Технологический процесс изготовления детали Штуцер


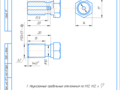
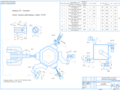
- Добавлен: 24.01.2023
- Размер: 4 MB
- Закачек: 1
Описание
Состав проекта
![]() |
![]() |
![]() ![]() ![]() ![]() |
![]() |
![]() |
![]() ![]() ![]() ![]() |
![]() |
![]() |
![]() ![]() |
![]() ![]() |
![]() ![]() |
![]() ![]() |
![]() ![]() |
![]() ![]() |
![]() ![]() |
![]() ![]() |
![]() |
![]() ![]() ![]() |
![]() ![]() ![]() |
Дополнительная информация
Деталь.cdw

Сталь Ст3 ГОСТ 1050-88
БГТУ им. В.Г. Шухова
Курсовая работа по основам
технологии машиностроения
Схема технологической наладки.cdw

Станок: токарно-револьверный
стандарта инструмента
Резец подрезной 16х10х100
Резец проходной 16х10х100
Резец канавочный 16х10х100
Резец фасочный 16х10х100
Плашка резьбонарезная М12х1
Резец отрезной 16х10х100
Материал детали - Сталь 30 ГОСТ 1050-88
Настройку выполнить по эталону.
Курсовая работа по основам
технологии машиностроения
Схема технологической
БГТУ им. В.Г. Шухова
Записка.docx
Белгородский Государственный Технологический Университет им. В. Г. Шухова
Кафедра Технологии Машиностроения
По дисциплине: основы технологии машиностроения
На тему: «Составление технологического процесса изготовления детали «Штуцер»
Выбор типа производства . ..
Обоснование выбора заготовки
1. Определение допусков припусков и размеров заготовки
1.1. Штамповка на КГШП . ..
1.2. Штамповка на ГКМ ..
2. Расчет массы заготовок ..
3. Расчет технико-экономических показателей заготовок .
Выбор способов обработки поверхностей и назначение технологических баз . .
Укрупненный технологический маршрут изготовления детали «Штуцер» . ..
Технологическая операция 05 – токарная. .
Расчет припусков на механическую обработку . ..
Режимы обработки силы резания
Качество поверхности
Техническое нормирование .
Экономическая оценка технологического процесса
Список литературы . .
Штуцер входит в состав рабочего тормозного гидроцилиндра барабанных тормозов автомобиля. Через данный штуцер жидкость под давлением попадает в рабочий цилиндр после нажатия на педаль тормоза.
Штуцер представляет собой тело вращения цилиндрической формы. Деталь цельная простая.
Габаритные размеры детали: длина l=29 мм диаметр D=17 мм.
На наружной цилиндрической поверхности детали длиной 15 мм от торца имеется резьба М12х15. На расстоянии 15 мм от торца произведена выточка диаметром D=10 мм на длину l=5 мм. С одной стороны детали имеется шестигранная головка под гаечный ключ с размерами 145 х 17 мм. Сопряжения наружной цилиндрической поверхности и поверхности шестигранной головки с торцами выполнены фасками 1х45 о и 15х15 о соответственно.
Деталь имеет центральное глухое отверстие диаметром D=3 мм и глубиной l=20 мм выполняемое по 11 квалитету точности. Перпендикулярно оси детали на расстоянии 175 мм произведено сквозное отверстие диаметром D=2 мм выполняемое с допуском Н11.
Все поверхности детали выполнены с шероховатостью Ra=32 мкм. Неуказанные предельные отклонения: h14 H14 ±IT 142.
Выбор типа производства
Для определения типа производства воспользуемся рекомендациями и таблицами из [6].
Годовая программа выпуска N=30000 деталей.
Устанавливая тип производства по программе выпуска видим что производство будет серийным. Для того чтобы определить серийность производства найдем размер партии:
Примем для дальнейших расчетов n=1200Таким образом устанавливаем что производство будет являться крупносерийным.
