Технологический процесс изготовления шестерни



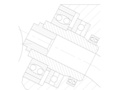
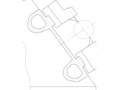
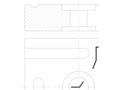
- Добавлен: 24.01.2023
- Размер: 8 MB
- Закачек: 0
Описание
Состав проекта
![]() |
![]() |
![]() |
![]() ![]() |
![]() ![]() ![]() |
![]() |
![]() ![]() ![]() |
![]() ![]() ![]() |
![]() ![]() ![]() |
![]() ![]() ![]() |
![]() |
![]() ![]() ![]() |
![]() ![]() ![]() |
![]() |
![]() ![]() |
![]() |
![]() |
![]() |
![]() |
![]() ![]() ![]() |
![]() |
![]() ![]() ![]() |
![]() ![]() ![]() |
![]() ![]() ![]() |
![]() |
![]() |
![]() ![]() ![]() |
![]() |
![]() ![]() ![]() |
![]() ![]() ![]() |
![]() ![]() ![]() |
![]() ![]() ![]() |
![]() ![]() ![]() |
![]() ![]() ![]() |
![]() ![]() ![]() |
![]() ![]() |
![]() ![]() |
![]() ![]() ![]() |
![]() ![]() |
![]() ![]() ![]() |
![]() ![]() ![]() |
![]() |
![]() |
![]() |
![]() |
![]() |
![]() |
![]() |
![]() |
![]() |
![]() |
![]() |
![]() |
![]() |
![]() |
![]() |
![]() |
![]() |
![]() |
![]() |
![]() ![]() ![]() |
![]() ![]() ![]() |
![]() |
![]() ![]() ![]() |
![]() ![]() ![]() |
![]() |
![]() |
![]() ![]() ![]() |
Дополнительная информация
09_Проектирование режущего инструмента.doc
Согласно индивидуальному заданию в качестве специального режущего инструмента рассмотрим протяжку шлицевую прохода для обработки шлицев в детали 130-1701112. Протяжка сложный многолезвийный инструмент. Позволяющий получить нужный профиль за один проход.
Чаще всего протяжки для обработки отверстий состоят из следующих основных частей (рис. 9.1 а): 1 —хвостовая часть; 2 — шейка; 3 — переходный конус; 4 — передняя направляющая часть; 5 — режущая часть; 6 — калибрующая часть; 7 — задняя направляющая часть. Для тяжелых и длинных протяжек дополнительно выполняют опорную цапфу 8 и задний хвостовик 9 (рис. 9.1 б).
Рассматриваемая протяжка имеет два хвостовика передний и задний служит для окончательной обработки. Первые зубья снимают припуск остальные круглые выглаживающие. Так как протяжка для окончательной обработки то снимаемый ей припуск не велик. Материал режущей части и заднего хвостовика Р6М5 ГОСТ 19265-71 материал переднего хвостовика сталь 40Х ГОСТ 4543-71. Так как протяжка для окончательной обработки то снимаемый ей припуск не велик Твёрдость режущей части и задней направляющей 63..66HRCЭ передней направляющей 61..66HRCЭ хвостовиков 43..51HRCЭ.
Протяжка работает по генераторной схеме резания. При этой схеме резания (рис. 9.2) припуски снимаются параллельными слоями каждым зубом протяжки не по всему профилю а лишь по его части. При этом форма каждого зуба идентична форме предварительно подготовленной под протягивание поверхности и только последние режущие зубья соответствуют форме окончательно обработанной поверхности.
Наличие стружкоразделительных канавок на режущих зубьях протяжек облегчает ее хорошую сворачиваемость в виток и свободное размещение во впадине между зубьями. Форма зубьев и стружечных канавок показана на рис.9.3.
1. Выбор конструктивных элементов протяжки
Формы хвостовых частей протяжек стандартизованы по ГОСТ 4044-70 ГОСТ 4043-70 и зависят от способа крепления в тяговом патроне протяжного станка.
Длинна шейки выбирается с учётом того что бы обеспечить необходимую длину протяжки до первого режущего зуба а её диаметр обычно на 03 1 мм меньше диаметра хвостовой части.
Длина переходного конуса берётся в пределах от 10 до 25 в зависимости от размеров протяжки. Меньший диаметр переходного конуса принимают равным диаметру хвостовика а больший – диаметру направляющей части.
Допуски на длину шейки и переходного конуса не задаются т.е. эти размеры являются свободными.
2. Порядок и результаты расчёта протяжки
Порядок расчёта соответствует методике изложиной в [ ].
наружный диаметр шлицевого отверстия мм;
внутренний диаметр шлицевого отверстия dВ = 60+003 мм;
ширина шлицев b = 11+008 мм;
фаска по внутреннему диаметру шлицев f = 03 мм;
число шлицев nZ = 10;
длина обрабатываемого изделия L = 45 мм;
обрабатываемый материал Сталь 25ХГМ;
наибольший ход ползуна
Расстояние до первого зуба
Припуск под протягивание А = 0005×D+(01 02)×L12 = 12 мм;
Диаметр отверстия до протягивания D01 = DП = D0 – A = 60 – 12 =588 мм;
Диаметр хвостовика d1 = 40 мм;
Площадь хвостовика FХ = 8042 мм2;
Шаг режущих зубьев tР = m×L12 = 14×4512 = 939 мм;
Принятый шаг зубьев 95 мм;
Наибольшее число одновременно работающих зубьев zMAX = 1 + L tР =
Глубина стружечной канавки hK = 3 мм;
Площадь стружечной канавки FK = 492 мм2;
Коэффициент заполнения стружечной канавки K = 4;
Подача допустимая по размещению стружки в канавке sZK = FK (K×L) =
= 492 (4×45) = 0027 ммзуб;
Наибольшее усилие допустимое хвостовиком PХ = FХ ×sХ = 300×8042 = =241260 Н;
Наибольшее усилие допускаемое протяжкой по первому зубу P1 = p×(D01 – – 2h)2 s1 4 = p×(688-2×3)2 450 4 = 1393161 Н;
Расчётная сила резания PP = (PХ; PC×09) m
Наибольшая ширина срезаемого слоя Bp = (bШ + 2×f +05)×nZ = (11 +2×03 + +05)×10 = 121 мм;
Подача допустимая по расчётному усилию SZP = (Pp BP×CP×zMAX)1X =
= (241260 121×3110×5)54 = 0078 ммзуб;
Наибольшая ширина срезаемого слоя при нарезании BШР = bШ ×nZ = 11× 10 = = 110 мм;
Подача допустимая по расчётному усилию резания SZP = (Pp BРШ×CP×zMAX)54 = (241260 110×3110×5)54 = 0086 ммзуб;
Наибольшая ширина срезаемого слоя круглых зубьев BPK = p×dВ – (bШ + 2×f)х
Подача допустимая по усилию резания для круглых зубьев SZP =
= (Pp BРК×CP×zMAX)54 = (241260 778×3110×5)125 = 013 ммзуб;
Так как SZK SZP то окончательно принимаем для шлицевых и круглых зубьев одинарную схему резания.
Припуск D снимаемый фасочными зубьями D = dВ min + 2×f + 03 – D01 =
= 60 + 2×03 + 03 – 588 = 21 мм;
Число фасочных зубьев zФ = (D 2×SZP )+ 1 = (21 2×0078) +1 = 15;
Длина режущей части фасочных зубьев
Диаметры фасочных зубьев:
Число шлицевых зубьев zРШ = 10 2×0078 +1 = 65;
Диаметры шлицевых зубьев DШ1=dВ + 2×f = 60 + 2×03 = 60 6 мм
Длина режущей шлицевой части
Шаг калибрующих зубьев tK » 07×tР = 657 мм;
Число калибрующих зубьев zК =5;
Длина калибрующей шлицевой части
Число круглых зубьев zКР = 5;
Длина круглой режущей части
Число круглых калибрующих зубьев zКК = 7;
Длина калибрующей круглой части
Длина заднего направления
Общая длина протяжки LПР = l = 325 + 12207 +61035 + 3285 +45 =
= 113527 мм что удовлетворяет условию LПР 2000 мм;
Необходимая длина рабочего хода для работы lРХ = lР + lР + L =
= 12207 + 61035 + 3285 + 45 = 81027 мм;
Форма заднего направления протяжки – круглая с центрированием по внутреннему диаметру;
Форма переднего направления протяжки – шлицевая с центрированием по боковым сторонам и внутреннему диаметру;
Определение угла b1 = 450 – arcsin(bШ dВ) = 450 – arcsin(11 60) =
= 450 - 10564 = 344360;
Шаг режущих зубьев для групповой схемы резания tP = 15×L12 = 15×4512 =
Глубина стружечной канавки hK = 4 мм;
Наибольшее число одновременно работающих зубьев zMAX = 1 + L tР = 1 + 451006 = 547 » 5;
= 1256 (3×45) = 009 ммзуб;
Допустимое усилие по прочности первого зуба P1 = p×(d – 2hК)2 s 4 = p×(60 - 2×4)2 ×450 4 = 955118 Н;
Допустимая подача усилию резания SZP = (Pp × nZ BO×CP×zMAX×KP)54
Расчётная подача для групповой схемы резания SZP = 0153 ммзуб;
рис14.1.dwg

01_Описание объекта производства.doc
В данной дипломной работе произведена разработка технологического процесса на деталь шестерня Iой передачи вторичного вала коробки передач 130-1701112 автомобиля ЗИЛ-130.
Шестерня представляет собой одновенцовое цилиндрическое прямозубое зубчатое колесо с внешним зацеплением число зубьев z = 45 модуль m = 425 мм. Отличительной особенностью шестерни является наличие центрального шлицевого отверстия с числом зубьев равным 10. Материал шестерни сталь 25ХГМ ГОСТ 4543-71 требуемая твёрдость поверхности зубьев HRCЭ 57 60 сердцевины HRCЭ 35-45.
Шестерня в процессе работы может перемещаться по шлицевому валу с помощью вилки и находиться в зацеплении либо свободно вращаться вместе с валом.
0_Оглавление.doc
Назначение сборочной единицы и обрабатываемой детали.
Анализ технологичности конструкции детали
Выбор типа и организационной формы производства.
Выбор способа получения заготовки.
Анализ базового варианта технологического процесса.
Проектирование технологического процесса механической обработки.
Проектирование станочного приспособления.
Проектирование режущего инструмента.
Проектирование средств автоматизации.
Выбор транспортных средств.
Технико - организационная часть.
Энергетическая часть.
Охрана окружающей среды.
Автоматизация проектирования и расчетов.
Экономическая часть проекта.
Стандартизация в проекте.
