Проектирование технологического процесса изготовления детали корпус тяги и средств технологического оснащения для его реализации




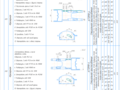
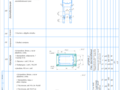
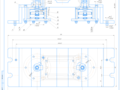
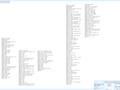
- Добавлен: 24.01.2023
- Размер: 11 MB
- Закачек: 5
Описание
Состав проекта
![]() |
![]() |
![]() |
![]() |
![]() |
![]() |
![]() |
![]() |
![]() ![]() ![]() |
![]() |
![]() |
![]() ![]() ![]() ![]() |
![]() ![]() ![]() ![]() |
![]() |
![]() ![]() ![]() ![]() |
![]() ![]() ![]() ![]() |
![]() ![]() ![]() ![]() |
![]() ![]() ![]() ![]() |
![]() ![]() ![]() ![]() |
![]() |
![]() ![]() ![]() ![]() |
![]() ![]() ![]() ![]() |
![]() |
![]() |
Дополнительная информация
РПЗ.docx
ДЕТАЛЬ ТИП ПРОИЗВОДСТВА ТЕХНОЛОГИЧНОСТЬ ТЕХНОЛОГИЯ ТЕХНОЛОГИЧЕСКОЕ ОСНАЩЕНИЕ РЕЖИМЫ ОБРАБОТКИ РАСЧЕТ ПРИСПОСОБЛЕНИЯ БАЗИРОВАНИЕ ПЛАНИРОВКА ЭКОНОМИЧЕСКАЯ ЭФФЕКТИВНОСТЬ САПР ТП.
Цель работы - повышение производительности и качества изготовления детали стакан путем совершенствования структуры технологического процесса.
Объектом исследования в работе является технологический процесс изготовления детали корпус тяги в условиях серийного производства.
Полученные результаты и их новизна – в данном дипломном проекте были решены задачи поставленные для достижения повышения производительности труда в условиях серийного производства. Используя основные направления в современной технологии машиностроения был выбран оптимальный метод получения заготовки что дало возможность значительно снизить трудоёмкость обработки детали на металлорежущих станках и сократить расход металла. Применение станков с числовым программным управлением приспособлений с быстродействующими зажимами позволило повысить производительность труда. Снижение трудоёмкости перемещения детали между рабочими местами было учтено при разработке участка механической обработки что позволило достигнуть лучших технико-экономических показателей по сравнению с существующими на «Воронежском Механическом Заводе».
Задание на выпускную квалификационную работу
Проектно-конструкторская часть
1 Конструктивно технологический анализ узла составной частью которого являются выбранная для проектирования деталь (условия работы технические требования и т.д.)
2 Назначение и краткое техническое описание детали
3 Разработка твердотельной 3D модели объекта для проектирования технологичной конструкции детали
4 Расчет силовых и деформационных параметров детали в процессе её
эксплуатации или изготовления с использованием САЕ.
Производственно-технологическая часть
1 Оценка технологичности детали
2 Установление типа производства
3 Анализ базового технологического процесса
4 Обоснование и разработка мероприятий по оптимизации базового технологического процесса
5 Выбор типа заготовки и предварительное назначение припусков
6 Выбор технологических баз и оценка точности базирования
7 Разработка плана обработки и маршрута операций технологического процесса обработки детали
8 Выбор моделей оборудования
9 Обоснование конструкции и расчет специальных средств технологического оснащения
9.1 Описание и расчет станочного приспособления
9.2 Выбор контрольного приспособления
10 Аналитический расчет технологических параметров
10.1 Расчет и назначение припусков
10.2 Аналитический расчет режимов резания
11 Автоматизированное проектирование технологического процесс изготовления детали и средств технического оснащения
11.1 Проектирование операционной технологии в Компас АВТОПРОЕКТ
11.2 Разработка управляющей программы с виртуальным моделированием обработки для станков с ЧПУ в САПР
12 Технологическое проектирование участка механического цеха
12.1 Определение потребности в оборудовании
12.2 Расчёт численности персонала
12.3 Определение производственной площади участка
12.4 Компоновка участка
12.5 Разработка технологической планировки участка цеха
Эксплуатационная часть
Научно-исследовательская часть
Исследование процесса заточки фрез для станков 6Р13РФ3 6Т13МФ4
Экономическая и организационно-управленческая часть
1 Экономическое обоснование проекта участка
1.1 Определение потребности в инвестициях для организации спроектированного участка
1.2 Организация оплаты труда на участке
1.3 Расчет текущих затрат
1.4 Расчет себестоимости продукции
2 Расчет технико-экономических показателей
3 Расчет показателей экономической эффективности проекта
4 Качественные показатели оценки элементов экономического потенциала
Экологичность и безопасность
1 Техника безопасности на машиностроительных предприятиях
2 Защита окружающей среды на машиностроительном предприятии
Список литературы 116
Приложение А Комплект чертежей
Приложение Б Комплект карт технологического процесса
Перед технологами-машиностроителями стоят задачи дальнейшего повышения качества машин снижения трудоемкости себестоимости и материалоемкости внедрения поточных методов работы механизации и автоматизации производства и сокращения сроков подготовки производства новых объектов.
Постоянно возрастающая интенсивность работы деталей машин механизмов металлообрабатывающих инструментов и других изделий при одновременном уменьшении их массы предъявляет все более жесткие требования к качеству и надежности изделий которые становятся важнейшими факторами технического прогресса. Совершенствование технологических процессов обработки материалов определяет рост эффективности и производства заключающийся в повышении производительности труда экономии материальных и энергетических ресурсов а также качества продукции. Добиться высокого комплекса свойств определяющих конструкционную прочность материала детали можно применением специальных материалов обладающих высокими механическими свойствами и высокоэффективных методов упрочнения.
Целью настоящего дипломного проектирования является разработка технологии и технологического оснащения для обработки детали корпус тяги; численное проектирование эффективной операционной технологии с составлением программ на ЧПУ; численное обоснование метода изготовления заготовки; численное формирование состава переходов и операций; обоснование необходимости использования программных средств для технологического проектирования.
Для достижения указанной цели необходимо решение ряда технологических задач:
Совершенствование маршрутного технологического процесса путем замены традиционных способов механической обработки современными высокопроизводительными способами размерной обработки.
Совершенствование операционного технологического процесса за счет концентрации операций с применением специального комбинированного режущего инструмента специальной оснастки и много инструментальных станков с ЧПУ.
Оснащение металлорежущего оборудования специальными высокоточными установочными и контрольными приспособлениями.
Проведение организационно-технических мероприятий по перепланировке производственного участка предназначенного для выпуска детали и оценке последствий его функционирования на экологию окружающей среды и безопасность жизнедеятельности человека. Для практической реализации поставленных целей и задач дипломного проектирования целесообразно выявить новые технические решения в области способов и устройств для комбинированной обработки деталей оснастки и металлорежущего инструмента провести их конструкторскую проработку а также провести технико-экономический анализ целесообразности организации специализированного предметного участка в составе механического цеха.
1 Конструктивно технологический анализ узла составной частью которого
являются выбранная для проектирования деталь
Управление вертолетом т. е. изменение его балансировочного положения относительно трех пространственных осей производится путем изменения значения и направления силы тяги несущего винта значения силы тяги рулевого винта.
Управление силами тяги несущего и рулевого винтов осуществляется с помощью системы управления вертолетом.
Система управления включает отдельные самостоятельные цепи продольного поперечного путевого управлений и вертикального перемещения. Цепи продольного и поперечного управлений связаны с ручкой управления циклическим шагом несущего винта и автоматом перекоса цепь путевого управления - с педалями и механизмом изменения шага рулевого винта цепь вертикального перемещения с ручкой ШАГ-ГАЗ - с двигателями и автоматом перекоса.
В корпусе тяги монтируется механизм позволяющий изменять вертикальную составляющую для перемещения вертолета по вертикали. Корпус тяги входит в сборочную единицу рукоятки ШАГ-ГАЗ служащую для изменения положения вертолета по вертикали. Для вертикального перемещения вертолета необходимо изменить вертикальную составляющую что достигается изменением общего шага несущего винта. Изменение тяги несущего винта по величине достигается при помощи ручки объединенного управления ШАГ-ГАЗ путем одновременного изменения общего шага несущего винта и режима работы двигателей. Наряду с объединенным управлением двигателями с помощью ручки ШАГ-ГАЗ на вертолете имеются рычаги раздельного управления двигателями. Рычаги позволяют производить раздельное опробование двигателей без изменения общего шага несущего винта а также обеспечивают возможность подбора оптимального режима работы в случае вынужденного полета на одном работающем двигателе.
Рисунок 1.1 – Корпус тяги
Корпус тяги предназначен для управления движения рукояткой набора высоты с поворотом на определенный градус и перемещения по направляющим одной оси. Корпус тяги имеет множество отверстий и пазов для прохождения сквозь них валов для крепления и связи с другими элементами требуемой конструкции. В связи с небольшими нагрузками и необходимости небольшого веса для изготовления корпуса тяги зачастую используют цветные сплавы. Корпус тяги (смотри рисунок 1.1) – деталь к которой предъявляется требование высокой поверхностной твердости при невысокой прочности сердцевины; работающая в условиях износа при трении [4].
Корпус тяги изготавливается из алюминиевого ковочного сплава АМ4 ГОСТ 2858-79. Алюминий АМ4 имеет высокий предел текучести малую чувствительность к концентраторам напряжений.
Алюминий ковочный обладает хорошей прокаливаемостью и малой чувствительностью к отпускной хрупкости.
Химический состав механические свойства при Т=200 и физические свойства материала представлеы в таблице 1 [3].
Таблица 1.1 - Характеристика материала АМ4
Для изготовления сложных штамповок
Механические свойства при Т=200С
Предел кратковременной прочности (Sв МПа)
Предел пропорциональности (предел текучести для остаточной деформации) (Sт МПа)
Относительное удлинение при разрыве (d5 %)
Ударная вязкость (KCU кДжм2)
Твердость по Бринеллю (НВ МПа)
Физические свойства материала
Температура при которой получены данные свойства (Т град)
Модуль упругости первого рода (Е10-5 МПа)
Коэффициент температурного (линейного) расширения (α106 1град)
Удельная теплоемкость материала (С Дж(кг*град))
Удельное электросопротивление (R109 Ом*м)
Сплав хорошо деформируется в горячем состоянии хорошо обрабатывается резанием удовлетворительно сваривается склонен к коррозии под напряжением и чувствителен к межкристаллитной коррозии поэтому детали следует анодировать и защищать лакокрасочными покрытиями.
Термообработка: закалка и искусственное старение.
Чертеж детали является основным источником информации для выполнения дипломного проекта. Размещенные на нем виды и проекции дают полное представление о конструкции детали.
Точность обработки поверхностей детали соответствует 8÷14 квалитетам точности следовательно все поверхности детали проходят неоднократную обработку.
Корпус тяги является ответственной корпусной деталью. К надёжности его работы предъявляются высокие требования поэтому упрощение конструкции детали и замена материала невозможны. Чистота обработки поверхностей варьируется от Ra 1.6 до Ra 63 то есть поверхности проходят многократную обработку: черновую получистовую и чистовую.
Необходимые информационные данные для анализа технических условий представлены на рабочем чертеже детали.
Заготовкой детали является отливка в закрытых штампах которая проходит закалку и искусственное старение.
Большинство радиусных размеров детали до 6 мм обеспечиваются инструментом.
Построение твердотельной модели детали ведем в программе Unigrafics NX 4.
Система трехмерного твердотельного моделирования предназначена для создания трехмерных параметрических моделей отдельных деталей и сборочных единиц содержащих как оригинальные так и стандартизованные конструктивные элементы.
Подсистема Unigrafics NX 4 предназначена для создания трехмерных параметрических моделей деталей с целью передачи геометрии в расчетные пакеты и в пакеты разработки управляющих программ для оборудования с ЧПУ а также расчета их геометрических и массо-центровочных характеристик.
В запущенной программе выбираем команду файл Создать деталь.
В дереве модели выбираем плоскость XY. На панели «Элемент построения» выбираем пиктограмму эскиз и в поле чертежа с помощью графических примитивов строим наружный контур детали с внутренними отверстиями и пазами все построения ведутся в мм (рисунок 1.2).
Рисунок 1.2 – Построение наружного контура детали
Закрываем эскиз. С помощью операции выдавливания строим твердотельную модель толщиной 30 мм (рисунок 1.2).
Рисунок 1.3 – Построение твердотельной модели с помощью выдавливания
Строим отверстия с помощью команды выдавливания (рисунок 1.4).
Рисунок 1.4 – Построение околодца с помощью команды выдавливани
Строим одно из четырех сквозных отверстий. С помощью операции «Массив по концентрической сетке» создаем остальные три отверстия. (рисунок 1.5).
Рисунок 1.5 – Построение глухих отверстий.
Построение 2D модели объекта детали ведем в программе КОМПАС-3D
Имеет смысл параметризовать чертежи деталей при модификациях которых изменяются только размеры и не меняется топология изображения. Однажды созданная параметрическая модель детали может быть быстро перестроена простым изменением значений размеров.
Выбираем в меню: ФайлСоздатьЧертеж.
Затем выбираем в меню: ВставкаВид с моделиСтандартные.
Создаем дополнительные виды разрезы выноски образмериваем чертёж проставляем шероховатости (рисунок 1.7).
Рисунок 1.6 – Создание стандартных видов
Рисунок 1.7 – Формирование рабочего чертежа детали
4 Расчет силовых и деформационных параметров детали в процессе её
SolidWorks имеет простой в использовании новый инструмент анализа напряжений для пользователей COSMOSXpress. COSMOSXpress может помочь снизить стоимость и сократить время от начального замысла проекта до его внедрения на рынок выполняя тестирование проектов с помощью компьютера вместо проведения дорогостоящих и долговременных производственных испытаний. Точность результатов анализа зависит от свойств материала ограничений и нагрузок. Чтобы получить надежные результаты указанные свойства материала должны точно представлять материал детали а ограничения и нагрузки должны точно представлять условия эксплуатации детали.
Реакция детали зависит от того из какого материала она сделана. Программе COSMOSXpress необходимо знать упругие свойства материала из которого сделана деталь. Материал назначается для детали путем его выбора из библиотеки материалов. Для материалов в SolidWorks существует два набора свойств: видимые и физические (механические). COSMOSXpress использует только физический набор свойств. Библиотека материалов SolidWorks содержит уже заданные свойства материалов
На вкладке Ограничения определяются ограничения. Каждое ограничение может содержать несколько граней. Для ограниченных граней сохраняются взаимосвязи во всех направлениях. Во избежание сбоя анализа из-за движения твердого тела необходимо указать ограничение хотя бы для одной грани детали.
