) -Х)– наиболее дешевый и распространенный элемент. Хромповышаеттвердость и прочность незначительноуменьшаяпластичностьувеличиваеткоррозионную стойкость; содержание больших количеств хрома делает сталь нержавеющей и обеспечивает устойчивость магнитных сил.
Молибден (( Mo ) -М)увеличивает красностойкость упругость предел прочности на растяжение антикоррозионные свойства и сопротивление окислению при высоких температурах.
Химический состав в % стали 25ХГМ
Микроструктура: мелкие равноосные зерна сорбидообразного перлита и феррита.
Технологические свойства:
Обрабатываемость резанием – удовлетворительная
Свариваемость – низкая
Пластичность при холодной обработке давлением – удовлетворительная
Коэффициент использования металла Ки.м равный 058 показывает что получение заготовки методом свободной ковки не неэкономично т.к. 43% металла уходит в стружку. Заготовка получаемая методом свободной ковки по конфигурации не соответствует форме готовой детали. Поэтому необходимо увеличить Ки.м для этого лучше применить метод получения заготовки такой как штамповка в закрытых штампах на ГКМ.
В результате чего заметно значительное увеличение Ки.м что ведет к снижению себестоимости экономии металла.
2 Расчет действительного годового фонда времени и определение типа производства на основе расчета такта выпуска и коэффициента закрепления операций.
Вывод о типе производства сделаем на основе анализа количества выпускаемой продукции. Основным критерием для разграничения типов производств является коэффициент закрепления операции выполняемых в течении месяца к числу рабочих мест.
Для массового производства-Кз.о.=1
Для крупносерийного производства-Кз.о.=1-10
Для среднесерийного производства-Кз.о.=10-20
Для мелкосерийного производства-Кз.о.=20-40
Для единичного производства-Кз.о.>40
Но для того чтобы рассчитать сколько операций у нас выполняется в течении месяца вычислим такт выпуска:
где:В – годовая производственная программа выпуска изделий шт.
- действительный годовой фонд времени работы оборудования мин.
где: - коэффициент учитывающий простои оборудования в плановых ремонтах (для металлорежущего оборудования весом до 10т. К=097)
- количество рабочих дней в году
=8 – продолжительность рабочей смены час.
Значит производство крупносерийное.
Расчетное количество оборудования
Коэффициент загрузки – отношение рассчитаного количества рабочих мест к принятому.
Коэффициент загрузки оборудования всей линии
3 Типовой технологический процесс обработки одновенцовых цилиндрических шестерен.
Конструктивные особенности автомобильных одновенцовых цилиндрических зубчатых колес состоят в том что их наружный диаметр больше высоты а центральное отверстие имеет гладкую поверхность или шлицы.
Технологическая схема обработки заготовок для всех одновенцовых цилиндрических колес на ЗИЛе одинакова и представляет собой следующую последовательность:
Обработка центрального отверстия и одного из торцов
Обработка детали по наружному контуру — черновая и чистовая
Нарезание зубьев наружного и внутреннего вендов
Зубозакругление и снятие фасок на зубьях.
Зубошевингование (зубья наружного венца).
Чистовая обработка центрального отверстия и базовых торцов относительно зубчатого венца. Чистовая отделка зубьев зубчатых колес.
На КАМАЗе заготовку сначала обрабатывают по контуру за два установи. Сначала - точение с одной стороны затем точение с другой стороны.
Хонингование базового отверстия производят по схеме - жесткое крепление хонинговальной головки и плавающее крепление детали и приспособления. Этот способ хонингования значительно упрощает конструкцию хонинговальной головки и не требует точного центрирования обрабатываемой детали по оси шпинделя станка. Базовые торцы зубчатого венца обрабатывают от базового отверстия на жестких и точных одно- двух шпиндельных фронтальных токарных станках одновременно двумя резцами по окончании их обработки протягивают выступающий торец ступицы. Такая схема обеспечивает малое отклонение от параллельности торцов необходимое при зубофрезеровании заготовок пакетом. Приведенный технологический процесс обеспечивает высокую и стабильную точность.
Второй технологический процесс с использованием для формирования точных баз шлифования отверстия и торцов применяется дня обработки заготовок колес-дисков коробки передач легкового автомобиля.
Опыт передовых автозаводов показал что для токарной обработки заготовок зубчатых колес-дисков вместо многошпиндельных прутковых и патронных автоматов более экономично применять фронтальные токарные автоматы обеспечивающие большую производительность точность обработки и лучшие условия для автоматизации. Эти станки удобнее и проще в наладке смене инструмента уборке стружки и т.д.
В типовом технологическом процессе изготовления цилиндрических зубчатых колес автомобильных трансмиссий повышенной производительности при зубофрезеровании достигают: применением жестких мощных высокопроизводительных станков; использованием многозаходных червячных фрез повышенной скорости резания и подачи. Для изготовления зубчатых колес с модулем свыше 4 мм прогрессивным методом является зубофрезерование за два последовательных рабочих хода. Период стойкости червячных фрез повышается при работе длинными сборными фрезами с поворотными вставными рейками многозаходными многореечными или цельными фрезами покрытыми нитридом титана. Стойкость фрез покрытых нитридом титана по сравнению со стойкостью фрез без покрытия повышается в два и более.
Зубозакругление прямозубых цилиндрических колес более экономично производить на одно- двухшпиндельных станках чашечными фрезами. Метод обработки чашечными фрезами универсален обеспечивает высокую производительность и качество. Чашечные фрезы имеют высокую стойкость ими можно получить остроугольное и сфероидальное закругления и фаски любой формы. Снятие фасок и заусенцев с острых кромок производят различными методами. Рекомендуются фаски в виде запятой для косозубых колес и по всему контуру профиля зуба для прямозубых.
Типовым высокопроизводительным методом чистовой обработки зубьев является шевингование. При массовом выпуске зубчатых колес до модуля 4 мм наиболее эффективно врезное шевингование а для колес с модулем свыше 4 мм - черновое и чистовое диагональное. При отсутствии спецстанков экономично применять диагональное шевингование.
Для термической обработки автомобильных зубчатых колес применяют нитроиементацию. Этот метод обеспечивает высокую производительность и небольшие деформации зубьев. Удаление забоин и заусенцев после термической обработки производят на станках простой конструкции обкаткой между трех каленых зубчатых колес в плотном зацеплении. Хонинговаиие отверстия после термической обработки производят аналогично хонингованию перед термической обработкой.
Широко распространен технологический процесс когда у колес дисков перед зубофрезерованием и после термообработки базовые поверхности - отверстие и торцы с одной стороны заготовки шлифуют за один установ на внутришлифовальных станках. Используют кулачковые и мембранные зажимные приспособления с базированием по наружному диаметру и торцу колес-дисков перед зубофрезерованием и по боковым поверхностям зубьев и торцу для колес после термообработки. Противоположные торцы колес шлифуют на плоскошлифовальных станках.
В качестве финишной обработки зубьев закаленных зубчатых колес наиболее часто применяется шлифование или зубохонингование. Последнее позволяет улучшить форму зуба сгладить поверхность зубьев и достичь максимально возможной плавности хода.
4 Выбор и обоснование технологических баз
Базами называются поверхности линии или точки данной детали по отношению к которым определяется положение других поверхностей линий или точек.
