Расчет ректификационной колонны с клапанными тарелками для разделения смеси сероуглерод - четыреххлористый углерод



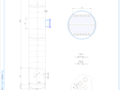
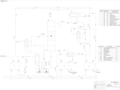
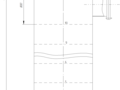
- Добавлен: 25.01.2023
- Размер: 649 KB
- Закачек: 1
Описание
Состав проекта
![]() |
![]() |
![]() ![]() ![]() |
![]() ![]() ![]() ![]() |
![]() ![]() ![]() |
![]() ![]() ![]() |
![]() ![]() ![]() ![]() |
Дополнительная информация
ВВЕДЕНИЕ.docx
Дытнерский Ю.И. Процессы и аппараты химической технологии: Учебник для вузов. Изд. 3-е. В 2-х кн.: Часть 2. Массообменные процессы и аппараты. М.: Химия 2002. – 368 с.: ил.
Иоффе И.Л. Проектирование процессов и аппаратов химической технологии: Учебник для техникумов. – Л.: Химия 1991. – 352 с. ил.
Касаткин А.Г. Основные процессы и аппараты химической технологии. Изд. 14-е. М.:ОООНД «Альянс» 2008-753с.
Плановский А.Н. Рамм В.М. Каган С.З. Процессы и аппараты химической
технологии. Изд. 5-е стереотипное. М. Химия 1968 848с.
Под ред. Судакова. “Расчёт основных процессов и аппаратов нефтепереработки” справочник М. Химия 1979 568с. ил.
Скобло А.И. Трегубова И.А. Молоканов Ю.К. “Процессы и аппараты нефтеперерабатывающей и нефтехимической промышленности”. – 2-е изд. перераб. и доп. – М. Химия 1982 584с.
Соколов В.Н. “Машины и аппараты химических производств” Л. Машиностроение Ленинградское объединение 1982 384с. ил.
Тимонин А.С. Основы конструирования и расчета химико-технологического и природоохранного оборудования: Справочник. Т.2. – Калуга. Издательство Н. Бочкаревой 2002. – 1028 с.
Дытнерский Ю.И. Основные процессы и аппараты химической технологии: Пособие по проектированию. Изд. 3-е. стереотипное. М:. ОООИД «Альянс» 2007-496 с.
Литературный обзор по теме .
Ректификация известна с начала XIX века как один из важнейших технологически процессов главным образом спиртовой и нефтяной промышленности. В настоящее время ректификацию все шире применяют в самых различных областях химической технологии где выделение компонентов в чистом виде имеет весьма важное значение (в производства органического синтеза изотопов полимеров полупроводников и различных других веществ высокой чистоты).
Процесс ректификации осуществляется путем многократного контакта между неравновесными жидкой и паровой фазами движущимися относительно друг друга.
При взаимодействии фаз между ними происходит массо- и теплообмен обусловлены стремлением системы к состоянию равновесия. В результате каждого контакта компонент перераспределяются между фазами: пар несколько обогащается низкокипящим компонентом жидкость - высококипящим. Многократное контактирование приводит к практически полном разделению исходной смеси.
Устройство ректификационных аппаратов.
Рис. 1 Ректификационная колонна непрерывного действия.
– колонна; 2 – кипятильник; 3 – дефлегматор
Таким образом отсутствие равновесия (и соответственно наличие разности температур фаз при движении фаз с определенной относительной скоростью и многократном их контактированиии являются необходимыми условиями проведения ректификации.
Процессы ректификации осуществляются периодически или непрерывно при различны давлениях: при атмосферном давлении под вакуумом (для разделения смесей высококипящих веществ) а также под давлением больше атмосферного (для разделения смесей являющихся газообразными при нормальных температурах).
1.Сущность проектируемого процесса.