В процессе анализа напряжений или статического анализа на основе материала ограничений и нагрузок рассчитываются перемещения нагрузки и напряжения в детали. Материал разрушается когда напряжение достигнет определенного уровня. Разные материалы разрушаются при различных уровнях напряжения. Для расчета напряжений COSMOSXpress использует линейный статический анализ на основе метода конечных элементов. Чтобы рассчитать напряжения в детали при линейном статическом анализе делается несколько допущений(смотри рисунок 1.8).
Рисунок 1.8 – Напряжение-Эпюра1
COSMOSXpress составляет уравнения управляющие поведением каждого элемента и учитывающие его связи с другими элементами. Эти уравнения устанавливают взаимосвязь между перемещениями и известными свойствами материалов ограничениями и нагрузками.
Затем программа преобразует уравнения в большую систему алгебраических
уравнений. Решающая программа обнаруживает перемещения в направлениях X Y и Z в каждом узле (смотри рисунок 1.9).
Используя перемещения программа рассчитывает нагрузки действующие в различных направлениях. Наконец программа использует математические выражения для расчета напряжений(смотри рисунки 1.10-1.11).
COSMOSXpress результаты анализа проектирования базируются на линейном статическом анализе и предполагается изотропный материал.
Линейный статический анализ предполагает что:
) поведение материала является линейным согласно закону Гука
) вызванные нагрузкой смещения являются достаточно небольшими чтобы не учитывать изменения жесткости в результате нагрузки и
) нагрузки прикладываются медленно чтобы не учитывать динамические эффекты.
Рисунок 1.9 – Перемещение-Эпюра2
Рисунок 1.10 – Деформация –Эпюра 3
Рисунок 1.11– Проверка проектирования – эпюра 4
Рисунок 1.12 – Проверка проектирования
Под технологичностью конструкции понимают степень соответствия конструкции изделия оптимальным производственно-технологическим условиям его изготовления при заданном объеме выпуска; технологичной считается та удовлетворяющая эксплуатационным требованиям конструкция освоение и выпуск которой при заданном объеме производства будет протекать с минимальными производственными издержками – с наименьшей трудоемкостью и материалоемкостью и с кратчайшим производственным циклом.
Корпус тяги является ответственной корпусной деталью. К надёжности его работы предъявляются высокие требования поэтому упрощение конструкции детали и замена материала невозможны. Все поверхности детали подлежат обработке. Чистота обработки поверхностей варьируется от Ra 1.6 до Ra 63 то есть поверхности проходят многократную обработку: черновую получистовую и чистовую.
Выбор наиболее простой формы изготовления корпуса тяги и выбор материала обуславливает наиболее простое и экономичное его изготовление.
В корпусе тяги обрабатываются торцевые поверхности внутренние поверхности резьбовые. Имеются сквозные отверстия. Отверстия корпуса можно одновременно обрабатывать на станках либо многошпиндельной головкой либо на многоцелевых станках с поворотным столом и с горизонтальным расположением оси шпинделя.
Конструкция корпуса тяги обеспечивает свободный доступ инструмента к обрабатываемым поверхностям при его неизменной установке.
При изготовлении корпуса тяги используются станки серийного изготовления. Оснастка достаточно проста. Правильный выбор типа заготовки обуславливает высокий коэффициент использования материала. Использование станков с ЧПУ позволяет повысить производительность изготовления корпуса тяги. Трудоемкость изготовления невысока так как технологический процесс частично автоматизирован.
За счет литейных работ на стадии заготовительного процесса (изготовление заготовки) уменьшается объем окончательной механической обработки корпуса тяги что позволяет увеличить выпуск деталей уменьшить расход металла на единицу изделия.
Определим коэффициент сложности конструкции детали:
где – коэффициенты определяемые как – уточняющие коэффициенты.
Коэффициент зависит от количества поверхностей на исходной заготовке с которых удаляется стружка при изготовлении детали.
где – количество обрабатываемых резанием и общее количество формообразующих поверхностей детали соответственно.
Подставляя численные значения требуемых показателей из чертежа детали и технологического процесса обработки детали резанием находим:
Коэффициент учитывает общее количество заданных на чертеже данных по обеспечению требуемых точностей формы и взаимного расположения поверхностей в пределах 005 мм.
где – количество поверхностей детали к которым предъявляются требования по точности формы и их взаимному расположению в пределах 005 мм.
Подставляя численные значения требуемых показателей находим:
Коэффициент учитывает количество различных видов обработки резанием.
где – количество различных видов обработки резанием;
– общее количество технологических переходов обработки резанием.
Подставляя численные значения требуемых показателей из карт технологического процесса обработки детали резанием находим:
Коэффициент учитывает соответствие точности и шероховатости поверхностей корпуса оптимальным экономически и конструктивно обоснованным величинам.
Величина определяется по формуле:
где – количество зон на которых параметр для j-ой поверхности отстоит от оптимального сочетания.
Коэффициент сложности конструкции детали будет составлять:
Коэффициент применяемости унифицированных или стандартных конструктивных элементов детали определяют по формуле:
где – общее количество конструктивных элементов в детали;
– количество унифицированных конструктивных элементов;
n – количество неунифицированных элементов.
Поскольку все формообразующие поверхности корпуса можно считать унифицированными то коэффициент применяемости унифицированных или стандартных конструктивных элементов детали принимаем равным .
Коэффициент повторяемости конструктивных элементов детали рассчитывают по формуле
где – количество повторяющихся конструктивных элементов детали;
– общее количество конструктивных элементов детали.
Коэффициент использования материала
где Мдет – масса детали кг;
Мзаг – масса заготовки кг.
По полученным значениям показателей технологичности можно сделать вывод о среднем уровне технологичности детали.
1 Установление типа производства
Общее количество типовых деталей выпускаемых на участке в течение года определяется на основе расчета приведенной программы по формуле:
где FД – действительный годовой фонд времени работы оборудования в соответствии с принятым режимом работы участка;
Кз – плановый коэффициент загрузки оборудования Кз = 085;
А – Коэффициент допустимых потерь на переналадку оборудования А = 005;
Тшт = 283 мин. (на операцию №040 по проектному варианту техпроцесса).
где Др – число рабочих дней в году Др = 251 дней;
mсм – число рабочих смен в сутки mсм = 1 смена;
tcм – продолжительность рабочей смены ч tcм = 8;
kп – плановые потери времени на ремонт % (kп= 5%).
Принимаем Nгод = 34000в год .
Количество наименований выпускаемых изделий определяется по формуле:
программа выпуска деталей равна N = 400 шт.
МД = 34000 400 = 85 наименований
Принимаем МД = 85 наименования.
На основании определенной программы определяется величина такта выпуска изделия.
Такт выпуска 34 миншт.
Темп - величина обратная такту производства – количество изделий или заготовок одинакового наименования выпускаемого в единицу времени (час):
Количество деталей в партии для одновременного запуска n (шт.) определяется по формуле [8 с. 22]
где F – количество рабочих дней в году равно 251 а – число дней на которое необходимо иметь запас деталей (периодичность запуска-выпуска соответствующая потребности в сборке). Для того что бы в течение месяца было произведено не более 3-4 запусков партии деталей а принимаем равным 10.
Ритм R определяется по формуле
Тип производства зависит от размера производственной программы характера продукции а также технических и экономических условий осуществления производственного процесса или трудоемкости изготовления детали.
Под типом производства понимается совокупность признаков определяющих организационно-технологическую характеристику производственного процесса. Тип производства во многом предопределяет формы организации производственного процесса. Он определяется с помощью коэффициента серийности:
где tв - такт выпуска изделий - среднее штучное время.
Для разработанного технологического процесса = 283 мин.
Значение 1≤Кс≤10 соответствует серийному типу производства [20].
Серийным называется такое производство при котором изготовление изделий производится партиями состоящими из одноименных однотипных по конструкции и одинаковых по размерам изделий запускаемых в производство одновременно. В таком производстве технологический процесс дифференцирован т.е. расчленен на отдельные операции которые закреплены за определенными станками а номенклатура изделий – ограничена. Характерно использование специализированного и специального оборудования станков с ЧПУ обрабатывающих центров гибких автоматизированных систем. Оборудование расставляется по технологическим группам с учетом направления основных грузопотоков. В большинстве случаев создается высокопроизводительная специальная оснастка. В качестве заготовок используется горячий и холодный прокат точные штамповки и прессовки. Требуемая точность достигается методами автоматического получения размеров.
Форма организации производства представляет собой определенное сочетание во времени и в пространстве элементов производственного процесса выраженное системой устойчивых связей.
Для участков механической обработки деталей наиболее распространенными являются технологическая и предметная формы организации производства.
Технологическая форма организации производства предполагает создание участков на которых оборудование располагается группами по признаку технологической однородности и размеров. Такая форма организации обеспечивает максимальную загрузку оборудования в условиях мелкосерийного производства и приспособлена к частым изменениям в технологическом процессе. В то же время применение технологической формы имеет ряд отрицательных последствий. Большое количество деталей и их многократное перемещение в процессе обработки приводят к росту объема незавершенного производства и увеличению числа пунктов промежуточного складирования. Значительную часть производственного цикла составляют потери времени обусловленные сложной межучастковой связью.
При предметной форме организации производства на участке устанавливается как правило все оборудование необходимое для обработки группы деталей с начала и до конца технологического процесса. Если технологический цикл обработки замыкается в пределах участка то он называется предметнозамкнутым. Предметное построение участков обеспечивает прямоточность и уменьшение длительности производственного цикла изготовления деталей. В сравнении с технологической формой организации предметная позволяет снизить общие расходы на транспортировку деталей потребность в производственной площади на единицу продукции. Вместе с тем данная форма имеет и недостатки. Главный из них состоит в том что при определении состава оборудования устанавливаемого на участке на первый план выдвигается необходимость выполнения определенных видов обработки что не всегда обеспечивает полную загрузку оборудования. Кроме того расширение номенклатуры выпускаемой продукции ее обновление обуславливает потребность в перепланировке производственных участков изменении структуры парка оборудования.
Анализ заводского технологического процесса является важной стадией проектирования так как позволяет выявить преимущества и недостатки присущие базовой технологии [3].
Технологический процесс обработки детали является совокупностью механообрабатывающих операций в процессе выполнения которых деталь принимает окончательные форму и размеры поверхностей. Построение и содержание технологического процесса обработки заготовки детали определяется в основном выбором баз и размерными связями между различными поверхностями.
На базовом предприятии технологический процесс (ТП) разработан для мелкосерийного производства.
Чертеж на деталь включает все необходимые данные и не имеет ошибок в размерных цепях.
Анализируя базовый технологический процесс механической обработки заготовки достоинством является минимизированное число операций.
Методы обработки в технологическом процессе приняты правильно. Станки при обработке данных деталей используютcя при мелкосерийном производстве. Недостатком является их износ.
Технологический процесс изготовления обеспечивает высокую долговечность и надёжность корпуса тяги. Но в тоже время базовый технологический процесс имеет целый ряд недостатков. Среди которых следует отметить следующие:
- Технологический процесс (ТП) разработан в виде маршрутной карты нет подробной разбивки технологического процесса на отдельные операции.
- Малая степень автоматизации.
- В нём нет ссылок на специальную оснастку или специальный инструмент.
- Базовая технология плохо представляет особенности эксплуатации данной детали.
При разработке нового технологического процесса механической обработки необходимо учитывать положительные и отрицательные стороны действующего технологического процесса на изготавливаемую деталь.
При анализе технологического процесса необходимо обратить особое внимание на уровень механизации и автоматизации всех производственных процессов изготовления деталей а также соответствия требованиям ЕСКД ЕСТД ЕСТПП [3].
При увеличении программы выпуска базовый технологический процесс перестает удовлетворять технико-экономическим требованиям современного производства поэтому для его усовершенствования необходимо произвести оптимизацию способа получения заготовки а также механизировать несколько приспособлений что значительно сократит трудоёмкость изготовления детали и увеличит производительность [4].
Вывод: проектируемый ТП будет выгодно отличаться от базового. Данный технологический процесс будет более эффективным и технологичным по сравнению с заводским т.к. сократится время на токарные операции сократится количество слесарных операций вследствие чего уменьшатся затраты на оборудование электроэнергию амортизацию площади сократится количество рабочих мест и увеличатся затраты на заработную плату.
Деталь имеет неравномерное распределение металла по длине то есть имеет сложную форму. Исходя из этого для подробного анализа видов получаемой заготовки представляется необходимым взять следующие варианты:
Деталь изготавливается методом штамповки.
Расчёт ведём по [2]. Стоимость заготовок получаемых такими методами литья как литьё в обычные земляные формы и кокили литьё по выплавляемым моделям литьё под давлением штамповка можно с достаточной точностью определить по формуле:
Литьё которое способно обеспечить минимальный необходимый для механической обработки припуск но это должен быть специальный вид литья в то же время существенный объём металла будет расходоваться на литниковую систему;
- коэффициенты зависящие от класса точности группы сложности массы марки материала и объёма производства заготовок;
Q – масса заготовки руб;
q – масса готовой детали кг;
Sот – цена 1 тонны отходов руб.
Тогда определим стоимость получения заготовки методом литья по формуле (2.16)
Если деталь изготавливается из проката то затраты на заготовку определяются по весу проката требующегося на изготовление детали и весу сдаваемой стружки. При этом принимается во внимание стандартная длина прутков:
где Q – масса заготовки кг;
S – цена одного килограмма материала заготовки руб;
– цена одной тонны отходов руб.
Тогда по формуле (2.17) получим
Количественную оценку точности ведут по методике изложенной в ЕСКД. При этом коэффициент использования материала (КИМ) определяется по формуле:
где - масса детали по чертежу кг;
– масса материала израсходованного на изготовление детали кг.
В первом случае масса детали равна 235 кг минимально необходимая масса базовой заготовки составляет 31 кг. Во втором случае масса детали равна 235 кг минимально необходимая масса базовой заготовки составляет 57 кг.
Тогда по уравнении (1.7) получим
Из приведённых расчётов видно что метод штамповки литья под давлением значительно дороже чем метод получения заготовки литье под давлением. Однако при получении заготовки методом штамповки значительно вырастает коэффициент неиспользованного материала. Для изготовления заготовки выбираем метод литья под давлением так как его можно автоматизировать средний коэффициент использования материала низкую шероховатость применяют для стали чугуна и цветных сплавов.
