Расчёт ректификационной колонны для разделения смеси пропан-пропилен


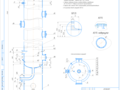
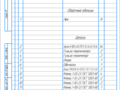
- Добавлен: 25.01.2023
- Размер: 501 KB
- Закачек: 2
Получить бесплатный доступ добавив свой материал или получить скидку оплатив сразу нескольких материалов
Подписаться на ежедневные обновления каталога:
Описание
Расчёт ректификационной колонны для разделения смеси пропан-пропилен
Состав проекта
![]() |
![]() |
![]() ![]() ![]() ![]() |
![]() ![]() ![]() ![]() |
![]() ![]() ![]() |
Дополнительная информация
Контент чертежей
Спецификация.spw

Тарелка III-1800-400-09Г2С ОН 26-02-29-66
Днище 1800х18-60-09Г2С ГОСТ 6533-68
Болт М26х150 ГОСТ 7798-70
Гайка М26 ГОСТ 5927-70
Шайба 26 ГОСТ 9649-78
Болт М16х80 ГОСТ 7798-70
Колонна(пропан-пропилен).cdw

Техническая характеристика
Аппарат предназначен для отделения пропилена от смеси с пропаном.
Производительность 5 тч по сырью.
Давление в колонне (избыточное) 1
Среда в аппарате - токсичная
Номинальная емкость 85 куб.м.
Технические требования
испытании и поставке аппарата должны
а) ГОСТ 12.2.003-91 "Оборудование производственное. Общие
требования безопасности";
б) ОСТ 26-291-94 "Сосуды и аппараты стальные сварные.
Материал тарелок и остальных сборочных единиц - 09Г2С ГОСТ 5520-84.
Материал опоры - сталь 09Г2С ГОСТ 5520-84.
Материал прокладок - паронит ПОН-1 ГОСТ 481-80.
выполняться требования:
и сталь Ст 20 ГОСТ 380-94.
Сварные соединения должны соответствовать требованиям
Сварные швы в объеме 100% контролировать рентгенопросвечиванием.
Не указанный вылет штуцеров 200 мм.
ОСТ 26-01-82-77 "Сварка в химическом машиностроении".
Схема расположения штуцеров
Количество тарелок - 54.
Питание подаётся на 29 тарелку.
Курсовой(пропилен-пропан)2.doc
Пермский государственный технический университет.
Пояснительная записка к курсовому проекту:
“Расчёт ректификационной колонны”
Материальный баланс колонны и рабочее флегмовое число7
Скорость пара и диаметр колонны13
КПД контактных устройств17
Расчёт высоты колонны18
Расчёт гидравлического сопротивления тарелок19
Расчет высоты куба колонны20
Тепловой расчёт колонны20
Расчет диаметров штуцеров ректификационной колонны20
Прочностной расчет колонны22
Список используемой литературы23
Колонные аппараты можно классифицировать в зависимости от технологического назначения способа осуществления контакта между газом (паром) и жидкостью состояния межфазной поверхности.
По технологическому назначению аппараты подразделяются на колонны атмосферно-вакуумных установок термического и каталитического крекингов вторичной перегонки нефтепродуктов для ректификации газов для моноэтаноламиновой очистки газов и пр.
По способу осуществления контакта между паром (газом) и жидкостью все аппараты можно подразделить на аппараты с непрерывной подачей обеих фаз пульсационной и цикличной подачей. Цикличная подача состоит в том. что газ и жидкость подаются в аппарат попеременно.
По состоянию межфазной поверхности. В соответствии с этим колонные аппараты классифицируются на группы: 1) аппараты с фиксированной поверхностью фазового контакта: 2) аппараты с поверхностью контакта образуемой в процессе движения потоков; 3) аппараты с внешним подводом энергии.
Наиболее типичные широко применяемые в промышленности аппараты распределяются по группам указанным в таблице.
Классификация колонных аппаратов по состоянию межфазной поверхности
Колонны с фиксированной поверхностью
образуемой в процессе движения фаз
Колонны с внешним подводом энергии
Поверхностные аппараты
Распылительные колонны
Колонны с механическими мешалками
Инжекторные (струйные) колонны
Центробежные колонны
Пульсационные колонны
Тарельчатые контактные устройства можно классифицировать по многим признакам: например по способу передачи жидкости с тарелки на тарелку различают тарелки с переточными устройствами и тарелки без переточных устройств (провальные).
