Разработка технологического процесса изготовления детали “Корпус”


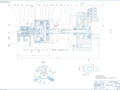
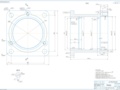
- Добавлен: 23.11.2022
- Размер: 2 MB
- Закачек: 6
Описание
1.1 Описание конструкции и служебного назначения детали
Деталь “Корпус” согласно ЕСКД относится к 73 классу (Детали - не тела вращения корпусные, опорные, емкостные). Торцевая поверхность детали 140х150 имеет 4 сквозных отверстия диаметром 15 мм с позиционным допуском расположения 0.2 мм. На противоположном торце детали имеются три глухих резьбовых отверстия М10-7Н с позиционным допуском расположения равным 0.2 мм. Стоит отметить, что деталь имеет центральное, сквозное, ступенчатое отверстие, где наиболее точными поверхностями являются поверхности, предназначенные для посадки под подшипник: поверхность диаметром , на которой расположена канавка под стопорное кольцо шириной 2,2 мм и диаметром 103.5 мм, и поверхность диаметром , которая одновременно является и базовой поверхностью на ней так же как и на поверхности диаметром имеется канавка под стопорное кольцо шириной 3 мм и диаметром 111 мм. Торцевая поверхность детали 140х150 имеет допуск торцевого биения относительно базы В равный 0,08 мм. Поверхность детали диаметром имеет допуск цилиндричности равный 0,01 мм и допуск радиального биения относительно базы В равный 0,025 мм. Поверхность детали диаметром имеет допуск цилиндричности равный 0,01 мм и допуск торцевого биения относительно базы В равный 0,045 мм. Неуказанная шероховатость поверхностей детали Ra=25 мкм. Твердость поверхности детали 163-229 НВ. Общие допуски по ГОСТ 30893.1. Годовая программа выпуска деталей N=1500 шт. Деталь изготавливается из серого чугуна СЧ20 ГОСТ 1412-85, химический состав, механические свойства серого чугуна представлены в таблицах 1.1, 1.2 соответственно.
Состав проекта
![]() ![]() ![]() |
![]() |
![]() ![]() ![]() ![]() |
![]() ![]() ![]() |
![]() ![]() ![]() ![]() |
![]() ![]() ![]() ![]() |
![]() ![]() ![]() |
![]() ![]() ![]() ![]() |
![]() ![]() ![]() ![]() |
![]() ![]() ![]() ![]() |
![]() ![]() ![]() |
![]() ![]() ![]() |
![]() ![]() ![]() ![]() |
![]() ![]() ![]() |
Дополнительная информация
Корпус вала шкива ГОТ11.cdw

Чертеж ОЭ1.cdw

лист4-присп.-токарн.патрон.cdw

Спец-патрон.spw

Чертеж ОЭ2.cdw

Чертеж заготовка.cdw

Чертеж ОЭ3.cdw

Рекомендуемые чертежи
- 24.01.2023
- 01.07.2014