6 Выбор технологических базовых поверхностей и оценка точности
Выбор поверхностей пригодных для использования их в качестве технологических баз обычно ведут с учётом классификатора способов базирования и конкретной конфигурации поверхностей обрабатываемой детали. Применительно к случаю обработки корпуса заданной конструкции это реализуется следующим образом.
Так как корпус представляет собой симметричное тело у которого механической обработке резанием подвергаются внутренние поверхности и задняя цилиндрическая поверхность. По этой причине наиболее целесообразным представляется использование передней торцевой поверхности корпуса в качестве первоначальной базовой поверхности относительно которой следует подрезать торец и расточить поверхность заготовки. Затем развернув заготовку на 1800 и установив в кулачках выполнить черновое и чистовое точение внутренних поверхностей. Дальнейшая смена баз происходит по мере токарной обработки корпуса.
При расчёте точности обработки учитывались величина возможного рассеивания отклонений заданного параметра.
Положение заготовок в приспособлении зависит от погрешности выполнения базовой поверхности заготовки неточности изготовления износа опорных элементов приспособления нестабильности силы закрепления.
Погрешности установки заготовок в приспособлении у вычисляется с учётом погрешности базирования б погрешности закрепления з погрешности изготовления и износа опорных элементов приспособления пр. Погрешность установки определяется как предельное поле рассеивания положений измерительной поверхности относительно поверхности отсчёта в направлении выдерживаемого размера.
Так как указанные погрешности являются случайными величинами то погрешность установки определяется по формуле:
При определении погрешности базирования использованы справочные данные. Так при установке детали в самоцентрирующемся патроне с упором в торец погрешность базирования равна нулю а погрешность закрепления равна 120 мкм.
Тогда результат расчёта суммарной погрешности по формуле (2.19) составляет:
7 Разработка плана обработки и маршрута операций технологического про-
цесса обработки детали
Разработка маршрута обработки детали начинается с предварительного выбора видов обработки отдельных поверхностей заготовки и определения методов достижения точности соответствующей требованиям чертежа.
Построение маршрутной технологии во многом зависит от конструктивно-технологических особенностей детали и требований точности предъявляемых к ее основным наиболее ответственным поверхностям. Для основных поверхностей с учетом точности выбранной заготовки назначают число и последовательность переходов определяют содержание операций. Деление всего объема обработки на операции выбор оборудования формирование операций по содержанию зависят от условий производства. В поточном производстве штучное время любой операции должно соответствовать такту выпуска а для этого в некоторых случаях требуется применять специальные приспособления инструментальные наладки и станки.
При обработке на универсальных станках стремятся к более полному использованию их возможностей. Наиболее точные станки используют для чистовой и отделочной обработки выполняемой в отдельные операции.
В маршрутной технологии в процессе обработки предусматривают межоперационный контроль для технологического обеспечения заданных параметров качества обрабатываемой детали. План технологического процесса в виде маршрутной технологии составляют по рабочему чертежу. Планом технологического процесса устанавливаются границы между операциями последовательность операций установочные базы степень концентрации операций поверхности базирования и способы закрепления детали. При установлении общей последовательности обработки сначала обрабатывают поверхности принятые за технологические базы. Затем обрабатывают оставшиеся поверхности в последовательности повышения степени их точности. Последней обрабатывается наиболее точная поверхность. В таблице 2.1 приведен перечень операций по изготовлению корпуса тяги.
Таблица 2.1 – Перечень операций по изготовлению корпуса тяги
Наименование операции
Станок горизонтально-фрезерная 6Р13РФ-3
Станок горизонтально-фрезерный 6Т13МФ4
Станок горизонтально-фрезерный 6Т13РФ-4
Станок горизонтально-фрезерный 6Т13РФ-3
9 Обоснование конструкции и расчёт специальных средств технологическо
Спроектированное приспособление применяется для автоматического закрепления детали при сверлении отверстий. Что значительно сокращает время на установку и закрепление увеличивает надежность обработки (смотри рисунок 2.1).
Рисунок 2.1 – Приспособление специальное
Принцип работы сводится к следующему: деталь устанавливается на плиту нижнюю а сверху накрывается верхней плитой с втулками. К нижней плите присоединен пневмоцилиндр который создает условие зажима. Давление из пневмосети подается в верхнюю полость пневмоцилиндра поршень опускается вниз зажимая заготовку. Затем просверливаются отверстия через втулки. После завершения операции сбрасывается давление в пневмосети пружина поднимает поршень вверх перемещая коромысло с откидными шпильками и разжимает деталь.
Разработка расчетной схемы и расчет теоретического зажимного усилия.
Для расчёта силы закрепления используем схему (рисунок 2.2).
Рисунок 2.2 – Схема действия сил при фрезеровании
Мкр.= См · Dq · Sy · Kр; (2.21)
Значения коэффициентов и показателей степеней берём из справочных нормативных таблиц.
См = 00345; q = 2; y = 08; Kр=1; D=30.
Подставив данные в формулу (2.21) получаем:
Теоретическое зажимное усилие рассчитывается по формуле:
где f – коэффициент трения (обрабатываемая поверхность контактирует с плоскостью опорного или контактного элемента) f=01;
D – диаметр опорной поверхности под шайбой D=320 мм.
Подставив имеющиеся значения в формулу (2.8) получаем:
Расчет коэффициента запаса зажимного усилия.
где k1 = 15 – гарантированный коэффициент надёжности;
k2 = 12 – коэффициент учитывающий увеличение сил резания при наличии неровностей на заготовке;
k3 = 1 – коэффициент непрерывности резания;
k4 = 1 – коэффициент учитывающий непостоянство зажимного усилия при механизированном приводе приспособления.
Если значение то принимаем . Если то принимаем его значение.
Определяем необходимое зажимное усилие:
С учётом коэффициентов получаем: Q = 14555 Н.
Определяем усилие привода: P=Q=14555 Н.
Определяем диаметр пневмоцилиндра:
где q – усилие пружины Н;
р – давление воздуха в пневмосети р = 01 МПа;
– КПД пневмосети = 085.
q = 015·РП = 015·14555 = 2183 Н;
По паспорту выбираем диаметр цилиндра: Dц = 80 мм. По диаметру цилиндра определяем диаметр штока: dшт = 25 мм.
Измерительная головка с одноточечным щупом
Исходные данные. Деталь «Корпус тяги». Требуется определить межоперационный и общий припуски и размер заготовки на поверхность «отверстие». Окончательные требования - отверстие 46Н8 шероховатость Ra = 16 мкм. Материал детали – АМ4. Общая длина детали – 20 мм. Метод получения заготовки - Литье. Обработка производится на вертикально-сверлильном станке.
Назначаем технологический маршрут обработки:
- растачивание предварительное
- растачивание окончательное
- развертывание предварительное
- развертывание окончательное.
Таблица 2.2 Расчет припусков на размер
Маршрут обработки поверхности
Элементы припуска мкм
Расчетный припуск мкм
Допуск по переходам в мкм
Предельные размеры мм
Предельные припуски мм
Растачивание предвар.
Развертывание предварительное
Развертывание окончательное
Результаты расчетов режимов резания представлены в картах технологического процесса
11 Автоматизированное проектирование технологического процесс изготов-
ления детали и средств технологического оснащения
Разработка технологических процессов в Компас – АВТОПРОЕКТ осуществляется в режимах:
- проектирование на основе технологического процесса-аналога (автоматический выбор соответствующего ТП из базы данных с последующей его доработкой в диалоговом режиме);
- формирование ТП из отдельных блоков хранящихся в библиотеке типовых технологических операций и переходов;
- объединение отдельных операций архивных технологий;
- автоматическая доработка типовой технологии на основе данных переданных с параметризированного чертежа КОМПАС–ГРАФИК (чертежно-конструктор-ского редактора);
- разработка ТП в режиме прямого документирования в диалоговом режиме с помощью специальных процедур к справочным базам данных.
В системе реализована процедура позволяющая проектировать сквозные технологии включающие одновременно операции механообработки штамповки термообработки сборки сварки и т.д.
В комплект разрабатываемой документации входят: титульный лист карта эскизов маршрутная маршрутно-операционная операционная карты ТП ведомость оснастки материалов и другие документы в соответствии с ГОСТ. В базовую поставку системы включены более 60 видов технологических карт. Они выполнены в среде MS Excel. Распечатывать их можно как в горизонтальном так и вертикальном исполнении. При необходимости пользователь может разрабатывать новые карты а также вносить изменения в существующие образцы. Эскизы и графическая часть технологических карт выполняются в среде КОМПАС–ГРАФИК и вставляются в листы MS Excel как OLE – объекты.
Для разработки документов произвольной формы используется специальный генератор отчетов также формирующий технологические карты в среде MS Excel.
Технологические процессы разработанные в КОМПАС–АВТОПРОЕКТ помещаются в архив системы в сжатом виде. Оглавление такого архива доступно для ручного просмотра и корректировки. Автоматический поиск ТП в архиве производится либо по коду геометрической формы детали либо по отдельным характеристикам: тип детали принадлежность к изделию вид заготовки габаритные размеры и т.д. По заданным критериям поиска система находит несколько ТП оставляя окончательный выбор за технологом.
Оглавлением архива разработанных технологических процессов служит база данных конструкторско-технологических спецификаций (КТС) включающих в себя уровни изделий узлов и деталей. Система обеспечивает свободное перемещение от одного уровня к другому позволяя при этом просматривать и редактировать состав изделий узлов и деталей. Каждый уровень имеет подчиненную таблицу «Документы» записи которой содержат ссылки на документы созданные в различных приложениях: графические текстовые файлы архивные технологи и т.д.
Выбор ТП осуществляется процедурой разархивации которая извлекает технологический процесс из архива и помещает его в рабочее поле КОМПАС–АВТОПРОЕКТ доступное для внесения изменений. Информация о текущем технологическом процессе распределяется по уровням: деталь – операция – переход.
Пользователю предоставлена возможность перемещаться по уровням отслеживать состав переходов по каждой технологической операции осуществлять необходимую корректировку. При этом технологический процесс находящийся в архиве не меняется. Модифицированная технология может быть помещена обратно в архив под прежним или новым именем.
Процедуры обработки КТС позволяют производить выборку деталей по принадлежности к изделиям сборочным единицам цехам изготовления и т.д. На их основе формируются сводные нормы заявки на материал комплектующие карты и другие технологические документы.
В системе реализованы процедуры позволяющие глобально корректировать любую информацию в архиве технологических процессов (например замена устаревших ГОСТов технологической оснастки) рассчитывать суммарную трудоемкость изготовления деталей и сборочных единиц определять материалоемкость и себестоимость изделия в целом.
Система обеспечивает удобную организацию баз данных и быстрый доступ к требуемой информации. Она обладает хорошо организованным диалоговым интерфейсом обеспечивающим легкое и наглядное перемещение по всем базам данных. Приемы работы с базами данных идентичны что упрощает их сопровождение. Программа поддерживает диалоговый доступ к сведениям об оборудовании инструментах материалах и т.д. В любой момент эти данные могут быть выведены на экран скорректированы или пополнены. В информационном пространстве КОМПАС–АВТОПРЕКТ можно создавать новые информационные массивы корректировать состав и размерность их полей. Взаимодействие между таблицами данных в КОМПАС–АВТОПРОЕКТ построено на динамически формируемых SQL-запросах. Операторы SQL генерируются либо автоматически либо по шаблону заданному пользователем. В базовую поставку системы входит около 3000 реляционных таблиц различной структуры и подчиненности.
Работа с базами данных организована в архитектуре клиент-сервер что исключает дублирование и обеспечивает защиту информации. В качестве SQL – серверов в КОМПАС–АВТОПРОЕКТ могут быть использованы InterBase MS SQL Oracle. Данные могут располагаться как на локальной станции так и на выделенном сервере. Имеющиеся у пользователя информационные массивы легко включаются в состав баз данных системы КОМПАС–АВТОПРЕКТ.
Одним из основных преимуществ КОМПАС–АВТОПРОЕКТ является возможность модернизации системы без участия разработчика самими пользователями. Корректируются состав и структура всех баз данных настраиваются формы технологических документов подключаются новые программные модули.
САПР КОМПАС–АВТОПРОЕКТ позволяет повысить производительность труда технолога сократить сроки и трудоемкость технологической подготовки производства. В состав данного интегрированного программного комплекса входят подсистемы проектирования технологий: механообработки штамповки сборки сварки термообработки покрытий гальваники.
В САПР КОМПАС–АВТОПРОЕКТ реализован механизм позволяющий отобразить структуру изделия (детали) взаимосвязи между оборудованием технологической оснасткой и методами обработки. Модель технологического процесса в САПР ТП занимает центральное место. В КОМПАС–АВТОПРОЕКТ – это трехуровневая цепочка связанных реляционных таблиц записи которых имеют различную логическую структуру. Такая модель является универсальной и настраиваемой. Она позволяет создавать технологии различных переделов и включать в них любые средства технологического оснащения в том числе и принципиально новые.
Вся информация о текущем технологическом процессе распределена по уровням «Деталь» - «Операция» - «Переход». Пользователю предоставлена возможность перемещаться по уровням отслеживать состав переходов каждой технологической операции вносить необходимые изменения на любом из уровней. Особенностью этой модели является наглядная форма представления информации. Записи таблицы «Переходы» содержащие тексты переходов режущие инструменты приспособления режимы резания и др. выводятся на экран одним списком. Такая возможность достигается тем что физические записи данного уровня имеют различную логическую структуру. Этот же механизм позволяет проектировать технологии включающие одновременно операции механообработки штамповки термообработки покрытий и т.д. Подключение нового технологического передела производится самим пользователем.
Одним из основных преимуществ КОМПАС–АВТОПРОЕКТ является возможность модернизации системы без участия разработчика. Корректируется состав и структура всех баз данных настраиваются формы технологических документов подключаются новые программные модули. Гибкость программного и информационного обеспечения позволяет быстро адаптировать систему к любым производственным условиям.
Разработка технологического процесса изготовления корпуса тяги
Разработка технологического процесса начинается с загрузки в рабочее поле системы режима «Технология» из раздела «Базы данных».
Перед началом разработки нового технологического процесса необходимо очистить поле текущей технологии (рисунок 2.3) произведя двойной щелчок на пиктограмме «Очистка технологии». Затем следует установить курсор на нужной записи и нажатием клавиши F12> запустить требуемый режим. Во всех таблицах текущей технологии будут удалены все записи.