04_Выбор формы организации.doc
Тип производства по ГОСТ 3.1108–74 характеризуется коэффициентом закрепления операций: 1КЗО10 – массовое и крупносерийное 10КЗО20 – среднесерийное 20КЗО40 – мелкосерийное производство. В единичном производстве КЗО не регламентируется.
Значение КЗО принимается для планового периода равного одному месяцу и определяется по формуле:
Рi - явочное число рабочих участка выполняющих различные операции при работе в одну смену.
Условное число однотипных операций выполняемых на одном станке в течении одного месяца при работе в две смены:
где н - планируемый нормативный коэффициент загрузки станка (075);
з - коэффициент загрузки станка проектируемой (заданной) операцией:
где Тшт. - штучно-калькуляционное время необходимое для выполнения проектируемой операции мин;
Nм - месячная программа выпуска заданной детали шт.:
Nм = Nг 12 = 150000 24 = 6250 шт.
где Nг - годовой объем выпуска заданной детали шт.:
Fм - месячный фонд времени работы оборудования в две смены ч:
Fм = 4055 24 = 169 ч.
Поi = 60 FмkВ н (Тшт.Nм).
Необходимое число рабочих для обслуживания одного станка (при работе в две смены):
Рi = ПоiТшт.Nм (60FмрkВ)
где Fмр – месячный фонд времени работы рабочего Fмр = 176 ч.
Результаты расчётов по приведенным выше зависимостям представлены в таблице 4.1.
Тогда коэффициент закрепления операции равен:
Кзо = 2921 1152 = 253.
Производство крупносерийное.
Решение о целесообразности организации поточной формы производства обычно принимается на основании сравнений заданного суточного выпуска изделий и расчетной суточной производительности поточной линии при двухсменном режиме работы и ее загрузке 65-75%.
Заданный суточный выпуск изделий:
где 257 - количество рабочих дней в году.
Nc = 150000 257 = 584 шт.
Суточная производительность поточной линии:
где Fc - суточный фонд времени работы оборудования (при двухсменном режиме работы-960мин.);
Тср - средняя станкоёмкость основных операций мин.
Средняя станкоёмкость операций:
kВ - средний коэффициент выполнения норм времени;
n-количество основных операций.
Тср = 28665 (16 × 13) = 138.
Qc = 960 × 08 138 = 557 шт.
Так как заданный суточный выпуск изделий больше суточной производительности поточной линии Nc >Qc при условии ее загрузки на 65-75% то применение одно-номенклатурной поточной линии целесообразно.
Такт производства определяем по формуле:
= 60 Fэ Nг = 60 × 4055 150000 = 162 мин.
15_Охрана окружающей среды.doc
В процессе обработки металлов резанием основными загрязнениями являются: стружка масляный туман смазочно-охлаждающая жидкость и её аэрозоли в воздухе рабочей зоны различные виды пыли которые при помощи системы вентиляции попадают из заводских помещений в окружающую среду.
Для приготовления СОЖ промывки изделий в больших объёмах используется вода которая в результате использования для технологических целей в значительной степени загрязняется металлической пылью абразивными и другими мелкодисперсными механическими примесями кроме того в ней как правило содержаться различные масла сода растворители. С целью предотвращения попадания вредных веществ в окружающую среду применяют различные методы очистки самыми распространёнными из которых являются: процеживание фильтрование флотация отстаивание в специальных отстойниках используются циклоны и другие инерционные устройства.
Процеживание используется для выделения из сточных вод крупных нерастворимых примесей а так же более мелких волокнистых загрязнений. Отстаивание связано с процессом осаждения твёрдых частиц или выделения более лёгких маслянистых фракций однако этом метод очистки требуем больших временных затрат. Для удаления стружки и других металлических примесей из воды используют с достаточно высокой эффективностью магнитную сепарацию.
Для уменьшения вредных воздействий на окружающую среду обуславливаемых работой металлорежущего оборудования применяется обильное охлаждение режущих инструментов при помощи эмульсии что приводит к снижению пыле- и газовыделений при обработке особенно на шлифовальных станках. При этом снижается также тепловыделение. Рекомендуется применение на станках различных отсасывающих пыль и стружку устройств что также позволит сократить пылевыделение и кроме этого экономить материалы.
Воздух же отводимый из рабочей зоны как правило имеет многоступенчатую очистку. Грубая очистка осуществляется посредством использования пылеуловительных камер различных конструкции для более тонкой очистки эффективно использование скрубберов наивысшая степень очистки достигается за счёт фильтрования. Очистка воздуха от различных аэрозолей эффективна в случае применения ультразвука (процессы коагуляции).
Твёрдые отходы машиностроительного предприятия имеют ограниченную номенклатуру и относительно постоянны по составу. Ниже приведены усреднённые данные о количестве твёрдых отходов производимых средним машиностроительным производством:
Горелая формовочная смесь
На производстве могут также присутствовать всевозможные токсичные отходы (отходы гальванических цехов травильных участков и др.) которые в обязательном порядке должны нейтрализовываться и обезвреживаться.
Основными источниками промышленного шума и вибраций являются работающие компрессоры вентиляторные установки металлорежущие станки вращающиеся длинные прутки краны и загрузочные агрегаты разливные ковочные штамповочные машины а также различные виды транспорта в особенности железнодорожный.
!11_Выбор транспортных средств.doc
Одним из основных резервов повышения производительности труда является совершенствование и дальнейшее снижение трудоёмкости процесса перемещения деталей. Транспорт непрерывно связан с производством он является частью производственного процесса непосредственно влияет на длительность его цикла и способствует точному выполнению каждым рабочим установленных норм времени. Во многих случаях он приобретает роль фактора организующего производство.
При выборе транспортных средств исходят из величины грузопотока. Рассчитывается масса на годовую программу следующих грузопотоков: межцехового – из заготовительного в данный механический цех; межоперационный – от станка к станку при механической обработке; массы стружки образующейся в процессе обработки заготовки.
Межцеховой грузопоток в нашем случае рассчитывают по следующей формуле:
Q = Gi Ni = 5×150000 = 750000 кг
Ni – годовая программа.
Межоперационный грузопоток q:
q = qi Ni = 3045×150000 = 456750 кг
где qi – чистовая масса детали кг.
Масса грузопотока стружки Qс образующейся в отделении за один час при обработке нескольких деталей:
Qс = (Gi – qi)Ni Fд = (5 – 3045)150000 4030 = 7276 кгчас.
На основании рекомендаций изложенных в [11] выбираем межцеховой межоперационный транспорт и определяем способ уборки стружки.
Руководствуясь величиной межцехового грузопотока в нашем случае при расстоянии между механообрабатывающим и заготовительным цехами около 300 метров наиболее целесообразно применение электрокар грузоподъёмностью 2 тонны обеспечивающие производительность до 42 тонны в час при этом стоимость одного машино-часа составляет около 256000 тыс.руб. а стоимость транспортировки одной тонны 61000 руб.
В качестве межоперационного транспорта наиболее целесообразно может быть применение подвесного цепного конвейера с ручным съёмом и установкой заготовок.
Для уборки стружки образующейся в процессе обработки в нашим случае можно использовать шнековый конвейер с выходом на сборный магистральный конвейер который обеспечивает доставку стружки в отделение переработки и брикетирования. Принятый вид конвейера обеспечивает производительность до одной тонны в час может обеспечивать скорость движения до 2ммин при 20 обмин диаметр шнека 200 мм мощность приводного двигателя 4кВт масса одного погонного метра составляет 144 кг.
05_Выбор метода получения заготовки.doc
Согласно базовому варианту заготовку получают на кривошипном горячештамповочном прессе в открытых облойных штампах из прутка стали 25ХГМ диаметром 80 мм. Технологию получения заготовки можно представить в следующей последовательности:
Резка сортового проката осуществляется на ножницах. Пруток предварительно нагревают ТВЧ после отрезки получают цилиндр длиной 180 мм массой 7070 кг.
Загрузка разрезанного проката в накопитель перед нагревателем КИН-51.
Нагрев заготовки в нагревателе ТВЧ до температуры 1100 1200 С0.
Транспортировка цепным транспортёром прутка к рабочей зоне пресса.
Штамповка на КГШП с усилием 25000 Н температура штамповки 1200-900С0.
Транспортировка заготовки к ОГШП для обрезки облоя и прошивания отверстия температура заготовки должна быть не менее 800-900С0 в противном случае требуется подогрев.
Масса заготовки после обрезки облоя составляет 61 кг. С учётом допускаемых отклонений на длину и диаметр проката масса обрезаемого облоя может колебаться в пределах 04 – 07 кг около 03 кг составляет вес перемычки.
Штамповка в открытых штампах характеризуется тем что штампы в процессе деформации остаются открытыми. Зазор между подвижной и неподвижной частями является переменным в него выдавливается металл при деформировании образуя заусенец что существенно увеличивает расход металла кроме того для обрезки заусенца (облоя) необходимо применять специальные обрезные пресса и штампы. Исследования показали что при обработке штампованных заготовок большая часть отходов 70-80% приходится на припуск и заусенец.
Одним из путей совершенствования метода получения заготовки является безоблойная штамповка т.е. штамповка в закрытых штампах. Однако основной трудностью при его применении является повышенные требования к точности отрезаемого прутка по массе (объёму). Эта задача может быть решена в случае применения специальных отрезных станков в частности станков фирмы «Кизерлинг» (ФРГ) моделей НТ-62 НТ-125 и т.д. Особенностью этих машин является то что во время резки два охватывающих режущих инструмента приводятся в движение от двух маховиков с кулачками. В результате двустороннего отрезного удара металл срезается ровно. Производительность 150-300 детмин допуск на длину заготовки ± 015 мм. поверхность среза получается чистой без заусенцев. В этом случае колебание объёма отрезаемого прутка будет в значительно меньших пределах и эта погрешность может быть скомпенсирована за счёт изменения толщины перемычки. При этом для прошивки отверстия в заготовке можно будет применять менее мощные и как следствие более дешёвые пресса. Кроме того способ получения заготовки в закрытых штампах позволяет повысить точность штамповки а это значит снизить припуски на механическую обработку и как следствие снизить трудоёмкость изготовления изделия.
Выбор метода получения заготовки должен так же выбираться в зависимости от типа производства. Тип производства для проектируемого технологического процесса механической обработки детали 130-1701112 – крупносерийное методика выбора типа производства отражена ниже в разделе 4.
В настоящее время заготовка получается штамповкой в открытых штампах я предлагаю получать заготовку в закрытых штампах. Для определения целесообразности изменения способа получения заготовки воспользуемся методикой изложенной в [3].
