Расчет привода ленточного конвейера, с применением клиноременной передачи и одноступенчатым цилиндрическим редуктором


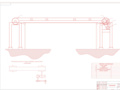
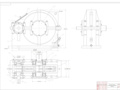
- Добавлен: 24.01.2023
- Размер: 517 KB
- Закачек: 0
Подписаться на ежедневные обновления каталога:
Описание
Расчет привода ленточного конвейера, с применением клиноременной передачи и одноступенчатым цилиндрическим редуктором
Состав проекта
![]() |
![]() ![]() ![]() ![]() |
![]() ![]() ![]() |
![]() ![]() ![]() ![]() |
Дополнительная информация
Контент чертежей
одноступцилиндрредуктор.dwg

пояснительная записка.docx
Кинематический расчёт
Выбор электродвигателя
Передаточное отношение привода и его передач
Частоты вращения угловые скорости мощности и моменты на валах привода
Расчёт цилиндрической зубчатой передачи редуктора
Материалы зубчатых колес и допускаемые напряжения
Расчёт геометрических параметров зубчатой передачи
Проверочный расчёт прочности зубьев цилиндрической передачи
Расчёт ременной передачи
Исходные данные для расчета
Сечение ремня диаметры шкивов
Межосевое расстояние длина ремня
Количество ремней в передаче
Предварительное натяжение ремня действующая нагрузка на валы ширина шкивов
Нормы для контроля предварительного натяжения ремня
Расчет шпоночных соединений
Конструктивные размеры редуктора
Спроектировать привод ленточного конвейера содержащий: асинхронный электродвигатель клиноременную передачу одноступенчатый редуктор с прямозубыми цилиндрическими колесами и компенсирующей муфтой по схеме 4 варианту 6. Схема привода дана на рисунке 1.1
Рисунок 1.1 – Схема привода
- электродвигатель; 2- ремень клиновой; 3- одноступенчатый редуктор ( прямозубый) ; 4- муфта компенсирующая; 5- барабан; 6- лента конвейера.
Срок службы редуктора десять лет при непрерывной двухсменной работе.
Кратковременные перегрузки превышают номинальную нагрузку не более чем в два раза.
Мощность передаваемая муфтой на вал конвейера Р3=336 кВт.
Кинематический и силовой расчет привода
1. Выбор электродвигателя
1.1 Требуемая мощность электродвигателя
где Р3 - мощность на барабане (на выходе привода) кВТ;
где 1 2подш- соответственно КПД ременной зубчатой передач и пары подшипников качения.
Руководствуясь рекомендациями 2с.5 принимаем р=096 з=098 подш=099.
После подстановки численных значений параметров в формулы (2.2) и (2.1) получим КПД привода
и требуемую мощность
1.2 С учетом требуемой мощности Ртр=365 кВт рассмотрим возможность выбора асинхронных двигателей серии 4А с номинальными мощностями Рн=30 кВт и Рн=40 кВт 2с.390. Для первого перегрузка составляет (383-3)100%3=276% при допускаемой перегрузке 5%.
Остановим выбор на двигателе мощностью 4 кВт.
Для двигателей с мощностью 4 кВт рассчитаны следующие номинальные частоты вращения nн:2880 1430 950 720 обмин.
Для ориентировки в выборе двигателя по частоте вращения оценим передаточное отношение привода iср вычисленное по средним значениям рекомендуемых передаточных отношений отдельных передач.
iср=i1*i2 iср=1.8*4 iср=7.2
При таком передаточном отношении привода и частоте вращения вала n3=95 обмин потребуется двигатель с частотой вращения n1=iсрn3=95*7.2=684 обмин.
1.3 Окончательно выбираем 2с.390 ближайший по частоте вращения асинхронный электродвигатель марки 132S8 со следующими параметрами:
- номинальная мощность Рн=4кВт;
- номинальная частота вращения nн=750 обмин;
- отношение пускового момента к номинальному ТnTн=1.8 .