Рисунок 2.3 – Режим очистки содержимого таблиц текущей технологии
Ввод данных начинается с таблицы «Деталь». Процесс ввода и редактирования полей записи на всех уровнях идентичен. Для загрузки формы просмотра и корректировки полей необходимо нажать на инструментальной панели кнопку «Редактирование записи» или клавишу F4>. Данная форма имеет следующую структуру: слева располагаются имена полей справа— их значения.
Данные можно вводить с клавиатуры установив курсор в заполняемом поле или копировать из справочной базы данных (БД). Признаком привязки такой БД к определенному полю записи является пиктограмма «Книга» справа от поля ввода данных. Справочные БД могут быть подключены к любому полю. Например в таблице «Деталь» к соответствующим полям подключены БД по материалам заготовкам наименованиям деталей и т.д.
Чтобы скопировать данные из БД следует подвести курсор к пиктограмме «Книга» щелчком левой кнопки мыши запустить справочную БД выбрать нужную строку произвести двойной щелчок мышью или нажать клавишу F12>. Система вернется в форму редактирования и скопирует информацию в нужные поля.
После того как введены все данные о детали необходимо выйти из формы редактирования нажав кнопку «Выход» или комбинацию клавиш Alt>+ F4>. На уровне Деталь должна появиться запись с данными о детали. Необходимую корректировку можно произвести не входя в режим редактирования F4>. Для этого нужно выделить курсором требуемое поле и начать ввод с клавиатуры непосредственно в ячейке таблицы. Отмена ввода— нажатие клавиши Esc>. Если к полю привязан справочный массив данных то в таблице с правой стороны появляется кнопка с пиктограммой «Многоточие».
Переход на уровень Операции осуществляется нажатием кнопки «Переход на следующую таблицу» на инструментальной панели или клавиши F12>. При начальном вводе таблица Операции не содержит записей. Необходимо зарезервировать нужное количество строк клавишей Insert>. Затем последовательно в каждую строку ввести информацию об одной технологической операции. Порядок следования операций в технологическом маршруте задается порядком расположения строк в таблице. Режим корректировки полей F4> осуществляет загрузку формы редактирования (рисунок 2.4) аналогичной использующейся на уровне Деталь.
Рисунок 2.4 – Структура записи таблицы «Операции»
После того как введены сведения об операциях можно вводить данные о переходах. Для этого следует установить курсор на нужную операцию и нажать клавишу F12>. Система перейдет к следующему объекту и в рабочее поле системы будет загружена таблица Переходы.
Поскольку таблицы Операции и Переходы связаны уникальным ключевым полем ID (генерируемым автоматически при каждом вводе новой операции) то каждая строка объекта Операции будет иметь подчиненный список записей в таблице Переходы. При первоначальном вводе она не содержит записей. Нужно зарезервировать необходимое количество пустых записей клавишей Insert> и войти в режим редактирования первой строки нажав клавишу F4>.
Справочная таблица Тип перехода содержащая список наименований доступных баз данных представлена на рисунке 2.5.
Рисунок 2.5 – Справочные базы данных таблицы «Переходы»
Выделить курсором нужную БД и двойным щелчком поместить ее в рабочее поле системы. Из загруженного справочника выбирать информацию последовательно нажимая клавишу F12>. При достижении последнего уровня все необходимые данные будут скопированы и система вернется в форму редактирования записи таблицы Переходы. В зависимости от вида выбранной информации на форме «Редактирование записи» меняются наименования полей. Так например если были выбраны данные о режущем инструменте (рисунок 2.6) поле «Переход» изменит свое название на «Режущий инструмент». Данный механизм реализуется с помощью специальных режимов управления логической структурой данных F3>.
Рисунок 2.6 – Выбор режущего инструмента из справочника КОМПАС-Автопроект
В поле дублирующей технологии могут помещаться как реальные ТП связанные с базой данных КТС так и типовые ТП доступ к которым осуществляется из режима «Архив типовых технологий» в КОМПАС-АВТОПРОЕКТ-Технология.
Технологический процесс может быть разработан на основе библиотеки типовых операций. Последовательность действий реализующих данный режим будет
рассмотрена для проектирования фрезерной операции ТП «Корпус тяги».
Рисунок 2.7 – Формирование переходов фрезерования плоскости
Подсистема «Сквозной ТП» позволяет сформировать технологию состоящую из операций и переходов. В режиме текущей технологии на уровне «Операции» при обращении к справочнику в отличие от других подсистем диалог начинается с выбора вида операции. После выбора требуемого и нажатии клавиши F12> загружается соответствующая база данных. Из базы данных выбирается всё необходимое и таким образом формируется технологический переход и весь ТП в целом.
Для просмотра созданной технологии используется «Дерево технологий».
Чтобы представить данные о техпроцессе в виде дерева необходимо произвести двойной щелчок мыши на пиктограмме с изображением дерева в области «Процедуры» режима «Технология функции». Стартует приложение treetex.exe на форму которого выводятся два технологических процесса. Реализован механизм копирования и перемещения данных между этими ТП. Технологические операции копируются из одной технологии в другую вместе с подчиненными таблицами.
Структура дерева включает четыре уровня:
- разделы: «Переходы» «Эскизы» «Карты» «Контроль» «Комментарии»;
- содержимое разделов.
Когда технологический процесс в поле текущей технологии сформирован и отредактирован можно переходить к разработке комплекта документации. Для этого необходимо щелкнуть мышью на пиктограмме с изображением карт в области Процедуры. Стартует программа формирования комплекта технологической документации. Результатом данной процедуры является комплект документов технологического процесса обработки резанием представленный приложением к выпускной квалификационной работе.
11.2 Разработка управляющей программы с виртуальным моделированием
обработки для станков с ЧПУ в САПР
Система Unigrafics NX 4 (модуль обработки) предназначена для разработки управляющих программ при изготовлении деталей высокой сложности на всех типах станков с ЧПУ.
Среди возможностей программы: собственный геометрический редактор для создания математических моделей деталей и агрегатов; импорт моделей из всех известных CAD-систем и их доработка в соответствии с конкретным инструментом применяющимся на оборудовании с ЧПУ; подготовка управляющих программ с использованием любых видов геометрических данных плоских эскизов чертежей и поверхностей. При импорте модели комбинация их с твердыми телами. Задание контурной или поверхностной заготовки произвольной формы и сравнения результата обработки с математической моделью для оценки точности изготовления. Также при использовании программы Un использование станочных циклов с их настройкой на любые УЧПУ; подготовка технологических эскизов и технологических карт; визуализация обработки и возможность редактирования управляющих программ. Программа позволяет подготавливать управляющие программы для токарных сверлильных фрезерных и других станков с ЧПУ.
Запускаем программу Unigrafics NX 4 (модуль обработки) (рисунок 2.8)
Рисунок 2.8 – Unigrafics NX 4 (модуль обработки) В верхнем выпадающем меню
Создаем программу для обработки плоских поверхностей детали PLANAR_MILL (смотри рисунки 2.9-2.16)
Рисунок 2.9 – Параметры программы PLANAR_MILL
Рисунок 2.10 – Параметры резания стратегия
Рисунок 2.11 – Параметры резания припуск
Рисунок 2.12– Параметры резания недорез
Рисунок 2.13– Выбор режущего инструмента.
Рисунок 2.14 – Обрабатываемая часть – два цилиндрических колодца.
Рисунок 2.15 – Отображение траектории с режущим инструментом
После задания всех необходимых параметров нажимаем кнопку «Генерировать» после чего система переходит в режим генерации управляющей программы.
Для создания управляющей программы в верхнем выпадающем меню нажимаем «Постпроцессор»
Рисунок 2.16 – Создания управляющей программы.
Ниже представлена управляющая программа для широкоуниверсального станка с ЧПУ «6Р13РФ-3» (операция 030 – «Фрезерная») разработанная при помощи системы автоматизированного проектирования технологических процессов Unigrafics NX 4 (модуль обработки).
Информация создана для пользов.: Корпус тяги
Дата: 14.04.2013 12:11:48
Текущая рабочая деталь: E:PROGRAMMA11.9603.3751.101cam.prt
Имя узла: Корпус тяги
============================================================
N4 G00 G90 X-185.4 Y-39.608 S0 M03
N7 G01 Y-50. Z0.0 F250. M08
N9 G03 X-183.678 Y-110.302 I-2.4 J0.0
N10 X-183.026 Y-109.815 I-.144 J-.487
N12 G02 X-182.451 Y-100.212 I-6.3 J0.0
N13 G03 Y-99.788 I.461 J-.212
N14 G02 X-183.026 Y-97.157 I-5.725 J-2.631
N16 G02 X-182.451 Y-.212 I-6.3 J0.0
N17 G03 Y.212 I.461 J-.212
N18 G02 X-183.026 Y2.843 I-5.725 J-2.631
N20 G03 X-183.678 Y10.302 I.508 J0.0
N21 X-185.4 Y8. I-.678 J2.302
N23 G02 X-185.908 Y-50. I.508 J0.0
N25 G03 X-191.7 Y-50.508 I0.0 J.508
N27 G03 X-183. Y-116.7 I-8.7 J0.0
N29 G03 X-176.726 Y-116.192 I0.0 J-.508
N31 X-174.341 Y-100.752
N32 G03 Y-99.248 I.659 J-.752
N33 G01 X-176.726 Y-97.157
N35 X-174.341 Y-.752
N36 G03 Y.752 I.659 J-.752
N37 G01 X-176.726 Y2.843
N39 G03 X-177.234 Y16.7 I.508 J0.0
N41 G03 X-191.7 Y8. I0.0 J8.7
N47 G01 Y-50.401 Z-3.
N49 G03 X-.92 Y-17.414 I.508 J.002
N51 G03 X-4.457 Y-17.92 I-.001 J.508
N54 G03 X-25.838 Y-35.796 I0.0 J.508
N56 X-25.834 Y-35.887
N58 X-25.803 Y-35.865
N59 X-25.796 Y-35.712
N63 G03 X-25.838 Y-64.796 I0.0 J.508
N65 X-25.834 Y-64.887
N67 X-25.803 Y-64.865
N68 X-25.796 Y-64.712
N71 G03 X-3.95 Y-82.586 I-.508 J-.002
N73 G03 X-.414 Y-82.08 I.002 J-.508
N76 G03 X-3.414 Y-43.705 I6. J0.0
N81 G01 X5.902 Y-93.911 Z5.861
N82 X6.2 Y-94.647 Z5.403
N84 X5.649 Y-92.229 Z3.396
N85 X5.054 Y-92.544 Z3.007
N86 X5.512 Y-93.194 Z2.549
N87 X5.902 Y-93.911 Z2.077
N88 X6.2 Y-94.647 Z1.619
N90 G02 X5.247 Y-92.44 I6.2 J-8.843
N91 X4.85 Y-92.481 I.247 J-.444
N92 G01 X-1.678 Y-90.467
N94 G02 X5.157 Y-92.693 I.149 J.486
N95 X6.165 Y-94.561 I8.69 J5.893
N96 X6.203 Y-94.738 I.47 J.194
N97 G01 X6.573 Y-105.499
N102 G03 X.142 Y-83.264 I.033 J.023
N103 G01 X.14 Y-83.265
N104 G02 X0.0 Y-83.3 I.14 J-.265
N106 G03 X-8.903 Y-83.808 I0.0 J.508
N108 G03 X-8.781 Y-87.195 I-.508 J-.001
N109 G01 X-8.728 Y-87.257
N111 G03 X-8.221 Y-98.586 I-.508 J-.002
N114 G03 X-3.025 Y-116.7 I-.508 J0.0
N116 G03 X16.7 Y-108. I0.0 J-8.7
N119 G03 X16.192 Y-8.157 I.508 J0.0
N121 G02 X6.2 Y-7.649 I0.0 J-.508
N126 G02 X6.165 Y-5.439 I.508 J-.017
N127 X5.157 Y-7.307 I9.698 J-4.025
N128 X4.886 Y-7.508 I.42 J-.285
N129 G01 X-1.678 Y-9.533
N131 G02 X5.247 Y-7.56 I-.15 J.485
N132 X6.006 Y-8.024 I5.247 J9.44
N133 X6.228 Y-8.385 I.282 J.422
N134 G01 X7.046 Y-15.07
N135 G03 X7.059 Y-15.138 I-.504 J-.061
N136 G02 X7.3 Y-17. I7.059 J1.862
N138 G02 X7.168 Y-84.383 I7.3 J0.0
N139 G03 X7.567 Y-84.978 I-.499 J.097
N140 G02 X8.99 Y-85.423 I1.367 J6.865
N141 G03 X9.7 Y-84.957 I-.202 J-.466
N143 G03 X8.99 Y-14.577 I.508 J0.0
N144 G02 X7.591 Y-15.017 I2.79 J-6.42
N145 X6.986 Y-14.581 I.101 J-.498
N146 G01 X6.27 Y-8.727
N147 G02 X6.774 Y-8.157 I-.504 J-.062
N149 G03 X16.7 Y-7.649 I0.0 J-.508
N152 G03 X8. Y16.7 I8.7 J0.0
N154 G03 X-3.533 Y16.192 I0.0 J.508
N157 G03 X-8.728 Y-1.92 I-.001 J.508
N159 X-8.797 Y-12.636
N160 G03 X-8.903 Y-12.945 I-.402 J.311
N162 G03 X-8.395 Y-16.7 I-.508 J0.0
N164 G02 X.172 Y-16.754 I0.0 J.3
N165 X.3 Y-17. I.172 J.246
N167 G02 X.172 Y-83.246 I.3 J0.0
Проектирование участка механического цеха начинают с расчета потребности в металлорежущем оборудовании. Оборудование механических цехов подразделяется на три категории: основное производственное (расчетное) дополнительное (нерасчетное) и вспомогательное. Потребности в основном оборудовании определяют по формулам. Если при расчете оборудования получается дробное число то оно округляется до единицы. Расчетное количество станков по -й группе оборудования определяется на основании трудоемкости производственной программы и действительного фонда времени работы оборудования [21]:
где – годовая программа выпуска деталей j-ого типа шт.; - штучное время обработки детали типа j на – коэффициент выполнения норм по – годовой эффективный фонд времени работы одного станка – количество наименований деталей обрабатываемых на i-й группе оборудования.
где – число рабочих дней в году; – число рабочих смен в сутки; – продолжительность рабочей смены ч; – плановые потери времени на ремонт % КП = 2-8 %.
Подставляя в уравнение (2.3.2) исходные числовые значения согласно заданию на дипломное проектирование находим:
В соответствии с разработанным маршрутным технологическим процессом и годовой программой выпуска деталей по формуле (2.14) определяем потребности в оборудовании по конкретным группам металлорежущих станков.
