Разработка методики испытаний на соответствие нормам геометрической точности и жесткости, точности позиционирования для следящего привода токарного станка


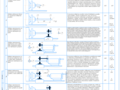

- Добавлен: 25.01.2023
- Размер: 303 KB
- Закачек: 0
Узнать, как скачать этот материал
Подписаться на ежедневные обновления каталога:
Описание
Разработка методики испытаний на соответствие нормам геометрической точности и жесткости, точности позиционирования для следящего привода токарного станка
Состав проекта
![]() |
![]() |
![]() ![]() ![]() |
![]() ![]() ![]() ![]() |
![]() ![]() ![]() ![]() |
Дополнительная информация
Контент чертежей
1 лист испыт.cdw

2-й лист.cdw

Рекомендуемые чертежи
- 29.05.2022
Свободное скачивание на сегодня
Обновление через: 8 часов 59 минут