Проектирование привода с одноступенчатым горизонтальным цилиндрическим косозубым редуктором и клиноременной передачей. Вариант 12



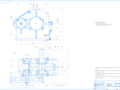
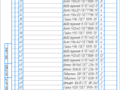
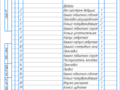
- Добавлен: 24.01.2023
- Размер: 2 MB
- Закачек: 0
Описание
Проектирование привода с одноступенчатым горизонтальным цилиндрическим косозубым редуктором и клиноременной передачей. Вариант 12
Состав проекта
![]() |
![]() |
![]() ![]() ![]() ![]() |
![]() ![]() ![]() ![]() |
![]() ![]() ![]() ![]() |
![]() ![]() ![]() |
Дополнительная информация
5.04.05Клинорем +редуктор цилиндрический(kompasV10).cdw

Общее передаточное число i
Скорость вращения тихоходного вала
Мощность на тихоходном валу Р
Валы собранного редуктора должны проворачиваться от руки плавно
Сопряженные поверхности корпуса и крышек покрыть тонким слоем герметика
ВГК-18 N2 МРТУ 07-6012-63.
Необработанные наружные поверхности редуктора покрыть серой эмалью:
Редуктор обкатать без нагрузки при частоте вращения быстроходного вала
18.02.07Спецификац Клинорем+Редукт Л1(kompasV10).cdw

Пояснительная записка
Вал шестерня ведущий
Крышка подшипника сквозная
Прокладка регулировочная
Кольцо мазеудерживающее
Крышка подшипника глухая
Кольцо уплотнительное
Крышка корпуса редуктора
Крышка смотрового окна
Маслоуказатель жезловый
17.02.07Специфик Клинорем+Редуктор Л2(kompasV10).cdw

Кольцо уплотнительное
Пресс-масленка М10x1 ГОСТ 20905-75
Болт М10x30 ГОСТ7808-70
Шайба пружинная 10 ГОСТ 6402-70
Болт М6x20 ГОСТ7798-70
Болт М16x120 ГОСТ7798-70
Шайба пружинная 16 ГОСТ 6402-70
Болт М12x40 ГОСТ7808-70
Шайба пружинная 12 ГОСТ 6402-70
Болт М16x140 ГОСТ7808-70
Болт М12x30 ГОСТ7808-70
Шайба плоская 20 ГОСТ 11371-78
Гайка М16 ГОСТ 5915-70
Гайка М12 ГОСТ 5915-70
Гайка М20 ГОСТ 5915-70
Шпонка 18x11x65 ГОСТ 2336-78
Шпонка 10x8x36 ГОСТ 2336-78
Подшипник 308 ГОСТ 8338-75
Подшипник 312 ГОСТ 8338-75
Штифт 10x35 СТС ЗВ 240
Пояснительная записка 12.02.2008.doc
ГОУ ВПО «Уральский государственный технический университет–УПИ»
Кафедра «Детали машин»
ПОЯСНИТЕЛЬНАЯ ЗАПИСКА
к курсовому проекту по предмету
на тему: РАСЧЕТ И ПРОЕКТИРОВАНИЕ ПРИВОДА
С КЛИНОРЕМЕННОЙ ПЕРЕДАЧЕЙ
И ОДНОСТУПЕНЧАТЫМ ЦИЛИНДРИЧЕСКИМ КОСОЗУБЫМ РЕДУКТОРОМ
ПреподавательКомаров С. Б.
ЗАДАНИЕ НА ПРОЕКТИРОВАНИЕ
Спроектировать одноступенчатый горизонтальный цилиндрический косозубый редуктор и клиноременную передачу для привода к ленточному конвейеру (рис. 1).
Полезная сила передаваемая лентой конвейера Fл = 32 кН
cкорость ленты Vл = 13 мс
диаметр приводного барабана Dб =400 мм
Редуктор нереверсивный предназначен для длительной эксплуатации; работа двухсменная; валы установлены на подшипниках качения.
Рис. 1. Привод ленточного конвейера с цилиндрическим редуктором и клиноременной передачей:
– электродвигатель; 2 – клиноременная передача; 3 – одноступенчатый цилиндрический редуктор; 4 – муфта; 5 – приводной барабан; 6 – лента конвейерная
РАСЧЕТ И КОНСТРУИРОВАНИЕ
Выбор электродвигателя и кинематический расчет
Коэффициент полезного действия пары цилиндрических зубчатых колес
коэффициент учитывающий потери пары подшипников качения h2 = 099;
КПД клиноременной передачи h3 = 095;
коэффициент учитывающий потери в опорах приводного барабана h4=099 [1 c. 23 ; 2 c. 5 ]
h-коэффициент полезного действия (КПД) привода равный произведению КПД передач входящих в кинематическую схему:
h = h1 × h2 × h3 × h4 = 098 × 0992 × 095 × 099 × 099 = 090.
