Расчет ДВС УЗАМ-3318


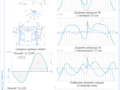
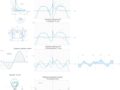
- Добавлен: 04.11.2022
- Размер: 364 KB
- Закачек: 0
Узнать, как скачать этот материал
Подписаться на ежедневные обновления каталога:
Описание
Курсовой проект - Расчет ДВС УЗАМ-3318
Состав проекта
![]() |
![]() ![]() ![]() ![]() |
![]() ![]() ![]() ![]() |
![]() ![]() ![]() |
![]() |
Дополнительная информация
Контент чертежей
график ДВС УЗАМ.frw

А1 график УЗАМ.cdw

Рекомендуемые чертежи
Свободное скачивание на сегодня
Обновление через: 4 часа 12 минут