Проектирование и расчёт рабочих органов харвестеров




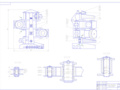
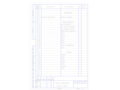
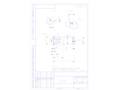
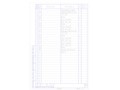
- Добавлен: 25.10.2022
- Размер: 1 MB
- Закачек: 0
Описание
Состав проекта
![]() |
![]() |
![]() ![]() ![]() ![]() |
![]() ![]() ![]() ![]() |
![]() ![]() ![]() ![]() |
![]() |
![]() ![]() ![]() |
![]() ![]() ![]() |
![]() ![]() ![]() |
![]() ![]() ![]() |
![]() ![]() ![]() |
![]() ![]() ![]() |
![]() ![]() ![]() |
![]() ![]() ![]() ![]() |
![]() ![]() ![]() ![]() |
![]() ![]() ![]() ![]() |
![]() ![]() ![]() ![]() |
![]() |
![]() ![]() ![]() |
Дополнительная информация
Втулка 1.cdw

Спецификация1.cdw

Палец.cdw

Втулка.cdw

Спецификация2.cdw

Палец 1.cdw

Харвестерная головка.cdw

пз.doc
Пояснительная записка
ПРОЕКТИРОВАНИЕ И РАСЧЕТ ЗАХВАТНОГО УСТРОЙСТВА5
ПРОЕКТИРОВАНИЕ И РАСЧЕТ СРЕЗАЮЩЕГО УСТРОЙСТВА.26
РАСЧЕТ СУЧКОРЕЗНОГО МЕХАНИЗМА33
ПРОЕКТИРОВАНИЕ И РАСЧЕТ ПРОТАСКИВАЮЩЕГО МЕХАНИЗМА36
ПОВОРОТНАЯ ВАЛОЧНАЯ СКОБА 38
СПИСОК ИСПОЛЬЗОВАННОЙ ЛИТЕРАТУРЫ39 ПРИЛОЖЕНИЯ 40
Лесопромышленный комплекс России включает в себя лесозаготовительную промышленность (заготовка и первичная обработка древесины); лесоперевалочные работы; производства деревообработки. Заготовкой и переработкой древесины занимается более 30 тысяч крупных средних и мелких предприятий расположенных во всех регионах страны.
Деятельность отраслей лесопромышленного комплекса базируется на использовании возобновляемого ресурса – леса. По обеспеченности лесами Россия занимает первое место в мире обладая примерно четвертью мировых запасов древесины.
Современная лесная политика основывается на принципах рационального лесопользования своевременного воспроизводства лесных ресурсов сохранения биологического разнообразия. Важными моментами в реализации этой политики являются развитие системы не сплошных рубок леса в первую очередь рубок ухода и переход на сортиментную технологию лесозаготовок там где это экономически и экологически оказывается более эффективным.
Примером успешного развития рубок ухода сортиментных технологий и соответствующих машин и оборудования могут стать страны Северной Европы а именно Финляндия и Швеция. Именно в этих странах появились первые специальные комплексы машин для заготовки леса по сортиментной технологии – харвестеры и форвардеры.
Харвестер – от английского harvester (жнец машина для уборки урожая) устоявшееся международное определение лесного комбайна (валочно-сучкорезно-раскряжевочной машины).
ПРОЕКТИРОВАНИЕ И РАСЧЕТ ЗАХВАТНОГО УСТРОЙСТВА
Исходные данные представлены в таблице 1.1.
Таблица 1.1 – Исходные данные
Максимальный диаметр обрабатываемого дерева на высоте груди
Минимальный диаметр обрабатываемого дерева на высоте груди
Давление в гидросистеме
Основной конструкционный материал
Проектирование захватного устройства (ЗУ) начинается с разработки компоновочно-кинематической схемы (ККС). ККС строим на основании приведенных в исходных данных диаметров обрабатываемых деревьев D0 и d0. При проектировании указаны значения диаметров на высоте груди D1.3. Для их пересчета в диаметры в плоскости срезания D0 следует умножить значения диаметров на высоте груди на поправочный коэффициент формы ствола.
