Разработка технологии и средств технологического оснащения для изготовления корпуса 456.852.32




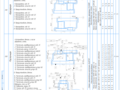
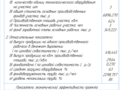

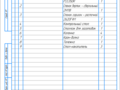
- Добавлен: 24.01.2023
- Размер: 18 MB
- Закачек: 4
Описание
Состав проекта
![]() |
![]() |
![]() |
![]() |
![]() ![]() ![]() ![]() |
![]() |
![]() |
![]() |
![]() |
![]() ![]() ![]() ![]() |
![]() ![]() ![]() ![]() |
![]() |
![]() |
![]() |
![]() |
![]() ![]() ![]() ![]() |
![]() |
![]() |
![]() ![]() ![]() ![]() |
![]() |
![]() |
![]() |
![]() |
![]() ![]() ![]() |
![]() |
![]() |
![]() |
![]() ![]() ![]() ![]() |
![]() |
![]() |
![]() |
![]() |
![]() |
![]() |
![]() ![]() ![]() ![]() |
![]() ![]() ![]() ![]() |
![]() |
![]() ![]() ![]() ![]() |
![]() |
![]() |
![]() |
![]() ![]() ![]() ![]() |
![]() |
![]() |
![]() ![]() ![]() ![]() |
![]() |
![]() |
![]() |
![]() |
![]() |
![]() |
![]() |
![]() |
![]() ![]() |
![]() ![]() ![]() |
![]() |
![]() ![]() ![]() |
![]() ![]() ![]() |
![]() ![]() ![]() |
![]() ![]() ![]() |
![]() ![]() ![]() |
![]() ![]() |
![]() ![]() ![]() |
![]() ![]() ![]() |
![]() ![]() ![]() |
![]() ![]() ![]() |
![]() ![]() ![]() |
![]() ![]() ![]() |
![]() ![]() ![]() |
![]() ![]() ![]() |
![]() |
![]() |
![]() |
![]() |
![]() |
![]() |
![]() |
![]() |
![]() |
![]() ![]() ![]() |
![]() |
![]() |
![]() |
![]() ![]() ![]() ![]() |
![]() ![]() ![]() ![]() |
![]() ![]() ![]() ![]() |
![]() |
![]() ![]() ![]() ![]() |
![]() |
![]() |
![]() ![]() ![]() ![]() |
![]() |
![]() |
![]() |
![]() |
![]() |
![]() |
![]() |
![]() |
![]() |
![]() |
![]() |
![]() |
![]() |
Дополнительная информация
Сборка.cdw

маршрутка без сверления.cdw

Резец расточной Р6М5 ГОСТ 10044-73
Резец расточной ВК8 ГОСТ 9795-73
А.Установить деталь и после
Фрезеровать пов. (1).
Фрезеровать начисто пов. (1).
Б. Переустановить деталь.
Фрезеровать пов. (2.).
Фрезеровать начисто пов. (2).
Фрезеровать пов. (3).
Фрезеровать начисто пов. (3).
В. Переустановить деталь.
Фрезеровать пов. (4).
Фрезеровать начисто пов. (4).
Расточить предварительно отв. (1).
Расточить начисто отв. (1).
Расточить предварительно отв.(3).
Расточить начисто отв. (3).
Расточить предварительно отв. (4).
Расточить начисто отв. (4).
Расточить тонко отв. (4).
Расточить предварительно отв. (5).
Расточить начисто отв. (5).
Расточить тонко отв. (5).
Расточить предварительно уступ (6).
Расточить начисто уступ (6).
Б. Переустановить деталь
Расточить предварительно отв. (7).
Расточить начисто отв. (7).
Расточить предварительно уступ (8).
Расточить начисто уступ (8).
Повернуть стол на 90
Подрезать торец (9).
Точить пов. (9) согласно эскизу.
Расточить предварительно отв. (10).
Расточить начисто отв. (10).
Расточить предварительно отв. (11).
Расточить начисто отв. (11).
Расточить тонко отв. (11).
Расточить фаску (12) предварительно.
Расточить фаску (12) начисто.
Разработка технологии и средств технологического
оснащения для изготовления корпуса 456.852.32
Технологический процесс
изготовления корпуса 456.852.32
(выборочные операции)
Станок вертик.-фрезерный FSS350R
Приспособление при станке
Штангельциркуль ШЩ-I-250-0
Специальное приспособление
Станок горизонтально-расточной 262ОГФ1
маршрутка.cdw

Резец расточной Р6М5 ГОСТ 10044-73
Резец расточной ВК8 ГОСТ 9795-73
Штангельциркуль ШЩ-I-250-0
А.Установить деталь и после
Фрезеровать пов. (1).
Фрезеровать начисто пов. (1).
Б. Переустановить деталь.
Фрезеровать пов. (2.).
Фрезеровать начисто пов. (2).
Фрезеровать пов. (3).
Фрезеровать начисто пов. (3).
В. Переустановить деталь.
Фрезеровать пов. (4).
Фрезеровать начисто пов. (4).
Сверлить 2 отв. напроход и 2 отв. на
Зенкеровать 4 отв. (1)
Нарезать резьбу 4 отв. (1) на глубину
Сверлить фаску 4 отв. (1) согласно
Расточить предварительно отв. (1).
Расточить начисто отв. (1).
Расточить предварительно отв.(3).
Расточить начисто отв. (3).
Расточить предварительно отв. (4).
Расточить начисто отв. (4).
Расточить тонко отв. (4).
Расточить предварительно отв. (5).
Расточить начисто отв. (5).
Расточить тонко отв. (5).
Расточить предварительно уступ (6).
Расточить начисто уступ (6).
Метчик М6 ГОСТ 3266-81
Штангенциркуль ШЩ-I-250-0
Пробка резьбовая М6-7Н ГОСТ 17758-83
Сверлить 6 отв. на 10 мм. (2)
Зенкеровать 6 отв. на 10 мм. (2)
Нарезать резьбу 6 отв. (2) на глубину
Сверлить фаску 6 отв. (2) согласно
Б. Переустановить деталь
Расточить предварительно отв. (7).
Расточить начисто отв. (7).
Расточить предварительно уступ (8).
Расточить начисто уступ (8).
Повернуть стол на 90
Подрезать торец (9).
Точить пов. (9) согласно эскизу.
Расточить предварительно отв. (10).
Расточить начисто отв. (10).
Расточить предварительно отв. (11).
Расточить начисто отв. (11).
Расточить тонко отв. (11).
Расточить фаску (12) предварительно.
Расточить фаску (12) начисто.
Разработка технологии и средств технологического
оснащения для изготовления корпуса 456.852.32
Технологический процесс
изготовления корпуса 456.852.32
(выборочные операции)
Станок вертик.-фрезерный FSS350R
Приспособление при станке
Специальное приспособление
Станок горизонтально-расточной ИР320ПМФ4
Станок вертик.-сверлильный 2Н118
Станочное приспособление.cdw

Усилие зажима max при давлении
в пневмосистеме от 0
Технические требования
*Размеры для справок
Подвижные части приспособления должны передвигаться свободно
Трущиеся поверхности периодически покрывать смазкой ЦИА ТИМ 221
Маркировать по СТП предприятия
Разработка технологии и средств технологического оснащения
для изготовления корпуса 456.852.32
Чертеж.cdw

для изготовления корпуса 456.852.32
Отливка 2 класса точности по ГОСТ 2009-55
Неуказанные предельные отклонения размеров обрабатываемых
поверхностей диаметров - по Н9
* Размеры для справок.
Маркировать электрохимическим методом
гемма2.cdw

научно-исследовательская часть.cdw

маркирования УПЭК- 901
- поролоновые подушки;
- клавиши задания режима;
- стол для маркирования мелких деталей.
Технические характеристики УПЭК- 901:
- напряжение питания
- рабочее напряжение
- время маркирования:
при автоматической выдержке 2-2
(мм); - мощность 150 (Вт);
- габаритные размеры
Для маркирования корпуса 456.852.32 выбираем следующие параметры:
Состав электролита - бромистый калий 5-10%
азотнокислый аммоний 5-10%.
Напряжение на электродах - 6(В.).
Время обработки - 1 (с.).
Шероховатость поверхности не выше Ra=5(мкм.).
электрохимическое маркирование в меньшей степени влияет на местную концентрацию напряжений
и является предпочтительным по сравнению с механическим способом нанесения информации.
Эффективные коэффициенты концентрации напряжений для АК7 ГОСТ 1583-93:
- после механического маркирования - 1
- после электрохимического маркирования - 1
Контроль (спецификация).cdw

для изготовления корпуса 456.852.32
Контрольное приспособление
Самоцинтрирующаяся оправка
Индикатор многооборотный 1МИС ГОСТ 9696-75
Измерительное приспособление.cdw

для изготовления корпуса 456.852.32
Индикатор 1МИС ГОСТ 9696-75
Цена деления индикатора 0
Деталь считать годной при отклонении стрелки индикатора не
более чем на 13 делений
Погрешность измерения составит 0
* Размеры для справок
заготовка.cdw

Литейные уклоны не более 5
*Размеры для справок
Предельные отклонения литейных размеров по ГОСТ 26645-85
Разработка технологии и средств технологического оснащения
для изготовления корпуса 456.852.32
План участка(спецификация).cdw

для изготовления корпуса 456.852.32
Станок вертик.-фрезерный
Станок вертик. - сверлильный
Станок горизон. - расточной
Сталлаж для заготовок
План участка.cdw