2. Передаточное отношение привода и отдельных его передач
Общее передаточное отношение привода при частоте вращения его входного вала
Примем 2с.6 передаточные отношения – для ременной зубчатой и цепной передач редуктора соответственно iр=18 iзуб= 4
3. Частоты вращения угловые скорости мощности и моменты на валах
3.1. Частоты вращения валов:
3.2. Угловые скорости валов:
3.3. Мощности на валах привода:
Р2 = Р1 р п = 365 096 099 = 346 кВт;
Р3 = Р2 з п = 346 098 099 = 335 кВт;
3.4. Моменты на валах привода:
Таблица 2.1-Частоты вращения угловые скорости мощности и моменты на валах привода
1 Материалы зубчатых колес и допускаемые напряжения
1.1 Назначим дешёвую углеродистую качественную конструкционную сталь 45 по ГОСТ 1050 – 88. После улучшения (закалка и высокий отпуск до окончательной обработки резанием) материал колёс должен иметь нижеследующие механические свойства
Твёрдость НВ 230 260 НВ 200 225
Предел текучести т не менее 440 МПа 400 МПа
Предел прочности в не менее 750 МПа 690 МПа
1.2 Допускаемые контактные напряжения при расчете зубьев на выносливость в общем случае:
КHL – коэффициент долговечности;
[SH] – коэффициент безопасности.
Для стальных колес с твердостью менее НВ 350
Коэффициент долговечности 2с.33
где NНО – базовое число циклов;
NНЕ – эквивалентное число циклов перемены напряжений.
Для стали с твердостью НВ 200 базовое число циклов NНО = 107
Эквивалентное число циклов
NНЕ = 60 с n t (3.4)
где с – число зубчатых колес сцепляющихся с данным колесом;
n – частота вращения этого колеса обмин;
t – срок службы передачи в часах.
Для шестерни и для колеса с = 1 n2 = 2057 обмин =6997 обмин. По заданию на расчетную работу срок службы составляет 10 лет при двухсменной работе. Приняв число рабочих дней в году 250 а продолжительность смены 8 часов получим t=1022508=40000 часов.
Расчет по формуле (3.4) дает для шестерни и колеса соответственно
Без вычислений по формуле (3.3) видно что коэффициент долговечности для каждого из колес окажется меньше единицы так как > и >. В таком случае следует принимать=1.
Если взять коэффициент безопасности [SH]=115 2 с.33 то расчет по формулам (3.1) и (3.2) даст допускаемые контактные напряжения для шестерни и колеса соответственно:
1.3 Допускаемое контактное напряжение при кратковременных перегрузках для колес из нормализованной улучшенной и объемно закаленной стали зависит от предела текучести и вычисляется по формуле
где =400 МПа – предел текучести (минимальное значение для колеса по пункту 3.1.1)
1.4 Допускаемые напряжения изгиба при проверочном расчете зубьев на выносливость вычисляется по формуле
КFL – коэффициент долговечности при расчете зубьев на изгиб;
КF – коэффициент учитывающий влияние двустороннего приложения
нагрузки на зубья ( в случае реверсивной передачи);
[SF] – допускаемый коэффициент безопасности (запаса прочности).
По рекомендации берем:
– для нормализованных и улучшенных сталей F l
– при одностороннем нагружении зубьев принимая привод не реверсивным КFC =1;
– для стальных поковок и штамповок при твердости менее НВ 350 [SF] =175.
Коэффициент долговечности
где m – показатель корня;
NFO – базовое число циклов;
NFE – эквивалентное число циклов.
Для колес с твердостью зубьев до и более НВ 350 величина m равна соответственно 6 и 9. Для всех сталей принимается NFO = 4 106.
Для обоих колес NFE имеет те же численные значения что и NНE .Оба эти значения (для шестерни -70107 для колеса 21107) больше NFO= 4 106. Поэтому принимается коэффициент долговечности КFL=1.
Расчет по формуле (3.7) дает соответственно для шестерни и колеса
Примечание – Здесь как и при расчете [Н] взято минимальное значение твердости.