где q0 – поправочный коэффициент формы ствола по таблице 1 [2] принимаем q0 = 12.
Срединный диаметр Dc м т.е. диаметр на половине высоты ствола определяется по формуле:
где qc – коэффициент зависящий от породы дерева (для сосны – 065).
Вершинный диаметр Dв т.е. диаметр в месте обрезки вершины дерева для хвойных пород принимается 006 м.
Высота дерева H м по второму разряду высот – 29 261м.
Расстояние от плоскости реза до центра масс дерева hт м определяется по формуле:
k – коэффициент зависящий от породы ( для сосны – 037);
H = 29 – высота дерева м.
Расстояние от плоскости реза до центра приложения аэродинамических сил hд м находится по формулам:
При ветровой нагрузке:
Расчётная длина хлыста L м определяется по формуле:
где h – длина обрезаемой вершинной части м; h = 2 3м.
Объём ствола (хлыста) Q м3 для расчётного диаметра зависит от высоты дерева и его породы. При проведении проектировочных расчётов объём хлыста можно приближённо оценить по диаграмме на рис. 1.2 [1]:
Масса ствола (хлыста) Mств кг определяется по формуле:
где = 800 кгм3 – плотность древесины для сосны.
Масса дерева М кг включая массу ствола сучьев хвои и листьев определяется по формуле:
где k – коэффициент отношения массы дерева к объёму кгм3; значения данного коэффициента (в тм3) для деревьев второго разряда высот представлены на рис. 1.3. [1]. Для сосны принимаем k=112 тм³.
Масса кроны Мкр кг принимаем равной разности массы дерева и массы ствола:
Мидель кроны Sкр (проекция кроны на вертикальную плоскость) м3 определяется по формуле:
где - коэффициент формы кроны
– коэффициент густоты заполнения кроны
Hкр – протяжённость (высота) кроны
Dкр – наибольшая ширина кроны.
По таблице 1.3 [1] определяем эти параметры: =067 =045 Нкр=525м Dкр=273м.
Момент инерции дерева Jд кг·м2 относительно перемычки недопила (оси проходящей через плоскость реза) определяется по формуле:
где j – коэффициент равный 021 – 022.
Момент инерции дерева относительно центра масс Jo кг·м2:
Количество сучьев зависит от диаметра ствола. При проектировании машин производящих обрезку сучьев после трелёвки можно принять что число сучьев у обрабатываемой сосны равно 10-18.
Размеры сучьев. У сосны средний диаметр сучка – 5 6 см а максимальны может достигать 15 см.
Угол врастания сучьев – это угол наклона сучьев к стволу. Для сосны принимаем 30°. Величина усилия при срезании сучьев характеризуется следующими данными: для срезания сучка сосны диаметром 4 см – 8 кН.
1 Обоснование расчетного случая нагружения захватных рычагов харвестерной головки
1.1 Натяг дерева при его срезании
На рисунке 1.1 показана схема натяга дерева при его срезании.
Рисунок 1.1 – Расчетная схема натяга дерева захватными рычагами при срезании
Условие исключающее проскальзывание захватных рычагов по стволу при натяге:
где FТР – суммарная сила трения дерева о захватные рычаги и корпус Н;
РН – усилие натяга Н.
Величина усилия натяга должна обеспечить беззажимное срезание дерева удерживая его от оседания. Поэтому необходимо приложить такое вертикальное усилие которое было бы равно силе тяжести самого дерева или несколько больше его.
Суммарная сила трения
где n – число захватов (плоскости где располагаются захватные рычаги) n = 4;
F3 – сила трения корпуса о ствол дерева в контактной точке 3 направленная вдоль ствола Н;
F1 – сила трения ролика о ствол дерева в контактной точке 1 направленная вдоль ствола Н.
Сила трения ролика о ствол дерева в контактной точке 1
где N1 – сила прижима рычага с роликом к стволу Н;
= 057 063 – коэффициент трения стального ролика о корпус дерева.
где N3 – сила нормального давления корпуса харвестерной головки на ствол дерева Н;
= 057 063 – коэффициент трения стального корпуса о ствол дерева.
Для определения силы N3 составим уравнение проекций всех сил на ось Х
где – угол обхвата принимаем = 25°.