для изготовления корпуса 456.852.32
МОЙ ДИПЛОМ2.doc
ГОСУДАРСТВЕННОЕ ОБРАЗОВАТЕЛЬНОЕ УЧРЕЖДЕНИЕ
ВЫСШЕГО ПРОФЕССИОНАЛЬНОГО ОБРАЗОВАНИЯ
«ВОРОНЕЖСКИЙ ГОСУДАРСТВЕННЫЙ ТЕХНИЧЕСКИЙ УНИВЕРСИТЕТ»
Кафедра: «Технология машиностроения»
Специальность: 120100 (151001) «Технология машиностроения»
ВЫПУСКНАЯ КВАЛИФИКАЦИОННАЯ РАБОТА
Тема дипломного проекта: Разработка технологии и средств технологического оснащения для изготовления корпуса 456.852.32
Пояснительная записка
дата Инициалы фамилия
по экономической и организационно-
управленческой части А.А. Мордовцев
по экологии и безопасности .
Студент группы: ТМ-061в
(фамилия имя отчество)
на выпускную квалификационную работу
утверждена распоряжением по факультету № 6 от « » января 2012 г.
Технические условия: режим работы участка–односменный .
программа выпуска–3010 штук в год. .
Содержание (разделы графические работы расчеты и проч.):
Графическая часть: 1) титульный лист – 1 лист (А1); 2) сборочный чертеж узла – 1 лист (А1); 3) рабочий чертёж детали – 1 лист (А1); 4) твердотельная модель – 1 лист (А1);5) результаты расчета корпуса 456.852.32 в 6) чертеж заготовки – 1 лист (А1); 7) разработка технологического процесса в САПР ТП – 1 лист (А1); 8) плакаты с иллюстрацией разработанного технологического процесса – 1 лист (А1); 9) управляющая программа в ГеММа-3D; 10) сборочный чертеж установочного приспособления – 1 лист (А1); 11) сборочный чертёж контрольного приспособления – 1 лист (А1); 12) плакат с результатами научно-исследовательской части; 13) планировка участка – 1 лист (А1); 14) плакат с технико-экономическими показателями спроектированного участка – 1 лист (А1).
Расчётно-пояснительная записка: 1) производственно-технологическая часть; 2) проектно-конструкторская часть; 3) научно-исследовательская часть; 4) экс-плуатационная часть; 5) экономическая и организационно-управленческая часть. 6) безопасность и экологичность. Комплект карт технологического процесса
План выполнения дипломного проекта
с « » 2012г. по « » 2012 г.
Название элементов проектной
руководи-теля кон-сультанта
Проектно-конструкторская часть
Производственно-технологическая часть
Эксплуатационная часть
Научно-исследовательская часть
Экономическая и организационно- управленческая часть
Безопасность и экологичность
Комплект карт технологического процесса
Руководитель дипломного проекта
(подпись) (Фамилия имя отчество)
Дипломный проект закончен
(подпись дипломника)
Пояснительная записка и все материалы просмотрены
Консультанты: Мордовцев Александр Анатольевич
к защите дипломного проекта в Государственной аттестационной комиссии
(подпись) (Инициалы фамилия)
Пояснительная записка: 141 листа 29 таблицы 29 рисунков 15 источников 3 приложения.
КОРПУС ЧЕРВЯЧНОЙ ТАЛИ ТЕХНОЛОГИЯ ТЕХНОЛОГИЧЕСКОЕ ОСНАЩЕНИЕ РЕЖИМЫ ОБРАБОТКИ РАСЧЕТ ПРИСПОСОБЛЕНИЯ ЭКОНОМИЧЕСКАЯ ЭФФЕКТИВНОСТЬ ПЛАНИРОВКА УЧАСТКА.
Объект исследования или разработки – корпус 456.852.32.
Цель работы – совершенствование операционного технологического процесса изготовления корпуса 456.852.32; проектирование эффективной операционной технологии с использованием САПР; численное обоснование метода изготовления заготовки; формирование состава переходов и операций; расчёт станочного приспособления; расчёт контрольного приспособления; проектирование производственного участка; расчёт экономических показателей участка.
Полученные результаты и их новизна – в данном дипломном проекте были решены основные задачи поставленные для достижения повышения производительности труда в условиях крупносерийного производства. Используя основные направления в современной технологии машиностроения был выбран рациональный метод получения заготовки что дало возможность значительно снизить трудоемкость обработки детали на металлорежущих станках а также сократить расход металла. Применение станка с числовым программным управлением приспособления с быстродействующими зажимами позволило повысить производительность труда. Снижение трудоемкости перемещения детали между рабочими местами было учтено при разработке участка механической обработки что позволило достигнуть лучших технико-экономических показателей по сравнению с существующими на заводе.
Экономическая эффективность или значимость работы – экономический эффект от производства продукции с применением разработанного в дипломном проекте технологического процесса за расчётный период составит 2741634 тысяч рублей.
Проектно-конструкторская часть 9
1 Конструктивно-технологический анализ узла составной частью
которого является выбранная для проектирования деталь 9
2 Назначение и краткое технологическое описание детали 10
3 Разработка параметрической твердотельной модели объекта для проектирования технологичной конструкции детали 13
4 Расчет силовых и деформационных параметров детали в процессе ее
эксплуатации или изготовления с помощью САЕ 14
Производственно-технологическая часть 47
1 Оценка технологичности детали 13
2 Установление типа производства 14
3 Анализ базового технологического процесса 14
4 Обоснование и разработка мероприятий по оптимизации базового технологического процесса
5 Выбор типа заготовки и предварительное назначение припусков 16
6 Назначение технологических баз и оценка точности базирования 18
7 Разработка плана обработки и маршрута операций технологического процесса обработки детали 21
8 Обоснование выбора моделей оборудования 26
9 Обоснование конструкции и расчет специальных средств технологического оснащения 53
9.1 Станочное установочно-зажимное приспособление 53
9.2 Контрольное приспособление 55
10 Аналитический расчет технологических параметров 30
11 Автоматизированное проектирование технологического процесса изготовления детали и средств технологического оснащения 33
11.1 Обоснование выбора программных средств для проектирования технологической подготовки производства 33
11.2 Использование САЕ для решения технологических задач(При отсутствии П.1.4.)
11.3 Использование прикладных библиотек Сапр при проектировании технологии изготовления детали
11.4 Проектирование операционной технологии с разработкой управля-
ющих программ и виртуальным моделированием обработки для станков с ЧПУ в САПР 34
12 Технологическое проектирование производственного подразделения 40
12.1 Расчет количества технологического оборудования и графика
12.2 Определение производственной площади участка 58
12.3 Расчет численности персонала 43
12.4 Выбор системы складирования 58
12.5 Разработка технологической планировки
Эксплуатационная часть 66
1 Эксплуатация режущего инструмента 66
1.1 Эксплуатация резцов 66
1.2 Эксплуатация фрез 69
Научно-исследовательская часть 60
1 Расчет режимов обработки и инструмента для электрохимического маркирования 60
2 Выбор оборудования для электрохимического маркирования 62
3 Влияние электрохимического маркирования на эксплутационные характеристики детали 65
Экономическая и организационно-управленческая часть 72
1 Экономическое обоснование проекта участка 72
1.1 Определение потребности в инвестициях для организации спро-
ектированного участка 72
1.2 Организация оплаты труда на участке 75
1.3 Расчет себестоимости продукции 82
1.4 Расчет текущих затрат 78
2 Расчет показателей экономической эффективности проекта 86
3 Расчет технико-экономических показателей экономической эффек-
4 Организационный вопрос 90
Экологичность и безопасность 93
1 Техника безопасности 94
2 Производственная санитария и гигиена труда 95
3 Противопожарные мероприятия и средства пожаротушения 97
4 Охрана окружающей среды 98
Список литературы 101
Приложение А. Графическая часть проекта 103
Сборочный чертеж узла
Чертеж детали с твердотельной моделью
Результаты расчета САЕ
Маршрут операций технологического процесса со схемами базирования и обработки детали
Специальное станочное приспособление
Специальное контрольное приспособление
Результаты автоматизированного проектирования технологического процесса изготовления детали и средств технологического оснащения
Планировка участка работ
Результаты работ проведенных в исследовательской части проекта
Показатели экономической эффективности проектных решений
Приложение Б. Спецификации к графической части проекта 117
Приложение В. Комплект документов технологического процесса обра-
ботки детали корпус 456.852.32 123
1 Конструктивно-технологический анализ узла составной частью которого является выбранная для проектирования деталь
Таль - грузоподъемное устройство с ручным электрическим или пневматическим приводом подвешиваемое к балкам или специальным тележкам перемещающимся по подвесному монорельсовому пути. Тали предназначены для подъема опускания и горизонтального перемещения груза подвешенного на крюковой подвеске. Отличительным признаком тали является компактность. Промышленностью выпускаются тали грузоподъемностью от 025 до 16 тонн с электроприводом и тали ручные грузоподъемностью: 1; 32; 5 и 8 тонн. Высота и скорость подъема груза талей соответственно не более 30 м и 005 015 м.
Данный узел может эксплуатироваться как в закрытом помещении так и на открытом воздухе. Особенности этого механизма:
- кованные подвесной и грузовой крюки из нержавеющей высоколегированной стали;
- повышенный запас прочности;
- высокая стойкость к механическим повреждениям.
Ручные тали (с ручным приводом) производят подъем груза с помощью грузовых пластинчатых или сварных комбинированных цепей приводимых в движение вручную с помощью звездочек. Часто грузовая цепь образует полиспаст кратностью 2; 3 и реже 4 [10]. Различают червячные и шестеренные ручные тали.
На рисунке 1.1 представлен механизм подъема ручной червячной тали. Подъемный механизм включает в себя тяговую звездочку 1 закрепленную на быстроходном валу 2 червячного редуктора. Подъем груза осуществляется с помощью сварной тяговой цепи (на рисунке 1.1 не показана). Барабаны 4 размещены с двух сторон тихоходного вала 3. Обычно в этом случае используется сдвоенный полиспаст (разрез А–А рисунок 1.1) уравнительный блок 5 которого закрепляется на корпусе 6 редуктора с помощью кронштейна 7 винтами 8.
Конструкция барабанов 4 – литая с нарезкой. Нарезка канавок на барабанах под канат выполняется в разные стороны. Груз при этом поднимается строго вертикально. Блок 5 валы червяка и колеса установлены на подшипниках качения 9 и 10 закрытых крышками 11 и 18 с манжетами 12 (подшипники и крышки на валу червяка не показаны). Осевое смещение барабанов на валу исключается винтами 13 и торцевой шайбой 14. Передача движения с вала 3 на колесо и барабаны осуществляется с помощью шпонок 15. Смещение колеса 4 вдоль оси вала исключается втулкой 16. Корпус 6 редуктора литой неразъемный. Размер крышки 17 позволяет вынимать (вправо) червячное колесо в сборе с тихоходным валом после отвинчивания винтов 13 червячный вал при этом должен быть вынут через отверстия подшипниковых гнезд вала червяка (на чертеже не показаны). Подшипники уравнительного блока 5 устанавливаются на оси 19. Осевое перемещение оси 19 исключается ригелем 20 закрепленным винтами 21 к кронштейну 7 и головкой оси слева (разрез А–А рисунок 1.1).
Рисунок 1.1 – Механизм подъема червячной тали
2 Назначение и краткое техническое описание детали
Деталь представляет собой корпус грузовой тали. Название – корпус. Заготовка детали – литая. Вес детали – 13 кг. Габаритные размеры: длина – 1715 мм высота – 158 мм ширина – 90 мм. Код 456.852.32. Материал детали – алюминиевый сплав АК7ч ГОСТ 1583 – 93. Химический состав материала описан в таблице 1.1. Механические свойства материала описаны в таблице 1.2.
Таблица 1.1 – Химический состав сплава АК7ч ГОСТ 1583 – 93 %
Таблица 1.2 – Механические свойства АК7ч ГОСТ 1583 – 93
Предел прочности при растяжении МПа
Твердость по БриннелюНВ
Корпусные детали в большинстве случаев являются базовыми деталями на которые монтируют отдельные сборочные единицы и детали соединяемые между собой с требуемой точностью относительного положения. Корпусные детали должны обеспечить постоянство точности относительного положения деталей и механизмов как в статическом состоянии так и в процессе эксплуатации машин.
Корпус червячной тали (рисунок 1.2) представляет собой конструкцию из двух параллельных и одного перпендикулярного к ним цилиндров а также других унифицированных и стандартизированных конструктивных элементов. При этом деталь имеет оригинальные конструктивные элементы замена которых невозможна так как это отрицательно сказывается на работоспособности изделия в конструкцию которого входит данная деталь.
Рисунок 1.2 – Корпус червячной тали
Конструкция детали обеспечивает свободный доступ инструмента для обработки и контроля. Точность детали выражена полями допусков: IT 9 Н9 Н7. Разброс шероховатости от Ra 125 до Ra 125 мкм. К детали предъявляются технические требования по геометрической форме и взаимному расположению поверхностей (рисунок 1.2):
необходимо не допустить разностенность стенок между поверхностями 18 и 9 а также между поверхностями 17 и 12.
необходимо обеспечить симметричность детали относительно оси отверстия 12.
необходимо обеспечить параллельность поверхностей 1 и 2 поверхности 16.
не допустить несоосности поверхностей 19 и 9.
3 Разработка твердотельной 3D модели детали
Для изготовления твердотельной 3D модели детали будем использовать программу КОМПАС-3D V10 разработанную компанией АСКОН.
Основная задача решаемая системой КОМПАС-3D – моделирование изделий с целью существенного сокращения периода проектирования и скорейшего их запуска в производство. Эти цели достигаются благодаря возможностям:
- быстрого получения конструкторской и технологической документации необходимой для выпуска изделий;
- передачи геометрии изделий в расчетные пакеты;
- передачи геометрии в пакеты разработки управляющих программ для оборудования с ЧПУ;
- создания дополнительных изображений изделий (например для составления каталогов создания иллюстраций к технической документации и т.д.).
Начинаем работу с запуска программы и выбора в верхней панели значка Создать. В появившемся окне выбираем значок Деталь (рисунок 2.1).
Рисунок 2.1 – Начало работы с программой
Далее с помощью графических примитивов строим контур детали. После окончания закрываем эскиз. После этого с помощью операции выдавливания строим твердотельную модель (рисунок 2.2).
Рисунок 2.2 – Построение твердотельной модели с помощью операций выдавливания
С помощью команды скругление выполняем ряд скруглений острых кромок поверхности модели. Для этого поочередно выбираем нужную кромку и указываем радиус скругления для нее (рисунок 2.3).
Рисунок 2.3 – Скругление острых кромок
Чтобы получить внутренние поверхности детали используем операции вырезания. Для этого сначала строим эскиз поверхности которую нужно получить а потом выполняем саму операцию вырезания (рисунок 2.4).
Рисунок 2.4 – Получение внутренних поверхностей детали
Выбираем команду «Фаска» и указываем поверхности на которых ее следует построить (Рисунок 2.5).
Рисунок 2.5 – Построение фасок
Далее строим 10 отверстий. Сначала делаем эскиз т.е. указываем место нахождения отверстия. Потом выбираем из библиотеке форму и размер требуемого отверстия (рисунок 2.6).
Рисунок 2.6 – Построение 10 отверстий
На заключительном этапе следует построить «Условное изображение резьбы» для 10 отверстий. На рисунке 2.7 представлен окончательный вид модели корпуса.
Рисунок 2.7 – Построение резьбы
4 Расчет силовых и деформационных параметров детали в процессе ее изготовления с помощью САЕ
SolidWorks имеет простой в использовании новый инструмент анализа напряжений для пользователей COSMOSXpress. COSMOSXpress может помочь снизить стоимость и сократить время от начального замысла проекта до его внедрения на рынок выполняя тестирование проектов с помощью компьютера вместо проведения дорогостоящих и долговременных производственных испытаний. Точность результатов анализа зависит от свойств материала ограничений и нагрузок. Чтобы получить надежные результаты указанные свойства материала должны точно представлять материал детали а ограничения и нагрузки должны точно представлять условия эксплуатации детали.
Исходя из режимов резания заданных в разработанном технологическом процессе найдём все составляющие силы резания для токарной операции обработки корпуса.
P(zyx) =10Cp tx Sy n Kp (2.1)
где Рz Рх и Ру – составляющие силы резания;
Кр – коэффициент учитывающий реальные условия резания.
Pz =10403271060758270 225=2004 (Н)
Работу начинаем с экспортирования модели в формат модель_10.stp. Открываем файл в программе SolidWorks и запускаем программу COSMOS-Xpress (рисунок 2.8).
Рисунок 2.8 – Выбор программы САЕ
Далее выбираем материал детали – легированный алюминий (сплав 2014) – как показано на рисунке 2.9.
Рисунок 2.9 – Выбор материала
Далее вводим ограничения на перемещение которое получается при установке и закреплении заготовки в приспособлении что и показано на рисунке 2.10.
Рисунок 2.10 – Выбор ограничений
Выбираем вид и размер прилагаемой нагрузки согласно проведённого расчёта. Процесс установки нагрузки показан на рисунке 2.11.
Рисунок 2.11 – Установка нагрузки
Проводим анализ. После чего получаем результат представленный на рисунке 2.12.
Рисунок 2.12 – Результат приложения нагрузки
Производственно- технологическая часть
1 Оценка технологичности детали
Технологичность конструкции детали - это показатель характеризующий удобно ли с технической точки зрения достигать заданную конструктором форму детали обеспечить точность и качество обработки; возможна ли обработка заданной детали на стандартном оборудовании стандартным режущим инструментом доступен ли его подвод и нормальное условие обработки. Оценка бывает двух видов: качественная и количественная.
Качественная оценка производится субъективно т.е. самим технологом на основании опыта производства и заключается в выше перечисленных условиях.
Количественная оценка технологичности производится по некоторым числовым показателям:
- коэффициент унификации конструктивных элементов
где Qуэ и Qэ – соответственно число унифицированных конструктивных элементов и общее.
Унифицированные конструктивные элементы – это те которые образуются стандартным режущим инструментом.
- коэффициент использования металла
где Q и q – соответственно масса заготовки и масса детали.
Определим технологичность нашей детали. Для этого определим коэффициент унификации конструктивных элементов и коэффициент использования металла.
При Куэ=084 > 06 и Ким=076 > 08 деталь технологична [4].
Ко всем обрабатываемым поверхностям обеспечен удобный подход режущих инструментов. Отсутствуют поверхности с необоснованно высокой точностью обработки.
Проанализировав все вышеперечисленные факторы будем считать деталь технологичной.
2 Установление типа производства
В машиностроении различают три типа производства: единичное серийное и массовое. Серийное производство в свою очередь подразделяется на мелкосерийное среднесерийное и крупносерийное.
Важным этапом в разработке технологического процесса является определение типа производства. Основным критерием при определении типа производства является коэффициент закрепления операций за одним рабочим местом или единицей оборудования. Он определяется как отношение числа всех технологических операций выполняемых в течении месяца на механическом участке (О) к числу рабочих мест (Р) на этом механическом участке.
Типы машиностроительного производства характеризуются следующими значениями коэффициента закрепления операции:
Кзо≤1 – массовое производство.
Кзо≤10 – крупносерийное производство.
Кзо≤20 – среднесерийное производство.
Кзо≤40 – мелкосерийное производство.
Кзо – единичное производство.
На практике обычно известна годовая программа выпуска и тогда определение Кзо удобно по следующей формуле:
где ФД– годовой фонд работы оборудования (18924 часов);
Обаз – число операций механической обработки по базовому техпроцессу;
Тшт – трудоемкость изготовления детали мин (78184 минут);
Nгод – годовая программа выпуска(3010 штук).
Вывод: производство является крупносерийном.
Для серийного производства эффективна предметная форма организации производства на участке. В этом случае всё оборудование необходимое для обработки деталей устанавливается в технологической последовательности что обеспечивает прямоточность уменьшение производственного цикла по длительности а также снижение себестоимости продукции.
3 Анализ базового технологического процесса
Заводской технологический процесс был разработан для единичного производства. При его изучении и тщательном анализе были выявлены его недостатки. Уровень автоматизации действующего технологического процесса низкий. Оснастка специальная разработанная непосредственно для действующего технологического процесса. При обработке по данному технологическому процессу деталь неоднократно переустанавливается. Заготовку изготавливается методом литья в песчано-глинистые формы. Это увеличивает число проходов так как шероховатость поверхности невелика.
При анализе основного и вспомогательного времени на обработку выявлено что затраты на вспомогательное время очень велики. Это объясняется тем что станки для обработки располагаются по группам. По действующему технологическому процессу применяется неавтоматизированные универсальные приспособления.
В процессе проектирования технологического процесса маршрут и трудоемкость обработки уменьшились. Сократилось количество операций и появилась возможность обрабатывать больше поверхностей за один установ детали. Это стало возможным в результате замены универсального оборудования на станки с ЧПУ.
5 Выбор типа заготовки и предварительное назначение припусков
Метод выполнения заготовок для деталей машин определяется назначением и конструкцией деталей материалом техническими требованиями масштабом и серийностью выпуска а также экономичностью изготовления.
Выбрать заготовку значить установить способ ее получения наметить припуски на обработку каждой поверхности рассчитать размеры и указать допуски на неточность изготовления.
Для рационального выбора заготовки необходимо одновременно учитывать все вышеперечисленные исходные данные так как между ними существует тесная взаимосвязь.
Окончательное решение можно принять только после экономического комплексного расчёта себестоимости заготовки и механической обработки в целом.
Заготовку будем получать литьем. Отливку второго класса точности можно получить несколькими способами литья. Так как наружные поверхности детали не подвергаются механической обработке их следует получить при изготовлении заготовки. Проведем сравнительный экономический расчет себестоимости заготовки при литье под давлением и литье по выплавляемым моделям.
Себестоимость заготовки можно определить по формуле:
Q – масса заготовки кг;
Sотх – цена 1 т отходов руб.;
q – масса готовой детали кг;
kт kс kв kм kп – коэффициенты зависящие от класса точности группы сложности массы марки материала и объема производства заготовок.
Данные необходимые для расчета стоимости заготовок получаемых литьем по выплавляемым моделям представлены в таблице 1.3.
Таблица 1.3 - Данные для расчета
В соответствии с формулой 1.5 стоимость заготовок получаемых литьем по выплавляемым моделям будет составлять:
Данные необходимые для расчета стоимости заготовок полученных литьем под давлением представлены в таблице 1.4.
Таблица 1.4 - Данные для расчета
На основании проведенных расчетов следует что наиболее рациональным способом получения заготовки для корпуса 456.852.32 является литье под давлением так как оно обеспечивает меньшую технологическую себестоимость детали.
Литье под давлением применяется в основном для получения фасонных отливок из цинковых алюминиевых магниевых и латунных сплавов. Способ считается целесообразным при партии 1000 и более деталей. Производительность метода до 1000 деталей в час. Можно получить отливки массой до 100 кг. с минимальной толщиной стенок 05 мм.; точность 11 12-го квалитетов по СТ СЭВ 144-75 параметр шероховатости поверхности до Ra=063 мкм.[8].
На основании справочных данных для корпуса 456.852.32 значения припусков и допусков представлены в таблице 1.5.
Таблица 1.5 – Значения припусков и допусков
Номинальный размер детали мм
Число предварите-льных обтачиваний
Допуск на размеры отливки мм
Припуск на механи-ческую обработку (на сторону) мм
Коробление отливки мм
Суммарный припуск на размер мм
Номинальный размер отливки мм
Наружные поверхности
Внутренние поверхности
6 Выбор технологических баз и оценка точности базирования
Процесс базирования заготовки заключается в её ориентации и последующем жёстком закреплении в координатной системе станка или приспособления в требуемом положении необходимом для выполнения операции обработки или сборки.
Для повышения точности обработки детали необходимо учитывать принцип совмещения баз т.е. конструкторская технологическая и измерительная базы должны совпадать. Если базы выбраны правильно то требуемая точность изготовления детали будет обеспечена.
В зависимости от числа идеальных опорных точек с которыми база находится в контакте или в зависимости от числа отнимаемых степеней свободы различают установочную базу находящуюся в контакте с тремя опорными точками; направляющую базу находящуюся в контакте с двумя опорными точками; упорную базу имеющую контакт с одной опорной точкой.
Каждая из перечисленных баз определяет положение заготовки относительно одной из плоскостей системы координат в направлении перпендикулярном к этой базе т.е. в направлении одной из координатных осей. Очевидно что для полной ориентировки заготовки в приспособлении необходимо использовать комплект из всех трёх баз.
Также при выборе баз необходимо учитывать дополнительные условия: удобство установки и снятия заготовки надежность закрепления заготовки в выбранных местах приложения сил зажима возможность подвода режущих инструментов с разных сторон заготовки и др. Для установки заготовки на первой операции используют необработанные поверхности так называемые черновые базы.
Базовые поверхности по маршруту обработки корпуса 456.852.32 представлены в таблице 1.6.
Таблица 1.6 - Базирование по маршруту обработки
Верхняя и нижняя поверхности
Верхняя нижняя и внутренние поверхности
Продолжение таблицы 1.6
Верхняя поверхность и два отверстия
Расчет точности обработки производится с целью оценки величины возможного рассеивания заданного параметра. Вследствие погрешности выполнения базовой поверхности заготовок неточности изготовления износа опорных элементов приспособления нестабильности усилия закрепления положения заготовок в приспособлении будут разным. Погрешность установки заготовок в приспособлении Δу вычисляют с учетом погрешности базирования Δб погрешности закрепления заготовок Δз и погрешности изготовления и износа опорных элементов приспособления Δпр. Погрешность установки определяют как предельное поле рассеивания положений измерительной поверхности относительно поверхности отсчета в направлении выдерживаемого размера[6]. Так как указанные выше погрешности являются случайными величинами то
где Δб - погрешность базирования;
Δз - погрешность закрепления;
Δпр – погрешность приспособления.
Погрешность базирования по размеру:
Погрешность закрепления заготовки:
так как сила зажима действует перпендикулярно выдерживаемому размеру.
Погрешность установки по размеру:
Суммарная погрешность обработки:
где - поправочный коэффициент[2]
- погрешность технологической системы определяемая как средняя экономическая точность обработки.
Допустимая погрешность установки[2]:
где Т – допуск размера мм.
Следовательно и предлагаемая схема базирования приемлема.
Суммарная погрешность приспособления[2]:
При применении данного приспособления требуемый параметр будет выдержан.
7 Разработка маршрута операций технологического процесса обработки
Разработку технологического процесса начнем с загрузки в рабочее поле системы режима «Технология» из раздела «Базы данных».
Перед началом разработки нового технологического процесса очистим поле текущей технологии (рисунок 1.3) произведя двойной щелчок на пиктограмме «Очистка технологии». Во всех таблицах текущей технологии будут удалены все записи.
Рисунок 1.3 – Очистка поле текущей технологии
Ввод данных начнем с таблицы «Деталь». Процесс ввода и редактирования полей записи на всех уровнях идентичен. Для загрузки формы просмотра и корректировки полей нажимаем на инструментальной панели кнопку «Редактирование записи» или клавишу F4>. Данная форма имеет следующую структуру: слева располагаются имена полей справа — их значения.
Данные вводим с клавиатуры установив курсор в заполняемом поле или копируем из справочной базы данных (БД). Признаком привязки такой БД к определенному полю записи является пиктограмма «Книга» справа от поля ввода данных (рисунок 1.4). Справочные БД могут быть подключены к любому полю. Например в таблице «Деталь» к соответствующим полям подключены БД по материалам заготовкам наименованиям деталей и т.д.
Рисунок 1.4 – Обращение к справочной базы данных
Переход на уровень Операции осуществляем использованием команды «Переход на следующую таблицу» на инструментальной панели или клавиши F12>. При начальном вводе таблица Операции не содержит записей. Необходимо зарезервировать нужное количество строк клавишей Insert>. Затем последовательно в каждую строку вводим информацию об одной технологической операции. Порядок следования операций в технологическом маршруте задается порядком расположения строк в таблице. Режим корректировки полей F4> осуществляет загрузку формы редактирования (рисунок 1.5) аналогичной использующейся на уровне Деталь.
Рисунок 1.5 - Структура записи таблицы «Операции»
Информация в поля таблицы расположенной на уровне Операции может вводить как с клавиатуры так с помощью справочных баз данных.
После того как введены сведения об операциях вводим данные о переходах. Для этого следует устанавливаем курсор на нужную операцию и нажимаем клавишу F12>. Система переходит к следующему объекту и в рабочее поле системы будет загружена таблица Переходы.
Поскольку таблицы Операции и Переходы связаны уникальным ключевым полем ID (генерируемым автоматически при каждом вводе новой операции) то каждая строка объекта Операции будет иметь подчиненный список записей в таблице Переходы. При первоначальном вводе она не содержит записей. Нужно зарезервировать необходимое количество пустых записей клавишей Insert> и войти в режим редактирования первой строки нажав клавишу F4>.
Справочная таблица Тип перехода содержащая список наименований доступных баз данных представлена на рисунке 1.6.
Рисунок 1.6 - Справочные базы данных таблицы «Переходы»
Выделяем курсором нужную БД и двойным щелчком помещаем ее в рабочее поле системы. Из загруженного справочника выбираем информацию последовательно нажимая клавишу F12>. При достижении последнего уровня все необходимые данные будут скопированы и система вернется в форму редактирования записи таблицы Переходы. В зависимости от вида выбранной информации на форме «Редактирование записи» меняются наименования полей. Так например если были выбраны данные о режущем инструменте (рисунок 1.7) поле «Переход» изменит свое название на «Режущий инструмент». Данный механизм реализуется с помощью специальных режимов управления логической структурой данных F3>.
Рисунок 1.7 - Выбор режущего инструмента из справочника
В поле дублирующей технологии могут помещаться как реальные ТП связанные с базой данных КТС так и типовые ТП доступ к которым осуществляется из режима «Архив типовых технологий» в КОМПАС-АВТОПРОЕКТ-Технология.
Технологический процесс может быть разработан на основе библиотеки типовых операций. Последовательность действий реализующих данный режим будет рассмотрена для проектирования фрезерной операции ТП «корпус».
Подсистема «Сквозной ТП» позволяет сформировать технологию состоящую из операций и переходов (рисунок 1.8). В режиме текущей технологии на уровне «Операции» при обращении к справочнику в отличие от других подсистем диалог начинается с выбора вида операции. После выбора требуемого и нажатия клавиши F12> загружается соответствующая база данных. Из базы данных выбирается всё необходимое и таким образом формируется технологический переход и весь ТП в целом.
Рисунок 1.8 - Сквозной технологический процесс
Для просмотра созданной технологии используем «Дерево технологий».
Чтобы представить данные о техпроцессе в виде дерева (рисунок 1.9) производим двойной щелчок мыши на пиктограмме с изображением дерева в области «Процедуры» режима «Технология функции». Стартует приложение treetex.exe на форму которого выводятся два технологических процесса. Реализован механизм копирования и перемещения данных между этими ТП. Технологические операции копируются из одной технологии в другую вместе с подчиненными таблицами. Структура дерева включает четыре уровня:
- разделы: «Переходы» «Эскизы» «Карты» «Контроль» «Комментарии»;
- содержимое разделов.
Рисунок 1.9 - Дерево технологий
Когда технологический процесс в поле текущей технологии сформирован и отредактирован переходим к разработке комплекта документации. Для этого щелкаем мышью на пиктограмме с изображением карт в области Процедуры. Стартует программа формирования комплекта технологической документации. Результатом данной процедуры является комплект документов технологического процесса обработки резанием представленный приложением к выпускной квалификационной работе.
8 Обоснование выбора моделей оборудования
Выбор модели станка прежде всего определяется его возможностью обеспечить точность размеров и формы а также качество поверхности изготовления детали. Также следует учитывать соответствие станка габаритам обрабатываемых деталей устанавливаемых по принятой схеме обработки соответствие станка по производительности заданному масштабу производства соответствие станка по мощности наименьшая себестоимость обработки.
После сравнения станков на функциональное назначение технические и рабочие характеристики с теми характеристиками и показателями которые необходимо получить в результате обработки корпуса 456.852.32 был сделан выбор станочного оборудования. Данные по выбору оборудования представлены в таблице 1.7.
Таблица 1.7 – Оборудование по маршруту обработки
Вертикально-фрезерная
Вертикально-фрезерный станок FSS350R
Вертикально-сверлильный
Вертикально-сверлильный станок 2Н118
Горизонтально-расточная
Горизонтально-расточной станок 262ОГФ1
Вертикальный консольно-фрезерный станок модели FSS350R (аналог станка 6Т12) предназначен для фрезерования всевозможных деталей из стали чугуна и цветных металлов торцевыми концевыми цилиндрическими радиусными и другими фрезами. На станках можно обрабатывать вертикальные горизонтальные и наклонные плоскости пазы углы рамки зубчатые колеса. Технические характеристики станка FSS350R в таблице 1.8.
Таблица 1.8 - Технические характеристики станка FSS350R
Размеры рабочей поверхности стола(длина ширина) мм
Наименьшее и наибольшее расстояние от торца шпинделя до рабочей поверхности стола мм
Расстояние от оси шпинделя до вертикальных направляющих станины мм
Перемещение стола на одно деление лимба(продольное поперечное вертикальное) мм
Посадочное место для крепление инструмента крутой конус
Продолжение таблицы 1.8
Наибольшее перемещение стола мм
Наибольшая масса обрабатываемой детали кг
Мощность электродвигателя главного движения кВт
Частота вращения шпинделя обмин
Наибольшее осевое перемещение шпинделя мм
Универсальный вертикально-сверлильный станок модель 2Н118 предназначен для выполнения следующих операций: сверление рассверливания зенкерования нарезания резьбы и подрезки торцов ножами. Технические характеристики станка 2Н118 в таблице 1.9.
Таблица 1.9 - Технические характеристики станка 2Н118
Наибольший диаметр сверления мм
Конус Морзе шпинделя
Расстояние от конца шпинделя до стола мм
Продолжение таблицы 1.9
Тип двигателя главного движения
Номинальное напряжение В
Число оборотов двигателя обмин
Пределы частот вращения шпинделя обмин
Габариты(длина х ширина х высота) мм
Горизонтально-расточной станок 262ОГФ1 предназначен для комплексной обработки сложных корпусных деталей из конструкционных материалов в условиях многономенклатурного производства в автономном режиме или в составе гибких производственных систем. Технические характеристики станка 262ОГФ1 в таблице 1.10.
Таблица 1.10 - Технические характеристики станка 262ОГФ1
Исполнение конуса шпинделя
Мощность главного привода кВт
Скорость вращения шпинделя
Наибольшая масса обрабатываемой заготовки кг
Программируемые перемещения:
- сани стола – по оси Х мм
- шпиндельная бабка вертикально – по оси Y мм
- ползун продольно – по оси Z мм
- поворотный стол – по оси А рад
9 Обоснование конструкции и расчет специальных средств технологического оснащения
9.1 Станочное установочно-зажимное приспособление
Проектируемое установочно-зажимное приспособление предназначено для установки и закрепления заготовки на горизонтально-расточном станке 262ОГФ1.
Использование этого приспособления предполагается на третьей операции. Базирование заготовки происходит на плоскость и 2 пальца (цилиндрический и срезанный). Обрабатываемые поверхности и выдерживаемые размеры представлены в графической части работы.
Закрепление происходит приложением силы зажима перпендикулярно к ее базовой плоскости. Эта схема обеспечивает доступность режущего инструмента к обрабатываемой заготовке с разных сторон. При этом конструкция приспособления является достаточно простой.
Направление и максимальное значение силы резания рассчитывается исходя из условия неподвижности заготовки при обработке. Данные для расчета берутся в справочной литературе.
Направление силы резания будет параллельно обрабатываемой плоскости и будет стремиться сдвинуть заготовку перпендикулярно нормали к обрабатываемой плоскости (рисунок 2.13)
Рисунок 2.13 – Схема действия сил
Величина силы резания рассчитывается по формуле (2.2):
Где t – глубина резания в мм.;
s – подача в мм.зуб;
v – скорость резания м.мин.;
Кр – поправочный коэффициент учитывающий фактические условия резания;
Численные значения показателей степени коэффициентов Кр и Ср представлены в справочной литературе [5].
Посчитаем максимальную силу резания по формуле (2.2):
Сила зажима при данной схеме закрепления определяется по формуле (2.3):
где К - коэффициента надежности закрепления К=365;
- коэффициенты трения.
В нашем случае опираясь на схему действия сил (рисунок 2.13) делаем вывод что сила исходного закрепления равна силе закрепления .
Диаметр пневмоцилиндра определяется по формуле:
где D – рабочий диаметр цилиндра мм;
р – давление рабочее в пневмосистеме МПа.
По конструктивным соображениям принимаем диаметр мембраны 100мм тем самым обеспечиваем дополнительный запас по усилию прижатия заготовки.
При проектировании приспособления необходимо предусмотреть отверстия в плите для выхода инструмента при цикле обратной расточки.
Приспособление базируется на станке посредством трех взаимно перпендикулярных плоскостей. Базирование происходит по боковым направляющим в угол тумбы станка которая закреплена на столе где «закреплен» программный ноль станка. Координация элементов приспособления происходит по двум плоскостям.
9.2 Контрольное приспособление
При изготовлении детали необходимо выполнить требования точности взаимного расположения поверхностей.
На чертеже детали указаны требования к точности взаимного расположения поверхностей. Это неперпендикулярность поверхностей 9 и 1. Не перпендикулярность должна быть не более 004 мм.
В этом пункте разработана схема контроля (рисунок 2.14) поверхностей 9 и 1. В этой схеме используется плита 1 прилегающая к поверхности 1 и разжимная самоцентрирующаяся оправка 2 которая жестко связана с плитой и перпендикулярна ей. Неперпендикулярность плиты и оправки назначается в соответствии со справочной литературой и равна 0003 мм. На оправку закреплен индикаторный узел 4 который может вращаться на ней. Между узлом и оправкой посадка с зазором H7h6. Максимальный зазор между оправкой и индикаторным узлом составляет 0027 мм. В индикаторном узле применяется индикатор многооборотный 1 МИС ГОСТ 9696-75 с ценой деления 001 мм. Предельная погрешность измерения составляет 003 мм. Плита выполняется с непараллельностью ее плоскостей 0002 мм.
Разжимная самоцентрирующаяся оправка выполнена с тремя шариками 5 которые разжимаются упорным винтом 3.
Рисунок 2.14 – Схема контроля
Произведем расчет погрешности измерения при использовании этой оправки.
Погрешность измерения будет складываться из следующих составляющих: непараллельности плоскостей плиты неперпендикулярности оправки плите половина зазора между индикаторным узлом и оправкой и погрешностью индикатора.
Суммарная максимальная погрешность измерения вычисляется по формуле (2.5):
где Dпар – непараллельность плоскостей плиты;
Dпер – неперпендикулярность оправки и плиты;
S – зазор между индикаторным узлом и оправкой;
Dизм – погрешность измерения.
По формуле (2.5) получаем:
Исходя из вышеизложенного можно составить порядок работы данного контрольного приспособления.
Установить на приспособление индикатор 1 МИС ГОСТ 9696-75.
Установить приспособление на деталь оперев плоскостью и вставив оправку в отверстие.
Винтом разжать оправку вращая болт от руки до упора.
Проверить визуально плотности прилегания плиты к детали.
Установить на индикаторе предварительный натяг 1 мм.
Установить нулевое положение на шкале индикатора.
Повернуть индикаторный узел вокруг оправки на 180° следя за показаниями индикатора.
Деталь считать годной при отклонении стрелки индикатора от нулевого положения не более чем на 012 мм (12 делений индикатора).
Вывернуть разжимной болт.
Снять приспособление с детали.
Снять индикатор с приспособления.
10 Аналитический расчет технологических параметров
Расчет припусков для отверстия 40 Н9 (40 +0062)
Минимальный припуск определяется по формуле 1.9:
ei – погрешность установки заготовки на выполняемом переходе.
Результаты расчетов заносятся в карту расчета припусков на обработку (таблица 1.11).
Таблица 1.11 - Карта расчета припусков
Допуск на изготовление
Размеры по переходам
Полученные предельные припуски
Проверка расчета осуществляется по формуле 1.10:
Tdз – Тdд = 2z0min – 2z0max(1.10)
гдеTdз – допуск на заготовку;
Тdд – допуск на готовую деталь;
z0max - общий максимальный припуск.
00-62=4910-2472=2438 мкм.
Схема припусков изображена на рисунке 1.10.
Рисунок 1.10 – Схема припусков
Определим режимы резания на фрезерование расчётно-аналитическим методом.
Операция 010 фрезерная.
Фрезеровать поверхность; глубина фрезерования t=31 мм; ширина фрезерования В = 80 мм; диаметр фрезы D = 80 мм; число зубьев фрезы z = 8 шт; подача Sz = 035мм.об.; период стойкости фрезы Т = 180 мин.
Скорость резания при фрезеровании определяется по формуле:
Значение коэффициента C и показателей степени приведены в [5 таблица 39 с. 286]. Общий поправочный коэффициент на скорость резания учитывающий фактические условия резания:
где Kmv - коэффициент учитывающий качество обрабатываемого материала;
Knv - коэффициент учитывающий состояние поверхности заготовки;
Kuv -коэффициент учитывающий материал инструмента.
Частота вращения шпинделя определяется по формуле:
nприн = 300 обмин - ближайшее большее значение числа оборотов по паспорту станка.
Сила резания при фрезеровании определяется по формуле:
где z - число зубьев фрезы; n - частота вращения шпинделя об.мин.
Значения коэффициента Q и показателей степени приведены в [5 таблица 41 с. 196] поправочный коэффициент на качество обрабатываемого материала Кмр для алюминия - в [5 таблица 10 с. 265].
Эффективная мощность резания определяется по формуле:
Производим проверку выбранного режима по мощности.
Мощность электрического двигателя станка (с учетом его к.п.д.) должна быть больше мощности резания т.е.
Мощность электрического двигателя вертикально-фрезерного станка
Nдв=8 кВт = 08 следовательно 188 кВт 64 кВт.
Мощность привода достаточна для выполнения операции на расчетных режимах резания.
Остальные режимы резания рассчитываем при помощи КОМПАС-АВТОПРОЕКТ Технология.
11 Автоматизированное проектирование технологического процесса изготовления детали и средств технологического оснащения
11.1 Обоснование выбора программных средств для проектирования технологической подготовки производства
В связи с большим количеством различных систем автоматизированного проектирования предлагаемых рынком в настоящее время все большую актуальность приобретают вопросы связанные с оптимальным выбором конкретных программ а также со стратегией их внедрения. Для крупных машиностроительных предприятий существенную роль играют такие параметры как цена функциональные возможности наличие систем параметризации и ассоциативности возможность интеграции и обмена данными с другими программами совместимость с технологическим оборудованием наличие средств разработки прикладного программного обеспечения удобство интерфейса наличие русскоязычной документации динамичность развития системы.
Необходимо обратить внимание на особенности движения модели изделия между основными элементами разработанной ранее схемы внедрения. Лучший вариант – это передача модели из одного элемента схемы в другой без применения конверторов преобразование данных что обеспечит гибкую ассоциативную связь между основными блоками сквозной системы проектирования а также позволит сэкономить время при групповой работе над одним проектом. В противном случае может возникнуть следующая картина: например если разработанную в какой-либо одной 3D-CAD-системе модель передать через встроенные конверторы в систему CAM с целью подготовки управляющих программ для станков с ЧПУ то произойдет разрушение параметризации и ассоциативности. Последнее приводит к потере рабочего времени так как после модификации исходной модели изделия необходимо самостоятельно обновлять управляющую программу.
В дипломном проекте будем использовать следующие программы: для построения модели детали – КОМПАС-3D для проектирования технологии изготовления детали – КОМПАС-АВТОПРОЕКТ 9.3; для решения технологических задач – COSMOSWorks 2006; для проектирования операционной технологии с разработкой управляющих программ и виртуальным моделированием обработки для станков с ЧПУ – ГеММа – 3D.
11.4 Проектирование операционной технологии с разработкой управляющих программ и виртуальным моделированием обработки для станков с ЧПУ в САПР
Система ГеММа-3D предназначена для разработки управляющих программ при изготовлении деталей высокой сложности на всех типах станков с ЧПУ.
ГеММа-3D является самостоятельной CAM-системой состоит из нескольких модулей обеспечивающих в совокупности полный сервис для работы технолога-программиста или оператора станка с ЧПУ.
Помимо этого система ГеММа-3D позволяет создавать программы обработки наиболее сложных деталей изготавливаемых с помощью фрезерования сверления электроэрозионной резки вырубки токарной обработки гравировки. В состав системы входит библиотека постпроцессоров в исходных текстах.
Среди возможностей программы: собственный геометрический редактор для создания математических моделей деталей и агрегатов; импорт моделей из всех известных CAD-систем и их доработка в соответствии с конкретным инструментом применяющимся на оборудовании с ЧПУ; подготовка управляющих программ с использованием любых видов геометрических данных плоских эскизов чертежей и поверхностей. При импорте модели комбинация их с твердыми телами. Задание контурной или поверхностной заготовки произвольной формы и сравнения результата обработки с математической моделью для оценки точности изготовления. Также при использовании программы ГеММа-3D возможно параметрическое задание технологических данных как в переходах так и между переходами; использование станочных циклов с их настройкой на любые УЧПУ; подготовка технологических эскизов и технологических карт; визуализация обработки и возможность редактирования управляющих программ. Программа позволяет подготавливать управляющие программы для токарных сверлильных фрезерных и других станков с ЧПУ.
Создаём контур детали для обработки в КОМПАС-3D и сохраняем *.dxf после этого импортируем этот файл в ГеММа – 3D (рисунок 1.10).
Рисунок 1.10 – Создание контура и импортирование его в ГеММа – 3D
В верхнем выпадающем меню выбираем в разделе «Обр.2D» «токарный контур» в появившемся окне задаём параметры инструмента стратегию обработки и параметры управляющей программы (рисунок 1.11).
Рисунок 1.11 – Задавание параметра инструмента стратегии обработки и сохранение прохода
После задания всех необходимых параметров нажимаем кнопку «Ввод» после чего система переходит в режим диалога. На запрос «Укажите обрабатываемую часть контура» правой кнопкой мыши указываем внешний контур (ПКМ) и нажатием ПКМ подтверждаем выбор. При запросе «Обрабатываемая часть» нажатием ЛКМ выбираем внешнюю часть контура и нажатием ПКМ подтверждаем выбор. Далее в открывшемся окне вводим координаты точки начала обработки.
Запрос – «Направление верно?» - ЛКМ выбираем направление ПКМ – подтверждаем выбор.
Запрос – «Координаты точки конца обработки» – в открывшемся окне вводим координаты – «Ввод».
Далее система формирует проход по контуру и предлагает сохранить этот проход. Если всё устраивает нажимаем кнопку «Да» (рисунок 1.11).
Для создания управляющей программы в верхнем выпадающем меню нажимаем «Обр.2D» и выбираем «Управл. прогр.» «Новая». В открывшемся окне нажимаем кнопку «Добавить ряд проходов» и указываем все созданные проходы после чего нажав кнопку «Постпроцессор» выбираем нужный и нажимаем кнопку «Создать УП» (рисунок 1.12).
Рисунок 1.12 – Создание и открытие управляющей программы
Ниже представлена управляющая программа для горизонтально – расточного обрабатывающего центра с ЧПУ 262ОГФ1 (операция 025 – «Расточная») разработанная при помощи системы автоматизированного проектирования технологических процессов ГеММа-3D.
PROGRAMME 00 CC100M M RWED 4
N8X-14.374Y-5.88F198.9
N14X-45.734Y-5.507F198.9
N19X14.187Y-48.627F198.9
N24X54.133Y-48.814F198.9
N30X-50.027Y9.053F198.9
N36X-3.018Y-1.036F198.9
N41X70.954Y-1.237F198.9
N46X58.954Y-50.057F198.9
N52X-14.068Y-5.887F198.9
N58X-46.198Y-5.916F198.9
N64X-8.946Y-6.064F198.9
N70X-50.92Y-5.978F198.9
12 Технологическое проектирование производственного подразделения
12.1 Расчет количества технологического оборудования и графика загрузки станков
Расчетное количество станков по i-той группе оборудования определяется на основании трудоемкости производственной программы и действительного фонда времени оборудования [11]:
где Nj - годовая программа выпуска деталей j-го типа шт;
n - количество наименований деталей обрабатываемых на i-й группе оборудования.
где Др- число рабочих дней в году;
mсм- число рабочих смен в сутки;
tсм- продолжительность рабочей смены (принять равным 8ч.);
kп - плановые потери времени на ремонт % (kn =2-8 %).
Годовой эффективный фонд времени работы одного станка
Средние коэффициенты загрузки оборудования по группам Кэi и по участку Кзу рассчитываются по формулам:
где m - число групп оборудования на участке.
Расчетное количество станков вертикально-фрезерной группы:
Коэффициент загрузки станков группы:
Расчетное количество станков вертикально-сверлильной группы:
Коэффициент загрузки станков:
Расчетное количество станков горизонтально-расточной группы:
Коэффициент загрузки станков горизонтально-расточной группы:
FSS350R 2Н118 262ОГФ1
Рисунок 1.13 - График загрузки оборудования на участке изготовления корпусов 456.852.32
Результаты расчетов количества оборудования и коэффициентов загрузки заносятся в таблицу 1.11.
Коэффициент загрузки оборудования участка:
Таблица 1.11 - Расчет потребности оборудования на участке
Вертикально-фрезерный
Горизонтально-расточной
12.2 Определение производственной площади участка
Производственная площадь участка занимаемая непосредственно оборудованием и рабочими местами определяется исходя из удельной площади приходящейся на один станок и числа основных станков.
Удельная площадь на один мелкий станок – 10 – 12 м2 средний станок - 15 – 25 м2 крупный 30 -45 м2.
К мелким станкам относятся станки с габаритами до 1800х800 мм средним – до 4000х2000 мм к крупным – до 8000х4000 мм.
На участке по изготовлению корпуса 456.852.32 располагаются 1 мелкий и 2 средних станка.
Производственная площадь участка рассчитывается исходя из удельной площади приходящейся на один станок:
где К – количество станков;
Sуд – удельная площадь на один станок.
Производственная площадь непосредственно занимаемая оборудованием:
Проходы и проезды составляют до 20% производственной площади:
Общая площадь производственного участка составляет:
12.2.1 Выбор системы складирования
В единичном и серийном производствах цеховой склад заготовок и полуфабрикатов размещают в начале пролетов в соответствии с обрабатываемыми деталями. Для хранения крупных заготовок склады располагают на специальных открытых или закрытых эстакадах для хранения 2÷3-х дневного запаса заготовок. Хранение штучных грузов (отливок поковок деталей и т.д.) должно производиться в унифицированной таре которая позволяет использовать механизированные погрузочно-разгрузочные транспортирующие устройства и многоярусное хранение в штабелях или на стеллажах. Запас материалов и заготовок в цеховом складе должен быть невелик так как назначением его является только обеспечивать регулярное снабжением цеха (участка) материалами. При расчете площади складов заготовок исходят из необходимости запаса и грузонапряженности пола [14]:
где Р – площадь складов заготовок м2;
Q – масса заготовок обрабатываемых в цехе в течение года т;
Т – запас заготовок дни;
f – среднее число рабочих дней в году;
q – средняя грузонапряженность склада тм2;
кр – коэффициент использования площади склада представляющий отношение полезной площади склада к его общей площади и учитывающий проходы и проезды (кр = 04÷05).
Склад готовых деталей предназначен для хранения деталей перед отправкой на сборку. Склад готовых деталей и комплектовочный склад размещают в конце пролетов механического цеха на пути следования деталей на сборку. Площадь склада готовой продукции определяется также как и общая площадь под заготовки и материалы. Грузонапряженность площади пола складов принимается меньшей чем в цеховом складе заготовок так как готовые детали хранятся как правило на стеллажах или специальных подставках столах и таре. Допускаемую грузонапряженность следует принимать равной: при удельном весе материалов более 1÷4 т на 1 м2 для мелких и средних деталей и 15 т на 1 м2 для крупных; при удельном весе материалов до 4 т – соответственно 04 и 06 на 1 м2.
12.3 Расчет численности персонала
В серийном производстве численность основных рабочих для выполнения нормируемых работ определяется по формуле [11]:
Nj- годовой объем выпуска изделий j-го вида шт.;
Фд.р.- действительный годовой фонд времени работы рабочего ч.;
Квн- коэффициент выполнения норм на i-й операции.
где a - коэффициент учитывающий потери рабочего времени - неявки установленные законодательством (можно принять 2-12%).
Численность рабочих для вертикально-фрезерной операции:
Численность рабочих для вертикально-сверлильной операции:
Численность рабочих для горизонтально-расточной операции
Трудоемкость работ выполняемых за год по вертикально-фрезерной операции N1:
(404 х 3010) 60 = 202673 (н.ч).
Трудоемкость работ выполняемых за год по вертикально-сверлильной операции N2:
(11824 х 3010) 60 = 59317 (н.ч).
Трудоемкость работ выполняемых за год по горизонтально-расточной операции N3:
(2596 х 3010) 60 = 130233 (н.ч).
Таблица 1.12 - Расчет требуемого количества основных рабочих
обслуживаемых станков
Общая трудоемкость работ выполняемых за год нормо-ч
Количество рабочих чел
Оператор станков с ЧПУ
Определение численности вспомогательных рабочих производится по нормам обслуживания. На основании этих норм составляется ведомость вспомогательных рабочих (таблица 1.13).
Таблица 1.13 – Ведомость вспомогательных рабочих
Определяющий показатель
Норма обслуживания на 1 рабочего
Расчетное количество чел
Слесари по ремонту оборудования
Электромонтеры (дежурные)
Количество ед. оборудо-вания в смену
Слесари по ремонту и оснастке
Водители электрокар и автопогрузчиков
Количество тонн груза в смену
(при массе изделий до 1 кг)
Слесарь по межремонтному обслуживанию
Продолжение таблицы 1.13
Подносчики и раздатчики инструмента
Единиц оборудования на человека
Распределители работ
Количество основных рабочих
Процент от чис-ленности основных рабочих
Уборщики производственных помещений
Убираемая площадь м2
При расчете численности ИТР следует пользоваться следующими нормативами. В подчинении мастера должно быть 20-25 рабочих; старший мастер назначается для руководства не менее чем для двух мастеров (участка или сменными); начальник участка руководит двумя-тремя старшими мастерами; начальник цеха руководит четырьмя – пятью начальниками участка.
На основании нормативов количество мастеров на участке:
На основании нормативов количество старших мастеров:
1 Эксплуатация режущего инструмента
1.1 Эксплуатация резцов
Эффективное использование резцов возможно в условиях повышенной жесткости точности и быстроходности станков.
Для повышения жесткости системы СПИД необходимо закреплять заготовку в патронах при длинных заготовках – в патронах с поджимом центром задней бабки сокращать вылет резца из резцедержателя при строгании вылет резца устанавливать в пределах 18-80 Н для отогнутых и 08-10 Н для прямых резцов [5].
Глубина резания при черновой обработке выбирается наибольшей. Подача назначается с учетом рекомендаций приведенных в таблицах 4.1 4.2
Таблица 4.1 – Ориентировочные значения подачи (мм.об.) для чернового точения труднообрабатываемых материалов с sв 900 МПа
Диаметр заготовки мм
Глубина резания t мм
Примечание. К труднообрабатываемым материалам отнесены теплостойкие хромоникелевые хромомолибденовые сложнолегированные стали перлитного ферритного мартенситного аустенитного и аустенитно-мартенситного классов.
Таблица 4.2 – Ориентировочные значения подачи (ммоб) для чернового точения конструкционных углеродистых сталей стального и чугунного литья
Продолжение таблицы 4.2.
Примечание. Большие значения подач следует принимать для обработки мягких сталей при работе в центрах с отношением длины к диаметру заготовки меньше 6 или в патроне с отношением длины вылета из патрона к диаметру заготовки меньше 2.
Ниже приведены данные характеризующие зависимость поперечной подачи s мм.об. от ширины резца амм и диаметра отрезки D мм обрабатываемого материала при отрезке отрезными резцами:
В условиях малой жесткости СПИД глубину резания при точении следует уменьшать до 03 мм угол в плане выбирать не менее 60° резец устанавливать выше центра на 11-15 % от диаметра обработки.
Рекомендуемые размеры площади поперечного сечения резцов при точении в зависимости от площади сечения срезаемого слоя приведены в таблице 4.3.
Таблица 4.3 – Размеры площади поперечного сечения резцов (НхВхН) с углом в плане (j = 45°) в зависимости от площади сечения срезаемого слоя
Площадь сечения срезаемого слоя мм2
Значение допустимого износа по задней грани резцов из быстрорежущих сталей и резцов оснащенных твердым сплавом рекомендуется принимать равным значениям приведенным в таблице 4.4.
Таблица 4.4 – Допустимый износ h3 резцов из быстрорежущих сталей мм
Обрабатываемый материал
Сталь стальное литье чугун ковкий при работе
Токарный проходной подрезной или расточной
Токарный прорезной и отрезной
Строгальный проходной
Строгальный поперечный подрезной
Долбежный прорезной и отрезной
В таблице 4.6 приведены возможные неисправности при точении твердосплавными резцами и рекомендуемые меры по их устранению.
Таблица 4.6 – Возможные неисправности при точении твердосплавными резцами и рекомендуемые меры по их устранению
Возможные неисправности
Пластическая деформация лезвия
Увеличить скорость резания
Уменьшить скорость резания
Продолжение таблицы 4.6
Уточнить скорость глубину подачу
Выбрать более прочную марку сплава
Увеличить радиус при вершине
Увеличить положительный передний угол
Применить больший задний угол
Применить более жесткий резцедержатель
Увеличить жесткость СПИД
Исключить водные СОЖ
Применить меньший отрицательный передний угол
Уточнить радиус при вершине
Снизить припуск на переточки
1.2 Эксплуатация фрез
С целью экономической работы и длительной службы фрез необходимо придерживаться следующих правил: применять только рекомендуемые режимы резания а не применять слишком больших подач и скоростей резания своевременно затачивать фрезу следить за тем чтобы износ режущих кромок не доходил до крайних допустимых норм (таблица 4.7) и ориентироваться по допустимой шероховатости обрабатываемой поверхности при фрезеровании малых деталей небольшими фрезами малой производительности рекомендуется более часто подправлять (доводить) режущие кромки фрез чугунным притиром с пастой не снимая фрез со станка не останавливать и не включать вращения шпинделя пока фреза находится в контакте с заготовкой следить чтобы станок работал без вибраций [5].
Таблица 4.7 – Допустимый износ по задней поверхности зуба фрезы
Материал режущей части фрезы
Допускаемый износ по задней поверхности мм
с напаянными пластинками
Прорезные и отрезные
После заточки и доводки у фрезы контролируют биение режущих кромок размеры рабочей части инструмента геометрические параметры и чистоту режущих поверхностей. Допустимое радиальное биение зубьев фрез приведено в таблице 4.8. Допустимые отклонения углов заточки a a1 и g до 10° находятся в пределах ±1° а при их значениях равных 10-20° ±2° отклонение угла в плане
j ± (2-3°) j0 ± 2° и вспомогательного угла в плане j1 ± (0°30-1°).
Таблица 4.8 – Допустимое биение фрез мм.
между двумя смежными зубьями
для двух противоположных зубьев
Цельные насадные торцовые цилиндрические и дисковые
Насадные цилиндрические со вставными ножами из быстрорежущей стали
Насадные цилиндрические оснащенные пластинками из твердого сплава
Сборные насадные торцовые и дисковые
Цельные концевые из быстрорежущей стали и твердого сплава
Пазовые затылованные
Отрезные и прорезные классов
1 Выбор режимов обработки для электрохимического маркирования
Маркирование металлических изделий применяется в тех отраслях машиностроения где необходимо опознавание каждой отдельной детали на всех стадиях обработки и сборки. Отсутствие опознавательного знака на деталях может привести к значительным задержкам сборки изделий ввиду необходимости повторного установления отличительных признаков.
Одним из методов маркирования является электрохимическое маркирование. Процесс протекает в водных растворах нейтральных солей (хлористого натрия азотнокислого калия и др.) при напряжении технологического тока до 8 (В).
При расчётных режимах маркирования можно получать контуры знаков с шириной штриха менее 01 (мм). Это обеспечивает нанесение информации стандартными шрифтами высотой знака 15 (мм) и более.
Электрохимическим методом можно маркировать детали любой формы и габаритов из токопроводящих материалов. Силы возникающие в зоне формирования знаков не превышают 100 (Н) что не может вызвать деформацию и поломку деталей.
Использование электрохимического маркирования позволяет механизировать и автоматизировать процесс повысить качество наносимой информации при снижении трудоёмкости операции.
Процесс электрохимического маркирования имеет свои специфические особенности: во-первых его осуществляют без прокачки электролита; во-вторых требуемая для маркирования малая ширина штриха рабочей части катода существенно меняет условия газонаполнения массопереноса в зазоре что оказывает определяющее влияние на технологические показатели процесса.
Применяемые при маркировании электролиты не должны содержать соединений которые могут образовать твёрдые продукты восстановления на катоде. Поэтому в основном используют нейтральные растворы солей щелочных металлов при которых образующиеся на аноде ионы тяжёлых металлов не достигают катода переходя в гидроокиси в межэлектродном промежутке или в прикатодном диффузионном слое. Для получения точного отображения катода на аноде необходимо применять электролиты с малой электропроводностью и большой пассивирующей способностью. Это обеспечивает требуемую ширину штриха.
В данном случае для маркировки корпуса из материала АК7 (алюминиевый сплав) выбираем следующий состав электролита: бромистый калий 5-10% азотнокислый аммоний 5-10% [13].
Также необходимо определить напряжение на электродах. Нижний предел напряжения обуславливается условиями поддержания химических реакций на электродах и составляет 3-4 (В). Максимальное напряжение ограничивается возможностью электрического пробоя между электродами требованиями техники безопасности и целесообразностью реализации больших рабочих токов проходящих через электрохимическую ячейку.
Напряжение выбирают в диапазоне 3-30 (В). При маркировании когда величина рабочего зазора колеблется от 002 - 015 (мм) рабочий диапазон 3 -16 (В). При напряжении 9-11 (В) получается хорошая чёткость и стойкость знака при удовлетворительной точности и допустимом содержании водорода. Эти значения можно принять в качестве рабочего диапазона изменения напряжения.
