Проектирование сварных конструкций(проектирование технологического оснащения)




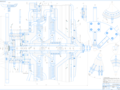

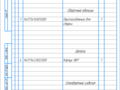
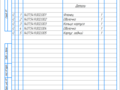
- Добавлен: 24.01.2023
- Размер: 3 MB
- Закачек: 0
Описание
Проектирование сварных конструкций(проектирование технологического оснащения)
Состав проекта
![]() |
![]() ![]() ![]() |
![]() |
![]() ![]() ![]() ![]() |
![]() ![]() ![]() |
![]() ![]() ![]() |
![]() ![]() ![]() ![]() |
![]() |
![]() ![]() ![]() |
![]() |
![]() |
![]() |
![]() |
![]() |
![]() |
![]() |
![]() |
![]() |
![]() |
![]() |
![]() |
![]() |
![]() |
![]() |
![]() |
![]() |
![]() |
![]() ![]() ![]() ![]() |
![]() ![]() ![]() ![]() |
![]() ![]() ![]() ![]() |
![]() ![]() ![]() ![]() |
![]() |
![]() ![]() ![]() |
Дополнительная информация
Спецификация корпус ВВТ.spw

Спецификация на раб место.spw

Приспособа1.cdw

Корпус ВВТ.cdw

Рабочее место МОЁ Рекомендац Ильдара без разреза.cdw

Специфа 4 курс.spw

Рекомендуемые чертежи
- 24.01.2023
- 24.01.2023
- 24.01.2023
- 24.01.2023
Свободное скачивание на сегодня
- 06.06.2020