При выборе баз особое внимание надо уделить черновым базам руководствуясь следующими правилами:
Черновая база должна быть по возможности гладкой и ровной.
Черновой базой может быть поверхность которая в окончательно обработанной детали не подлежит обработке но положение сё важно для конструкции детали.
Черновой базой может быть поверхность которая подлежит наиболее точной обработке и имеющая важное значение для обработки детали.
Черновой базой может быть поверхность при установке по которой с обработанной поверхности снимается минимальный слой металла.
Черновые базы можно использовать в технологическом процессе только один раз так как после первой позиции появляются более чистые и точные поверхности которые в дальнейшем могут быть использованы в качестве баз.
При выборе чистовых базовых поверхностей необходимо использовать принцип их постоянства.
На первой стадии техпроцесса происходит черновая и чистовая обработка всех поверхностей. На второй стадии - термическая обработка; на третьей - отделочные операции.
На первой стадии обработки производится протягивание внутреннего отверстия осуществляется подготовка технологической базы для последующих операций. На данной операции технологической установочной базой является торец ступицы - это черновая база но она не имеет штамповочных уклонов и обеспечивает наиболее точную установку детали на данной операции. После обработки отверстия применяем его для базирования детали на второй операции токарной обработки.
Здесь имеет принцип совмещения баз - отверстие является технологической измерительной и конструкторской базой что обеспечивает максимальную точность при обработке. На токарной операции за одну установку обрабатываются все поверхности заготовки (кроме отверстия). Производится многоинструментальная обработка что значительно снижает время технологического процесса значительно сокращается количество используемого оборудования.
Приступаем к обработке зубчатого венца. Для нарезания зубьев необходимой степени точности венец подвергают чистовой обработке и отделке (нарезание шлифование хонингованне зубьев). Для базирования применяют уже обработанные поверхности - отверстие торец. Зубья нарезают на зубофрезерном станке применяя специальное приспособление для закрепления детали и ведут обработку червячной фрезой.
Для повышения точности зубчатого венца шестерни применяют чистовую обработку - шевингование. Базой для этой операции является отверстие что дает наибольшую точность обработки.
После черновых и чистовых операций деталь подвергают термохимической обработке - нитроцементации. Нитроцементация повышает прочность поверхностного слоя и износостойкость зубьев; позволяет исключить процесс шлифования зубьев а применить хонингование что дает более высокую точность зацепления и повышает долговечность зубьев.
По завершению токарной обработки венец зубчатого колеса подвергают отделочной операции.
- проведение внутришлифовальной операции по обработке отверстия и торца базирование производим по рабочим и эвольвентным поверхностям зубьев.
- затем базируя заготовку по отверстию и торцу производим хонингование зубьев.
Тем самым снижается отклонение от заданной формы зуба и повышается точность его изготовления. Завершающей операцией является шлифование торца ступицы для получения необходимого значения шероховатости и точности размеров.
Технологический маршрут
Операция 010 ПротяжнаяВертикально-протяжной автомат мод. 7720В
Операция 020 ЛоботокарнаяСтанок токарный 8-ми шпиндельный па мод. 1282
Операция 030 АгрегатнаяАгрегатный станок
Операция 040 Алмазно-расточнаяАлмазно-расточной мод. 2А-715
Операция 050 Летучий контрольСтол контролера
Операция 060 ЗубофрезернаяЗубофрезерный мод. СТ-1161МС
Операция 070 Маркирование
Операция 080 ЗубозакруглениеЗубозакругляющий мод. 75 Кросс
Операция 090 Очистка
Операция 100 ЗубошевинговальнаяЗубошевинговальный мод. СТ-1508
Операция 110 ПромывкаМоечная машина
Операция 120 Летучий контрольСтол контролера
Операция 130 Транспортирование
Операция 140 Термическая
Операция 150 Зубообкатывающая
Операция 160 ШлифовальнаяПлоскошлифовальный мод. 3Б-756
Операция 170 ЗубохонинговальнаяЗубохонинговальный мод. 3Б-756
Операция 180 ШлифовальнаяПлоскошлифовальный мод. 3Б-756
Операция 190 Промывка
Операция 200 Летучий контрольСтол контролера
Операция 210 Приемочный контроль
5 Изготовление заготовок зубчатых колес
Методы изготовления.
Зубчатые колеса в зависимости от области применения изготовляют из различных материалов: стали чугуна цветных металлов пластмасс и др. Каждый из этих материалов удовлетворяет определенным требованиям. Самым распространенным материалом из которого изготовляют зубчатые колеса является сталь. Её применяют для зубчатых передач автомобилей тракторов самолетов станков и других машин которые передают большие нагрузки. Определяющими факторами для этих колес являются: прочность зубьев на изгиб контактная прочность и износ зубьев. При этом следует учитывать стоимость материала возможность обработки резанием степень деформирования в процессе закалки и т.д.
Для снижения уровня шума зубчатые колеса изготовляют из чугуна и пластмассы. Эти материалы по сравнению со сталью имеют меньшую стоимость лучшую обрабатываемость но колеса из этих материалов передают меньший крутящий момент чем стальные колеса. Зубчатые венцы червячных колес чаще всего изготовляют из бронзы которая обладает высокими антифрикционными и антикоррозионными свойствами. Зубчатые колеса насосов экономично изготовлять из металлического порошка.
Выбор метода изготовления заготовки зависит от формы и размеров детали её материала и назначения объемов производства и т.д. Лучшим методом является тот при котором заготовки получаются более дешевыми включая стоимость последующей механической обработки и имеют требуемое качество. Важнейшим фактором при выборе метода изготовления заготовок является экономия металла. Значительное сокращение расхода металла достигается при использовании технологических процессов малоотходного производства заготовок размеры которых максимально приближаются к размерам деталей. Экономия металла достигается благодаря сокращению припусков под механическую обработку и повышению точности размеров заготовки. Уменьшается трудоемкость механической обработки благодаря более высоким режимам резания исключению черновых операций например точеная зубофрезерования и других а также замене их получистовыми и чистовыми операциями.
В крупносерийном и массовом производстве к числу основных малоотходных методов изготовления заготовок зубчатых v колес относятся: поперечно-клиновая прокатка ступенчатых валов горячая высадка на многопозиционных автоматах холодная штамповка порошковая металлургия горячее накатывание и горячая штамповка заготовок с зубьями вырубка.
Особенно высокие требования предъявляют к качеству заготовок которые предназначены для обработки в автоматизированном производстве (автоматы автоматические линии гибкие производственные системы) с применением ЧЛУ. К этим заготовкам обычно предъявляют более жесткие требования в отношении припусков точности размеров твердости структуры металла массы и т.д. Перед механической обработкой заготовки целесообразно подвергать входному контролю в соответствии с техническими условиями.
В мелкосерийном производстве заготовки зубчатых колес особенно крупных размеров изготовляют другими методами. Заготовки обычно имеют простую форму с повышенными и неравномерными припусками под последующую механическую обработку резким колебанием твердости и др. Чтобы уменьшить трудоемкость изготовления заготовок в процессе ковки и последующей механической обработки форму заготовки целесообразно ограничивать плоскими или цилиндрическими поверхностями избегать применения заготовок сложных ступенчатых форм.