Станок фрезерный модели 6Р13РФ3:
Принимаем СП = 6 станков
Станок фрезерный модели 6Т13МФ4:
Принимаем СП = 4 станков
Средние коэффициенты загрузки оборудования по участку в целом Кзу и по группам Кзi рассчитываются по формулам [19]:
где m – число групп оборудования на участке.
Определим коэффициент загрузки оборудования по участку в целом составит:
Средний коэффициент загрузки оборудования по участку в целом K равен:
Подставив значения в формулу получим коэфциент загрузки оборудования
Результаты расчетов необходимого станочного оборудования а также их балансовую стоимость для наглядности представляем в виде таблице 2.2.
Таблица 2.2 – Расчет потребности участка механического цеха в технологическом оборудовании
Количество борудования
Рисунок 2.18 – График загрузки оборудования на участке изготовления корпуса тяги
Штат механического цеха состоит из основных и вспомогательных рабочих инженерно-технических работников служащих младшего обслуживающего персонала работников технического контроля. Численность основных рабочих можно определять по формулам. Количество остальных работников цеха принимается по соответствующим установленным нормам в процентах от основных производственных рабочих.
В среднесерийном производстве численность основных рабочих для выполнения нормируемых работ определяется по формуле [21]:
где – трудоемкость – годовой объем выпуска изделий j-ого вида шт.; – действительный годовой фонд времени работы рабочего ч; – коэффициент выполнения норм на i-й операции.
где - коэффициент учитывающий потери рабочего времени – неявки установленные трудовым законодательством (10-12%).
Принятое количество рабочих устанавливается путем соответствующего округления полученного значения Чор до целого.
Определим число операторов фрезерного станка (ст. 6Р13РФ3):
Принимаем число операторов станков с ЧПУ: 6 человек.
Определим число операторов фрезерного станка (ст. 6Т13МФ4):
Принимаем число операторов станков с ЧПУ: 4 человек.
Принимаем количество основных рабочих равным 10 человек.
Расчет потребного количества основных рабочих оформлен в виде таблицы 2.3.
Таблица 2.3 - Расчет потребного количества основных рабочих
Количество рабочих чел.
Фрезеровщики (ст. 6Р13РФ3)
Фрезеровщики (ст. 6Т13МФ4)
В таблице 2.4. в соответствии с рекомендациями [19] представлен необходимый перечень вспомогательных рабочих проектируемого участка.
Таблица 2.4 - Ведомость вспомогательных рабочих
Окончание таблицы 2.4
Определяющий показатель
Норма обслужив. на 1 раб.
Слесарь по рем. оборуд.
Кол-во ед. об. в см.
Слесарь по рем. Оснастки
Кол-во осн. Рабочих
Слесарь по межрем. обсл.
Ед. оборуд. на человека
Подносчик и раздатчики инструмента
Распределители работ
Количество основных рабочих
Процент от осн. Раб.
Уборщик произв. Площ.
Водители электрокаров и автопогрузчиков
Количество тонн груза в смену
при массе детали до 1 кг
Производственная площадь участка занятая непосредственно оборудованием и рабочими местами определяется из удельной приходящейся на один станок и числа основных станков [19].
Удельная площадь на один мелкий станок – 10-12 м2 средний – 15-25 м2 крупный – 30-45 м2.
К мелким относятся станки с габаритами 1800800 мм средним – до 40002000 мм крупным – до 80004000 мм [19].
Производственную площадь участка Sпр находят по формуле [21]:
где Sу – удельная площадь на один станок м2; n – число станков.
Общая площадь участка (производственная вспомогательная служебно-бытовая) в укрупненных расчетах принимается 12 от производственной площади.
В единичном и серийном производствах цеховой склад заготовок и полуфабрикатов размещают в начале пролетов в соответствии с обрабатываемыми деталями. Для хранения крупных заготовок склады располагают на специальных открытых или закрытых эстакадах для хранения 2÷3-х дневного запаса заготовок. Хранение штучных грузов (отливок поковок деталей и т.д.) должно производиться в унифицированной таре которая позволяет использовать механизированные погрузочно-разгрузочные транспортирующие устройства и многоярусное хранение в штабелях или на стеллажах. Запас материалов и заготовок в цеховом складе должен быть невелик так как назначением его является только обеспечивать регулярное снабжением цеха (участка) материалами. При расчете площади складов заготовок исходят
из необходимости запаса и грузонапряженности пола [9]:
где Р – площадь складов заготовок м2;
Q – масса заготовок обрабатываемых в цехе в течение года т;
Т – запас заготовок дни;
f – среднее число рабочих дней в году;
q – средняя грузонапряженность склада тм2;
кр – коэффициент использования площади склада представляющий отношение полезной площади склада к его общей площади и учитывающий проходы и проезды (кр = 04÷05).
Q = 2400×192 = 46080 кг = 4608 т.
Произведём расчёт по формуле (2.31)
P = 4608×5253×25×04 1 м².
Склад готовых деталей предназначен для хранения деталей перед отправкой на сборку. Склад готовых деталей и комплектовочный склад размещают в конце пролетов механического цеха на пути следования деталей на сборку. Площадь склада готовой продукции определяется также как и общая площадь под заготовки и материалы. Грузонапряженность площади пола складов принимается меньшей чем в цеховом складе заготовок так как готовые детали хранятся как правило на стел- лажах или специальных подставках столах и таре. Допускаемую грузонапряженность следует принимать равной: при удельном весе материалов более 1÷4 т на 1 м2 для мелких и средних деталей и 15 т на 1 м2 для крупных; при удельном весе материалов до 4 т – соответственно 04 и 06 на 1 м2.
Q = 2400×62= 14880 = 1488 т; P = 1488×7253×25×04 05 м².
При разработке схемы участка необходимо учесть что предметно замкнутые участки имеют как правило ячеистую структуру то есть оборудование предназначенное для выпуска однотипных изделий или семейства конструктивно и технологически сходных деталей группируются в одном месте ячейке. Такое построение участка дает возможность расставить все оборудование по ходу технологического процесса сохранить путь движения деталей и обеспечить передачу их с операции на операцию без завоза на склад [19].
Состав производственных отделений и участков механических цехов определяется характером изготовляемых изделий технологическим процессом объемом и организацией производства.
Станки на участке располагаем последовательно в соответствии с технологическими операциями. Последовательный переход детали со станка на станок образует технологическую линию движения детали.
При разработке плана размещения станков следует координировать их расположение относительно колонн; этим достигается возможность точного определения места каждого станка независимо от положения других станков. При расстановке станков надо руководствоваться нормальными размерами промежутков (разрывов) между станками и поперечных направлениях и размерами расстояний от стен и колонн. Эти размеры должны гарантировать удобство выполнения работ на станках безопасность рабочих достаточную свободу движения людей и транспортных средств с грузом возможность выполнения ремонта. Разрывы между станками регламентируются правилами охраны труда и существующими нормативами которые учитывают удобство эксплуатации станков.
Расстояние между станками с ЧПУ при поперечном расположении к проезду "в затылок" - 900 мм. Расстояние от стены здания до боковой стороны станка – 800 мм [6] с.119 табл.10. У каждого металлообрабатывающего станка расположено место для складирования деталей. В начале участка механического цеха предусматриваем ворота.
Технологические требования к помещению участка.
К помещениям с термоконстантным режимом в зависимости от характера и точности выполняемых работ предъявляются технологические требования в части температурного режима относительной влажности чистоты воздуха и компоновочных решений.
Согласно ГОСТ 9249-59 нормальная температура для линейных и угловых измерений +200С. Допустимые отклонения от нормальной температуры не должны превышать 10С. Относительная влажность воздуха в помещениях должна быть в пределах 40-60%. Допустимая скорость движения воздуха не более 05 мс [6].
Кроме указанных требований при компоновке термоконстантных производств необходимо руководствоваться следующим:
- помещения с термоконстантным режимом должны иметь минимальное число дверей ворот и наружных стен;
- недопустимо размещение вблизи термоконстантных помещений оборудования вызывающего вибрацию (компрессоры молоты и др.);
- промежуточные кладовые для хранения точных деталей на стадии финишной обработки склад готовых деталей а также кладовые инструментов и приспособлений должны размещаться в помещении с термоконстантным режимом.
При проектировании участка механического цеха необходимо предусмотреть мероприятия по соблюдению правил охраны труда и техники безопасности. К основным из них относятся [6 с.127-129]:
- точное соблюдение норм технологического проектирования которыми предусматриваются нормальные расстояния между оборудованием проходы и проезды обеспечивающие снижение травматизма на участке;
- максимально возможная механизация производственных процессов посредством применения станков с ЧПУ и подъёмно-транспортных средств сокращающих ручной труд и обеспечивающих безопасность работы.
Согласно СНиП – 2.М2-72 проектируемый участок по категории пожаро- и взрывоопасности относится к категории Д кроме отдельных помещений (в которых располагаются установка для удаления заусенцев и моечная машина) относящихся к категории В [6 с.128] табл. 20.
Основываясь на произведённых расчётах и учитывая приведённые выше рекомендации выполняем планировку участка механического цеха по обработке корпуса тяги (см. графическую часть дипломного проекта)
Организация ремонта технологического оборудования на участке
Рассмотрим порядок организации ремонта и технического обслуживания оборудования на участке по обработке корпуса тяги. Современные машиностроительные предприятия оснащаются дорогостоящим и разнообразным оборудованием автоматизированными комплексами в частности станками с ЧПУ. Для бесперебойной работы оборудования с заданными точностными характеристиками требуется систематическое техническое обслуживание выполнение ремонтных работ и мероприятий по его технической диагностике . Более подробно рассмотрим смазочные материалы для станка с ЧПУ.
Смазка станка периодичность материалы Для станка с ЧПУ(6р13рф3) .
Система смазки состоит из двух систем:
Система автоматической централизованной дозированной смазки опор качения всех подвижных узлов шариковых чаек шестерён коробки скоростей подшипника поворота стола.
Система периодической консистентной смазки подшипников зубчатых зацеплений.
Применяемые масла и их заменители.
Жидкие смазки: Индустриальное И12А Турбинное 22П; Индустриальное И20А; Индустриальное И12А; Индустриальное И20А
Консистентная смазка: Циатим - 203 Литол 24
Организация ремонтного хозяйства и техническое обслуживание оборудования базируются на системе планово-предупредительных ремонтов. Системой планово-предупредительных ремонтов оборудования называется совокупность запланированных организационных и технических мероприятий по уходу надзору за оборудованием его обслуживанию и ремонту. Основная цель этих мероприятий – предотвращать прогрессивно нарастающий износ предупреждать аварии и поддерживать оборудование в состоянии постоянной готовности к работе. Эта система включает в себя техническое обслуживание и плановые ремонты – текущий и капитальный.
Техническое обслуживание – это комплекс операций по поддержанию работоспособности оборудования при использовании его по назначению при хранении и транспортирования. В процессе технического обслуживания периодически повторяющиеся операции-осмотры промывки проверки на точность – регламентированы выполняются по заранее разработанному графику. Кроме того производственные рабочие слесари электрики смазчики повседневно наблюдают за состоянием оборудования соблюдают правила его эксплуатации устраняют возникающие мелкие неисправности. Некоторые операции регламентированного технического обслуживания могут быть совмещены по времени например смена масла с осмотрами.
Текущий ремонт производится в процессе эксплуатации оборудования. При этом виде ремонта заменяются и восстанавливаются отдельные части оборудования и выполняется регулировка его механизмов. Цель такого ремонта – обеспечение работоспособности оборудования и выполнение регулировок до очередного планового ремонта. Капитальный ремонт осуществляют для восстановления полного или близкого к полному ресурса. Обычно он сопровождается модернизацией оборудования.
Ремонты вызываемые отказами и авариями оборудования называются внеплановыми или аварийными. При хорошо организованной системе обслуживания ремонта и высокой культуре эксплуатации оборудования необходимости в неплановых ремонтах как правило не возникает.
Система ремонта и технического обслуживания в зависимости от характера и условий эксплуатации оборудования может функционировать в различных организационных формах:
-в виде послеосмотровой системы;
-в виде системы периодических ремонтов;
-в виде системы стандартных ремонтов.
При системе послеосмотровых ремонтов по заранее разработанному графику выполняется осмотр оборудования в процессе которого устанавливается его состояние и составляется ведомость дефектов. На основании данных осмотра определяются сроки и содержание предстоящего ремонта.
Система периодических ремонтов и нормативная её часть положены в основу типовой системы технического обслуживания и ремонта металлообрабатывающего оборудования. При этой системе планируются сроки и объёмы ремонтных работ всех видов. Фактический объём работ корректируется при осмотре. Эта система находит наиболее широкое применение в машиностроении.
При системе стандартных ремонтов объём и содержание их планируются и строго соблюдаются независимо от фактического состояния оборудования. Эта система базируется на точно установленных нормативах и применяется к оборудованию внеплановая остановка которого недопустима.
Нормативы типовой системы дифференцируются по группам оборудования. Важнейшими из них являются: ремонтные циклы и их структура категории сложности ремонта трудоемкость и материалоемкость ремонтных работ запас деталей узлов и агрегатов. На основе расчетов этих нормативов разрабатывают годовые графики планово-предупредительных ремонтов определяют трудоемкость предстоящих работ и устанавливают штат ремонтного персонала.
Ремонт и техническое обслуживание технологического оборудования на машиностроительных предприятиях осуществляют ремонтно-механические цехи и ремонтные службы цехов. В зависимости от доли работ выполняемых производственными ремонтно-механическими цехами и цеховыми ремонтными службами различают три формы организации ремонта:
-децентрализованная;
При централизованной форме все виды ремонта производит ремонтно-механический цех предприятия.
При децентрализованной – ремонт выполняется силами цеховых ремонтных баз. На этих же базах изготовляют новые и восстанавливают изношенные детали.
При смешанной форме наиболее трудоёмкие работы проводятся в ремонтно-механическом цехе а техническое обслуживание и текущие ремонты – силами цеховых ремонтных баз комплексными бригадами слесарей закрепляемых за отдельными участками.
Основными направлениями совершенствования ремонтного хозяйства являются: внедрение прогрессивных методов технологических процессов и организационных форм выполнения работ применение современных средств технической диагностики состояния оборудования комплексная механизация работ внедрение технологических процессов заводская аттестация работ специализация бригад ремонтников по типам оборудования.
1 Исследование процесса заточки фрез для станков 6Р13РФ3 6Т13МФ4
Инструмент при воздействии на деталь со временем притупляется и его необходимо периодически затачивать в научно исследовательской части я рассмотрел заточку фрез для станков(6Р13РФ3 6Т13МФ4).