Значения напряжения и времени обработки: напряжение 6-7 (В) время -1 (с) [13]. Время обработки должно быть выдержано с погрешностью не более 01 - 02 (с) иначе резко нарушается качество знаков. Информацию можно наносить на поверхность с шероховатостью не выше Rа = 5 (мкм).
Носителем информации при электрохимическом маркировании является контур нанесённый на рабочую поверхность инструмента профильными знаками.
При получении рабочей части инструмента с использованием шрифтов подобранные знаки отливают по технологии типографского производства далее производят механическую обработку рабочей поверхности (сверление мелких отверстий для удержания изоляции зачистку профиля и др.). После изготовления рабочие части инструмента окончательно контролируют устанавливают соответствие чертежу номера шрифта положение и наличие всех знаков контролируют качество диэлектрических покрытий и выступов определяющих межэлектродный зазор.
Для мелкого маркирования целесообразно использовать инструменты с литыми знаками [13].
Мелкое маркирование деталей может выполняться с помощью ручного инструмента переносных приборов настольных и стационарных установок.
2 Выбор оборудования для электрохимического маркирования
В качестве оборудования для маркирования номера на данном корпусе наиболее оптимально подходит универсальный прибор УПЭК – 901 [13]. Это переносной прибор предназначен для маркирования плоских и круглых деталей (по трафарету и печатными знаками) для маркирования деталей (рисунок 3.1).
Рисунок 3.1 - Универсальный переносной аппарат для мелкого маркирования УПЭК- 901
Технические характеристики УПЭК- 901:
- напряжение питания 220 (В);
- рабочее напряжение от 2 до 16 В);
- время маркирования:
при автоматической выдержке 2-25 (с);
при ручной выдержке не ограничено;
- размеры шрифта свыше 1 (мм);
- глубина знака до 002 (мм);
- мощность 150 (Вт);
- габаритные размеры 300
Переносные приборы выполняют обычно в виде чемодана с отделениями для хранения инструмента электролитов.
Универсальный прибор УПЭК - 901 позволяет маркировать плоские и слабо изогнутые поверхности на рабочем столе прибора (масса деталей до 10 кг) и выносной головкой с длиной шнура 2 (м.).
УПЭК- 901 состоит из следующих частей (рисунок 6.1):
- поролоновые подушки;
- клавиши задания режима;
- стол для маркирования мелких деталей.
На столе прибора имеется устройство для накатывания для нанесения информации на круглые детали диаметром до 25 мм. Все вспомогательные устройства закреплены на съёмной крышке прибора. Там находятся выносная головка с ручным штемпелем и шнуром провод для подключения прибора к сети съёмная часть электрохимического накатника устройство для дозирования электролита включающее мерные технические шприцы с иглами концы которых введены в поролоновые подушки расположенные в прозрачных коробках. На каждой коробке указана марка маркируемого материала. Приборы оснащены тремя шприцами в которых находятся электролиты для маркирования сталей цветных и титановых сплавов. Объём шприца 10 (мл.) объём каждой подушки 12 (см3) разовая подача электролита 15 - 2 (мл.). После нажатия на поршень шприца часть электролита поступает в подушку которая используется в дальнейшем взамен тампона. Количество электролита должно быть таким чтобы обеспечить смачивание поверхности без накопления электролита в виде капель что существенно снижает чёткость знака.
Выносная головка (рисунок 3.2) выполнена в виде ручки 4 из капролона цанги 2 со штемпелем 1 закрепленным шаровым шарниром 3 на ручке. Головка соединена прибором шнуром 6 с быстроразъемным штекерным устройством 7; её масса не более 80 (г.). Маркирование происходит объемными знаками.
Рисунок 3.2 – Выносная головка УПЭК - 901
Точная фиксация головки относительно маркируемой поверхности происходит за счёт шарнирного крепления рабочей части относительно ручки. Допускаемый перекос до 8°. Величина прижима головки к детали ограничена подпружиненным упором который при силе 500 (Н) воздействует на микровыключатель 5 и включает технологический ток. Время действия тока задаётся с помощью реле и определяется автоматом либо периодом нажатия на упор.
Электрическая схема прибора включает блок питания обеспечивающий подачу стабилизированного напряжения с погрешностью не более 01 (В). Напряжение изменяют дискретно через 1 (В) от 2 до 5 (В) и через 2 (В) до 16 (В) клавишным переключателем на лицевой стороне прибора. От этого блока получает питание реле времени и блок управления позволяющий выдать команды на автоматическую или ручную выдержку времени обработки.
Производительность прибора — до 800 плоских и до 200 цилиндрических деталей в час. Прибор позволяет получать качественное изображение на деталях при общей площади наносимой информации до 50 (мм2).
3 Влияние электрохимического маркирования на эксплуатационные характеристики детали
При маркировании детали из сплава АК7 внутреннее напряжение на поверхности достигает ±40-60 (МГЦ). Рассмотрение контура клеймения показывает что после механического маркирования имеет место упорядоченная направленность волокон по контуру клеймения которая свойственна технологическим процессам связанным с пластическим деформированием металлов.
После электрохимического маркирования не обнаружено каких - либо дефектов снижающих прочность материала что указывает на возможность исключения концентраторов напряжений характерных для механического маркирования.
На основе экспериментальных данных получены эффективные коэффициенты концентрации напряжений позволяющие рассчитать механические характеристики различных материалов [13].
- после механического маркирования - 157;
- после электрохимического маркирования - 137.
Следовательно электрохимическое маркирование в меньшей степени влияет на местную концентрацию напряжений и является предпочтительным по сравнению с механическим способом нанесения информации.
Экономическая и организационно-управленческая часть
1 Экономическое обоснование проекта участка
1.1 Определение потребности в инвестициях для организации
спроектированного участка
Создание предметно-замкнутого участка требует определенных затрат: во-первых на технологическую подготовку производства а во-вторых на закупку установку и наладку технологического энергетического подъемно-транспортного контрольно-измерительного оборудования а также технологической оснастки инвентаря и хозяйственных принадлежностей. Затраты на здание не учитываются так как предполагается что спроектированный участок разместится на имеющихся площадях предприятия [11]. В таблице 5.1 указана стоимость металлорежущих станков используемых на участке.
Таблица 5.1 - Стоимость металлорежущих станков используемых на участке
Наименование оборудования (станок)
Мощность электро-двигателя
Единицы оборудо-вания
Капиталовложения в оборудование Ко р. рассчитываются по формуле:
где Кот – капиталовложения в технологическое оборудование тыс. р;
Коэ – капиталовложения в энергетическое оборудование тыс. р;
Кпт – капиталовложения в подъемно-транспортное оборудование тыс. р;
Коу – капиталовложения в средства контроля и управления тыс. р.
Вложения в технологическое оборудование определяются по формуле:
kтз – коэффициент транспортно-заготовительных расходов kтз = 005;
kс – коэффициент учитывающий затраты на строительные работы в том чис-
ле устройство фундаментов kс = 007;
kм – коэффициент учитывающий затраты на монтаж и наладку оборудования kм = 01.
Капиталовложения в технологическое оборудование по формуле (5.2):
Укрупнено капиталовложения в энергетическое оборудование принимаем равным 5% от стоимости технологического оборудования.
Укрупнено капиталовложения в подъемно-транспортное оборудование составляют 10% от стоимости технологического оборудования.
Капиталовложения в средства контроля и управления технологическим процессом принимаются равными 1% от стоимости технологического оборудования.
Определяем величину капиталовложений в оборудование:
Затраты на оснастку укрупнено принимаем 7% от стоимости технологического оборудования:
Вложения в инвентарь и хозяйственные принадлежности долговременного пользования примем в размере 3 % от стоимости технологического оборудования.
Результаты расчета капитальных вложений в основные производственные фонды участка представлены в таблице 5.2.
Таблица 5.2 – Результаты расчета капитальных вложений в основные производственные фонды участка
Виды основных фондов
Количество ед. оборудования
Балансовая стоимость
ед. оборудования тыс.р.
Балансовая стоимость основных фондов тыс.р.
Годовая сумма амортизационных отчислений
Технологическое обору-дование всего в том числе:
Продолжение таблицы 5.2
Энергетиче-ское оборудо-вание
Подъемно-транспортное оборудование
Средства контроля и управления
Технологическая оснастка
Инвентарь и хозяйствен-ные принад-лежности
1.2 Организация оплаты труда на участке
На участке применяется сдельно-премиальная и повременно-премиальная оплата труда. У основных рабочих форма оплаты труда сдельная у вспомогательных рабочих - тарифная ставка.
Тарифный фонд сдельщиков определяется как сумма расценок по операциям каждой детали умноженная на годовую программу:
где Ризj - расценка на изделие j-го вида р.
при отсутствии конкретных данных можно принять i =1.
где cmчi - часовая тарифная ставка соответствующая разряду по i-й операции р.ч.
Часовые тарифные ставки:
-го разряда: 4300 22 8 = 2443 (р.ч.);
-го разряда: 2443 х 15 = 3664 (р.ч.);
-го разряда: 24.43 х 17 = 4153 (р.ч.);
-го разряда: 2443 х 2 = 4886 (р.ч.);
-го разряда: 2443 х 22 = 5374 (р.ч.);
-го разряда 2443 х 25 = 6107 (р.ч).
Результаты расчета расценок на изготовление корпуса 456.852.32 представлены в таблице 5.3
Таблица 5.3 – Результаты расчета расценок на изготовление корпуса 456.852.32
0 – Вертикально-фрезерная
5 – Вертикально-сверлильная
0 – Горизонтально-расточная
Тарифный фонд сдельщиков:
Тарифный фонд заработной платы рабочих повременщиков (вспомогательных рабочих) определяется по формуле:
где - численность рабочих-повременщиков
- часовая тарифная ставка 1-го разряда;
- тарифный коэффициент рабочих повременщиков определяется по формуле:
- тарифный коэффициент рабочих-повременщиков i-го разряда принимается по справочной литературе [11].
Тарифный фонд заработной платы рабочих-повременщиков:
Таблица 5.4 - Штатное расписание аппарата управления участком
на участке (факт.) чел.
Доплаты (премии) следует принимать размере 30-40% от тарифного фонда.
Дополнительная заработная плата – это выплаты предусмотренные законодательством о труде или коллективным договором за неотработанное на производстве время (например оплата очередных и дополнительных отпусков). Процентное соотношение между основной и дополнительной заработной платой укрупнено можно принять в размере 10-20% от основной зарплаты.
Фонд заработной платы ИТР рассчитывается исходя из штатного расписания определенного в параграфе 1.5 и должностных окладов и премий. Расчет фонда заработной платы различных категорий работников участка предприятия представлен в таблице 5.5.
Таблица 5.5 - Фонд заработной платы работников участка
заработной платы тыс. р.
вспомогательные рабочие
1.3 Расчет себестоимости продукции
В данном разделе определим себестоимость корпуса 456.852.32 изготавливаемого по спроектированной технологии а также рассчитаем общие годовые затраты на производство продукции на спроектированном участке.
Расчет себестоимости детали изготавливаемой по спроектированной технологии представлен в таблице 5.7.
Таблица 5.7 - Калькуляция себестоимости детали
Основные материалы (стоимость заготовки)
где НР – норма расхода материала
на изделие НР = 17 кг;
ЦМ – оптовая цена материала
где Но – норма отходов на
деталь кгНо = 04 кг;
Цо – цена отходов ркг Цо = 20 р.кг.
Основная заработная плата основ-ных произ-водственных рабочих
ная заработная плата основных производственных рабочих
где Кдоп - процент дополнительной зарплаты
Начисления на социальные нужды
Ксоц. - процент начисления на соцнужды
Продолжение таблицы 5.7.
Износ специальных инструментов и приспособлений
где Рсп - расходы на специальную оснастку и инструмент тыс. р. принимаются по таблице 5.2; машинное время (принимается в размере 85% от tшт) мин.
где Крсэо - процент расходов на содержание
и эксплуатацию оборудования;
где - расходы на содержание и эксплуатацию оборудования участка на год (строка «итого» из табл. 5.6)
где Кц процент цеховых расходов
цеховая себестоимость детали
где Крх = 140% – коэффициент общехозяйственных расходов
производственная себестоимость детали
полная себестоимость детали
Годовые текущие издержки Иг р. определяются по формуле [15]:
где Nг – годовая программа выпуска изделий шт.
1.4 Расчет текущих затрат
Смета расходов на содержание и эксплуатацию оборудования включает следующие статьи: амортизация оборудования эксплуатация оборудования текущий ремонт оборудования содержание и эксплуатация транспорта износ малоценных и быстроизнашивающихся инструментов и приспособлений прочие расходы.
Расходы на амортизацию оборудования Ра = 460034 тыс. р.
Расходы на эксплуатацию оборудования включают затраты на вспомогательные материалы потребляемые в процессе эксплуатации оборудования; затраты на силовую энергию для приведения в движение производственных машин и механизмов; затраты на сжатый воздух для эксплуатации оборудования; затраты на воду для производственных нужд; основную и дополнительную заработную плату вспомогательных рабочих обслуживающих оборудование на участке с начислениями на социальные нужды.
Затраты на вспомогательные материалы потребляемые в процессе эксплуатации оборудования принимаются равными 5 % от стоимости технологического оборудования.
Затраты на силовую энергию потребляемую для приведения в движение производственных машин и механизмов определяются по формуле:
где Мэ – суммарная мощность электродвигателей оборудования кВт;
kв – коэффициент загрузки оборудования по времени kв = 06;
kм–коэффициент загрузки электродвигателей по мощности kм=05;
kпс – коэффициент учитывающий потери электроэнергии в сети kпс = 104;
Цэ – цена электроэнергии р.(кВт·ч) Цэ=19 р.(кВт·ч);
– средний КПД электродвигателей оборудования = 065.
Затраты на сжатый воздух для эксплуатации оборудования определяемые
как произведение годового расхода сжатого воздуха (из расчета 5м3 на один станок
в смену) на стоимость 1м3 сжатого воздуха.
где Ссв – объем сжатого воздуха приходящийся на один станок в смену м3;
Др – число рабочих дней в году;
Nст – число станков шт.;
Цсв – цена сжатого воздуха р.м3.
Затраты на воду для производственных нужд (принять средний расход на
один металлорежущий станок 06 литра в час) определяются по формуле:
где Св – средний расход воды на один станок м3ч;
Затраты на основную и дополнительную заработную плату вспомогательных рабочих обслуживающих оборудование с начислениями на соцнужды принять укрупнено в размере 30% от основной и дополнительной зарплаты и начислений на соцнужды от всех вспомогательных рабочих.
где – коэффициент начислений на социальные нужды;
– годовой фонд заработной платы вспомогательных рабочих.
Расходы на текущий ремонт оборудования транспортных средств и дорогостоящего инструмента составляют 15% от балансовой стоимости указанных средств.
Расходы на содержание и эксплуатацию транспорта принимают в размере 5% от стоимости транспортных средств.
Расходы на износ малоценных инструментов и приспособлений определяется укрупненно из расчета 50 тыс.р. на один станок в год.
Прочие расходы составляют 3% от общей суммы затрат по перечисленным выше статьям.
Смета расходов на содержание и эксплуатацию оборудования представлена в таблице 5.6.
Таблица 5.6 – Смета расходов на содержание и эксплуатацию оборудования
Амортизация оборудования
Эксплуатация оборудования:
- затраты на вспомогательные материалы;
- затраты на силовую энергию;
- затраты на сжатый воздух;
- затраты на основную и дополнительную заработную плату вспомогательных рабочих обслуживающих оборудование с начислениями на соц. нужды
Расходы на текущий ремонт оборудования
Расходы по содержанию и эксплуатации транспорта
Расходы на износ малоценных и быстроизнашиваемых инструментов и приспособлений
2 Расчет показателей экономической эффективности проекта участка
Экономический эффект от функционирования участка на котором детали изготавливаются по вновь спроектированной технологии рассчитывается на конкретный период. Исходя из темпов обновления промышленной продукции в состав которой входит изготавливаемая деталь принимаем этот период равным десяти годам.
Экономический эффект реализации проекта участка за расчетный период может быть определен по формуле [15]:
где РГ – неизменная по годам расчетного периода стоимостная оценка результатов производства продукции с использованием разработанного технологического процесса р.;
ЗГ – неизменные по годам расчетного периода затраты на продукцию с применением разработанного технологического процесса р.;
– норма реновации исчисленная для периода использования спроектированной технологии =00468 (период использования технологии – 12 лет);
Ен – норматив приведения разновременных результатов и затрат численно равный нормативу эффективности капитальных вложений Ен=01.
Величина Рг определяется по формуле [15]:
n – число наименований деталей изготавливаемых на спроектированном участке по разработанным технологиям.
где Кнр – коэффициент рентабельности к себестоимости продукции Кнр = 15.
Величина Зг определяется по формуле [15]:
где И – текущие издержки производства без учета амортизации основных производственных фондов используемых при изготовлении продукции И = 1725036 тыс. р.;
Лi – остаточная стоимость основных фондов на момент окончания применения разработанной технологии р.
Остаточная стоимость основных фондов на момент окончания использования разработанной технологии определяется по формуле [15]:
– норма реновации соответствующая сроку службы основных фондов
примем = 00315 что соответствует сроку службы в 15 лет.
– норма реновации соответствующая (tсл – ) = (15-12) = 3 =03021.
Внутренняя норма доходности проекта определяется по формуле [15]:
где К – единовременные затраты на создание участка.
Срок окупаемости капитальных вложений в проект определяется по формуле:
Таким образом а срок окупаемости капитальных вложений – Ток = 357 года – меньше срока использования разработанной технологии (12 лет) на спроектированном участке следовательно можно сделать вывод о том что разработанные в дипломном проекте инженерные решения являются экономически эффективными.
К показателям эффективности проекта также относятся снижение себестоимости изготовления детали экономия металла снижение трудоемкости изготовления детали условное высвобождение численности рабочих.
Снижение себестоимости изготовления детали определяется по формуле [15]:
где Сцб – цеховая себестоимость детали по базовому технологическому процессу р. (по данным предприятия);
Сцн – цеховая себестоимость детали по проектируемому технологическому процессу р.
Снижение трудоемкости изготовления детали определяется по формуле [15]:
где t1 – трудоемкость изготовления единицы продукции по базовому техпроцессу мин;
t2 – трудоемкость изготовления единицы продукции по спроектированному техпроцессу мин.
Условное высвобождение численности рабочих определяется по формуле:
принимаем: 1 человека.
Рассчитанные показатели экономической эффективности проекта представлены в таблице 5.9.
Таблица 5.9 – Показатели экономической эффективности проекта
Наименование показателей
Интегральный экономический эффект тыс. р.
Внутренняя норма доходности
Срок окупаемости капитальных вложений лет
Снижение себестоимости изготовления детали %
Снижение трудоемкости изготовления детали %
Условное высвобождение численности рабочих чел.
3 Организационный вопрос
Типовая система предусматривает обязательную подготовку к проведению ремонтных работ и формы организации ремонта оборудования. Своевременное проведение всех подготовительных работ значительно сокращает сроки ремонта улучшает качество и снижает стоимость ремонтных работ. Подготовка к ремонту включает техническую материальную и организационную подготовку.
Техническая подготовка предусматривает разработку конструкторской и технологической документации: альбом чертежей сменных деталей и узлов; паспорт оборудования; схему управления; инструкции по регулировке и уходу за оборудованием в процессе эксплуатации; технологические карты разборки и сборки агрегатов и механизмов; типовые технологические процессы изготовления и ремонта запасных деталей; типовую оснастку и приспособления для механизации трудоемких ремонтных работ. При подготовке технической документации необходимо большую ее часть получать централизованно от специализированных конструкторских организаций или заводов-изготовителей поставляющих уникальное и специальное оборудование.
Материальная подготовка ремонтных работ заключается в своевременном приобретении или изготовлении и запасных деталей и узлов снабжении инструментом и приспособлениями а также материалами и покупными комплектующими изделиями.
Наряду с технической и материальной подготовкой необходимо проводить организационные мероприятия по выводу оборудования в ремонт т.е. согласование сроков ремонта с выполнением календарного плана производства на данном участке. Это обеспечивается созданием заделов подменными станками сменностью работы. В процессе организационной подготовки комплектуются ремонтные бригады организуются и оснащаются рабочие места определяются методы выполнения работ формы стимулирования труда и другие мероприятия обеспечивающие выполнение ремонта в установленные сроки.
Типовая система предусматривает создание специализированных бригад по капитальному ремонту механической части оборудования и комплексных бригад по ремонту и техническому обслуживанию оборудования с ЧПУ. Формы оплаты труда ремонтников определяются конкретными условиями на данном предприятии. Так для слесарей комплексных бригад может применяться нормативно-сдельная бригадная оплата; для слесарей специализированных бригад РМЦ по капитальному ремонту и слесарей ЦРБ по текущему ремонту и техническому обслуживанию целесообразна сдельно-премиальная индивидуальная система оплаты труда. На аварийных работах а также капитальном ремонте автоматических линий и оборудования лимитирующего ход производства наиболее эффективной может быть аккордная оплата. Труд станочников РМЦ оплачивается как правило сдельно; в ЦРБ при незначительной загрузке (менее 2 тыс. ремонтных единиц) используется повременно-премиальная индивидуальная оплата станочников. Показателями премирования как для слесарей так и для станочников являются выполнение месячного плана сокращение простоя в ремонте состояние оборудования.
Оперативная подготовка и организация выполнения всех ремонтных работ осуществляется на основе ведомости дефектов оборудования. Она составляется в процессе планового осмотра за два-три месяца до очередного планового ремонта и окончательно уточняется при разборке агрегата для капитального или среднего ремонта. В ведомости дефектов фиксируются фактическое состояние оборудования перечень характер и объем предстоящих ремонтных работ что обеспечивает своевременную подготовку сменных деталей и узлов необходимой оснастки. Ведомость дефектов используется также для проверки качества последнего ремонта и определения объема предстоящего ремонта.
Технологическая последовательность основных этапов выполнения плановых ремонтов такова: 1) подготовка к ремонту; 2) проверка точности (до разборки); 3) разборка станка на узлы; 4) разборка узлов на детали; 5) промывка деталей; 6) уточнение ведомости дефектов и принятие технологических решений для восстановления или ремонта основных деталей; 7) замена пригонка деталей сборка и регулировка узлов; 8) общая сборка; 9) регулировка станка; 10) испытание станка; 11) окраска станка; 12) сдача техническому контролю.
Формы организации ремонтных работ определяются в основном размерами предприятий и особенностями оборудования..
На средних заводах имеющих более 5 тыс. условных ремонтных единиц оборудования преобладает сменная форма организации ремонта. В данном случае все капитальные ремонты и наиболее сложные ремонтные работы выполняет ремонтно-механический цех а вес остальные ремонтные работы (около 50%) и техническое обслуживание - цеховые ремонтные базы.
На небольших заводах с количеством оборудования до 5 тыс. ремонтных единиц применяется централизованная форма ремонта при которой все виды ремонтных работ выполняются ремонтно-механическим цехом. Дежурные ремонтники прикрепленные к основным производственным цехам осуществляют только техническое обслуживание оборудования.
Оборудование с ЧПУ на всех заводах ремонтируется централизованно специальной лабораторией РМЦ или выездными бригадами специальных ремонтных предприятий (по договорам).
Во всех случаях планирование техническое руководство и контроль выполнения ремонтных работ осуществляются централизованно отделом главного механика предприятия.
Экологичность и безопасность
В процессе трудовой деятельности на человека могут воздействовать опасные производственные факторы которые приводят к травме или другому внезапному резкому ухудшению здоровья. К ним относятся: движущиеся машины и механизмы различные подъемно-транспортные устройства и перемещаемые грузы; незащищенные подвижные элементы производственного оборудования (приводные и передаточные механизмы режущие инструменты вращающиеся и перемещающиеся приспособления и др.) отлетающие частицы обрабатываемого материала и инструмента электрический ток повышенная температура поверхностей оборудования и обрабатываемых материалов и т.д. А также вредные производственные факторы которые приводят к заболеванию или снижению трудоспособности. Таковыми факторами являются: повышенная и пониженная температура воздуха рабочей зоны; высокие влажность и скорость движения воздуха; повышенные уровни шума вибрации. Также к вредным физическим факторам относятся запыленность и загазованность воздуха рабочей зоны; недостаточная освещенность рабочего места а также проходов и проездов; повышенная яркость света и пульсация светового потока.
Между вредными и опасными производственными факторами наблюдается определенная взаимосвязь. Во многих случаях наличие вредных факторов способствует проявлению травмоопасных факторов. Так чрезмерная влажность в производственном помещении и наличие токопроводящей пыли (вредные факторы) повышают опасность поражения человека электрическим током (опасный фактор).
Уровни воздействия на работающих вредных производственных факторов нормированы предельно-допустимыми уровнями значения которых указаны в соответствующих стандартах системы стандартов безопасности труда и санитарно-гигиенических правилах.
1 Техника безопасности
Оборудование устанавливается по операциям технологического процесса: фрезерный станок сверлильный станок токарный станок. После выполнения операции на одном станке заготовку перемещают на другой станок согласно технологического процесса. При перемещении груза необходима соблюдать правила техники безопасности. Минимальная ширина проходов для людей передвигающихся с грузом должен предусматриваться не менее 2 м без груза – не менее 1 м. Расстояния между станками и элементами здания а также ширина проходов выбраны согласно норм техники безопасности.
При работе на различного вида оборудования при выполнении разработанного технологического процесса необходимо соблюдать следующие требования техники безопасности:
Все открытые и вращающиеся части станков фрезерного FSS350R и сверлильного 2Н118 должны быть закрыты глухими кожухами плотно прикрепленными к станку. Основные требования к кожухам: прочность отсутствие шумообразования и простота конструкции.
Станки FSS350R и 2Н118 должны быть снабжены специальными устройствами полностью защищающими работающего от стружки искр осколков поломанного инструмента и брызг СОЖ. Для защиты от стружки кроме защитного экранов и щитков применяются очки. Большую роль играют современные методы борьбы со стружкой - поломкой ее и удалением из зоны резания.
На фрезерном станке FSS350R большую опасность представляет сама фреза. Эта опасность значительно уменьшается при наличии специального ограждения. Ограждение изготовляется в виде сварных или литых кожухов из стали или ковкого чугуна.
Для защиты станочников от поражения током все электрооборудование станков выполнено в защищенном исполнении. Для превращения замыкания фазы на корпус в однофазовое короткое замыкание оборудование занулено (на участке применяется четырехпроводная трехфазная сеть с заземленной нейтралью). В совокупности с использованием автоматов защиты от токов короткого замыкания это обеспечивает быстрое срабатывание последних.
На всех дверцах электрошкафов применяются предупредительные знаки в соответствии с требованиями ГОСТ 15508 – 70.
Работы по ремонту оборудования и механизмов производят только после полного отключения от сети электропитания с обязательным вывешиванием в местах отключения предупредительных табличек.
Перед каждым станком должен находиться деревянный настил который не позволяет переохлаждаться организму человека препятствует проникновению стружки в обувь и частично изолирует работающего.
Конструкция и расположение органов управления станком должна исключать возможность непроизвольного включения и выключения оборудования.
Конструкция пневматического приспособления должна обеспечивать предотвращение разжима и падания обрабатываемых деталей (самотормозящие элементы обратные клапана и т. д.).
Металлорежущий инструмент должен иметь определенную геометрию а также должны быть канавки предназначенные для скола стружки.
2 Производственная санитария и гигиена труда
Существенное влияние на здоровье людей оказывает микроклимат в производственном помещении предусматриваемый ГОСТ 12.1.005-76 категория тяжести труда. Для создания благоприятных условий труда следует постоянно контролировать микроклимат производственных помещений замеряя показатели температуры влажности и скорости движения воздуха.
Для холодного времени года оптимальные параметры:
-температура воздуха 18 20°С;
-относительная влажность 40 60%;
-скорость движения воздуха на рабочем месте 02мс.
Допустимые параметры соответственно:
-температура воздуха 17 23°С;
-относительная влажность не более 75%;
-скорость движения воздуха на рабочем месте 0Змс.
В теплый период года оптимальные параметры:
-температура воздуха 21 23°С;
- температура воздуха 18 27°С;
- относительная влажность не более 75%;
- скорость движения воздуха на рабочем месте 02 04 мс.
В соответствии с требованиями СНИП 11-38-75 двери и технические проемы механических цехов оборудованы воздушными завесами. С целью более эффективного улавливания пыли мелкой стружки применяется местное вытяжное устройство типа зонтов.
Для разбавления вредных веществ до их ПДК используется общеобменная вытяжная вентиляция.
Поддержание параметров микроклимата в заданных приделах обеспечивается главным образом за счет общеобменной приточно-вытяжной вентиляции а также естественной вентиляции осуществляемой аэрацией.
Свет на разработанном участке играет большую роль в сохранении здоровья и работоспособности человека. Для создания нормальных условий труда источники света в производственных помещениях должны достаточно и равномерно освещать рабочие места; не вызывать слепящего действия блесткости и излишней яркости в поле зрения работающего; не вызывать резких теней. Важное гигиеническое значение имеет рациональный выбор источников света. На участке должно предусматриваться естественное и искусственное освещение.
Для снижения шума и вибрации на участке по изготовлению корпусов 456.852.32 предусматриваются следующие требования:
-снижение вибрации в источнике возникновения;
-рациональная планировка наиболее шумное оборудование располагается в специальном месте;
-использование звукоизолирующих экранов и кожухов;
-использование индивидуальных средств защиты. К ним отнесены следующие устройства: оградительные виброизолирующие виброгасящие и вибропоглощающие (см. ГОСТ 12.4.011-75) а также средства автоматического контроля сигнализации дистанционного управления.
Важное значение имеет разработка и внедрение физиологически обоснованных режимов труда и отдыха лиц подвергающихся воздействию вибрации а также обеспечение их средствами индивидуальной защиты.
Для защиты рабочего от воздействия общей вибрации применяют обувь с амортизирующими подошвами.