Типовой технологический маршрут изготовления кованых и штампованных заготовок: очистка металла от поверхностных дефектов разрезка на мерные части нагрев заготовки осадка и штамповка заготовки на несколько рабочих ходов пробивка отверстия у колес-исков термообработка.
В последнее время значительно усовершенствована трудоемкая и низкого качества операция резки на пилах ножницах и др. Высокая производительность и хорошее качество среза круглых и фасонных прутков достигаются на специальных отрезных станках например НТ-62 НТ-125 НТ-200 НТ-250 фирмы «Кизерлинг» (ФРГ). Во время резки два охватывающих режущих инструмента приводятся в действие одновременно от двух маховиков с кулачками. В результате двустороннего отрезного удара металл срезается ровно. Производительность 150-300 детмин допуск на длину заготовки ±015 мм. Поверхность среза получается чистая без заусенцев. Для повышения точности заготовок в автомат можно вставлять мини-ЭВМ контролирующую длину отрезанной части прутка что обеспечивает постоянство объема (массы) заготовки.
Технология горячей ковки и штамповки оказывает значительное влияние на процесс изготовления и качество зубчатого колеса. Неправильная штамповка влияет на обрабатываемость резанием срок службы инструмента деформацию при термообработке стоимость обработки параметр шероховатости окончательно обработанных поверхностей срок службы зубчатого колеса. Основная причина в том что штамп недостаточно наполнен для получения требуемой плотности и исключения пористости в штампованных заготовках. Гарантированное требуемое наполнение штампа достигается путем увеличения температуры штамповки для обеспечения однородного пластического течения удаления окалины и раковины в ковочном штампе увеличения размера штампованной заготовки. Правильно отштампованная заготовка зубчатого колеса имеет максимальную однородную плотность. Окалина и другие инородные частицы не должны попадать в заготовку. После штамповки заготовки подвергают нормализации или отжигу. Крупнозернистая структура полученная при температуре ковки переходит в более мелкую. Это позволяет уменьшить деформацию во время последующей термообработки и улучшить обрабатываемость. Структура металла должна состоять из феррита и перлита твердость НВ 170-207.
Расчет припусков операционных размеров и назначение допусков на обработку для 2х наиболее точных поверхностей с необходимой исходной информацией.
Расчет припуска на обработку отверстия 1264-0260
Для достижения заданной шероховатости обработку обтачивание производим в 2 этапа:
Черновое обтачивание
Чистовое обтачивание
По таблицам 3 и 5 (мет. 741) определяем значения шероховатости Rz и дефектного слоя П.
ЗаготовкаRz=160мкмП=200мкм
Черновая обработкаRz=160мкмП=100мкм
Чистовая обработкаRz=80мкмП=25мкм
По т.23 т.10 определяем допуски:
Тзаг=055+045=1мм=1000мкм
По т.4 опрееляем ρзаг т.е. пространственное отклонение заготовки:
Где: - допускаемая погрешность поковки по смещению осей
- погрешность эксцентричности отверстия.
Для последующих переходов кривизна отверстия:
где: Ky – коэффициент уточнения
Погрешность установки по операциям определяем по т.9 (мет. 741) в зависимости от применяемого зажимного приспособления.
На операциях хонингования погрешность закрепления
Определяем расчетные значения минимальных припусков:
Определяем расчетные припуски:
Определяем расчетные размеры:
Определяем наибольшие предельные размеры:
Определяем наименьшие предельные размеры:
Определяем предельные значения припусков:
Определяем предельные значения общих припусков
Элементы припуска мкм
Расчетный размер А мм
Предельные размеры мм
Предельные припуски мкм
Предварительная расточка
Расчет припуска на обработку линейного размера 436-01
Для достижения заданной шероховатости обработку отверстия производим в 3 этапа:
По таблицам 1314 и 16 (мет. 741) определяем величину припуска на обработку.
Черновое точение15 мм
Чистовое точение11 мм
Суммарный припуск=15+11+04=3 мм
7 Расчет режимов резания и норм времени на обработку на 2-х операциях.
I Операция 010 Протяжная
1Назначение скорости резания по нормативам в зависимости от твердости обрабатываемого материала V=6ммин
2Определение силы резания F=P*Sz
где: Р-удельная сила резания при протягивании кгмм2
3Корректировка скорости резания по мощности двигателя
При N=032 кВт V=5ммин
4Расчет машинного времени протягивания:
где: Lр.х.-длина рабочего хода мм
К – коэф. учитывающий соотношение рабочего и обратного ходов
где: lp-длина протягивания мм
lр.ч.п.-длина рабочей части протяжки мм
lдоп-дополнительная длина хода мм
4Определение штучного времени
где: tм-машинное время мин
tв-вспомогательное время мин
tт.о.-время технического обслуживания мин
tо.о.-время организационного обслуживания мин
tпод-время подналадки мин
II. Операция 020 Токарная
Оборудование - токарный 8-ми шпиндельный полуавтомат
1Определение длины рабочего хода суппорта:
где: Lрез-длина резания мм
y-подвод врезание и перебег инструмента мм
Резец 1L1=28+2+1=31 мм
2 Назначение подачи суппорта на оборот шпинделя
3 Определение стойкости инструмента
где: Тм – стойкость в минутах машинной работы станка
λ – коэффициент времени резания
Если λ>07 то принимаем Тр=Тм
Резец 1 Тр выбираем по таблице Тр=120 мин
Резец 2 Тр выбираем по таблице Тр=120 мин
Резец 3 Тр выбираем по таблице Тр=120 мин
Резец 4 Тр выбираем по таблице Тр=120 мин
Резец 5 Тр выбираем по таблице Тр=120 мин
4 Расчет скорости резания и числа оборотов шпинделя станка
где: Vтабл – нормативная скорость резания
К1 – коэффициент зависящий от обрабатываемого материала
К2 – коэффициент зависящий от стойкости и марки твердого сплава
К3 - коэффициент зависящий от вида обработки
Резец 1 V=140*08*08*12=1075 ммин
Резец 2 V=125*08*1*1=100 ммин
Резец 3 V=140*08*08*1=896 ммин
Резец 4 V=120*08*08*1=768 ммин
Резец 5 V=120*08*08*1=768 ммин
Расчет чисел оборотов шпинделя:
где: d – диаметр обработки в мм.
5 Определение времени цикла
где: Sм – минутная подача мммин
Резец 1Sм=06*272=1632 мммин
Резец 2Sм=06*318=1908 мммин
Резец 3Sм=06*523=3138 мммин
Резец 4Sм=06*194=1164 мммин
Резец 5Sм=06*330=198 мммин
Лимитирующим инструментом является резец 1 т.к. у него наибольшая длина рабочего хода и наибольшее время работы.
6 Расчет штучного времени
tшт=028+01875+003+0025+015=05711мин
III Мероприятия но усовершенствованию технологических процессов механообработки.
Используя опыт передовых автозаводов (ВАЗ КАМАЗ АЗЛК) и зарубежных фирм (Фиат Рено) можно предложить следующие мероприятия по совершенствованию технологии изготовлении деталей КПП автомобилей:
При изготовлении косозубых цилиндрических колес применить метод фрезерования по способу «Тронта» при котором имеет место непрерывное смещение зацепления червячной фрезы и снижение tM за счет уменьшения времени врезания и выхода фрезы по сравнению с обычным фрезерованием (опыт ВАЗа).