Обоснование выбора заготовки
Исходя из конструкции и конфигурации детали и ее размеров как метод производства можно предложить обработку металла давлением также учитывая конструкцию детали следует как вариант рассмотреть изготовление заготовок из шестигранного стального проката.
В пользу выбора варианта с использованием обработки металла давлением говорят технологические свойства металла детали: сталь 30 обладает относительно высокой пластичностью: относительное удлинение составляет 16% ударная вязкость равна 49 кДжсм2 относительное сужение поперечного сечения – 40%.
Предполагаемые точность и качество поверхности заготовки позволяют использовать способы обработки металлов давлением. Серийность производства позволяет предположить использование объемной штамповки.
В нашем случае основными рассматриваемыми методами будут: штамповка на кривошипном горячештамповочном прессе (КГШП) штамповка в горизонтально-ковочной машине (ГКМ) и производство заготовок из шестигранного стального проката. После расчетов как основной будет выбран тот способ который наиболее выгоден с экономической точки зрения.
1 Определение припусков допусков и размеров заготовки
Масса детали = 0026 кг.
Расчетная масса поковки:
По ГОСТ 7505 - 89 принимаем Кр =15
Мп.р=0026*15= 0039 кг
Средняя массовая доля углерода составляет 03% суммарная массовая доля легирующих элементов около 092%. Следовательно группа стали М1.
Степень сложности определяем по формуле где - масса поковки - масса геометрической фигуры в которую вписывается форма поковки.
В данном случае фигурой описывающей форму поковки является цилиндр. Размеры цилиндра определяются путем умножения соответствующих размеров детали на рекомендованный ГОСТ 7505-89 коэффициент 105.
Следовательно степень сложности поковки С1. Конфигурация поверхности разъема штампов плоская.
1.1 Штамповка на КГШП
Класс точности поковки принимаем Т3. Согласно ГОСТ 7505-89 исходный индекс 5.
По специальным таблицам [10] находим необходимые параметры представленные в таблице 1:
Номинальный размер Аid мм
Допускаемые отклонения
Номинальный размер Аiз мм
Штамповочные наружные уклоны принимаем величиной 3°. Радиусы закругления наружных углов равны 05 мм.
1.2 Штамповка на ГКМ
Класс точности поковки принимаем Т4. Согласно ГОСТ 7505-89 исходный индекс 7.
По специальным таблицам [10] находим необходимые параметры представленные в таблице 2
Штамповочные наружные уклоны принимаем величиной 3°. Радиусы закругления наружных углов равны 2 мм. Допускаемая высота торцового заусенца 1 мм.
2 Расчет массы заготовок
Расчет массы заготовки производился в КОМПАС -3D V10.
Масса заготовки получаемой штамповкой на КГШП mз=0039 кг.
Масса заготовки получаемой штамповкой на ГКМ mз=0042 кг.
Масса заготовки из шестигранного стального проката mз=0043 кг.
3 Расчет технико-экономических показателей заготовок
Количественный уровень технологичности способа получения заготовки может быть определен после расчета себестоимости заготовки по сравниваемым вариантам.
- базовая стоимость 1 тонны заготовок руб.;
Sотх - базовая стоимость 1 тонны отходов руб.;
Q - масса заготовки кг;
- коэффициент зависящий от класса точности;
- коэффициент зависящий от группы сложности заготовок;
- коэффициент зависящий от массы заготовок;
- коэффициент зависящий от марки материала
- коэффициент зависящий от объема производства заготовок.
Коэффициент весовой точности:
) Для поковок получаемых на КГШП:
С1=1500 руб; Sотх= 270 руб; q=0026 кг; Q=0039 кг;
Kt=103 Kc=077 Kв=1 Kм=118 Кп=1
) Для поковок получаемых на ГКМ:
С1=1500 руб; Sотх= 270 руб; q=0026 кг; Q=0042 кг;
Kt=102 Kc=077 Kв=1 Kм=118 Кп=1
) Для заготовок из проката:
Из расчетов видим что себестоимость заготовки изготовленной на КГШП ниже а коэффициент весовой точности выше чем у заготовки изготовленной на ГКМ. Но так как изготовление заготовки из проката обойдется дешевле то ее принимаем за основной вариант.
