Ремонт промежуточного вала коробки передач ЗИЛ 130



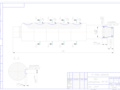
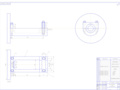
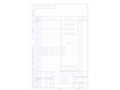
- Добавлен: 25.10.2022
- Размер: 775 KB
- Закачек: 1
Описание
Состав проекта
![]() |
![]() ![]() |
![]() ![]() ![]() |
![]() ![]() ![]() |
![]() ![]() |
![]() ![]() ![]() |
![]() ![]() |
![]() |
![]() ![]() ![]() ![]() |
![]() ![]() ![]() |
![]() ![]() ![]() ![]() |
![]() ![]() |
![]() ![]() |
Дополнительная информация
Опер кар мех 2.doc
Инструмент (код наименование)
вспомогательный режущий измерительный
Режимы обработки (резания)
Мерить посадочное место под подшипник.
Точить вал под резьбу .
Проходной резец с на-
пайкой из сплава Т5К10
Мерить диаметр вала под резьбу.
Снять деталь со станка
Ключ к трёхкулачковому
Точить вал под резьбу
Резать резьбу резцом М33х15g6
Резьбовой резец с на-
пайкой из сплава Т15К6
Мерить резьбу М33х15g6
Кольцо резьбовое про-
ходное и не проходнгое
Шлифовать посадочное место под подшипник
Наждачная бумага 5 мкр
до номинального размера
Снять вал с фрезерного станка
Маршрутная карта.doc
Единица нормирования
Наименование и содержание операции
Оборудование (код наименование инвентарный номер)
Приспособление инструмент (код наименование)
Объем производственной
Токарная. Точить посадочное место под
подшипник до размера 36р6
Токарная. Точить вал под резьбу до
Слесарная. Закрепить вал в приспособление
Слесарная. Установить приспособление с валом
Механическая. Запрессовать втулку на вал при
Фрезерная. Фрезеровать шпон-паз до размера
Токарная. Точить посадочное место под подшип-
ник до размера: диаметр 40р8 мм. длинна 18 мм.
Токарная. Точить вал под резьбу до размера 33h6.
Токарная. Резать резьбу резцом М33х15g6.
Токарная. Шлифовать в токарном станке посадоч-
ное место под подшипник до номинального раз-
Наждачная бумага 5мкр.
курсовая1.doc
ВЛАДИВОСТОКСКИЙ ГОСУДАРСТВЕННЫЙ УНИВЕРСИТЕТ
КАФЕДРА СЕРВИСА И ТЕХНИЧЕСКОЙ ЭКСПЛУАТАЦИИ АВТОМОБИЛЕЙ
ПОЯСНИТЕЛЬНАЯ ЗАПИСКА
по дисциплине “Ремонт автомобилей”
Ремонт промежуточного вала коробки передач ЗИЛ 130
Принятые сокращения . .. 3
Технологическая часть . .5
1. Анализ исходных данных для разработки технологического процесса .5
2. Обоснование размеров производственной партии 7
3. Выбор рационального способа восстановления детали 7
4. Разработка схем технологического процесса восстановления
4.1.Схема технологического процесса восстановления вала. .9
5. План технологических операций восстановления детали 11
6. Разработка операций 13
6.1. Постановка дополнительной детали 13
6.2. Расчет режима механической обработки (нарезание резьбы)
и норм времени на операцию 16
Список используемых источников . . .. 21
Принятые обозначения
В - временное сопротивление ;
- относительное удлинение;
нв -твердость нормализованной стали
N- количество автомобилей агрегатов ремонтируемых в год.
nа – количество одноимённых деталей в агрегате.
Крm – маршрутный коэффициент ремонта.