За счет совокупности технологических и организационных решений повысить уровень режимов резания в среднем на 20-30% (опыт ВАЗа). Например при работе многолезвийным инструментом (наборные фрезы расточные головки) высокая точность изготовления инструментов и связанная с этим более равномерная нагрузка на каждый зуб позволяют применять повышение (в 15-2 раза) минутные подачи.
Для повышения точности обработки шлиц на валах следует использовать вместо прямобочных эвольвентные шлицы и изготавливать их методом холодного формообразования на накатных станках «Roto-Flo»(CLUA) производительностью до 300 штчас.
Для исключения транспортировки деталей в термический цех выполнять термическую обработку в технологических потоках используя индукционные агрегаты для закалки ТВЧ
Повысить производительность обработки за счет широкого использования в крупносерийном производстве принципа концентрации операций и совмещения неоднородных по технологическому признаку автоматических линий и агрегатов в единую систему. Например комплексная АЛ изготовления тел вращения включает: токарную обработку тонкую расточку импульсную расточку подгонку по весу и гальванопокрытие. Агрегаты связываются гибким транспортером с накопителями. При производительности АЛ 350детчас она обслуживается 4 рабочими (опыт ВАЗа).
На токарных операциях широко использовать останов шпинделей и дополнительные устройства обеспечивающие такие операции как фрезерование шестигранника сверление поперечных отверстий нарезание зуба накатки и т.д.
Использовать новые технологические схемы обработки вместо традиционных.
Например замена традиционной схемы торцефрезерование-центрирование всех деталей класса валов - автоматами совмещающими врезное торцевание с одновременным оформлением центров с криволинейной образующей что наряду с уменьшением количества станков повышает точность обработки.
Использовать для операций токарной обработки валов точные и высокопроизводительные токарные гидрокопировальные станки обеспечивающие допуск до 004 мм достаточный для отказа от операции шлифования перед нарезанием шлиц иди резьб.
Повысить производительность обработки применяя режимы резания используемые на европейских заводах:
- токарную обточку хвостовика первичного вала КПП выполнять на гидрокопировальных станках со скоростью 130-63 ммин;
- фрезеровать зубья шестерен КПП в АЛ со скоростями резания (65-76-33*45 ммин) (опыт ВАЗа) повышение производительности в 18 раза;
- при долблении зубьев шестерен КПП скорость резания увеличить в 15 раза (300-900 ходмин);
- повысить спорость резания на токарных многошпиндельных автоматах в 15 роза (50-75 ммин)
С целью повышения уровня режимов резания улучшить качество применяемого инструмента за счет мероприятий повышающих егостойкость. (На европейских заводах к качеству материалов и геометрической точности инструмента предъявляются исключительно высокие требования).
Определяющей конструкцией инструмента находящей массовое
применение на токарных и фрезерных операциях должна быть принята система державок-корпусов с механическим креплением неперетачиваемых твердосплавных пластин. Например на ВАЗ 70% токарных операций выполняются резцами указанной конструкции и 22% всех операций по фрезерованию плоскостей производится фрезами с механическим креплением пластин. В сравнении с твердосплавными капанными инструментами режимы инструмента с механическим креплением выше на 10-15% при увеличении стойкости на 20-25%. К достоинствам указанного инструмента с механическим креплением. Следует отнести также быстроту замены пластины не требующей как правило подналадку станка; сокращение персонала обеспечивающего инструментом рабочие места; сокращение парка заточного оборудования.
Повысить требования предъявляемые к абразивному инструменту работающему на высоких скоростях. Например шлифование вторичного вала КПП в АЛ — 35 мс вышлифовка канавок на валах взамен точения скорость 63мс.
Важным элементом комплексе обеспечивающих интенсификацию процессов резания является новый подход к проблеме охлаждения инструмента. Необходимо резко увеличить норму СОЖ на единицу инструмента. (При установленной на заводах страны норме 30-70 лмин на шпиндель необходимо применять норму 100-200 ммин. )
Осуществить ряд мероприятий по подготовке и переработке СОЖ Эмульсия должна подвергаться 100% фильтрации на специальных установках. Система подачи жидкости должна быть полностью централизована а система отвода СОЖ совмещена с централизованной системой удаления отходов обработки. Размещение устройств для сбора СОЖ и отходов производства обычно осуществляется в двух тоннелях со специальными транспортерами. Обильное охлаждение исключает необходимость ручной очистки посадочных мест в приспособлениях от стружки а фильтрация по опыту западных фирм повышает стойкость инструмента на 10-12% уменьшает юное подвижных элементов оборудования.
На агрегатных и специальных станках использовать магазины автозагрузки. (На ВАЗе 65% всех протяжных станков механообрабатывающего производства имеют средства автоматической загрузки с магазинами 37% парка агрегатных и зубофрезерных станков оснащены магазинами-накопителями).
Широко использовать на операциях шлифования и хонингования средства автоматического контроля с обратной связью. На ВАЗе 70% всего шлифовального и хонинговального оборудования оснащено такими устройствами.
За счет конструктивных особенностей оборудования высокой надежности гидравлических электрических пневматических его систем особенно систем контроля должны быть обеспечены коэффициенты использования оборудования не ниже чем на западных фирмах:
зубошевинговальных и шлифовальных станков - 094;
остального металлорежущего оборудования - 095-096.
С целью повышения надежности при высоких эксплуатационных режимах целесообразно вертикальные токарные полуавтоматы типа «Буллард» заменить автоматическими линиями или лоботокарныни станками.
1 Описание конструкции контрольного приспособления.
Контрольное приспособление применяемое для контроля параметров зубчатого венца шестерни
В производстве зубчатых колес комплексная двухпрофильная проверка является самой распространенной ее применяют после отдельных операциях технологического процесса - зубофрезерования зубодолбления зубошевингования а также после окончательной обработки зубчатого колеса дл>. того чтобы на сборку не попадали дефектные зубчатые колеса.
При комплексном двухпрофильном контроле проверяемое зубчатое колесо (рис. 15 а) находится в плотном двухпрофильном зацеплении с измерительным колесом 3 под действием пружины 2. При взаимной обкатке вследствие погрешностей проверяемого зубчатого колеса происходит перемещение подвижной каретки 4. Смещение фиксируется и анализируется в электронном приборе 5 затем результаты измерения указываются на экране дисплея б и могут быть записаны на ленте. При этом виде контроля проверяют: колебание измерительного межосевого расстояния за оборот колеса рисунок и на одном зубе.
Рисунок 15. Комплексный двухпрофильный контроль:
а - схема прибора; б — колебание измерительного межосевого расстояния за оборот колеса и на одном зубе; в — радиальное биение; S — отклонение шага
Отклонение межосевого расстояния припуск под шевингование наличие забоин на зубьях. На современных приборах кроме контроля в двухпрофильном зацеплении путем добавления к прибору измерительных устройств которые устанавливают на ось подвижной каретки 4 можно контролировать радиальное биение F. (рис. 15 б) и отклонение шага fp (рис.-15 г). Эти приборы -универсального типа с их помощью можно контролировать зубчатые колеса с "прямыми и косыми зубьями внешнего и внутреннего зацепления конические и червячные передачи
Рисунок 16 Схема автомата для комплексного двухпрофильного контроля зубчатых колес.