Для борьбы с шумом на пути его распространения на участке устанавливают звукоизолирующие и звукопоглощающие конструкции а также глушители аэродинамических шумов.
3 Противопожарные мероприятия и средства пожаротушения
Причиной пожара могут стать искры возникающие при фрезеровании на FSS350R и обточке на 262ОГФ1 алюминиевого сплава твердыми сплавами на высоких скоростях а также промасленная ветошь в контейнерах пробой электропроводки и обмоток электродвигателей.
Для обеспечения безопасности работы на участке необходимо соблюдать следующие меры предупреждения пожаров:
Содержание в чистоте рабочих мест своевременно очищать от мусора и ветоши которые складываются в специальных металлических контейнерах закрывающихся крышкой.
Цех оснащен двумя эвакуационными выходами ширина путей эвакуации должна быть не менее 1 м а ширина дверей в путях – не менее 08 м высота прохода - не менее 2м.
Удаление дыма при пожаре предусматривается через аэрационные фонари.
В воздухе вентиляционной системы устанавливается огнепреградительные и быстродействующие заслонки.
Использование дымового пожарного извещателя ДИП – 1 действие которого основано на фотоэлектрическом принципе.
Для тушения пожара также использовать ручные углекислотные огнетушители ОУ – 5.
На участке расположены два пожарных гидранта.
Соответствующими приказами устанавливается порядок регулярного проведения с рабочими противопожарного инструктажа.
Успешное тушение пожара в значительной степени зависит от правильно организованной и надежно действующей связи и сигнализации.
4 Охрана окружающей среды
При обработке металлов резанием основную вредность для окружающей среды представляют: отработанная СОЖ и промывочная вода; твердые отходы - стружка; загрязненный в результате отделочных операций механической обработки воздух.
Во избежание загрязнения окружающей среды на участке предусмотрены следующие мероприятия:
Для улавливания крупных фракций частиц пыли применяют установки типа «циклоны». Механическая обработка на металлорежущих станках сопровождается выделением пыли стружки туманов масел и эмульсий которые через систему вентиляции выбрасываются из помещения в окружающую среду.
Для возможности повторного использования отработанной СОЖ и промывочной воды в условиях серийного производства предусмотрены отдельные замкнутые системы водоснабжения. Для разложения отработанной СОЖ используется метод электрокоагуляции. На основе полученной повторно воды изготавливают новую СОЖ а оставшуюся масляную составляющую сжигают в печах чугунолитейного производства. В целях экономии на заводе предусмотрена одна централизованная станция для разложения СОЖ.
Для очищения промывочной воды на участке предусмотрены отстойники и флотационные установки включенные в замкнутую цеховую оборотную систему.
Для недопущения загрязнения окружающей среды твердыми отходами (стружкой) предусматриваются следующие мероприятия:
-сбор стружки по территории цеха с последующим ее прессованием;
-последующая ее переработка.
Для переработки стружки предусматривается специальный участок что позволяет сократить затраты на погрузочно-разгрузочные работы снижает безвозвратные потери при их переплавке и транспортировке и высвобождает транспортные средства.
Стружку которая образуется при обработке деталей корпус 456.852.32 собирают и перерабатывают на стружко-дробилках брикетировочных прессах.
Регулярный плановый ремонт станков на участке исключает не предусмотренное конструкцией трение а регулярная чистка смазка замена выработавших свой срок узлов снизит количество твердых отходов в целом.
В выпускной квалификационной работе был усовершенствован типовой технологический процесс изготовления корпуса 456.852.32.
Исходя из разработанного технологического процесса и объёма выпуска продукции был спроектирован участок по изготовлению корпусов 456.852.32. Оборудование участка позволяет вести серийный выпуск деталей. Для обеспечения полной загрузки оборудования на данных станках будет производиться выпуск подобных деталей – других корпусов.
Был проведён анализ базового технологического процесса производства детали и выявлена возможность повышения качества и экономической эффективности производства.
Спроектирована операционная технология производства детали и конструкция приспособления. При этом были задействованы прогрессивные средства разработки технологического процесса обработки детали в САПР.
Был спроектирован участок механического цеха рассчитано количество необходимого оборудования определен тип производства состав основных и вспомогательных рабочих. Было выявлено сокращение количества операций количества оборудования вследствие чего уменьшились затраты на оборудование электроэнергию амортизацию а также снижение себестоимости детали.
Определена плановая себестоимость изделий составлена смета производственных расходов.
Определены технико-экономические показатели проектируемого предметно-замкнутого участка.
Справочник технолога-машиностроителя. В 2-х т. Под ред. А. Г. Косиловой и Р.К. Мещерякова. – 4-е изд. переработ. и доп. Т.1 – М.: Машиностроение 1986. – 656 с. ил.
Станочные приспособления: Справочник. В 2-х т. Под ред. Б.Н. Вардашкина А.А. Шатилова. Т.1. – М.: Машиностроение 1984. – 592 с.
Станочные приспособления: Справочник. В 2-х т. Под ред. Б.Н. Вардашкина В.В. Данилевского. Т.2. – М.: Машиностроение 1984. – 656 с.
Маталин А.А. Технология машиностроения. – Л.: Машиностроение 1985.
Справочник технолога-машиностроителя. В 2-х т. Под ред. А. Г. Косиловой и Р.К. Мещерякова. – 4-е изд. переработ. и доп. Т.2 – М.: Машиностроение 1986. – 496 с. ил.
Корсаков В.С. Основы конструирования приспособлений: Учебник для вузов. – 2-е изд. переработ. и доп. – М.: Машиностроение 1983. – 277 с. ил.
Анурьев В.И. Справочник конструктора – машиностроителя. В 3-х т. Под ред. И.Н. Жестоковой. – 8-е изд. переработ. и доп. Т.1 – М.: Машиностроение 2001. – 920 с. ил.
Руденко П.А. Проектирование и производство заготовок в машиностроении: Учеб. Пособие П.А. Руденко Ю.А. Харламов В.М. Плескач; Под общ. ред. В.М. Плескача. – К.: Высшая шк. 1991. – 247 с. ил.
Майникова Н.Ф. Проектирование встраиваемых механизмов подъема и передвижения талей: Учеб. Пособие Н.Ф. Майникова. – Тамбов: Изд-во Тамб. гос. техн. Ун-та 2007. – 36 с.
Методические указания по выполнению курсовой работы по курсу «Организация производства и менеджмент» для студентов специальности 151001 «Технология машиностроения» очно-заочной (вечерней) и заочной форм обучения Сост. А.В. Ростова. Воронеж 2005.- 32с.
Егоров М.Е. Основы проектирования машиностроительных заводов. 6-е изд. перераб. и доп. - М.: Высш. Школа 1969. – 479 с.
Справочник инструментальщика Под ред. И.А. Ординарцева. - М.: Машиностроение 1987.
Система СADCAMCAPP ADEM. Copyringht (C) 1897-2006 ADEM technologies ltd.
Методические указания по выполнению организационно-экономической части дипломных проектов для студентов специальности 151001 «технология машиностроения» всех форм обучения Сост. И.П. Кондратьева А.В. Ростова. Воронеж 2004.- 23 с.
Комплект операционных карт обработки детали корпус 456.852.32
Реферат.doc
КОРПУС ЧЕРВЯЧНОЙ ТАЛИ ТЕХНОЛОГИЯ ТЕХНОЛОГИЧЕСКОЕ ОСНАЩЕНИЕ РЕЖИМЫ ОБРАБОТКИ РАСЧЕТ ПРИСПОСОБЛЕНИЯ ЭКОНОМИЧЕСКАЯ ЭФФЕКТИВНОСТЬ ПЛАНИРОВКА УЧАСТКА.
Объект исследования или разработки – корпус 456.852.32.
Цель работы – совершенствование операционного технологического процесса изготовления корпуса 456.852.32; проектирование эффективной операционной технологии с использованием САПР; численное обоснование метода изготовления заготовки; формирование состава переходов и операций; расчёт станочного приспособления; расчёт контрольного приспособления; проектирование производственного участка; расчёт экономических показателей участка.
Полученные результаты и их новизна – в данном дипломном проекте были решены основные задачи поставленные для достижения повышения производительности труда в условиях крупносерийного производства. Используя основные направления в современной технологии машиностроения был выбран рациональный метод получения заготовки что дало возможность значительно снизить трудоемкость обработки детали на металлорежущих станках а также сократить расход металла. Применение станка с числовым программным управлением приспособления с быстродействующими зажимами позволило повысить производительность труда. Снижение трудоемкости перемещения детали между рабочими местами было учтено при разработке участка механической обработки что позволило достигнуть лучших технико-экономических показателей по сравнению с существующими на заводе.
Экономическая эффективность или значимость работы – экономический эффект от производства продукции с применением разработанного в дипломном проекте технологического процесса за расчётный период составит 2741634 тысяч рублей.
Список литературы.doc
Станочные приспособления: Справочник. В 2-х т. Под ред. Б.Н. Вардашкина А.А. Шатилова. Т.1. – М.: Машиностроение 1984. – 592 с.
Станочные приспособления: Справочник. В 2-х т. Под ред. Б.Н. Вардашкина В.В. Данилевского. Т.2. – М.: Машиностроение 1984. – 656 с.
Маталин А.А. Технология машиностроения. – Л.: Машиностроение 1985.
Справочник технолога-машиностроителя. В 2-х т. Под ред. А. Г. Косиловой и Р.К. Мещерякова. – 4-е изд. переработ. и доп. Т.2 – М.: Машиностроение 1986. – 496 с. ил.
Корсаков В.С. Основы конструирования приспособлений: Учебник для вузов. – 2-е изд. переработ. и доп. – М.: Машиностроение 1983. – 277 с. ил.
Анурьев В.И. Справочник конструктора – машиностроителя. В 3-х т. Под ред. И.Н. Жестоковой. – 8-е изд. переработ. и доп. Т.1 – М.: Машиностроение 2001. – 920 с. ил.
Руденко П.А. Проектирование и производство заготовок в машиностроении: Учеб. Пособие П.А. Руденко Ю.А. Харламов В.М. Плескач; Под общ. ред. В.М. Плескача. – К.: Высшая шк. 1991. – 247 с. ил.
Майникова Н.Ф. Проектирование встраиваемых механизмов подъема и передвижения талей: Учеб. Пособие Н.Ф. Майникова. – Тамбов: Изд-во Тамб. гос. техн. Ун-та 2007. – 36 с.
Методические указания по выполнению курсовой работы по курсу «Организация производства и менеджмент» для студентов специальности 151001 «Технология машиностроения» очно-заочной (вечерней) и заочной форм обучения Сост. А.В. Ростова. Воронеж 2005.- 32с.
Егоров М.Е. Основы проектирования машиностроительных заводов. 6-е изд. перераб. и доп. - М.: Высш. Школа 1969. – 479 с.
Справочник инструментальщика Под ред. И.А. Ординарцева. - М.: Машиностроение 1987.
Система СADCAMCAPP ADEM. Copyringht (C) 1897-2006 ADEM technologies ltd.
Методические указания по выполнению организационно-экономической части дипломных проектов для студентов специальности 151001 «технология машиностроения» всех форм обучения Сост. И.П. Кондратьева А.В. Ростова. Воронеж 2004.- 23 с.
1.doc
1 Конструктивно-технологический анализ узла составной частью которого является выбранная для проектирования деталь
Таль - грузоподъемное устройство с ручным электрическим или пневматическим приводом подвешиваемое к балкам или специальным тележкам перемещающимся по подвесному монорельсовому пути. Тали предназначены для подъема опускания и горизонтального перемещения груза подвешенного на крюковой подвеске. Отличительным признаком тали является компактность. Промышленностью выпускаются тали грузоподъемностью от 025 до 16 тонн с электроприводом и тали ручные грузоподъемностью: 1; 32; 5 и 8 тонн. Высота и скорость подъема груза талей соответственно не более 30 м и 005 015 м.
Данный узел может эксплуатироваться как в закрытом помещении так и на открытом воздухе. Особенности этого механизма:
- кованные подвесной и грузовой крюки из нержавеющей высоколегированной стали;
- повышенный запас прочности;
- высокая стойкость к механическим повреждениям.
Ручные тали (с ручным приводом) производят подъем груза с помощью грузовых пластинчатых или сварных комбинированных цепей приводимых в движение вручную с помощью звездочек. Часто грузовая цепь образует полиспаст кратностью 2; 3 и реже 4 [10]. Различают червячные и шестеренные ручные тали.
На рисунке 1.1 представлен механизм подъема ручной червячной тали. Подъемный механизм включает в себя тяговую звездочку 1 закрепленную на быстроходном валу 2 червячного редуктора. Подъем груза осуществляется с помощью сварной тяговой цепи (на рисунке 1.1 не показана). Барабаны 4 размещены с двух сторон тихоходного вала 3. Обычно в этом случае используется сдвоенный полиспаст (разрез А–А рисунок 1.1) уравнительный блок 5 которого закрепляется на корпусе 6 редуктора с помощью кронштейна 7 винтами 8.
Конструкция барабанов 4 – литая с нарезкой. Нарезка канавок на барабанах под канат выполняется в разные стороны. Груз при этом поднимается строго вертикально. Блок 5 валы червяка и колеса установлены на подшипниках качения 9 и 10 закрытых крышками 11 и 18 с манжетами 12 (подшипники и крышки на валу червяка не показаны). Осевое смещение барабанов на валу исключается винтами 13 и торцевой шайбой 14. Передача движения с вала 3 на колесо и барабаны осуществляется с помощью шпонок 15. Смещение колеса 4 вдоль оси вала исключается втулкой 16. Корпус 6 редуктора литой неразъемный. Размер крышки 17 позволяет вынимать (вправо) червячное колесо в сборе с тихоходным валом после отвинчивания винтов 13 червячный вал при этом должен быть вынут через отверстия подшипниковых гнезд вала червяка (на чертеже не показаны). Подшипники уравнительного блока 5 устанавливаются на оси 19. Осевое перемещение оси 19 исключается ригелем 20 закрепленным винтами 21 к кронштейну 7 и головкой оси слева (разрез А–А рисунок 1.1).
Рисунок 1.1 – Механизм подъема червячной тали
2 Назначение и краткое техническое описание детали
Деталь представляет собой корпус грузовой тали. Название – корпус. Заготовка детали – литая. Вес детали – 13 кг. Габаритные размеры: длина – 1715 мм высота – 158 мм ширина – 90 мм. Код 456.852.32. Материал детали – алюминиевый сплав АК7ч ГОСТ 1583 – 93. Химический состав материала описан в таблице 1.1. Механические свойства материала описаны в таблице 1.2.
Таблица 1.1 – Химический состав сплава АК7ч ГОСТ 1583 – 93 %
Таблица 1.2 – Механические свойства АК7ч ГОСТ 1583 – 93
Предел прочности при растяжении МПа
Твердость по БриннелюНВ
Корпусные детали в большинстве случаев являются базовыми деталями на которые монтируют отдельные сборочные единицы и детали соединяемые между собой с требуемой точностью относительного положения. Корпусные детали должны обеспечить постоянство точности относительного положения деталей и механизмов как в статическом состоянии так и в процессе эксплуатации машин.
Корпус червячной тали (рисунок 1.2) представляет собой конструкцию из двух параллельных и одного перпендикулярного к ним цилиндров а также других унифицированных и стандартизированных конструктивных элементов. При этом деталь имеет оригинальные конструктивные элементы замена которых невозможна так как это отрицательно сказывается на работоспособности изделия в конструкцию которого входит данная деталь.
Рисунок 1.2 – Корпус червячной тали
Конструкция детали обеспечивает свободный доступ инструмента для обработки и контроля. Точность детали выражена полями допусков: IT 9 Н9 Н7. Разброс шероховатости от Ra 125 до Ra 125 мкм. К детали предъявляются технические требования по геометрической форме и взаимному расположению поверхностей (рисунок 1.2):
необходимо не допустить разностенность стенок между поверхностями 18 и 9 а также между поверхностями 17 и 12.
необходимо обеспечить симметричность детали относительно оси отверстия 12.
необходимо обеспечить параллельность поверхностей 1 и 2 поверхности 16.
не допустить несоосности поверхностей 19 и 9.
3 Оценка технологичности детали
Технологичность конструкции детали - это показатель характеризующий удобно ли с технической точки зрения достигать заданную конструктором форму детали обеспечить точность и качество обработки; возможна ли обработка заданной детали на стандартном оборудовании стандартным режущим инструментом доступен ли его подвод и нормальное условие обработки. Оценка бывает двух видов: качественная и количественная.
Качественная оценка производится субъективно т.е. самим технологом на основании опыта производства и заключается в выше перечисленных условиях.
Количественная оценка технологичности производится по некоторым числовым показателям:
- коэффициент унификации конструктивных элементов
где Qуэ и Qэ – соответственно число унифицированных конструктивных элементов и общее.
Унифицированные конструктивные элементы – это те которые образуются стандартным режущим инструментом.
- коэффициент использования металла
где Q и q – соответственно масса заготовки и масса детали.
Определим технологичность нашей детали. Для этого определим коэффициент унификации конструктивных элементов и коэффициент использования металла.
При Куэ=084 > 06 и Ким=076 > 08 деталь технологична [4].
Ко всем обрабатываемым поверхностям обеспечен удобный подход режущих инструментов. Отсутствуют поверхности с необоснованно высокой точностью обработки.
Проанализировав все вышеперечисленные факторы будем считать деталь технологичной.
4 Анализ базового технологического процесса
Заводской технологический процесс был разработан для единичного производства. При его изучении и тщательном анализе были выявлены его недостатки. Уровень автоматизации действующего технологического процесса низкий. Оснастка специальная разработанная непосредственно для действующего технологического процесса. При обработке по данному технологическому процессу деталь неоднократно переустанавливается. Заготовку изготавливается методом литья в песчано-глинистые формы. Это увеличивает число проходов так как шероховатость поверхности невелика.
При анализе основного и вспомогательного времени на обработку выявлено что затраты на вспомогательное время очень велики. Это объясняется тем что станки для обработки располагаются по группам. По действующему технологическому процессу применяется неавтоматизированные универсальные приспособления.
В процессе проектирования технологического процесса маршрут и трудоемкость обработки уменьшились. Сократилось количество операций и появилась возможность обрабатывать больше поверхностей за один установ детали. Это стало возможным в результате замены универсального оборудования на станки с ЧПУ.
5 Установление типа производства
В машиностроении различают три типа производства: единичное серийное и массовое. Серийное производство в свою очередь подразделяется на мелкосерийное среднесерийное и крупносерийное.
Важным этапом в разработке технологического процесса является определение типа производства. Основным критерием при определении типа производства является коэффициент закрепления операций за одним рабочим местом или единицей оборудования. Он определяется как отношение числа всех технологических операций выполняемых в течении месяца на механическом участке (О) к числу рабочих мест (Р) на этом механическом участке.
Типы машиностроительного производства характеризуются следующими значениями коэффициента закрепления операции:
Кзо≤1 – массовое производство.
Кзо≤10 – крупносерийное производство.
Кзо≤20 – среднесерийное производство.
Кзо≤40 – мелкосерийное производство.
Кзо – единичное производство.
На практике обычно известна годовая программа выпуска и тогда определение Кзо удобно по следующей формуле:
где ФД– годовой фонд работы оборудования (18924 часов);
Обаз – число операций механической обработки по базовому техпроцессу;
Тшт – трудоемкость изготовления детали мин (78184 минут);
Nгод – годовая программа выпуска(3010 штук).
Вывод: производство является крупносерийном.
Для серийного производства эффективна предметная форма организации производства на участке. В этом случае всё оборудование необходимое для обработки деталей устанавливается в технологической последовательности что обеспечивает прямоточность уменьшение производственного цикла по длительности а также снижение себестоимости продукции.
6 Выбор типа заготовки и предварительное назначение припусков
Метод выполнения заготовок для деталей машин определяется назначением и конструкцией деталей материалом техническими требованиями масштабом и серийностью выпуска а также экономичностью изготовления.
Выбрать заготовку значить установить способ ее получения наметить припуски на обработку каждой поверхности рассчитать размеры и указать допуски на неточность изготовления.
Для рационального выбора заготовки необходимо одновременно учитывать все вышеперечисленные исходные данные так как между ними существует тесная взаимосвязь.
Окончательное решение можно принять только после экономического комплексного расчёта себестоимости заготовки и механической обработки в целом.
Заготовку будем получать литьем. Отливку второго класса точности можно получить несколькими способами литья. Так как наружные поверхности детали не подвергаются механической обработке их следует получить при изготовлении заготовки. Проведем сравнительный экономический расчет себестоимости заготовки при литье под давлением и литье по выплавляемым моделям.
Себестоимость заготовки можно определить по формуле:
Q – масса заготовки кг;
Sотх – цена 1 т отходов руб.;
q – масса готовой детали кг;
kт kс kв kм kп – коэффициенты зависящие от класса точности группы сложности массы марки материала и объема производства заготовок.
Данные необходимые для расчета стоимости заготовок получаемых литьем по выплавляемым моделям представлены в таблице 1.3.
Таблица 1.3 - Данные для расчета
В соответствии с формулой 1.5 стоимость заготовок получаемых литьем по выплавляемым моделям будет составлять:
Данные необходимые для расчета стоимости заготовок полученных литьем под давлением представлены в таблице 1.4.
Таблица 1.4 - Данные для расчета
На основании проведенных расчетов следует что наиболее рациональным способом получения заготовки для корпуса 456.852.32 является литье под давлением так как оно обеспечивает меньшую технологическую себестоимость детали.
Литье под давлением применяется в основном для получения фасонных отливок из цинковых алюминиевых магниевых и латунных сплавов. Способ считается целесообразным при партии 1000 и более деталей. Производительность метода до 1000 деталей в час. Можно получить отливки массой до 100 кг. с минимальной толщиной стенок 05 мм.; точность 11 12-го квалитетов по СТ СЭВ 144-75 параметр шероховатости поверхности до Ra=063 мкм.[8].
На основании справочных данных для корпуса 456.852.32 значения припусков и допусков представлены в таблице 1.5.
Таблица 1.5 – Значения припусков и допусков
Номинальный размер детали мм
Число предварите-льных обтачиваний
Допуск на размеры отливки мм
Припуск на механи-ческую обработку (на сторону) мм
Коробление отливки мм
Суммарный припуск на размер мм
Номинальный размер отливки мм
Наружные поверхности
Внутренние поверхности
7 Выбор технологических баз и оценка точности базирования
Процесс базирования заготовки заключается в её ориентации и последующем жёстком закреплении в координатной системе станка или приспособления в требуемом положении необходимом для выполнения операции обработки или сборки.
Для повышения точности обработки детали необходимо учитывать принцип совмещения баз т.е. конструкторская технологическая и измерительная базы должны совпадать. Если базы выбраны правильно то требуемая точность изготовления детали будет обеспечена.
В зависимости от числа идеальных опорных точек с которыми база находится в контакте или в зависимости от числа отнимаемых степеней свободы различают установочную базу находящуюся в контакте с тремя опорными точками; направляющую базу находящуюся в контакте с двумя опорными точками; упорную базу имеющую контакт с одной опорной точкой.
Каждая из перечисленных баз определяет положение заготовки относительно одной из плоскостей системы координат в направлении перпендикулярном к этой базе т.е. в направлении одной из координатных осей. Очевидно что для полной ориентировки заготовки в приспособлении необходимо использовать комплект из всех трёх баз.
Также при выборе баз необходимо учитывать дополнительные условия: удобство установки и снятия заготовки надежность закрепления заготовки в выбранных местах приложения сил зажима возможность подвода режущих инструментов с разных сторон заготовки и др. Для установки заготовки на первой операции используют необработанные поверхности так называемые черновые базы.
Базовые поверхности по маршруту обработки корпуса 456.852.32 представлены в таблице 1.6.
Таблица 1.6 - Базирование по маршруту обработки
Верхняя и нижняя поверхности
Верхняя нижняя и внутренние поверхности
Продолжение таблицы 1.6
Верхняя поверхность и два отверстия
Расчет точности обработки производится с целью оценки величины возможного рассеивания заданного параметра. Вследствие погрешности выполнения базовой поверхности заготовок неточности изготовления износа опорных элементов приспособления нестабильности усилия закрепления положения заготовок в приспособлении будут разным. Погрешность установки заготовок в приспособлении Δу вычисляют с учетом погрешности базирования Δб погрешности закрепления заготовок Δз и погрешности изготовления и износа опорных элементов приспособления Δпр. Погрешность установки определяют как предельное поле рассеивания положений измерительной поверхности относительно поверхности отсчета в направлении выдерживаемого размера[6]. Так как указанные выше погрешности являются случайными величинами то
где Δб - погрешность базирования;
Δз - погрешность закрепления;
Δпр – погрешность приспособления.
Погрешность базирования по размеру:
Погрешность закрепления заготовки:
так как сила зажима действует перпендикулярно выдерживаемому размеру.
Погрешность установки по размеру:
Суммарная погрешность обработки:
где - поправочный коэффициент[2]
- погрешность технологической системы определяемая как средняя экономическая точность обработки.
Допустимая погрешность установки[2]:
где Т – допуск размера мм.
Следовательно и предлагаемая схема базирования приемлема.
Суммарная погрешность приспособления[2]:
При применении данного приспособления требуемый параметр будет выдержан.
8 Разработка маршрута операций технологического процесса обработки
Разработку технологического процесса начнем с загрузки в рабочее поле системы режима «Технология» из раздела «Базы данных».
Перед началом разработки нового технологического процесса очистим поле текущей технологии (рисунок 1.3) произведя двойной щелчок на пиктограмме «Очистка технологии». Во всех таблицах текущей технологии будут удалены все записи.
Рисунок 1.3 – Очистка поле текущей технологии
Ввод данных начнем с таблицы «Деталь». Процесс ввода и редактирования полей записи на всех уровнях идентичен. Для загрузки формы просмотра и корректировки полей нажимаем на инструментальной панели кнопку «Редактирование записи» или клавишу F4>. Данная форма имеет следующую структуру: слева располагаются имена полей справа — их значения.
Данные вводим с клавиатуры установив курсор в заполняемом поле или копируем из справочной базы данных (БД). Признаком привязки такой БД к определенному полю записи является пиктограмма «Книга» справа от поля ввода данных (рисунок 1.4). Справочные БД могут быть подключены к любому полю. Например в таблице «Деталь» к соответствующим полям подключены БД по материалам заготовкам наименованиям деталей и т.д.
Рисунок 1.4 – Обращение к справочной базы данных
Переход на уровень Операции осуществляем использованием команды «Переход на следующую таблицу» на инструментальной панели или клавиши F12>. При начальном вводе таблица Операции не содержит записей. Необходимо зарезервировать нужное количество строк клавишей Insert>. Затем последовательно в каждую строку вводим информацию об одной технологической операции. Порядок следования операций в технологическом маршруте задается порядком расположения строк в таблице. Режим корректировки полей F4> осуществляет загрузку формы редактирования (рисунок 1.5) аналогичной использующейся на уровне Деталь.
Рисунок 1.5 - Структура записи таблицы «Операции»
Информация в поля таблицы расположенной на уровне Операции может вводить как с клавиатуры так с помощью справочных баз данных.
После того как введены сведения об операциях вводим данные о переходах. Для этого следует устанавливаем курсор на нужную операцию и нажимаем клавишу F12>. Система переходит к следующему объекту и в рабочее поле системы будет загружена таблица Переходы.
Поскольку таблицы Операции и Переходы связаны уникальным ключевым полем ID (генерируемым автоматически при каждом вводе новой операции) то каждая строка объекта Операции будет иметь подчиненный список записей в таблице Переходы. При первоначальном вводе она не содержит записей. Нужно зарезервировать необходимое количество пустых записей клавишей Insert> и войти в режим редактирования первой строки нажав клавишу F4>.
Справочная таблица Тип перехода содержащая список наименований доступных баз данных представлена на рисунке 1.6.
Рисунок 1.6 - Справочные базы данных таблицы «Переходы»
Выделяем курсором нужную БД и двойным щелчком помещаем ее в рабочее поле системы. Из загруженного справочника выбираем информацию последовательно нажимая клавишу F12>. При достижении последнего уровня все необходимые данные будут скопированы и система вернется в форму редактирования записи таблицы Переходы. В зависимости от вида выбранной информации на форме «Редактирование записи» меняются наименования полей. Так например если были выбраны данные о режущем инструменте (рисунок 1.7) поле «Переход» изменит свое название на «Режущий инструмент». Данный механизм реализуется с помощью специальных режимов управления логической структурой данных F3>.
Рисунок 1.7 - Выбор режущего инструмента из справочника
В поле дублирующей технологии могут помещаться как реальные ТП связанные с базой данных КТС так и типовые ТП доступ к которым осуществляется из режима «Архив типовых технологий» в КОМПАС-АВТОПРОЕКТ-Технология.
Технологический процесс может быть разработан на основе библиотеки типовых операций. Последовательность действий реализующих данный режим будет рассмотрена для проектирования фрезерной операции ТП «корпус».
Подсистема «Сквозной ТП» позволяет сформировать технологию состоящую из операций и переходов (рисунок 1.8). В режиме текущей технологии на уровне «Операции» при обращении к справочнику в отличие от других подсистем диалог начинается с выбора вида операции. После выбора требуемого и нажатия клавиши F12> загружается соответствующая база данных. Из базы данных выбирается всё необходимое и таким образом формируется технологический переход и весь ТП в целом.
Рисунок 1.8 - Сквозной технологический процесс
Для просмотра созданной технологии используем «Дерево технологий».
Чтобы представить данные о техпроцессе в виде дерева (рисунок 1.9) производим двойной щелчок мыши на пиктограмме с изображением дерева в области «Процедуры» режима «Технология функции». Стартует приложение treetex.exe на форму которого выводятся два технологических процесса. Реализован механизм копирования и перемещения данных между этими ТП. Технологические операции копируются из одной технологии в другую вместе с подчиненными таблицами. Структура дерева включает четыре уровня:
- разделы: «Переходы» «Эскизы» «Карты» «Контроль» «Комментарии»;
- содержимое разделов.
Рисунок 1.9 - Дерево технологий
Когда технологический процесс в поле текущей технологии сформирован и отредактирован переходим к разработке комплекта документации. Для этого щелкаем мышью на пиктограмме с изображением карт в области Процедуры. Стартует программа формирования комплекта технологической документации. Результатом данной процедуры является комплект документов технологического процесса обработки резанием представленный приложением к выпускной квалификационной работе.
9 Обоснование выбора моделей оборудования
Выбор модели станка прежде всего определяется его возможностью обеспечить точность размеров и формы а также качество поверхности изготовления детали. Также следует учитывать соответствие станка габаритам обрабатываемых деталей устанавливаемых по принятой схеме обработки соответствие станка по производительности заданному масштабу производства соответствие станка по мощности наименьшая себестоимость обработки.
После сравнения станков на функциональное назначение технические и рабочие характеристики с теми характеристиками и показателями которые необходимо получить в результате обработки корпуса 456.852.32 был сделан выбор станочного оборудования. Данные по выбору оборудования представлены в таблице 1.7.