Себестоимость заготовки с достаточной степенью точности можно определить по приведенной ниже зависимости:
Q – масса заготовки кг.;
kт kc kв kм kп - коэффициенты зависящие от класса точности группы сложности массы марки материала и объема производства заготовок.
q – масса готовой детали кг.;
Sотх – цена 1 т отходов руб.;
kт = 1; kc = 077; kв = 088; kм = 121; kп = 08;
Стоимость заготовки для заводского техпроцесса (в открытых штампах):
Стоимость заготовки в закрытых штампах:
Как видно из приведенных расчётов расчётная себестоимость заготовки получаемой в закрытых штампах ниже экономия на материале при годовой программе выпуска шестерни 150000 составит:
Э = (SЗАГ 1 – SЗАГ 2)N = (255751 – 215816)х150000 = 59902500 руб.
Кроме того отпадает необходимость в оборудовании для обрезки облоя что тоже немало важно. Так же в закрытых штампах точность поковки выше чем в открытых вследствие чего уменьшаются припуски под механообработку в результате уменьшается износ инструмента.
Значит применение предложенного метода экономически целесообразно.
06_Анализ техпроцесса....doc
1 Анализ применяемого технологического оборудования
Согласно методике изложенной в [2] анализ применяемого технологического оборудования для производства шестерни передач 130-1701112 будет проводится на основании представленных ниже таблиц.
Таблица 6.1.1 Технологические возможности применяемого оборудования
Предельные или наибольшие размеры обрабатываемой заготовки мм
Технологические возможности метода обработки мкм
Диаметр (ширина) d(b)
Шероховатость обрабатываемой поверхности мкм
Как видно из приведенной таблицы применяемое оборудование для изготовления рассматриваемой детали обеспечивает приемлемую точность и качество обработки. Размеры рабочей зоны станков соответствуют габаритам обрабатываемой детали.
Для дальнейшей оценки оборудования проанализируем данные следующей таблицы.
Таблица 6.1.2 Характеристика возраста стоимости сложности производительности и степени использования применяемого оборудования
Год изготовления станка
Категория ремонтной сложности
Количество станков на операции
Коэффициент загрузки станка
Проанализировав данные табл.6.1.2 видно что практически всё оборудование имеет срок службы более десяти лет (средний возраст станков 28 лет) поэтому весь станочный парк нуждается в замене. Станки могут заменяться на аналогичные новые или же более совершенными их модификациями либо новыми моделями что более предпочтительно. Станки имеют относительно невысокую стоимость и величину категорий ремонтной сложности за исключением некоторых моделей что делает оправданным их выбор. Кроме того на некоторых операциях механической обработки коэффициенты загрузки имеют довольно низкие значения поэтому по возможности необходимо догрузить это оборудование подобными деталями с других участков или цехов.
Для оценки требований точности обработки и схем базирования заготовок руководствуемся представленным на рис.6.1 эскизом детали номерами обозначим поверхности на которые устанавливается деталь в процессе обработки.
Таблица 6.1.3 Базирование заготовок при обработке
№ и название операции
Выдерживаемые размеры мм
Номера поверхностей – баз
Погрешность базирования
Двойная направляющая
5 Вертикально-сверлильная
0 Токарно-револьверная
5 Горизонтально протяжная
0 Токарно-многорезцовая
5 Токарно-многорезцовая
0 Вертикально-протяжная
5 Токарно-винторезная
5 Зубошевинговальная
0 Внутришлифовальная
0 Зубохонинговальная
Рис.6.1 Поверхности для базирования
На основании данных приведенной выше табл. 6.1.3 можно говорить о сравнительно невысоких требованиях к точности обработки зубчатого колеса что не налагает дополнительных требований у применяемому оборудованию и его обслуживанию. Необходимо отметить что применяемые схемы обработки на рассматриваемых операциях достаточно прогрессивны.
Улучшить технологический процесс обработки можно за счёт применения инструмента с большей стойкостью заменой устаревшего оборудования на более новое (менее энергоёмкое). Кроме того в условиях крупносерийного производства более приемлемым будет использование автоматов и полуавтоматов.
Станок вертикально-сверлильный 2135 заменим на 2Н135 так как 2135 устаревший. Горизонтально-протяжной 7А520 заменим на вертикально-протяжной 7Б65 так как имеется возможность автоматизации станок занимает меньше места. Зубозакругляющий станок ЕЗ-77 заменим на 5Н580 так как ЕЗ-77 устаревший. Вертикально-протяжной Э108 заменим на более новый 7Б65. 1К62 заменим на 16К20 как морально устаревший. 5702 заменим на 5702В. Si-4А заменяем на 3К227А так как этот станок выпускается машиностроительных заводах СНГ. Зубохонинговальный GH-12 заменим на 5А913 как на более новый.
2. Анализ применяемых режущих и вспомогательных инструментов
Для наиболее полной оценки применяемого режущего и вспомогательного инструментов составим таблицы 6.2.1 и 6.2.2.
Как видно из данной таблицы основным инструментальным материалом для изготовления режущего инструмента является сталь Р6М5 более целесообразным было бы применение стали марки Р5К10 позволяющей работать с более высокими режимами резания а величина модуля обрабатываемой шестерни допускает возможность применения твёрдосплавных червячных фрез. Кроме того применяемый в качестве смазочно-охлаждающей жидкости сульфофрезол желательно заменить на менее опасные для рабочего и более современные марки СОЖ например Castrol.
В рассматриваемом технологическом процессе применяется специальный вспомогательный инструмент. Время на смену одного инструмента сравнительно не велико и соответствует современным требованиям. Способ крепления позволяет обеспечить постоянство положения занимаемого режущим инструментом в процессе резания.
Рассмотрим один из применяемых инструментов – протяжку шлицевую II го прохода. Протяжка – сложный многолезвийный инструмент. Позволяет за один проход получить нужный профиль. Рассматриваемая протяжка имеет два хвостовика передний и задний количество зубьев 44 и служит для окончательной обработки. Первые 33 зуба снимают припуск остальные круглые выглаживающие. Так как протяжка для окончательной обработки то снимаемый ей припуск не велик Материал режущей части и заднего хвостовика Р6М5 ГОСТ 19265-71 материал переднего хвостовика сталь 40Х ГОСТ 4543-71. Так как протяжка для окончательной обработки то снимаемый ей припуск не велик Твёрдость режущей части и задней направляющей 63..66HRCЭ передней направляющей 61..66HRCЭ хвостовиков 43..51HRCЭ. Чертёж инструмента представлен в приложении.
Таблица 6.2.1 Режущий инструмент
Наименование инструмента
Вид инструмента (станд. спец.)
Материал режущей части
Стойкость (фактическая) мин.
Метод настройки на размер
Обеспечивается инстр.
Шевер абразивный карандаш мастер-шевер
Таблица 6.2.2 Вспомогательные инструменты
Установка режущего инструмента во вспомогательный
Время на смену (правку) одного инструмента мин
Стойка для крепления зенкера
По плоскости винтами
Втулка к зенкеру МН1006-60
Стойка для резца 6720-5016
Державка для резцов 6500-5014
Патрон для протяжки МН 104-60
Стойка для резца 68-1103
Стойка для резцов 6729-5015
Оправка для фрезы 6224-5012
По цилиндрическому валу и шпонке
Цанга для фрезы 6112-5005
Улавливатель 7074-5005
3. Анализ применяемых установочно-зажимных
Для оценки применяемых установочно-зажимных приспособлений составим таблицу 6.3.1.
Таблица 6.3.1 Установочно-зажимные приспособления
Название приспособления
Привод приспособления и уд. давл. (для пневмо – и гидроприв.)
Количество приспособлений на станке шт.
Время на установку и снятие заготовки мин.
Приспособление 13-150
Планшайба опорная 76-132
Планшайба поводковая
Приспособление 7560-5063
Как видно из приведенной выше таблицы основная масса приспособлений являются специализированными что неизбежно приводит к некоторому увеличению сроков подготовки технологической оснастки однако их конструкция позволяет многократное применение с использованием различных наладок. Кроме того наличие гидравлического или пневматического привода значительно уменьшает утомляемость рабочего и позволяет уменьшить время на установку и снятие обрабатываемой детали.
Рассмотрим зубофрезерное приспособление гидравлического действия. Приспособление предназначено для механизации закрепления обрабатываемой детали в рабочей зоне станка. Приспособление питается от гидросистемы станка. Заготовка садится на шлицевый вал который оснащен устройством доворота срабатывающим в случае попадания на зуб колеса. Заготовка во время обработки удерживается зажимной цангой. Корпус приспособления закреплён на столе станка неподвижно заготовка имеет возможность вращаться в процессе обработки. В конце цикла обработки срабатывает разжимная цанга шлицевый вал выходит из зацепления с заготовкой и заготовка выталкивается из приспособления. Чертёж приспособления приведён в приложении.
4. Методы и средства межоперационного контроля
Характеристика средств технического контроля представлена в табл.6.4.1.
Таблица 6.4.1 Средства технического контроля
Наименование инструмента (прибора)
Вид инструмента (универс. спец.)
Точность измерения мкм
Допуск на измеряемый размер мм
Время на измерение мин
Штангенциркуль ШЦ-1-125-01
Штангенциркуль ШЦ-2-125-005
Калибр на расположение
Штатив Ш-IIН ГОСТ10197-70
Индикатор ИЧ 10 кл1 ГОСТ577-68
Контрольный стол: скоба шаблон скоба регулировочная штангенциркуль калибр калибр комплексный штатив оправка контрольная
Скоба шаговая 57689-0064
Контр. Прибор МЦ-400Б
Измерительное колесо
Шаблон радиусный R 6±10
Контрольный стол: визуальный осмотр шаблон радиусный R 6±10 шаблон 150х3хR6 Контр. Прибор МЦ-400Б Измерительное колесо оправка контрольная индикатор ИЧ10 кл.1
Прибор активного контроля
Индикаторный нутромер
Пробка 60+003 «ПР» «НЕ»
Оправка контрольная набор колец
Применяется специальный мерительный инструмент что соответствует данному типу производства (массовое) точность измерений позволяет обеспечивать надлежащее качество выпускаемой продукции. Кроме того на отдельных операциях используется выборочный контроль параметров зубчатого колеса производимый на специальных приспособлениях установленных в цехе.
рис14.6.dwg

10_Проектирование средств автоматизации.doc
Автоматизация является одним из наиболее эффективных средств повышения производительности качества высвобождения рабочих занятых ручным трудом и т.д.
Опыт работы станков-автоматов и автоматических линий показывает что автоматизация загрузки и выгрузки станков приводит к повышению производительности на 20-30%. Это объясняется прежде всего уменьшением вспомогательного времени при автоматической загрузке и выгрузке исключением задержки между отдельными операциями и возможностью работать во время перерывов и т.д.