Ректификация - массообменный процесс который осуществляется в противоточных колонных аппаратах с контактными элементами (насадки тарелки). В процессе ректификации происходит непрерывный обмен между жидкой и паровой фазой. Жидкая фаза обогащается более высококипящим компонентом а паровая фаза - более низкокипящим. Процесс массообмена происходит по всей высоте колонны между стекающей вниз флегмой и
поднимающимся вверх паром. Что интенсифицировать процесс массообмена применяют контактные элементы что позволяет увеличить поверхность массообмена. В случае применения насадки жидкость стекает тонкой пленкой по ее поверхности в случае применения тарелок пар проходит через слой .Ректификация представляет собой процесс многократного частичного испарения жидкости конденсации паров. Процесс осуществляется путем контакта потоков пара и жидкости имеющих различную температуру и проводятся обычно в колонных аппаратах. При каждом контакте и жидкости испаряется преимущественно низкокипящий компонент которым обогащаются пары из паров конденсируется преимущественно высококипящий компонент переходящий в жидкости. Такой двусторонний обмен компонентами повторяемый многократно позволяет получить в конечном счете пары представляющие собой почти чистый низкокипящий компонент. Эти пары после конденсации в отдельном аппарате дают дистиллят (ректификат) и флегму – жидкость возвращаемую для орошения колонны и взаимодействия с поднимающимися нарами. Пар получают путем частичного испарения снизу колонны остатка являющегося почти чистым высококипящим компонентом.
2. Аппараты используемые для проведения проектируемого процесса.
Для проведения процессов ректификации применяют аппараты разнообразных конструкций основные типы которых не отличаются от соответствующих типов абсорберов.
В ректификационных установках используют главным образом аппараты двух типов:
насадочные и тарельчатые ректификационные колонны. Кроме того для ректификации. Для проведения процессов ректификации применяют аппараты разнообразных конструкций основные типы которых не отличаются от соответствующих типов абсорберов.
насадочные и тарельчатые ректификационные колонны. Кроме того для ректификации.
вакуумом применяют пленочные и роторные колонны различных конструкций
Насадочные барботажные а также некоторые пленочные колонны по конструкции внутренних устройств (тарелок насадочных тел и т. д.) аналогичны абсорбционным колоннам. Однако в отличие от абсорберов ректификационные колонны снабжен теплообменными устройствами - кипятильником (кубом) и дефлегматором (рис. 1). Кроме того для уменьшения потерь тепла в окружающую среду ректификационные аппараты покрывают тепловой изоляцией.
Рис- 2. Варианты установки дефлегматоров
а - на колонне: б - ниже верха колонны;
-дефлегматоры; 2 - колонны: 3 - насос.
Кипятильник или куб предназначен для превращения в пар части жидкости стекающей из колонны и подвода пара в ее нижнюю часть (под насадки или нижнюю тарелку). Кипятильники имеют поверхность нагрева в виде змеевика или представляют собой кожухотрубчатый теплообменник встроенный в нижнюю часть колонны. Более удобны для ремонта и замены выносные кипятильники которые устанавливают ниже колонны с тем чтобы обеспечить естественную циркуляцию жидкости.
Дефлегматор предназначенный для конденсация паров и подачи орошения (флегмы) колонну представляет собой кожухотрубчатый теплообменник в межтрубном пространстве которого обычно конденсируются пары а в трубах движется охлаждающий агент (вода).
Рис. 3. Сетчатая колонна.
а - схема устройства колонны; б – схема устройства тарелки; 1 - корпус; 2 - тарелка; 3 - переливная труба; 4 - стакан.
В случае частичной конденсации паров дефлегматоре его располагают непосредственно над колонной чтобы обеспечить большую компактность установки либо вне колонны (рис 2). При этом конденсат (флегму) из нижней части дефлегматор подают непосредственно через гидравлический затвор на верх колонны так как в данном случае отпадав необходимость в делителе флегмы.
В случае полной конденсации паров в дефлегматоре его устанавливают выше колонны непосредственно на колонне или ниже верха колонны для того чтобы уменьшить общую высоту установки. В последнем случае флегму из дефлегматора 1 подают в колонну 2 насосом. Такое размещение дефлегматора часто применяют при установке ректификационных колонн вне зданий что более экономично в условиях умеренного климата.
Барботажные (тарельчатые) колонны.(Рис 3). Эти аппараты в процессах ректификации наиболее широко распространены. Они применимы для больших производительностей широкого диапазона изменения нагрузок по пару и жидкости могут обеспечить весьма четкое разделение смесей Недостаток барботажных аппаратов – относительное высокое гидравлическое сопротивление - в условия ректификации не имеет существенного значения. При ректификации повышение гидравлического сопротивления приводит лишь к некотором увеличению давления и соответственно повышению температуры кипения жидкости кипятильнике колонны. Однако тот же недостаток сохраняет свое значение для процессов ректификации под вакуумом.
