Расчёт средств технологического оснащения для изготовления детали корпус




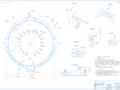
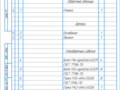
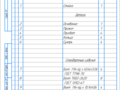
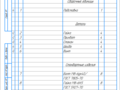
- Добавлен: 25.01.2023
- Размер: 874 KB
- Закачек: 0
Описание
Расчёт средств технологического оснащения для изготовления детали корпус
Состав проекта
![]() |
![]() |
![]() ![]() ![]() ![]() |
![]() ![]() ![]() ![]() |
![]() ![]() ![]() ![]() |
![]() ![]() ![]() ![]() |
![]() |
![]() ![]() ![]() ![]() |
![]() ![]() ![]() ![]() |
![]() ![]() ![]() ![]() |
![]() ![]() ![]() ![]() |
![]() ![]() ![]() |
![]() |
![]() ![]() ![]() ![]() |
![]() ![]() ![]() ![]() |
![]() ![]() ![]() ![]() |
Дополнительная информация
Контрольное приспособление..cdw

изготовления детали Корпус
При "нулевом" положении поверхности Б и В; Д и Г должны
пересекаться в одной точке
отклонение не более 0
Погрешность показаний при проверке на микроскопе не более
Фаскомер предназначен для измерения фасок с допуском не
Прис. растачное..cdw

изготовления детали Корпус
* Размеры и параметры для аттестации.
** Размеры для справок.
Работает на станке расточном.
Остальные технические требования по ОСТ 92-8828-76.
Присп. для ток.-карус. операции 1..cdw

оснащения для изготовления
* Размеры для справок.
Работает на токарно-карусельном станке.
Остальные технические требования по ОСТ 92-8828-76.
Вариант крепления детали
Прис. вертик.-2 для нарезания резьбы..cdw

изготовления детали Корпус
* Размеры и параметры для аттестации.
** Размеры для справок.
Работает на токарно-карусельном станке.
Остальные технические требования по ОСТ 92-8828-76.
СП(Прис. для ток.-карус.операции11).spw

Болт М16-6g х 60.66.45.06
Винт М6-6g х 10.14Н.06
Гайка М20-6H.04.45.06.
Гайка М24-6H.04.45.06.
Гайка М42-6H.04.45.06.
Шпилька М24-6gх320.66.45.06
СП(Прис. для нарезания резьбы1).spw

Болт М24-6gх60.66.45.029
Гайка М24-6Н.4.45.026
Гайка М42-6Н.4.45.026
Спецификация к фаскомеру1.spw

СП(Прис. расточное новое-1).spw

поясниловка.doc
1Назначение и конструкция детали .3
2Анализ технологичности конструкции детали .5
3Определение типа производства 10
4Расчет количества деталей в партии ..12
5 Анализ существующего технологического процесса .13
6Выбор технологических баз 17
7Выбор способа получения заготовки ..19
8Разработка маршрута обработки .21
Конструкторская часть .45
1Разработка токарно-карусельного приспособления .45
2Приспособление расточное .47
3Приспособление для нарезания резьбы 53
4Контрольное приспособление 55
Экономическая часть 57
1Основные фонды цеха .57
2Себестоимость продукции 59
3Затраты на основные материалы .59
4Расчет фондов заработной платы рабочих ..60
5Расчеты на содержание и эксплуатацию оборудования 66
6Оборотный капитал 70
7Производственный капитал 70
8Определение цены единицы продукции ..71
9Финансовый план ..71
Рентабельность проекта и технико-экономические показатели 73
Охрана труда и безопасность проекта .75
Список литературы 92
Совокупность методов и приемов изготовления машин выработанных в течение длительного времени и используемых в определенной области. Поэтому возникают такие понятия: технология обработки давлением литья сварки сборки машин. Все эти области производства относятся к технологии машиностроения охватывающей все этапы процесса изготовления машинной продукции.
Однако под “технологией машиностроения” принято понимать научную дисциплину изучающую процессы металлической обработки деталей и сборки машин и попутно затрачивающую вопросы выбора заготовки и методы их изготовления. В процессе технической обработки деталей машин возникает большое количество простейших вопросов связанных с необходимостью выполнения технических требований поставленными конструкторами перед изготовителями.
Эти обстоятельства объясняет развитие “технологии машиностроения“ как научной дисциплиной в первую очередь в направлении изучения вопросов технологии металлической обработки и сборки в наибольшей мере влияющие на производственную деятельность предприятия.
Технологическая часть
1. Назначение и конструкция детали
Деталь Корпус предназначена для изделия Отопительно-вентиляционная установка ОВ-95. Применяется для обогрева кузовов-фургонов различной спецтехники салонов вахтовых автобусов.
Деталь работает при высоких температурах поэтому к ней предъявляются требования высокой прочности.
В соответствии с ТЗ на Корпус действуют следующие нагрузки:
внутреннее давление величина которого составляет 120 кгссм2;
Деталь выполнена из титанового сплава ОТ4 ОСТ 1.90018-81 который является эффективным материалом т.к. титановый сплав сочетает в себе нехладноломкость алюминия и аустенитных сталей высокую коррозионную стойкость лучших медноникилиевых сплавов и нержавеющих сталей немагнитность прочность и удельную прочность более высокие чем у большинства конструкционных материалов.
Основные механические и физические свойства титанового сплава ОТ4 [2 с.10]
Временное сопротивление разрыву В Нмм2 (кГмм2)
Предел текучести Т Нмм2 (кГмм2)
Относительное удлинение
Относительное сужение
Ударная вязкость KCU Джсм2 (кГмсм2)
Режимы термической обработки титанового сплава ОТ4 [3 лист 8]
Вид термической обработки
Температура нагрева оС
Продолжительность выдержки ч
2. Анализ технологичности конструкции детали
При изучении чертежа детали «Корпус» я сделал следующие выводы:
Чертёж содержит все необходимые сведения дающие полное представление о детали т.е. все проекции разрезы и сечения дают полное представление о конфигурации детали и о возможных способах получения заготовки;
На чертеже указаны все размеры с необходимыми отклонениями требуемая шероховатость обрабатываемых поверхностей допустимые отклонения от правильных геометрических форм а также взаимного расположения поверхностей;
Чертёж содержит все необходимые сведения о материале детали термической обработке массе детали.
На основании изучения условий работы детали а так же учитывая заданную годовую программу я сделал следующие выводы:
Упрощение конструкции детали возможно если исключить пазы проточки выборки карманы однако это приведет к увеличению веса детали и существенно не снизит стоимости заготовки;
Конфигурация детали сложна для выполнения;
Допускается применение станков с ЧПУ что повышает производительность обработки;
Труднодоступных мест для подвода инструмента нет;
Все допуски шероховатость поверхностей и отклонения формы обеспечивается технологическими возможностями оборудования при выполнении операций;
Измерение заданных на чертеже размеров не представляет особой сложности и может выполняться предельным мерным инструментом за исключением
Метод получения заготовки (поковка) в условиях данного производства выбран правильно хотя возможно заменить на штамповку что позволит сократить расход материала на припуски;
Материал детали выбран правильно;
Термическая обработка выбрана верно.
В целом деталь достаточно технологична т.к. позволяет использовать производительное оборудование и выбрать удобные базы для установки однако некоторую сложность при обработке представляют поверхности так называемые карманы и глухие отверстия бобышки.
Уровень технологичности конструкции по точности обработки.
где Кб.тч Ктч – соответственно базовый и достигнутый коэффициенты точности обработки.
Определение коэффициента точности:
где Тср – средняя точность обработки:
Тср = (SТi × ni) Sni
Тср = 2514 234 = 1074;
Ктч = 1 - 1 1074 =091.
Уровень технологичности конструкции по шероховатости поверхности:
где Кб.ш Кш – соответственно базовый и достигнутый коэффициенты шероховатости поверхности.
Коэффициент шероховатости поверхности определяется по формуле:
где Шср – средняя шероховатость обработанных поверхностей:
Шср = (SШi × ni) Sni
Значения достигнутых уровней технологичности конструкции по точности обработки и шероховатости следует определять после завершения технологического контроля чертежа детали и внесения в него рациональных изменений. Т.к. чертёж детали после завершения технологического контроля не подвергся пересмотру и изменению поэтому уровень технологичности конструкции по этим показателям равен единице.
Уровень технологичности конструкции по использованию материала.
где Кб.и.м Ки.м – соответственно базовый и достигнутый коэффициенты использования материала.
Базовый коэффициент использования материала (при использовании поковки в качестве исходной заготовки):
Кб.и.м. = mд mз = 175 220 =008.
Достигнутый коэффициент использования материала (при использовании штамповки в качестве исходной заготовки):
Ки.м. = mд mз = 175 70=025.
где mд – масса готовой детали mд = 175 кг; mз – масса заготовки.
Уровень технологичности конструкции по использованию материала:
Ку.и. = Кб.и.м. Ки.м. =008 025 = 032.
Уровень технологической конструкции по трудоемкости изготовления:
где Ти Тб.и –соответственно достигнутая и базовая трудоемкость изготовления детали.
Ку.т. = 3207 4203 = 076
Уровень технологичности конструкции по технологической себестоимости:
где Ст Сб.т – соответственно достигнутая и базовая технологическая себестоимость детали.
Ку.с = 5077776 13451179 = 038.
3. Определение типа производства
Тип производства характеризуется коэффициентом закрепления операций Кз.о. Значение коэффициента закрепления операций принимается для планового периода равного одному году.
Расчет типа производства ведется для основных операций.
годовая программа выпуска изделия N = 100 шт;
действительный годовой фонд времени работы оборудования Fд = 4029ч [7 табл.2.1 с.22].
Данные по существующему заводскому технологическому процессу.
Токарно-карусельная
Горизонтально-расточная
Координатно-расточная
Количество станков mp определяется по формуле:
где Тшт – штучное время; з.н. – нормативный коэффициент загрузки оборудования з.н = 08 [7с. 20].
Принятое число рабочих мест Р определяется округлением до ближайшего целого числа полеченного значения mр.
Фактический коэффициент загрузки рабочего места:
Количество операций выполняемых на рабочем месте О:
Коэффициент закрепления операций:
Производство серийное т.к. 10 20 [ с.6].
4. Расчет количества деталей в партии
Программа выпуска изделия N = 100 шт.;
Периодичность запуска-выпуска изделия а = 24 дня;
Число рабочих дней в году F = 250 дней;
Средняя трудоемкость операций Тшт.ср :
где Тшт. n – количество операций.