Выбор способов обработки поверхностей и назначение технологических баз
рис.1. Назначение способов обработки штуцера
Номер и наименование обрабатываемой поверхности
Вид механической обработки
Номер базовой поверхности
– наружная цилиндрическая поверхность
С лишением 5 степеней свободы
– резьбовая поверхность
Нарезание резьбы плашкой
С лишением 6 степеней свободы
– отверстие радиальное
Технологическая операция
Задача – спроектировать операцию 05 – подобрать производительный и эффективный вариант токарной обработки наружной цилиндрической поверхности и торца заготовки.
Обработку поверхностей целесообразно выполнить точением. При этом будут легко достигнуты точность размеров соответствующая 12 квалитету и шероховатость поверхностей в пределах Ra=10 63.
С учетом серийности производства деталей операцию можно выполнять на токарно-револьверном станке 1Г340П за один установ с последовательной обработкой каждой поверхности соответствующим резцом (рис.2.).
Операция включает 7 переходов. На позиции I заготовка (шестигранный пруток) устанавливается в патрон. Переход 1 – подрезка торца подрезным резцом осуществляется на позиции II.
Переход 2 – точение наружной цилиндрической поверхности проходным резцом производят на позиции III.
Далее на позиции IV широким резцом производят выточку – 3 переход.
Переход 4 – сверление осевого отверстия – позиция V.
На позиции VI плашкой нарезается резьба М20х15 – 5 переход.
переход производится на VII позиции на которой происходит снятие фасок.
На позиции VIII отрезным резцом производят отрезку заготовки – 7 переход.
рис.2. Базирование и распределение переходов по позициям
Расчет припусков на механическую обработку
Так как деталь не является ответственной и к ней не предъявляются высокие требования по точности то припуски на механическую обработку назначаем по справочным таблицам [3] и приближенным формулам.
Припуск на подрезку торца и отрезку назначаем по справочным таблицам [3]: на подрезку торца – 2 мм на отрезку – 3 мм.
Припуск на точение наружной поверхности будет обусловлен видом заготовки – шестигранного проката. Исходя из этого припуск будет равен разности наибольшего размера проката (диаметр описанной окружности) dокр и требуемого номинального размера dдет:
z=dокр-dдет=17-12=5 мм
Разница между диаметром наружной поверхности полученной на предыдущей операции dдет и требуемым номинальным диаметром выточки dвыт даст величину припуска на обработку последней:
z=dдет-dвыт=17-12=5 мм
При сверлении величина припуска равна половине диаметра сверла dCB. Для осевого отверстия:
Для радиального отверстия:
Результаты расчетов сведем в таблицу 4:
Точение наружной поверхности
Токарная обработка выточки
Сверление осевого отверстия
Сверление радиального отверстия
Режимы обработки силы резания
Установим режимы обработки силы резания и необходимую мощность станка для операции 05. Операция 05 – токарная. Выполняется на токарно-револьверном станке 1Г340П. На шести рабочих позициях подрезают торец обрабатывают наружную поверхность штуцера производят выточку сверлят осевое отверстие снимаются фаски и отрезают заготовку. На каждой позиции выполняют по одному переходу.
рис.3. Схема технологической наладки станка на позиции IV.
Позиция IV переход 3 – точить выточку (рис.3).
Глубина резания будет равна:
t=(Bзаг-Вдет)2=(12-10)2=1 мм.
Подачу примем по [3] S=009 ммоб (соответствует одной из ступеней по паспортным данным станка).