Мощность на валу барабана:
Рб = Fл × Vл =416 кВт
Требуемая мощность электродвигателя:
Ртр = Рб h =416090=462 кВт
Угловая скорость барабана:
wб =2Vл Dб =65 радс.
Частота вращения барабана:
nб = 30wб p =30×65314=611 обмин
Рекомендуемые значения передаточного отношения (i ) для зубчатых передач равны 2–6 [1 c. 58 ] и [2 c. 7 ] для ременных 2-4 [2 c. 7 ]. Таким образом передаточное отношение привода следующее:
Выбираем электродвигатель с таким числом оборотов чтобы передаточное отношение привода было не меньше 4 и не больше 24.
При выборе электродвигателя мы видим что мощность по паспорту отличается от требуемой. В этом случае надо учитывать два обстоятельства: большой запас мощности электродвигателя приводит к повышению расхода электроэнергии перегрузка – к перегреву двигателя (допускается перегрузка не более 5 %). Поэтому следует применять электродвигатель с ближайшим большим значением мощности [3 с. 24].
Выбираем электродвигатель трехфазный короткозамкнутый серии 4А закрытый обдуваемый 4А132S6 с параметрами Рдв = 55 кВти с асинхронной частотой вращения n =965 обмин (табл. П. 2.1);
wдв = p × nдв 30 =314×96530=101 радс
Передаточное отношение:
i = wдв wб =10165=155
что можно признать приемлемым так как оно находится между 4 и 24.
Передаточное число для редуктора принимаем из стандартного ряда по ГОСТ 2185-66 (табл. П. 2.20): u = ip = 5.
Вычисляем передаточное число для клиноременной передачи:
Угловая скорость и частота вращения ведущего вала редуктора:
w1 = wб × u =65*5=325 радс;
n1 = nб × u =611*5=3055 обмин.
Вращающий момент на валу А (ведущем валу ременной передачи)
Т1РЕМ = Ртр wдв =462101= 457 Нм.
Вращающий момент на валу В (ведомом валу ременной передачи – Т2РЕМ и ведущем валу редуктора – Т1 ):
Т1 = Т2РЕМ =457*31=14167
Вращающий момент на валу С (ведомом валу редуктора):
Рис. 2. Кинематическая схема привода:
А – вал электродвигателя; В – ведущий вал редуктора; С – ведомый вал редуктора и вал барабана
Частота вращения угловая скорость валов и крутящие моменты на валах (рис. 2):
Т2РЕМ = Т1 = 14167 Нм
Расчет клиноременной передачи
Исходные данные для расчета:
– передаваемая мощность Ртр = 462 кВт
– частота вращения ведущего (меньшего) шкива nдв =965 обмин;
– передаточное отношение
– скольжение ремня e = 0015.
Сечение ремня выбираем по номограмме ( прил. 1)
В нашем случае при Ртр.= 457 кВти nдв=965 обмин принимаем сечение клинового ремня Б.
Диаметр меньшего шкива:
Округляем диаметр шкива до ближайшего значения (табл. П.2.20);.
Диаметр большего шкива мм
d2= iк.р ×d1(1-e) =31*140(1-0015)=427 мм
Округляем диаметр шкива до ближайшего значения (табл. П. 2.20):
Уточненное передаточное отношение
При этом угловая скорость вала В будет:
w1=wдв iкр =101326= 309 радс.
Расхождение с заданным значением:
что более допускаемого (допускается до 3%)
Следовательно диаметры шкивов выбраны не верно. Используя справочник Ануфреева выбираем диаметр большого шкива d =425 мм. этот размер диаметра считается нежелательным(второстепенным) но т.к. для сборки нашей конструкции требуется такой шкив то мы можем его использовать.
Уточнённое передаточное отношение:
w1=wдв iкр =101308= 324 радс..
что менее допускаемого (допускаемое отклонение 3%)
Следовательно окончательно принимаем диаметры шкивов
Межосевое расстояние в интервале:
amin=055(d1+ d2)+Т0 = 055(140+425)+11=3217 мм
amax= d1+ d2 = 140+425= 565 мм.
где То = 11 мм (высота сечения ремня табл. П.2.19)
Принимаем предварительно близкое значение – a=560 мм..
Расчетная длина ремня:
L=2a+05(d1+ d2)+ (d2 – d1)24a =
Ближайшее значение длины ремня по стандарту (см. табл. П.2.19 ):
Уточненное межосевое расстояние с учетом стандартной длины ремня L= 2000 мм
где w=05p (d1+ d2) = 05*314*(140+425)=88705 мм;
y=(d2–d1)2 = 425-140) =81230 мм;
a=025*[(2000-88705)+ (2000-88705) -2*81230]=5376 мм
Угол обхвата ремнем малого шкива:
a1= 180–57 × (d2-d1)а =1498°150°
Коэффициент режима работы учитывающий условия эксплуатации передачи приведены в табл. П. 2.22 для привода к ленточному конвейеру при двухсменной работе Ср=11.
Коэффициент учитывающий влияние длины ремня приведен в табл. П. 2.21; для ремня сечения при длине L= 2000 ммкоэффициент СL= 098.
