Расчет привода ленточного конвейера




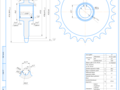
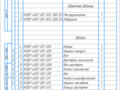
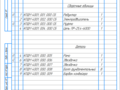
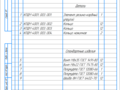
- Добавлен: 24.01.2023
- Размер: 1 MB
- Закачек: 0
Описание
Расчет привода ленточного конвейера
Состав проекта
![]() |
![]() |
![]() ![]() ![]() |
![]() |
![]() ![]() ![]() ![]() |
![]() ![]() ![]() ![]() |
![]() ![]() ![]() ![]() |
![]() ![]() ![]() ![]() |
![]() ![]() ![]() ![]() |
![]() ![]() ![]() ![]() |
![]() ![]() ![]() ![]() |
![]() ![]() ![]() ![]() |
![]() ![]() ![]() ![]() |
![]() ![]() ![]() ![]() |
![]() ![]() ![]() ![]() |
![]() |
![]() ![]() ![]() ![]() |
![]() ![]() ![]() ![]() |
![]() ![]() ![]() ![]() |
![]() ![]() ![]() ![]() |
![]() ![]() ![]() ![]() |
![]() ![]() ![]() ![]() |
![]() ![]() ![]() ![]() |
![]() ![]() ![]() ![]() |
![]() |
![]() ![]() ![]() ![]() |
Дополнительная информация
ДМ1.cdw

быстр. вал.cdw

крышка зак.cdw

звездочка.cdw

вал шестерня.cdw

кон.шестер..cdw

муфта..spw

кон.колесо.cdw

ред.кон.цил..spw

шестерня цилиндрическая.cdw

Вал тихоходный.cdw

привод конвейера.spw

редуктор.cdw

стакан.cdw

основание ред..cdw

общий вид ред.cdw

Крышка ред..cdw

крышка подшипника.cdw

муфта.cdw

крышка.cdw

Рекомендуемые чертежи
- 24.01.2023
- 24.01.2023