Повышение производительности при комплексном двухпрофильном контроле можно достигнуть путем применения автоматов. Преимуществом автоматических измерительных приборов являются их высокая производительность и точность измерения. Автоматические измерительные приборы особенно эффективны когда требуется сплошной контроль например после окончательной обработки зубчатых колес. У приборов с автоматическим циклом измерения загрузка и разгрузка производятся автоматически с разделением на группы по точности и выявлением брака. Продолжительность цикла проверки составляет 36-6 с для каждого колеса.
На рис. 16 приведена схема автомата с пультом 15 управления для комплексного двухпрофильного контроля. Заготовки 14 катятся по наклонному подводящему лотку а отсекатель 7 по одной заготовке выдает их в зону измерения где зубчатое колесо 2 обкатывается в плотном зацеплении с измерительным колесом 3 под давлением пневмоцилиндра 16. После измерения шток цилиндра 16 опускается проверенное зубчатое колесо по наклонному отводящему лотку направляется в сортировочное устройство . Фактические размеры измерения указываются на экране 5 а допуск на размер — на экране 6. Если фактические размеры не укладываются в допуск то зажигаются лампы 4. Общее число проверенных зубчатых колес указывается на экране 8 а бракованных — на экране 9. Эти данные необходимы для анализа производственного процесса.
Погрешности проверяемого зубчатого колеса во время обкатки с измерительным колесом регистрируются усиливаются и передаются в два фильтра. Фильтр низких частот регистрирует отклонения за оборот колеса (по этим данным судят о точности колеса) а фильтр высоких частот — погрешности зацепления на каждом зубе забоины заусенцы и т. д.
Результаты измерения сравниваются с допустимыми значениями. О годных и бракованных зубчатых колесах дается сигнал в сортировочное устройство . Годные зубчатые колеса направляются по лотку 22 по другим лоткам перемещаются колеса с дефектами:
— на доработку; 20 — с забоинами; 19 — с повышенным биением; 17 18'— с отклонением межосевых расстояний. Когда на зубьях имеются небольшие заусенцы целесообразно перед контролем эти зубчатые колеса обкатывать в специальном обкаточном устройстве 12. Обкатываемое колесо 13 устанавливают между тремя обкаточными колесами 10 которые вращаются под давлением и удаляют забоины и заусенцы. В зону обкатки зубчатые колеса подаются по одному через отсекатель 11 после обкатки они по лотку поступают в автомат на измерение.
Станция для контроля межосевого расстояния.
Данное приспособление состоит из корпуса 1 управляющей системы 2 каретки 3. К корпусу 1 прикреплен фланец 4 внутри которого размещен вал 5 обеспечивающий перемещение каретки 3. К каретке крепится кронштейн 6 с упором 7. На оправке 8 установлен датчик 9 который обеспечивает контроль межосевого расстояния.
Управляющая система 2 состоит из блока шестерен 11 12 и 13 обеспечивающего перемещение контрольного диска 10.
При включении двигателя вал 5 установленный во фланце 4 начинает перемещать каретку 3 установленную в корпусе 1. Для осуществления контроля датчик 9 закрепленный в оправке 8 обеспечивает контакт с упором 7 установленном на кронштейне 6. Для измерения соответствующих параметров зубчатого колеса используется диск 10 установленный на оправке. Перемещение диска осуществляется за счет системы блока шестерен 11 12 13.
Погрешность измерения должна удовлетворять условию 003
Погрешность измерения определяется по формуле
где уст = 0002 мм– погрешность установки;
напр = 0001 мм – погрешность направляющих устройства при перемещении элементов прибора;
констр=0005 мм – погрешность конструкции элементов прибора;
пр=00001 мм – погрешность самого измерительного прибора;
п= 0005 мм – погрешность подвижных элементов связанных с показывающим прибором.
Следовательно данное устройство обеспечит требуемую точность измерения.
2 Описание конструкции рабочего приспособления.
В мембранных патронах (рис.1) центрование и зажим зубчатого колеса осуществляются шестью кулачками2мембраны1к которым привертываются сменные кулачки3с зажимными поверхностямиЕ.В процессе съема и установки колеса шток8прогибает мембрану1вправо и кулачки расходятся. Зубчатое колесо устанавливают в патрон вместе с надетой на него обоймой с шестью роликами15.Дополнительное базирование по торцу колеса обеспечивается тремя сменными опорами13.Во избежание биения сменных кулачков3их шлифуют на месте для чего в кулачках2предусмотрены выточкиГпод установочное кольцо14.Винт4служит для регулировки сменных кулачков3перед их шлифованием.
Шток8предназначен для соединения патрона с механизированным приводом расположенным на заднем конце шпинделя станка. Предохранительное кольцо7ограничивает ход штока вперед (при разжиме). В направляющей втулке6смонтирована втулка12служащая для направления калибра активного контроля в процессе шлифования. Патрон базируется по поверхностямЖиИ.Опорная поверхностьМслужит для установки сменных кулачков3.Установочное кольцо14базируется по поверхностям кулачковЛиП'.Для измерения перемещения кулачка под действием осевого усилия штока предусмотрена поверхностьС.Для обеспечения безопасности при работе патрон защищен кожухом11который крепится винтами10к корпусу9.Уравновешивание патрона осуществляется за счет установки шести противовесов 5.
Измерение в процессе шлифования на внутришлифовальных станках осуществляется автоматически. Для этого необходимы средства активного контроля управляющие циклом и обеспечивающие заданный размер. По мере приближения к заданному размеру механизм активного контроля даёт команду исполнительным органам станка на уменьшение поперечной подачи круга чистовую правку выхаживание и отвод круга. Активный контроль осуществляют мерительными автокалибрами рычажноследящими устройствами и пневмодатчиками.
Использование автокалибров покажем на примере. После установки детали в патроне оператор вручную подводит шлифовальный круг до начала шлифования и включает самоход. Далее процессом управляет механизм активного контроля. Шток с закреплённым на нём измерительным калибром-2 (Рис. 2.1.) при возвратнопоступательном движении в полом шпинделе передней бабки подводит калибр до упора к шлифуемому отверстию с нерабочей стороны. Калибр выполнен ступенчатым. Когда диаметр отверстия достигает размера d 1 калибр входит в отверстие передней частью и через рычаг 3 и шток 4 размыкает
Рис. 2. Схемы наладки для шлифования отверстия и торца зубчатого колеса: а - мембранный патрон; 6 - схема установки зубчатого колеса на роликах; в - схема измерения обрабатываемого отверстия автокалибром
Когда диаметр отверстия достигает размера d 1 калибр входит в отверстие передней частью и через рычаг 3 и шток 4 размыкает контакт 5 в электроконтактной головке сообщая при этом команду на правку круга. После правки шлифование продолжается. При достижении d 2 калибр полностью входит в отверстие размыкает контакт 6 и шлифовальный круг отходит в исходное положение. Для повышения точности работы применяют плавающие калибры. Плавание калибра обеспечивается с помощью зазора 05 мм между штоком-1 и направляющей втулкой-7 а также зазора 005 мм при прокладке калибра-2 на болте-8.
