Расчёт и проектирование привода конвейера (Шеврон)




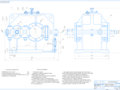
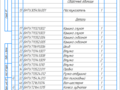
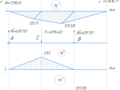
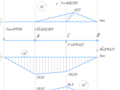
- Добавлен: 24.01.2023
- Размер: 4 MB
- Закачек: 0
Описание
Расчёт и проектирование привода конвейера (Шеврон)
Состав проекта
![]() |
![]() |
![]() ![]() ![]() ![]() |
![]() ![]() ![]() |
![]() |
![]() ![]() ![]() |
![]() |
![]() ![]() ![]() |
![]() |
![]() |
![]() |
![]() |
![]() ![]() ![]() |
![]() ![]() ![]() |
![]() |
![]() |
![]() ![]() ![]() |
![]() |
![]() |
![]() ![]() ![]() |
![]() |
![]() |
![]() ![]() ![]() ![]() |
![]() |
![]() |
![]() |
![]() |
![]() |
![]() |
![]() ![]() ![]() ![]() |
![]() ![]() ![]() ![]() |
![]() ![]() ![]() |
![]() |
![]() ![]() ![]() |
![]() |
![]() |
![]() ![]() ![]() |
![]() ![]() ![]() ![]() |
![]() |
![]() |
![]() ![]() ![]() |
Дополнительная информация
Чертеж лист2.cdw

эпюры ведущий вал.frw

силы в зацеплении.frw

схема нагружения подш ведущ.frw

схема нагружения подш ведом.frw

Фрагмент.frw

Спецификация.spw

Чертеж лист 1.cdw

Деталировка Вал.cdw

деталировка колесо.cdw

эпюры ведомый вал.frw

Рекомендуемые чертежи
- 24.01.2023
- 24.01.2023