1.5 Допускаемое напряжение изгиба при расчете зубьев на кратковременные перегрузки при твердости менее НВ 350
Расчет по этой формуле с учетом характеристик материала ( см. пункт 3.1.1) дает для шестерни и колеса соответственно
2 Расчёт геометрических параметров зубчатой передачи
Межосевое расстояние цилиндрической зубчатой передачи из условия контактной выносливости активных поверхностей зубьев
где – коэффициент равный 495 и 43 для прямозубых и косозубых колёс соответственно;
u – передаточное число зубчатой пары;
Т2=Т3 – момент на колесе (большем из колёс);
– коэффициент учитывающий неравномерность распределения
нагрузки по ширине венца;
– допускаемое контактное напряжение МПа;
– коэффициент ширины венца по межосевому расстоянию.
Передаточное число u=
Допускаемое напряжение =408 МПа;
Коэффициент ширины венца по межосевому расстоянию
Каждое из колес разделенной передачи расположено симметрично относительно опор для этого случая примем пока ориентировочно
В итоге расчет по формуле (3.10) дает
Межосевое расстояние округляем до стандартного значения 200 мм
Нормальный модуль mn = (001 002) = (001 002) 200 = 2 4 мм. Из стандартного числа модулей берем mn= 4 мм.
Предварительно принимаем угол наклона зубьев = 0
Тогда число зубьев шестерни:
Тогда число зубьев колеса Z2 = Z1u = 204 = 80
Уточненное значение:
Делительные диаметры шестерни и колеса соответственно:
Правильность вычислений подтверждается проверка:
Диаметры вершин зубьев шестерни и колеса:
Диаметры впадин зубьев
b2 = ba = 025200 = 50 мм
b1 = b2+5 = 50+5 = 55 мм
Коэффициент ширины шестерни по диаметру:
bd2 = b2:d2 = 55:80 = 0.69
3. Проверочный расчёт прочности зубьев цилиндрической передачи
3.1. Расчётное контактное напряжение для цилиндрических передач
где KH – коэффициент нагрузки;
b – ширина колеса расчётная (наименьшая).
Окружная скорость колёс
При такой скорости назначаем восьмую степень точности.
Коэффициент нагрузки при проверочном расчёте на контактную прочность
где – коэффициент учитывающий неравномерность распределения нагрузки между зубьями;
– коэффициент учитывающий неравномерность распределения нагрузки по длине зуба;
– коэффициент учитывающий дополнительные динамические нагрузки.
По рекомендациям назначаем следующие значения коэффициентов:
– = 10 при окружной скорости =167 мс и восьмой степени точности;
– = 109 при значении коэффициента =069 твёрдости зубьев менее НВ 350 и симметричном расположении относительно опор;
– = 1 при окружной скорости =167 мс восьмой степени точности и твердости менее НВ 350.
Расчет по формуле (3.12) дает .
Ширину колеса берем в расчет минимальную и суммарную для обоих колес т.е. в=80. Момент на колесе Т2= 320 Нм.
Расчет по формуле (3.11) дает
Условие прочности выполняется.
3.3 Напряжение изгиба зубьев цилиндрических колёс при проверочном расчёте на выносливость вычисляются по формуле
где Ft – окружная сила;
KF – коэффициент нагрузки;
YF – коэффициент формы зуба;
Y – коэффициент компенсирующий погрешности возникающие из-за
применения для косых зубьев той же расчётной схемы что и для
KFA – коэффициент учитывающий неравномерность распределения на
грузки между зубьями;
b – ширина колеса находящаяся в зацеплении мм;
– модуль нормальный мм;
В зацеплении колёс быстроходной передачи действуют следующие силы:
Коэффициент нагрузки
где – коэффициент учитывающий неравномерность распределения нагрузки по длине зубьев;
Примем =110 с учетом что твердость колес менее НВ 350 коэффициент а каждое из колес расположено симметрично относительно опор.
Назначим =115 учитывая дополнительно что окружная скорость =167 мс а степень точности принята 8.
Тогда по формуле (3.14) =110·115=1265
Без расчётов руководствуясь только рекомендацией возьмём КFA=092.