Граничное условие удержания дерева при натяге
где МД*g – сила тяжести дерева Н;
МД – масса расчетного дерева кг;
g = 981 мс2 – ускорение свободного падения;
kН = 13 – коэффициент запаса натяга.
где k – коэффициент отношения массы дерева к объему хлыста (кгм3) значение которого в тм3 для деревьев второго разряда лесов по рисунку 1.3 [3] принимаем k = 1120 кгм3;
V – объем ствола (хлыста)по рисунку 1.2[3] принимаем V = 035м3.
Граничное условие удержания дерева
Тогда потребная сила прижима определится с учетом того что число захватов 2:
1.2 Отрыв дерева от пня после его срезания (рисунок 1.2)
Рисунок 1.2 – Расчетная схема отрыва дерева от пня
При отрыве дерева от пня на него действует сила R:
где ФИН – сила инерции Н.
где W – ускорение отрыва дерева от пня мс2.
Предположим что сила трения F равномерно распределена по всем шести контактным точкам т.е. F1 = F2 = =F6.
Граничное условие удержания дерева запишется:
где k = 6 – количество контактных точек.
Тогда граничное условие примет следующий вид:
Потребная сила прижима:
1.3 Перенос дерева в вертикальном положении
При переносе дерева в вертикальном положении на него действуют силы веса МД*g и инерции ФИН (рисунок 1.3) которые стремятся создавая момент относительно точки 6 нижнего захвата разжать захватные рычаги и ножи верхнего уровня.
Центробежная сила ФИН :
где = 05 – угловая скорость поворота манипулятора в горизонтальной плоскости с-1;
L – вылет манипулятора м.
Момент стремящийся разжать захватные рычаги верхнего уровня:
где hцт – высота центра масс дерева м.
Рисунок 1.3 – Расчетная схема переноса дерева
где k – коэффициент зависящий от породы дерева для сосны k = 037;
Н – высота дерева по таблице 1.1[3] принимаем Н = 29 м.
Сила прижима захватного рычага к стволу дерева:
1.4 Подтаскивание дерева за комель при волочащейся вершине
В этом режиме рассматривается подтаскивание максимального расчетного дерева на подъем 15° 20° с ускорением 05g. При этом дерево стремится вырваться из захватного устройства чему способствуют сила трения кроны о землю сила инерции и продольная составляющая силы веса дерева. Дерево в захватном устройстве необходимо обжать рычагами так чтобы суммарная сила трения элементов захватного устройства о ствол в продольном направлении превышала силы стремящиеся вырвать дерево.
Рисунок 1.4 – Схема сил действующих на дерево
Суммарная сила RΣ стремящаяся вырвать дерево из захватного устройства (рисунок 1.5):
где n = 045 – доля силы веса дерева приходящаяся на захватное устройство;
fвол = 065 09 – коэффициент сопротивления волочению кроны;
α – угол уклона местности.
Рисунок 1.5 – Схема сил действующих на дерево со стороны захватного устройства в плоскости верхних рычагов
1.5 Наклон дерева в положение от машины (рисунок 1.6)
Рисунок 1.6 – Расчетная схема при наклоне дерева
где φ – угол наклона дерева от вертикали.
При значениях угла φ близких к 90° при наклоне дерево касается кроной земли и на захватные рычаги харвестерной головки действует не весь вес дерева а приблизительно половина. Поэтому сначала надо определить угол φ при котором крона касается земли.
Рисунок 1.7 – Схема наклона дерева
где НК = 06*Н = 06*29 = 17.4 м – высота кроны дерева;
DК= 02*Н = 02*29 = 5.8 м – наибольшая ширина кроны дерева.
Тогда угол φ принимаем 755°(угол близкий но меньший чем φ).
В данном режиме расчет силы прижима ведем для рычагов верхнего уровня т.к. для них требуется усилие прижима больше чем рычагов нижнего уровня.