Тшт.ср. = 2522 8 = 31525 мин.
Расчетное количество деталей в партии:
Расчетное число смен на обработку партии деталей на участке.
Принятое число смен Спр = 9 смен.
Принятое число деталей в партии:
где 476 – действительный фонд времени работы оборудования в смену мин;
– нормативный коэффициент загрузки станков в серийном производстве.
5. Анализ существующего технологического процесса
Анализ производится для изыскания возможностей совершенствования технологического процесса повышения производительности и обеспечения качеств обработки.
Анализ ТП включает следующий перечень вопросов и ответов:
Целесообразность способа получения заготовки для заданных условий производства.
В базовом ТП заготовкой является поковка. При обработке данной заготовки приходится снимать очень много материала коэффициент использования материала очень маленький. Данный тип заготовок характерен для единичного производства.
Правильность выбора баз.
По моему мнению в данном ТП базы выбраны правильно.
Целесообразность применяемых способов обработки.
Способы обработки в ТП подобраны наиболее производительные.
Правильность последовательности операций для достижения заданной точности детали.
Для достижения заданной точности операции т.е. их последовательность подобраны правильно сначала черновые (токарные) для формирования баз затем чистовые.
Операции: фрезерования сверления резьбонарезания. Порядок расположения этих операций в процессе обработки не играет большого значения.
Соответствие параметров применяемого оборудования требованиям данной операции.
Технологический процесс составлялся на основе существующих станков в цехе и поэтому существует возможность того что станки могут быть большими габаритами чем необходимые станки для обработки этой детали. А со стороны параметров применяемого оборудования то они соответствуют требованиям операций выполняемых на них.
Степень концентрации операций.
Концентрация операций в данном технологическом процессе отсутствует. Все операции выполняются в строгой последовательности.
Обоснованность режимов резания.
Режимы резания подобраны таким образом чтобы свести к минимуму появления брака при обработке детали но при этом чтобы время на обработку также было минимальным.
Степень оснащенности операций технологической оснасткой [данные ТП].
На первой токарно-карусельной и следующих горизонтально-расточных операциях деталь устанавливается в специальные приспособления с механическим зажимом.
При нарезании резьбы деталь закрепляется на угольнике.
При назначении оснастки целесообразно использовать пневмозажимы вместо механических это сократило бы время на установку и снятие детали.
Обоснованность применяемого режущего инструмента [данные ТП].
На токарных операциях используются следующие резцы:
- резец 2112-0057 ВК8 ГОСТ 18880-73 для подрезки торца;
- резец 2112-0063 ВК8 ГОСТ 18880-73 для подрезки торца;
- резец 2130-0521 ВК8 ГОСТ 18874-73;
- резец расточной 2141-0031 ВК8 ГОСТ 18883-73;
- резец 2141-0045 IV-ВК8-1 ГОСт 1883-73 для растачивания фаски;
- резец спец. с двумя R2 для точения канавки.
- резец канавочный спец. с двумя
На фрезерных операциях используются специальные фрезы с материалом режущей части ВК8.
На сверлильной операции используется сверло (сверло 2309-0117 ВК8 ГОСТ 17275-77).
На слесарной операции используются следующие инструменты:
- напильник 2820-0023 ГОСТ 1465-80 для зачистки заусенец;
- шкурка ГОСТ 6456-82;
- ветошь ГОСТ 6456-82;
Контроль производится следующими инструментами:
- образцы шероховатости ГОСТ 9378-75;
- кольцо 8211-0112 8д. ГОСТ 17763-72; кольцо 8211-1112 8д. ГОСТ 17763-72 для контроля резьбы;
- скоба индикаторного типа СИ 600 ГОСТ 11098-75;
- калибры ГОСТ 18362-73;
- штангенглубиномер ШГ-160 ГОСТ 166-89;
- штангенрейсмас ШР-250-005 ГОСТ 164;
- штангенциркули: ШЦ-1-125-01 ГОСТ 166-89 ШЦ-11-160-005 ГОСТ 166-89 ШЦ-11-250-005 ГОСТ 166-89 ШЦ-111-400-01 ГОСТ 166-89;
- микрометр МК-50-1 ГОСТ 6507-78;
- индикатор ИЧ 10 кл.1 ГОСТ 577-68;
Производительность обработки.
Производительность обработки невысокая т.к. на токарных операциях используются универсальные станки при использовании станков с ЧПУ сократилось бы время на вспомогательные операции; горизонтально - расточные операции можно заменить на высокоскоростное фрезерование что также повысит производительность обработки. Много ручного труда на слесарных операциях (напильник это орудие труда наших дедов) использовании шлифмашинок при снятии заусенцев намного облегчило бы труд слесаря.
Данное технологическое оборудование вполне обеспечивает заданное качество т.е. обеспечивает заданную шероховатость точность и отклонение формы и расположения.
В результате анализа существующего на предприятии ТП я предлагаю следующие изменения:
- возможно заменить заготовку получаемой ковкой на штамповку это позволит уменьшить расход материала и исключить обдирочную операцию;
- можно заменить станки: 1516 на 1512 и 1512Ф3; 2636 на 2В622МФ3 при этом повысится производительность обработки.
6. Выбор технологических баз
Одним из главных вопросов при разработке технологического процесса является правильный выбор баз и способов установки на станке заготовки при ее обработке. От него зависит точность обработки заготовки и величина необходимого припуска.
Основные соображения которыми я руководствовалась при выборе установочных баз:
Необходимо использовать по возможности принцип совмещения баз т.е. в качестве установочной базы брать поверхность являющуюся измерительной базой.
Следует соблюдать принцип постоянства баз т.е. в ходе обработки на всех основных технологических операциях использовать в качестве установочной базы одни и те же поверхности.
Когда постоянство установочной базы не может быть обеспечено в качестве новой установочной базы выбираются обработанные поверхности.
Установочная база должна обеспечивать достаточную устойчивость и жесткость установки заготовки. Это достигается соответствующими размерами базовых поверхностей и их взаимным расположением.
Установочную базу следует выбирать с учетом простоты и дешевизны зажимного приспособления а также удобства установки детали и ее закрепления.
Выбранные в качестве установочных баз поверхности должны быть обработаны на первых операциях.
Для выбора черновой установочной базы руководствуются следующим:
Для заготовок у которых все поверхности обрабатываются за черновую установочную базу принимают поверхности имеющие наименьшие припуски.
Черновые базовые поверхности должны быть по возможности гладкими не должны иметь штамповочных уклонов на них не следует размещать прибыли плоскости разъема моделей штампов и форм.
7. Выбор способа получения заготовки
Для изготовления детали «Корпус» заготовкой является поковка по ОСТ 1.9000-70. Особенностью получения заготовок ковкой является то что при ковке используют универсальные инструменты и оборудование что важно для мелкосерийного производства. Недостатками является низкая производительность значительный расход металла на припуски и напуски.
В качестве другого варианта заготовки я предлагаю штамповку. Преимуществом такой заготовки является снижение припусков в 2-3 раза; возможность получения поверхности не требующих механической обработки; меньшие допуски на размер; низкая шероховатость.
Себестоимость получения заготовки рассчитываю для последующего сравнения себестоимости технологических процессов.
Данные для расчетов стоимости заготовки по вариантам [данные с завода]
Наименование показателей
Масса заготовки Q кг
Стоимость 1 т заготовок принятых за базу Ci руб.
Стоимость 1 т стружки Sотх руб.
Стоимость заготовки из поковки [3c.31].
где C Кт – коэффициент зависящий от точности заготовки Кт = 1 – поковка нормальной точности [3 с. 37]; Кс – коэффициент зависящий от степени сложности Кс = 081 [3 табл.2.12 с. 38]; Кв – коэффициент зависящий от массы Кв = 07 [3 табл.2.12 c. 38]; Км – коэффициент зависящий от марки материала Км = 179 [3 с. 37]; Кп – коэффициент зависящий от объема производства заготовок Кп = 1 [3 с. 38]; Q – масса заготовки; q – масса детали q = 175 кг;
Стоимость заготовки штамповки:
где C Кт = 1 – штамповка нормальной точности [3 с. 37]; Кс = 081 [3 табл.2.12 с. 38]; Кв = 07 [3 табл.2.12 c. 38]; Км = 179 [3 с. 37]; Кп = 1 [3 с. 38].
Экономический эффект для сопоставления способов получения заготовок при которых технологический процесс механической обработки не меняется рассчитываю по формуле:
Эз = (Sзаг1 - Sзаг2) N
где N – годовая программа N=100 шт.
Эз = (1299003 – 470607) 100 = 8283960 руб.
Экономический эффект от замены заготовки получаемой ковкой заготовкой получаемой штамповкой при неизменном технологическом процессе получается положительным.
По данным расчетов принимаю заготовку штамповку т.к. этот вариант наиболее рациональный для данных условий производства.
8. Разработка технологического маршрута обработки
(в сравнении с базовым вариантом)
Критический анализ базового варианта ТП позволил внести технические корректировки и технические решения которые представлены в табл. 2.3.
Заготовительная и термообработка
Изготовление заготовки и термообработка производится в др. цеху.
Токарно-карусельный 1512
В базовом ТП обработка поверхностей ведется резцами с напаянным твердосплавными пластинами.
Я применяю резцы с механическим креплением многогранных твердосплавных неперетачиваемых пластин по ГОСТ.
Применение пластин обеспечивает:
- повышение стойкости на 20-30% по сравнению с напаянными;
- возможность повышения режимов резания за счет простоты восстановления режущих свойств многогранных пластин путем их поворота;
- сокращение затрат на инструмент в 2-3 раза вспомогательного времени на смену и переточку резцов;
- упрощение инструментального хозяйства;
- уменьшение расхода абразива.
Для обточки применяю материал режущей пластины ВК8.
В базовом ТП обработка ведется на токарно-карусельном станке 1516. Т.к. технологический процесс составлялся на основе существующих в цехе крупногабаритных станков то данную операцию целесообразнее выполнить на станке с меньшим типоразмером. Я меняю станок на 1512.
Токарно-карусельный с ЧПУ 1512МФ3
В базовом ТП обработка ведется на станке 1516.
Я применяю станок 1512МФЗ с ЧПУ который меньше по габаритам и подходит для обработки моей детали. Обработка на станке с ЧПУ сокращает время на вспомогательные переходы повышает точность обработки снижает возможность появления брака появляется возможность многостаночного обслуживания.