-– коэффициент трения
d – диаметр контактирующих поверхностей
L –длинна запрессовки
p – удельное контактное давление сжатия
dно - нижнее предельные отклонения вала;
dво - верхнее предельные отклонения втулки;
Δ – максимальный расчётный натяг
С1– коэффициент охватываемой детали
С2 - коэффициент охватывающей детали
Е1 – модуль упругости материала охватываемой детали
Е2 – модуль упругости материала охватывающей детали
d 0 - диаметр охватываемой детали
D – наружный диаметр охватывающей детали
и 2 - коэффициенты Пауссона
t - глубина резанья
i - число рабочих проходов
d – максимальный диаметр обрабатываемой детали
nф –фактическое число оборотов
необходимая мощность главного электродвигателя станка.
действительная мощность главного электродвигателя станка.
фактическая мощность затрачиваемая на резание
Vф – фактическая скорость резания
механический КПД станка
Т0 - основное время
L – длина обрабатываемой поверхности по чертежу;
I1 – величина врезания резца
I2 - величина перебега при обтачивании на проход
tус - время на установку и снятие детали;
tизм - время на измерения
tпер – время перехода
t 1изм –измерение штангенциркулем
t 2изм – проверка детали резьбовым калибром
L –диаметр вала под резьбу;
K– число точек замеров;
L –длина навинчивания;
Топ - оперативное время
Тд - дополнительное время
КI – % дополнительного времени от оперативного
Тп-з - подготовительно-заключительное время
Тш.к.- штучно-калькуляционное время
Основная задача которую преследуют ремонтные предприятия это снижение себестоимости ремонта автомобилей и агрегатов при обеспечении гарантий потребителей т.е. гарантии после-ремонтного ресурса.
Исследования ремонтного фонда (автомобилей и агрегатов поступающих в ремонт) показали что в среднем около 20% деталей – утильных 25 40% - годных а остальные 40 55 % - можно восстановить. Даже процент утильных деталей можно значительно снизить на АРП если оно будет располагать эффективными способами дефектации и восстановления.
Технологии восстановления деталей относятся к разряду наиболее ресурсосберегающих так как по сравнению с изготовлением новых деталей сокращаются затраты на 70%. Основным источником экономии ресурсов являются затраты на материалы. Средние затраты на материалы при изготовлении деталей составляют 38% а при восстановлении – 66% от общей себестоимости. Для восстановления работоспособности изношенных деталей требуется в 5 8 раз меньше технологических операций по сравнению с изготовлением новых деталей.
В данной курсовой работе закрепим пройденный материал по курсу восстановления деталей применим на практике знания по написанию маршрутных карт рассмотрим вопрос о выборе методов восстановления деталей оформлением графической части а также систематизации исходных данных.
Технологическая часть
1. Анализ исходных данных для разработки технологического процесса.
Согласно задания необходимо отремонтировать промежуточный вал коробки передач ЗИЛ-130
Износ поверхности под задний шарикоподшипник до диаметра менее 3998 мм. исходный размер был 400мм.
Срыв и смятие резьбы более двух ниток размер резьбы
Износ поверхности под шпонку до размера более 1098 мм. изначальный размер 100мм.
Данный вал изготовлен из стали марки 25 ХГМ . Это хромомарганцевая сталь подлежащая термической обработке. Возможные методы обработки – цементация или цианирование закалка низкотемпературный отжиг.
Состав стали 25ХГМ – углерод - 023-029% кремний – 017-037 % марганец – 090-120 % хром – 090-120 % молибден – 02-030 %.
Механические свойства данной стали :
- временное сопротивление (В) 120 кгсмм2 ;
- относительное удлинение () 110 %;
- ударная вязкость (αн) 8 кгн*мсм2
-твердость нормализованной стали (нв) не более HRC 60-65
Масса детали – 47 кг
Оборудование –токарный станок 1К62 ОСТ 2 квалитет 6 Фрезерный станок ОСТ пресс гидравлический.
Промежуточный вал устанавливается в корпус коробки на двух опорных подшипниках. На вал действуют вращательные и радиальные силы. При работе в узле деталь подвергается изгибу кручению ударным нагрузкам возможен нагрев детали до 90С.
Износ поверхностей детали подлежащие восстановлению – равномерный поверхность под шпонку изношена с одной стороны.
