Расчет ректификационной колонны



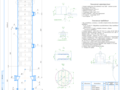
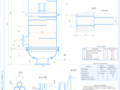
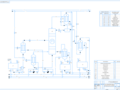
- Добавлен: 25.01.2023
- Размер: 938 KB
- Закачек: 1
Узнать, как скачать этот материал
Подписаться на ежедневные обновления каталога:
Описание
Расчет ректификационной колонны
Состав проекта
![]() |
![]() |
![]() ![]() ![]() ![]() |
![]() ![]() ![]() |
![]() ![]() ![]() ![]() |
![]() ![]() ![]() ![]() |
Дополнительная информация
Контент чертежей
Технологическая схема.cdw

Дефлегматор.cdw

Колонна ректификационная.cdw

Рекомендуемые чертежи
- 24.01.2023
Свободное скачивание на сегодня
Обновление через: 10 часов 22 минуты