Одним из важнейших условий обеспечивающих эффективное использование кругов из синтетических алмазов и кубического нитрида бора является применение смазочно – охлаждающих жидкостей (СОЖ). Современные СОЖ могут быть представлены тремя основными группами:
)минеральные масла различной вязкости в которые в зависимости условий их применения добавляется ряд специальных присадок;
) масляные эмульсии которые получаются в результате растворения эмульсола в воде;
)синтетические или химические жидкости.
Способность СОЖ влиять на характер процесса шлифования инструментальных материалов является результатом ее смазочного моющего и охлаждающего действий.
Смазочное действие СОЖ влиять проявляется главным образом в том что жидкость взаимодействуя с рабочей поверхностью круга и шлифуемой поверхностью создает на них поверхностные планки различного типа. Свойства смазочных пленок зависят от ингредиентов входящих в состав СОЖ и совокупности физико – механических и физико – химических свойств связки круга зерен абразива и обрабатываемого материала. Чаще всего различные смазочные пленки образуются и действуют одновременно но какой – то определенный вид как правило оказывает наиболее сильное влияние на характер взаимодействия связки круга сверхтвердого абразивного зерна и обрабатываемого материала.
Моющее действие СОЖ представляет собой ее способность предотвращать наличие отходов шлифования на связку круга и зерна абразивного материала и удалять отходы из зоны шлифования. При недостаточной моющей способности рабочая поверхность круга заволакивается отходами шлифования.
Охлаждающее действие СОЖ выражается в отводе тепла образующегося в зоне шлифования.
Чрезмерный нагрев при шлифовании снижает точность обработки изменяет физико – механические свойства шлифуемого материала.
Для реализации названных функциональных свойств СОЖ большое значение имеет ее проникающая способность особенно в условиях длительного непрерывного контакта шлифуемого инструмента с абразивным кругом (например при упругом шлифовании). Она зависит от двух факторов:
) степени растекания жидкости по поверхности контактирующего с ней твердого тела;
) сцепляемости (смачиваемости) жидкости с этой поверхностью.
Рассмотрим на конкретных примерах как влияют различные составы СОЖ на основные технологические показатели процесса шлифования твердых сплавов и быстродействующих сталей кругами из синтетических алмазов и кубического нитрида бора. В число испытанных СОЖ входили жидкости трех групп:
а) водные растворы электролитов и поверхностно – активных веществ;
При шлифовании твердых сплавов кругами из синтетических алмазов на металлических и органических связках лучшие результаты по производительности обработки удельному расходу алмазов и качеству обрабатываемых поверхностей получены при применении в качестве СОЖ водных растворов поверхностно – активных веществ и низко концентрированных эмульсий. При исследовании влияния СОЖ на алмазных кругах на металлической связке МО 13 при шлифовании твердого сплава ВК 6 в условиях жесткой заточки наименьшей удельный расход алмазов получен при применении 3% -й эмульсии замасливателя Б 8 1%-го водного раствора кальцинированной соды.
При определении влияния состав СОЖ на удельный расход алмазов при жесткой обработке твердого сплава ВК 6 совместно со стальной державкой алмазными кругами на керамической связке К 1 лучшими СОЖ при этом
оказывались 1%-ный водный раствор кальцинированной Соды и неконцентрированные эмульсии из эмульсола НГЛ -25 и замасливателя БВ.
При шлифовании быстрорежущих сталей кругами из синтетических алмазов и кубонита наиболее эффективными оказались СОЖ имеющие в своем составе сульфированное касторовое масло.
Лучшие результаты по производительности шлифования и удельному расходу алмазов а также рекомендации по назначению эффективных составов СОЖ для конкретных условий обработки с учетом применения рациональных режимов шлифования и оптимальных характеристик кругов из синтетических алмазов и кубонита на основании проведенных исследований сводим в таблицы 4.1 и 4.2.
Таблица 4.1 – СОЖ для алмазной обработки твердосплавного инструмента
Заточка твердосплавной части с касанием по стальной стружке
) 15 – 3%-ная эмульсия из эмульсола НТЛ 205 или замасливателя;
) 05 – 1% -ный водный раствор кальцинированной соды (Na2CO3).
Заточка твердосплавной части вместе со стальной державкой
Составы 1 или 2 или состав (%):
кальцинированная сода – 10; триэтаноламин (С6Н15О3N) – 10;
бура (Na2B2O7 10H2O) -03; вазелиновое масло (ГОСТ 3164-52)- 005;остальное вода
Заточка и доводка твердосплавной части
Состав (%): тринатрий фосфат
(Na3PO4)006; ализариновое масло – 05; бура – 025; азотистокислый натрий – 025; остальное вода
Осерненное масло «Индустриальное 12» (на 10 л масла 80г серы)
Таблица 4.2 – СОЖ для обработки инструмента из быстрорежущих сталей кругами из синтетеческих алмазов и кубонита
Доводка алмазными кругами
) 15 - 3%-ная эмульсия замасливателя БВ;
) Состав: триэтаноламин – 06;
бура – 025; азотокислый натрий-025; ализированное масло – 05; вода
Заточка кругами из кубонита
) Состав (%): триэтаноламин – 06; ализированное масло – 05;
азотокислый натрий – 025;бура –
) Состав (%): тринатрий фосфат – 06; бура -025; азотисто – кислый натрий -025; ализированное масло;
) 03 – 05% водный раствор азоткислого натрия
Резьбошлифование кругами из кубанита
Осерненное масло «Индустриальное 12» (на 10 л масла 80 г серы)
1.1 Определение потребности в инвестициях для организации спроектиро
Создание предметно-замкнутого участка требует затрат на технологическую подготовку производства закупку установку и наладку технологического энергетического подъемно-транспортного оборудования технологическую оснастку инвентарь и хозяйственные принадлежности а также затрат на производственную площадь.
Капиталовложения в оборудование рассчитываются по формуле [4]:
где - капиталовложения соответственно в технологическое оборудование энергетическое оборудование подъемно-транспортное оборудование в средства контроля и управления.
Вложения в технологическое оборудование определяются так [4]:
где – оптовая цена единицы оборудования
- коэффициент транспортно - заготовительных расходов соответственно для тяжелого и легкого оборудования;
- коэффициент учитывающий затраты на строительные работы в том числе устройство фундаментов ;
- коэффициент учитывающий затраты на монтаж и наладку оборудования от оптовой цены оборудования.
Оптовые цены единицы оборудования: станок фрезерный 6Р13РФ3 – 1800 тыс. р станок фрезерный 6Т13МФ4 – 2000 тыс. р.
Укрупненно капиталовложения в энергетическое оборудование принимаются равными 5-20 % от стоимости технологического оборудования:
Капиталовложения в подъемно-транспортное оборудование принимаются равными 10-15 % от стоимости технологического оборудования:
Капиталовложения в средства контроля и управления технологическим процессом принимаются равными 1 % от стоимости технологического оборудования [25]:
Капиталовложения в оборудование равны:
Затраты на технологическую оснастку при укрупненных расчетах можно принять в размере 7-10 % от стоимости технологического оборудования [4]:
Вложения в инвентарь и хозяйственные принадлежности долговременного пользования принимаются в размере 3-5 % от стоимости технологического оборудования [25]:
Капитальные вложения в здания определяются по формуле [4]:
где - стоимость 1 м2 здания р;
- площадь участка который определяется исходя из его планировки.
Результаты расчета капитальных вложений в основные производственные фонды участка оформлены в виде таблицы 5.1.1. В нее занесены рассчитанные по каждой группе основных фондов годовые суммы амортизационных отчислений. Нормы амортизационных отчислений взяты из справочной литературы [16].
Таблица 5.1 – Сводная ведомость капитальных вложений
Виды основных фондов
Кол-во ед. оборуд. шт.
Балансовая стоимость ед. оборуд. тыс. р
Балансовая стоимость основн. фондов тыс. р
Годовые амортиз. отчисл. тыс. р
Окончание таблицы 5.1
Энергетическое оборудование
Подъемно - трансп. оборудов.
Средства контр. и управления
Технологич. Оснастка
Инвентарь и хоз. принадлежности
Расходы на подготовку и освоение производства (Рпу) включают: затраты на освоение нового участка т.е. пусковые расходы; на разработку технологического процесса; на проектирование средств технологического оснащения и др.
Данные расходы переносятся на себестоимость изделия равными долями в течение двух лет. Списание Рпу на себестоимость продукции можно осуществить пропорционально заработной плате основных производственных рабочих. Для этих целей рассчитывается величина Кпо:
где Рпу – общая сумма затрат на подготовку производства на проектируемом участке тыс. р.;
Форо – фонд основной зарплаты основных производственных рабочиучастка на год тыс. р.
Рпу = Роу+Ртпп (5.5)
где Роу – затраты на освоение нового участка (пусковые расходы);
Ртпп – затраты на проектирование ТП и приспособлений.
Затраты на проектирование ТП и приспособлений рассчитываются по трудоемкости проектных работ и стоимости 1 человеко-часа работы разработчиков.
Определим расходы на технологическую подготовку производства исходя из трудоемкости проектных работ. Укрупнено они определяются по формуле:
Ртпп = tТПиОр·СНZ (5.6)
где tТПиОр - норма времени на разработку и внедрение технологического процесса и конструирование технологической оснастки;
С - стоимость одного человеко-часа р.
Таблица 5.2 – Нормы времени на разработку и внедрение технологического процесса и конструирование технологической оснастки
Отработка детали на технологичность
Разработка операционного ТП
Конструирование универсально-наладочных и
контрольных приспособлений
Конструирование режущего и вспомогательного
Стоимость 1 человеко-часа рассчитывают исходя из среднемесячной заработной платы технологов и конструкторов с учетом начислений на нее и номинального фонда времени работы в месяц.
где ЗП – среднемесячная заработная плата технологов и конструкторов с учетом всех начислений на неё р.;
Фном – номинальный фонд рабочего времени в месяц ч.
На разработку технологического процесса и конструирование оснастки для клина центрального приходится
Ртпп = 415·845 = 350675 р. = 350675 тыс. р.
Затраты на освоение нового участка складываются из следующих калькуляционных аналитических статей:
Роу = Рпсд + Рпн р + Рсп + Рп (5.8)
где Рпсд – разработка проектно-сметной документации;
Рпн р – расходы на пусконаладочные работы и по комплексному опробованию оборудования;
Рсп – содержание персонала занятого на пусконаладочных работах;
Рп – прочие расходы.
В связи с тем что участок создаётся на уже имеющихся площадях при действующем производстве пусковые расходы связаны с установкой и подключением оборудования к имеющимся энергосетям. Т.о. затраты на установку подключение и наладку оборудования (металлорежущего энергетического подъёмно-транспортного) составляют 3 % от их стоимости.
Общая сумма затрат на подготовку производства на проектируемом участке
Рпу = 2889936+7913=2969066 тыс. р.
Процент расходов на содержание и эксплуатацию оборудования определяется по формуле:
где – расходы на содержание и эксплуатацию оборудования участка на год;
Ф°ор – фонд основной зарплаты основных производственных рабочих участка за изготовление партии в 34000 деталей на год тыс.р.;
– коэффициент загрузки оборудования на участке. 1749792
Фонд зарплаты складывается из основной и дополнительной зарплаты; в основную входят тарифный фонд и различного рода доплаты большую часть которых составляет премия [4].
Тарифный фонд основных производственных рабочих-сдельщиков определяется как сумма расценок по операциям умноженная на годовую программу:
где - расценка на изделие типа j р;
где - сдельная расценка по операции
- коэффициент учитывающий многостаночность работы можно принять = 1.
где - часовая тарифная ставка соответствующая разряду операции i рч. Расчет расценок на изготовление детали оформлен в виде таблицы 5.3. Часовые тарифные ставки по разрядам работ принимаем по данным базового предприятия: ставка пятого - =5318 р.ч. Таблица 5.3 – Расчет сдельных расценок на деталь
Доплаты составляют 50 % от [20] что соответственно равно 53060 тыс.р. Итого основная зарплата основных производственных рабочих равна
Дополнительная зарплата принимается в размере 10 % от основной [10]:
Тарифный фонд заработной платы рабочих-повременщиков р. определяют по формуле:
где Чп – численность рабочих-повременщиков чел.; – часовая тарифная ставка 1-го разряда р.ч.; – средний тарифный коэффициент рабочих- повременщиков;
Таблица 5.4 – Часовые ставки вспомогательных рабочих
Тарифный коэффициент
Часовые ставки руб.ч
где Чп Kiп – тарифный коэффициент рабочих–повременщиков i-го разряда.
Определяем средний тарифный коэффициент рабочих-повременщиков:
Тарифный фонд заработной платы рабочих-повременщиков:
Доплаты составляют 50 % от что соответственно равны 202482 тыс.р.
Итого основная зарплата вспомогательных рабочих равна:
Дополнительная зарплата принимается в размере 10 % от основной [16]:
При расчете численности аппарата управления следует пользоваться следующими примерными нормативами. В подчинении мастера должно быть 20÷25 рабочих; старший мастер назначается для руководства не менее чем для двух мастеров (участка или сменными).
Таким образом фактическое количество и состав аппарата управления участком механической обработки корпуса станочного приспособления:
На 6 человек основных рабочих: 025 мастера из расчёта 1 мастер на 24 чел соответственно старший мастер 0175.
Таблица 5.5 – Штатное расписание аппарата управления участком
Количество на участке (факт.) чел.
Результаты расчета фондов заработной платы различных категорий работников представлены в таблице 5.6.
Таблица 5.6 – Результаты расчета фондов заработной платы различных категорий работников
Фонд основной зп тыс. р.
Среднемесячная зп 1 работающего
Смета расходов на содержание и эксплуатацию оборудования включает следующие статьи: амортизация оборудования эксплуатация оборудования расходы по содержанию и эксплуатации транспорта износ малоценных и быстроизнашивающихся инструментов и приспособлений прочие расходы.
Расходы на амортизацию МРС энергетического и подъёмно-транспортного оборудования
Ра =153672+5046+383=197018 тыс. р.
Расходы на эксплуатацию оборудования включают в себя: затраты на вспомогательные материалы потребляемые в процессе эксплуатации оборудования; затраты на силовую энергию потребляемую для привидения в движение производственных машин; затраты на сжатый воздух для эксплуатации оборудование; затраты на воду для производственных нужд; затраты на основную плату вспомогательных рабочих обслуживающих оборудование.
Затраты на вспомогательные материалы Мвт принимаются в размере 5 % от стоимости технологического оборудования Кот.