Коэффициент Y определим по формуле :
Коэффициент формы зуба для прямозубых колес зависит от эквивалентного числа зубьевкоторое составляет
для шестерни и колеса соответственно
Допускаемое напряжение
По табл. 3.9 для стали 45 улучшенной при твердости ≤ HB350
коэффициент запаса прочности
Расчет по формуле (3.13) дает для шестерни и колеса соответственно (в МПа):
Это значительно меньше вычисленных в пункте 3.1.4 допускаемых напряжений =237 МПа и =206 МПа.
Таблица 3.1 – Геометрические параметры колес зубчатой передачи
Межосевое расстояние мм
Нормальный модуль мм
Угол наклона зубьев град
Делительные диаметры мм
Диаметры вершин зубьев мм
Диаметры впадин зубьев мм
Ширина венцов колёс мм
Расчет ременной передачи
1 Исходные данные для расчета
– передаваемая мощность P1=365кВт;
– частота вращения ведущего шкива n1 = nдв =719 обмин ;
– передаточное отношение = 18;
– момент на ведущем шкиве T1=4850 Н·м ;
– относительное скольжение ремня =0015 возьмем по рекомендации
2 Сечение ремня диаметры шкивов.
В зависимости от частоты вращения малого шкива и передаваемой мощности выбираем по номограмме ремень сечения Б.
Диаметр меньшего шкива :
Принимаем диаметр d1=140 мм.
Диаметр большего шкива :
Принимаем стандартную величину мм
3 Межосевое расстояние длина ремня
Литература рекомендует принимать межосевое расстояние в интервале
где Т0 – высота сечения ремня в мм.
Для ремня типа Б T0=105 мм .
Расчет по формулам (4.1) дает:
Принимаем предварительно межосевое расстояние передачи а`р= 300 мм.
Соответствующая принятому межосевому расстоянию расчетная длина ремня
Ближайшая стандартная длина ремня L=1250 мм . Соответствующее ей уточненное межосевое расстояние
После подстановки получаем:
При конструировании передачи следует обеспечить возможность уменьшения межосевого расстояния на 001L=001×314=314 мм для свободного надевания ремней на шкивы а также возможность увеличения его на 0025×L=0025×314 = 785 мм для регулировки предварительного натяжения ремней. Прибавим в качестве резерва к этим цифрам соответственно 4 и 10 мм. Тогда при окончательном обоснованном межосевом расстоянии 314 мм в конструкции должна предусматриваться возможность его изменения от плюс 55 до минус 22 мм.
4 Количество ремней в передаче
Количество ремней вычисляется по формуле (2 с. 135)
где P – мощность передаваемая ременной передачей кВт;
Сp – коэффициент режима работы;
Po – мощность допускаемая для передачи одним ремнем кВт;
СL – коэффициент учитывающий влияние длины ремня;
Сa – коэффициент учитывающий влияние угла охвата меньшего шкива;
Cz – коэффициент учитывающий число ремней в передаче.
Передаваемая мощность P= P1=365кВт (см. пункт 2.1.1).
Коэффициент режима работы Cp=13 при двухсменной работе и кратковременных перегрузках составляющих 200% от номинальной нагрузки .
Коэффициент СL=095 для ремня с сечением Б и длиной L=3150 мм.
Коэффициент Cz = 090 принят в предположении что число ремней составит 3-4.
Для выбора коэффициента Сa найдем сначала угол охвата меньшего шкива
При таком значении a следует принять Сa=082.
Расчет по формуле (4.3) дает
Окончательно принимаем число ремней z=3.
5 Предварительное натяжение ремня нагрузка действующая на валы ширина шкивов
5.1 Предварительное натяжение ветвей одного клинового ремня вычисляется по формуле
где u – скорость ремня мс;
– коэффициент учитывающий влияние центробежной силы.
Скорость ремня мc. Значение =018 принимаем по рекомендации.
Расчет по формуле (4.4) дает
5.2 Нагрузка от натяжения всех ремней действующая на валы
5.3 Ширина обода шкива в мм
где е – расстояние между канавками на ободе мм;
f – расстояния от середины крайних канавок до краев обода мм.