Класс детали круглые стержни. Деталь имеет цилиндрическую форму ее длина значительно превышает диаметр.
Вал обтачивается в токарном станке класс точности по ОСТ «2» квалитет «6». Для механической обработке будут использоваться резцы из сплава Т5К10 при котором коэффициент обрабатываемости 10 – 15 а при нарезании резьбы Т15К6.
Шероховатость вала :
- посадочные поверхности под неподвижные посадки «p6» - (Rа) – 125 ммк
- резьбовые соединения обрабатываются с допуском «q7» шероховатость – 125ммк
- шпоночное соединение обрабатываются с допуском «H6» шероховатость – 50ммк
2. Обоснование размеров производственной партии
Размер партии определяем по формуле:
3. Выбор рациональных способов восстановления детали
Износ поверхности под шпонку до размера более 1098 мм. изначальный размер 100мм
Срыв и смятие резьбы более двух ниток размер резьбы 36 Х 15
Первый дефект это- износ поверхности под задний шарикоподшипник до диаметра менее 3998 мм. Этот дефект можно устранить несколькими способами:
Можно наплавить электродуговой сваркой посадочное место и проточить на токарном станке. Данный способ потребует отжига сварочные работы механическая обработка на токарном и шлифовальном станке и последующей закалки.
Следующий способ это «установка дополнительной ремонтной детали». Для этого вал протачивается на меньший диаметр и устанавливается на него дополнительная отдельно выточенная втулка соответствующих размеров. После этого вал в месте ремонта протачивается и шлифуется до окончательных соответствующих размеров. Весь процесс восстановления проходит в механическом цехе.
Дефект износ поверхности под шпонку до размера более 1098 мм. также можно устранить несколькими способами:
Можно прорезать посадочное место под шпонку с другой стороны вала но этот способ вызовет нежелательное ослабление вала.
Следующий способ заплавать электродуговой сваркой посадочное место и проточить на токарном станке. Данный способ потребует отжига сварочные работы механическая обработка на фрезерном и шлифовальном станке и последующей закалки. Однако этот способ опасен тем что во время выполнения сварочных работ под действием односторонней температуры может изогнуть вал или образоваться микротрещины в нутрии него что приведёт к браку.
Можно просто расширить шпонпаз на фрезерном станке до размера 12 мм. Выдержав соответствующие допуски на посадку а для сборки агрегата изготовить фасонную шпонку. . Весь процесс восстановления проходит в механическом цехе.
Срыв и смятие резьбы более двух ниток также восстанавливается несколькими способами:
Один из них это наплавать электродуговой сваркой место где резьба до соответствующего размера проточить на токарном станке и нарезать новую резьбу. Данный способ потребует отжига сварочные работы механическая обработка на токарном станке и последующей закалки.
Следующий способ чисто механический – проточить вал и нарезать резьбу меньшего диаметра. При сборке агрегата взять гайку соответствующего размера.
Проанализировав способы ремонта всего вала выберем следующие:
«Установка дополнительной ремонтной детали». Для этого вал протачивается на меньший диаметр и устанавливается на него дополнительная отдельно выточенная втулка соответствующих размеров. После этого вал в месте ремонта протачивается и шлифуется до окончательных соответствующих размеров. Весь процесс восстановления проходит в механическом цехе.
Расширить шпонпаз на фрезерном станке до размера 12 мм. Выдержав соответствующие допуски на посадку а для сборки агрегата изготовить фасонную шпонку. Весь процесс восстановления проходит в механическом цехе.
Проточить вал и нарезать резьбу меньшего диаметра. При сборке агрегата взять гайку соответствующего размера. Процесс восстановления проходит в механическом цехе.
Весь процесс восстановления пройдет в механическом цехе что облегчит задачу и не потребует движения по другим цехам сэкономит время и ресурсы при восстановлении детали.
4. Разработка схем технологического процесса восстановления дефектов
«Установка дополнительной ремонтной детали». Для этого вал протачивается на меньший диаметр и устанавливается на него дополнительная отдельно выточенная втулка соответствующих размеров. После этого вал в месте ремонта шлифуется до окончательных соответствующих размеров.