Тарелки с переточными устройствами имеют специальные каналы по которым жидкость перетекает с одной тарелки на другую причем по этим каналам не проходит газ. На провальных тарелках нет переливных устройств и жидкость и газ проходят через одни и те же отверстия или прорези в полотне тарелки. Эти прорези работают периодически: в определенный момент времени одни прорези пропускают пар. другие — жидкость: затем их роли меняются.
По характеру взаимодействия газового и жидкостного потоков различают тарелки барботажного и струйного типов. Тарелки на которых сплошной фазой является жидкость а дисперсной — газ или пар называют барботажными. На струйных тарелках дисперсной фазой является жидкость сплошной — газ. потоки взаимодействуют в прямоточном режиме на поверхности капель и жидкостных струй взвешенных в газовом потоке.
По числу потоков (сливов) тарелки выполняют одно- двух- и многопоточными (рис. 1.1). Применяют также многосливные тарелки с равномерно распределенными по площади сливами и тарелки с каскадным расположением полотна.
Рис .1. Схемы тарелок: а- однопоточной; б- двухпоточной; в -трехпоточной г- четырехпоточной; д - каскадной.
Многопоточные и многосливные тарелки используют в колоннах большого диаметра и при значительных расходах жидкости. Такие тарелки обеспечивают более равномерные уровень жидкости и распределение газа по площади контактных устройств. Это связано с уменьшением напряженности слива в гидравлическом отношении и длины пути жидкости на тарелке. В колоннах со значительным изменением по высоте жидкостной нагрузки устанавливают тарелки с различным числом потоков.
В зависимости от направления движения газовой и жидкой фаз в зоне контакта выделяют тарелки трех основных групп:
) Тарелки перекрестные в которых движение газа и жидкости осуществляется перекрестным током. Эти тарелки имеют специальные переливные устройства для перетока жидкости с одной тарелки на другую.
причем газ по переливам не проходит (колпачковые с S-образными элементами клапанные ситчатые).
)Тарелки противоточные (провального типа) в которых переливные
устройства отсутствуют так что газ и жидкость проходят через одни и те же
отверстия. На этих тарелках контакт газа и жидкости осуществляется по схеме
полного перемешивания жидкости (решетчатые).
)Тарелки прямоточные (с однонаправленным движением газа и
жидкости). В данном случае газ выходит из отверстий в направлении движения
жидкости по тарелке: это вызывает снижение продольного перемешивания
жидкости и способствует движению жидкости что приводит к уменьшению
гидравлического градиента. Тарелки описанного типа обычно имеют
переливные устройства но существуют и конструкции без переливов (струйные
и струйные с отбойниками).
По конструктивному решению элементов тарелки разделяются в соответствии с ГОСТ 2.790-74. (Обозначения условные графические. Аппараты колонные.) Предлагаемые стандартом обозначения колонных аппаратов в конструкторской документации всех отраслей промышленности представлены в таблице 2.
Рис.2. Классификация тарелок по способу организации движения пара и жидкости а- протнвоточные б- прямоточные в- перекрестного тока
Устройство тарелок клапанных описано многими авторами. Такие тарелки изготовляют с дисковыми и прямоугольными клапанами.
Диаметр дисковых клапанов обычно составляет 50 мм; диаметр отверстия под клапаном в полотне тарелки 30 — 40 мм высота подъема клапана б — 8 мм. При этом площадь проходного сечения щели между полотном тарелки и пластиной клапана при его полном подъеме немного меньше площади отверстия под клапаном. В нижнем положении клапан опирается на выступы которые получают обычно просечкой и отгибанием краев пластины клапана так. чтобы между пластиной и полотном тарелки оставался зазор 05— 1.5 мм. Это позволяет исключить влияние сил поверхностного натяжения на работу клапана.
Рис. 3. Конструкции клапанов: а — типа «Глитч». б — типа «Флекситреи» Для ориентирования при движении клапан снабжен направляющими. Применяют клапаны (рис. 4) с нижними направляющими (клапаны типа «Глитч») и направляющими установленными на полотне тарелки (клапаны типа «Флекситреи»). Клапаны располагают рядами в шахматном порядке к направлению потока жидкости.
В колоннах применяют балластные клапанные тарелки которые благодаря более равномерной работе имеют улучшенные показатели. Клапаны таких тарелок могут иметь индивидуальный и групповой балласт. При работе таких устройств вначале поднимается пластина 1 клапана (рис. 5) затем она упирается в балласт 2 и поднимается вместе с балластом.