3 Подборка материалов по инструментальному обеспечению технологического процесса.
Номенклатура применяемого инструмента.
На токарных операциях применяются резцы с неперетачиваемыми
TI5K6-для чистовой обработки:
T14К8 - для получистовой обработки;
Т5К10 - для черновой обработки.
На операции зубофрезерования обработка осуществляется трехзаходной червячной фрезой с m=35 материал фрезы - сталь P18.
На шлифовальных операциях:
ПП 37 (плоский прямого профиля наружный диаметр 37 мм высота 37 мм диаметр отверстия 10 мм 23А - марка абразивного материала (электрокорунд белый 99% Аl2O3) 25-номер зернистости твердостью СМ2 на керамической связке К с номером структуры 5 рабочая скорость круга не должна превышать 45 мсек.)
ПВ 38 (плоский с выточкой наружный диаметр 38 мм высота 25 мм диаметр отверстия 10 мм 23А - марка абразивного материала (электрокорунд белый 99% Аl2O3) 16-номер зернистости твердостью СМ2 на керамической связке К с номером структуры 8 рабочая скорость круга не должна превышать 60 мсек.)
ЧЦ 85x30x20 23A16CM28K5 45 мс. (чашечный цилиндрический наружный диаметр 85 мм высота 30 мм диаметр отверстия 20 мм 23А - марка абразивного материала (электрокорунд белый 99% Аl2O3) 16-номер зернистости твердостью СМ2 на керамической связке К с номером структуры 5 рабочая скорость круга не должна превышать 45 мсек.)
На шевинговальной операции обработка осуществляется шевером облегающим левым с нормальным модулем m=35 материал - сталь Р18 (Сталь инструментальная быстрорежущая)
Режущие и вспомогательные инструменты (державки алмазные карандаши хонинговальная головка и др.) хранятся на складе и периодически по мере их износа в комплектах поступают на линию из передвижных накопителей «Унифлекс» с помощью транспортной системы «Робокар».
Так как на токарных операциях применяются резцы с неперетачиваемымн режущими поворотными пластинами треугольной или ромбической формы то после износа одной кромки пластины она поворачивается и после
этого ведется дальнейшая обработка до тех пор пока все кромки пластины не потеряют свою режущую способность.
Правка шлифовальных кругов производится по мере их «засаливания» алмазными карандашами. Другие используемые инструменты подвергают заточке вне линии.
Смена инструмента происходит по графику что предупреждает его затупление и поломку обеспечивая тем самым качественную обработку деталей.
Настройка инструментов для токарных операций проводится перед каждой операцией вне станка с помощью прибора фирмы «Питтлер».
4 Система активного обслуживания инструментом автоматических и поточных линий.
Системой предусматривается:
Доставка режущего инструмента на производственные участки для пополнения страховых запасов работниками централизованной инструментальной раздаточной кладовой.
Смена затупившегося инструмента по специальному графику.
Смена инструмента по графику предупреждает чрезмерное затупление и его поломку обеспечивает качественную обработку деталей.
Система устраняет потери рабочего времени наладчиков на сдачу и получение инструмента повышает производительность автоматических и поточных линий.
Специальные инструментальные шкафы размером 650х1000х1900мм устанавливаются непосредственно на производительных участках и являются местом хранения инструмента и рабочим местом наладчика.
Система внедрена на автомобильных заводах: Московском имени И.А. Лихачева производительного объединения «ЗИЛ» Заволжском моторном Челябинском автомеханическом заводах.
Экономический эффект от внедрения на 1 металлорежущий станок составляет 3500 руб. в год.
Система может быть применена в цехах механической обработки как автомобильных так и др. заводах машиностроительной промышленности.
IV Аналитическое исследование.
Алмазные инструменты.
При автоматической обработке деталей для получения большой точности геометрических размеров и высокого класса чистоты поверхностей необходимо иметь такой режущий инструмент который обладал бы высокой размерной стойкостью. Этим требованиям удовлетворяет алмазный режущий инструмент.
Алмазные инструменты из кристаллов алмаза используются в металлообрабатывающей промышленности для тонкого точения и растачивания фрезерования гравирования волочения и резки стекла; в оптико-механической промышленности - для деления шкал сеток лимбов дифракционных решеток и т.д.
Алмазные инструменты в машиностроительной промышленности можно разделить на две основные группы:
)инструменты из порошков алмаза;
)инструменты из кристаллов технических алмазов.
К первой группе инструментов относятся круги шлифовальные на металлической и органической связках круги отрезные хонинговальные бруски надфили пасты и порошки алмазные.
Ко второй группе относятся резцы волоки карандаши иглы и ролики для правки абразивных кругов а также стеклорезы.
Инструменты второй группы изготовляются из кристаллов алмаза путем шлифования и доводки (огранки).
Для отдельных типов правящего инструмента и стеклорезов используются неграненые алмазы.
Сырьем для инструментов из кристаллов алмаза служат технические алмазы причем более высокого качества по сравнению с алмазным бортом предназначенным для дробления в порошки.
Типы и размеры алмазного инструмента регламентированы ГОСТом либо нормалями. В табл. 1 приведена основная номенклатура алмазных инструментов выпускаемых в настоящее время специализированными заводами.
Название инструментов
Круги шлифовальные алмазные
Круги отрезные алмазные
OH14059 ОН14060 ОН14061 НИИАлмаза
РТМ 61 -62 ВНИИИМаш. ОН6-152- 63 до ОН6-173-63 НИИЧаспром
Карандаши алмазно-металлические
Круги шлифовальные алмазные.
Из всех алмазов применяемых сейчас в промышленности 70% используется в качестве алмазного порошка для изготовления кругов брусков надфилей и других инструментов.
Алмазные круги состоят из корпуса и рабочего алмазоносного слоя. Корпуса изготовляются из стали алюминиевых сплавов или полимеров. Алмазоносный слой состоит из алмазного порошка связки и наполнителя.
В настоящее время выпускаются три вида кругов - на металлических на органических н на керамических связках.
Алмазные круги на металлических связках отличаются повышенной прочностью и теплостойкостью значительным сроком службы хорошо сохраняют свою геометрическую форму но быстро засаливаются и требуют частой правки. Эти круги применяются для предварительной обработки когда требуется сошлифовать значительный объем материала с получением 8—9-го классов шероховатости поверхности.
Алмазные круги на органических связках предназначены для окончательной (чистовой) обработки (доводки) когда необходимо достигнуть 10—12-го классов шероховатости. Эти круги отличаются большей производительностью и почти не засаливаются но по сравнению с кругами на металлической связке расход алмаза на единицу веса снятого материала в 3 раза больше.
При работе алмазными кругами на металлической связке применение охлаждения обязательно. Кругами на органической связке можно работать и без охлаждения но при этом увеличивается износ круга.
Одной из важнейших характеристик алмазного круга определяющей при прочих равных условиях экономичность и эффективность его работы является степень концентрации алмазов т. е. количество (в миллиграммах) алмазного зерна в 1 мм3 алмазоносного слоя.
