Расчет рабочих процессов ДВС 8ЧНСП 3А 22/28-2




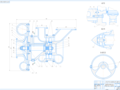
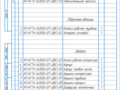
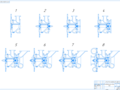
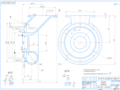
- Добавлен: 25.01.2023
- Размер: 3 MB
- Закачек: 0
Описание
Расчет рабочих процессов ДВС 8ЧНСП 3А 22/28-2
Состав проекта
![]() |
![]() ![]() ![]() |
![]() ![]() ![]() |
![]() ![]() ![]() |
![]() ![]() ![]() |
![]() |
![]() ![]() ![]() ![]() |
![]() ![]() ![]() |
![]() ![]() ![]() ![]() |
![]() ![]() ![]() ![]() |
![]() ![]() ![]() ![]() |
![]() ![]() ![]() ![]() |
![]() ![]() ![]() ![]() |
![]() ![]() ![]() |
![]() ![]() ![]() |
Дополнительная информация
list_2.cdw

shema_komb_dv.frw

list_1.cdw

list_4.cdw

list_5.cdw

list_3.cdw

spec.spw

Рекомендуемые чертежи
- 01.07.2014