Клапанные тарелки благодаря регулируемому сечению обеспечивают высокую эффективность в сравнительно широком диапазоне нагрузок. Они менее склонны к загрязнениям но коксоотложения могут нарушать их работу [4].
Рис.4. Балластный клапан
В отечественной практике широко применяют прямоточные тарелки с дисковыми клапанами. Клапан такой конструкции (рис. 6) имеет три направляющие расположенные в плане под углом 120° две из которых имеют большие вес и длину. При работе с возрастающей скоростью паров сначала поднимается легкая часть клапана обращенная против потока жидкости а затем клапан принимает положение при котором пары выходят в направлении движения жидкости. Короткая ножка клапана расположена в вырезе на кромке отверстия полотна тарелки что обеспечивает заданное положение клапана в плане при его подъеме. Стандартом предусмотрены тарелки однопоточные диаметром 1000—4000 мм. двухпоточные — 1400—9000 мм и четырехпоточные — 3200—5500 мм. Тарелки выполняют разборными. Тарелку любого из этих диаметров можно изготовлять в трех вариантах с шагом между рядами клапанов 50 75 и 100 мм. что предопределяет различное число клапанов и соответственно разную площадь свободного сечения тарелки. Кроме того для каждого из этих вариантов предусмотрены две модификации тарелок отличающиеся площадями слива. При больших диаметрах (7000— 9000 мм) две смежные по высоте тарелки опираются на общую центральную балку и каждая тарелка имеет боковые балки.
Клапанные прямоточные тарелки типа ТКП применяют в нефтеперерабатывающей и нефтехимической промышленности при атмосферном или повышенном давлении изменяющихся нагрузках по пару (газу) и жидкости а также при повышенных требованиях к качеству и четкости разделения смеси.
Рис. 5. Схема работы клапана прямоточной тарелки стандартной конструкции при нагрузках по парам: а — малых; б — средних; в — больших.
Клапаны прямоточной тарелки с групповым балластом показаны на рис. 6 [4].
Рис. 6. Клапаны прямоточной тарелки с групповым балластом: 1 — полотно; 2 — клапан; 3 — балласт
Материальный баланс колонны и рабочее флегмовое число.
Содержание легколетучего компонента:
тч - производительность по исходной смеси.
Пропилен Мa =42 кгкмоль
Пропан Mb = 44 кгкмоль
Производительность колонны по исходной смеси GF кубовому остатку GW определим из уравнений материального баланса колонны [2]:
Пересчитаем составы фаз из мольных долей в массовые по соотношению
где MА и Мb - молекулярные массы соответственно пропилена и смеси кгкмоль.
Относительный мольный расход питания:
Таблица 1.2.Расчёт равновесной кривой системы пар- жидкость [6].
Парциальное давление пропилена мм.рт.ст.
Парциальное давление пропана мм.рт.ст.
По примеру [2] стр. 326. y=x* pпропиленаП
Где: p – парциальные давления компонентов П – общие давление системы.
График 1. Равновесная линия ректификации смеси пропилен-пропан.
Определение флегмового числа и рабочих линий.
Определяем минимальное число флегмы Rmin по уравнению:
где yF*- концентрация легколетучего компонента в паре находящемся в равновесии с исходной смесью кмолькмоль смеси.
При (моль.) =059% (моль.)
Рабочее число флегмы по уравнению:
Уравнение рабочих линий:
а)верхней (укрепляющей) части колонны
б)нижней (исчерпывающей) части колонны
Равновесная и рабочие линии процесса.
Средние массовые расходы (нагрузки) по жидкости для верхней и нижней частей колонны определяют из соотношений [1];
где МD и MF - мольные массы дистиллята и исходной смеси; МВ и МН - средние мольные массы жидкости в верхней и нижней частях колонны.
Средние мольные массы жидкости в верхней и нижней частях колонны соответственно равны:
хср в и хср н - средний мольный состав жидкости в верхней и нижней частях колонны:
Мольная масса исходной смеси:
Мольная масса дистиллята:
Подставим рассчитанные величины в выражения для средних массовых расходов получим:
Средние массовые потоки пара в верхней GВ и нижней GН частях колонны:
где МВ и МН - средние мольные массы паров в верхней и нижней частях колонны
Средние концентрации пара находим по уравнениям рабочих линий [2]:
Подставив численные значения получим:
Скорость пара и диаметр колонны.