Срыв и смятие резьбы более двух ниток размер резьбы 36Х15
Проточить вал и нарезать резьбу меньшего диаметра.
Износ поверхности под шпонку до размера более 1098 мм.
Расширить шпонпаз на фрезерном станке до размера 12 мм. Выдержав соответствующие допуски на посадку
4.1.Схема технологического процесса восстановления вала
Наименование и содержание операции
Износ поверхности под задний шарикоподшипник
Установка дополнительной ремонтной детали
Проточить поверхности под задний шарикоподшипник до размера 36мм.
Центра используемые при изготовлении детали
Запрессовать втулку на вал при помощи пресса
Торец вала поверхность переднего
подшипника посадочное место под шестерню
Проточить поверхности под задний шарикоподшипник до номинального размера 40р6мм.
Шлифовать вал до номинального размера
Срыв и смятие резьбы более двух ниток
Проточить резьбу и нарезать резьбу меньшего диаметра
сточить резьбу до размера 33мм.
Нарезать резьбу резцом диметр 33 мм. шаг 15мм.
Износ поверхности под шпонку
Фрезеровать на фрезерном станке посадочное место под шпонку
Фрезеровать на фрезерном станке посадочное место под шпонку до размера 12 H8-5.0
Цилиндрическая часть вала
5.План технологических операций восстановления детали.
Проточить посадочное место род подшипник до размера 36р6
Токарный станок1К62 ОСТ 2 квалитет 6
Проходной резец с напайкой из сплава Т5К10
Микрометр ГОСТ 6507-68
Проточить вал под резьбу до размера 335h6
Слесарная Закрепить вал в приспособление для удержания вала
Приспособление для удержания вала
Ключ накидной гаечный 14 мм
Установить приспособление с валом на пресс
Фрезеровать шпон-паз до размера 12H8
Фрезерный станок ОСТ 2 квалитет 6
Штангенрейсмус ГОСТ 164-73
Проточить посадочное место под подшипник до размера диаметр 40р6мм.
Токарный станок 1К62 ОСТ 2 квалитет 6
Проточить вал под резьбу до размера 33h6
Нарезать резцом резьбу М33х15g6
Резьбовой резец с напайкой из сплава Т15К6
Шагомеры НЦ-1; НЦ-2; НЦ-3; ГОСТ 3883-74; кольца резьбовые не регулируемые проходные и непроходные ГОСТ 1774-71
Шлифовать в токарном станке посадочное место под подшипник до номинального размера 40p6-1.25
Приспособление для удержания наждачной бумаги
Наждачная бумага 5мкр
6.Разработка операций
Исходные данные к разработке операций:
- Вал промежуточный ЗИЛ – 130 ремонтировать посадочное место под подшипник с размера- менее 3998 до размера- 4000; ремонтировать резьбу на конце вала- резьба 36Х15 (повреждение более трёх ниток) до размера 33Х15.
-Деталь изготовлена из стали марки 25 ХГМ.
-После ремонта термообработка ремонтируемых поверхностей не требуется.
-Деталь имеет следующие свойства:
Твёрдость – HRC 60-65
Предел текучести - 110 КГСмм2
Временное сопротивление – 120 КГСмм2
Ударная вязкость – 8 КГС*Мсм2
Масса детали – 47кг
Оборудование –токарный станок 1К62 ОСТ 2 квалитет 6 Фрезерный станок ОСТ 6 пресс гидравлический.
При токарной и шлифовальной обработке базовыми являются центра используемые при изготовлении детали
Вал обрабатывается :
- посадочные поверхности под неподвижные посадки с допуском «р6» шероховатость – 125 ммк
- резьбовые соединения обрабатываются с допуском «6q» шероховатость – 125ммк
- шпоночное соединение обрабатываются с допуском «6h» шероховатость – 50ммк
При токарной обработке использовать резцы из сплава Т5К10 что позволит добиться коэффициента обрабатываемости – 10 – 075 при нарезании резьбы резцы из сплава Т15К6
6.1.Постановка дополнительной детали
Содержание перехода.