Обработка на станке с ЧПУ ведется таким образом: сначала обрабатывается партия деталей по одной программе потом меняют программу и эту же партию деталей обрабатывают с другой стороны.
Горизонтально-расточной с ЧПУ 2В622Ф4
В базовом ТП на данных операциях использовались концевые фрезы с материалом режущей части ВК6 по ГОСТ. Данный материал применяется при обработке титановых сплавов по корке. Поэтому при черновом фрезеровании я применяю специальные твердосплавные фрезы повышенной жесткости с материалом режущей части ВК8 а при чистовой обработке – спец. фрезы повышенной жесткости с материалом режущей части Р18Ф2К8М (подробное обоснование выбора фрез новой конструкции рассмотрены в исследовательской части)
В существующем ТП на данных операциях обработка производилась на горизонтально-расточном станке 2636. Я меняю этот станок на станок с ЧПУ модели 2В622МФ3.
В данной операции я добавляю нарезание резьбы в отверстиях которое в базовом ТП проводилось на слесарной операции вручную.
Координатно-расточной 2А470
Т.к. на данной операции сверлятся глухие отверстия то нет возможности применить специальный комбинированный инструмент поэтому используется стандартный инструмент: сверла (ВК8 Р5М5); зенковка; метчики.
В данной операции я добавляю нарезание резьбы в отверстиях которое в базовом ТП проводилось на слесарной операции вручную.
Токарно-карусельный с ЧПУ 1516Ф3
Для нарезания резьбы в отверстиях на операции применяется токарный резьбовой резец с пластинами из твердого сплава ВК8 по ГОСТ.
В базовом ТП нарезание резьбы производится на токарно-карусельном станке 1516. Я применяю станок с ЧПУ 1512МФ3.
В базовом ТП для снятия заусенцев применяются: напильник 2820-0023 ГОСТ 1465-80; шабер. Производительность у такого инструмента очень низкая.
Я применяю шлифовальную ручную машинку В 228-П-6 и комплект насадных абразивных инструментов производительность этой машинки гораздо больше чем у напильника.
При контроле размеров используется стандартный инструмент (образцы шероховатости скобы штангенциркуль штангенглубиномер микрометр пробки гладкие и резьбовые калибры) и специальный (фаскомер шаблоны)
Произвожу сравнение базового технологического процесса и разработанного мной [7 с.39].
Стоимость механической обработки по базовому технологическому процессу:
Операция № 025. Токарно-карусельная. Обработка ведется на токарно-карусельном станке 1516; деталь устанавливается в 4-х кулачковый патрон. Цена станка 2200 тыс. руб. Габариты станка (длина х ширина х высота): 3190 х 3360 х 4100 мм. Мощность электродвигателя главного движения 30 кВт.
Норма штучного времени на операцию: Тшт = 53 мин.
Часовые приведенные затраты:
Сп3 = С3 + Счз + Ен (Кс + Кз)
где С3 – основная и дополнительная зарплата с начислениями руб.ч; Счз – часовые затраты по эксплуатации рабочего места руб.ч; Ен – нормативный коэффициент экономической эффективности капитальных вложений (в машиностроении Ен = 015); Кс Кз – удельные часовые капитальные вложения соответственно в станок и здание руб.ч.
Основная и дополнительная зарплата с начислениями и учетом многостаночного обслуживания:
где – коэффициент учитывающий дополнительную зарплату начисления на социальное страхование и приработок к основной зарплате в результате перевыполнения норм = 153 [c. 39]; Стф – часовая тарифная ставка станочника-сдельщика соответствующего разряда руб.ч Стф = 9271 руб.ч (станочник 5-го разряда);
k – коэффициент учитывающий зарплату наладчика k = 1 [с. 39] т.к. наладка выполняется самим рабочим; y – коэффициент учитывающий оплату рабочего при многостаночном обслуживании y = 1 [с. 40] т.к. на каждый станок по одному рабочему.
С3 = 153 · 9271 · 1 · 1 = 1418 руб.ч;
Часовые затраты по эксплуатации рабочего места:
где - часовые затраты на базовом рабочем месте в условиях двухсменной работы = 35 руб.ч – в серийном производстве [с.40]; Км – коэффициент показывающий во сколько раз затраты связанные с работой данного станка больше чем аналогичные расходы у базового станка Км = 49 [прил. 2 с. 148]; φ – поправочный коэффициент:
где α – доля постоянных затрат в себестоимости часовых на рабочем месте α = 057 [прил. 2 с. 148]; 3 – коэффициент загрузки станка 3 = 08 – для серийного производства;
Капитальные вложения в станок руб.ч:
где Ц – балансовая стоимость установки Ц = 2200000 · 11 = 2420000 руб; Fд – действительный годовой фонд времени работы станка Fд = 4029 ч;
Капитальные вложения в здание руб.ч:
где F – производственная площадь занимаемая станком с учетом проходов м2
где f – площадь станка в плане f = 319 336 = 1072 м2; kf – коэффициент учитывающий дополнительную производственную площадь проходов проездов и др. Кf = 2 для станка с площадью в плане свыше 10 до 20 м2 [с. 43];
F = 1072 · 2 = 2144 м2;
Сп3 = 1418 + 1715 + 015 · (75081+052) = 14403 руб.ч;
Технологическая себестоимость операции:
где Тшт (ш-к) – штучное или штучно-калькуляционное время на операцию; Кв – коэффициент выполнения норм Кв = 13 [3 с. 43].
Операция № 035. Токарно-карусельная. Обработка ведется на токарно-карусельном станке 1516; деталь устанавливается в 4-х кулачковый патрон. Цена станка 2200 тыс. руб. Габариты станка (длина х ширина х высота): 3190 х 3360 х 4100 мм. Мощность электродвигателя главного движения 30 кВт.
Норма штучного времени на операцию: Тшт = 86 мин.
где = 153 [c. 39]; Стф = 9271 руб.ч (станочник 5-го разряда); k = 1 [с. 39] т.к. наладка выполняется самим рабочим; y = 1 [с. 40] т.к. на каждый станок по одному рабочему.
где = 35 руб.ч – в серийном производстве [с.40]; Км = 49 [прил. 2 с. 148];
где α = 057 [прил. 2 с. 148]; 3 = 08 – для серийного производства;
где f = 319 336 = 1072 м2; kf = 2 для станка с площадью в плане свыше 10 до 20 м2 [с. 43];
Операция № 045. Токарно-карусельная. Обработка ведется на токарно-карусельном станке 1516; деталь устанавливается в специальное приспособление. Цена станка 2200 тыс. руб. Габариты станка (длина х ширина х высота): 3190 х 3360 х 4100 мм. Мощность электродвигателя главного движения 30 кВт.
Норма штучного времени на операцию: Тшт = 285 мин.
Операция № 055. Горизонтально-расточная. Обработка ведется на горизонтально-расточном станке 2636; деталь устанавливается в специальное приспособление. Цена станка 2600 тыс. руб. Габариты станка (длина х ширина х высота): 6960 х 5070 х 4805 мм. Мощность электродвигателя главного движения 37 кВт.
Норма штучного времени на операцию: Тшт = 640 мин.
где = 35 руб.ч – в серийном производстве [с.40]; Км = 44 [прил. 2 с. 148];
где α = 065 [прил. 2 с. 148]; 3 = 08 – для серийного производства;
где Ц – балансовая стоимость установки Ц = 2600000 · 11 = 2860000 руб; Fд – действительный годовой фонд времени работы станка Fд = 4029 ч;
где f = 696 507 = 3528 м2; kf = 15 для станка с площадью в плане более 20 м2 [с. 43];
F = 3528 · 15 = 5293 м2;
Сп3 = 1418 + 1567 + 015 · (88732+129) = 16314 руб.ч;
Операция № 065. Горизонтально-расточная. Обработка ведется на горизонтально-расточном станке 2636; деталь устанавливается в специальное приспособление. Цена станка 2600 тыс. руб. Габариты станка (длина х ширина х высота): 6960 х 5070 х 4805 мм. Мощность электродвигателя главного движения 37 кВт.
Норма штучного времени на операцию: Тшт = 838 мин.
Часовые приведенные затраты (из ранее рассчитанного):
Операция № 070. Горизонтально-расточная. Обработка ведется на горизонтально-расточном станке 2636; деталь устанавливается в специальное приспособление. Цена станка 2600 тыс. руб. Габариты станка (длина х ширина х высота): 6960 х 5070 х 4805 мм. Мощность электродвигателя главного движения 37 кВт.
Норма штучного времени на операцию: Тшт = 296 мин.
Операция № 090. Токарно-карусельная. Обработка ведется на токарно-карусельном станке 1516; деталь устанавливается в специальное приспособление которое закрепляется на угольнике. Цена станка 2200 тыс. руб. Габариты станка (длина х ширина х высота): 3190 х 3360 х 4100 мм. Мощность электродвигателя главного движения 30 кВт.
Норма штучного времени на операцию: Тшт = 64 мин.
Стоимость механической обработки по разработанному технологическому процессу:
Операция № 025. Токарно-карусельная. Обработка ведется на токарно-карусельном станке 1512; деталь устанавливается в 4-х кулачковый патрон. Цена станка 1700 тыс. руб. Габариты станка (длина х ширина х высота): 2875 х 2660 х 4100 мм. Мощность электродвигателя главного движения 30 кВт.
Норма штучного времени на операцию: Тшт = 6538 мин.
где = 35 руб.ч – в серийном производстве [с.40]; Км = 36 [прил. 2 с. 148];
где α = 041 [прил. 2 с. 148]; 3 = 08 – для серийного производства;
где Ц – балансовая стоимость установки Ц = 1700000 · 11 = 1870000 руб; Fд – действительный годовой фонд времени работы станка Fд = 4029 ч;
где f = 2875 2660 = 765 м2; kf = 25 для станка с площадью в плане свыше 10 до 20 м2 [с. 43];
F = 765 · 25 = 19125 м2;
Сп3 = 1418 + 1216 + 015 · (58014+046) = 11342 руб.ч;
Операция № 030. Токарно-карусельная. Обработка ведется на токарно-карусельном станке с ЧПУ 1512МФ3; деталь устанавливается в специальное приспособление. Цена станка 3000 тыс. руб. Габариты станка (длина х ширина х высота): 4260 х 3610 х 5615 мм. Мощность электродвигателя главного движения 42 кВт.