Коэффициент учитывающий влияние длины обхвата С:
П 1= 150°коэффициент С = 092
Коэффициент учитывающий число ремней в передаче:
Предполагая что число ремней от 2 до 3 принимаем Сz=.095
Число ремней в передаче
z=Р × Ср(Ро × СL × Сa × Сz)
где Р – мощность передаваемая одним клиновым ремнем кВт
(табл. П. 2.20); для ремня сечения Б при работе на шкиве d1= 140 мм и i ≥ 3 мощность Ро = 237 кВт
Принимаем число ремней z =3
Предварительное натяжение ветви ремня
Fо=850 Р Сp СL(z v Сa) + qv2
где скорость v=05 wдв d1 = 05*101*140*10-3 =707 мс.
q-коэффициент ×учитывающий влияние центробежных сил:
Для сечения ремня Б коэффициент q=018 Н×с2м2. Тогда
Сила действующая на вал:
Fв= Fо × z × sin(a12) =226*3*0.965=6548 Н.
Ширина шкивов Вш (табл. П.2.23);
Вш= (z – 1)e+2f =(3-1)*19+2*125=63 мм.
Расчет зубчатых колес
1. Выбор материала и определение размеров заготовок
Диаметры заготовок для шестерни dз1 и колеса dз2:
dз2 = dз1×U=83*5=415
Поскольку в задании нет требований относительно габаритов передачи выбираем материал со средними механическими характеристиками
Для шестерни сталь 45 термическая обработка – улучшение; при диаметре заготовки до 90 мм – твердость НВ 230.
Для колеса сталь 45 термическая обработка – улучшение; при диаметре заготовки более 120 мм – твердость НВ 200.
2. Расчет зубчатых колес на контактную выносливость
sНР – допускаемые контактные напряжения.
где s°Нlimв – предел контактной выносливости при базовом числе циклов.
КHL -коэффициент долговечности
при числе циклов больше базового КHL =1.
SH – коэффициент безопасности SH = 11 [ 7 с. 33]
sНР= s°Нlimв×КHL SH= (2*230+70)*111=481 МПа
sНР= s°Нlimв×КHL SH =(2*200+70)*111=427 МПа.
Расчетное допускаемое контактное напряжение
sНР = 045 (sНР1 +sНР2) =045(481+427)=4086 МПа.
Требуемое условие sНР 123sНРmin выполнено.
Межосевое расстояние определяем по формуле
где T2 – крутящий момент на ведомом валу (колесе);
Yва – коэффициент ширины венца по межосевому расстоянию
Yва = ваw = 05 (табл. П.2.3);
KHb – коэффициент учитывающий распределение нагрузки по ширине венца
KHb = 125 (табл. П.2.9);
Kа – коэффициент для косозубых колес Ka =43.
Округляем межосевое расстояние до ближайшего значения
-й ряд: 40 50 63 80 10 125 160 200 250 315 400 500 630 800 100 1250;
-й ряд: 71 90 112 140 180 224 280 355 450 560 710 900 1120 1400 1800.
Нормальный модуль зацепления принимаем по следующей рекомендации
mn=(001 002) по ГОСТ 9563-60 принимаем mn =25мм
Определим число зубьев шестерни и колеса по формуле
Примем предварительно угол наклона зубьев b=10°;
z1 =2*200* cos10°(5+1)*25=262
z2 = z1 ×U =26*5=130
уточняем угол наклона зубьев b:
cos b= (z1 +z2) mn 2аw= (26+130)*252*200=0.975
Определим основные параметры шестерни и колеса.
Диаметры делительные:
d1= mn ×z1cosb = 2.5*260.975=66.7
d2= mn ×z2cosb =2.5*1300.975=333.3
aw=(d1+d2)2=(66.7+333.3)2=200 мм.
Диаметры вершин зубьев:
da1=d1 + 2mn= 667+2*25=717
da2=d2 + 2mn=3333+2*25=3383
Диаметр окружности впадин зубьев:
df1= d1 – 25mn= 667-2*25=617
df2= d2 – 25mn=3333-2*25=3283
в2 = Yва аw= 05*200=100 мм
принимаем в2 = 100 мм.
в1 = в2 + 5=100+5=105 мм
Определяем коэффициент ширины шестерни по диаметру:
Yвd =в1d1=105667=157
Определяем окружную скорость колеса:
V=w1×d12= 325*6672*10-3=108 мс
При скорости до 10 мс для косозубых колес рекомендуется 8-я степень точности [7. c. 32].
Коэффициент нагрузки:
КH = КHb × КHa × КHv
где КHb – коэффициент учитывающий неравномерность распределения нагрузки по ширине венца; при Yвd =157 НВ 350 и несимметричном расположении колес (учет натяжения клиноременной передачи) КHb =122
КHa – коэффициент учитывающий неравномерность распределения нагрузки между зубьями; при v = 108 мс и 8-й степени точности КHa = 106
КHv – динамический коэффициент зависящий от окружной скорости колес и точности их изготовления; для косозубых колес при скорости менее 5 мс КHv= 10 (табл. П.2.11).