В таких колоннах используют различные виды тарелок: ситчатые колпачковые провальные клапанные пластинчатые и др.
Клапанные тарелки. (рис. 5).Принцип действия клапанных тарелок состоят в том что свободно лежащий что свободно лежащий над отверстием в тарелке круглый клапан с изменением расхода газа своим весом автоматически регулирует величину площади зазора между клапаном и плоскостью тарелки для прохода газа и тем самым поддерживает постоянной скорость газа при его истечении в барботажный слой.
Рас. 5. Клапанные тарелки.
а б - с круглыми колпачками; в с пластинчатым клапаном; г - балластная; 1 - клапан; 2 - кронштейн- ограничитель; 3 - балласт.
При этом с увеличением скорости газа в колонне гидравлическое сопротивление клапанной тарелки увеличивается незначительно. Высота подъема клапана ограничивается высотой кронштейна ограничителя и обычно не превышает 8 мм.
Достоинства клапанных тарелок: сравнительно высокая пропускная способность по газу и гидродинамическая устойчивость постоянная высокая эффективность в широком интервале нагрузок по газу.
Насадочные колонны. В этих колоннах используются насадки различных типов но в промышленности наиболее распространены колонны с насадкой из колец Рашига. Меньшее гидравлическое сопротивление насадочных колонн по сравнению с барботажными особенно важно при ректификации под вакуумом. Даже при значительном вакууме в верхней части колонны вследствие большого гидравлического сопротивления ее разрежение в кипятильнике может оказаться недостаточным для требуемого снижения температуры кипения исходной смеси.
Для уменьшения гидравлического сопротивления вакуумных колонн в них применяю насадки с возможно большим свободным объемом.
В самой ректификационной колонне не требуется отводить тепло. Поэтому трудность отвода тепла из насадочных колонн является скорее достоинством чем недостатком насадочных колонн в условиях процесса ректификации.
Однако и при ректификации следует считаться с тем что равномерное распределение жидкости по насадке в колоннах большого диаметра затруднено. В связи с этим диаметр промышленных насадочных ректификационных колонн обычно не превышает 08-1 м.
Пленочные аппараты. Эти аппараты применяется для ректификации под вакуумом смесей обладающих малой термической стойкостью при нагревании (например различные мономеры полимеры а также другие продукты органического синтеза).
В ректификационных аппаратах пленочного типа достигается низкое гидравлического сопротивление. Кроме того задержка жидкости в единице объема работающего аппарата мала. К числу пленочных ректификационных аппаратов относятся колонны с регулярной насадкой в виде пакетов вертикальных трубок диаметром 6-20 мм (многотрубчатые колонны) а также пакетов плоскопараллельной или сотовой насадки с каналами различной формы изготовленной и перфорированных металлических листов или металлической сетки.
Недостатки роторных колонн: ограниченность их высоты и диаметра (из-за сложности изготовления и требований предъявляемых к прочности и жесткости ротора) а также высоки эксплуатационные расходы.
3. Описание технологической схемы.
Исходная смесь метиловый-спирт вода поступает в емкость Е1. Из емкости с насосом Н1 подается в подогреватель П где нагревается до температуры кипения 76 С и поступает на тарелку питания 8.Пары GW = поступает в межтрубное пространство дефлегматора Р где при охлаждении холодной водой происходит конденсация дистиллята которая поступает в распределитель R. Из распределителя R часть конденсата в количестве GR = поступает на орошение колонны в качестве флегмы. Дистиллят 2000кгч через холодильник Х2 и через емкость Е3 насосом N3 направляется к потребителю. Охлаждение Х2 производится холодной водой В4.Часть кубового остатка GW = через кипятильник К подогретый водяным паром поступает в нижнею часть колонны а часть кубового остатка Н2 через холодильник Х1 сливается емкость Е2 и насосом N2 относится к потребителю.
ТЕХНОЛОГИЧЕСКАЯ СХЕМА.frw

Наименование среды в
Условное обозначение
Вода прямая (подача)
Паро-жидкостная смесь
Колонна ректификационная
Вентиль регулирующий
Кубовый остаток потреб.
