Разработка технологического процесса для изготовления детали Корпус ракетного клапана




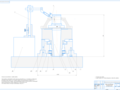
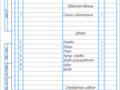
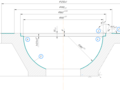
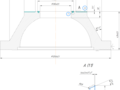
- Добавлен: 24.01.2023
- Размер: 11 MB
- Закачек: 0
Описание
Разработка технологического процесса для изготовления детали Корпус ракетного клапана
Состав проекта
![]() |
![]() |
![]() |
![]() |
![]() ![]() |
![]() ![]() |
![]() |
![]() |
![]() |
![]() |
![]() |
![]() |
![]() |
![]() ![]() ![]() ![]() |
![]() |
![]() |
![]() |
![]() |
![]() |
![]() |
![]() |
![]() |
![]() ![]() ![]() ![]() |
![]() ![]() ![]() |
![]() ![]() ![]() |
![]() |
![]() |
![]() |
![]() |
![]() |
![]() |
![]() ![]() ![]() |
![]() |
![]() |
![]() |
![]() |
![]() |
![]() |
![]() ![]() ![]() |
![]() ![]() ![]() |
![]() |
![]() |
![]() |
![]() |
![]() ![]() ![]() |
![]() |
![]() |
![]() |
![]() ![]() ![]() |
![]() |
![]() |
![]() |
![]() |
![]() ![]() ![]() |
![]() |
![]() ![]() ![]() |
![]() |
![]() |
![]() ![]() ![]() |
![]() |
![]() |
![]() |
![]() |
![]() |
![]() |
![]() |
![]() |
![]() |
![]() |
![]() |
![]() |
![]() |
![]() |
![]() |
![]() |
![]() |
![]() |
![]() |
Дополнительная информация
приспособление контрольное.spw

контрольное приспособление.cdw

Токарная-карусельная с чпу 2 переустанов.frw

Фрагмент.frw

Координатно расточная переустанов.frw

Токарная-карусельная с чпу 2.frw

Токарная-карусельная.frw

Токарная-карусельная с ЧПУ.frw

Координатно расточная.frw

заготовительная.frw

Рекомендуемые чертежи
- 24.01.2023
- 01.07.2014