Алмазные круги выпускаются 25- 50- и 100-процентной концентрации алмазного зерна. За 100-процентную концентрацию в практике принято считать 0.878 мгмм3 что соответствует 439 карата в 1 см алмазоносного слоя. Соответственно круги с 50-процснтной концентрацией содержат в 2 раза меньше алмазного зерна т. е. 0439 мгмм3 а с 25-процентной концентрацией — в 4 раза меньше (0.219 мгмм3)
При 100-процентной концентрации алмазные зерна в кругах независимо от материала связки занимают по объёму 25% алмазоносного слоя. Остальные 75% по объему занимают связка и наполнитель. Содержание компонентов в алмазоносном слое различной конфигурации для кругов на органической связке приведено в табл. 2.
Содержание алмазов связки и наполнителя в кругах на органической основе (в % по весу)
Название компонентов
Круги с большой концентрацией алмазов характеризуются большей производительностью. Поэтому высокая концентрация алмазов целесообразна при жестких режимах при шлифовании периферией круга и при необходимости избегать деформации круга. Например для профильного шлифования и при внутреннем шлифовании оптимальной концентрацией является 100-процентная.
Для большинства работ применяют круги 50-процентной концентрации. Круги пониженной концентрации (25%) используются на операциях доводки вручную.
Алмазные круги изготавливаются не только на различных связках и с различной степенью концентрации алмазов но и различными по форме и зернистости.
ГОСТ 24747-81 предусмотрено 68 типоразмеров кругов.
В табл. 3 представлены формы и основные размеры кругов. Каждый тип круга имеет буквенный индекс который состоит из 2х частей. Например в круге АПП буква А обозначает круг алмазный а ПП-плоский прямой. (Обозначение дано по ГОСТ 24747-81 в скобках дано старое обозначение кругов)
Наименование и обозначение круга
Шлифовальный плоский прямого профиля 1А1 (АПП)
Шлифовальный плоский прямого профиля без корпуса А8 (А1ПП)
Алмазные шлифовальные плоские прямого профиля трехсторонние 14V1 (А2ПП)
Шлифовальные чашечные конические 12А2=45° (АЧК)
Шлифовальные чашечные конические 12V2=45° (А2ЧК)
Шлифовальные тарельчатые 12А2=20°(АТ)
Шлифовальные плоские с двухсторонним коническим профилем 14EEIX(А2П)
Все алмазные круги маркируются на внутреннем торце металлического корпуса (наименование завода-изготовителя обозначение зернистости и марки связки характеристика концентрации алмаза высота алмазоносного слоя вес алмаза в каратах номера ГОСТ и круга год изготовления).
Например маркировка круга обозначена: АМ40Б1-50-3-29-9770-61-3240-64. Это значит: зернистость АМ40 на органической связке: марка Б1; концентрация алмаза 50%; высота алмазоносного слоя 3мм; вес алмаза 29 каратов; ГОСТ 9770-61; изготовлен под номером 3240 в 1964 г.
Диаметры отверстий алмазных кругов приняты в соответствии с размерами посадочных мест у шпинделей универсальных заточных станков по ГОСТ 3808-57. а также в соответствии с размерами отверстий шлифовальных кругов по ГОСТ
При выборе кругов для различных работ необходимо учитывать тип станка форму и размер обрабатываемой поверхности требуемые точность и шероховатость поверхности характер связки концентрацию алмазов и их зернистость.
Для рационального использования алмаза формы и размеры кругов выбираются применительно к конкретным операциям (например для шлифования по наружному диаметру для доводки по задней поверхности и т. д.).
Ширина алмазоносного кольца определяется характером работы круга (на проход или врезанием). При работе на проход следует применять круги с широкими рабочими поверхностями а при работе методом врезания—круги с рабочей частью не превышающей высоты обрабатываемой поверхности.
Рекомендуемые режимы шлифования приведены в табл. 4.
Рекомендуемые режимы алмазного шлифования
Внутреннее шлифование
Окружная скорость ммин
Продольная подача ммин
Поперечная подача ммдв. ход
Скорость вращения детали ммин
Номенклатура алмазных кругов выпускаемых по ГОСТ 24747-81 обеспечивает их применение почти на всех моделях шлифовальных станков при круглом (наружном и внутреннем) плоском и фасонном шлифовании.
Зернистость алмазных инструментов выбирают в зависимости от требуемого качества обрабатываемой поверхности согласно рекомендации приведены в табл.5
Выбор зернистости алмазных инструментов
Шероховатость обрабатываемой поверхности Ra мкм
Зернистость круга со связкой
Весьма эффективно используются алмазы и для обработки неметаллических материалов.
Наиболее выгодно обрабатывать алмазным инструментом неметаллические материалы; обладающие высокой твердостью и хрупкостью. К ним относятся различные виды керамики стекло ферриты корунд гранит диабаз полупроводниковые материалы (германий кремний) и ар.
НИИАлмазом выполнен ряд экспериментальных работ по исследованию процессов алмазной обработки неметаллических материалов на основании которых созданы специальные алмазные инструменты установлены режимы обработки и определены удельные расходы алмаза.
Алмазная обработка неметаллических материалов должна проводиться только с охлаждением и при соблюдении необходимых мер безопасности обеспечивающих сохранение здоровья рабочих.
Наиболее трудоемкой операцией при обработке неметаллических материалов
является разрезание для чего применяются алмазные отрезные круги при этом получается равномерная минимальная ширина реза повышается производительность труда и легко автоматизируется процесс резания.
Алмазные порошки представляют собой дробленые осколки или монокристаллы правильной кристаллической формы определенных размеров. За размер принимается половина суммы длины и ширины проекции зерна на предметное стекло микроскопа.
Алмазные порошки выпускаются по ГОСТ 9206-59 в виде шлифзерна
шлифпорошков и микропорошков.
Размеры зерен алмазных порошков определяют с помощью микроскопа снабженною окулярной шкалой или сеткой. Результаты микроскопического анализа выражают в процентах от количества зерен для каждой фракции отдельно. Основная фракция алмазного порошка (в %) состоит из совокупности зерен определенного размера преобладающих по количеству в составе данного порошка.
В табл. 6 приведены предельные размеры зерен основной фракции алмазных порошков.
Предельные размеры зерен алмазных порошков
Обозначение зернистости
Размер зерна основной
Верхний предел размера зерна указанный в табл. 6 соответствует размеру ячейки сита в микронах сквозь которое зерно основной фракции проходит а нижний предел - ячейки сита на котором зерно основной фракции остается.
На основе микропорошков АМ40-АМ1 изготовляют алмазные пасты. При доводке и полировании алмазные пасты обладают несколько большей производительностью.
В зависимости от обрабатываемого материала требований шероховатости и условий процесса применяются пасты различной зернистости и концентрации алмаза.
В табл. 7 приведены ориентировочные рекомендации НИИАлмаза по концентрации алмаза в пастах в зависимости от обрабатываемого материала и зернистости алмаза.
Концентрация алмаза в пастах.
Концентрация алмаза в %
Из этой таблицы видно что обработка вязких материалов требует увеличения зернистости и концентрации алмаза в пасте.
Оптимальные условия доводки (полирования) стали ШХ15 алмазными пастами следующие: скорость вращения детали—1.5—1.8 мсек; удельное давление-8- 28 кгсм2; материалы полировальников—самшит или чугун марки СЧ21-40; зернистость пасты—AMI4— АМ28; концентрация алмаза в пасте—10%.