Скорость резания равна:
где Cv – коэффициент скорости резания и xv yv m – показатели степеней принимают по [3]:
- коэффициент учитывающий конкретные условия резания:
Kv=KMv. Knv. Kиv. Kfv. Krv
KMv – коэффициент учитывающий свойства обрабатываемого материала:
Knv – коэффициент учитывающий состояние поверхности заготовки. Knv=09.
Kиv – коэффициент учитывающий влияние материала инструмента. Kиv=10.
Kfv Krv – коэффициенты учитывающие параметры резца. Kfv=1; Krv=1.
С учетом всех значений величина:
Kv=125 . 09.1.1.1=1125.
ТМ – стойкость инструмента в многоинструментальной наладке.
где Т – стойкость до затупления резца в одноинструментальной наладке Т=60мин а КТм=2.
Тогда скорость резания при обработке выточки:
Частота вращения шпинделя:
По паспорту станка принимаем n=2000 обмин тогда действительная скорость резания:
Найдем тангенциальную составляющую сил резания:
где - коэффициент сил резания и показатели степени по [3].
По той же формуле но с другими значениями коэффициентов и показателей рассчитаем радиальные составляющие силы резания:
Определим эффективную мощность при точении:
Назначим режимы резания и определим силы резания для остальных переходов операции 05 (табл. 5).
Максимальная эффективная мощность резания:
Мощность главного привода станка N=63 кН. С учетом потерь:
Мощность станка при обработке заготовок будет расходоваться практически полностью. Следовательно с технической стороны токарно-револьверный станок модели 1Г340П соответствует требованиям рационального выполнения данной токарной многоинструментальной операции.
Качество поверхности
Согласно технологическому процессу наружная поверхность под резьбу после токарной обработки должна иметь шероховатость поверхности не более Ra=32 мкм.
Величину шероховатости при продольном точении поверхности определяют по формуле:
где – передний угол резца r – радиус закругления режущей кромки резца r=05 мм S – принятая подача S=035 ммоб.
Таким образом в процессе токарной обработки будет обеспечиваться заданная шероховатость наружной поверхности под резьбу.
Техническое нормирование
Произведем расчет производительности и определим зарплату рабочего за выполнение операции 05 а также установим время выполнения остальных операций.
Основное время обработки поверхностей детали сведем в таблицу 6:
Вспомогательное время операции примем из [2] tв=01 мин.
Оперативное время обработки с учетом лимитирующего основного:
tоп= tо+ tв=011+01=021 мин.
По таблицам [2] примем время на техническое обслуживание станка tт.об.=03 мин; организационное обслуживание tо.об.=001 мин; время перерывов tд=002 мин.
С учетом всех значений штучное время:
tш=011+01+03+001+002=054 мин.
Подготовительно-заключительное время для наладки токарно-револьверного станка с 6 инструментами при установке заготовок в самоцентрирующий патрон tпз=10мин.
Штучно-калькуляционное время обработки партии n=1200 шт:
tшк=054+101200=055 мин.
Зарплата токаря III разряда за обработку одной детали:
Зс= tшк.К=055мин.268рубмин=15 руб.
Часовая норма выработки на операции 05:
N=60tш=60054=111 штч.
Коэффициент совмещения основного времени при сумме основного времени на обработку всех поверхностей 03 мин:
Расчеты показывают что для обработки партии заготовок n=1200на операции 05 станок модели 1Г340П будет загружен полторы рабочие смены. Стоимость выполнения операции получается низкой а рациональность схемы операции – коэффициент совмещения основного времени – хорошая.
Расчет времени для оставшейся операции 10 выполним по приближенной формуле.
tшк=0003.40=012 мин.
Экономическая оценка технологического процесса
Определим технологическую себестоимость операции 05 и определим экономическую целесообразность выполнения операции 05 на станках модели 1Г340П и модели ГС526У. Стоимость заготовки для сравниваемых вариантов одинакова и равна 006 руб.
По варианту 1 имеем: зс1=15 руб.; tоп=021 мин; tш-к.= 055 мин.