Норма штучного времени на операцию: Тшт = 19586 мин.
где Ц – балансовая стоимость установки Ц = 3000000 · 11 = 3300000 руб; Fд – действительный годовой фонд времени работы станка Fд = 4029 ч;
где f = 426 361 = 1538 м2; kf = 2 для станка с площадью в плане свыше 10 до 20 м2 [с. 43];
F = 1538 · 2 = 3076 м2;
Сп3 = 1418 + 1216 + 015 · (102383+075) = 18003 руб.ч;
Операция № 040. Горизонтально-расточная. Обработка ведется на горизонтально-расточном станке с ЧПУ 2В622МФ3; деталь устанавливается в специальное приспособление. Цена станка 3000 тыс. руб. Габариты станка (длина х ширина х высота): 6070 х 3950 х 3200 мм.
Норма штучного времени на операцию: Тшт = 46623 мин.
где = 35 руб.ч – в серийном производстве [с.40]; Км = 31 [прил. 2 с. 148];
где α = 056 [прил. 2 с. 148]; 3 = 08 – для серийного производства;
где f = 607 395 = 2397 м2; kf = 15 для станка с площадью в плане более 20 м2 [с. 43];
F = 2397 · 15 = 3596 м2;
Сп3 = 1418 + 1085 + 015 · (102383+087) = 17873 руб.ч;
Операция № 050. Горизонтально-расточная. Обработка ведется на горизонтально-расточном станке с ЧПУ 2В622МФ3; деталь устанавливается в специальное приспособление. Цена станка 3000 тыс. руб. Габариты станка (длина х ширина х высота): 6070 х 3950 х 3200 мм.
Норма штучного времени на операцию: Тшт = 67443 мин.
Операция № 055. Горизонтально-расточная. Обработка ведется на горизонтально-расточном станке с ЧПУ 2В622МФ3; деталь устанавливается в специальное приспособление. Цена станка 3000 тыс. руб. Габариты станка (длина х ширина х высота): 6070 х 3950 х 3200 мм.
Норма штучного времени на операцию: Тшт = 20081 мин.
Операция № 075. Токарно-карусельная. Обработка ведется на токарно-карусельном станке с ЧПУ 1512Ф3; деталь устанавливается в специальное приспособление которое закрепляется на угольник. Цена станка 3000 тыс. руб. Габариты станка (длина х ширина х высота): 4260 х 3610 х 5615 мм. Мощность электродвигателя главного движения 42 кВт.
Норма штучного времени на операцию: Тшт = 4163 мин.
Остальные операции по базовому и спроектированному технологическому процессу одинаковые.
Все расчету свожу в таблицу 1.5.
Сравнение вариантов ТП и методов получения заготовки
Наименование позиции
Отличающиеся виды заготовки
Стоимость заготовки руб.
Отличающиеся операции механической обработки
Технологическая себестоимость обработки руб.
5. Токарная обдирочная обработка на токарно-карусельном станке 1516
5. Токарная черновая на токарно-карусельном станке 1516.
5. Токарная черновая на токарно-карусельном станке 1512.
0. Токарная чистовая на токарно-карусельном станке 1516.
0. Токарная чистовая на токарно-карусельном станке с ЧПУ 1512Ф3.
5. Фрезерная черновая обработка на горизонтально-расточном станке 2636.
0. Фрезерная черновая обработка на горизонтально-расточном станке с ЧПУ 2В622МФ3.
5. Фрезерная чистовая обработка на горизонтально-расточном станке 2636.
0. Фрезерная чистовая обработка на горизонтально-расточном станке с ЧПУ 2В622МФ3.
0. Фрезерная обработка на горизонтально-расточном станке 2636.
5. Фрезерная обработка на горизонтально-расточном станке с ЧПУ 2В622МФ3.
0. Нарезание резьбы на токарно-карусельном станке 1516.
5. Нарезание резьбы на токарно-карусельном станке с ЧПУ 1512Ф3.
Технологическая себестоимость обработки по вариантам руб.
Остальные операции по обоим вариантам одинаковы
Годовой экономический эффект по технологическим операциям рассчитываю по формуле:
где ΣСО1 и ΣСО2 – общая технологическая себестоимость обработки изделия соответственно по 1-му и 2-му варианту ТП; N – программа выпуска N = 100 шт.
Эг = (13451179 – 5077776) 100 = 8373403 руб.
Из данных расчетов видно что применение второго варианта обработки изделия обеспечивает годовой экономический эффект в 8373403 руб. при этом экономится 150 кг титанового сплава ОТ4. Поэтому следует отдавать предпочтение этому варианту и принять его к подробной разработке.
Конструкторская часть.
1. Разработка токарно-карусельного приспособления.
Приспособление разработано для чистовой обработки на токарно-карусельном станке с ЧПУ 1512МФ3. Приспособление устанавливается на планшайбу станка.
По своему назначению приспособление является специальным т.к. в собранном виде рассчитано на установку и закрепление однотипных деталей. Приспособление собирается из отдельных нормализованных и стандартизованных узлов и деталей. Достоинством приспособления является несложность сборки и экономичность оснащения.
Заготовка базируется главной базой (торцем и наружным диаметром) на опорную пластину (основание) которая крепится к планшайбе станка. В качестве зажимного устройства используется винтовой Г-образный прихват (см. чертеж).
При обработке проточек и канавок и наружных поверхностей применяется второй вариант крепления детали при котором заготовка зажимается по верхнему торцу и внутреннему диаметру прижимом.
Точность размеров выполняемых на данной операции не зависит от приспособления. Т.к. операция выполняется на станке с ЧПУ поэтому заданная точность размеров будет обеспечиваться аттестованной программой.
2. Приспособление расточное.
2.1. Описание и принцип действия приспособления.
Приспособление разработано для обработки на горизонтально-расточном станке с ЧПУ 2В622МФ3. Приспособление устанавливается на стол станка. На данной операции выполняется фрезерование внутреннего контура карманов.
В базовом ТП в конструкции приспособления в качестве зажимного устройства использовался прихват в виде кольца который зажимал деталь по одной поверхности. Мною предложено заменить кольцо на «Г-образный» прихват что позволяет:
закрепить деталь по трем поверхностям;
обеспечить возможность регулировки положения прихвата по высоте;
при смене заготовок нет необходимости снимать прихват достаточно повернуть его в сторону.
Заготовка базируется торцем и наружным диаметром на опорную пластину (подставку) которая крепится на стол станка (рис. 1).
2.2. Расчет силы закрепления детали в приспособлении
– гайка 2 – прихват 3 – винт; 4 – пружина; 5 - стакан
Рис. 1. Схема установки детали в приспособление.
В конструкции приспособления применяется винтовой зажим (г-образный прихват). Элементами зажимного устройства являются гайка и прихват.
Ведущим звеном зажима является гайка а ведомым – винт которым развивается сила зажима Q.
где М – момент закрепления зажима
где М1 – составляющая момента которая необходима для обеспечения силы зажима Q Мтр – момент трения между гайкой и прихватом.
М1 = Р · r · tg(α + ρ)
где Р – осевая сила r – средний радиус резьбы r = 045 d = 045 · 12 = 54 мм; α – угол подъема винта α = 3о10'; ρ – приведенный угол трения в резьбе ρ = 10о30.
где f – коэффициент статического трения скольжения f = 016; D – наружный диаметр гайки D = 24 мм; d – внутренний диаметр гайки d = 16 мм.
Зависимость между силой зажима Q и осевой силой Р определяется из равенства моментов относительно точки О т.е. Р · l = 23 · N · L. В этом равенстве силы реакции опоры N представляют собой равнодействующие сил стремящихся перекосить прихват под действием осевой силы Р.
По закону силовых треугольников равнодействующие N приложены к прихвату на расстоянии равном L3.
Таким образом из указанного равенства моментов следует N = .
С другой стороны сила Р = Q + F где F – сила трения относящаяся к напраляющей части прихвата F = 2Nf. Подставляя в это равенство значение N получим
F = но Q = P – F следовательно Q = отсюда Р = .
Тогда момент будет равен М = .
Для решения уравнения найдем момент резания при фрезеровании карманов [5 с.290]:
где РZ – окружная сила при фрезеровании; D –диаметр фрезы D = 24 мм;
где Ср= 82 х=075; y = 06; n=10; q = 086; w=0 [5 табл. 41 с.291]; Кмр – поправочный коэффициент учитывающий качество обрабатывающего материала Кмр = 10 [5 табл.50с.298]; z – количество зубьев z = 4; n – частота вращения фрезы n =320 обмин; В – ширина фрезерования В = 2 мм.
Коэффициент запаса К определяется по формуле
К0–гарантированный коэффициент запаса К0=1.5; К1–характеризует наличие случайных неровностей на обработанной поверхности при выполнении операций чистовой обработки К1=1; К2–характеризует увеличение сил резания вследствие прогрессирующего затупления рабочего инструмента К2=1.5 ( материал заготовки жаропрочный сплав операция фрезерования); К3–характеризует привод зажимного устройства конструкции приспособления К3=13 (при ручном закреплении заготовок); К4–характеризует прерывистость обработки К4=1(при отсутствии прерывистой обработки ); К5–характеризует удобство расположения рукояток в ручных зажимных устройствах К5=1 ( α=3690º ); К6–характеризует наличие моментов стремящихся сместить либо развернуть заготовку относительно установочных элементов К6=15 (при наличии таких моментов).
Т.к. на приспособлении установлено 4 зажимных устройства то сила на один зажим равна Qo = Q 4 = 4178 4 = 10445 кН.
По найденной силе зажима нахожу диаметр винта d:
где с – постоянная зависящая от типа резьбы винта для метрической резьбы с = 14; [] – допускаемое напряжение на растяжение материала винта [] = 280 МПа [9 с.391]. Тогда расчетный диаметр винта:
Принимаю стандартный диаметр винта d = 10 мм.
3. Приспособление для нарезания резьбы.
3.1. Описание и принцип действия приспособления.
Для нарезания резьбы в детали спроектировано специальное приспособление которое устанавливается на токарно-карусельный станок.
Заготовка базируется на опорную пластину приспособления (основание) и зажимается прижимом по торцу и внутреннему диаметру (см. чертеж). В качестве корпуса приспособления используется угольник который крепится на стол станка.
При нарезании резьбы в заготовке выдерживается два размера: М80х1-7Н и 51±08. Приспособление не влияет на точность этих размеров т.к. размер М80х1-7Н будет обеспечиваться инструментом а размер 51±08 – аттестованной программой.