Механизация и автоматизация технологических процессов механической обработки зубчатых колёс предусматривает ликвидацию или максимальное сокращение ручного труда связанного с транспортированием загрузкой выгрузкой и обработкой на всех этапах производства включая контрольные операции.
В качестве средства механизации транспортирования заготовок на участке производства детали шестерня ведомая 130-1701112 рассмотрим конструкцию и принцип работы автооператора.
Автооператор применяется для автоматической смены заготовки в конце цикла обработки.
Рука автооператора 1 принимает заготовки из накопителя 2 и подаёт в рабочую зону станка. Далее деталь закрепляется в приспособлении станка. Причём автооператор не отводиться а разжимается кожух 4 что даёт возможность придать детали вращательное движение. Начинается обработка.
После окончания обработки кожух 4 зажимается автооператор перемещает деталь в накопитель 3. Далее берётся деталь из накопителя 2 и процесс повторяется.
!08_ Проектирование приспособления.doc
Согласно индивидуальному заданию проведём анализ и расчёт приспособления зубофрезерного под номером 7533–5235.
Данное приспособление служит для установки и автоматического закрепления заготовки на зубофрезерном станке. Приспособление состоит из корпуса (9) – основной детали приспособления на которую крепятся все остальные детали узлы и крепежные элементы а так же относительно основания корпуса рассчитываются основные размеры и допуски до базовых поверхностей заготовок. Сам корпус базируется относительно основания на столе станка и закрепляется с помощью винтов М16 установленных в отверстия стола. В целях экономии материала и повышения жесткости приспособления (ребра жесткости и т. п.) корпус выполняется сборным.
Сверху на корпус закрепляются сухарь и кулачек патрона. Между сухарем и толкателем пневмоцилиндра установлен рычаг который служит для передачи силы зажима на сухарь и следовательно на кулачек.
Заготовка устанавливается в кулачки. После чего подается рабочий воздух в бесштоковую полость пневмоцилиндра шток перемещаясь вертикально воздействует на сухарь (10) который в свою очередь сдвигает кулачек. Кулачки сдвигаются и удерживают заготовку в процессе обработки.
После обработки для снятия заготовки с приспособления рабочий воздух подается в шоковую полость пневмоцилиндра шток перемещается в исходное положение. Автоматическое закрепление заготовок позволяет сэкономить время на смену заготовок.
Для определения требуемых параметров гидроцилиндра предварительно определим величину силы действующей на детали в процессе обработки пользуясь методикой изложенной в [1].
Силу резания определим по зависимости вида:
где Ср – учитывает условия обработки;
t – глубина резания мм;
В – ширина фрезерования мм;
n – частота вращения обмин;
хyn – показатели степени;
Kр– поправочный коэффициент на качество обрабатываемого материала.
Подставив значения получим:
Рz = 10 × 300 × 18 1 × 026 075 × 795-015 × 093 = 949 Н.
1Силовой расчет приспособления
Расчёт приспособления произведём согласно методике изложенной в [1].
Обрабатываемая деталь находится в равновесии вследствие действия сил как возникающих в процессе обработки так и зажима и реакций опор. Основными силами процесса обработки являются силы резания. При расчете сил зажима редко учитываются силы веса центробежные и инерционные возникающие при определенных условиях обработки.
Величина сил зажима рассчитывается исходя из условия равновесия всех перечисленных сил при полном сохранении контакта базовых поверхностей обрабатываемой детали с установочными элементами приспособления и при исключении возможности сдвига в процессе обработки. При расчетах следует определять требуемую силу зажима с учетом коэффициента запаса k предусматривающего возможное увеличение силы резания из-за затупления режущего инструмента неоднородности обрабатываемого металла неравномерности припуска непостоянства установки ненадлежащего закрепления заготовки и т. д.
Зажимные устройства должны быть такими чтобы:
при зажиме не нарушалось заданное положение детали;
приложение силы зажима было как можно ближе к месту обработки;
точка приложения силы зажима находилась в зоне образованной условными линиями соединяющими опорные точки детали в приспособлении;
зажимы не вызывали деформации деталей и порчи их поверхностей;
закрепление и открепление детали производилось с минимальной затратой сил и времени рабочего силы резания по возможности не воздействовали на зажимные устройства;
при закреплении недостаточно жестких деталей силы зажима располагались над опорами или близко к ним.
При расчете сил зажима определяются место их приложения и направления а также величины:
сил резания и моменты их воздействия на обрабатываемую деталь а при необходимости — инерционные и центробежные силы возникающие при обработке;
сил зажима путем умножения найденного их значения на коэффициент запаса.
В общем виде усилие равновесия детали в приспособлении. возникающее под действием сил резания и сил зажима может быть представлено в виде формулы:
где k — коэффициент запаса; f — коэффициент трения в местах контакта детали и приспособления Ррез - усилия резания.
Коэффициент k рассчитывается применительно к конкретным условиям обработки по формуле:
k = k0 × k1 × k2 × k3 × k4 × k5 × k6
где k0 —гарантированный коэффициент запаса для всех случаев;
k1 - коэффициент учитывающий состояние поверхности заготовок для черновой заготовки;
k2 - коэффициент учитывающий увеличение сил резания от прогрессирующего затупления инструмента;
k3 - коэффициент учитывающий увеличение силы резания при прерывистом резании;
k4 - коэффициент учитывающий постоянство силы зажима развиваемой силовым приводом приспособления.
k5 - коэффициент учитывающий эргономику ручных зажимных элементов;
k6 - коэффициент учитываемый только при наличии крутящих моментов стремящихся повернуть обрабатываемую деталь.
После определения силы зажима составляется расчетная схема приспособления и находят размеры силовых элементов.
Составим расчетную схему приспособления:
Рис.8.1. Расчетная схема приспособления
Рис.8.2. Схема направления зажимающей силы
Усилие зажима определим по формуле:
где W0 – требуемое усилие зажима на каждом кулачке в зависимости от диаметра обработки:
k = 306 – коэффициент запаса;
k1 = 105 – коэффициент учитывающий дополнительные силы трения в патроне;
М = 4819 Н×мм- крутящий момент от усилия резания;
Рz =949 Н - окружное усилие резания;
f = 08— коэффициент трения на рабочих поверхностях кулачков;
D1 =506 мм - диаметр обрабатываемой поверхности;
D = 192 мм - диаметр зажимной поверхности;
f1 = 01 - коэффициент трения в направляющих кулачков;
n = 3 – количество кулачков;
Для определения параметров гидроцилиндра уточним что при рабочем ходе масло подаётся в штоковую полость. Рабочий диаметр цилиндра определится по представленной ниже зависимости:
где P – сила на штоке патрона Н;
р – рабочее давления в системе МПа;
– КПД гидроцилиндра.
Расчётный диаметр полости гидроцилиндра равен:
Наиболее близкий стандартный диаметр по ОСТ 2 Г21-1-73 составляет 40 мм поэтому принимаем гидроцилиндр с D = 40 мм а диаметр штока d = 15 мм.
2Точностной расчет приспособления
При расчете приспособлений на точность суммарная погрешность при обработке детали не должна превышать величину допуска Т размера .
Суммарная погрешность зависит от ряда факторов и в общем случае может быть представлена выражением:
где - погрешность установки детали в приспособлении;
- погрешность обработки детали;
- расчетная погрешность приспособления.
Погрешность установки представляет собой отклонение фактического положения закрепленной детали в приспособлении от требуемого теоретического. Погрешность установки включает погрешности: базирования закрепления и положения детали в приспособлении :
Погрешность положения детали в приспособлении состоит из погрешностей: изготовления приспособления по выбранному параметру установки приспособления на станке и положения детали из-за износа элементов приспособления :
При наличии в приспособлении элементов для направления режущего инструмента (кондукторные втулки) следует учитывать погрешность от перекоса инструмента .
В результате для расчета точности приспособления можно использовать упрощенную формулу:
где Т — допуск выполняемого размера; k — соответственно погрешности: базирования закрепления установки приспособления на станке положения детали из-за износа установочных элементов приспособления и от перекоса (смещения) инструмента; (w - экономическая точность обработки - 1 12—коэффициент учитывающий отклонение рассеяния значений составляющих величин от закона нормального распределения; = 08 085 - коэффициент учитывающий уменьшение предельного значения погрешности базирования при работе на настроенных станках; = 06 08 — коэффициент учитывающий долю погрешности обработки в суммарной погрешности вызываемой факторами не зависящими от приспособления.
На основе полученного значения производится расчет размерной цепи приспособления. За замыкающее ее звено принимается погрешность по принятому параметру .
Погрешность базирования представляет собой отклонение фактического положения установленной в приспособлении детали от требуемого теоретического и определяется как предельный допуск рассеяния расстоянии между измерительной и технологической базами в направлении выполняемого размера. Данная погрешность устанавливается геометрическим расчетом или с помощью анализа размерных цепей. Возникает погрешность базирования при не совмещении установочной (технологической) и измерительной баз при совпадении этих баз данная погрешность равна нулю. Для уменьшения погрешности базирования следует совмещать измерительные и установочные базы выбирать рациональные размеры и расположение установочных элементов уменьшать зазоры при посадке детали на установочные элементы.
Погрешность закрепления состоит в изменении положения детали в результате приложения к ней усилия закрепления и определяется как разность между наибольшей и наименьшей проекциями смещения измерительной базы в направлении выполняемого размера. В большинстве случаев при выявлении погрешности закрепления учитываются контактные перемещения в местах сопряжения деталей с опорными поверхностями приспособления деформации корпуса которого и других его элементов не учитывается.
Можно принять что = 0 при постоянной силе закрепления заготовок и одинаковом качестве их базовых поверхностей. Величину уменьшают стабилизируя силу закрепления (например применяя пневматические и гидравлические зажимы вместо ручных) повышая жесткость стыка опоры приспособления улучшая качество базовых поверхностей а также увеличивая жесткость приспособления в направлении передачи силы закрепления.
Погрешность установки приспособления на станке зависит от смещений или перекосов корпуса приспособления на столе планшайбе или шпинделе станка. Смещения и перекосы возникают из-за зазоров между сопрягаемыми поверхностями приспособления и станка. Для уменьшения зазоров рекомендуется повышать точность посадочных мест приспособления разносить на корпусе ориентирующие его элементы и подгонять посадочные места к станку. В массовом производстве при использовании одного приспособления и неизменном его закреплении погрешность установки может быть частично или полностью устранена настройкой станка. При использовании нескольких одинаковых приспособлений (дублеров и спутников) эта величина не компенсируется настройкой станка и полностью входит в состав погрешности установки приспособления на станке.