Сила трения в верхнем уровне определится:
Для определения силы нормального давления корпуса на ствол дерева составим уравнение проекций всех сил на ось Х:
Определим усилие РВ с которым наклонное дерево давит на рычаги верхнего уровня стремясь их разжать. Составим уравнение равновесия дерева относительно точки О:
Откуда полагая РВ = RВ получаем:
Тогда с учетом всех условий сила прижима рычагов к стволу:
2 Определение сил действующих на захватный рычаг и расчет привода гидроцилиндра рычага
За расчетный режим нагружения принимаем наклон дерева в положении от машины т.к. в этом случае потребная сила давления рычагов максимальна:
В плоскости перпендикулярной плоскости рычага в контактной точке 1 на него действует сила F:
В плоскости движения рычага он нагружен силой N действующей со стороны дерева в точке 1.
Кроме этой силы в точке 1 возникает сила трения рычага о ствол действующая в плоскости движения рычага.
Величина этой силы составляет некоторую часть от силы нормального давления и определяется из условия что линия равнодействующей силы N и Т проходит через точки 1 и 3.
где λ=325º – угол между равнодействующей сил N и Т и силы Т.
Для определения потребного усилия гидроцилиндра составим уравнение равновесия рычага относительно шарнира “рычаг – корпус” (точка О1). Тогда:
где hN hTh P– плечи сил определяемые из ККС(hN = 0160 м hT = 0035 м hP = 0127 м).
Потребное усилие гидроцилиндра:
По усилию гидроцилиндра РГЦ произведем расчет его диаметра причем его работа осуществляется поршневой полостью.
Диаметр гидроцилиндра:
где р = 20 МПа – давление в гидросистеме.
Из ККС определяем потребный ход штока S который в натуральной величине (масштаб 1:1) будет 40 мм. По таблице 5.3 [3] выбираем гидроцилиндр по рассчитанному диаметру D = 50 мм и ходу штока S = 125 мм. Принимаем гидроцилиндр 1-40-125 ГОСТ 6540-80(рисунок 1.8).
Размеры в миллиметрах
Рисунок 1.8 – Гидроцилиндр двойного действия
Точное усилие развиваемое гидроцилиндром:
Произведем корректировку сил нагружающих рычаг захватного устройства:
На рисунке 1.9 представлена модель нагружения захватного рычага.
Рисунок 1.9 – Силы действующие на захватный рычаг
3 Расчет нагрузок в опасном сечении рычага захватного устройства (рисунок 1.10)
Рисунок 1.10 – Опасное сечение рычага
Рассматривая рычаг как балку определим нагрузки в сечении.
Изгибающий момент в плоскости движения рычага:
где – плечи сил определяемые из ККС; (рисунок 1.11)
Рисунок 1.11 – Схема для определения нагрузок в сечении рычага
Изгибающий момент в плоскости перпендикулярной плоскости движения рычага:
где lF – плечо силы F определяемое из ККС ( lF = 00149м)
где r – плечо силы определяемое из ККС (r = 0.0138 м).
Нормальная нагрузка:
где g – угол наклона сечения к линии действия силы N определяется из ККС
Касательные нагрузки:
4 Определение геометрических характеристик сечения захватного рычага
Толщину стенки сечения определим согласно условию (с.91[1]):
Размеры сечения в опасной точке: В = 0065 м Н = 0086 м.
Определим геометрические характеристики сечения
Момент инерции относительно оси Х:
Момент инерции относительно оси Y:
Момент инерции при кручении:
Момент сопротивления при кручении:
Статический момент наружной стенки относительно оси Y:
5 Расчет рычага на прочность
Для сечения рычага показанного на рисунке максимальные нормальные растягивающие напряжения возникают в точке Е. Их величина определяется по формуле:
где – допускаемое напряжение для материала рычага МПа.
где – предел текучести по таблице 3.1[3] для стали 14Г2 по ГОСТ 4543–71.
Условие выполняется.
Максимальное касательное напряжение обусловленное кручением данного сечения
В точках L и M возникают также касательные напряжения t от нагрузок QX и QY определяемые по формуле Журавского:
где Q – поперечная сила Н;
SCT – статический момент отсеченной части м3;
J – момент инерции относительно соответствующей оси м4
l – ширина сечения в рассматриваемом слое м.
Приблизительно эти напряжения можно принять равными:
где [] – допускаемые касательные напряжения материала.
