Технологический процесс изготовления деталей Корпуса и проектирование устройства для бурения




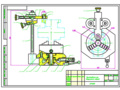
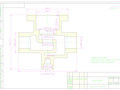
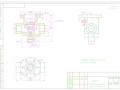
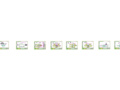
- Добавлен: 24.01.2023
- Размер: 5 MB
- Закачек: 0
Описание
Состав проекта
![]() |
![]() ![]() |
![]() ![]() ![]() ![]() |
![]() ![]() ![]() ![]() |
![]() ![]() ![]() ![]() |
![]() ![]() ![]() ![]() |
![]() ![]() |
![]() ![]() ![]() |
![]() ![]() ![]() |
![]() |
![]() |
![]() |
![]() |
![]() ![]() ![]() |
![]() |
![]() |
![]() |
![]() |
![]() |
![]() |
![]() |
![]() |
![]() |
![]() |
![]() |
![]() |
Дополнительная информация
Главный вид.dwg

тех процес.dwg

Заготовка корпуса.dwg

кондуктор корпуса.dwg

Рекомендуемые чертежи
- 24.01.2023
- 28.03.2023
- 07.09.2016
- 24.01.2023
- 25.01.2023