Таблица 1.7 – Оборудование по маршруту обработки
Вертикально-фрезерная
Вертикально-фрезерный станок FSS350R
Вертикально-сверлильный
Вертикально-сверлильный станок 2Н118
Горизонтально-расточная
Горизонтально-расточной станок 262ОГФ1
Вертикальный консольно-фрезерный станок модели FSS350R (аналог станка 6Т12) предназначен для фрезерования всевозможных деталей из стали чугуна и цветных металлов торцевыми концевыми цилиндрическими радиусными и другими фрезами. На станках можно обрабатывать вертикальные горизонтальные и наклонные плоскости пазы углы рамки зубчатые колеса. Технические характеристики станка FSS350R в таблице 1.8.
Таблица 1.8 - Технические характеристики станка FSS350R
Размеры рабочей поверхности стола(длина ширина) мм
Наименьшее и наибольшее расстояние от торца шпинделя до рабочей поверхности стола мм
Расстояние от оси шпинделя до вертикальных направляющих станины мм
Перемещение стола на одно деление лимба(продольное поперечное вертикальное) мм
Посадочное место для крепление инструмента крутой конус
Продолжение таблицы 1.8
Наибольшее перемещение стола мм
Наибольшая масса обрабатываемой детали кг
Мощность электродвигателя главного движения кВт
Частота вращения шпинделя обмин
Наибольшее осевое перемещение шпинделя мм
Универсальный вертикально-сверлильный станок модель 2Н118 предназначен для выполнения следующих операций: сверление рассверливания зенкерования нарезания резьбы и подрезки торцов ножами. Технические характеристики станка 2Н118 в таблице 1.9.
Таблица 1.9 - Технические характеристики станка 2Н118
Наибольший диаметр сверления мм
Конус Морзе шпинделя
Расстояние от конца шпинделя до стола мм
Продолжение таблицы 1.9
Тип двигателя главного движения
Номинальное напряжение В
Число оборотов двигателя обмин
Пределы частот вращения шпинделя обмин
Габариты(длина х ширина х высота) мм
Горизонтально-расточной станок 262ОГФ1 предназначен для комплексной обработки сложных корпусных деталей из конструкционных материалов в условиях многономенклатурного производства в автономном режиме или в составе гибких производственных систем. Технические характеристики станка 262ОГФ1 в таблице 1.10.
Таблица 1.10 - Технические характеристики станка 262ОГФ1
Исполнение конуса шпинделя
Мощность главного привода кВт
Скорость вращения шпинделя
Наибольшая масса обрабатываемой заготовки кг
Программируемые перемещения:
- сани стола – по оси Х мм
- шпиндельная бабка вертикально – по оси Y мм
- ползун продольно – по оси Z мм
- поворотный стол – по оси А рад
10 Аналитический расчет технологических параметров
Расчет припусков для отверстия 40 Н9 (40 +0062)
Минимальный припуск определяется по формуле 1.9:
ei – погрешность установки заготовки на выполняемом переходе.
Результаты расчетов заносятся в карту расчета припусков на обработку (таблица 1.11).
Таблица 1.11 - Карта расчета припусков
Допуск на изготовление
Размеры по переходам
Полученные предельные припуски
Проверка расчета осуществляется по формуле 1.10:
Tdз – Тdд = 2z0min – 2z0max(1.10)
гдеTdз – допуск на заготовку;
Тdд – допуск на готовую деталь;
z0max - общий максимальный припуск.
00-62=4910-2472=2438 мкм.
Схема припусков изображена на рисунке 1.10.
Рисунок 1.10 – Схема припусков
Определим режимы резания на фрезерование расчётно-аналитическим методом.
Операция 010 фрезерная.
Фрезеровать поверхность; глубина фрезерования t=31 мм; ширина фрезерования В = 80 мм; диаметр фрезы D = 80 мм; число зубьев фрезы z = 8 шт; подача Sz = 035мм.об.; период стойкости фрезы Т = 180 мин.
Скорость резания при фрезеровании определяется по формуле:
Значение коэффициента C и показателей степени приведены в [5 таблица 39 с. 286]. Общий поправочный коэффициент на скорость резания учитывающий фактические условия резания:
где Kmv - коэффициент учитывающий качество обрабатываемого материала;
Knv - коэффициент учитывающий состояние поверхности заготовки;
Kuv -коэффициент учитывающий материал инструмента.
Частота вращения шпинделя определяется по формуле:
nприн = 300 обмин - ближайшее большее значение числа оборотов по паспорту станка.
Сила резания при фрезеровании определяется по формуле:
где z - число зубьев фрезы; n - частота вращения шпинделя об.мин.
Значения коэффициента Q и показателей степени приведены в [5 таблица 41 с. 196] поправочный коэффициент на качество обрабатываемого материала Кмр для алюминия - в [5 таблица 10 с. 265].
Эффективная мощность резания определяется по формуле:
Производим проверку выбранного режима по мощности.
Мощность электрического двигателя станка (с учетом его к.п.д.) должна быть больше мощности резания т.е.
Мощность электрического двигателя вертикально-фрезерного станка
Nдв=8 кВт = 08 следовательно 188 кВт 64 кВт.
Мощность привода достаточна для выполнения операции на расчетных режимах резания.
Остальные режимы резания рассчитываем при помощи КОМПАС-АВТОПРОЕКТ Технология.
11 Автоматизированное проектирование технологического процесса изготовления детали и средств технологического оснащения
11.1 Обоснование выбора программных средств для проектирования технологической подготовки производства
В связи с большим количеством различных систем автоматизированного проектирования предлагаемых рынком в настоящее время все большую актуальность приобретают вопросы связанные с оптимальным выбором конкретных программ а также со стратегией их внедрения. Для крупных машиностроительных предприятий существенную роль играют такие параметры как цена функциональные возможности наличие систем параметризации и ассоциативности возможность интеграции и обмена данными с другими программами совместимость с технологическим оборудованием наличие средств разработки прикладного программного обеспечения удобство интерфейса наличие русскоязычной документации динамичность развития системы.
Необходимо обратить внимание на особенности движения модели изделия между основными элементами разработанной ранее схемы внедрения. Лучший вариант – это передача модели из одного элемента схемы в другой без применения конверторов преобразование данных что обеспечит гибкую ассоциативную связь между основными блоками сквозной системы проектирования а также позволит сэкономить время при групповой работе над одним проектом. В противном случае может возникнуть следующая картина: например если разработанную в какой-либо одной 3D-CAD-системе модель передать через встроенные конверторы в систему CAM с целью подготовки управляющих программ для станков с ЧПУ то произойдет разрушение параметризации и ассоциативности. Последнее приводит к потере рабочего времени так как после модификации исходной модели изделия необходимо самостоятельно обновлять управляющую программу.
В дипломном проекте будем использовать следующие программы: для построения модели детали – КОМПАС-3D для проектирования технологии изготовления детали – КОМПАС-АВТОПРОЕКТ 9.3; для решения технологических задач – COSMOSWorks 2006; для проектирования операционной технологии с разработкой управляющих программ и виртуальным моделированием обработки для станков с ЧПУ – ГеММа – 3D.
11.2 Проектирование операционной технологии с разработкой управляющих программ и виртуальным моделированием обработки для станков с ЧПУ в САПР
Система ГеММа-3D предназначена для разработки управляющих программ при изготовлении деталей высокой сложности на всех типах станков с ЧПУ.
ГеММа-3D является самостоятельной CAM-системой состоит из нескольких модулей обеспечивающих в совокупности полный сервис для работы технолога-программиста или оператора станка с ЧПУ.
Помимо этого система ГеММа-3D позволяет создавать программы обработки наиболее сложных деталей изготавливаемых с помощью фрезерования сверления электроэрозионной резки вырубки токарной обработки гравировки. В состав системы входит библиотека постпроцессоров в исходных текстах.
Среди возможностей программы: собственный геометрический редактор для создания математических моделей деталей и агрегатов; импорт моделей из всех известных CAD-систем и их доработка в соответствии с конкретным инструментом применяющимся на оборудовании с ЧПУ; подготовка управляющих программ с использованием любых видов геометрических данных плоских эскизов чертежей и поверхностей. При импорте модели комбинация их с твердыми телами. Задание контурной или поверхностной заготовки произвольной формы и сравнения результата обработки с математической моделью для оценки точности изготовления. Также при использовании программы ГеММа-3D возможно параметрическое задание технологических данных как в переходах так и между переходами; использование станочных циклов с их настройкой на любые УЧПУ; подготовка технологических эскизов и технологических карт; визуализация обработки и возможность редактирования управляющих программ. Программа позволяет подготавливать управляющие программы для токарных сверлильных фрезерных и других станков с ЧПУ.
Создаём контур детали для обработки в КОМПАС-3D и сохраняем *.dxf после этого импортируем этот файл в ГеММа – 3D (рисунок 1.10).
Рисунок 1.10 – Создание контура и импортирование его в ГеММа – 3D
В верхнем выпадающем меню выбираем в разделе «Обр.2D» «токарный контур» в появившемся окне задаём параметры инструмента стратегию обработки и параметры управляющей программы (рисунок 1.11).
Рисунок 1.11 – Задавание параметра инструмента стратегии обработки и сохранение прохода
После задания всех необходимых параметров нажимаем кнопку «Ввод» после чего система переходит в режим диалога. На запрос «Укажите обрабатываемую часть контура» правой кнопкой мыши указываем внешний контур (ПКМ) и нажатием ПКМ подтверждаем выбор. При запросе «Обрабатываемая часть» нажатием ЛКМ выбираем внешнюю часть контура и нажатием ПКМ подтверждаем выбор. Далее в открывшемся окне вводим координаты точки начала обработки.
Запрос – «Направление верно?» - ЛКМ выбираем направление ПКМ – подтверждаем выбор.
Запрос – «Координаты точки конца обработки» – в открывшемся окне вводим координаты – «Ввод».
Далее система формирует проход по контуру и предлагает сохранить этот проход. Если всё устраивает нажимаем кнопку «Да» (рисунок 1.11).
Для создания управляющей программы в верхнем выпадающем меню нажимаем «Обр.2D» и выбираем «Управл. прогр.» «Новая». В открывшемся окне нажимаем кнопку «Добавить ряд проходов» и указываем все созданные проходы после чего нажав кнопку «Постпроцессор» выбираем нужный и нажимаем кнопку «Создать УП» (рисунок 1.12).
Рисунок 1.12 – Создание и открытие управляющей программы
Ниже представлена управляющая программа для горизонтально – расточного обрабатывающего центра с ЧПУ 262ОГФ1 (операция 025 – «Расточная») разработанная при помощи системы автоматизированного проектирования технологических процессов ГеММа-3D.
PROGRAMME 00 CC100M M RWED 4
N8X-14.374Y-5.88F198.9
N14X-45.734Y-5.507F198.9
N19X14.187Y-48.627F198.9
N24X54.133Y-48.814F198.9
N30X-50.027Y9.053F198.9
N36X-3.018Y-1.036F198.9
N41X70.954Y-1.237F198.9
N46X58.954Y-50.057F198.9
N52X-14.068Y-5.887F198.9
N58X-46.198Y-5.916F198.9
N64X-8.946Y-6.064F198.9
N70X-50.92Y-5.978F198.9
12 Технологическое проектирование производственного подразделения
12.1 Расчет количества технологического оборудования и графика загрузки станков
Расчетное количество станков по i-той группе оборудования определяется на основании трудоемкости производственной программы и действительного фонда времени оборудования [11]:
где Nj - годовая программа выпуска деталей j-го типа шт;
n - количество наименований деталей обрабатываемых на i-й группе оборудования.
где Др- число рабочих дней в году;
mсм- число рабочих смен в сутки;
tсм- продолжительность рабочей смены (принять равным 8ч.);
kп - плановые потери времени на ремонт % (kn =2-8 %).
Годовой эффективный фонд времени работы одного станка
Средние коэффициенты загрузки оборудования по группам Кэi и по участку Кзу рассчитываются по формулам:
где m - число групп оборудования на участке.
Расчетное количество станков вертикально-фрезерной группы:
Коэффициент загрузки станков группы:
Расчетное количество станков вертикально-сверлильной группы:
Коэффициент загрузки станков:
Расчетное количество станков горизонтально-расточной группы:
Коэффициент загрузки станков горизонтально-расточной группы:
FSS350R 2Н118 262ОГФ1
Рисунок 1.13 - График загрузки оборудования на участке изготовления корпусов 456.852.32
Результаты расчетов количества оборудования и коэффициентов загрузки заносятся в таблицу 1.11.
Коэффициент загрузки оборудования участка:
Таблица 1.11 - Расчет потребности оборудования на участке
Вертикально-фрезерный
Горизонтально-расточной
12.2 Расчет численности персонала
В серийном производстве численность основных рабочих для выполнения нормируемых работ определяется по формуле [11]:
Nj- годовой объем выпуска изделий j-го вида шт.;
Фд.р.- действительный годовой фонд времени работы рабочего ч.;
Квн- коэффициент выполнения норм на i-й операции.
где a - коэффициент учитывающий потери рабочего времени - неявки установленные законодательством (можно принять 2-12%).
Численность рабочих для вертикально-фрезерной операции:
Численность рабочих для вертикально-сверлильной операции:
Численность рабочих для горизонтально-расточной операции
Трудоемкость работ выполняемых за год по вертикально-фрезерной операции N1:
(404 х 3010) 60 = 202673 (н.ч).
Трудоемкость работ выполняемых за год по вертикально-сверлильной операции N2:
(11824 х 3010) 60 = 59317 (н.ч).
Трудоемкость работ выполняемых за год по горизонтально-расточной операции N3:
(2596 х 3010) 60 = 130233 (н.ч).
Таблица 1.12 - Расчет требуемого количества основных рабочих
обслуживаемых станков
Общая трудоемкость работ выполняемых за год нормо-ч
Количество рабочих чел
Оператор станков с ЧПУ
Определение численности вспомогательных рабочих производится по нормам обслуживания. На основании этих норм составляется ведомость вспомогательных рабочих (таблица 1.13).
Таблица 1.13 – Ведомость вспомогательных рабочих
Определяющий показатель
Норма обслуживания на 1 рабочего
Расчетное количество чел
Слесари по ремонту оборудования
Электромонтеры (дежурные)
Количество ед. оборудо-вания в смену
Слесари по ремонту и оснастке
Водители электрокар и автопогрузчиков
Количество тонн груза в смену
(при массе изделий до 1 кг)
Слесарь по межремонтному обслуживанию
Продолжение таблицы 1.13
Подносчики и раздатчики инструмента
Единиц оборудования на человека
Распределители работ
Количество основных рабочих
Процент от чис-ленности основных рабочих
Уборщики производственных помещений
Убираемая площадь м2
При расчете численности ИТР следует пользоваться следующими нормативами. В подчинении мастера должно быть 20-25 рабочих; старший мастер назначается для руководства не менее чем для двух мастеров (участка или сменными); начальник участка руководит двумя-тремя старшими мастерами; начальник цеха руководит четырьмя – пятью начальниками участка.
На основании нормативов количество мастеров на участке:
На основании нормативов количество старших мастеров:
тл.doc
ГОСУДАРСТВЕННОЕ ОБРАЗОВАТЕЛЬНОЕ УЧРЕЖДЕНИЕ
ВЫСШЕГО ПРОФЕССИОНАЛЬНОГО ОБРАЗОВАНИЯ
«ВОРОНЕЖСКИЙ ГОСУДАРСТВЕННЫЙ ТЕХНИЧЕСКИЙ УНИВЕРСИТЕТ»
Кафедра: «Технология машиностроения»
Специальность: 120100 (151001) «Технология машиностроения»
ВЫПУСКНАЯ КВАЛИФИКАЦИОННАЯ РАБОТА
Тема дипломного проекта: Разработка технологии и средств технологического оснащения для изготовления корпуса 456.852.32
Пояснительная записка
дата Инициалы фамилия
по экономической и организационно-
управленческой части А.А. Мордовцев
по экологии и безопасности О.В. Козлова
Студент группы: ТМ-041в
(фамилия имя отчество)
на выпускную квалификационную работу
утверждена распоряжением по факультету № 6 от «20 » января 2010 г.
Технические условия: режим работы участка–односменный .
программа выпуска–3010 штук в год. .
Содержание (разделы графические работы расчеты и проч.):
Графическая часть: 1) титульный лист – 1 лист (А1); 2) сборочный чертеж узла – 1 лист (А1); 3) рабочий чертёж детали – 1 лист (А1); 4) твердотельная модель – 1 лист (А1);5) результаты расчета корпуса 456.852.32 в 6) чертеж заготовки – 1 лист (А1); 7) разработка технологического процесса в САПР ТП – 1 лист (А1); 8) плакаты с иллюстрацией разработанного технологического процесса – 1 лист (А1); 9) управляющая программа в ГеММа-3D; 10) сборочный чертеж установочного приспособления – 1 лист (А1); 11) сборочный чертёж контрольного приспособления – 1 лист (А1); 12) плакат с результатами научно-исследовательской части; 13) планировка участка – 1 лист (А1); 14) плакат с технико-экономическими показателями спроектированного участка – 1 лист (А1).
Расчётно-пояснительная записка: 1) производственно-технологическая часть; 2) проектно-конструкторская часть; 3) научно-исследовательская часть; 4) экс-плуатационная часть; 5) экономическая и организационно-управленческая часть. 6) безопасность и экологичность. Комплект карт технологического процесса
План выполнения дипломного проекта
с « » 2010 г. по « » 2010 г.
Название элементов проектной
руководи-теля кон-сультанта
Производственно-технологическая часть
Проектно-конструкторская часть
Научно-исследовательская часть
Эксплуатационная часть
Экономическая и организационно- управленческая часть
Безопасность и экологичность
Комплект карт технологического процесса
Руководитель дипломного проекта
(подпись) (Фамилия имя отчество)
Дипломный проект закончен
(подпись дипломника)
Пояснительная записка и все материалы просмотрены
Консультанты: Мордовцев Александр Анатольевич
к защите дипломного проекта в Государственной аттестационной комиссии
(подпись) (Инициалы фамилия)
3.doc
1 Выбор режимов обработки для электрохимического маркирования
Маркирование металлических изделий применяется в тех отраслях машиностроения где необходимо опознавание каждой отдельной детали на всех стадиях обработки и сборки. Отсутствие опознавательного знака на деталях может привести к значительным задержкам сборки изделий ввиду необходимости повторного установления отличительных признаков.
Одним из методов маркирования является электрохимическое маркирование. Процесс протекает в водных растворах нейтральных солей (хлористого натрия азотнокислого калия и др.) при напряжении технологического тока до 8 (В).
При расчётных режимах маркирования можно получать контуры знаков с шириной штриха менее 01 (мм). Это обеспечивает нанесение информации стандартными шрифтами высотой знака 15 (мм) и более.
Электрохимическим методом можно маркировать детали любой формы и габаритов из токопроводящих материалов. Силы возникающие в зоне формирования знаков не превышают 100 (Н) что не может вызвать деформацию и поломку деталей.
Использование электрохимического маркирования позволяет механизировать и автоматизировать процесс повысить качество наносимой информации при снижении трудоёмкости операции.
Процесс электрохимического маркирования имеет свои специфические особенности: во-первых его осуществляют без прокачки электролита; во-вторых требуемая для маркирования малая ширина штриха рабочей части катода существенно меняет условия газонаполнения массопереноса в зазоре что оказывает определяющее влияние на технологические показатели процесса.
Применяемые при маркировании электролиты не должны содержать соединений которые могут образовать твёрдые продукты восстановления на катоде. Поэтому в основном используют нейтральные растворы солей щелочных металлов при которых образующиеся на аноде ионы тяжёлых металлов не достигают катода переходя в гидроокиси в межэлектродном промежутке или в прикатодном диффузионном слое. Для получения точного отображения катода на аноде необходимо применять электролиты с малой электропроводностью и большой пассивирующей способностью. Это обеспечивает требуемую ширину штриха.
В данном случае для маркировки корпуса из материала АК7 (алюминиевый сплав) выбираем следующий состав электролита: бромистый калий 5-10% азотнокислый аммоний 5-10% [13].
Также необходимо определить напряжение на электродах. Нижний предел напряжения обуславливается условиями поддержания химических реакций на электродах и составляет 3-4 (В). Максимальное напряжение ограничивается возможностью электрического пробоя между электродами требованиями техники безопасности и целесообразностью реализации больших рабочих токов проходящих через электрохимическую ячейку.
Напряжение выбирают в диапазоне 3-30 (В). При маркировании когда величина рабочего зазора колеблется от 002 - 015 (мм) рабочий диапазон 3 -16 (В). При напряжении 9-11 (В) получается хорошая чёткость и стойкость знака при удовлетворительной точности и допустимом содержании водорода. Эти значения можно принять в качестве рабочего диапазона изменения напряжения.
Значения напряжения и времени обработки: напряжение 6-7 (В) время -1 (с) [13]. Время обработки должно быть выдержано с погрешностью не более 01 - 02 (с) иначе резко нарушается качество знаков. Информацию можно наносить на поверхность с шероховатостью не выше Rа = 5 (мкм).
Носителем информации при электрохимическом маркировании является контур нанесённый на рабочую поверхность инструмента профильными знаками.
При получении рабочей части инструмента с использованием шрифтов подобранные знаки отливают по технологии типографского производства далее производят механическую обработку рабочей поверхности (сверление мелких отверстий для удержания изоляции зачистку профиля и др.). После изготовления рабочие части инструмента окончательно контролируют устанавливают соответствие чертежу номера шрифта положение и наличие всех знаков контролируют качество диэлектрических покрытий и выступов определяющих межэлектродный зазор.
Для мелкого маркирования целесообразно использовать инструменты с литыми знаками [13].
Мелкое маркирование деталей может выполняться с помощью ручного инструмента переносных приборов настольных и стационарных установок.
2 Выбор оборудования для электрохимического маркирования
В качестве оборудования для маркирования номера на данном корпусе наиболее оптимально подходит универсальный прибор УПЭК – 901 [13]. Это переносной прибор предназначен для маркирования плоских и круглых деталей (по трафарету и печатными знаками) для маркирования деталей (рисунок 3.1).
Рисунок 3.1 - Универсальный переносной аппарат для мелкого маркирования УПЭК- 901
Технические характеристики УПЭК- 901:
- напряжение питания 220 (В);
- рабочее напряжение от 2 до 16 В);
- время маркирования:
при автоматической выдержке 2-25 (с);
при ручной выдержке не ограничено;
- размеры шрифта свыше 1 (мм);
- глубина знака до 002 (мм);
- мощность 150 (Вт);
- габаритные размеры 300
Переносные приборы выполняют обычно в виде чемодана с отделениями для хранения инструмента электролитов.
Универсальный прибор УПЭК - 901 позволяет маркировать плоские и слабо изогнутые поверхности на рабочем столе прибора (масса деталей до 10 кг) и выносной головкой с длиной шнура 2 (м.).
УПЭК- 901 состоит из следующих частей (рисунок 6.1):
- поролоновые подушки;
- клавиши задания режима;
- стол для маркирования мелких деталей.
На столе прибора имеется устройство для накатывания для нанесения информации на круглые детали диаметром до 25 мм. Все вспомогательные устройства закреплены на съёмной крышке прибора. Там находятся выносная головка с ручным штемпелем и шнуром провод для подключения прибора к сети съёмная часть электрохимического накатника устройство для дозирования электролита включающее мерные технические шприцы с иглами концы которых введены в поролоновые подушки расположенные в прозрачных коробках. На каждой коробке указана марка маркируемого материала. Приборы оснащены тремя шприцами в которых находятся электролиты для маркирования сталей цветных и титановых сплавов. Объём шприца 10 (мл.) объём каждой подушки 12 (см3) разовая подача электролита 15 - 2 (мл.). После нажатия на поршень шприца часть электролита поступает в подушку которая используется в дальнейшем взамен тампона. Количество электролита должно быть таким чтобы обеспечить смачивание поверхности без накопления электролита в виде капель что существенно снижает чёткость знака.
Выносная головка (рисунок 3.2) выполнена в виде ручки 4 из капролона цанги 2 со штемпелем 1 закрепленным шаровым шарниром 3 на ручке. Головка соединена прибором шнуром 6 с быстроразъемным штекерным устройством 7; её масса не более 80 (г.). Маркирование происходит объемными знаками.
Рисунок 3.2 – Выносная головка УПЭК - 901
Точная фиксация головки относительно маркируемой поверхности происходит за счёт шарнирного крепления рабочей части относительно ручки. Допускаемый перекос до 8°. Величина прижима головки к детали ограничена подпружиненным упором который при силе 500 (Н) воздействует на микровыключатель 5 и включает технологический ток. Время действия тока задаётся с помощью реле и определяется автоматом либо периодом нажатия на упор.
Электрическая схема прибора включает блок питания обеспечивающий подачу стабилизированного напряжения с погрешностью не более 01 (В). Напряжение изменяют дискретно через 1 (В) от 2 до 5 (В) и через 2 (В) до 16 (В) клавишным переключателем на лицевой стороне прибора. От этого блока получает питание реле времени и блок управления позволяющий выдать команды на автоматическую или ручную выдержку времени обработки.
Производительность прибора — до 800 плоских и до 200 цилиндрических деталей в час. Прибор позволяет получать качественное изображение на деталях при общей площади наносимой информации до 50 (мм2).
3 Влияние электрохимического маркирования на эксплуатационные характеристики детали
При маркировании детали из сплава АК7 внутреннее напряжение на поверхности достигает ±40-60 (МГЦ). Рассмотрение контура клеймения показывает что после механического маркирования имеет место упорядоченная направленность волокон по контуру клеймения которая свойственна технологическим процессам связанным с пластическим деформированием металлов.
После электрохимического маркирования не обнаружено каких - либо дефектов снижающих прочность материала что указывает на возможность исключения концентраторов напряжений характерных для механического маркирования.
На основе экспериментальных данных получены эффективные коэффициенты концентрации напряжений позволяющие рассчитать механические характеристики различных материалов [13].
- после механического маркирования - 157;
- после электрохимического маркирования - 137.
Следовательно электрохимическое маркирование в меньшей степени влияет на местную концентрацию напряжений и является предпочтительным по сравнению с механическим способом нанесения информации.
Заключение.doc
Исходя из разработанного технологического процесса и объёма выпуска продукции был спроектирован участок по изготовлению корпусов 456.852.32. Оборудование участка позволяет вести серийный выпуск деталей. Для обеспечения полной загрузки оборудования на данных станках будет производиться выпуск подобных деталей – других корпусов.
Был проведён анализ базового технологического процесса производства детали и выявлена возможность повышения качества и экономической эффективности производства.
Спроектирована операционная технология производства детали и конструкция приспособления. При этом были задействованы прогрессивные средства разработки технологического процесса обработки детали в САПР.
Был спроектирован участок механического цеха рассчитано количество необходимого оборудования определен тип производства состав основных и вспомогательных рабочих. Было выявлено сокращение количества операций количества оборудования вследствие чего уменьшились затраты на оборудование электроэнергию амортизацию а также снижение себестоимости детали.
Определена плановая себестоимость изделий составлена смета производственных расходов.
Определены технико-экономические показатели проектируемого предметно-замкнутого участка.
Содержание.doc
1 Конструктивно-технологический анализ узла составной частью
которого является выбранная для проектирования деталь 9
2 Назначение и краткое технологическое описание детали 10
3 Оценка технологичности детали 13
4 Анализ базового технологического процесса 14
5 Установление типа производства 14
6 Выбор типа заготовки и предварительное назначение припусков 16
7 Выбор технологических баз и оценка точности базирования 18
8 Разработка маршрута операций технологического процесса
9 Обоснование выбора моделей оборудования 26
10 Аналитический расчет технологических параметров 30
11 Автоматизированное проектирование технологического процесса изготовления детали и средств технологического оснащения 33
11.1 Обоснование выбора программных средств для проектирования технологической подготовки производства 33
11.2 Проектирование операционной технологии с разработкой управля-
ющих программ и виртуальным моделированием обработки для станков с ЧПУ в САПР 34
12 Технологическое проектирование производственного подразделения 40
12.1 Расчет количества технологического оборудования и графика
12.2 Расчет численности персонала 43
Проектно-конструкторская часть 47
1 Разработка твердотельной 3D модели детали 47
2 Расчет силовых и деформационных параметров детали в процессе ее
эксплуатации или изготовления с помощью САЕ 50
3 Обоснование конструкции и расчет специальных средств технологического оснащения 53
3.1 Станочное установочно-зажимное приспособление 53
3.2 Контрольное приспособление 55
4 Определение производственной площади участка 58
4.1 Выбор системы складирования 58
Научно-исследовательская часть 60
1 Расчет режимов обработки и инструмента для электрохимического маркирования 60
2 Выбор оборудования для электрохимического маркирования 62
3 Влияние электрохимического маркирования на эксплутационные характеристики детали 65
Эксплуатационная часть 66
1 Эксплуатация режущего инструмента 66
1.1 Эксплуатация резцов 66
1.2 Эксплуатация фрез 69
Экономическая и организационно-управленческая часть 72
1 Экономическое обоснование проекта участка 72
1.1 Определение потребности в инвестициях для организации спро-
ектированного участка 72
1.2 Организация оплаты труда на участке 75
1.3 Расчет текущих затрат 78
1.4 Расчет себестоимости продукции 82
2 Расчет технико-экономических показателей экономической эффек-
3 Расчет показателей экономической эффективности проекта участка 86
4 Организация подготовки ремонтных работ 90
Безопасность и экологичность 93
1 Техника безопасности 94
2 Производственная санитария и гигиена труда 95
3 Противопожарные мероприятия и средства пожаротушения 97
4 Охрана окружающей среды 98
Список литературы 101
Приложение А. Графическая часть проекта 103
Приложение Б. Спецификации к графической части проекта 117
Приложение В. Комплект документов технологического процесса обра-
ботки детали корпус 456.852.32 123
Приложение.doc
2.doc
1 Разработка твердотельной 3D модели детали
Для изготовления твердотельной 3D модели детали будем использовать программу КОМПАС-3D V10 разработанную компанией АСКОН.
Основная задача решаемая системой КОМПАС-3D – моделирование изделий с целью существенного сокращения периода проектирования и скорейшего их запуска в производство. Эти цели достигаются благодаря возможностям:
- быстрого получения конструкторской и технологической документации необходимой для выпуска изделий;
- передачи геометрии изделий в расчетные пакеты;
- передачи геометрии в пакеты разработки управляющих программ для оборудования с ЧПУ;
- создания дополнительных изображений изделий (например для составления каталогов создания иллюстраций к технической документации и т.д.).
Начинаем работу с запуска программы и выбора в верхней панели значка Создать. В появившемся окне выбираем значок Деталь (рисунок 2.1).
Рисунок 2.1 – Начало работы с программой
Далее с помощью графических примитивов строим контур детали. После окончания закрываем эскиз. После этого с помощью операции выдавливания строим твердотельную модель (рисунок 2.2).
Рисунок 2.2 – Построение твердотельной модели с помощью операций выдавливания
С помощью команды скругление выполняем ряд скруглений острых кромок поверхности модели. Для этого поочередно выбираем нужную кромку и указываем радиус скругления для нее (рисунок 2.3).
Рисунок 2.3 – Скругление острых кромок
Чтобы получить внутренние поверхности детали используем операции вырезания. Для этого сначала строим эскиз поверхности которую нужно получить а потом выполняем саму операцию вырезания (рисунок 2.4).
Рисунок 2.4 – Получение внутренних поверхностей детали
Выбираем команду «Фаска» и указываем поверхности на которых ее следует построить (Рисунок 2.5).
Рисунок 2.5 – Построение фасок
Далее строим 10 отверстий. Сначала делаем эскиз т.е. указываем место нахождения отверстия. Потом выбираем из библиотеке форму и размер требуемого отверстия (рисунок 2.6).