Кн= КHb × КHa× КHv =122*106*10=129.
Проверка контактных напряжений:
Фактические напряжения не превышают допустимые. Поэтому принимаем ранее выбранную ширину зубчатых колес.
3. Расчет зубьев на выносливость при изгибе
Силы действующие в зацеплении:
Ft = 2T1 d1 =2*14167*103667=4248 Н
Fr = Ft×tga cosb = 4248*tg20°cos128°=15855
Fa = Ft×tgb = 4248*tg128°=9651Н
Проверяем зубья на выносливость по напряжениям изгиба по формуле
sF = (Ft × KF×YF × Yb × KFL) (b × mn) sFР.
где KFb-коэффициент учитывающий неравномерность распределения нагрузки по ширине венца (коэффициент концентрации нагрузки) при
Yвd =157 НВ 350 и несимметричном расположении колес (учет натяжения клиноременной передачи) KFb = 145(табл. П.2.12);
KFV-коэффициент учитывающий динамическое действие нагрузки (коэффициент динамичности) KFV= 11(табл. П.2.13).
KF = KFb × KFV =145*11=1595
Коэффициент YF учитывающий форму зуба определяем по эквивалентному числу зубьев ZV:
ZV1 = Z1 cos 3b = 26(0975)3=28
ZV2 = Z2 cos 3b = 130(0975)3=140
Учитывая что коэффициент смещения исходного контура x=0 коэффициент формы зуба YF будет иметь следующие значения:
– для шестерни YF1= 384(табл. П. 2.14);
– для колеса YF2=36 (табл. П. 2.14).
Допускаемые напряжения на изгиб:
SF-коэффициент учитывающий нестабильность материала зубчатых колес
SF = 175 (табл. П.2.15);
SF – коэффициент учитывающий способ получения заготовки для изготовления зубчатого колеса для поковок и штамповок SF =10.
s°Flimb1 = 18 НВ (табл. П. 2.15).
s°Flimb1 = 18*230=415МПа(для шестерни)
s°Flimb2 = 18*200=360 МПа(для колеса).
Допускаемые напряжения:
sFР2 =360175=206МПа.
Определим коэффициенты:
Yb = 1 – b140 = 1-128140=1-058=091
KFa = 4 + (xa-1)(n-5) 4xa.
xa-коэффициент торцевого перекрытия
n-степень точности колес n = 8.
Проверяем прочность зуба по формуле
sF=(Ft×KF×YF×Yb× KFa)b×mn.
sF1 = (4248*1595*384*091*092)105*25=8298МПа ≤sFР1=237МПа
sF2 = (4248*1595*36*091*092)100*25=8168≤sFР2 ==206МПа
Условие прочности при изгибе зубьев выполнено.
Предварительный расчет валов редуктора
1. Расчет ведущего вала
Диаметр выходного конца вала:
где [tк] – допустимые касательные напряжения при кручении
Принимаем ближайшее большее значение из стандартного ряда
(табл. П. 2.24) dв2 =36мм. Высота буртов вала 3.5мм — в соответствии с табл. П. 2.25. Диаметр вала под подшипниками dп2 = 40мм(табл. П. 2.16).
Диаметры остальных участков вала назначаем из конструктивных соображений с учетом рекомендаций табл. П. 2.24 и П. 2.25.
Из технологических соображений целесообразно вал и шестерню выполнять в виде отдельных деталей но в данном случае мы будем иметь слишком тонкую стенку между внутренним диаметром шестерни и шпоночным пазом поэтому шестерню выполним за одно целое с валом. Конструкция ведущего вала приведена на рис. 3.
Рис. 3. Конструкция ведущего вала
2. Расчет ведомого вала
Диаметр выходного конца вала
Принимаем ближайшее большее значение из стандартного ряда (табл. П.2.24) dв2=60мм.
Высота буртов вала — в соответствии с табл. П.2.25. Диаметр вала под подшипниками dп2= 65мм(табл. П.2.16) под зубчатым колесом dк2=70мм.
Диаметры остальных участков вала назначаем из конструктивных соображений с учетом рекомендаций табл. П.2.24 и П.2.25. Конструкция ведомого вала приведена на рис. 4.
