Расчет ректификационной установки для разделения бинарной смеси Толуол-Ксилол




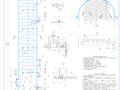
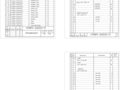
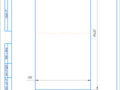
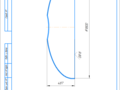
- Добавлен: 25.01.2023
- Размер: 502 KB
- Закачек: 0
Описание
Состав проекта
![]() |
![]() |
![]() ![]() ![]() |
![]() ![]() ![]() ![]() |
![]() ![]() ![]() ![]() |
![]() ![]() ![]() ![]() |
![]() ![]() ![]() ![]() |
![]() ![]() ![]() ![]() |
![]() ![]() ![]() ![]() |
Дополнительная информация
спецификация.frw

Фланец11.cdw

Крышка11.cdw

Патрубок11.cdw

сборочный чертеж11.cdw

общий вид11.cdw

Рекомендуемые чертежи
- 15.04.2023
- 04.04.2021
- 24.01.2023
- 25.01.2023
- 17.03.2024