Расчет по формуле (4.5) при е=19 мм и f =125 мм дает
6 Нормы для контроля предварительного натяжения ремня
Предварительное натяжение ремня Fo при сборке передачи и во время ее эксплуатации контролируют обычно не непосредственно а косвенно измеряя стрелу прогиба ремня b под определенной нагрузкой G приложенной перпендикулярно к ремню в середине ветви как показано на рисунке 5.1 .
Зависимость между Fo b и G для передачи по схеме рисунка 4.1 выражается формулой
где Е – модуль упругости ремня Нмм2;
А – площадь сечения ремня мм2.
Зададимся стрелой прогиба b = 50 мм. Для ремня типа Б величина = 250000 Н.
Рисунок 5.1 – Иллюстрация контроля предварительного натяжения ремня
По формуле (5.6) после ее преобразования вычислим
Окончательно принимаем b =501 мм G = 423Н.
Предварительный расчет валов
Минимальный диаметр вала в миллиметрах при этом расчете на чистое кручение определяется по формуле
где Т-крутящий момент на валуНм;
[к]- допускаемое напряжение при крученииМПа.
Крутящие моменты для валов от 1 до 4 определены в пункте 2.3.4.
Валы 34 испытывают дополнительные консольные нагрузки от ременной и цепной передач соответственно. Поэтому для этих валов возьмем допускаемое напряжение [к]=20 МПа. Для валов 12которые таких нагрузок не испытываютвозьмем большую величину [к]=25 МПа.
Расчет диаметров валов и их длины на шестерне и колесе :
Ступень вала и ее размеры dl
d2=d1+2t=21+225=26 мм
d2=d1+2t=27+228=33мм
l2=125 d2=12533=41мм
d3= d2+32r=26+322534 мм
d3= d2+32r=33+323=42мм
Для всех валов предусматриваем шпонки призматические по ГОСТ 23360-78 со скругленными торцами. Материал шпонок- сталь 45 по ГОСТ 1050-88 нормализованная. Сечения шпонок и их рекомендуемое соответствие диаметрам валов берем по 2с.169
Условие прочности соединения по напряжениям смятия 2с.169-171
где Т- моментпередаваемый соединениемНм
Сечение шпонки bh мм выбираем по диаметру валаа необходимую по условию прочности длину l вычисляем по преобразованной формуле:
Детали шпоночных соединений редуктора стальные поэтому берем для них с учетом кратковременных перегрузок допускаемое напряжение смятия =70 МПа.
Ведущий вал редуктора запроектирован как вал-шестерня. Его шпоночное соединение расположено на диаметре d=35 мм для которого b×h=10×8 мм t1=5 мм. Момент на валу Т2=16907 Нм.
Тихоходный вал редуктора имеет минимальный диаметр d=50 мм передаваемый валом момент Т=48224 Нм. При сечении шпонки b×h=16×10 ммt1=6 мм ее длина по формуле
Длина шпонки на при диаметре d=65 мм b×h=20×12 мм t1=75 мм
Размеры определяем исходя из конструктивных соображений. Принимаем подшипники средней серии по ГОСТ 8338-75 №308 d×D×B=40×90×23 мм.
Размеры определяем исходя из конструктивных соображений. Принимаем подшипники легкой серии по ГОСТ 8338-75 №312 d×D×B=60×130×31 мм.
Определяется в основном технологическими эксплуатационными и эстетическими условиями с учетом его прочности и жесткости.
Габаритные размеры корпуса определяются размерами расположенной в корпусе редукторной пары и кинематической схемой редуктора.
Толщина стенок корпуса и ребер жесткости
где Т2- вращающий момент на тихоходном валу Нм.
Внутренний контур стенок корпуса очерчивается по всему периметру корпуса с учетом зазоров х и у между контуром и вращающимися деталями.
2 Диаметры болтов соединяющих основание и крышку корпуса.
d=(0030036)*а+12=(0030036)*200+12=18 мм.
3 Диаметр винтов крепящих крышку.
d1=(07075)*d=(07075)*12=1415 мм.
Принимаем болты М16.
Для редуктора предусматривается картерная система смазки. Колеса ступени погружены в масло максимально на 20 мм. Это вдвое превышает минимально рекомендуемую нору4с.42 но зато допускает работу редуктора при возможном в эксплуатации снижения уровня масла на 10 мм. Интервал уровней должен быть учтен при конструировании жезлового маслоуказателя.