Затраты на силовую энергию считаются по формуле [10]:
где – суммарная установленная мощность электродвигателей оборудования кВт;
– коэффициент загрузки оборудования по времени Кв = 04-07;
– коэффициент загрузки электродвигателей по мощности Км= 05-08;
– коэффициент учитывающий потери электроэнергии в сети завода Кпс = 104-108;
- средний коэффициент полезного действия электродвигателей оборудования = 065;
– цена 1 кВт-ч электроэнергии р.
Затраты на сжатый воздух определяются как произведение годового расхода сжатого воздуха из расчета 5 м3 на один станок в смену на цену 1 м3 сжатого воздуха [20]:
где - количество воздуха его объем приходящийся на один станок в смену ;
- цена 1 м3 сжатого воздуха; = 1955 р м3.
Затраты на воду рассчитываются по формуле [10]:
где - средний расход воды на один металлорежущий станок в час ;
Затраты на основную и дополнительную заработную плату вспомогательных рабочих обслуживающих оборудование с начислениями на социальные нужды определяются укрупнённо в размере 30 % от годового фонда заработной платы и начислений на социальные нужды всех вспомогательных рабочих:
где – коэффициент начислений на социальные нужд
Расходы на текущий ремонт металлорежущего оборудования транспортных средств технологической оснастки и энергетического оборудования составляют 15 % от балансовой стоимости указанных средств.
Расходы на содержание и эксплуатацию транспортных средств принимают в размере 5% от стоимости транспортных средств.
Расходы на износ малоценных инструментов и приспособлений определяется укрупненно из расчета 50 тыс. р. на один станок в год.
Прочие расходы составляют 3% от общей суммы затрат по перечисленным выше статьям.
Рпр = 003·4531293 = 136 тыс. р.
Смета расходов на содержание и эксплуатацию оборудования представлена в таблице 5.7.
Таблица 5.7 – Смета расходов на содержание и эксплуатацию оборудования
Амортизация оборудования.
Эксплуатация оборудования:
- затраты на вспомогательные материалы;
- затраты на силовую энергию;
- затраты на сжатый воздух;
- затраты на воду для производственных нужд;
- затраты на основную и дополнительную заработную плату вспомогательных рабочих обслуживающих оборудование с начислениями на социальные нужды.
Расходы на текущий ремонт оборудования.
Расходы на содержание и эксплуатацию транспорта.
Расходы на износ малоценных и быстроизнашивающихся инструментов.
Расчет себестоимости а также общие годовые расходы на производство детали изготавливаемой по спроектированной технологии сводим в таблицу 5.8 [4].
Таблица 5.8 - Калькуляция себестоимости детали.
где НР – норма расхода материала на изделие НР = 05 кг;
ЦМ – оптовая цена материала ЦМ = 125 ркг.
где Но – норма отходов на деталь Но = 066 кг;
Цо – цена отходов ркг Цо = 12 ркг
Основная заработная плата основных производственных рабочих
Д = 05·Риз=05·5146 = 268 рдеталь.
Дополнительная зп основных производственных рабочих
Начисления на социальные нужды
Ос = (7719+772)· 0277 = 2352
Расходы на подготовку производства
Расходы на содержание и эксплуатацию оборудования
где – процент расходов на содержание и эксплуатацию оборудования
Износ инструментов и приспособлений целевого назначения и прочие специальные расходы
где Рсп – цена оснастки
Окончание таблицы 5.8
Кцр – процент цеховых расходов Кцр = 125%.
себестоимость изготовления детали:
Сц = Мо – Ов + Зо + Зд + Ос + Рсэо +
Сц=15875-792+7719+772+2352
+798145+19560+2361+9649
Общехозяйственные расходы
где Крх – коэффициент общехозяйственных расходов по данным ВМЗ Крх = 320 %.
Производственная себестоимость изготовления детали
Коммерческие расходы
где Кком – коэффициент коммерческих расходов Кком = 8 %.
Полная себестоимость изготовления детали
Годовые текущие издержки участка определяют по формуле [4]:
где - годовая программа выпуска изделий шт.
Технико-экономические показатели проектируемого участка в составе механического цеха приведены в таблице 5.9 [16].
Таблица 5.9 - Технико-экономические показатели проектируемого участка
Наименование показателей
Величина показателя по участку
Абсолютные показатели
1 Годовой выпуск продукции:
в натуральном выражении шт.
в стоимостном выражении тыс.р
2 Количество единиц технологического оборудования
3 Общая стоимость основных производственных фондов тыс.р
4 Общая площадь участка м2
5 Численность основных рабочих чел.
6 Фонд заработной платы основных рабочих тыс.р
Относительные показатели:
1 Выпуск продукции на одного производственного рабочего
в денежном выражении тыс.р чел.
2 Выпуск продукции на кв.м производственной площади тыс.ркв.м
4 Средняя загрузка оборудования %
5 Фондовооруженность труда тыс.р чел.
6 Уровень механизации труда %
Экономический эффект от функционирования участка на котором детали изготавливаются по вновь спроектированной технологии рассчитывается на конкретный период. Исходя из темпов обновления промышленной продукции в состав которой входит изготавливаемая деталь принимаем этот период равным одному году.
Экономический эффект реализации проекта участка за расчетный период может быть определен по формуле [25]:
где - неизменная по годам расчетного периода стоимостная оценка результатов производства продукции с использованием разработанного технологического процесса р;
- неизменные по годам расчетного периода затраты на продукцию с применением разработанного технологического процесса р;
- норма реновации исчисленная для периода использования проектируемой технологии; ;
- норматив приведения разновременных результатов и затрат численно равный нормативу эффективности капитальных вложений .
Величина определяется по формуле [25]:
где - оптовая цена детали производимой на спроектированном участке р;
- коэффициент рентабельности к себестоимости продукции; ;
- годовая программа выпуска деталей шт.
Величина определяется по формуле [28]:
где - текущие издержки производства (себестоимость годового выпуска продукции с использованием разработанного технологического процесса) без учета амортизации основных производственных фондов используемых при изготовлении продукции р;
И = Иг – Аопф (5.23)
где Иг – годовые текущие издержки посчитанные по формуле (5.19);
Аопф – амортизация основных производственных фондов.
- среднегодовая стоимость основных производственных фондов используемых при производстве продукции на спроектированном участке;
- ликвидационное сальдо основных фондов либо их остаточная стоимость на момент окончания применения разработанной технологии р. Ликвидационное сальдо основных фондов принимают в размере 5 % от их первоначальной стоимости. Остаточная стоимость основных фондов на момент окончания использования разработанной технологии определяется по формуле:
где - первоначальная (балансовая) стоимость основных фондов р;
- норма реновации соответствующая сроку службы основных фондов = 00627 (10 лет);
- норма реновации соответствующая = 01054 (срок использования нового технологического процесса – 3 года срок использования основных производственных фондов – 10 лет).
И = 59490806-242247=57068336 тыс. р.
Внутренняя норма доходности (внутренний коэффициент эффективности) проекта определяется по формуле:
где – единовременные затраты на создание участка р.
Срок окупаемости капитальных вложений в проект определяется по формуле:
Таким образом а срок окупаемости . Следовательно можно сделать вывод о том что разработанные инженерные решения являются экономически эффективными.
К показателям эффективности проекта относятся также снижение себестоимости изготовления детали экономия металла снижение трудоемкости изготовления детали условное высвобождение численности рабочих.
Снижение себестоимости изготовления детали % [15]:
где - цеховая себестоимость по базовому и новому техпроцессу р.
Определим экономию металла по формуле:
ΔМ = (М1 – М2) · N(5.28)
где М1 М2 - соответственно расход материала на деталь в базовом и проектном вариантах кг
ΔМ = (141-127) · 34000 = 4760 кг
Снижение трудоемкости изготовления детали % [15]:
где - трудоемкость изготовления единицы продукции по базовому и новому техпроцессу мин.
Условное высвобождение численности рабочих чел [15]:
где - эффективный фонд рабочего времени за год ч;
- коэффициент выполнения норм.
Все рассчитанные показатели экономической эффективности спроектированного участка сведены в таблице 5.9.
Таблица 5.9 – Показатели экономической эффективности проекта
Интегральный экономический эффект тыс. р
Внутренняя норма доходности
Срок окупаемости капитальных вложений лет
Снижение себестоимости изготовления детали %
Снижение трудоемкости изготовления детали %
Условное высвобождение численности рабочих чел.
Выводы: получен экономический эффект ЭТ = 1465049 млн.р. внутренняя норма доходности е = 064 больше норматива эффективности капитальных вложений ЕН = 01 а срок окупаемости капитальных вложений Ток = 18 года меньше срока использования разработанной технологии следовательно предложенные в дипломном проекте инженерные решения можно считать экономически эффективными
Управление развитием экономического потенциала современного предприятия действующего в конкурентной среде должно основываться на объективной информации о его состоянии. Кроме того следует иметь в виду что состояние экономического потенциала во многом определяется качественным состоянием всего объекта управления - предприятием. Вместе с тем экономический потенциал характеризуется сочетанием и взаимодействием образующих его элементов.
Проблемы развития мотивации и оценки кадрового потенциала как показывает практика всегда являлись основой ключевых концепций и парадигм. Однако значительные сложности в данном вопросе касаются даже не столько проблемы выработки критериев оценки персонала сколько поиску основ для создания действенных программ стимулирования и развития на основе системы оценки кадров. Значимость данного вопроса столь очевидна что в свое время нашла поддержку в общегосударственных нормативных актах касающихся оценки эффективности труда и формирования управленческих решений на предприятии.
Вместе с тем исследование проблем оценки кадров и программ кадрового развития в отрыве от производственной деятельности не представляется возможным. Помимо этого кадровая политика должна опираться и строиться исходя из реальных возможностей современного предприятия что опять-таки возвращает к вопросам формирования направления развития на основе комплексной оценки экономического потенциала.
Также не менее значимым моментом определяющим возможность и направление развития предприятия и экономического потенциала. Становление рынка активно способствовало внедрению в практику функционирования современного предприятия целой системы показателей оценки его финансового положения и возможностей. И в этой связи вполне уместным будет применить для формирования системы оценки финансового потенциала предприятия отдельные группы показателей среди которых: показатели финансовой устойчивости ликвидности оборачиваемости и рентабельности.
В связи с тем что определенное количество характеристик элементов экономического потенциала не имеет смысла формировать в виде относительных величин также достаточно затруднительно выразить их абсолютно то наиболее целесообразно при оценке элементов экономического потенциала предприятия использовать два больших класса: количественные икачественные методы.
Оценка элементов образующих экономический потенциал должна сводиться к анализу конкретных характеристик объектов. Каждый из указанных элементов может быть охарактеризован множеством показателей среди которых следует выделить как количественные так и качественные. Дальнейшее решение проблемы предполагается перенести в русло преобразования получаемых значений по качественным и количественным показателям диагностики элементов потенциала к единому стандарту позволяющему оценить общий уровень экономического потенциала с последующей выработкой стратегии его развития.
В таблице конкретизирован состав качественных показателей диагностики экономического потенциала. Так показатели характеризующие потенциал функционирования развития управления отнесены к кадровой составляющей экономического потенциала вместе с тем перечисленные группы с большой степенью значимости могут оказывать влияние на состояние потенциала производственного. В связи с этим видовая принадлежность групп показателей к определенному элементу экономического потенциала имеет несколько условный характер.
Проиллюстрировать это можно следующим: формально потенциал управления исполнения функционирования и организации отнесен к кадровому элементу экономического потенциала однако значимость показателей входящих в состав перечисленных групп не менее велика как для производственного так и для научно-технического потенциалов.
Аналогичные рассуждения можно провести и для остальных групп показателей. Причем подобное свойство сбалансированной системы показателей как видно из рисунка касается не только качественных (таблица 5.8) но и количественных показателей.
Таблица 5.9 - Качественные показатели оценки элементов экономического потенциала предприятия
Потенциал управления
Уровень квалификации административно-управленческого персонала; уровень профессиональной подготовленности; этико-правовая среда управления; культура общего руководства; философии менеджмента и стиля управления; способности топ-менеджеров.
Потенциал исполнительский
Общий уровень исполнительской дисциплины; уровень подготовки работающих; социально - психологический климат; уровень исполнительского соответствия; гибкость темпа работы по категориям; гибкость рабочего времени по категориям персонала.
Потенциал функционирования
Наличие систем оценки персонала; наличие систем нематериального стимулирования.
Возможность обучения и переобучения кадров; возможность осуществления развития за счет собственных источников; наличие планов развития и пополнения научных фондов; наличие планов закупки новейших образцов техники; качество вырабатываемых стратегических решений; общее понимание и поддержка целей и задач развития; соответствие программ развития предприятия миссии и общим целям
Потенциал организации управления
Наличие системы стратегического управления и планирования; наличие специфических методов управления; эффективность методов и порядка контроля за исполнением решений
Потенциал инновационый
Уровень исследований по новым товарам; возможности развития продукции; степень востребованности исследований и разработок; сотрудничество с другими организациями; состояние лабораторной базы и испытательного оборудования; соответствие разрабатываемых объектов международным стандартам (превосходство).
Потенциал информационной базы
Состояние информационного обеспечения инновационного процесса; полнота охвата тематики нововведений собственными научными фондами предприятия; уровень (наличие) тематического научно-технического и патентного рубрикатора; полнота поступающей патентной информации (межотраслевой и отраслевой); уровень автоматизации сбора обработки передачи и хранения информации; степень соответствия стандартам и требованиям; активность коммуникационных связей внутри предприятия; активность коммуникационных связей с внешними источниками; активность обратной связи внутри предприятия; активность обратной связи с внешними источниками; доступность международных информационных источников.
Потенциал производственный
Наличие комплексного резерва мощностей и ресурсов; доступность и надежность источников сырья и материалов; уровень обеспечения контроля качества товаров; безопасность производственных процессов; экологичность производственных процессов.
Потенциал финансовый
Степень деловой активности; экономическая безопасность; степень доверия (деловая репутация); рост стоимости имущества
Безопасность и экологичность
Рассматриваемый участок цеха относится к участкам механообрабатывающего типа. В данном технологическом процессе существуют следующие вредные и опасные факторы:
а) энергия и механические влиянием на человека к которым относятся шумы и вибрации возникающие от колебаний движущихся частей машин и механизмов;
б) электрические – электрический ток. В цехе используется электрооборудование которое требует соблюдения норм электробезопасности;
в) электромагнитные – освещенность;
г) химические – наличие вредных примесей в воздухе вызванных электрохимической обработкой;
д) психофизиологические – утомление стресс и тому подобное.
