Совершенствование техпроцесса механической обработки червяка Н0401Б0201051 и сборки редуктора Н0401Б.02.11, 000 СБ в условиях ОАО Могилевлифтмаш




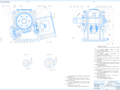
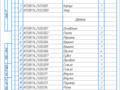
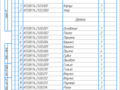
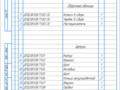
- Добавлен: 24.01.2023
- Размер: 4 MB
- Закачек: 0
Описание
Совершенствование техпроцесса механической обработки червяка Н0401Б0201051 и сборки редуктора Н0401Б.02.11, 000 СБ в условиях ОАО Могилевлифтмаш
Состав проекта
![]() |
![]() |
![]() ![]() ![]() ![]() |
![]() ![]() ![]() ![]() |
![]() ![]() ![]() ![]() |
![]() |
![]() ![]() ![]() ![]() |
![]() |
![]() ![]() ![]() ![]() |
![]() ![]() ![]() ![]() |
![]() ![]() ![]() ![]() |
![]() ![]() ![]() ![]() |
![]() ![]() ![]() |
![]() ![]() ![]() ![]() |
![]() ![]() ![]() ![]() |
![]() ![]() ![]() ![]() |
![]() |
![]() |
![]() |
![]() ![]() ![]() |
![]() ![]() ![]() ![]() |
![]() ![]() ![]() ![]() |
![]() ![]() ![]() ![]() |
![]() |
![]() |
![]() ![]() ![]() |
![]() |
![]() ![]() ![]() |
![]() ![]() ![]() ![]() |
![]() |
![]() ![]() ![]() |
![]() |
![]() |
![]() |
![]() ![]() ![]() ![]() |
![]() ![]() ![]() |
![]() |
![]() ![]() ![]() ![]() |
![]() |
![]() ![]() ![]() ![]() |
![]() ![]() ![]() |
![]() ![]() ![]() |
![]() ![]() ![]() |
![]() ![]() ![]() |
![]() ![]() ![]() ![]() |
![]() ![]() ![]() |
![]() ![]() ![]() ![]() |
![]() ![]() ![]() ![]() |
![]() |
![]() ![]() ![]() |
![]() ![]() ![]() ![]() |
![]() ![]() ![]() |
![]() ![]() ![]() |
![]() ![]() ![]() |
![]() ![]() ![]() ![]() |
![]() ![]() ![]() |
![]() ![]() ![]() ![]() |
![]() |
![]() |
![]() ![]() ![]() ![]() |
![]() ![]() ![]() ![]() |
Дополнительная информация
Схема сборки.cdw

Поковка ujnjdfz.cdw

Спецификация Редуктор.spw

Эскизы операционные .bak.cdw

Сборочный Чертеж1.cdw

1. Червяк - чертеж детали.cdw

Сборочный чертеж 2.cdw

Sborka_eskizy (1).cdw

РТКомплекс.cdw

Экономика.cdw

РТКарта.cdw

Фрагмент Оп 065.frw

Фрагмент Оп 010.frw

Фрагмент Оп 015б.frw

Фрагмент Оп 040.frw

Фрагмент Оп 030,1.frw

Приспособление.spw

Фрагмент Оп 030.frw

Фрагмент Оп 015а.frw

Фрагмент Оп 075.frw

Фрагмент Оп 055.frw

Фрагмент Оп 070.frw

Фрагмент 060.frw

Сборка эскизы.cdw

Приспособление.spw

Приспособление.cdw

Рекомендуемые чертежи
- 24.01.2023
- 09.04.2021
- 24.01.2023
- 23.04.2016
- 25.05.2024
- 08.06.2018
Свободное скачивание на сегодня
- 22.08.2014
- 29.08.2014