РАСЧЕТКА.doc
Пусть GD и GW – массовые расходы дистиллята и кубового остатка кгчас.
Уравнение материального баланса:
– общий баланс (1) (5 с.319.)
Из системы уравнений материального баланса определяем GD и GW:
GD=7596 кгч GW=12420 кгч.
2. Перерасчёт концентраций из массовых долей в мольные. МНК и МВК – мольные массы НК и ВК кгкмоль.
Определяем число питания:
Равновесный состав смеси сероуглерод-четыреххлористый углерод :
Находим по диаграмме состав – состав (x – y) которую строим по данным о фазовом равновесии разделяемой бинарной системы [1 таб.1024] – мольная доля НК в паре равновесном с жидкостью питания.
Вычисляем минимальное флегмовое число:
Рабочее флегмовое число: R = 13Rmin + 03 [5ст. 321]
R = 13095+ 03 = 1535
3.Определяем уравнения рабочих линий [5. с. 320]:
а) для верхней (концентрационной) части колонны:
б) для нижней (отгонной) части колонны:
4.Определение скорости пара и диаметра колонны
Средние концентрации жидкости:
Средние концентрации пара (по уравнениям рабочих линий):
5.Определяем средние температуры пара и по диаграмме «температура – состав состав» (t – которую строим по равновесным данным
Средние мольные массы пара:
6.Определим средние плотности пара:
Средняя плотность пара в колонне:
7.Определяем температуры флегмы и кубовой жидкости по диаграмме t – x y при xD и xW.
Из справочника находим:
а) плотность жидкого НК при tВ
б) плотность жидкого ВК при tН
Средняя плотность жидкости в колонне:
Максимально допустимая скорость пара в колонне [5. ст.322]
Коэффициент вычисляем по формуле :
где h = 035 м - межтарельчатое расстояние;
q = q0 = 10 м2ч – линейная плотность орошения т.е. отношение объёмного расхода к периметру слива П (длине сливной планки);
k1 = 115 k2 = 1 при атмосферном и повышенном давлениях k3 = 03410-3.
Вычисляем по вышеуказанной формуле:
Определяем мольную массу дистиллята
Средняя температура пара в колонне
Объёмный расход пара в колонне:
Вычислим диаметр колонны
Из каталога “Колонные аппараты” выбираем ближайший диаметр колонны D = 14 м.
Определяем периметр сливной перегородки (П)
8.Определяем среднюю мольную массу жидкости в верхней части колонны.
Объёмный расход в верхней части колонны
Линейная плотность орошения в верхней части колонны
9. Определение числа тарелок и высоты колонны
Строим рабочую диаграмму процесса ректификации т.е. чертим равновесную и рабочие линии процесса. Вписываем прямоугольные треугольники между равновесной и рабочими линиями получаем число теоретических тарелок в верхней и нижней частях колонны: ; .
Средний КПД тарелок равен
Вычислим число действительных тарелок в верхней и нижней частях колонны с запасом 20 %:
Общее число тарелок в колонне: n =10 + 12 = 22
Высота тарельчатой части колонны:
HT = (n – 1)h = (22 – 1)04 = 82 (м)
Гидравлический расчёт колонны
1. Гидравлическое сопротивление тарелки равно сумме потерь напора на сухой тарелке и в слое жидкости: Па
а) верхняя часть колонны
Потеря напора на неорошаемой тарелке
– коэффициент сопротивления; для клапанной тарелки при полностью открытом клапане = 363
– скорость пара в отверстии:
где f – доля свободного сечения тарелки;
– средняя плотность пара в верхней части колонны. Па
Потеря напора в слое жидкости:
– высота сливной планки ориентировочно принимаем 60 мм.
– подпор жидкости над сливной планкой. При прямой сливной планке
где – объёмный расход жидкости в верхней части колонны м3ч.
– средняя плотность жидкости
Определяем сопротивление орошаемой тарелки
б) нижняя часть колонны
Сопротивление сухой тарелки
где – средняя плотность пара в нижней части колонны.