4. Контрольное приспособление
4.1. Описание и принцип действия приспособления.
Для измерения фасок в детали было спроектировано контрольное приспособление – фаскомер. Приспособление позволяет измерять фаски под углом 30о и 45о с допуском не менее 05 мм.
Приспособление состоит из корпуса 1 в котором перемещается движок 2. Движок имеет две измерительные поверхности В и Г расположенные под углом 45о и 30о соответственно. На поверхности движка нанесена измерительная шкала с ценой деления 1 мм. К корпусу приспособления крепятся две планки 3 и 4. Нижняя планка 3 имеет измерительную шкалу с ценой деления 01 мм. Верхняя планка 4 является направляющей для прямолинейного перемещения движка. Перемещение движка осуществляется за счет поджатия пружины 5 винтом 6.
Проверяемая деталь устанавливается на базовые поверхности приспособления Б (для фаски под углом 45о) или Д (для фаски пол углом 30о) которые при «нулевом положении» должны пересекаться в одной точке с поверхностями В и Г соответственно (отклонение не более 005 мм).
Измерение фаски производится при совмещении поверхностей приспособления В и Г с поверхностью измеряемой фаски. Величину фаски определяют по шкале.
1. Основные фонды цеха (основной капитал).
Стоимость зданий и сооружений:
Фзд = Sосн × Спр + SБК × Сбк = 6258·10000 + 152424·11000 = 79346640 руб.
где Sосн = 6258 м2 – площадь производственного корпуса; SБК = 152424 м2 – площадь вспомогательного корпуса; Спр – стоимость 1 м2 промышленных зданий руб.; Сбк – стоимость 1 м2 бытовых помещений руб.;
Стоимость силового оборудования и машин:
Фс = Nу ×Сэ=(6282+765) × 2405 = 152921925 руб.
Nу – вся установленная мощность электродвигателей в цехе кВт (по табл. 1 2);
Сэ – стоимость 1 кВт установленной мощности электродвигателей руб.
Стоимость технологического оборудования (по табл. 1):
Фсто = 409798037 руб.
Стоимость вспомогательного оборудования (по табл. 2):
Стоимость подъёмно-транспортного оборудования:
Капитальные вложения в транспортные средства принимаются в размере 10% от первоначальной стоимости технологического (основного) оборудования.
Фпто = 01×409798037 = 409798037 руб.
Стоимость технологической оснастки:
Стоимость технологической оснастки принимается укрупнёно в размере 10% от первоначальной стоимости технологического (основного) оборудования.
Фто = 01×409798037 = 40978037 руб.
Стоимость производственного и хозяйственного инвентаря:
Стоимость производственного и хозяйственного инвентаря принимается в размере 15 % от первоначальной стоимости технологического (основного) оборудования.
Фпхи = 0015×409798037 = 61469705 руб.
Результаты расчётов сводятся в табл. 3.1
Наименование основных фондов
Первоначальная стоимость руб.
Отчисления в ремонтный фонд (25%) руб.
Амортизационные отчисления
Силовое оборудование и машины
Рабочие машины и оборудование:
Транспортные средства
Инструменты и приспособления
Производственный и хоз. инвентарь
2. Себестоимость продукции.
Переменные затраты – затраты на основные материалы покупные комплектующие изделия зарплата основных производственных рабочих с отчислениями на социальные нужды. Постоянные затраты – расходы на содержание и эксплуатацию оборудования.
3 Затраты на основные материалы
Затраты на основные материалы определяются исходя из норм расхода материала на деталь цены весовой единицы материала с учётом транспортно-заготовительных расходов и данных о количестве и стоимости возможных отходов.
Планово-заготовительные цены на материалы определяются по действующим прейскурантам с добавлением к ним транспортно-заготовительных расходов (7%). Расчёт ведётся табличным методом .
Расчёт затрат на основные материалы.
Планово-заготовительная цена руб.кг.
Приведённая программа цеха
Общая потребность в материалах
Стоимость основных материалов за вычетом отходов руб.
4 Расчёт фондов заработной платы рабочих.
Существуют фонды заработной платы: тарифный часовой дневной и годовой.
Фонд заработной платы рабочих сдельщиков:
где Nв – приведённая программа цеха шт; t Cчас–часовая тарифная ставка рабочего-сдельщика соответствующая разряду выполняемой работы рубч; n – количество операций выполняемых рабочими данной профессии и разряда.
Фонд заработной платы рабочих повременщиков:
где Cчас– часовая тарифная ставка рабочего-повременщика соответствующая разряду выполняемой работы рубч; Фэ – эффективный фонд времени рабочего ч;
Рвсп– списочная численность рабочих-повременщиков данной профессии и разряда.
Тарифные ставки для рабочих промышленных и непромышленных групп действующие на НПО “Искра” с 01. 01. 2003 г. по 31. 12. 2003 г.
Фонд заработной платы токарей (5 разряд).
Счас = 10008 рубч Nпр=2500 tток = 1046 + 4064 = 511 ч.
Фонд заработной платы расточников (5 разряд).
Счас = 10008 рубч; tраст. = 22494 ч.
Фонд заработной платы расточников (4 разряд).
Счас = 8896 рубч; tсв = 4466 ч.
Вспомогательные рабочие.
Фонд заработной платы рабочих-повременщиков 5-го разряда (станочники по ремонту станочники отделения РПИН наладчики станков с ЧПУ ИТР):
Счас= 9028 рубч.; Фэ=1654 ч.; Рвсп = 67 чел.
Звсп 5 = Счас · Фэ · Рвсп = 9028 · 1654 · 67 = 10004649 руб.
Фонд заработной платы рабочих-повременщиков 4-го разряда (слесари по ППР и межремонтному обслуживанию смазчики электрики слесари отделения РПИН контролёры):
Счас = 8025 рубч.; Рвсп = 85 чел.
Звсп 4 = 8025 · 1654 · 85 = 112823475 руб.
Фонд заработной платы рабочих-повременщиков 3-го разряда (транспортные рабочие распределители работ кладовщики раздатчики инструмента служащие МОП):
Счас = 7078 рубч; Рвсп = 56 чел.
Звсп 3 = 7078 · 1654 · 56 = 6555927 руб.
Фонд заработной платы рабочих-повременщиков 2-го разряда (уборщики производственных помещений ученики):
Счас = 6242 рубч.; Рвсп = 15 чел.
Звсп 2 = 6242 · 1654 · 15 = 15486402 руб.
Фонд часовой зарплаты определяется суммированием тарифного фонда зарплаты и всех доплат входящих в часовой фонд.
К числу доплат до часового фонда заработной платы относятся:
а) премии по сдельно-премиальной и повременно-премиальной системам оплаты
б) доплата за условия труда;
в) доплата за многостаночное обслуживание и совмещение профессий;
г) доплата за работу в вечернюю и ночную смены и др.
Процент премий и доплат принять равным 50% для основных рабочих и 40% - для вспомогательных.
Зчас= Зр+ Зр × %Прем 100%
Дневной фонд зарплаты рассчитывается путём суммирования часового фонда и доплат до дневного фонда.
Здн= Зчас+ Зчас × %Прем 100%
Годовой фонд рассчитывается путём суммирования дневного фонда и доплат до годового фонда.
Згод= Здн+ Здн × %Прем 100%
Доплаты до дневного и годового фонда принимаются равными 10%.
Результаты расчёта сводятся в табл.9.
Расчёт фонда заработной платы производственных рабочих.
Вспомогательные рабочие
Количество н. ч. на программу
Часовые тарифные ставки руб.
Фонд прямой зп рабочих
ИТОГО тарифный фонд зп
Доплаты до основного фонда
ИТОГО основной фонд зп
Доплаты до дневного фонда
ИТОГО дневной фонд зп
Доплаты до годового фонда
ИТОГО годовой фонд зп
ВСЕГО годовой фонд зп
Среднегодовая зп рабочего
Распределение фонда заработной платы и отчислений на
социальные нужды по статьям калькуляции.
Количество работающих
Категория работающих
Сумма отчислений на социальные нужды (356%)
Сумма фонда зп и суммы отчислений на соц. нужды
Зарплата основных рабочих
Расходы на содержание и эксплуатацию оборудования:
Дежурный персонал наладчики смазчики и др.
Слесари станочники по ремонту
Транспортные рабочие
- износ малоценных и быстро изнашивающихся инструментов
Слесари станочники РПИН
Контролёры ОТК распорядители работ кладовщики
Вспомогательные рабочие ученики МОП
Уборщики производственных помещений
Фонд зарплаты соответствующих категорий рабочих по статьям калькуляции определяется исходя из среднегодовой зарплаты одного вспомогательного рабочего и численности данной категории рабочих.
5 Расходы на содержание и эксплуатацию оборудования (РСЭО).
Смета РСЭО составляется табличным методом (табл. 11) с учётом результатов ранее проведённых расчётов. Расходы на вспомогательные эксплуатационные материалы определяются в размере 05% от стоимости технологического
Затраты на силовую электроэнергию.
Суммарная мощность электродвигателей технологического и вспомогательного оборудования цеха: Ny = 63585 кВт; средний коэффициент загрузки электродвигателей по мощности Км = 08; средний коэффициент загрузки электродвигателей по времени Кз = 06; коэффициент одновременной работы электродвигателей Код = 08; коэффициент потерь электроэнергии в сети Кw = 106; кпд электродвигателей = 08; стоимость 1 кВтч электроэнергии Сэл = 065 руб.
Затраты на сжатый воздух для технологических нужд.
При расчёте потребности в сжатом воздухе укрупнено принимается: количество станков подлежащих обдувке – 138 × 02 = 21 станков; расход сжатого воздуха на станок Qчас ст =1 м3ч на пневмозажим Qчас пз =015 м3ч на пневмоинструмент Qчас пи = 4 м3ч средний коэффициент загрузки оборудования Кз=094 стоимость 1000 м3 сжатого воздуха Свозд=150 руб.
Потребность в режущем и мерительном инструменте определяется укрупнено исходя из среднего расхода на 1 рабочего 5000 руб.год.
Смета расходов на содержание и эксплуатацию оборудования цеха.
Амортизация на полное вос-
становление оборудования и
транспортных средств доро-
гостоящего инструмента
Амортизационные отчисления на полное восстановление по действующим нормам от первоначальной стоимости силового основного вспомогательного оборудования транспортных средств дорогостоящего инструмента
Эксплуатация оборудования
(кроме расходов на ремонт)
Затраты на вспомогательные эксплуатационные материалы.