Рис. 4. Конструкция ведомого вала
Конструктивные размеры шестерни и колеса
Технологичнее изготавливать шестерню и вал отдельными деталями но в данном случае мы имеем маленькое расстояние между впадинами зубьев и шпоночным пазом и поэтому шестерню выполним за одно целое с валом. Размеры шестерни и колеса определенные ранее:
Расчет размеров колеса:
dcт=16 × dк2= 16 × 70 = 112 мм;
lct= 13 × dк2 = 13 × 70 = 91 мм
d0 = 3mn = 3 × 25 = 75 мм
C = 03× b2 = 03 × 100 = 30 мм
Конструктивные размеры корпуса редуктора
Толщина стенок корпуса и крышки: d = 0025 aw + 1 где aw — межосевое расстояние редуктора.
d1= 002 × аw + 1 =002*200+1=5
Толщина фланцев верхнего пояса корпуса и крышки:
нижнего пояса корпуса
принимаем р = 20 мм.
d=(003 0036) aw + 12 = 18 192мм
принимаем болты с резьбой М20
– крепящих крышку к корпусу у подшипников
d2=(07 075) d1 = 14 15мм
принимаем болты с резьбой М16
– соединяющих крышку с корпусом
d3=(05 06) d1 =10 12мм
принимаем болты с резьбой М12
Первый этап компоновки редуктора
Принимаем зазор между торцом шестерни и внутренней стенкой корпуса
Принимаем зазор от окружности вершин зубьев колеса до внутренней стенки корпуса А= d = 8мм
Принимаем расстояние между наружным кольцом подшипника ведущего вала и внутренней стенкой корпуса А= d = 8мм
В соответствии с рекомендациями [9 с.136] выбираем радиальные шарикоподшипники средней серии и схему их установки с одной фиксирующей опорой. Габариты подшипников выбираем по диаметру вала в месте посадки подшипников dп1= 40 мм и dп2= 65 мм.
Согласно табл. П. 2.16 имеем следующие данные:
Условное обозначение подшипника
Предварительная компановка редуктора приведена на рис. 5.
Рис. 5. Предварительная компановка редуктора.
Выбор муфты для соединения концов валов редуктора и приводного вала конвейера
Муфта соединяющая быстроходные валы (вал электродвигателя) в целях уменьшения пусковых моментов должна иметь малый момент инерции.
К муфтам которые соединяют сравнительно тихоходные валы (например редуктор и приводной вал конвейера) не предъявляют повышенных требований в отношении малого момента инерции. В то же время если исполнительный механизм и привод не располагаются на общей раме то от муфты требуются сравнительно высокие компенсирующие свойства.
Основной паспортной характеристикой муфты является допускаемый вращающий момент на передачу которого она рассчитана. По этому моменту и подбирают стандартные муфты:
где Т – номинальный длительно действующий момент на соединяемых валах Н·м;
К – коэффициент динамичности нагрузки; для ленточных конвейеров К= 125 15; цепных скребковых К=15 20.
где диаметр делительной окружности
здесь t – шаг цепи z – число зубьев полумуфты
Исходя из требуемых компенсирующих свойств крутящего момента и частоты вращения выбираем цепную муфту по табл. П.2.35 со следующими характеристиками:
– крутящий момент до 1000Нм.
– частота вращения до 780обмин;
– число зубьев звездочки полумуфты – 12;
– допустимое смещение валов до 04 мм;
– допустимое угловое смещение валов до 1°;
– цепь Пр -508-22680
Из-за неизбежной несоосности соединяемых валов зубчатая муфта нагружает вал дополнительной консольной силой Fм определяемой по формуле:
Fм = 02 (2Т 103dд) = 02(2*70835*103)196=1445Н
где диаметр делительной окружности:
dд = tsin(180ºz) =508sin(18012)=196мм
z – число зубьев полумуфты –
Проверка долговечности подшипника
1. Определение реакций в опорах ведущего вала
Расчетная схема ведущего вала приведена на рис. 6. Из предыдущих расчетов имеем силы в зубчатом зацеплении:
Сила действующая на вал в клиноременной передаче: Fрп=6548Н.
Из первого этапа компоновки l1 = 87мм
Рассматриваем худший вариант когда Ft и Fрп направлены в одну сторону:
Rx1 = [Ftl1 + Fрп( l0 +2l1 )]2l1 = [4248*87+6548*(80+2*87)]2*87=3080Н
Rx2=( Ft l1 – Fрпl0 ) 2l1 = 1823Н
(Rx1 + Rx2) – (Ft + Fрп) = (3080+1823)-(4248+6548)=0
Ry1= (Fr l1+ Fa d12 )2l1= (1585.5*87+965.1*66.62)2*87=97745
Ry2= (Fr l1 – Fa d1 2 )2l1= (1585.5*87-965.1*66.62)2*87=60805
Ry1 + Ry2 – Fr= 977.45+608.05-1585.5=0
Рис. 6. Расчетная схема ведущего вала
Рr1= (Rx12 + Ry12 )12 = (30802+977.452)12=3231Н
Рr2= (Rx22 + Ry22) 12 = (18232+608052)12=1922Н
2. Проверка долговечности подшипников ведущего вала
Подбираем подшипники по более нагруженной опоре 1.
Намечаем радиальные шариковые подшипники 308; d=40; D= 90
В = 23 С = 410Со = 224(табл. П. 2.16).
Эквивалентная нагрузка:
Рэ=(ХVPr1 + YPa1 ) KsKT
где Pr1 – радиальная нагрузка Pr1 = 3231Н
Pa1 – осевая нагрузка Pa1 = Fa = 9651Н
V – коэффициент зависящий от того какое кольцо подшипника вращается; при вращении внутреннего кольца V = 1;
Отношение FaСо = 0043
этой величине соответствует е 025 (табл. П. 2.17).