Принимаем [t] = 200 МПа. Тогда суммарные касательные напряжения с учетом кручения и касательной силы в точках L и М:
В точках М М L L середин боковых стенок возникают нормальные напряжения:
С точки зрения оценки нормальных напряжений наиболее опасными являются точки L и М где растягивающие напряжения суммируются. Оценим в этих точках приведенные напряжения sL и sМ по четвертой теории прочности:
Расчет сварного шва проводим по формуле:
где hШ = 0.005 – катет сварного шва (его величина меньше ) м;
[tШ] – допускаемое напряжение для шва.
6 Расчет проушины рычага
В сечении А-А (рисунок 1.12) действует изгибающий момент
где l – высота проушины определяем из ККС (l = 0024 м).
Рисунок 1.12 – Схема проушины рычага
Потребный момент сопротивления
где [s] – допускаемое напряжения металла рычага.
Момент сопротивления сечения:
7 Расчет шарнирных соединений
Основными шарнирными соединениями захватного устройства являются шарниры «рычаг – корпус» «рычаг – гидроцилиндр» и «гидроцилиндр – корпус».
Шарнирные соединения «рычаг – гидроцилиндр» и «гидроцилиндр – корпус» имеют однотипную конструкцию (рисунок 1.13).
Рисунок 1.13 – Шарнирное соединение.
7.1 Расчет шарнира «рычаг – гидроцилиндр»
На палец шарнира действует нормальная к его оси сила РГЦ.
Минимально допустимый диаметр пальца по условию изгиба:
[s] – допускаемое напряжение для материала пальца МПа.
Принимаем dП = 25 мм. Полученное значение диаметра пальца проверяем на срез:
Наружный диаметр втулки:
Давление пальца на втулку шарнира:
где с – ширина втулки мм;
[p] – допускаемое удельное давление на стальную втулку МПа.
7.2 Расчет шарнира «гидроцилиндр – корпус»
Принимаем dП = 25 мм.
Полученное значение диаметра пальца проверяем на срез:
где с – ширина втулки м;
7.3 Расчет шарнира «рычаг – корпус» (рисунок 1.14)
Рисунок 1.14 – Шарнир «рычаг – корпус»
В местах контакта пальца с верхней и нижней втулками на него действуют усилия равные по величине:
где h – расстояние между центрами втулок м;
М – момент силы F приложенной в точке контакта рычага со стволом и направленной вдоль ствола перпендикулярно рычагу относительно точки центра шарнира Н*м.
Кроме сил А1 и А2 в контактных точках пальца с втулками действует сила RШ2.
Сила RШ определяется геометрически с использованием ККС. Для этого на ККС принимается масштаб сил. Все силы действующие на рычаг в плоскости его движения N T PГЦ путем параллельного переноса приводятся в центр шарнира и складываются графически по правилу сложения сил. Суммарная сила измеряется на схеме и через принятый масштаб переводится в размерность силы.
Таким образом в центре верхней втулки будет действовать суммарная сила Р1:
Определяем диаметр пальца по условию среза:
где МИЗГ – максимальный изгибающий момент Н*м.
Принимаем dП = 55 мм.
Допускаемое давление во втулках:
– внутренний диаметр втулки м.
ПРОЕКТИРОВАНИЕ И РАСЧЕТ ЦЕПНОГО СРЕЗАЮЩЕГО УСТРОЙСТВА
1 Определение основных параметров цепного срезающего механизма
Диаметр звёздочки Dзв ( в м) приводящей цепь в движение по формуле:
где Δ = 0015 м – шаг цепи (ПЦУ – 15М)
z = 6 – число зубьев на ободе звёздочки
Длина пильной шины определяется по формуле:
Рисунок 2.1 – Расчётная схема компановки срезающего устройства
2 Компоновка срезающего аппарата на корпусе захватно – срезающего устройства
Центр подвижной системы координат О определяется:
где - расстояние от центра подвижной системы координат до центра пропила.
Положение центра О2 относительно подвижной системы координат О определяется следующим образом:
где φ = 70° - угол врезания пильной шины
R = 003 м – радиус минимального обрабатываемого дерева.
Центральный угол определяется:
где α = 90° - принимаем исходя из соображений компановки.