Стоимость электроэнергии и сжатого воздуха
Зарплата с отчислениями на социальные нужды вспомогательных рабочих обслуживающих оборудование
оборудования транспортных
средств дорогостоящей
Отчисления в ремонтный фонд
Внутрицеховое перемещение
Зарплата с отчислениями на социальные нужды транспортных рабочих
Затраты по эксплуатации транспорта
быстроизнашивающихся
Сумма износа малоценных и быстроизнашивающихся инструментов и приспособлений
Расходы по восстановлению и ремонту
Зарплата с отчислениями на социальные нужды контролёров ОТК распределителей работ кладовщиков и др. исключая уборщиков производственных помещений
ВСЕГО расходов по эксплуатации и содержанию оборудования
Расчёт общепроизводственных общехозяйственных и
внепроизводственных расходов.
Общепроизводственные расходы связаны с обслуживанием и управлением производством. Рассчитываются укрупнено в размере 500% от основной зп основных производственных рабочих. Общехозяйственные расходы равны 400% от основной зп основных производственных рабочих. Внепроизводственные расходы равны 2% от заводской себестоимости товарной продукции.
Калькуляция себестоимости продукции.
Наименование статей расхода
ИТОГО прямых материальных затрат
Основная зарплата основных рабочих
Дополнительная зарплата основных рабочих
Отчисления на социальные нужды
ИТОГО переменных затрат
Расходы на содержание и эксплуатацию оборудования
Общепроизводственные расходы
Общехозяйственные расходы
Производственная себестоимость
Внепроизводственные расходы
ИТОГО постоянные затраты
Полная себестоимость
6 Оборотные средства (оборотный капитал)
Величина оборотного капитала определяется по всем видам нормируемых оборотных средств.
Затраты на материал Ом = 695344125 руб.; величина планируемого периода в днях Тп = 365; норматив запаса материала в днях Нм = 15; себестоимость годового
объёма продукции С = 8459716941 руб.; норматив на незавершенное производство в днях Ннзп = 5; норматив запаса готовой продукции в днях Нгп=7
7 Производственный капитал
где Оск берется из табл. 7 тогда производственный капитал будет равен:
Пк = 5475611222 + 5638855398 = 60394967618 руб.
8 Определение цены единицы продукции.
Сед = 5639811 руб.; Rent = 015 · Сед = 845972 руб.;
НДС = 02·(Сед + Rent) = 1297156 руб.;
Цед = Сед + Rent + НДС = 5639811+845972+1297156=7782939 руб.
Расчет плановой суммы прибыли
Расчет плановой суммы балансовой прибыли
Выручка от реализации: Цед×Nпр
82939×15000 =1167440850 руб.
НДС (расчётная ставка 16)
Прибыль от реализации
Доходы от иной деятельности
ИТОГО: балансовая прибыль
Расчёт чистой прибыли
Налоги из балансовой прибыли.
Величина налога руб.
Налог на имущество 2%
(5475611222 - 4272391633) × 002 = 1009674412
Налог на содержание милиции 3%
0 × 469 ·12 · 003 = 16884
Налог на образование 1%
(989326343 + 572577048) × 001 = 15619034
Налог на прибыль 24%
(1268956809 - 1009674412 -16884 -15619034) ×024 = 2799385393
68956809 - 3824847679 = 8864720411
Формирование баланса доходов и расходов
Баланс доходов и расходов.
Доходы и поступление средств
Расходы и отчисления средств
Прибыль от реализации продукции
Доходы от внереализацонной деятельности
Безубыточный объём производства продукции (график безубыточности)
где Зпост – постоянные затраты определенные на объем производства
Зпост = 13721230389 руб.; Зпер – переменные затраты на единицу продукции
Зпер = 4725063 руб.; Цед = 7782939 руб.
10. Рентабельность проекта и технико-экономические показатели
Рентабельность производственного капитала и продукции.
Пбаланс. = 1268956809 руб.; Пк = 60394967618 руб.; С = 8459716941 руб.
Результаты расчётов.
Технико-экономические показатели цеха.
Значение показателей
Годовая приведённая программа
Трудоёмкость единицы продукции
Количество ед. технологического оборудования
Стоимость основного капитала
Себестоимость ед. продукции в т. ч.
- переменные затраты
- постоянные затраты
Цена единицы продукции
Выручка от реализации
Средняя зарплата рабочего:
- рентабельность производственного капитала
- рентабельность продукции
Охрана труда и безопасность проекта
Основными требованиями безопасности предъявляемыми к конструкции машин и механизмов являются безопасность для здоровья и жизни человека надежность удобство эксплуатации.
Безопасность производственного оборудования должна обеспечиваться:
-выбором принципов действия конструктивных схем безопасных элементов конструкции;
-применением в конструкции средств механизации автоматизации и дистанционного управления;
-применением в конструкции средств защиты;
-выполнением эргономических требований;
-включением требований безопасности в техническую документацию по монтажу эксплуатации ремонту транспортированию и хранению;
-применением в конструкции соответствующих материалов.
Предупреждение травмирования движущимися частями станка обрабатываемой деталью и режущим инструментом предупреждение глазных травм отлетающей стружкой и порезов ленточной стружкой обеспыливание требуют серьезного внимания особенно на универсальных и специальных станках.
Производственный травматизм и профессиональные заболевания – это сложные многофакторные явления обусловленные действием на человека в процессе его трудовой деятельности опасных (вызывающих травмы) и вредных (вызывающих заболевания) факторов.
Защита от опасных производственных факторов
Движущиеся и вращающиеся части производственного оборудования
Применяются два основных метода защиты персонала от потенциально опасных технических объектов:
Обеспечение недоступности к опасно действующим частям оборудования. Этот метод состоит в пространственном или временном разделении рабочей и опасной зоны к нему относится всё что связано с конструктивными особенностями как самих машин и оборудования так и устройств ограждающих и блокирующих опасные зоны.
Применение приспособлений непосредственно защищающих человека от опасного производственного фактора: дистанционное управление а также устройства автоматически прекращающие работу оборудования или подачу энергии в систему.
Средства достижения безопасности:
Средства коллективной защиты (СКЗ) обеспечивающие защиту всех рабочих и исследователей на участке. К ним относятся:
-звуковая и световая сигнализации;
-использование тормозных и выключающих устройств.
Средства индивидуальной защиты (СИЗ) повышающие защитные
свойства человека или отдельных его органов. К ним относятся:
-специальная одежда;
-защитные каски; маски;
-защитные устройства от вибраций и шума.
При назначении СКЗ и СИЗ необходимо выполнять или руководствоваться требования ниже перечисленных ГОСТов:
ГОСТ 12.2.003 – 91 ССБТ. «Оборудование производственное. Общие
требования безопасности».
ГОСТ 12.2.009 – 99 ССБТ. «Станки металлообрабатывающие. Общие требования безопасности».
ГОСТ 12.2.049 – 80 ССБТ. «Оборудование производственное. Общие эргономические требования».
ГОСТ 12.2.061 – 81 ССБТ. «Оборудование производственное. Общие
требования безопасности к рабочим местам».
ГОСТ 12.3.002 – 75 ССБТ. «Процессы производственные. Общие требования безопасности».
ГОСТ 12.4.026 – 2001 ССБТ. «Цвета сигнальные и знаки безопасности».
ГОСТ 12.1.003 – 83 ССБТ. «Шум. Общие требования безопасности».
ГОСТ 12.1.012 – 90 ССБТ. «Вибрационная безопасность. Общие требования безопасности».
ГОСТ 12.2.007.1 – 75 ССБТ. «Машины электрические вращающиеся. Требования безопасности».
ГОСТ 12.2.062 – 81 ССБТ. «Оборудование производственное. Ограждения защитные. Общие требования безопасности».
Погрузочно-разгрузочные работы на участке транспортировка заготовок
Поскольку масса детали примерно 666 кг и при установке на станок или стойки используется кран необходимо соблюдать следующие требования безопасности к погрузочно – разгрузочным работам:
ГОСТ 12.3.002 – 75 ССБТ. «Процессы производственные. Общие требования безопасности»
ГОСТ 12.3.009 – 76 ССБТ «Работы погрузочно-разгрузочные. Общие требования безопасности»
ГОСТ 12.3.010 – 82 ССБТ «Тара производственная. Требования безопасности при эксплуатации»
ГОСТ 12.3.020 – 80 ССБТ «Процессы перемещения грузов на предприятиях. Общие требования безопасности»
ГОСТ 12.3.021 – 80 ССБТ «Работы погрузочно-разгрузочные в портах. Требования безопасности»
ГОСТ 19433 – 88 ССБТ Грузы опасные. Классификация. Знаки опасности».
При защите от данного фактора могут использоваться средства защиты перечисленные для предыдущего фактора.
Для обеспечения безопасности при перемещении заготовок и готовых изделий следует всемерно стремиться к механизации межоперационных транспортных операций.
Для предупреждения аварий и травм во время эксплуатации все грузоподъёмные машины оборудуют предохранительными и блокировочными устройствами. К ним относятся:
-концевые выключатели
- предохранительные щиты
-ограничители грузоподъёмности
-указатели грузоподъёмности
-сигнальные приборы
-ограждения и другие устройства.
Стружка обрабатываемых материалов и осколки инструментов
Организация и выполнение технологических процессов обработки резанием должны соответствовать требованиям
ГОСТ 12.3.025 – 80 ССБТ «Обработка металлов резанием. Требования безопасности»
ГОСТ 12.2.009 – 99 ССБТ «Станки металлообрабатывающие».
Стружку от станков и рабочих мест необходимо убирать в специальную металлическую тару по возможности необходимо механизировать этот процесс. В местах хранения должны быть средства пожаротушения.
Так же рабочие и служащие цехов и участков обработки резанием должны быть обеспечены спецодеждой спец обувью и предохранительными приспособлениями в соответствии с «Типовыми отраслевыми нормами». Средства индивидуальной защиты применяемые при обработке резанием должны соответствовать требованиям ГОСТ 12.4.011 – 89 «Средства защиты работающих. Классификация».
Для защиты кожного покрова от воздействия пыли токсичных металлов следует применять дерматологические защитные средства (пасты мази биологические перчатки) по ГОСТ 12.4.064 – 84 (ГОСТ Р 12.4.196-99 ССБТ «Костюмы изолирующие. Общие технические требования и методы испытаний»).