Средняя мольная масса жидкости в нижней части колонны:
Средняя мольная масса питания:
Объёмный расход жидкости в нижней части колонны:
Сопротивление слоя жидкости на тарелке
Сопротивление орошаемой тарелки
Суммарное сопротивление всех тарелок
2. Проверка работоспособности тарелок
Проверка проводится по величине межтарельчатого уноса жидкости или по пропускной способности переливного устройства.
Тарелка работает устойчиво при
– высота слоя вспенённой жидкости в переливном кармане м.
y – вылет ниспадающей струи м.
b – максимальная ширина переливного кармана
– высота слоя невспенённой жидкости в сливном устройстве м.
– относительная плотность вспенённой жидкости. для средневспенивающихся жидкостей.
Высота слоя светлой жидкости
– сопротивление тарелки;
Δ – градиент уровня жидкости на тарелке м. Для клапанных тарелок можно принять Δ = 0005.
Сопротивление движению жидкости в перетоке [5 с. 273]:
– скорость жидкости в минимальном сечении переливного кармана [5 с. 275]:
kж = 080 для среднепенящихся жидкостей;
* – скорость всплывания пузырей грибообразной формы:
– средний коэффициент поверхностного натяжения жидкости при средней температуре в колонне Нм.
Условие (а) выполняется.
Вылет струи [6 с. 199]
Условие (б) выполняется.
Рабочая скорость пара в отверстии тарелки не должна быть меньше минимальной скорости пара в отверстии тарелки обеспечивающей беспровальную работу клапанной тарелки [5 с. 285]:
Тепловой расчёт установки
1. Расход тепла отдаваемого парами воде при конденсации в дефлегматоре:
– теплота конденсации паров Джкг [2 с. 541]
2. Расход тепла получаемого кубовой жидкостью от греющего пара в кипятильнике:
сD и cW при tВ и tН cF при tF [2 с. 562]
3. Расход тепла в паровом подогревателе питания
cF – принята при средней температуре
tнач – температура до подогревателя принимаемая равной 18°С.
4. Расход тепла отдаваемого дистиллятом воде в холодильнике
– принята при средней температуре
tкон – температура после холодильника принимаемая равной 25°С.
5. Расход тепла отдаваемого кубовым остатком воде в холодильнике
Расход греющего пара с давлением и степенью сухостью x =095%.
б) в подогревателе питания:
Всего пара 026 + 002= 028 кгс или 007 тч.
Расход охлаждающей воды при нагреве на 20°С.
св – теплоёмкость воды
б) в холодильнике дистиллята
в) в холодильнике дистиллята
Всего воды 608 + 014 + 046 = 668 кгс или 185 тч.
В данном курсовом проекте в результате проведённых инженерных расчетов была подобрана ректификационная колонна диаметром D = 125 м для разделения смеси cероуглерод-четыреххлористый углерод в которой применяется клапанные тарелки расстояние между которыми h = 035 м. Высота тарельчатой части H = 84 м. Колонна работает в нормальном режиме.
В ряде химических нефтяных пищевых и других отраслях производства в результате различных технологических процессов получают смеси жидкостей которые необходимо разделить на составные части. Для разделения смесей жидкостей и газовых смесей в промышленности применяют способ простой перегонки (дистилляции) перегонки под вакуумом и с водяным паром молекулярной перегонки и ректификации. Ректификацию широко используют в промышленности для полного разделения смесей летучих жидкостей частично или целиком растворимых одна в другой.
Ректификацией называется процесс разделения жидкой смеси на компоненты при этом происходит массообмен т.е. переход вещества из жидкой фазы в паровую и наоборот.
Процесс ректификации осуществляется в ректификационной установке включающей ректификационную колонну состоящую из нижней части в которой происходит удаление легколетучего компонента из стекающей вниз жидкости и верхней (укрепляющей) части в которой происходит удаление легко-летучего компонента его насыщение дефлегматор (обычно представляет собой кожухотрубчатый теплообменник). В ряде случаев в дефлегматоре происходит конденсация всех паров вышедших из колонны. В концевом холодильнике дистиллят охлаждается до заданной температуры. Иногда в дефлегматоре конденсируется лишь часть паров для получения флегмы а полная конденсация и охлаждение происходит в холодильнике.
компоновочка.frw

ЧЕРТЕЖ.cdw

Рекомендуемые чертежи
- 24.01.2023
- 15.04.2023