Принимаем гидроцилиндр 1-40-80 ГОСТ 6540-80 ( Приложении 4 )
3 Кинематика пиления
Скорость надвигания vн ( в мс) пилы рассчитывается из кинематического соотношения при пилении:
где v = 16 мс – необходимая скорость пиления;
t = 60 мм – шаг по режущим зубьм;
c = 1 мм – подача на зуб.
Данные для расчёта берутся из Приложения 5 .
Тогда угловая скорость (в радс) поворота пильной шины равна:
Тяговое усилие на пильной цепи
Усилие резания при пилении Р ( в Н) рассчитывается по следующей формуле:
где k - удельная работа резания при пилении мДжм3;
b = 00081 м – ширина пропила ;
H= 0192 м – высота пропила (H = D0);
где = 16.6 мДжм3-удельная работа резания при распиловке воздушно сухой сосны (Приложение 6 );
= 1 – породный коэффициент для сосны;
= 14 – коэффициент зависящий от степени заострения зубьев (при заточке один раз в смену);
= 09 – коэффициент учитывающий влажность древесины;
= 1 – температурный коэффициент (лето).
Тяговое усилие на пильной цепи Т (в Н) определяется по формуле:
где = 020 – коэффициент трения пильной цепи о пильную шину;
= 1 – коэффициент зависящий от степени затупления зубьев пильной цепи.
Потребная мощность двигателя привода пильной цепи
Потребная мощность двигателя N (в Вт) равна:
где - полный КПД устройств передающих энергию от двигателя к пильной цепи.
где = 095 – КПД пильной цепи;
= 09 – КПД редуктора.
Частота вращения ведущей звёздочки nз (в обс) определяется:
По величине потребной мощности и давления в гидросистеме выбираем аксиально-поршневой гидродвигатель регулируемый реверсивный: 207.20.11 N = 295 кВт
Расчёт пильной цепи на прочность
Полное натяжение пильной цепи S ( в Н) при набегании её на ведущую звёздочку:
где S0 = 100Н – монтажное натяжение;
Рц – натяжение от действия центробежной силы Н;
где = 046 кг – масса одного метра цепи ( Приложение 5 )
Условие прочности для цепи выполняется:
Рисунок 2.2 – Расчётная схема шарнира цепи
7 Расчёт звеньев цепи на разрыв
Касательное напряжение в заклёпках цепи ( в МПа) определяются:
где - допускаемое касательное напряжение на разрыв звеньев цепи;
d1 = 0004 м – диаметр отверстия под заклёпку в боковом звене цепи.
8 Расчёт заклёпок цепи на смятие
Напряжение смятия G ( в МПа) определяются:
где = 150МПа – допустимое напряжение смятия заклёпок;
= 00015 м – толщина боковых звеньев цепи.
9Расчёт заклёпок цепи на разрыв
Удельное давление в шарнирах цепи p (в МПа) равно:
где - допускаемое удельное давление в шарнирах цепи;
= 00063 м – диаметр отверстия под заклёпку в среднем звене цепи;
= 00018 м – толщина среднего звена цепи.
10 Расчёт гидропривода механизма надвигания пилы
Потребное усилие надвигания пильной шины на дерево PH ( в Н) равно:
где = 09 – коэффициент формы затупления зубьев.
При расчёте гидроцилиндра должны выполняться два условия:
- по величине потребного усилия на штоке гидроцилиндра механизма надвигания пилы определяется диаметр dр (в м) этого гидроцилиндра:
где hH = 0280 м – плечо силы надвигания относительно оси поворота пильной шины;
hгц = 008 м – плечо силы развиваемой приводным гидроцилиндром механизма надвигания пилы относительно той же оси.
p = 20*106 МПа – давление в гидросистеме.
- для обеспечения требуемой производительности пиления объёмная подача насоса QH (в м3) привода механизма надвигания должна быть равна:
где = 006 м – ход штока из ККС;
= 08 – КПД гидросистемы;
= 5с – регламентированное время срезания.
11 Расчёт шарнирных соединений
Диаметр пальца dп ( в м) по условию изгиба определяется по формуле:
где аbl – размеры шарнирного соединения принимаются коструктивно.
