Технологический процесс изготовления отливки в песчаную форму для заданной детали



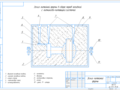
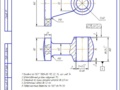
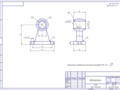
- Добавлен: 04.12.2022
- Размер: 719 KB
- Закачек: 0
Описание
Технологические процессы в машиностроении
Введение
1 Литейное производство
2 Обработка металлов давлением
3 Сварочное производство
4 Обработка резанием
Список литературы
Разработать технологический процесс изготовления отливки в песчаную форму для заданной детали. Производство крупносерийное. Формовка машинная.
Состав проекта
![]() ![]() ![]() ![]() |
![]() ![]() ![]() |
![]() ![]() ![]() ![]() |
![]() ![]() ![]() ![]() |
![]() ![]() ![]() ![]() |
Дополнительная информация
Эскиз литейной формы (вар. 13).cdw

Деталь (вар. 13).cdw

Эскиз отливки (вар. 13).cdw

Эскиз заготовки (штамповка) вар. 13.cdw

Рекомендуемые чертежи
- 24.01.2023
- 13.12.2022
- 24.01.2023
- 28.03.2023