Расчет и проектирование привода ленточного конвейера




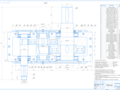
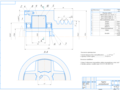
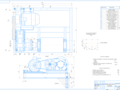
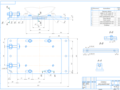
- Добавлен: 24.01.2023
- Размер: 1 MB
- Закачек: 1
Описание
Состав проекта
![]() |
![]() |
![]() ![]() ![]() |
![]() ![]() ![]() ![]() |
![]() ![]() ![]() ![]() |
![]() ![]() ![]() ![]() |
![]() ![]() ![]() ![]() |
![]() ![]() ![]() ![]() |
Дополнительная информация
Лист4(А2).cdw

Лист1(А1).cdw

Лист2(А1).cdw

Лист5(А2).cdw

Лист3(А1).cdw

Рекомендуемые чертежи
- 24.01.2023
- 24.01.2023
- 24.01.2023