График 3.Диограмма состояния температура-концентрация.
) Определение плотностей жидкости и пара [2]:
Средние температуры пара [2] :
Средняя плотность пара в колонне:
Средняя плотность жидкости: где - средняя массовая концентрация пропилена которая рассчитывается:
)для верхней части колонны:
)для нижней части колонны:
Средняя плотность жидкости в колонне:
Объёмный расход паровой фазы:
Объёмный расход жидкой фазы вверху колонны:
Объёмный расход жидкой фазы внизу колонны:
Расчет требуемого диаметра колонны проводим согласно методике [1]. Диаметр колонны проверяется по величине рабочей площади тарелки рассчитываемой по формуле
где VП объемный расход газа в колонне м3с
WР скорость газа (пара) в рабочем сечении колонны мс
За рабочее сечение колонны принимают площадь основания тарелки на которой установлены контактные элементы (без учета площади сливных устройств). Скорость пара в рабочем сечении принято рассчитывать по уравнению:
где j фактор вспениваемости жидкости для перегонки газов он находится в интервале 09-10 принимаем что значение j = 09.
rж –плотность жидкости на тарелке кгм3
rп –плотность пара на тарелке кгм3
Значение коэффициента С определяется по графику 1 в зависимости от расстояния между тарелками и комплексного показателя J определяемого по уравнению
График 4. Значения коэффициента (С)
где GЖ – расход жидкости на тарелке кгчас
GП – расход пара на тарелке кгчас
расстояние между тарелками принимаем равным 04 м
Определив минимальную рабочую площадь тарелки необходимую для нормальной работы колонны по справочным данным [5] выбираем клапанную тарелку с ближайшей большей рабочей площадью и определяем ее фактический диаметр.
Если получившийся диаметр меньше существующего то реальная тарелка справится с заданной нагрузкой если - же расчетный диаметр больше существующего то при таком режиме работы данная тарелка не сможет эффективно работать что нарушит процесс ректификации и не позволит получить продукт требуемого качества.
Необходимая рабочая поверхность колонны:
По справочнику «Колонные аппараты» берем D=1800 мм с рабочей поверхностью 183 м2 тогда скорость пара в колонне будет:
Во избежание захлебывания сливного устройства скорость жидкости в нем должна отвечать условию:
Для верха: 0020300226·040800670130.
Для низа колонны: 00250220226·050800830130.
где: FСЛ - площадь сливного устройства для выбранной тарелки м2.
К5 n2-коэффициенты учитывающие вспениваемость жидкости равные 0226 и 08 .
Скорость жидкости в зазоре между основанием тарелки и нижней кромкой сливного стакана должна отвечать условию:
Для верха: 002(143·009)0450155045.
Для низа колонны: 0025(143·009)0226·05080194045.
где: а - величина зазора (м) принимаемая в зависимости от типа тарелки: для клапанных тарелок a=009 м.
Все условия соблюдаются значит расстояние между тарелками можно принять 04м а тарелки однопоточными.
КПД контактных устройств.
КПД определяется по графику 2.
График 5. Значение КПД тарелок
- клапанная; 2-ситчатая; 3 - колпачковая; 4 – решетчатая.
КПД тарелки равно 086.
Расчёт высоты колонны.
График 6.Построение ступеней изменения концентрации.
В верхней части получили 30 ступеней изменения концентрации.
В нижней части получили 26 ступеней изменения концентрации.
Количество тарелок в верхней части 30086=35
Количество тарелок в нижней части (26-1)086=29
Общее количество тарелок 35+29=54.
Расчёт гидравлического сопротивления тарелок.
Гидравлическое сопротивление тарелки
Гидравлическое сопротивление сухой тарелки:
-коэффициент гидравлического сопротивления тарелки;
- свободное сечение тарелки.
Перепад высоты слоя жидкости на тарелке:
Где: k- газосодержащие слоя жидкости на тарелке.
Гидравлическое сопротивление газожидкостного слоя (пены) на тарелке :
Где: -высота переливной перегородки м.
Общее гидравлическое сопротивление колоны:
Выбранное межтарельчатое расстояние удовлетворяет этому условию.
Расчет высоты куба колонны.
Высоту куба определяют исходя из запаса остатка на 300 с. Объем жидкости внизу колонны определяется по формуле:
где G- расход жидкости 0653 кгс;
- плотность жидкости 45026 кгм.