В серийном производстве при частой переустановке приспособления на влияют износ и повреждение сопрягаемых поверхностей. При соблюдении требований к смене приспособлений и правильном выборе зазоров в спряжениях = 002 01 мм.
В каждом конкретном случае рекомендуется выполнять расчет погрешности установки приспособления на станке в зависимости от ее схемы и заданной точности изготовления посадочных элементов.
Погрешность положения детали из-за износа элементов приспособления . На износ влияют размеры и конструкция установочных элементов материал и масса обрабатываемой детали состояние ее базовых поверхностей. Наиболее интенсивно изнашиваются опоры с точечным и линейным контактами наименее — опорные пластины с большими поверхностями контакта. Приближенно износ установочных элементов может определяться по формуле:
U = Uo × k1× k2× k3× k4
где Uo — средний износ установочных элементов для чугунной заготовки при усилии зажима Ро = 10 кН и базовом числе установок N = 100000 k1 k2 k3 k4 -
соответственно коэффициенты учитывающие влияние материала заготовки оборудования условий обработки и числа установок заготовки отличающиеся от принятых при определении Uo N — число установок заготовки.
Погрешность от перекоса или смещения инструмента определяется точностью направления или настройки инструмента относительно положения обрабатываемой детали.
В процессе обработки поверхностей при настройке положения инструмента по отношению к приспособлению с помощью щупа погрешность от смещения инструмента может быть определена по формуле
где DН – погрешность установки инструмента по щупу зависящая от точности механизма перемещения инструмента ТЩ – допуск на изготовление щупа.
Расчет сводим в таблицу 8.1.
Таблица 8.1. Точностной расчет приспособления
Токарное приспособление
= 0 так как установочная поверхность совпадает с исходной
= 012 по [1 табл. 78] для закрепления в приспособлении с гидравлическим зажимом с установкой на штампованную поверхность
Установки приспособления
= 0 так как обеспечен надежный контакт приспособления со столом станка а обработка производится без переустановки приспособления
Смещения инструмента
= 0 так как отсутствуют направляющие элементы для инструмента
Износа установочных элементов U =
где U = Uo × k1×k2×k3×k4×() = 0030×097×125×094×1×(); по[1 табл. 81] Uo= 0.075 для опорных пластин из стали 40Х; по табл. 82 k1 = 097 при обработке стали; k2 = 125 для обработки на спецстанке; k3 = 094 для точения стали с охлаждением; k4 = 1 до N = 100103 установок
Экономическая точность об работки
w = 0039 для точения по 8-му квалитету
Допустимая погрешность изготовления приспособления
Продолжение таблицы 8.1
т.к. измерительная база совпадает с установочной.
Точность обеспечивается.
0К_075.doc
“Технология машиностроения”
Наименование операции
Сталь 25ХГТ ГОСТ4543-88
Оборудование устройства ЧПУ
Обозначение программы
Установить деталь в приспособление.
Оправка специальная Центр передний 7032-0035 ГОСТ13214-67 Центр задний 7032-0112 ГОСТ13214-67
Хонинговать зубья Z = 40 m = 45 a = 20° .
Шевер абразивный специальный Карандаш 3908-00581 ГОСТ 607-75 Индикатор ИРБ 5584-75 Приспособление для индикатора специальное
Контрольный прибор МЦ 400Б Измерительное колесо специальное Установочный диск для измерительного колеса Установочный диск для
контролируемого колеса Втулка для контролируемого колеса
Снять деталь в ручную после ее полной остановки
Контроль параметров 100%
0К_035.doc
“Технология машиностроения”
Наименование операции
Сталь 25ХГТ ГОСТ4543-88
Оборудование устройства ЧПУ
Обозначение программы
Установить деталь в приспособление и закрепить.
Приспособление специальное
Закруглить торцы зубьев шестерни Z = 40 m = 45 a = 20° со стороны более выступающей ступицы выдерживая размеры 1-7.
Цанга Фреза пальцевая специальная Р5К10 Шаблон специальный на р-р R 55 ± 05 Шаблон специальный на р-р R 24 ± 3
Зачистить заусенцы и очистить от стружки.
Контроль размеров 10%
0К_065.doc
“Технология машиностроения”
Наименование операции
Вертикально-протяжная
Сталь 25ХГТ ГОСТ4543-88
Оборудование устройства ЧПУ
Обозначение программы
Протянуть окончательно шлицевое отверстие выдерживая размеры 1-3 и параметры таблицы.
Планшайба опорная Патрон рабочий Патрон вспомогательный протяжка шлицевая специальная Пробка плоская специальная на р-р 60
Пробка “не” 7068 специальная Пробка плоская “не” на р-р 60 + 016 специальная.
Очистить протяжку от стружки.
Щетка торцовая ГОСТ 10597-65.
Контроль размеров 15%.
МК.doc
Кафедра”Технология машиностроения
Сталь 25ХГТ ГОСТ 4543-88
Код наименование операции
Обозначение документа
Код наименование оборудования
5 4110 Токарно-многорезцовая КТМ 201410001 КТМ 601410001 СТИ по ОТ 65
Токарный 8-и позиционный 1К282 19158 2 1Р 1 7 1
0 4182 Вертикально-протяжная КТМ 201410002 КТМ 601410002 СТИ по ОТ 70
Вертикально-протяжной 7Б68 17485 2 1Р 1 1 1
5 4110 Токарно-многорезцовая КТМ 201410003 КТМ 601410003 СТИ по ОТ 65
Токарно-многорезцовый 1Н713 19158 2 1Р 1 1 1
0 Контрольная СТИ по ОТ 65
Стол контрольный 13063 2 1Р
5 4153 Зубофрезерная КТМ 201410004 КТМ 601410004 СТИ по ОТ 73
Специальный АВС-12-1676 12273 2 1Р 1 1 1
ГОСТ 3.1404-86 Форма 1а
Наименование детали сб. единицы или материала
0 0190 Слесарная СТИ по ОТ 89
Верстак 4 16641 3 1Р 1 1 1
5 4156 Зубозакругляющая КТМ 201410005 КТМ 601410005 СТИ по ОТ 73
Зубозакругляющий 5Н580 12273 2 1Р 1 1 1
5 4158 Зубофасочная КТМ 201410006 КТМ 601410006 СТИ по ОТ 75
Зубофасочный 5525-2 12273 2 1Р 1 1 1
0 4157 Зубошевинговальная КТМ 201410007 КТМ 601410007 СТИ по ОТ 75
Специальный АВС 02В 12277 2 1Р 1 1 1
5 0190 Слесарная СТИ по ОТ 89
0 0208 Термическая СТИ по ОТ 83
5 4182 Вертикально-протяжная КТМ 201410008 КТМ 601410008 СТИ по ОТ 70
0 Зубообкатывающая КТМ 20141009 КТМ 60141009 СТИ по ОТ
Зубообкатной 5В722 1Р 1 1 1
5 4162 Зубохонинговальная КТМ 2014100010 КТМ 601410010 СТИ по ОТ 74
Зубохонинговальный 5В913 12277 2 1Р 1 1 1
5 1000 Контрольная КТМ 201030001 КТМ 601030001 СТИ по ОТ 79
Стол контрольный 2 16572 4 1Р 1 1 1
0_Титульный лист.doc
НА ТЕХНОЛОГИЧЕСКИЙ ПРОЦЕСС МЕХАНИЧЕСКОЙ ОБРАБОТКИ
0К_010.doc
“Технология машиностроения”
Наименование операции
Вертикально-протяжная
Сталь 25ХГТ ГОСТ4543-88
Оборудование устройства ЧПУ
Обозначение программы
Протянуть предварительно шлицевое отверстие выдерживая размеры 1-5 и параметры таблицы.
Планшайба опорная Патрон рабочий Патрон вспомогательный протяжка шлицевая специальная Пробка плоская специальная на р-р 6008 + 005.
Очистить протяжку от стружки.
Щетка торцовая ГОСТ 10597-65.
Контроль размеров 15%.
0К_025.doc
“Технология машиностроения”
Наименование операции
Сталь 25ХГТ ГОСТ4543-88
Оборудование устройства ЧПУ
Обозначение программы
Установить деталь в приспособление и закрепить.
Приспособление специальное
Фрезеровать зубья шестерни Z = 40 m = 45 a = 20° с припуском под шевингование
Оправка для фрезы специальная Фреза червячная сборная специальная Т15К6 Скоба шаговая специальная на р-р 62336 – 01.
Снять деталь вручную при полной остановке станка
Контроль размеров согласно таблице 20%.
ТК.doc
Наименование операции
Наименование марка материала
Наименование оборудования
Контролируемые параметры
Наименование средств в ТО
Проверить отсутствие трещин
Образцы шероховатости ГОСТ 9378-85
забоин заусенцев шероховатость
Шаблон 62 ± 15; 45 °.
Проверить диаметр венца.
Проверить ширину венца.
Технический контроль
ГОСТ 3.1502-85 Форма 2а
Проверить наружный диаметр
Пробка плоская «не» 60 + 016
Проверить наличие товарного
знака и клейма ОТК терм. цеха.
Проверить внутренний диаметр
Проверить ширину шлиц.
Проверить расположение шлиц.
Калибр на расположение
Проверить закругление зубьев.
Шаблон R55 ± 05 Шаблон R24 ± 3
Проверить т. у. (смотри табл.)
Контрольный прибор МЦ 400Б Измерительные колеса
Установочный диск для измерительного колеса
Установочный диск для проверочной шестерни
Втулка для проверочной шестерни Оправка Кольцо
установочное Индикатор ИЧ10 кл.1 ГОСТ 577-85
Центра контрольные ПБ-500 Штатив ГОСТ 10197 –85
Индикатор ИРБ ГОСТ 5584-85 Оправка контрольная
Годные детали клеймить
0К_070.doc
“Технология машиностроения”
Наименование операции
Сталь 25ХГТ ГОСТ4543-88
Оборудование устройства ЧПУ
Обозначение программы
Установить деталь на шестерни обкатные
Шестерни обкатные 3 шт.
Обкатать зубья Z = 40 m = 45 a = 20° .
Снять деталь в ручную после ее полной остановки
0К_045.doc
“Технология машиностроения”
Наименование операции
Сталь 25ХГТ ГОСТ4543-88
Оборудование устройства ЧПУ
Обозначение программы
Установить деталь в приспособление и закрепить.
Приспособление специальное
Снять фаску по контуру зуба Z = 40 m = 45 a = 20° со стороны менее выступающей ступицы выдерживая размер 1.
