Расчет тарельчатой ректификационной колонны для разделения смеси бензол-толуол


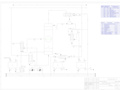
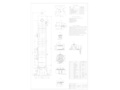
- Добавлен: 25.01.2023
- Размер: 663 KB
- Закачек: 1
Узнать, как скачать этот материал
Подписаться на ежедневные обновления каталога:
Описание
Расчет тарельчатой ректификационной колонны для разделения смеси бензол-толуол
Состав проекта
![]() |
![]() |
![]() ![]() ![]() |
![]() |
![]() ![]() ![]() ![]() |
![]() ![]() ![]() |
![]() ![]() ![]() |
![]() ![]() ![]() ![]() |
![]() ![]() ![]() |
![]() ![]() ![]() |
![]() ![]() ![]() |
Дополнительная информация
Контент чертежей
Тех.схем.тарелки.dwg

Колонна колпачковая.dwg

Рекомендуемые чертежи
- 15.04.2023
- 25.01.2023
Свободное скачивание на сегодня
Обновление через: 13 часов 32 минуты