Отношение Pa1 Pr1 =0299;
X= 056 и Y= 178(табл. П. 2.17).
Рэ=(056*1*3231+178*9651)*1*1=3527Н
Расчетная долговечность:
Согласно ГОСТ 16162 (редукторы общего назначения ) ресурс зубчатых редукторов должен составлять 40000 ч. Для этих значений и предпочтительна расчетная долговечность подшипника. Минимальная долговечность подшипника для зубчатого редуктора по ГОСТ 16162 может составлять 10000 ч [3 c. 158].
Долговечность подшипника удовлетворяет указанным требованиям.
3. Определение реакций в опорах ведомого вала
Расчетная схема ведомого вала приведена на рис. 7. Ведомый вал несет в зубчатом зацеплении такие же нагрузки как и ведущий:
Из первого этапа компоновки l2 =90
Опорные реакции определяем с учетом этих сил в следующем порядке.
А. Находим опорные реакции вала от нагрузки в зацеплении.
В вертикальной плоскости:
Rx3= Rx4= Ft 2 = 2124
В горизонтальной плоскости:
Ry3= (Fr l2 + Fa d22 ) 2l2 = (15855*90-965*33332)2*90=1686083
Ry4= (Fr l2 – Fa d2 2 )2l2= (15856*90-965*33332)2*90=-100583
Ry3 + Ry4 – Fr= 1686083-100583-15855=0
Суммарные радиальные реакции подшипников для опоры 3:
Рr3= (Rx32 + Ry32 )12 = 2712Н
Суммарные радиальные реакции подшипников для опоры 4:
Рr4= (Rx42 + Ry42) 12 = 2126Н
Б. Определяем опорные реакции вала от консольной силы Fм вызываемой муфтой.
Из-за неизбежной несоосности соединяемых валов зубчатая муфта нагружает вал дополнительной консольной силой Fм приложенной к середине посадочной поверхности и определяемой по формуле
здесь t – шаг цепи –
; z – число зубьев полумуфты –
Рис. 7. Расчетная схема ведомого вала
В. Определяем суммарные опорные реакции ведомого вала от нагрузки в зацеплении и муфты.
Рассмотрим худший случай:
Рr3 = Рr1+ Fм= 3231+1445=4676Н
Рr4 = Рr2+ Fм= 1922+1445=3367Н
Расчет подшипников ведомого вала будем производить по более нагруженной опоре – 1(Рr3=4676Н)
4. Проверка долговечности подшипников ведомого вала
Шариковые радиальные подшипники 313 средней серии: d =65мм
В = 33мм С = 923кНСо = 560кН (табл. П. 2.16).
Отношение Fa Со = 965156000=0017
этой величине соответствует е 019 (табл. П. 2.17).
Отношение Fa Pr3 = 96514676=0206
X=056Y= 230(табл. П. 2.17).
Рэ=(ХVPr3 + YPa1 ) KsKT = (056*1*4676+23*9651)*1*1=4838Н
L= (C Рэ)3 =(923004838)=6944 млн.об
Расчетная долговечность в часах:
Долговечность подшипника удовлетворяет требованиям.
Проверка прочности шпоночных соединений
Размеры шпонок пазов и длины шпонок определяем по табл. П. 2.18.
Материал шпонок — сталь 45 нормализованная.
Напряжения смятия и условие прочности определяются по формуле:
sсм 2Т (d (h-t1) (l-b ) ) [ sсм ].
Допускаемые напряжения смятия при стальной ступице
[ sсм ] =100120 МПа.
Проверяем шпонку на конце вала на котором закреплен шкив ременной передачи.
d= 36мм b х h = 10*8t1= 50(табл. П. 2.18);
длина шпонки l = 56мм (табл. П. 2.30) момент на ведущем валу
(материал полумуфт МУВП – чугун марки СЧ20).
Проверяем шпонку на конце вала соединенном с муфтой.
d= 60 мм b х h =18 х 11; t1= 70(табл. П. 2.18);
длина шпонки l = 100(табл. П. 2.30) момент на ведомом валу Т2 =70835
Проверяем шпонку под зубчатым колесом.
d =65мм; b х h =20 х 12; t1 = 75(табл. П. 2.18);
длина шпонки l =110мм момент на ведомом валу Т2 = 70835Нм
Уточненный расчет валов
Уточненный расчет валов состоит в определении коэффициентов запаса прочности S для опасных сечений и сравнении их с требуемыми значениями [S].
Условие прочности соблюдено при S ³ [ S] = 25.
Коэффициент запаса прочности по нормальным напряжениям
Ss = s-1 (Kses × sv + Ys sm )
где s-1 – предел выносливости стали при симметричном цикле изгиба;
Ks – эффективный коэффициент концентрации нормальных напряжений;
es – масштабный фактор для нормальных напряжений;
sv – амплитуда цикла нормальных напряжений;
Ys – коэффициент чувствительности материала к асимметрии цикла нормальных напряжений для углеродистых сталей Ys= 02 для легированных Ys= 025 – 030 [2 c.163];
sm – среднее напряжение цикла нормальных напряжений.