Установить вал в приспособление для закрепления.
Запрессовать втулку.
Снять приспособление с валом с пресса.
Вытащить вал из приспособления
Размеры обрабатываемой поверхности:
Диаметр вала – 36 р6() мм
Внутренний диаметр втулки – 36H7(+0025) мм
Наружный размер втулки – 405 мм
Длинна втулки – 190 мм
Длина посадочного места на валу – 18 мм
Усилие запрессовки подсчитаем по формуле:
-– коэффициент трения 008 .010
d – диаметр контактирующих поверхностей 36 (мм)
L –длинна запрессовки 18 (мм)
p – удельное контактное давление сжатия 57 (кгсмм2)
Диаметр контактирующих поверхностей определяем по формулам:
dно - нижнее предельные отклонения вала 36026 мм;
dво - верхнее предельные отклонения втулки - 36025 мм;
– толщина втулки мм;
Толщину втулки определяем по формуле:
n = 1[] – запас прочности
[] – допустимое напряжение кгссм2
Т –предел текучести для материала втулки 110 кгсмм2
Удельное контактное давление сжатия находим по формуле:
р = 10-3Δ[d(С1Е1+ С2Е2)]
Δ – максимальный расчётный натяг 0001 мкм
С1– коэффициент охватываемой детали 070
С2 - коэффициент охватывающей детали 983
Е1 – модуль упругости материала охватываемой детали 20500 кгсмм2
Е2 – модуль упругости материала охватывающей детали 20500 кгсмм2
Коэффициент охватываемой и охватывающей детали определим по -----------------------------------------------------------------------------------------------------------------------------------------------------------------------------------------------------------------------------------------------------------------------------------------------------------------------------------------------------------------------------------------------------------------------------------------------------------------------------------------------------------------------------------------------------------------------------------------------------------------------------------------------------------------------------------------------------------------------------------------------------------------------------------------------------------------------------------------
С1 = [(d2 + d 02)(d2 – d 02)] - 1
C2 = [( D2 + d2) ( D2 – d2 )] -2
d 0 - диаметр охватываемой детали (для вала d 0 = 0)
D – наружный диаметр охватывающей детали - 405 мм
и 2 Коэффициенты Пауссона для стали – 03
или берём из таблицы:
р = 10-3*0001[36*(07020500+98320500)] =57
F = 01*314*36*18*57 = 1150 Н
6.2.Расчет режима механической обработки (нарезание резьбы) и норм времени на операцию
Установить вал в центра станка.
Измерить посадочное место под резьбу штангенциркулем.
Резать резцом резьбу М33Х15.
Измерить резьбу резьбовым калибром.
Снять деталь со станка.
Размеры обрабатываемой поверхности под резьбу:
Размер резьбы до обработки М36 Х 15.
Размер резьбы после обработки М33Х15
Длина обрабатываемой поверхности. L = 18 мм.
Оборудование: токарно-винторезный станок 1К62.
резцы из сплава Т15К6
штангенциркуль Ш Ц – I – 125 – 0.1
микрометр ГОСТ 6507-68
Определение припусков на обработку для нарезания резьбы.
Определяем глубину резанья t и число рабочих проходов i
При диаметре вала до 40мм число проходов «i» – 3-4 (по нормативам) принимаем - 4.
Определяем глубину резанья при «hр» = 1305
t = 1.3054= 0.33 мм.
Выбираем величину подачи S
Величина подачи S ввиду нарезания резьбы равен шагу резьбы – 15 мм.
Определяем скорость резания V по нормативам
Скорость резания V по нормативам = 111ммин. Корректировка не требуется.
Рассчитаем частоту вращения детали по формуле:
V= 111 ммин - скорость резания
d = 33мм – максимальный диаметр обрабатываемой детали
Рассчитанную частоту вращения станка корректируем по паспортным данным
Частот вращения станка корректируемая по паспортным данным nф =1020обмин
Уточним скорость резания в соответствии с фактическими оборотами по формуле:
nф –фактическое число оборотов уточненное и принятое по паспорту станка
Определяем правильность выбора оборудования по мощности.