Рисунок 2.6 – Построение 10 отверстий
На заключительном этапе следует построить «Условное изображение резьбы» для 10 отверстий. На рисунке 2.7 представлен окончательный вид модели корпуса.
Рисунок 2.7 – Построение резьбы
2 Расчет силовых и деформационных параметров детали в процессе ее изготовления с помощью САЕ
SolidWorks имеет простой в использовании новый инструмент анализа напряжений для пользователей COSMOSXpress. COSMOSXpress может помочь снизить стоимость и сократить время от начального замысла проекта до его внедрения на рынок выполняя тестирование проектов с помощью компьютера вместо проведения дорогостоящих и долговременных производственных испытаний. Точность результатов анализа зависит от свойств материала ограничений и нагрузок. Чтобы получить надежные результаты указанные свойства материала должны точно представлять материал детали а ограничения и нагрузки должны точно представлять условия эксплуатации детали.
Исходя из режимов резания заданных в разработанном технологическом процессе найдём все составляющие силы резания для токарной операции обработки корпуса.
P(zyx) =10Cp tx Sy n Kp (2.1)
где Рz Рх и Ру – составляющие силы резания;
Кр – коэффициент учитывающий реальные условия резания.
Pz =10403271060758270 225=2004 (Н)
Работу начинаем с экспортирования модели в формат модель_10.stp. Открываем файл в программе SolidWorks и запускаем программу COSMOS-Xpress (рисунок 2.8).
Рисунок 2.8 – Выбор программы САЕ
Далее выбираем материал детали – легированный алюминий (сплав 2014) – как показано на рисунке 2.9.
Рисунок 2.9 – Выбор материала
Далее вводим ограничения на перемещение которое получается при установке и закреплении заготовки в приспособлении что и показано на рисунке 2.10.
Рисунок 2.10 – Выбор ограничений
Выбираем вид и размер прилагаемой нагрузки согласно проведённого расчёта. Процесс установки нагрузки показан на рисунке 2.11.
Рисунок 2.11 – Установка нагрузки
Проводим анализ. После чего получаем результат представленный на рисунке 2.12.
Рисунок 2.12 – Результат приложения нагрузки
3 Обоснование конструкции и расчет специальных средств технологического оснащения
3.1 Станочное установочно-зажимное приспособление
Проектируемое установочно-зажимное приспособление предназначено для установки и закрепления заготовки на горизонтально-расточном станке 262ОГФ1.
Использование этого приспособления предполагается на третьей операции. Базирование заготовки происходит на плоскость и 2 пальца (цилиндрический и срезанный). Обрабатываемые поверхности и выдерживаемые размеры представлены в графической части работы.
Закрепление происходит приложением силы зажима перпендикулярно к ее базовой плоскости. Эта схема обеспечивает доступность режущего инструмента к обрабатываемой заготовке с разных сторон. При этом конструкция приспособления является достаточно простой.
Направление и максимальное значение силы резания рассчитывается исходя из условия неподвижности заготовки при обработке. Данные для расчета берутся в справочной литературе.
Направление силы резания будет параллельно обрабатываемой плоскости и будет стремиться сдвинуть заготовку перпендикулярно нормали к обрабатываемой плоскости (рисунок 2.13)
Рисунок 2.13 – Схема действия сил
Величина силы резания рассчитывается по формуле (2.2):
Где t – глубина резания в мм.;
s – подача в мм.зуб;
v – скорость резания м.мин.;
Кр – поправочный коэффициент учитывающий фактические условия резания;
Численные значения показателей степени коэффициентов Кр и Ср представлены в справочной литературе [5].
Посчитаем максимальную силу резания по формуле (2.2):
Сила зажима при данной схеме закрепления определяется по формуле (2.3):
где К - коэффициента надежности закрепления К=365;
- коэффициенты трения.
В нашем случае опираясь на схему действия сил (рисунок 2.13) делаем вывод что сила исходного закрепления равна силе закрепления .
Диаметр пневмоцилиндра определяется по формуле:
где D – рабочий диаметр цилиндра мм;
р – давление рабочее в пневмосистеме МПа.
По конструктивным соображениям принимаем диаметр мембраны 100мм тем самым обеспечиваем дополнительный запас по усилию прижатия заготовки.
При проектировании приспособления необходимо предусмотреть отверстия в плите для выхода инструмента при цикле обратной расточки.
Приспособление базируется на станке посредством трех взаимно перпендикулярных плоскостей. Базирование происходит по боковым направляющим в угол тумбы станка которая закреплена на столе где «закреплен» программный ноль станка. Координация элементов приспособления происходит по двум плоскостям.
3.2 Контрольное приспособление
При изготовлении детали необходимо выполнить требования точности взаимного расположения поверхностей.
На чертеже детали указаны требования к точности взаимного расположения поверхностей. Это неперпендикулярность поверхностей 9 и 1. Не перпендикулярность должна быть не более 004 мм.
В этом пункте разработана схема контроля (рисунок 2.14) поверхностей 9 и 1. В этой схеме используется плита 1 прилегающая к поверхности 1 и разжимная самоцентрирующаяся оправка 2 которая жестко связана с плитой и перпендикулярна ей. Неперпендикулярность плиты и оправки назначается в соответствии со справочной литературой и равна 0003 мм. На оправку закреплен индикаторный узел 4 который может вращаться на ней. Между узлом и оправкой посадка с зазором H7h6. Максимальный зазор между оправкой и индикаторным узлом составляет 0027 мм. В индикаторном узле применяется индикатор многооборотный 1 МИС ГОСТ 9696-75 с ценой деления 001 мм. Предельная погрешность измерения составляет 003 мм. Плита выполняется с непараллельностью ее плоскостей 0002 мм.
Разжимная самоцентрирующаяся оправка выполнена с тремя шариками 5 которые разжимаются упорным винтом 3.
Рисунок 2.14 – Схема контроля
Произведем расчет погрешности измерения при использовании этой оправки.
Погрешность измерения будет складываться из следующих составляющих: непараллельности плоскостей плиты неперпендикулярности оправки плите половина зазора между индикаторным узлом и оправкой и погрешностью индикатора.
Суммарная максимальная погрешность измерения вычисляется по формуле (2.5):
где Dпар – непараллельность плоскостей плиты;
Dпер – неперпендикулярность оправки и плиты;
S – зазор между индикаторным узлом и оправкой;
Dизм – погрешность измерения.
По формуле (2.5) получаем:
Исходя из вышеизложенного можно составить порядок работы данного контрольного приспособления.
Установить на приспособление индикатор 1 МИС ГОСТ 9696-75.
Установить приспособление на деталь оперев плоскостью и вставив оправку в отверстие.
Винтом разжать оправку вращая болт от руки до упора.
Проверить визуально плотности прилегания плиты к детали.
Установить на индикаторе предварительный натяг 1 мм.
Установить нулевое положение на шкале индикатора.
Повернуть индикаторный узел вокруг оправки на 180° следя за показаниями индикатора.
Деталь считать годной при отклонении стрелки индикатора от нулевого положения не более чем на 012 мм (12 делений индикатора).
Вывернуть разжимной болт.
Снять приспособление с детали.
Снять индикатор с приспособления.
4 Определение производственной площади участка
Производственная площадь участка занимаемая непосредственно оборудованием и рабочими местами определяется исходя из удельной площади приходящейся на один станок и числа основных станков.
Удельная площадь на один мелкий станок – 10 – 12 м2 средний станок - 15 – 25 м2 крупный 30 -45 м2.
К мелким станкам относятся станки с габаритами до 1800х800 мм средним – до 4000х2000 мм к крупным – до 8000х4000 мм.
На участке по изготовлению корпуса 456.852.32 располагаются 1 мелкий и 2 средних станка.
Производственная площадь участка рассчитывается исходя из удельной площади приходящейся на один станок:
где К – количество станков;
Sуд – удельная площадь на один станок.
Производственная площадь непосредственно занимаемая оборудованием:
Проходы и проезды составляют до 20% производственной площади:
Общая площадь производственного участка составляет:
4.1 Выбор системы складирования
В единичном и серийном производствах цеховой склад заготовок и полуфабрикатов размещают в начале пролетов в соответствии с обрабатываемыми деталями. Для хранения крупных заготовок склады располагают на специальных открытых или закрытых эстакадах для хранения 2÷3-х дневного запаса заготовок. Хранение штучных грузов (отливок поковок деталей и т.д.) должно производиться в унифицированной таре которая позволяет использовать механизированные погрузочно-разгрузочные транспортирующие устройства и многоярусное хранение в штабелях или на стеллажах. Запас материалов и заготовок в цеховом складе должен быть невелик так как назначением его является только обеспечивать регулярное снабжением цеха (участка) материалами. При расчете площади складов заготовок исходят из необходимости запаса и грузонапряженности пола [14]:
где Р – площадь складов заготовок м2;
Q – масса заготовок обрабатываемых в цехе в течение года т;
Т – запас заготовок дни;
f – среднее число рабочих дней в году;
q – средняя грузонапряженность склада тм2;
кр – коэффициент использования площади склада представляющий отношение полезной площади склада к его общей площади и учитывающий проходы и проезды (кр = 04÷05).
Склад готовых деталей предназначен для хранения деталей перед отправкой на сборку. Склад готовых деталей и комплектовочный склад размещают в конце пролетов механического цеха на пути следования деталей на сборку. Площадь склада готовой продукции определяется также как и общая площадь под заготовки и материалы. Грузонапряженность площади пола складов принимается меньшей чем в цеховом складе заготовок так как готовые детали хранятся как правило на стеллажах или специальных подставках столах и таре. Допускаемую грузонапряженность следует принимать равной: при удельном весе материалов более 1÷4 т на 1 м2 для мелких и средних деталей и 15 т на 1 м2 для крупных; при удельном весе материалов до 4 т – соответственно 04 и 06 на 1 м2.
4.doc
1 Эксплуатация режущего инструмента
1.1 Эксплуатация резцов
Эффективное использование резцов возможно в условиях повышенной жесткости точности и быстроходности станков.
Для повышения жесткости системы СПИД необходимо закреплять заготовку в патронах при длинных заготовках – в патронах с поджимом центром задней бабки сокращать вылет резца из резцедержателя при строгании вылет резца устанавливать в пределах 18-80 Н для отогнутых и 08-10 Н для прямых резцов [5].
Глубина резания при черновой обработке выбирается наибольшей. Подача назначается с учетом рекомендаций приведенных в таблицах 4.1 4.2
Таблица 4.1 – Ориентировочные значения подачи (мм.об.) для чернового точения труднообрабатываемых материалов с sв 900 МПа
Диаметр заготовки мм
Глубина резания t мм
Примечание. К труднообрабатываемым материалам отнесены теплостойкие хромоникелевые хромомолибденовые сложнолегированные стали перлитного ферритного мартенситного аустенитного и аустенитно-мартенситного классов.
Таблица 4.2 – Ориентировочные значения подачи (ммоб) для чернового точения конструкционных углеродистых сталей стального и чугунного литья
Продолжение таблицы 4.2.
Примечание. Большие значения подач следует принимать для обработки мягких сталей при работе в центрах с отношением длины к диаметру заготовки меньше 6 или в патроне с отношением длины вылета из патрона к диаметру заготовки меньше 2.
Ниже приведены данные характеризующие зависимость поперечной подачи s мм.об. от ширины резца амм и диаметра отрезки D мм обрабатываемого материала при отрезке отрезными резцами:
В условиях малой жесткости СПИД глубину резания при точении следует уменьшать до 03 мм угол в плане выбирать не менее 60° резец устанавливать выше центра на 11-15 % от диаметра обработки.
Рекомендуемые размеры площади поперечного сечения резцов при точении в зависимости от площади сечения срезаемого слоя приведены в таблице 4.3.
Таблица 4.3 – Размеры площади поперечного сечения резцов (НхВхН) с углом в плане (j = 45°) в зависимости от площади сечения срезаемого слоя
Площадь сечения срезаемого слоя мм2
Значение допустимого износа по задней грани резцов из быстрорежущих сталей и резцов оснащенных твердым сплавом рекомендуется принимать равным значениям приведенным в таблице 4.4.
Таблица 4.4 – Допустимый износ h3 резцов из быстрорежущих сталей мм
Обрабатываемый материал
Сталь стальное литье чугун ковкий при работе
Токарный проходной подрезной или расточной
Токарный прорезной и отрезной
Строгальный проходной
Строгальный поперечный подрезной
Долбежный прорезной и отрезной
В таблице 4.6 приведены возможные неисправности при точении твердосплавными резцами и рекомендуемые меры по их устранению.
Таблица 4.6 – Возможные неисправности при точении твердосплавными резцами и рекомендуемые меры по их устранению
Возможные неисправности
Пластическая деформация лезвия
Увеличить скорость резания
Уменьшить скорость резания
Продолжение таблицы 4.6
Уточнить скорость глубину подачу
Выбрать более прочную марку сплава
Увеличить радиус при вершине
Увеличить положительный передний угол
Применить больший задний угол
Применить более жесткий резцедержатель
Увеличить жесткость СПИД
Исключить водные СОЖ
Применить меньший отрицательный передний угол
Уточнить радиус при вершине
Снизить припуск на переточки
1.2 Эксплуатация фрез
С целью экономической работы и длительной службы фрез необходимо придерживаться следующих правил: применять только рекомендуемые режимы резания а не применять слишком больших подач и скоростей резания своевременно затачивать фрезу следить за тем чтобы износ режущих кромок не доходил до крайних допустимых норм (таблица 4.7) и ориентироваться по допустимой шероховатости обрабатываемой поверхности при фрезеровании малых деталей небольшими фрезами малой производительности рекомендуется более часто подправлять (доводить) режущие кромки фрез чугунным притиром с пастой не снимая фрез со станка не останавливать и не включать вращения шпинделя пока фреза находится в контакте с заготовкой следить чтобы станок работал без вибраций [5].
Таблица 4.7 – Допустимый износ по задней поверхности зуба фрезы
Материал режущей части фрезы
Допускаемый износ по задней поверхности мм
с напаянными пластинками
Прорезные и отрезные
После заточки и доводки у фрезы контролируют биение режущих кромок размеры рабочей части инструмента геометрические параметры и чистоту режущих поверхностей. Допустимое радиальное биение зубьев фрез приведено в таблице 4.8. Допустимые отклонения углов заточки a a1 и g до 10° находятся в пределах ±1° а при их значениях равных 10-20° ±2° отклонение угла в плане
j ± (2-3°) j0 ± 2° и вспомогательного угла в плане j1 ± (0°30-1°).
Таблица 4.8 – Допустимое биение фрез мм.
между двумя смежными зубьями
для двух противоположных зубьев
Цельные насадные торцовые цилиндрические и дисковые
Насадные цилиндрические со вставными ножами из быстрорежущей стали
Насадные цилиндрические оснащенные пластинками из твердого сплава
Сборные насадные торцовые и дисковые
Цельные концевые из быстрорежущей стали и твердого сплава
Пазовые затылованные
Отрезные и прорезные классов
Введение.doc
Внедрение прогрессивных методов обработки деталей экономически обоснованное применение высокопроизводительного оборудования износостойкого режущего инструмента механизированной оснастки в механизированных цехах машиностроительного производства является актуальным.
Важнейшие современные направления развития технологии машиностроения по оптимизации режимов и процессов обработки автоматизации серийного производства и управления технологическими процессами применению технологических методов повышения эксплуатационных качеств изготовляемых изделий и других в значительной мере основываются на достижениях математических наук электронной вычислительной и управляющей техники робототехники металлофизики и других современных теоретических и технических наук.
Темой выпускной квалификационной работы является разработка технологии средств технологического оснащения для изготовления корпуса 456.852.32 в условиях крупносерийного производства.
В условиях нынешней экономической ситуации необходимо добиваться максимального эффекта от вложенных средств чтобы они смогли в будущем приносить наибольший доход это касается всех машиностроительных предприятий.
Таким образом целью выпускной квалификационной работы является совершенствование операционного технологического процесса изготовления корпуса 456.852.32 и достижение наилучших технико-экономических показателей.
Для достижения этой цели должны быть решены следующие задачи:
- выбор и обоснование метода получения заготовки;
- разработка средств технологического оснащения;
- расчет силовых и деформационных параметров корпуса 456.852.32 в процессе обработки с применением
- разработка технологии изготовления корпуса 456.852.32 в САПР ТП;
- разработка управляющей программы в ГеММа-3D;
- планировка участка для изготовления корпуса 456.852.32;
- расчет технико-экономических показателей участка.
В качестве прототипа для разработки технологического процесса принимается процесс используемый в производстве.
В условиях серийного производства имеется возможность сократить количество операций и уменьшить трудоёмкость изготовления деталей за счёт применения современного оборудования позволяющего производить обработку с более прогрессивными режимами резания.
6.doc
В процессе трудовой деятельности на человека могут воздействовать опасные производственные факторы которые приводят к травме или другому внезапному резкому ухудшению здоровья. К ним относятся: движущиеся машины и механизмы различные подъемно-транспортные устройства и перемещаемые грузы; незащищенные подвижные элементы производственного оборудования (приводные и передаточные механизмы режущие инструменты вращающиеся и перемещающиеся приспособления и др.) отлетающие частицы обрабатываемого материала и инструмента электрический ток повышенная температура поверхностей оборудования и обрабатываемых материалов и т.д. А также вредные производственные факторы которые приводят к заболеванию или снижению трудоспособности. Таковыми факторами являются: повышенная и пониженная температура воздуха рабочей зоны; высокие влажность и скорость движения воздуха; повышенные уровни шума вибрации. Также к вредным физическим факторам относятся запыленность и загазованность воздуха рабочей зоны; недостаточная освещенность рабочего места а также проходов и проездов; повышенная яркость света и пульсация светового потока.
Между вредными и опасными производственными факторами наблюдается определенная взаимосвязь. Во многих случаях наличие вредных факторов способствует проявлению травмоопасных факторов. Так чрезмерная влажность в производственном помещении и наличие токопроводящей пыли (вредные факторы) повышают опасность поражения человека электрическим током (опасный фактор).
Уровни воздействия на работающих вредных производственных факторов нормированы предельно-допустимыми уровнями значения которых указаны в соответствующих стандартах системы стандартов безопасности труда и санитарно-гигиенических правилах.
1 Техника безопасности
Оборудование устанавливается по операциям технологического процесса: фрезерный станок сверлильный станок токарный станок. После выполнения операции на одном станке заготовку перемещают на другой станок согласно технологического процесса. При перемещении груза необходима соблюдать правила техники безопасности. Минимальная ширина проходов для людей передвигающихся с грузом должен предусматриваться не менее 2 м без груза – не менее 1 м. Расстояния между станками и элементами здания а также ширина проходов выбраны согласно норм техники безопасности.
При работе на различного вида оборудования при выполнении разработанного технологического процесса необходимо соблюдать следующие требования техники безопасности:
Все открытые и вращающиеся части станков фрезерного FSS350R и сверлильного 2Н118 должны быть закрыты глухими кожухами плотно прикрепленными к станку. Основные требования к кожухам: прочность отсутствие шумообразования и простота конструкции.
Станки FSS350R и 2Н118 должны быть снабжены специальными устройствами полностью защищающими работающего от стружки искр осколков поломанного инструмента и брызг СОЖ. Для защиты от стружки кроме защитного экранов и щитков применяются очки. Большую роль играют современные методы борьбы со стружкой - поломкой ее и удалением из зоны резания.
На фрезерном станке FSS350R большую опасность представляет сама фреза. Эта опасность значительно уменьшается при наличии специального ограждения. Ограждение изготовляется в виде сварных или литых кожухов из стали или ковкого чугуна.
Для защиты станочников от поражения током все электрооборудование станков выполнено в защищенном исполнении. Для превращения замыкания фазы на корпус в однофазовое короткое замыкание оборудование занулено (на участке применяется четырехпроводная трехфазная сеть с заземленной нейтралью). В совокупности с использованием автоматов защиты от токов короткого замыкания это обеспечивает быстрое срабатывание последних.
На всех дверцах электрошкафов применяются предупредительные знаки в соответствии с требованиями ГОСТ 15508 – 70.
Работы по ремонту оборудования и механизмов производят только после полного отключения от сети электропитания с обязательным вывешиванием в местах отключения предупредительных табличек.
Перед каждым станком должен находиться деревянный настил который не позволяет переохлаждаться организму человека препятствует проникновению стружки в обувь и частично изолирует работающего.
Конструкция и расположение органов управления станком должна исключать возможность непроизвольного включения и выключения оборудования.
Конструкция пневматического приспособления должна обеспечивать предотвращение разжима и падания обрабатываемых деталей (самотормозящие элементы обратные клапана и т. д.).
Металлорежущий инструмент должен иметь определенную геометрию а также должны быть канавки предназначенные для скола стружки.
2 Производственная санитария и гигиена труда
Существенное влияние на здоровье людей оказывает микроклимат в производственном помещении предусматриваемый ГОСТ 12.1.005-76 категория тяжести труда. Для создания благоприятных условий труда следует постоянно контролировать микроклимат производственных помещений замеряя показатели температуры влажности и скорости движения воздуха.
Для холодного времени года оптимальные параметры:
-температура воздуха 18 20°С;
-относительная влажность 40 60%;
-скорость движения воздуха на рабочем месте 02мс.
Допустимые параметры соответственно:
-температура воздуха 17 23°С;
-относительная влажность не более 75%;
-скорость движения воздуха на рабочем месте 0Змс.
В теплый период года оптимальные параметры:
-температура воздуха 21 23°С;
- температура воздуха 18 27°С;
- относительная влажность не более 75%;
- скорость движения воздуха на рабочем месте 02 04 мс.
В соответствии с требованиями СНИП 11-38-75 двери и технические проемы механических цехов оборудованы воздушными завесами. С целью более эффективного улавливания пыли мелкой стружки применяется местное вытяжное устройство типа зонтов.
Для разбавления вредных веществ до их ПДК используется общеобменная вытяжная вентиляция.
Поддержание параметров микроклимата в заданных приделах обеспечивается главным образом за счет общеобменной приточно-вытяжной вентиляции а также естественной вентиляции осуществляемой аэрацией.
Свет на разработанном участке играет большую роль в сохранении здоровья и работоспособности человека. Для создания нормальных условий труда источники света в производственных помещениях должны достаточно и равномерно освещать рабочие места; не вызывать слепящего действия блесткости и излишней яркости в поле зрения работающего; не вызывать резких теней. Важное гигиеническое значение имеет рациональный выбор источников света. На участке должно предусматриваться естественное и искусственное освещение.
Для снижения шума и вибрации на участке по изготовлению корпусов 456.852.32 предусматриваются следующие требования:
-снижение вибрации в источнике возникновения;
-рациональная планировка наиболее шумное оборудование располагается в специальном месте;
-использование звукоизолирующих экранов и кожухов;
-использование индивидуальных средств защиты. К ним отнесены следующие устройства: оградительные виброизолирующие виброгасящие и вибропоглощающие (см. ГОСТ 12.4.011-75) а также средства автоматического контроля сигнализации дистанционного управления.
Важное значение имеет разработка и внедрение физиологически обоснованных режимов труда и отдыха лиц подвергающихся воздействию вибрации а также обеспечение их средствами индивидуальной защиты.
Для защиты рабочего от воздействия общей вибрации применяют обувь с амортизирующими подошвами.
Для борьбы с шумом на пути его распространения на участке устанавливают звукоизолирующие и звукопоглощающие конструкции а также глушители аэродинамических шумов.
3 Противопожарные мероприятия и средства пожаротушения
Причиной пожара могут стать искры возникающие при фрезеровании на FSS350R и обточке на 262ОГФ1 алюминиевого сплава твердыми сплавами на высоких скоростях а также промасленная ветошь в контейнерах пробой электропроводки и обмоток электродвигателей.
Для обеспечения безопасности работы на участке необходимо соблюдать следующие меры предупреждения пожаров:
Содержание в чистоте рабочих мест своевременно очищать от мусора и ветоши которые складываются в специальных металлических контейнерах закрывающихся крышкой.
Цех оснащен двумя эвакуационными выходами ширина путей эвакуации должна быть не менее 1 м а ширина дверей в путях – не менее 08 м высота прохода - не менее 2м.
Удаление дыма при пожаре предусматривается через аэрационные фонари.
В воздухе вентиляционной системы устанавливается огнепреградительные и быстродействующие заслонки.
Использование дымового пожарного извещателя ДИП – 1 действие которого основано на фотоэлектрическом принципе.
Для тушения пожара также использовать ручные углекислотные огнетушители ОУ – 5.
На участке расположены два пожарных гидранта.
Соответствующими приказами устанавливается порядок регулярного проведения с рабочими противопожарного инструктажа.
Успешное тушение пожара в значительной степени зависит от правильно организованной и надежно действующей связи и сигнализации.
4 Охрана окружающей среды
При обработке металлов резанием основную вредность для окружающей среды представляют: отработанная СОЖ и промывочная вода; твердые отходы - стружка; загрязненный в результате отделочных операций механической обработки воздух.
Во избежание загрязнения окружающей среды на участке предусмотрены следующие мероприятия:
Для улавливания крупных фракций частиц пыли применяют установки типа «циклоны». Механическая обработка на металлорежущих станках сопровождается выделением пыли стружки туманов масел и эмульсий которые через систему вентиляции выбрасываются из помещения в окружающую среду.
Для возможности повторного использования отработанной СОЖ и промывочной воды в условиях серийного производства предусмотрены отдельные замкнутые системы водоснабжения. Для разложения отработанной СОЖ используется метод электрокоагуляции. На основе полученной повторно воды изготавливают новую СОЖ а оставшуюся масляную составляющую сжигают в печах чугунолитейного производства. В целях экономии на заводе предусмотрена одна централизованная станция для разложения СОЖ.
Для очищения промывочной воды на участке предусмотрены отстойники и флотационные установки включенные в замкнутую цеховую оборотную систему.
Для недопущения загрязнения окружающей среды твердыми отходами (стружкой) предусматриваются следующие мероприятия:
-сбор стружки по территории цеха с последующим ее прессованием;
-последующая ее переработка.
Для переработки стружки предусматривается специальный участок что позволяет сократить затраты на погрузочно-разгрузочные работы снижает безвозвратные потери при их переплавке и транспортировке и высвобождает транспортные средства.
Стружку которая образуется при обработке деталей корпус 456.852.32 собирают и перерабатывают на стружко-дробилках брикетировочных прессах.
Регулярный плановый ремонт станков на участке исключает не предусмотренное конструкцией трение а регулярная чистка смазка замена выработавших свой срок узлов снизит количество твердых отходов в целом.
Доклад.doc
Уважаемые члены Государственной аттестационной комиссии!
Темой дипломного проекта является: «Разработка технологии и средств технологического оснащения для изготовления корпуса 456.852.32». Цели и задачи дипломного проектирования представлены на плакате 1.
Корпус 456.852.32 входит в состав механизма ручной червячной тали изображенной на плакате 2. Тали предназначены для подъема опускания и горизонтального перемещения груза подвешенного на крюковой подвеске. Отличительным признаком тали является компактность. Подъемный механизм приводится в движение вручную с помощью звездочек. Особенности механизма: кованные подвесной и грузовой крюки; повышенный запас прочности; высокая стойкость к механическим повреждениям.
На листе представлен рабочий чертеж корпуса червячной тали. Он служит для соединения между собой деталей которые смонтированы в нем с требуемой точностью относительного положения как в статическом состоянии так и в процессе эксплуатации машины. Материалом для его изготовления является алюминиевый сплав АК7.
Система трехмерного твердотельного моделирования предназначена для создания трехмерных моделей с целью сокращения периода проектирования. На листе 4 представлена твердотельная модель корпуса 456.852.32 и выборочные операции дерева построения.
На листе 5 представлены расчеты выполненные в COSMOSXpress: рассчитаны эпюры: эпюра 1 – узловое напряжение отражающее максимальное и минимальное узловое перемещение; эпюра 2 – статическое перемещение отражающая нагрузки в различных направлениях: максимальное и минимальное статическое перемещение; эпюра 3 – деформационная форма – отражает способ изменения модели; эпюра 4 – проверка проектирования – отражает коэффициент запаса прочности детали.
Методом получения заготовки был выбран – литье под давлением. Этим способом получают фасонные отливки из цинковых алюминиевых магниевых и латунных сплавов. Этот метод обеспечивает нужную точность и шероховатость поверхности заготовки а также меньшую технологическую себестоимость изготовления заготовки. Чертеж заготовки представлен на листе 6.
Разработка технологии в КОМПАС – АВТОПРОЕКТ Технология позволяет очищать текущую технологию создавать операции переходы выбирать режущий и измерительный инструмент из баз данных рассчитывать режимы резания а также формировать карты: операционную маршрутную и карту эскизов. На листе 7 представлена разработка технологии в КОМПАС-АВТОПРОЕКТ.
На листе 8 представлены выборочные операции разработанного технологического процесса изготовления корпуса 456.852.32.
Система ГеММа-3D предназначена для разработки управляющих программ при изготовлении деталей высокой сложности на всех типах станков с ЧПУ. Она повышает производительность труда ведет к увеличению результатов труда инженера. На листе 9 представлена программа для обработки корпуса 456.852.32.
Для выполнения расточной операции разработана конструкция установочного приспособления с пневматическим приводом представленная на листе 10. Базирование осуществляется на поверхность и два пальца (цилиндрический и срезанный). Зажим осуществляется прихватами. Обеспечивается быстрое и надежное закрепление детали.
Для контроля перпендикулярности отверстия относительно плоскости корпуса 456.852.32 разработана конструкция специального контрольного приспособления представленная на листе 11.
В научно-исследовательской части выбраны оборудование инструмент и режимы обработки для электрохимического маркирования. Был проведен анализ влияния электрохимического маркирования на эксплуатационные характеристики детали. Результаты представлены на плакате 12.
В соответствии со структурой технологического процесса выполнена технологическая планировка производственного участка представленная на листе 13. Количество и порядок расстановки станков соответствуют годовой производственной программе.
Расчетный интегральный экономический эффект разработки составил 2741634 тыс.р. на расчетную программу выпуска при уменьшении себестоимости детали на 986% и сроке окупаемости 357 года (Лист 14).
Спасибо за внимание доклад окончен.
программа.cdw