Коэффициент запаса прочности по касательным напряжениям
St= t-1 (Kt et×t v +Yt × tm)
где t-1 – предел выносливости стали при симметричном цикле кручения;
Kt – эффективный коэффициент концентрации касательных напряжений;
et – масштабный фактор для касательных напряжений;
tv – амплитуда цикла касательных напряжений;
Yt – коэффициент чувствительности материала к асимметрии цикла касательных напряжений Yt= 01 [2 c.166];
tm – среднее напряжение цикла касательных напряжений.
tv = tm =05 tmax = 05ТWк.
Результирующий коэффициент запаса прочности
S= Ss×St (Ss 2 + St2 )12 .
Нормальные напряжения от изгиба изменяются по симметричному циклу а касательные от кручения — по отнулевому (пульсирующему) циклу.
Поскольку шестерня выполнена заодно с валом материал вала тот же что и для шестерни: сталь 45 термическая обработка — улучшение.
При диаметре заготовки меньше 90 мм (в нашем случае
Dз1= 836 мм) среднее значение sв= 780 МПа (табл. П. 2.6).
Предел выносливости при симметричном цикле изгиба:
s -1 = 043sв = 043 ×780 = 3354 МПа.
Предел выносливости при симметричном цикле касательных напряжений:
t -1 058 s -1=058× 3354 = 194 МПа.
Это сечение при передаче вращающего момента от электродвигателя через муфту рассчитываем на кручение. Концентрацию напряжений вызывает наличие шпоночной канавки. Коэффициент запаса прочности:
S = St = t-1 (Kt et t v + Yt tm )
где амплитуда и среднее напряжение от нулевого цикла:
tv=tm =tmax2=T12 Wк нетто
здесь Wк нетто – момент сопротивления сечения кручению.
При d =36мм b х h = 10 х 8ммt1 =5мм.
Принимаем Kt= 168(табл. П. 2.26)
et= 075(табл. П. 2.29)
Материал вала — сталь 45 нормализованная.
sв = 570 МПа (табл. П. 2.6).
Пределы выносливости:
s-1 =043 ×570=245 МПа
t-1=058 ×245=142 МПа.
Диаметр вала в этом сечении
Концентрация напряжения обусловлена наличием шпоночной канавки:
Ks=159 (табл. П. 2.26)
Kt=149 (табл. П. 2.26)
es= 079(табл. П. 2.29)
et= 060(табл. П. 2.29)
М= Рr3 × l2 =4676*90=420840 Н*м
Момент сопротивления кручению:
d= 70 мм; b= 20 мм; t1= 75 мм;
Момент сопротивления изгибу:
Амплитуда и среднее напряжение цикла касательных напряжений:
Амплитуда нормальных напряжений изгиба:
sм=ЬФ-Ф Циз нетто= 42084029.47*103=1428МПа
среднее напряжение sm=0.
Коэффициенты запаса прочности:
Результирующий коэффициент запаса прочности для сечения А-А:
Концентрация напряжений обусловлена посадкой подшипника с гарантированным натягом (для диаметра вала 65 мм):
Ks es= 350 (табл. П. 2.28)
Ktet= 248 (табл. П. 2.28)
М4 = Fм ×l3=1445*86=124270 Н*м
Осевой момент сопротивления:
Амплитуда нормальных напряжений:
sv=smax=M4 W=12427026950=46МПа
Полярный момент сопротивления кручению:
Wк= 2W= 2*26950=53900мм3
tv=tm = T22 Wк = 70835*1032*53900=657МПа
Коэффициент запаса прочности по нормальным напряжениям:
Коэффициент запаса прочности по касательным напряжениям:
Результирующий коэффициент запаса прочности для сечения К–К:
Концентрация напряжения обусловлена переходом от 65 к 60 .
При Dd =6560=109; rd=2.2560=0.0375
Ks=1.65Kt= 1.19(табл. П. 2.27)
es =0.79et=0.675 (табл.П. 2.29).
Крутящий момент тот же что и в сечении К–К.
МL-L= Fм · XL-L =1445*70=101150 Н*м
W=pd3 32=314*60332=21190мм3
sv=sмах= МL-L W=10115021190=477МПа
Полярный момент сопротивления при кручении:
Wк= 2W=2*21190=42380мм3
tv=tm = T22 Wк =70835*103 2*42380=835МПа
Результирующий коэффициент запаса прочности для сечений Л–Л:
Концентрация напряжения обусловлена наличием шпоночной канавки:
Ks= 159(табл. П. 2.26);
es = 079(табл. П.2. 29)
Kt= 149(табл. П. 2.26)
et= 069(табл. П.2. 29).