Работа механообрабатывающего цеха сопровождается шумом. Под шумом понимается всякий нежелательный неприятный для восприятия человека звук. Шум неблагоприятно воздействует на организм человека. Вызывает психические и физиологические нарушения усиливает утомляемость работающего снижает работоспособность и создает предпосылки для общих и профессиональных заболеваний и производственного травматизма. С увеличением уровней до 70 дБ и выше шум может оказывать определенное физиологическое воздействие на человека приводя к видимым изменениям в его организме. Под воздействием шума превышающего 85÷90 дБ в первую очередь снижается слуховая чувствительность на высоких частотах. При длительном воздействии или большой интенсивности шума может произойти понижение остроты или даже полная потеря слуха. При действии шума очень высоких уровней (более 145 дБ) возможен разрыв барабанной перепонки. Средствами индивидуальной защиты на проектируемом участке являются наушники и вкладыши.
Под вибрацией понимается движение точки или механической системы при которой происходит поочередное возрастание и убывание во времени значений по крайней мере одной координаты. Причиной возбуждения вибраций являются возникающие при работе машин и агрегатов неуравновешенное силовое воздействие. Вибрация неблагоприятно воздействует на человека. Воздействие вибрации не только ухудшает самочувствие работающего и снижает производительность труда но и часто приводит к тяжелому профессиональному заболеванию – виброболезнь. Локальная вибрация в частности вызывает спазмы сосудов которые начинаются с концевых фаланг пальцев и распространяются на все предплечье захватывают сосуды сердца. Вследствие этого происходит ухудшение снабжения конечностей кровью. Неблагоприятное воздействие вибрации снижается виброгашением вибродемпфированием организацией работы и отдыха рабочего использованием средств индивидуальной защиты (защита опорных поверхностей).
Станки на участке 6Р13РФ-3 6Т13МФ-3 подключены к трехфазной цепи переменного тока. Рабочий участка дистанционно не может определить находится ли установка под напряжением или нет. Ток который протекает через тело человека действует на организм не только в местах контакта и по пути протекания тока но и на такие системы как кровеносная дыхательная и сердечно-сосудистая.
Основными мерами защиты от поражения током являются:
а) обеспечение недоступности токоведущих частей находящихся под напряжением для случайного прикосновения изоляцией токоведущих частей размещением их на недоступной высоте ограждением и др.;
б) электрическое разделение сети с помощью специальных трансформаторов;
в) применение малого напряжения;
г) двойная изоляция;
д) защита заземлением и занулением;
е) защитное отключение;
ж) организация безопасной эксплуатации электроустановок.
Большое значение имеют инструктажи каждого производственного рабочего:
а) вводный – ознакомление с общими вопросами техники безопасности – проводит инженер безопасности труда;
б) первичный – ознакомление с конкретными видами безопасности труда на данном рабочем месте – проводит руководитель работ;
в) повторный – проводит руководитель работ с периодичностью в полгода;
г) внеплановый – проводится руководителем работ в случае изменений в технологическом процессе при поступлении нового оборудования а также после несчастных случаев и длительных перерывах в работе;
д) целевой – проводит руководитель работ при выполнении работ не связанных с основной специальностью.
В конструкции каждого станка непременно должны быть предусмотрены устройства защищающие рабочих от различных травм. Например предусматриваются меры исключающие возможность прикосновения оператора во время работы станка к токоведущим деталям. Для этого электрооборудование располагается внутри корпуса станка и в специальном дополнительном электрошкафу. Корпус станка и шкаф должны быть надежно заземлены. В конструкции станка предусмотрены резисторы обеспечивающие стекание заряда с накопительных конденсаторов.
Защита окружающей среды – это комплексная проблема требующая усилий ученых многих специальностей. Наиболее активной формой защиты окружающей среды от вредного воздействия выбросов промышленных предприятий является безотходная технология. Под понятием «безотходная технология» следует понимать комплекс мероприятий в технологических процессах от обработки сырья до использования готовой продукции в результате чего сокращается до минимума количество вредных выбросов и уменьшается воздействие отходов на окружающую среду до приемлемого уровня.
Важная роль в защите окружающей среды отводится мероприятиям по рациональному размещению источников загрязнений. К ним относятся:
- Вынесение промышленных предприятий из крупных городов и сооружение новых в малонаселенных районах с непригодными и малопригодными для использования землями.
- Оптимальное расположение промышленных предприятий с учетом топографии местности и розы ветров.
- Установка санитарных охранных зон вокруг промышленных предприятий.
- Рациональная планировка городской застройки обеспечивающая оптимальные экологические условия для человека и растений.
Пассивные методы защиты окружающей среды включают комплекс мероприятий по ограничению выбросов промышленного производства с последующей утилизацией или захоронением отходов. К их числу относятся: очистка сточных вод от примесей; очистка газовых выбросов от вредных примесей; рассеивание вредных примесей в атмосфере; глушение шума на путях его распространения; экранирование источников энергетического загрязнения окружающей среды; захоронение токсичных и радиоактивных отходов.
На современном этапе развития промышленности пассивные методы защиты окружающей среды играют существенную роль они постоянно совершенствуются и широко внедряются в технологические эксплуатационные циклы во всех отраслях народного хозяйства.
Участок спроектированного цеха оснащен самыми различными видами технологического оборудования. Безопасность производственного оборудования обеспечивается правильным выбором принципа его действия кинематических схем конструктивных решений параметров рабочих процессов использование различных средств защиты. Большое значение в обеспечении надежной работы машин и механизмов имеет наличие необходимых контрольно-измерительных приборов и устройств автоматического управления и регулирования. Степень утомляемости работающих на основных видах оборудования обусловлена не только нервной и физической нагрузкой но и психологическим воздействием обстановки поэтому большое значение имеет выбор цвета внешних поверхностей оборудования и помещения. Важнейшим условием обеспечения безопасности машин и механизмов является учет и выполнение требований безопасности на всех этапах их создания начиная с разработки технического задания на проектируемое оборудование и заканчивая сдачей опытных образцов в серийное производство.
Охрана окружающей среды – это система государственных и общественных мероприятий обеспечивающих сохранение природной среды пригодной для жизнедеятельности нынешних и будущих поколений.
Наибольшую опасность представляют отходы производства. С развитием промышленности резко возрастает и количество отходов что свидетельствует о несовершенстве технологии.
Наиболее перспективный путь решения проблемы защиты окружающей среды – это дальнейшее совершенствование технологических процессов и создание безотходного производства с замкнутыми технологическими циклами.
Для рассматриваемого типа производства характерно загрязнение атмосферы металлической пылью в виде вентиляционных отбросов и попадания в сточные воды отработанных жидкостей: СОЖ эмульсий масла и так далее.
На предприятии должна быть организована единая система удаления пыли и стружки из зоны резания механизированное транспортированное их к месту сбора и брикетирования.
Такое решение позволяет устранить безвозвратные потери металла сократить большое число уборщиков стружки повысить безопасность труда улучшить гигиенические условия труда станочников и сократить количество вредных отходов и выбросов в атмосферу.
Каждая промышленная структура имеет систему водоснабжения и водоотведения. Предпочтение отдается системе оборотного водоснабжения при котором часть воды используется в технических операциях очищается и поступает вновь а часть сбрасывается. Система водоотведения предусматривает систему канализации которая включает различные устройства в том числе и очистные.
В выпускной квалификационной работе был разработан технологический процесс изготовления корпуса тяги.
Исходя из разработанного технологического процесса и объёма выпуска продукции был спроектирован участок по изготовлению корпуса тяги. Для обеспечения полной загрузки оборудования на данных станках будет производиться выпуск подобных деталей.
Был проведён анализ базового технологического процесса производства детали и выявлена возможность повышения качества и экономической эффективности производства.
Спроектирована операционная технология производства детали и конструкция приспособления. При этом были задействованы прогрессивные средства разработки технологического процесса обработки детали в САПР.
Был спроектирован участок механического цеха проведён расчёт относительных и абсолютных показателей спроектированного предметно-замкнутого участка. С его помощью было выявлено сокращение количества операций и переходов вследствие чего уменьшились затраты на оборудование электроэнергию амортизацию а также снижение себестоимости детали.
Справочник технолога-машиностроителя. В 2-х т. Под ред. А. Г. Косиловой и Р.К. Мещерякова. – 4-е изд. переработ. и доп. Т.1 – М.: Машиностроение 1986. – 656 с. ил.
Лахтин Ю.М. Леонтьева В.П. Материаловедение: Учебник для машиностроительных вузов – 2-е изд. перераб. и доп. – М.: Машиностроение 1980. – 493 с. ил.
Дипломное проектирование по технологии машиностроения: Учеб. пособие для вузов В.В. Бабук П.А. Горезко К.П. Забродин и др. Под общ. ред. В.В. Бабука – Минск: Выш. шк. 1979. – 464 с. ил.
Экономика машиностроительного производства Под ред. И.Э. Берзиня В.П. Калинина. – М.: Высшая школа 1988. – 304 с.
Станочные приспособления: Справочник. В 2-х т. Под ред. Б.Н. Вардашкина А.А. Шатилова. Т.1. – М.: Машиностроение 1984. – 592 с.
Станочные приспособления: Справочник. В 2-х т. Под ред. Б.Н. Вардашкина В.В. Данилевского. Т.2. – М.: Машиностроение 1984. – 656 с.
Маталин А.А. Технология машиностроения. – Л.: Машиностроение 1985.
Справочник технолога-машиностроителя. В 2-х т. Под ред. А. Г. Косиловой и Р.К. Мещерякова. – 4-е изд. переработ. и доп. Т.2 – М.: Машиностроение 1986. – 496 с. ил.
Проектирование механических цехов: Учебник для студентов машиностроительных специальностей вузов Под ред. А.М. Дальского – М.: Машиностроение 1990. – 352 с. ил.
Болотин Х.Л. Костромин Ф.П. Станочные приспособления – 5-е изд. переработ. и доп. – М.: Машиностроение 1973. – 344 с.
Корсаков В.С. Основы конструирования приспособлений: Учебник для вузов. – 2-е изд. переработ. и доп. – М.: Машиностроение 1983. – 277 с. ил.
Норенков И.П. Автоматизированное проектирование: Учеб. пособие. – М.: Изд-во МГТУ им. Н.Э. Баумана 2000. – 188 с.
Алямовский А.А. SolidWorks. Компьютерное моделирование в инженерной практике. – СПб.: БХВ-Петербург 2005. – 800 с. ил.
Методические указания по выполнению курсовой работы по дисциплине «Организация и менеджмент производства» для студентов специальности 120100 «Технология машиностроения» дневного обучения Сост. А.В. Ростова. – Воронеж.: ВГТУ 2003. – 33 с.
Комплексная оценка эффективности мероприятий направленных на ускорение научно-технического прогресса: Методические рекомендации – М.: 1989.
Инвестиционное проектирование: практическое руководство по экономическому обоснованию инвестиционных проектов Под ред. С.П. Шумилина. М.: «Финстатинформ» 1995. – 240 с.
Информационный лист CAE6501.150.cdw

ее эксплуатации с использованием САЕ.
Разработка технологии и средств технологического
оснащения для изготовления детали Корпус тяги
Проверка проектирования
корпус тяги.cdw

оснащения для изготовления корпуса тяги
Формовочные уклоны пред. откл.размеров отливки класс
Неуказанные внешние литейные радиуса скругления 2 мм.
Неуказанные внешние литейные радиуса сопряжений 5 мм.
Контроль радиографический отливок поштучно по схеме
Контроль деталей люминесцентный ЛЮМ17-П.
Предельные отклонения размеров обрабатываемых поверхностей
Предельные отклонения отливки по H14
Карта наладки1 лист.cdw

А.Установить деталь и после
Фрезеровать поверхность 1
Разверннуть 4 отв. 2
Фрезеровать торци с
Расточить фаски в двух
Отлить заготовку по технологии
заготовительного цеха.
Оправка расточная Развертка
Разработка техпроцесса и средств технологического
оснащения для изготовления Корпуса тяги
Очистка и обрубка отливки.
Спец. приспособление
Штангенциркуль ШЩ-I-250-0
Заготовка6501.150.003.cdw

оснащения для изготовления корпуса тяги
кд(ВАЛ 10)Т5 в песчаную форму
Пределные отклонения размеров отливки по H14
Неуказанные внешние литейные радиуса скругления 2 мм.
Неуказанные наружние литейные радиуса сопряжений 5 мм.
РТК 6501.150.003.cdw

ПЛАН участка2.cdw

для изготавления корпуса тяги
График загрузки оборудования
Карта наладки 2.cdw

А.Установить деталь и после
Развернуть отв 12Н8.
Сверлить отв. под заход фрезы.
Фрезеровать паз с другой стороны.
Фрезеровать торци отв. с
Фрезеровать торцы с другой стороны.
Рассточить фаски в отв. 1.5
Фрезеровать паз с одной стороны.
Z=2; Расточная оправка унив.;Зенкер
Расточная оправка унив.;Зенкер
Разработка технологии и средств технологического
оснащения для изготовления детали Корпус тяги
Штангенциркуль ШЩ-I-250-0
Специальное приспособление
Приспособа эксперемент .cdw

На деталях и сборках заусенцы
повреждения на допуск
Все детали поступающие на сборку пневмоцилиндра
должны быть чистыми. При сборке обеспечить чистоту
внутренних полостей.
Перед сборкой гильзы
смазать смазкой МС 70-ГОСТ 9762-76.
Посадочные места под резиновые кольца и уплотнения
перед сборкой смазать масломТС 3п-В ОСТ 01365-В4
Пневмоцилиндр в сборке испытать на
герметичностьпод дпавлением 2
Технические харакеристики:
Точность установки детали в приспособлении 0
Статическая сила на штоке не менее 1450 Н
Время сбрасывания - 3 сек.
Разработка технологии т средств технологического
оснащения для изготовления корпуса тяги
Мерительный1.cdw

Тип и модель- ВЕ-М101004А(ВЕ 200).
Диопозон измерений по координатам (мм-)
X=1000 (800); Y=1000; Z=400.
Дискретность отсчета (мкм)- 1; 0.5 ;0.2.
Допускаемая погрешность (мкм)- 2.5+3.5L.
Габоритные размеры 1900
Измерительная голова с одноточечным
Разработка технологии и средств технологического
оснащения для изготовления корпуса тяги
Схема контроля отклонений от формы
и расположения поверхностей
Рекомендуемые чертежи
- 24.01.2023
- 24.01.2023
- 24.01.2023
- 24.01.2023