Особо эффективные результаты получены НИИАлмазом совместно с заводом «Калибр» при доводке вставок микрометров из твердого сплава ВК6М алмазной пастой AMI4 10-процентной концентрации. В этом случае выбран следующий режим: скорость вращения притира—6 ммин; материал притира-—чугун марки СЧ21-40; давление притира на деталь—2 кгсм2; продолжительность доводки одного микрометра —30 сек. Шероховатость получаемой поверхности VI2—V14 классы.
Применение алмазной пасты AM14 10-процентной концентрации на доводке твердосплавных вставок микрометров позволило улучшить шероховатость обрабатываемой поверхности на один класс по сравнению с доводкой свободными алмазными порошками и сократить расход алмаза в 10 раз (с 1 до 001—0.08 мг). Наряду с этим установлена реальная возможность автоматизации процесса нанесения насты на притир так как пасты более удобны для автоматизации чем свободные порошки.
Эффективность алмазных паст подтверждается и данными полученными при доводке редуцированных плашек из твердого сплава ВК20. Так например алмазные пасты зернистостью АМЗ АМ14 и АМ28 позволили получить 11-Й класс шероховатости.
Алмазные пасты АМ28 и AM14 применяются на предварительной доводке при съеме припуска 20—30 мкм а наста АМЗ—на окончательной доводке до требуемых размеров. В этом случае расход алмаза составляет 25 карата на 10 комплектов плашек.
Как видно из табл. 8. алмазные пасты выпускаются двенадцати зернистостей которые условно делятся на четыре группы.
Классификация алмазных паст
Условное обозначение алмазной пасты
Размер зерен основной фракции мкм
Условная окраска упаковки
Условное название группы
Красная с серной полоской
Красная с серой полоской
Красная с белой полоской
Зеленая с черной полоской
Зеленая с серой полоской
Зеленая с белой полоской
Голубая с черной полоской
Голубая с серой полоской
Голубая с белой полоской
Желтая с черной полоской
Желтая с серой полоской
Желтая с белой полоской
По концентрации алмазные пасты различают на нормальную-Н (например АП14Н); повышенную-П (АП14П) и высокую-В (АП14В).
Алмазные хонинговальные бруски
Алмазные хонинговальные бруски являются одним из наиболее перспективных инструментов; они в 100— 120 раз более стойки чем абразивные бруски. Кроме того высокая стойкость алмазных хонинговальных брусков позволила резко сократить количество подналадок станков и автоматизировать процесс хонингования который происходит при низких температурах резания благодаря этому появилась возможность обрабатывать тонкостенные детали с большими перепадами сечения стенки.
Особенно успешно применяются алмазные хонинговальные бруски при обработке точных отверстий малого диаметра (до 10 мм) когда отклонения отверстий по диаметру находятся в пределах 3—5 мкм по непрямолинейности — в пределах 1 мкм и по конусности — не более 3 мкм. Это достигается благодаря высокой механической прочности брусков.
Алмазные хонинговальные бруски изготовляемые методом порошковой металлургии состоят из металлокерамического основания и алмазоносного слоя.
Алмазный инструмент для правки шлифовальных кругов
Алмазная правка шлифовальных кругов относится к числу важнейших областей применения алмазов в машиностроении.
Качество обработки шлифуемых деталей стойкость круга и производительность шлифования в значительной степени определяются точностью формы шлифовального круга и микрорельефам его поверхностного слоя которые зависят от конструкции правящего инструмента его износостойкости режимов и приемов правки.
Алмазная правка шлифовальных кругов обладает существенными
преимуществами по сравнению с другими способами. Благодаря весьма малой поверхности контакта алмаза со шлифовальным кругом достигаются минимальные усилия которые в сочетании с высокой износостойкостью алмаза создают условия дня получения высокой точности геометрической фирмы круга а отсюда и высокой точности и чистоты поверхности у шлифуемых деталей.
Правка алмазным инструментом обеспечивает повышение стойкости круга в 1.5-16 раза по сравнению с правкой безалмазными правящими инструментами.
В промышленности для правки шлифовальных кругов применяются следующие инструменты:
)алмазно-металлические карандаши;
)алмазы естественной формы закрепленные в оправах;
)ограненные (шлифованные) алмазные инструменты (резцы иглы);
)алмазные круги и бруски не металлической связке.
Изучение технологического процесса изготовления шестерни третьей передачи промежуточного вала КПП автомобиля Зил-130 показало что процесс изготовления находится на достаточно высоком технологическом уровне деталь технологична.
Но независимо от этого можно провести отдельные усовершенствования технологического процесса:
При изготовлении косозубых цилиндрических колес применить метод фрезерования по способу «Тронта» при котором имеет место непрерывное смещение зацепления червячной фрезы и снижение tM за счет уменьшения времени врезания и выхода фрезы по сравнению с обычным фрезерованием.
Повысить производительность обработки за счет широкого использования в крупносерийном производстве принципа концентрации операций и совмещения неоднородных по технологическому признаку автоматических линий и агрегатов в единую систему.
Типовые технологические процессы механической обработки деталей автомобилей. Каталоги. Руководящие материалы. НИИТавтопром. М. 1969.
Калашников А.С. Современные технологические процессы изготовления зубчатых колес в автотракторной промышленности. Конспект лекций по курсу «Технология автоматизированного производства». МАМИ. 1997.
Производство зубчатых колес. Под. ред. Б.А. Тайца. «Машиностроение» М. 1975.
Калашников С.Н. Калашников А.С Зубчатые колеса и их изготовление. - М. «Машиностроение» 1983.
Калашников С.Н. Калашников А.С Изготовление зубчатых колес. М. Высшая школа 1980.
Мерганский Д.П. Зуборезное дело. «Машиностроение» 1969.
Справочник. Производство зубчатых колес. Под. ред. Б.А. Тайца. -М. «Машиностроение» 1990.
А.С. Калашников СИ. Калашников. Комплексная автоматизация производства зубчатых колес. М. «Машиностроение» 1991.
Сильвестров Б. Н. Зубошлифовальные работы . М. Высш. школа 1985.
Ю.Марков А.Л. Измерение зубчатых колес допуски методы и средства контроля. Ленинград «Машиностроение» 1997.
М. У. к лаб. Работе № 12В. «Нормирование точности цилиндрических зубчатых колес и передач» по курсу «Взаимозаменяемость стандартизация и технические измерения». М. МАМИ 1986.
Харалампиев И.С. Обкатывающее протягивание зубьев зубчатых колес. М. «Машиностроение» 1981.
Патрон мембранный.cdw

шестери III передачи
промежуточного вала коробки передач автомолбиля ЗИЛ-4342
На виде справа деталь непоказана
спецификация Контрольное приспособлениее 1.doc
Винт М8-6g×16 ГОСТ 5993 – 58
Гайка М20-6Н.10 ГОСТ 5957 – 51
Технологический процесс изготовления шестерни
III передачи промежуточного вала КП автомобиля ЗиЛ-4342
Станция для контроля
межосевого расстояния
Рекомендуемые чертежи
- 24.01.2023
- 24.05.2017
- 30.03.2018