Изгибающий момент (XБ-Б = 40мм)
МБ-Б = Fм · XБ-Б =1445*40=57800
Момент сопротивления сечения нетто при b = 18t1 = 70
Амплитуда нормальных напряжений изгиба:
sv=МБ-Б Wиз нетто =578001825*103=316МПа
Момент сопротивления кручению сечения нетто:
tv=t m= T22 Wк нетто = 70835*10339440=1796МПа
Результирующий коэффициент запаса прочности для сечений Б–Б:
Сведем результаты проверки в таблицу:
Во всех сечениях S > [S]= 25.
Посадки зубчатого колеса шкива полумуфты подшипников
В соответствии с рекомендациями [2 с.263] назначаем:
– посадку зубчатого колеса на вал Н7
– посадку шкива на вал Н7
– посадку полумуфты на вал Н7p6.
В редукторе используем подшипники класса точности 0 [3 c. 179 – 182]
Предельные отклонения размеров посадочных поверхностей подшипников регламентированы ГОСТ 520-89. Посадки подшипников отличаются от обычных расположением и величинами полей допусков на посадочные поверхности колец.
С учетом вида нагружения колец назначаем следующие посадки:
Наружные кольца подшипников качения в корпусе
Внутренние кольца подшипников качения на валу
L0k6 [3 c. 179 – 182]
Смазочные системы и устройства. Выбор сорта масла
Для смазки зубчатых колес выбираем способ смазывания погружением зубчатых колес в масло залитое в картер редуктора. Данный способ используют при окружных скоростях менее 15 мс.Уровень масла в картере редуктора должен обеспечить погружение венца колеса на глубину до двух высот зубьев но не менее 10 мм [3 c. 223].
Объем масляной ванны принимают таким чтобы обеспечить отвод выделяющейся в зацеплении теплоты к стенкам корпуса. Для одноступенчатых цилиндрических редукторов объем масляной ванны рекомендуется принимать таким чтобы на 1 кВт мощности приходилось 035 07 л масла. [3 c. 224]. Учитывая что длина масляной ванны 430 мм ширина 125 мм а количество масла при мощности 533 кВт должно быть 19 37 л глубина масляной ванны должна быть 35 70 мм.
В спроектированном редукторе доступ масляных брызг к подшипникам качения затруднен и смазку подшипников масляными брызгами осуществить нельзя. Поэтому полость подшипника отделяем от внутренней части корпуса мазеудерживающим кольцом (сборочный чертеж поз. 5). Свободное пространство внутри подшипникового узла заполняем на 13 объема пластичной мазью. Для подачи в подшипниковую полость смазочного материала без снятия крышки используем пресс-масленки (сборочный чертеж поз. 52).
Для наблюдения за уровнем масла в картере редуктора используем жезловый маслоуказатель (сборочный чертеж поз. 13).
Во время работы в связи с нагревом воздуха и масла повышается давление внутри редуктора. Это приводит к выбрасыванию масляного тумана из корпуса через уплотнения и стыки. Чтобы избежать этого внутреннюю полость корпуса сообщают с внешней средой установкой отдушины (сборочный чертеж поз. 1) в верхней части корпуса.
При работе передачи масло постепенно загрязняется продуктами износа. С течением времени оно стареет свойства его ухудшаются. Поэтому масло налитое в корпус редуктора периодически меняют. Отработанное масло нужно слить таким образом чтобы не производить разборку механизмов привода. Для этой цели в нижней части корпуса редуктора предусматриваем сливное отверстие закрываемое пробкой (сборочный чертеж поз. 15)
В соответствии с рекомендациями [2 c. 253] для имеющих место в нашем случае контактных напряжений sн = 4086 МПа и скорости V = 13 мс.
рекомендуемая вязкость масла 34·10-6м2с. Принимаем масло индустриальное
И-40А по ГОСТ 20799-75 [2 c. 253].
Библиографический список
Комаров С.Б. Расчет и проектирование привода с клиноременной передачей и одноступенчатым цилиндрическим косозубым редуктором
С.Б. Комаров. Екатеринбург:ГОУ ВПО УГТУ–УПИ. 2006. 76 с.
Курсовое проектирование деталей машин С. А. Чернавский [и др.] М. : Машиностроение 1988. 416 с.
Чернилевский Д.В. Основы проектирования машин
Д.В. Чернилевский. М. : УМ и «Учебная литература» 1998. 472 с.
Шейнблит А.Е. Курсовое проектирование деталей машин
А.Е. Шейнблит. Калининград : Янтарный сказ 2004. 455 с.
Иванов М.Н. Детали машин М.Н. Иванов В.А. Финогенов. М. : Высшая школа 2003. 408 с.
Дунаев П.Ф. Конструирование узлов и деталей машин П.Ф. Дунаев О.П. Леликов. М. : Издательский центр «Академия» 2004. 496 с.
Проектирование механических передач С.А. Чернавский [и др.] М. : Машиностроение 1984. 560 с.
Рекомендуемые чертежи
- 18.02.2025
- 24.01.2023
- 15.02.2021
- 18.04.2023
- 24.01.2023