где необходимая мощность главного электродвигателя станка.
где фактическая мощность затрачиваемая на резание.
Vф – фактическая скорость резания = 106 ммин
nф – фактические обороты =1020 обмин
Pz = 10*Ср * tx * Sy * Vфn *Kp
Ср = 148 х = 1 y = 1.7 n = 0.71 – коэффициент и показатели степени зависящие от конкретных условий обработки взятые из таблицы по нормативам.
Kp = Kмр*Кφр *Кγр *Кλр *Кр
Кφр =089 ; Кγр = 11 ; Кλр = 1 ; Кр =1; Kмр =139
Kp = 139*089*11*1*1 = 136
Pz = 10 * 148 * 0331 * 1517 * 106071 * 136 = 362775 Н
механический КПД станка принимается
Определить основное время Т0
Где: L – 18 мм – длина обрабатываемой поверхности по чертежу;
I1 – величина врезания резца мм;
I2 - величина перебега при обтачивании на проход мм;
Для приближенных расчетов I1+I2 = 3мм
S – 15мм - подача ммоб;
n – 1020 - частота вращения детали обмин;
i – 4 - число проходов инструмента
Определить вспомогательное время
Твс = tус+ tизм+ tпер
tус –125 - время на установку и снятие детали(взято из таблиц по нормативам) мин;
tпер – 015 - время перехода (взято из таблиц по нормативам)мин;
tизм = t 1изм + t 2изм
t 1изм = 00816*L0.25*K0.65
L – 33 мм -диаметр вала;
K – 1 – число точек замеров;
t 1изм = 0.08616 * 33 0.25 * 1 0.65 = 0.2 мин
t 2изм = 00494*D027 * L075 *S0.77
L – 18 мм длина навинчивания;
D – 33 мм – диаметр резьбы;
S – 15 мм – шаг резьбы;
t 2изм = 00494 * 33 025 * 18 075 * 15 077 = 0019 мин
tизм = 02+0019 = 0219 мин
Твс = 125 +0219 + 015 = 1494 мин
Определить оперативное время Топ
Топ = 18 + 1494 = 19494 мин
Определить дополнительное время Тд
КI – 9 - % дополнительного времени от оперативного
Тд = 19494 * 9100 =1754 мин
Определить подготовительно-заключительное время Тп-з
Тп-з = 14 мин (взято из таблиц по нормативам)
Определим штучно-калькуляционное время Тш.к.
Тш.к. = То + Твс+ Тд + Тп.з.nn
nn –0.899 - размер партии деталей
Тш.к. = 18+1494+1754+140899 = 3682 мин
Курсовое проектирование проводилось с целью закрепления знаний полученных при изучении специальных дисциплин самостоятельного решения задач проектирования технологических процессов восстановления и изготовления деталей автомобилей.
В данной курсовой работе закрепили пройденный материал по курсу восстановления деталей применили на практике знания по написанию маршрутных карт рассмотрели вопрос о выборе методов восстановления деталей оформлением графической части а также систематизации исходных данных.
Спецификация.dwg

КП. 190604. СТ0000. 00.СП
Кп.190604. СТ0501. 12.СБ
КП.190604. СТ0501. 12.01
КП.190604. СТ0501. 12.02
КП.190604. СТ0501. 12.03
КП.190604. СТ0501. 12. 04
-6g х 120.109.40Х.26 ГОСТ 22034-76
Сборочный чертёж . Приспособление для крепления вала.dwg

КП.190604.СТ0501.11.СБ
КП.190604.СТ0501.11.01
КП.190604.СТ0501.11.02
КП.190604.СТ0501.11.03
КП.190604.СТ0501.11.04
вал.dwg

Рекомендуемые чертежи
- 24.01.2023
- 30.03.2018
- 24.01.2023
- 25.01.2023