Колесо тихоходной ступени погружено в масло примерно на 100 мм. Это вынужденное решение связано с большими размерами колеса.
Для подшипников предусмотрено смазывание маслом разбрызгивается на стенки корпуса и затем стекая вниз попадает в подшипники.
Для заливки масла и вентиляции редуктора на верхней части корпуса (крышке) предусмотрена пробка-отдушина а в нижней части- сливная пробка.
Объем масляной ванны составляет около 16 л.
Для уплотнения зазоров между валами и проходными крышками подшипников предусмотрены стандартные резиновые манжеты которые запрессовываются в крышки.
Все крышки подшипников уплотняются относительно корпуса картонными прокладками смазанными герметиком. Разъем корпуса также уплотняется герметиком.
Вязкость масла выбирается в зависимости от окружной скорости и контактных напряжений зубчатых колес.
В соответствии с рекомендациями выбирается масло индустриальное с присадками ИРП-150 по ТУ38-101451-78. Его вязкость 140 160 сСт при 500С.
Сначала собираются валы и сопряженные с ними детали (шпонки зубчатые колеса распорные втулки подшипники и др.)предусмотренные чертежом. Способ сборки зависит от характера соединения.
Основание корпуса устанавливается на сборочный стенд и валы в сборе укладываются подшипниками в постели основания. Фланец основания корпуса смазывается герметиком затем на него укладываются своим фланцем крышка корпуса которая фиксируется штифтами и закрепляется болтами с пружинными шайбами.
В проходные крышки запрессовываются манжеты и все крышки вместе с уплотнительными прокладками которые смазываются герметиком устанавливаются на свои места и крепятся болтами с пружинными шайбами.
Снаружи на корпус устанавливаются все детали предусмотренные чертежом и на этом сборка заканчивается.
Затем в редуктор заливается масло он устанавливается на стенд и обкатывается без нагрузки по 10 минут в каждую сторону. При обкатке не должно быть повышенного шума и течи уплотнений.
После обкатки масло заменяется все поверхности редуктора кроме обработанных окрашиваются производится консервация упаковка и заполнение паспорта.
На предприятии собирающем привод на валы редуктора устанавливаются шпонки насаживаются с помощью спец. приспособлений шкив и звездока и фиксируются деталями предусмотренными чертежом. На вал электродвигателя насаживается ведущий шкив.
Затем редуктор соединяется с рамой посредством болтов с пружинными шайбами. Электродвигатель со шкивом устанавливается на свое место на шкивы одеваются ремни устанавливаются все крепежные детали двигателя и производится регулировка взаимного положения шкивов и предварительного натяжения ремней. Нормы на эту регулировку указываются в технических требованиях чертежа привода. После регулировки электродвигатель окончательно крепится к раме.
Электродвигатель собранного привода подключается к электросети и привод обкатывается без нагрузки по 5 минут в каждую сторону. При этом не должно быть повышенного шума течи уплотнений и других дефектов.
После обкатки следует консервация упаковка оформление документов и отправка привода заказчику.
Жингаровский А. Н. Кейн Е. И. Коновалов М. Н. Задания к расчетным работам по теории механизмов и машин: Методические указания. – Ухта: УГТУ 2008. – 37с ил.
Курсовое проектирование деталей машин: учебное пособие для учащихся Машиностроительных специальностей техникумов С.А. Чернавский К.Н. Боков И.М. Чернин и др. 2-е изд. перераб. и доп. – М.: Машиностроение 1988. – 416 с.
Гузенков П.Г. Детали машин: Учеб. пособие для студентов вузов П.Г. Гузенков– 3-е изд. перераб. и доп. – М.: Высш. школа 1982.–351 с.
общий вид привода.dwg

Привод ленточного конвейера Чертеж общего вида
Краткая спецификация
цилиндрический гор. редуктор
Рекомендуемые чертежи
- 24.01.2023
- 24.01.2023
- 18.12.2020
Свободное скачивание на сегодня
Обновление через: 2 часа 58 минут