Оправка для круга специальная 2Круг шлифовальный ПП80325 24А25С2В35мс 2клБ ГОСТ 2424-83 2шт.
рис14.3.dwg

03_ Анализ технологичности.doc
1 Качественная оценка технологичности конструкции
Шестерня 130-1701112 изготовлена из стали 25ХГМ и проходит термическую обработку которая приводит к короблению детали при нагреве и охлаждении. В этом отношении перемычка связывающая тело зубчатого венца и ступицу расположена неудачно так как при термической обработке возникнут односторонние искажения. Зубчатый венец уменьшится в размерах и вызовет сжатие ступицы с левого торца. Таким образом отверстие приобретёт коническую форму что скажется на характере искажения зубчатого венца. Это в свою очередь приводит к обязательной калибровки шлицевого отверстия после термической обработки.
С точки зрения механической обработки зубчатые колёса вообще нетехнологичны так как операции нарезания зубьев со снятием стружки производится в основном малопроизводительными методами. Применение пластического формообразование затруднено из-за недостаточной жёсткости обрабатываемой шестерни.
Положительным следует считать наличие двух фасок в шлицевом отверстии наружный диаметр которых больше наружного диаметра шлицевого отверстия. Это позволяет протягивать шлицевые отверстия после изготовления фасок а торцы обрабатывать на многорезцовом станке. В этом случае резцы для подрезки торцов не будут доходить до шлицевого отверстия что обеспечит хорошие условия резания (не на прерывистой поверхности) и следовательно высокую точность.
В целом применительно для деталей данного класса обрабатываемую шестерню можно считать достаточно технологичной так как обеспечивается свободный доступ режущего и мерительного инструмента хорошие условия отвода стружки и СОЖ отсутствуют скрытые полости и высокоточные поверхности.
2 Количественная оценка технологичности конструкции
При количественной оценки технологичности детали согласно методике изложенной в [2] определяют значения следующих показателей:
Коэффициент унификации конструктивных элементов:
Ку.э. = Qу.э.Qэ = 913 = 069;
где Qу. э и Qэ – соответственно число унифицированных конструктивных элементов детали и общее шт.;
Коэффициент применяемости стандартизованных обрабатываемых поверхностей:
Кп.ст. = Dо.с.Dм.о. = 710 = 07;
где Dо.с. и Dм.о. – соответственно число поверхностей детали обрабатываемых стандартным режущим инструментом и всех подвергаемых механической обработке поверхностей;
Коэффициент обработки поверхностей:
Кп.о. = Dм.о.Qэ = 1013 = 077;
Коэффициент использования материала:
Ки.м. = qQ = 4561 = 073;
где q и Q – соответственно масса детали и заготовки кг;
Коэффициент применения типовых технологических процессов:
Кт.п. = Qт.п. Qи = 3 4 = 075;
где Qт.п. и Qи – соответственно число типовых технологических процессов для изготовления детали и общее;
Масса детали – 45 кг;
Максимальное значение квалитета обработки - 9;
Минимальное значение параметра шероховатости обрабатываемых поверхностей Ra – 063.
Из полученных результатов видно что значения коэффициентов использования материала и обработки поверхностей не высоки что требует в отношении первого пересмотра способа получения заготовки. В пользу технологичности свидетельствуют достаточно высокие значения коэффициентов применяемости стандартизованных обрабатываемых поверхностей коэффициента унификации применения типовых технологических процессов и обработки поверхностей.
14_ОХРАНА ТРУДА.doc
Для технологического процесса механической обработки шестерни 130-1701112 на участке характерны опасные и вредные производственные факторы (ОПФ и ВПФ) которые по природе действия подразделяются на: физические биологические психофизические и химические.
Химические ОПФ и ВПФ характерные для рассматриваемых технологических процессов оказывают на человека преимущественно раздражающее и сенсибилизирующее (воздействуют как аллергены) воздействие.
К психофизическим факторам можно отнести физические перегрузки перенапряжение отдельных органов человека монотонность труда.
К физическим факторам относятся:
движущиеся машины и механизмы подвижные части технологического оборудования;
повышенная или пониженная температура воздуха рабочей зоны;
отсутствие или недостаток естественного освещения;
повышенный уровень шума и вибраций;
повышенный уровень статического электричества;
острые кромки заусенцы шероховатость на поверхности заготовок инструментов и оборудования;
повышенная температура поверхностей оборудования;
повышенное значение напряжений в электрической цепи замыкание которое может произойти через тело человека;
повышенная загазованность воздуха рабочей зоны;
недостаточная освещенность рабочей зоны.
Биологические ОПФ и ВПФ включают в себя бактерии вирусы и продукты их жизнедеятельности. Источником этих факторов является (СОЖ).
В ходе техпроцесса в связи с применением СОЖ возникает масляной туман. Он состоит из капель размером менее 4 мкм (до 90%). Эти капельки характеризуются высокой проникающей способностью в легкие человека. Аэрозоли нефтяных масел входящих в состав СОЖ вызывают раздражение слизистых оболочек верхних дыхательных путей.
Накапливаясь во всем объеме рабочего помещения масляные туманы существенно ухудшают условия труда вызывая профессиональные заболевания.
В результате разбрызгивания и испарения СОЖ при обработке на токарных станках величина концентрации аэрозолей масла в воздухе производственного помещения превышает ПДК в 2 25 раза а в отсасываемом из рабочей зоны станка потоке воздуха концентрация составляет 15 22 мгм2. ПДК аэрозолей масел минеральных нефтяных – 5 мгм2. В соответствии с ГОСТ 12.1007 – 86 по степени воздействия на организм человека масляные туманы относятся к 3-му классу – вещества умеренно опасные.
При обработке материалов резанием в производственных помещениях механических цехов образуется пыль. На торце круглошлифовальном и зубошлифовальных станках выделяется пыль содержащая до 40% абразивного и 60% обрабатываемого материала. В час такой пыли выделяется 30-40 г. Проникая в органы дыхания глаза загрязняя кожный покров пыль способствует возникновению заболеваний дыхательных путей глаз и кожного покрова в зависимости от ее химического состава и степени превышения ПДК запыленности в рабочей зоне. Кроме того пыль загрязняет световые проемы (остекления) а также светильники общего и местного освещения значительно снижая нормативную освещенность рабочих мест. Проникая в механизмы и движущиеся части станков пыль способствует их износу и ухудшению качества продукции.
По ГОСТ 12.1.007-76 пыль относится к 3-му классу опасности (умеренно опасные) и ее ПДК составляет 6мгм3.
На рассматриваемом участке применяются следующие средства коллективной защиты от ОПФ и ВПФ: оградительные и предохранительные устройства; опознавательная окраска и значки безопасности; специальные средства безопасности (системы освещения и вентиляции производственных помещений). Также применяются средства индивидуальной защиты (СИЗ) от ОПФ и ВПФ средства защиты органов дыхания специальная одежда и обувь средства защиты рук головы глаз органов слуха защитные дерматологические средства(защитный крем для рук: «Силиконовый» и «Средство защитное для рук»).
Для обеспечения чистоты воздуха и нормализации параметров микроклимата в производственном помещении помимо местных отсасывающих устройств обеспечивающих удаление вредных веществ из зоны резания (пыли мелкой стружки аэрозолей СОЖ) предусмотрена приточная вентиляция в сочетании с естественной вентиляцией. Общеобменная вентиляция действует постоянно.
Приточная вентиляция обеспечивает подачу в производственные помещения чистого воздуха. Она применяется в производственных помещениях со значительными тепловыделениями и малой концентрацией вредных веществ.
Свежий приточный воздух по воздухопроводам направляют в различные зоны производственного помещения и через распределительные насадки попадают в рабочую зону.
Местная вытяжная вентиляция предназначена для удаления вредных веществ из зоны обработки. Она применяется на шлифовальных станках.
Допустимые микроклиматические условия для проектируемого участка механообработки;
а) для теплого времени года:
– температура 16 27° С;
относительная влажность – не более 70%;
скорость движения воздуха – не более 02 05 мс.
б) для холодного времени года:
– температура 15 21° С;
относительная влажность – не более 75%;
скорость движения воздуха – не более 04 мс.
Оптимальные микроклиматические условия:
а) для теплого времени года:
температура 20 22° С;
скорость движения воздуха – не более 03 мс;
относительная влажность – не более 40 60%.
– температура 17 19° С;
относительная влажность – не более 40 60%;
скорость движения воздуха – не более 02 мс.
Интенсивность теплового облучения на рабочих местах не превышает 100Втм2 и облучению подвергаются не более 25% поверхностей тела человека что соответствует нормам ГОСТ 12.1.005 – 88.
На участке используется как естественное так и искусственное освещение. Искусственное освещение по своему функциональному значению является рабочим используется в темное время суток и при недостаточном естественном освещении. Естественное освещение используется в дневное время суток осуществляется через окна и световые фонари (комбинированное освещение). Разряд зрительных работ III – работа высокой точности (наименьший размер объекта различения 03 05 мм) подразряд зрительных работ – в контраст объекта различения с фоном – средний фон – средний. Нормативное значение освещенности на рабочем месте – 750 лк.
Для совмещенного освещения КЕО = 3% (по СНБ 2.04.05 – 98). По рекомендациям СНБ 2.04.05 – 98 предлагается использовать следующие источники освещения: для общего искусственного освещения – светильники с люминесцентными лампами белого света (ЛБ); для местного освещения – лампы накаливания типа УНП.
Источниками вибрации на производственном участке являются вращающиеся неуравновешенные массы производственного оборудования. Вибрация является технологической так как возникает из – за работы стационарных машин. Для производственного участка характерно возникновение общей вибрации на рабочих местах. Это технологическая вибрация категории – 3а; ее параметры: виброскорость –до 15*10-2 мс логарифмический уровень виброскорости – до 85 дБ что значительно ниже предельно допустимого уровня вибрации по ГОСТ 2.1.012 – 90 (виброскорость до 02*10-2 мс логарифмический уровень виброскорости – до 92 дБ).
Для борьбы с нежелательными вибрациями предусмотрены следующие мероприятия: фундаменты станков выполняются с акустическими разрывами заполненными пористым материалом и акустическим швом расположенными в нижней части фундамента.
Источниками шума на участке являются рабочее оборудование (приводы электродвигателей) и режущий инструмент (лезвийная обработка). По ГОСТ 12.1003 – 83 шум является широкополосным постоянным и уровень звука за восьмичасовой рабочий день не должен изменяться во времени не более чем на 5 дБ и не превышать 80дБА. Снижение шума обеспечивается за счет динамической балансировки роторов электродвигателей применение звукоизоляции. Ожидаемый уровень звука на участке 55 – 65дБА.