Высокая температура поверхности обрабатываемых деталей и инструмента
Мероприятием по защите от этого фактора будет являться наличие предупреждающего знака или плаката говорящего о том что при обработке резанием выделяется значительное количество теплоты или о том что работать необходимо в рукавицах.
В целях безопасности необходимо использовать знак с поясняющей надписью «Осторожно! Скользко». Мероприятиями будут немедленная уборка производственных помещений и разработка и изготовление таких конструкций станков и оснащения станков которые исключают опасность для работающего поскользнуться споткнуться и упасть.
Физические перегрузки (статические динамические)
Защитой от данного опасного фактора является автоматизация и механизация производственного процесса (применение подъёмников кранов транспортёров и другой техники) правильная организация рабочего места. Его организация должна выполняться в соответствии с ГОСТ 12.2.032 – 78 ССБТ «Рабочее место при выполнении работ сидя. Общие эргономические требования» ГОСТ 12.2.033 – 78 ССБТ «Рабочее место при выполнении работ стоя. Общие эргономические требования» ГОСТ 12.2.049 – 80 ССБТ «Оборудование производственное. Общие эргономические требования» ОСТ 2Н08 – 1-86 «Станки металлорежущие. Общие требования технической эстетики и эргономики»
Повышенная загазованность парами бензина Б-70 ТУ 38-101.913-82
К основным средствам индивидуальной защиты можно отнести:
Приспособления для закрепления деталей
ГОСТ 12.2.009-99 ССБТ «Станки металлообрабатывающие. Общие требования безопасности» предусматривает требования к устройствам для установки закрепления деталей и инструмента на станках.
В частности вращающиеся устройства (патроны поводки планшайбы и др. должны иметь гладкие наружные поверхности а при наличии выступающих частей или углублений они должны иметь ограждения.
Повышенное напряжение в электрической цепи или статического электричества
Повышенное напряжение вызывает замыкание через тело человека.
Основной способ защиты от статического электричества заземление оборудования сосудов и коммуникаций в которых накапливается статическое электричество использование специальной обуви с электропроводящей подошвой и другие средства защиты.
Основными мерами защиты от поражения электрическим током являются:
-обеспечение недоступности токоведущих частей
-электрическое разделение сети
-использование двойной изоляции выравнивание потенциала использование защитного заземления защитного отключения
-применение специальных электрозащитных средств – переносных приборов и приспособлений (ЭС)
-организация безопасной эксплуатации электроустановок.
Электрозащитные средства делят на:
-основные: диэлектрические резиновые перчатки инструмент с изолирующими рукоятками с указателем напряжения до 1000 В.
-дополнительные: диэлектрические галоши ковры и изолирующие подставки.
Ограждающие: щиты ограждения – клетки изолирующие накладки и колпаки предупредительные плакаты устройства временного заземления.
Предохранительные: респираторы очки рукавицы и т.д.
Исправность средств защиты должна проверяться осмотром перед каждым их применением а также периодически через 6 12 месяцев.
Защита от вредного производственного фактора
Повышенная запылённость и загазованность воздуха рабочей зоны
Мероприятия по борьбе с пылью на данном производстве и её вредным влиянием на организм человека производятся по следующим направлениям:
Рационализация технологического процесса устраняющая образование пыли.
Автоматизация процессов при которых образуется пыль.
Применение СОЖ в качестве смачивания обработанной поверхности.
Применение пылеудаляющей вентиляции вентиляции общего и местного назначения.
Немедленная уборка помещений.
Обеспечение рабочих противопылевой спецодеждой респираторами очками и другими средствами защиты.
Создание на предприятии условий для выполнения мероприятий личной гигиены.
Содержание вредных веществ в воздухе регламентируетсяГОСТ12.1.005 – 88 ССБТ «Общие санитарно – гигиенические требования к воздуху рабочей зоны».
Высокий уровень шума и вибрации
Основные источники шума и вибраций в металлорежущих станках – динамические нагрузки в зубчатых передачах возникающие вследствие определенных погрешностей их изготовления переменность нагрузки воспринимаемой шариками или роликами в подшипниках качения динамические удары шариков или роликов о неровности поверхности беговых дорожек наружного и внутреннего колец подшипников и т.п.
Следовательно основными путями снижения вибраций и шума металлорежущих станков являются:
-применение высококачественных подшипников
- малошумных зубчатых передач и электродвигателей
-соблюдение технологической дисциплины при изготовлении и сборке узлов станка
-применение рациональных конструкций режущего инструмента и приспособлений жесткость их крепления и т. д.
Методы средства борьбы с шумом принято подразделять на:
-методы снижения шума в источнике его образования;
- методы снижения шума на пути его распространения СИЗ от шума.
Снижения шума в источнике его образования достигается путём:
-конструктивного изменения источника
- повышением качества балансировки
-повышением точности изготовления деталей;
-улучшением класса чистоты трущихся поверхностей и т.д.
Методы снижения шума на пути его распространения включают:
-акустическую обработку помещений (применение звукопоглощающих устройств);
-изоляцию источников шума или помещений от шума проникающего из вне (звукоизолирующие ограждения кожухи кабины экраны средства виброизоляции);
-применение глушителей шума.
К СИЗ от шума относят:
-противошумные вкладыши наушники и шлемы.
Нормативные документы:
ГОСТ 12.1.003 – 83 ССБТ «Шум. Общие требования безопасности»;
ГОСТ 12.1.028 – 80 ССБТ «Шум. Определение шумовых характеристик источников шума. Ориентировочный метод»
-изолирующие рукавицы перчатки
-вкладыши прокладки
-специальная обувь подмётки
-наколенники нагрудники пояса
-специальные костюмы.
Средства коллективной защиты от вибраций делят на:
-снижающие параметры вибрации воздействием на источник возбуждения (рациональный выбор массы и упругости колеблющейся системы изменение частоты вынуждающей системы и другие методы) и
-снижающие параметры вибрации в направлении её распространения (виброгасящие и виброизолирующие устройства демпфирующие покрытия средства динамического виброгашения).
Нормативная документация:
ГОСТ 12.1.012 – 90 ССБТ. «Вибрационная безопасность. Общие требования безопасности». Вибрации всех видов нормируются в соответствии с ГОСТ 12.1.012 – 90. ГОСТ 12.4.002 – 97 ССБТ «Средства индивидуальной защиты рук от вибрации. Технические требования и методы испытаний».
Недостаточная освещённость рабочей зоны
Естественное и искусственное освещение производственных помещений должно соответствовать требованиям СниП 23-05-95. Для металлорежущих станков необходимо предусматривать комбинированную систему освещения т.е. сочетание общего и местного освещения.
Для местного освещения следует применять светильники установленные на металлорежущие станки и отрегулированные не ниже допустимых значений освещенности. Кроме того необходимо производить чистку стекол оконных проёмов и световых фонарей не реже двух раз в год..
Местное освещение станка должно быть безопасным. В соответствии с ГОСТ 12.2.009-99 ССБТ «Станки металлообрабатывающие» для питания пристроенных светильников местного освещения с лампами накаливания следует применять напряжение не более 42 В (в нашем случае для металлообрабатывающих станков 24 В).
Конструкция кронштейна местного освещения должна обеспечивать фиксацию светильника во всех требуемых положениях без дополнительных операций по его закреплению. Подводка электрических проводов к светильнику осуществляется внутри кронштейна.
Должны соблюдаться требования стандартов:
ГОСТ 12.2.007.13-2000 ССБТ. Лампы электрические. Требования безопасности
ГОСТ 24940-96 Здания и сооружения. Метод измерения освещенности.
Пониженные и повышенные температуры воздуха
Защитой от данного вредного производственного фактора будет являться наличие: вентиляционной системы и калориферов подающих воздух требуемого объёма и температуры в производственные помещения; системы отопления (холодное время года) и других устройств создающих комфортную температуру в производственных помещениях. Выдача тёплой рабочей одежды также является защитой от данного фактора.
Оптимальные нормы температуры относительной влажности и скорости воздуха в рабочей зоне производственных помещений определяется согласно ГОСТ 12.1.005 – 88 ССБТ «Общие санитарно-гигиенические требования к воздуху рабочей зоны».
Повышенная концентрация аэрозолей масел и СОЖ
Для снижения количества аэрозолей СОЖ в воздухе рабочей зоны следует применять рекомендуемые ГОСТ 12.3.025-80 ССБТ «Обработка металлов резанием. Требования безопасности» конструкции сопел для подачи и распыления жидкости.
Выбор СОЖ необходимо осуществлять учитывая ГОСТ 12.3.025-80.
Антимикробная защита СОЖ должна проводиться добавлением бактерицидных присадок и периодической пастеризацией жидкости.
Периодичность замены СОЖ должна устанавливаться по результатам контроля ее содержания но не реже 1 раза в шесть месяцев при лезвийной обработке 1 раза в месяц – при абразивной обработке для масляных СОЖ и 1 раза в 3 месяца для водных СОЖ.
Не реже 1 раза в неделю должен проводиться анализ СОЖ на отсутствие микробов вызывающих кожные заболевания. Дополнительный контроль СОЖ может проводиться при появлении запаха или раздражения рук.
Для защиты кожного покрова от воздействия СОЖ применяют дерматологические защитные средства (профилактические пасты мази кремы и др.).
Нормативные документы:
ГОСТ 12.1.005 – 88 ССБТ. Общие санитарно-гигиенические требования к воздуху рабочей зоны».
ГОСТ 12.4.068 – 79 ССБТ «Средства дерматологические защитные. Классификация. Общие технические требования».
Кроме всего предложенного необходимо обеспечить комфортные условия труда а именно правильно организовать рабочее место.
Решение эргономических вопросов при определении общих размеров зон обслуживания и наладки оборудования определение размеров опасных зон требует обращения к стандартам:
ГОСТ 12.2.032 – 78 ССБТ «Рабочее место при выполнении работ сидя. Общие эргономические требования»
ГОСТ 12.2.033 – 78 ССБТ «Рабочее место при выполнении работ стоя. Общие эргономические требования»
ГОСТ 12.2.049 – 80 ССБТ. «Оборудование производственное. Общие эргономические требования»
ОСТ 2Н08 – 1 – 86 «Станки металлорежущие. Общие требования технической эстетики и эргономики».
Персонал допускаемый к участию в производственном процессе обработки резанием должен знать требования ГОСТ 12.3.025 – 80 пройти инструктаж и обучение условиям безопасности труда по ГОСТ 12.0.004 – 90.