цели и задачи.cdw

оснащения для изготовления корпуса 456.852.32
совершенствование операционного технологического процесса
изготовления корпуса 456.852.32
- выбор и обоснование метода получения заготовки;
- разработка средств технологического оснащения;
- расчет силовых и деформационных параметров
корпуса 456.852.32 в процессе обработки с применением
- разработка технологии изготовления корпуса 456.852.32 в САПР ТП;
- разработка управляющей программы в ГеММа-3D;
- планировка участка для изготовления корпуса 456.852.32;
- расчет технико-экономических показателей участка.
CAE.cdw

для изготовления корпуса 456.852.32
Результаты расчета корпуса 456.852.32
Результаты расчета корпуса 456.852.32 в COSMOSXpress
Эпюра 1 - Статическое узловое напряжение
Эпюра 3 - Деформированная форма
Эпюра 2- Статическое перемещение
Эпюра 4 - Проверка проектирования
Технико-экономические показатели участка.cdw

по изготовлению корпуса 456.852.32
Наименование показателя Величина
Абсолютные показатели:
а) годовой выпуск продукции
- в натуральном выражении
- в стоимостном выражении
б) количество единиц технологического оборудования
в) общая стоимость основных производственных
г) Производственная площадь участка
д) Численность основных рабочих участка
е) фонд заработной платы основных рабочих
Относительные показатели:
а) Выпуск продукции на одного производственного
рабочего в денежном выражении
( по цеховой себестоимости )
б) выпуск продукции на кв.м. производственной
в) фондоотдача ( по цеховой себестоимости )
г) средняя загрузка оборудования
д) фондовооружённость труда
е) уровень механизации труда
Показатели экономической эффективности проекта
а) интегральный экономический эффект
б) внутренняя норма доходности ( внутренний
коэффициент эффективности )
в) срок окупаемости капитальных вложений
г) снижение себестоимости изготовления детали
д) снижение трудоёмкости изготовления детали
е) условное высвобождение численности рабочих
автопроект.cdw

Выбор режущего инструмента
из справочника КОМПАС-Автопроект
Разработка технологии и средств технологического оснащения
для изготовления корпуса 456.852.32
Разработка маршрута операций
технологического процесса
обработки детали в САПР ТП
Разработка маршрута операций технологического процесса обработки детали в САПР ТП
Формирование перехода
Сквозной технологический процесс
модель.cdw

оснащения для изготовления корпуса 456.852.32
Твердотельная модель
Твердотельная модель корпуса 456.852.32 и выборочные операции дерева построения
Рекомендуемые чертежи
- 24.01.2023
- 24.01.2023
- 24.01.2023
- 31.05.2020
- 24.01.2023
Свободное скачивание на сегодня
- 24.01.2023