По опасности поражения электрическим током проектируемое производственное помещение относится к классу особо опасных так как имеются токопроводящие полы и имеется возможность одновременного прикосновения человека к имеющим контакт с землей металлическим конструкциям здания с одной стороны и металлическим частям с другой.
На участке предусмотрены меры защиты от поражения электрическим током: зануление корпусов оборудования защитное отключение применение пониженного напряжения изоляция токоведущих частей оборудования.
На проектируемом участке существуют следующие опасные зоны: зона резания зона перемещения режущих частей оборудования зона расположения токопроводящих элементов. Все используемое оборудование снабжено средствами защиты работающих: предохранительными оградительными блокирующими сигнализирующими и т.д.
Оборудование на участке располагается группами с соблюдением строительных норм на расположение. Рабочее место организовано таким образом что наклон рабочего вперед не превышает 15° рабочая зона станка располагается на высоте 800 мм при необходимости используется деревянная подставка. Органы управления станком находятся не далее 200 мм от расположения рабочего места во время загрузки станка. Ширина проездов – 45 м ширина проходов – 2 м.
Органы управления станком – кнопочные пульты определенной формы и окраски. Кнопка “Пуск” и кнопки управления утоплены в панель кнопка “Стоп” выступает и имеет красный цвет. Наружные поверхности оборудования окрашены в светло – зеленый цвет внутренние поверхности оградительных устройств – в красный.
По взрывопожарной опасности здание относится к категории Д (помещения в которых находятся негорючие вещества и материалы в холодном состоянии).
Производственные здания построены из искусственных и естественных каменных материалов и имеют незащищенные металлические конструкции. По СНиП 2.01.02 – 85 – степень огнестойкости здания – II (огнестойкость несущих стен не менее 1ч. перегородок – не мене 025ч.).
Возможными причинами пожаров на участке являются: неисправность электрооборудования самовозгорание промасленной ветоши курение в не установленных местах. Мероприятия по пожарной профилактике:
а) организационные – правильная эксплуатация оборудования правильное содержание зданий и сооружений;
б) противопожарный инструктаж работающих;
в) технические – соблюдение противопожарных норм и правил при проектировании зданий и оборудования освещения вентиляции отопления;
г) режимные – запрещение курения в не установленных местах;
д) эксплуатационные – своевременные профилактические осмотры ремонты и испытания технологического оборудования.
Промасленная ветошь собирается в отдельную металлическую тару и организованно вывозится с участка.
В цехе имеется два эвакуационных выхода которые обеспечивают безопасный выход людей наружу кратчайшим путем за минимальное время в случае пожара. Ширина эвакуационных выходов – не менее 1м ширина пожарных проездов – не менее 45 м.
В качестве первичных средств тушения пожаров используются огнетушители ОХП – 10 и ОУ – 5 расположенные по одному на каждые 600 800 м2 ящики с песком лопаты ведра пожарные краны.
2. Способы управления сливной стружкой в процессе резания.
Сливная стружка образуется в основном при точении вязких металлов (сталей) и представляет серьёзную опасность нанесения травм в виде порезов рук и ног токарей и уборщиков стружки.
Проблемы устойчивого изменения формы сливной стружки в процессе точения сталей и организованный её отвод из зоны резания давно изучается станкостроителями и заводами потребителями металлорежущих станков. В этой области известны работы ЭНИМС по дискретному (прерывистому) резанию; МВТУ имени Баумана и другие. Классификацию средств управления сливной стружкой приведена на рис. 14.1.
Организованный отвод сливной стружки без изменения достигается главным образом соответствующей компоновкой узлов станка обеспечивающей сход стружки на заднюю сторону станка. Обычно это станки с наклонным расположением суппорта эскиз на рис. 14.2. и станки с расположением резцедержателя снизу обрабатываемого изделия.
В обоих случаях производится отвод стружки на заднюю сторону станка в специальный стружкосборник. Однако в связи с большой упругостью сливная стружка часто выходит в сторону рабочего места и требуется дополнительное управление ею посредством ручного инструмента представленного на рисунке 14.3.
Несколько улучшает направленность схода сливной стружки в стружкосборник или приёмное отверстие шнекового транспортёра с наклонным суппортом полый резец (мортира Игнатьева) или щелевой стружкоотводчик Максимова представлены на рис. 14.4. и 14.5 соответственно.
Применение вышеперечисленных резцов было целесообразно при условии дополнительного индивидуального дробления стружки на выходе из её направляющих трубок. Поскольку в практике таких решений неизвестно то об этом модно говорить как о задаче.
Приведённые выше примеры являются пока только попыткой решить задачу безопасности и повышения производительности при точении сталей. Практически для управления сливной стружкой без изменения её формы в процессе резания остаются ручные инструменты – “крючки”.
Дробление сливной стружки и её завивание в винтовую спираль могут осуществляться путем придания передней грани резца криволинейной формы а так же устройство на передней грани резца порогов постоянных или регулируемых.
Принцип дробления и завивания стружки состоит в следующем:
Сливная стружка скользящая по передней поверхности резца попадая в канавку как бы повторяет её форму и отклоняемая канавка завивается в кольцо. При упоре завитка стружки в препятствие (деталь резец и т.д.) она дробиться на отдельные элементы.
Принцип дробления и завивания порогами аналогичен дроблению и завиванию канавками. В этом случае стружка движущаяся по пе6редней поверхности резца встречает препятствия и отклоняется им на обрабатываемую деталь заднюю грань резца и т.д. Упираясь в препятствие виток обламывается. Соответствующими параметрами инструмента особенно углами l и g а так же расположением порога по отношению к главной режущей кромке и его размерами достигается устойчивое дробление завивание ленточной стружки в определённом интервале режимов резания.
ВНИИ станкоинструментальной промышленности разработаны сборные резцы оснащенные многогранными неперетачиваемыми пластинами с мелкоразмерными лунками. Для этого применяются пластины с замкнутыми и незамкнутыми лунками.
При дискретном резании на автоматах с кулачковым приводом дробление стружки осуществляется соответствующим профилированием кулачков. Участок подъёма обеспечивает подачу инструмента а при обкатывании роликом горизонтальных участков подача прекращается и стружка срезается. На токарных станках с ходовым винтом периодическое выключение подачи осуществляется посредством муфты с механическим или электрическим выключением. На станках с гидроуправлением – прерывистой подачей масла. Время выключения подачи рекомендуется быть равным 14 – 18 оборота шпинделя.
При осциллирующем точении на постоянную подачу накладывается дополнительное возвратно-поступательное движение инструмента. Стружкодробление осуществляется при числе колебаний f не равному числу оборотов шпинделя n.
универсального устройства обеспечивающего устойчивое дробление стружки пока не разработано (не найдено);
наиболее легко устойчивое дробление и завивание стружки достигается криволинейной формой передней грани резца;
во всех случаях зона резания должна быть защищена прорезининым экраном;
необходима централизованная заточка инструмента.
! 07_Проектирование технологического процесса....doc
1. Выбор наиболее значимых операций и разработка операционного процесса
Из результатов расчётов проведенных по данным базового варианта (см. графики распределения показателей технологичности по операциям техпроцесса в приложении) видно что 70% всех временных затрат на изготовления шестерни приходится в сумме на операции зубофрезерования хонингования шевингования и зубозакругления. На основании этого можно наметить пути совершенствования технологического процесса заключающиеся в возможном для данного модуля зубчатого колеса применении на зубофрезерной операции твёрдосплавных фрез что позволит значительно повысить режимы обработки при неизменном периоде стойкости инструмента применение процесса шевингования с тангенциальной подачей как более производительного также позволит сократить время обработки последнее относится и к хонинговальной операции а также целесообразности замены применяемой быстрорежущей стали Р6М5 на сталь марки Р5К10 позволяющей работать с более высокими режимами резания. Снижение трудоёмкости изготовления шестерни позволит снизить общую себестоимость обработки. Кроме того использование горизонтально-протяжного станка на операциях обработки шлицевого отверстия нельзя назвать оправданным вследствие достаточно большой занимаемой производственной площади. Так как длина обрабатываемой заготовки не велика то эффективной может оказать замена этих станков на вертикально-протяжные.
Целесообразность вносимых изменений будет проверена в п.1618 при определении себестоимости изделия на основании сравнения базового и усовершенствованного вариантов.
Разработанный технологический процесс с учётом предлагаемых изменений представлен ниже в приложении.
2. Расчёт и назначение припусков на механическую обработку
В настоящее время существует два метода определения припусков: опытно-статистический и расчётно-аналитический.
В первом случае величина припуска устанавливается по данным таблиц на всю обработку без распределения припусков по операциям. Для этого используются соответствующие ГОСТы в которых приведены номинальные значения припусков которые в свою очередь являются несколько завышенными. Они не отражают полной реальной ситуации в каждом конкретном случае обработки.
В крупносерийном и массовом производствах применяют как правило расчётно-аналитический метод определения припусков. В качестве примера рассмотрим назначения припусков на охватываемую и охватывающую поверхности по методике изложенной в [3].
Расчёт припуска на наружный диаметр зубчатого венца 189 мм:
Обработка наружного диаметра осуществляется на 005 и 015 операциях операционные эскизы обработки представлены в приложении.
Исходными данными для расчёта припусков по ГОСТ 7505-89 являются:
Масса детали – 3045 кг;
Класс точности – Т3;
Степень сложности – С2;
Исходный индекс – 11.
Кроме этого исходными данными для расчёта являются: величина шероховатости поверхности Rz и глубина дефектного слоя h (табл. 4.25 [3]) суммарное пространственное отклонение для заготовки данного типа определяется по зависимости вида:
где ρкор – величина коробления заготовки;
погрешность установки заготовки при обработке определяется из выражения:
где б – погрешность базирования;
з – погрешность закрепления.
Погрешности заготовки вследствие их копирования при обработке частично сохраняются на обрабатываемой детали пропорционально коэффициенту уменьшения погрешности Ку = 006 – при обдирочной обработке Ку = 005 – при получистовой обработке . Минимальное значение межоперационного припуска определим по формуле:
Минимальный припуск под черновое точение:
Минимальный припуск под получистовое точение:
dp2 = 18854 + 472 = 18901 мм;
dp3 = 18901 + 2004 = 19102 мм;
Рассчитаем общий номинальный припуск и номинальный допуск заготовки:
dз ном = d0 ном + Z0 ном = 189+29 = 1919 мм.
Проверяем правильность выполнения расчетов:
Условия выполняются. Расчеты выполнены верно.
Полученные результаты сведены в табл. 7.2.1.
