Разработка технологического процесса детали


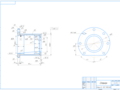
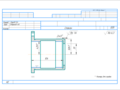
- Добавлен: 24.01.2023
- Размер: 3 MB
- Закачек: 0
Узнать, как скачать этот материал
Подписаться на ежедневные обновления каталога:
Описание
Разработка технологического процесса детали
Состав проекта
![]() |
![]() |
![]() ![]() ![]() |
![]() ![]() ![]() |
![]() ![]() ![]() |
![]() |
![]() ![]() |
![]() ![]() |
![]() ![]() |
![]() ![]() |
![]() ![]() |
![]() ![]() |
![]() ![]() |
![]() ![]() |
![]() ![]() ![]() |
![]() |
![]() ![]() ![]() |
![]() ![]() ![]() |
![]() |
![]() ![]() ![]() |
![]() ![]() ![]() ![]() |
![]() ![]() ![]() |
![]() ![]() ![]() ![]() |
![]() |
![]() ![]() ![]() |
![]() |
![]() |
![]() ![]() ![]() |
![]() ![]() |
![]() |
![]() ![]() ![]() |
Дополнительная информация
Контент чертежей
Деталь.cdw

КЭ.cdw

Рекомендуемые чертежи
- 24.01.2023
- 13.12.2022
- 24.01.2023
- 24.01.2023
Свободное скачивание на сегодня
Обновление через: 6 часов 11 минут
- 22.08.2014
- 29.08.2014