Будем считать что обработка на станке ГС526У ведется с теми же режимами и таким же режущим инструментом как и на станке 1Г340П.
to2=005+004+001+011+008+001+03=011 мин.
Расчет вспомогательного и подготовительно-заключительного времени выполним сложением составляющих элементов.
Расчет вспомогательного и подготовительно-заключительного времени операции (табл. 7):
Содержание вспомогательных переходов или работ
Взять заготовку установить открепить деталь отложить tуст.
Включить и выключить станок кнопкой
Повернуть резцовую головку на следующую позицию
Подвести инструмент к детали
Отвести инструмент в исходное положение
Время измерения при 5% контроле партии n=1200 шт.
Вспомогательное время tв=tуст+tупр+tизм=034+004+024+018+024=104 мин
Установка резцов в резцедержатель
Установка сверла в гнездо головки
Получение инструмента приспособлений сдача на склад
Подготовительно-заключительное время tпз=22 мин
Оперативное время операции:
tоп= tо+ tв=011+104=115 мин.
Время работы станка:
tоп’’= tо+ tупр=011+002=013 мин.
Время на техническое обслуживание рабочего места и перерывы 5% от tоп:
время организационного обслуживания 3%:
tо.об=003*115=003 мин.
Полное штучно-калькуляционное время операции составит:
tшк2= tоп+ tо.об+ tд+ tозn=115+003+006+002=126 мин.
Зарплата токаря III разряда с начислениями за обработку одной детали:
зс2= tшк2*К=126*268 рубмин=338 руб.
Затраты связанные с содержанием и эксплуатацией оборудования приходящиеся на одну деталь:
зоб1=021*11*06 рубмин=014 руб
зоб2=013*10*06 рубмин=008 руб.
Сведем в таблицу 8 все показатели технологической себестоимости:
Наименование показателей
Коэффициент машино-часа
Станкоемкость операции станко-минут
Зарплата станочника руб
Затраты на содержание и эксплуатацию руб
Стоимость заготовки руб
Технологическая себестоимость руб
Сравнение показателей позволяет заключить что выполнять операцию 05 на станке модели 1Г340П целесообразнее. Производительность труда повышается а технологическая себестоимость оказывается более чем в 2 раза ниже.
Анурьев В. И. Справочник конструктора. В 3-х томах. – М.: Машиностроение 2001.
Горбацевич А. Ф. Шкред В. А. Курсовое проектирование по технологии машиностроения: учебное пособие для вузов. – М.: Альянс 2007.
Справочник технолога машиностроителя. В 2-х томах. Под ред. Дальского А.М. Косиловой А.Г. – М.: Машиностроение 2001.
Егоров М. Е. Технология машиностроения: уч. для вузов. – М.: Высшая школа 1976.
Картавов С. А. Технология машиностроения. – Киев: Вища школа 1965.
Лебедев Л. В. Начала технологического проектирования: учебное пособие. – Б.: БТИСМ 1992.
Обработка металлов резанием: Справочник технологапод общ. ред. А.А. Панова. – М.: Машиностроение 2004.
Общемашиностроительные нормативы режимов резания для технологического нормирования работ на металлорежущих станках. Часть 1. Токарные карусельные токарно-револьверные сверлильные строгальные долбежные и фрезерные станки. – М.: Машиностроение 1974.
ГОСТ 2879-88 Прокат стальной шестигранный горячекатаный.
ГОСТ 7505-89 Поковки стальные штампованные. Допуски припуски и кузнечные напуски.
Укрупненный технологический маршрут изготовления штуцера.docx
Эскиз базирование примечания
Токарная обработка наружной цилиндрической поверхности под резьбу подрезка торца чистовая токарная обработка выточки сверление осевого отверстия нарезание резьбы плашкой
Токарно-револьверный станок 1Г340П
Сверление радиального отверстия
Вертикально-сверлильный станок МН25
Рекомендуемые чертежи
- 24.01.2023
- 13.12.2022