Расчёт припусков и предельных размеров по технологическим переходам
обработки поверхности 189-046 мм шестерни
Технологические переходы обработки 189
Расчётный размер dр мм
Предельный размер мм
Пред. значение припуска
Аналогично производим расчёт припусков на обработку отверстия 52 мм и результаты расчёта также представим в виде таблицы.
Расчёт припусков и предельных размеров по технологическим переходам обработки отверстия 52 мм шестерни
Технологические переходы обработки 52
Ниже представлены схемы расположения припусков и допусков на рассчитанные выше обрабатываемые поверхности.
На остальные поверхности припуски назначаем по ГОСТ 7505-89 и результаты сведём в таблицу.
Выдерживаемый размер
Как видно из полученных результатов расчётные значения припусков значительно ниже тех значений которые выбирались по ГОСТ это объясняется тем что в случае использования расчётно-аналитического метода учитываются конкретные условия и требования предъявляемые к обрабатываемой поверхности а не используются усреднённые значения.
3. Назначение режимов резания
Режимы резания устанавливаются в зависимости от требуемой точности и качества обрабатываемых поверхностей а также исходя из условий минимально возможной себестоимости и наибольшей производительности.
В настоящее время применяются как правило две методики по расчёту режимов обработки: расчётно-аналитический метод и по нормативным данным. В первом случае используется методика изложенная в [19] во втором пользуются справочником [17].
Рассмотрим подробно методику назначения режимов резания расчётно-аналитическим методом на примере 005 операции рассматриваемого технологического процесса (операционный эскиз смотреть в приложении). Ведётся токарная обработка наружного диаметра (189мм) зубчатого колеса (позиция IV).
Глубина резания t = 1 мм. Согласно методике изложенной в [19] скорость резания определим по зависимости вида:
где КV – поправочный коэффициент представляющий собой произведения ряда коэффициентов а именно:
КМV - учитывает влияние материала заготовки КМV = КГ (750GВ)
КГ – характеризует группу стали по обрабатываемости КГ = 10;
GВ – предел прочности обрабатываемого материала GВ = 620 МПа;
КnV – коэффициент отражающий фактическое состояние поверхности заготовки КnV = 08;
КИV - коэффициент учитывающий качество материала режущего инструмента КИV = 065;
КТИ – учитывает изменение стойкости при многоинструментальной обработке КТИ = 17;
КV = 10 (750620)10 ×08×065×17 = 107.
CV – поправочный коэффициент CV = 420;
Т – величина периода стойкости инструмента в нашем случае принимается равной 240 мин;
S – величина подачи назначается в соответствии с глубиной резания S = 026 ммоб;
mxy–показатели степени назначаются согласно рекомендациям в [19] m = 0.2 x = 0.15 y = 0.2.
Таким образом значение скорости резания определится как:
V = 420×107 (24002 × 1015 × 02602) = 197 ммин.
В качестве примера назначения режимов обработки на основании нормативных данных рассмотрим процесс зенкерования отверстия (47 мм) операция 005 позиция III. Согласно методике изложенной в [17] скорость резания определяется из следующей зависимости:
где Vтабл. – скорость резания определяемая по таблице Vтабл. = 58 ммин;
К1 – коэффициент зависящий от обрабатываемого материала К1 = 10;
К2 - коэффициент зависящий от отношения принятой подачи к подаче указанной в таблице Sтабл = 048 ммоб Sпр = 05 ммоб значит 05 048 = 104 соответственно К2 = 105;
К3 - коэффициент зависящий от стойкости инструмента Т = 240 мин значит К3 = 08.
Вследствие того что зенкерование идёт по корке то Vтабл. Уменьшаем на 20% и получаем что Vтабл. = 48 ммин.
Окончательно получим:
V = 48×11×105×08 = 45 ммин
Что соответствует n = 300 обмин.
Режимы резания для остальных операции механической обработки будем назначать руководствуясь нормативами [17] результаты расчётов сведены в табл. 7.4.1.
Режимы резания (расчётные)
Предлагаемый вариант
Продолжение таблицы 7.3.1
Анализируя результаты таблицы можно утверждать что применения более совершенных инструментальных материалов (см. п.7) позволяет работать с более высокими режимами а это в свою очередь открывает новые пути возможного повышения производительности и снижения себестоимости продукции. Приведенные результаты должны быть откорректированы в соответствии с технологическими возможностями используемого оборудования и окончательные их значения будут представлены ниже в п.7.4.
4. Техническое нормирование
Под технически обоснованной нормой времени понимается время необходимое для выполнения заданного объёма работы (операции) при определённых организационно-технических условиях и наиболее эффективном использовании всех средств производства.
В массовом производстве определяется норма штучного времени:
Тшт = То + Тв + Тоб + Тот
где То – основное время;
Тв – вспомогательное время время на управление станком (включить выключить и т.п.) установку и снятие заготовки подвод и отвод режущего инструмента измерение заготовки;
Тоб – время на обслуживание рабочего места;
Тот – время перерывав на отдых.
где Ттех – время на техническое обслуживание это смазка станка удаление стружки смена режущего инструмента определяемое в % от То или по формуле:
где Тсм – время на смену инструмента (-ов);
Тр – стойкость режущего инструмента;
Торг – время на организационное обслуживание это подготовка станка к работе в начале смены и уборка его в конце смены передача станка сменщику определяется в % от операционного времени а Топ = = То + Тв.
В качестве примера рассмотрим процесс нормирования токарной операции 015 и операции зубошевингования 050 пользуясь нормативными данными из [6]. Для этого составим сводную таблицу по режимам резания.
Сводные данные по режимам резания
Наименование операции
Продолжение таблицы 7.4.1
На токарной операции 025 основное время определим по формуле:
где Lр.х. = Lp + Lп + Lд
Lр – длина резания Lp = 19мм;
Lп – величина подвода Lп = 3 мм;
Lд – дополнительная длина хода Lд = 3 мм
значит: Lр.х. = 19 + 3 +3 = 25 мм.
То = 25 (031×250) = 032 мин;
Lр – длина резания Lp = 22мм;
Lд – дополнительная длина хода Lд = 0 мм
значит: Lр.х. = 22 + 3 = 25 мм.
То = 25 (02×250) = 05 мин;
Так как на поперечном суппорте время обработки больше то в расчетах используем его основное время.
Тв = 009 + 0024 + 001 = 0124 мин; Топ = 05 + 0124= 0624 мин;
Ттех = 05×172 240 = 00036 мин; Торг = 0624×0018 = 0011 мин;
Тоб = 00036 + 00117 = 00153 мин; Тот = 0624×006 = 0037 мин.
Тшт = 05 + 0124 + 00153 + 0037 = 0676 мин.
Нормирование зубошевинговальной операции также проведём на основе зависимостей представленных в [17]. С целью повышения производительности применяем шевингование с тангенциальной подачей поэтому:
аw – номинальное межосевое расстояние аw = 280 мм;
р – припуск на толщину зуба 2р = 011 мм;
b – ширина зубчатого венца b = 19 мм;
Σ – угол скрещивания осей детали и инструмента Σ = 15 0;
nц – количество двойных ходов за цикл обработки nц = 6;
То = 9467×6 115 = 0494 мин.
Тв = 008 мин; Тоб = 00179 мин; Тот = 0034 мин;
Тшт = 0494 + 008 + 00179 + 0034 = 0626 мин.
Аналогично нормируем оставшиеся технологические операции и полученные результаты сводим в табл. 7.4.2.
Сводная таблица технических норм времени по операциям
Как видно из приведенной выше таблицы применение новых инструментальных материалов новых методов обработки на некоторых операциях позволили существенно сократить нормы штучного времени. Это наглядно представляют приведенные в приложении графики распределения показателей технологичности по операциям.
5. Расчёт необходимого количества станков и его загрузки
Необходимое количество оборудования можно определить по общей зависимости вида:
где Fэ – эффективный годовой фонд времени работы единицы оборудования Fэ = 4030 часов.
Если полученное число единиц оборудования для данной операции окажется дробным оно округляется до целого в сторону увеличения.
Коэффициент загрузки станка з определяется как отношение расчётного количества станков mp занятых на данной операции процесса к принятому (фактическому) mпр.
Если на операции обработки принятого количества станков недостаточно для обеспечения их работы с загрузкой не превышающей планируемой (075 08) то необходимо с помощью технологических мероприятий увеличить их производительность или увеличить количество станков на операции. Коэффициенты загрузки станков не должны значительно превышать планируемый нормативный коэффициент загрузки оборудования т.е. на каждом рабочем месте должен быть необходимый резерв свободного времени.
Уровень механизации технологической операции характеризует коэффициент использования оборудования по основному времени. Он определяется как отношение основного времени к штучному. Низкое его значение указывает на большую долю ручного труда:
Коэффициент использования оборудования по мощности представляет собой отношение мощности необходимой для осуществления процесса обработки к фактической мощности установленного на станке привода главного движения:
При этом необходимая мощность для осуществления процесса резания определяется по зависимости вида:
где Ре – эффективная мощность используемая только на резание;
– коэффициент учитывающий потери в приводе станка (08 085).
Последний коэффициент показывает насколько удачно подобрано оборудование. Необходимо стремиться к его более полной загрузке.
Результаты расчётов представленных выше коэффициентов приведены в табл. 7.5.1.
Расчёт коэффициентов использования оборудования
Для наглядности оценки технико-экономической эффективности разработанного технологического процесса построим соответствующие диаграммы.
02_Назначение сборочной.doc
Коробка перемены передач предназначена для изменения передаточных чисел трансмиссии и обеспечения реверса и тем самым получения различных скоростей движения автомобиля ЗИЛ-130 передним и задним ходом.
Рассматриваемая деталь 16 – ведомая шестерня 130-1701112 расположена на шлицах вторичного вала 26 и имеет возможность перемещаться с помощью вилки само колесо в процессе работы входит в зацепление с вал шестерней 32. Эскиз сборочной единице представлен на рис.2.1.
Шестерня ведомая изготавливается из стали 25ХГМ ГОСТ 4543-71 химический состав и механические свойства которой представлены в табл.2.1. Данная деталь является цилиндрическим прямозубым зубчатым колесом и предназначена для передачи вращательного движения между валами с параллельными осями вращения. Зубчатая передача в состав которой входит рассматриваемая деталь является силовой т.е. служит для передачи крутящего момента с изменением частоты вращения валов.
Механические свойства
Gв – предел прочности;
Gт – предел текучести;
– относительное удлинение и относительное сужение соответственно.
Основными причинами вызывающими выход из строя шестерни являются: износ поверхностей зубьев усталостные разрушения связанные с явлением питтинга контактирующих поверхностей.
Рекомендуемые чертежи
- 24.01.2023