V= 0653·30045026 =0435 м.
Площадь поперечного сечения колонны F=314·18²4= 25434 м²
Тепловой расчёт колонны.
Расход теплоты отдаваемой охлаждающей воде в дефлегматоре-конденсаторе находим по уравнению:
Здесь rD-удельная теплота конденсации паров в дефлегматоре Джкг.
rD= r1+(1-)r2=0974291959+(1-0974) 275534=291532 Джкг.
где r1 и r2 –удельные теплоты конденсации пропилена и пропана при 50°С ( кДжкг[2] табл. XLV стр. 541)
Расход теплоты получаемой в кубе-испарителе от греющего пара находим по уравнению:
Qк= Qд+ GD СD tD+ GW СW tW – GF СF tF+Qпот
где Qпот приняты в размере 3% от полезно затрачиваемой теплоты; удельные теплоёмкости взяты соответственно при tD =45°С tW =54°С tF = 49°С; ([2] табл. XI стр. 562);
СW = 0005 3330 + (1-0005)3592 = 3590 Дж(кг К);
СF =0538 3330+(1 - 0538) 3592 =3451 Дж(кг К);
CD = 09743330+(1-0974) 3592= 3337 Дж(кг К).
Qк = (2964+0736333745– 1389345149 + 0653359054) 103=4954 кДжс
Расход греющего пара:
где кДжкг – удельная теплота конденсации кубового остатка.
Расчет диаметров штуцеров ректификационной колонны.
Диаметр входа флегмы:
D=м D=150 мм. ( [5] стр.522)
где - скорость жидкости в напорных трубопроводах( [2]стр.17 табл.1.1)
Диаметр входа питания:
D=м D=60 мм. ( [5] стр.522)
Диаметр выхода пара:
D=м D=200 мм. ( [5] стр.522)
Диаметр входа подогревающего пара:
D= D=250 мм. ( [5] стр.522)
Диаметр выхода кубового остатка:
Так как через трубу вывода кубового остатка выводится также жидкость в испаритель то необходимо прибавить к потоку кубового остатка поток греющего пара:
Прочностной расчет колонны.
Выбор конструкционного материала:
Для не коррозионноактивной среды Тср = 50 Р = 19 МПа
рекомендуемый конструкционный материал – сталь 09Г2С ГОСТ 5520-62.
Эта сталь не дорогая обладает хорошими механическими свойствами широко используется в химической промышленности.
Расчет толщины стенки обечайки:
где D – наружный или внутренний диаметр обечайки м; - допускаемое напряжение на растяжение для материала обечайки МНм2 ;
МНм2 при Т=500 С ( [5] стр. 399 табл.12.4)
Коэффициент учитывает ослабление обечайки из-за сварного шва и наличия неукрепленных отверстий:
Прибавка толщины с учетом коррозии Ск :
где - амортизационный срок службы аппарата (можно принять 10 лет); П – коррозионная проницаемость ммгод.
Давление испытания для аппаратов работающих при давлении более 05МПа:
Исходя из инженерно – конструктивных соображений примем толщину обечайки равной 18 мм.
Границей применимости расчетной формулы является условие:
Условие выполняется.
Расчет толщины стенки днищ:
Толщину стандартных эллиптических днищ рассчитывают по формуле:
Исходя из инженерно – конструктивных соображений примем толщину днищ равной 18 мм.
Список использованной литературы
Касаткин А. Г. Основные процессы и. аппараты химической технологии. Москва 2004 .
Павлов К. Ф. Романков П. Г. Носков А. А. Примеры и задачи по курсу процессов и аппаратов. Москва 2004.
Расчет и конструирование машин и аппаратов химических производств: Примеры и задачи: Учеб. пособие для студентов втузовпод общ. ред. М. Ф. Михалев. Л: Машиностроение Ленингр. отд-ние 1984.
Дытнерский Ю.А. Процессы и аппараты химической технологии. М.: Химия 1993.
Тимонин А. С. Основы конструирования и расчета химико-технологического и природоохранного оборудования: Справочник. Т.1.-Калуга: Издательство Н. Бочкаревой 2002..
Н.Б.Варгафтик.Справочник по теплофизическим свойствам газов и жидкостей. Государственное издательство физико-химической литературы Москва 1963.
Рекомендуемые чертежи
- 25.01.2023
- 15.04.2023
Свободное скачивание на сегодня
Обновление через: 7 часов 40 минут