Разработки технологического процесса изготовления детали вал




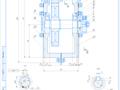
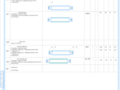
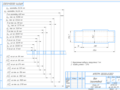
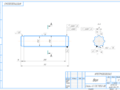
- Добавлен: 24.01.2023
- Размер: 694 KB
- Закачек: 0
Описание
Состав проекта
![]() |
![]() |
![]() |
![]() ![]() ![]() ![]() |
![]() ![]() ![]() ![]() |
![]() ![]() ![]() ![]() |
![]() ![]() ![]() ![]() |
![]() ![]() ![]() |
Дополнительная информация
Редуктор общего назначения Сергей 5.cdw

заготовка Сергей 5.cdw

Вал Сергей 5.cdw

тех.проц.Сергей 5.cdw

Рекомендуемые чертежи
- 24.01.2023
- 24.01.2023
- 24.01.2023