Электробезопасность.
Эксплуатация большинства машин и оборудования связана с применением электрической энергии. Электрический ток проходя через организм оказывает термическое электролитическое и биологическое воздействие вызывая местные и общие электротравмы. Основными причинами воздействия тока на человека являются:
- случайное прикосновение или приближение на опасное расстояние к токоведущим частям;
- появление напряжения на металлических частях оборудования в результате повреждения изоляции или ошибочных действий персонала;
- шаговое напряжение в результате замыкания провода на землю.
Основные меры защиты от поражения током: изоляция недоступность токоведущих частей применение малого напряжения (не выше 42 В а в особо опасных помещениях - 12 В) защитное отключение применение специальных электрозащитных средств защитное заземление и зануление. Одно из наиболее часто применяемой мерой защиты от поражения током является защитное заземление.
Заземление - преднамеренное электрическое соединение с землей металлических нетоковедущих частей которые могут оказаться под напряжением. Разделяют заземлители искусственные предназначенные для целей заземления и естественные - находящиеся в земле металлические предметы для иных целей. Для искусственных заземлителей применяют обычно вертикальные и горизонтальные электроды. В качестве вертикальных электродов используют стальные трубы диаметром 3 5 см и стальные уголки размером от 40 х 40 до 60 х 60 мм длиной 3 5 м.
Также применяют стальные прутки диаметром 10 20 мм и длиной 10 м. Для связи вертикальных электродов и в качестве самостоятельного горизонтального электрода используют сталь сечением не менее 4 х 12 мм и сталь круглого сечения диаметром не менее 6 мм. В качестве заземляющих проводников применяют полосовую или круглую сталь прокладку которых производят открыто по конструкции здания на специальных опорах. Заземлительное оборудование присоединяется к магистрали заземления параллельно отдельными проводниками
Пожарная безопасность.
Пожары на машиностроительных предприятиях представляют большую опасность для работающих и могут причинить огромный материальный ущерб. К основным причинам пожаров возникающих при производстве электродвигателей можно отнести: нарушение технологического режима неисправность электрооборудования (короткое замыкание перегрузки) самовозгорание промасленной ветоши и других материалов склонных к самовозгоранию несоблюдение графика планового ремонта реконструкции установок с отклонением от технологических схем. На проектируемом участке возможны такие причин пожара: перегрузка проводов короткое замыкание возникновение больших переходных сопротивлений самовозгорание различных материалов смесей и масел высокая конденсация воспламеняемой смеси газа пара или пыли с воздухом (пары растворителя). Для локализации и ликвидации пожара внутрицеховыми средствами создаются следующие условия предупреждения пожаров: курить только в строго отведенных местах подтеки и разливы масла и растворителя убирать ветошью ветошь должна находиться в специально приспособленном контейнере.
Проектируемый участок по степени средств пожаротушения принадлежит к категории Б (720 м2).
На участке имеется следующий пожароликвидирующий инвентарь:
- Углекислотный огнетушитель ОУ-5 (1шт)
- Воздушно-химический огнетушитель (2шт)
- Ящик с песком вместимостью 0.53.0 м3 и лопата
- Войлок кошта или асбест (1x1 2x2 м3)
Техника безопасности на участке.
Перед началом работы на проектируемом участке необходимо проверить исправность оборудования приспособлений и инструмента ограждений защитного заземления вентиляции. Проверить правильность складирования заготовок и полуфабрикатов. Во время работы необходимо соблюдать все правила использования технологического оборудования. соблюдать правила безопасной эксплуатации транспортных средств тары и грузоподъемных механизмов соблюдать указания о безопасном содержании рабочего места. В аварийных ситуациях необходимо неукоснительно выполнять все правила. регламентирующие поведение персонала при возникновении аварий и ситуаций которые могут привести к авариям и несчастным случаям. По окончании работы должно быть выключено все электрооборудование произведена уборка отходов производства и другие мероприятия обеспечивающие безопасность на участке.
Участок должен быть оснащен необходимыми предупредительными плакатами оборудование должно иметь соответствующую окраску должна быть выполнена разметка проезжей части проездов. Сам участок должен быть спланирован согласно требованиям техники безопасности а именно соблюдение: ширины проходов проездов минимальное расстояние между оборудованием. Все эти расстояния должны быть не менее допустимых
В рамках данного дипломного проекта были предложены и разработаны средства технологического оснащения на модернизированный технологический процесс изготовления детали Корпус для изделия ОВ-75. Дан экономический анализ предлагаемых технических решений и проанализированы вредные и опасные производственные факторы возникающие на механическом участке по обработке предложенной мной детали а также меры по их устранению.
Горбацевич А.Ф. Шкред В.А. Курсовое проектирование по технологии машиностроения: Учеб. Пособие для машиностроит. спец. Вузов. – 4-е изд. перераб. и доп. – Мн.: Выш. Школа 1983. – 256 с. ил.
Справочник технолога – машиностроителя. В 2-х т. Под ред. А.Г. Косиловой и Р.К. Мещерякова. – 4-е изд. перераб. и доп. – М.: Машиностроение 2003том1.
Справочник технолога – машиностроителя. В 2-х т. Под ред. А.Г. Косиловой и Р.К. Мещерякова. – 4-е изд. перераб. и доп. – М.: Машиностроение 2003 том1.
Дипломное проектирование по технологии машиностроения. Учебное пособие для вузов. Под общ. Ред. В.В. Бабука. – Мн.: Высш. школа 1979. – 464 с. ил.
Общемашиностроительные нормативы времени вспомогательного на обслуживание рабочего места и подготовительно-заключительного для технического нормирования станочных работ. Серийное производство. М. «Машиностроение» 1974 421с. (ЦБПНТ при НИИТруда).
Справочник металлиста. В 5-т.-М.: Машиностроение1977.
Расчеты экономической эффективности новой техники. Справочник. Под. ред. К.М. Великанова. Л. «Машиностроение» 1975. – 432 с.
Обработка металлов резанием: Справочник технолога А.А. Панов В.В. Аникин и др.; Под общ. ред. А.А. Панова. – М.: Машиностроение. 1988.–736 с.: ил.
Расчёты потребного количества технологического и транспортного оборудования в курсовом и дипломном проектах. Метод. указ. (Часть I). Составил Грисенко Е.В. Пермь ПГТУ 2002 г.
Расчёты площадей промышленного и вспомогательного корпусов. План цеха. Метод. указ. Составил Грисенко Е.В. Пермь ПГТУ 2002 г.
Мамаев В.С. Осипов Е.Г. Основы проектирования машиностроительных заводов. М.: «Машиностроение» 1982г.
Егоров М.Е. Основы проектирования машиностроительных заводов. М.: «Высшая школа» 1969г.
Мельников Г.Н. Вороненко В.П. Проектирование механосборочных цехов. М.: «Машиностроение» 1982г.
Составление бизнес-плана (на примере механического цеха): Метод. указания к курсовой работе для студентов специальности 1201 1202. Составили: В.В. Ленина Н.Н. Шубина Пермь ПГТУ 1997 г.
Горошкин А.К. Приспособления для металлорежущих станков: Справочник. – 7-е изд. перераб. и доп. – М.: Машиностроение 1979. – 303 с. ил.
Станочные приспособления: Справочник. В 2-х т. Ред. совет: Б.Н.
Вардашкин и др. – М.: Машиностроение 1984. – Т.1 Под ред. Б.Н. Вар-
дашкин–На 1984. 592с. ил.
Расчеты технологических операций на точность. Методическое указаниСост. В.И. Свирщев; Перм. политехн. ин-т. Пермь2005.
ПГТУ. Пермь 2005. – 38 с. ил.
DMG – innovative technologies журнал выпуск12005.
В.С. Корсаков .Основы конструирования приспособлений: Учебник для вузов.-2-е изд. перераб. и доп.- М.: Машиностроение 1983.-227с.ил.
Расчет технологического процесса на точность: Метод. указания Сост. В.И. Свирщев; Перм. политехн. ин-т. Пермь2005.
Примеры выполнения расчетов конструкций станочных приспособлений на точность: Метод. указания Сост. В.И. Свирщев; Перм. политехн. ин-т. Пермь2005.
Анурьев В.И. Справочник конструктора- машиностроителя. В 3-х т.-М.: Машиностроение1982.-736с.
Безопасность жизнедеятельности. Учебник для вузов С.В.Белов А.В. Ильницкая А.Ф.Козьяков и др. Под общей редакцией С.В. Белова.-2-е изд. испр. И доп.-М.: Высш.шк.1999448 с.
Методические указания по выполнению раздела «Безопасность жизнедеятельности» в дипломных проектах по всем специальностям МТФ А.Е. Шевченко О.В.Бердышев. – Пермь: Изд-во Перм. гос. техн. ун-та. 2007. - 33 с.
Дулицкий Г.А.. Комаревцев А.П. Электробезопасность при эксплуатации электроустановок напряжением до 1000 В. М.: Воениздат 1988. 127 с.
Долин П.А. Основы техники безопасности в электроустановках. М.: Энергоатомиздат 1984. 448 с.
Долин П.А. Справочник по технике безопасности. М.: Энергоатомиздат 1985. 824с.
Электробезопасность на промышленных предприятиях: Справочник Р.В. Сабарно и др. Киев: Техника 1985. 288 с.
Кораблев В.П. Устройства электробезопасности. М.: Энергоатомиздат 1985. 88 с. 94.Бургсдорф В.В. Якобе А.И. Заземляющие устройства электроустановок. М.: Энергоатомиздат 1987. 400 с.
Деталь 2.cdw

Деталь 3.cdw

Деталь 1.cdw

Штамповка по ОСТ 1.90000-70 гр.
Гр.4 ОСТ 92-9465-81.
На поверхностях детали
кроме поверхностей А
допускаются механические повреждения глубиной не более 0
при этом превышения металла над основной поверхностью
удалить. Шероховатость поверхностей в местах зачистки не
механические повреждения не
* Размеры обеспечиваются инструментом.
Согласно выносному элементу Ж(лист 3) нанести
электрографом риски глубиной и шириной 0
плоскостей стабилизации шрифтом ЦР-6 ГОСТ 2930-62.
Маркировать ч и клеймить К на бирке.
Остальные технические требования по ОСТ 92-0594-70 .
Рекомендуемые чертежи
- 24.01.2023
- 24.01.2023
- 24.01.2023
- 24.01.2023