Наружный диаметр втулки D (в м) равен:
Полученное значение диаметра проверяется на срез по формуле:
Проверяется втулка на смятие:
где dвт = 004м – внутренний диаметр втулки;
с = 0048 м – ширина втулки;
РАСЧЕТ СУЧКОРЕЗНОГО МЕХАНИЗМА
Исходя из задания сучкорезные ножи располагаем два вверху и один внизу.
1 Особенности конструкции
Точность копирования формы ствола и эффективность срезания сучьев определяются прежде всего типом режущего инструмента и конструкцией ножа от чего зависит в итоге качество обрезки сучьев. Сучкорезные ножи имеют такую форму чтобы копировать продольную кривизну ствола и срезать сучья заподлицо с поверхностью ствола без зарезания ножа в древесину последнего. Это достигается за счет придания ножам отрицательного заднего угла резания =3° 6° а также соответствующей формы поперечного сечения (рисунок 3.1).
Рисунок 3.1 – Схема срезания сучка ножом
Срезание сучка происходит примерно в направлении плоскости задней грани ножа: начинается на высоте Н которая по величине несколько больше первой. При заднем угле резания = 4° угле врастания α = 30° 90° и среднем диаметре сучьев d0 = 5 10см высота остатков сучьев на стволе (пеньков) составляет 6 10мм.
Радиус кривизны лезвия ножа (рисунок 3.2):
Рисунок 3.2 – Расчетная схема.
Длина ножа по хорде В:
где = 50° - берём из расчётной схемы.
2 Расчет сучкорезного механизма
При срезании группы сучьев усилие срезания может быть вычислено по формуле В.Г. Нестеренко:
где P1max P2max > Pimax – максимальные значения усилия срезания одиночных сучьев образующих мутовку.
При срезании одного сучка FP =Pmax.
Величина максимального значения усилия резания:
где dc – средний диаметр сучка для сосны dc = 003 005 м;
аП – коэффициент учитывающий породу дерева для сосны аП = 13;
= 1 – поправочный коэффициент учитывающий угол резания (при угле резания = 30° = 30°) град;
Так как на проектируемой харвестерной головке имеются два уровня ножей то первый уровень (верхний ряд) ножей срезает заподлицо 60–70% общего количества сучьев второй уровень (нижний) – остальные 30–40% [1].
Общее усилие резания P1max на ножах первого уровня определится:
где i – среднее количество перерезаемых сучьев для сосны i = 3.
Усилие резания P2max на ножах второго уровня при зачистке некоторого количества остатков сучьев с повторным срезанием:
Расстояние между верхним и нижним уровнем ножей (рисунок 4.1):
где LM – среднее расстояние между мутовками для сосны LM = 035 м;
п – любое целое положительное число.
Рисунок 3.3 – Расстояние между верхним и нижним уровнем ножей
ПРОЕКТИРОВАНИЕ И РАСЧЕТ ПРОТАСКИВАЮЩЕГО МЕХАНИЗМА
1 Потребное усилие протаскивания
Потребное усилие протаскивания РПР должно равняться сумме следующих сил (рисунок 4.1):
где РΣ – наибольшее общее усилие срезания из двух усилий рассчитанных для березы и ели Н;
FТР – сила трения сучкорезных ножей о ствол дерева Н;
FСОПР – сила сопротивления волочению кроны дерева по земле при обработке дерева в харвестерной головке Н;
FИН – сила инерции Н. При разгоне протяжки дерева сила берется со знаком минус при остановке – со знаком плюс;
Рисунок 4.1 – Схема сил для определения усилия протаскивания
Сила трения сучкорезных ножей о ствол дерева Н.
где - усилие прижима ножей к стволу Н;
= 060 – коэффициент трения ножа о дерево;
z = 3 – количество сучкорезных ножей;
Сила сопротивления волочению где М = 392 кг – масса расчётного дерева
g = 981 мс2 - ускорение свободного падения;
n = 045 – доля силы веса дерева приходящаяся на харвестерную головку;
= 07 – коэффициент сопротивления волочению кроны;
α = 17° - угол уклона местности.
где G = - сила тяжести дерева;
= 4 мс – скорость протаскивания;
t = 3 с – время разгоняя и замедления протаскивания дерева.
Усилие прижима одного вальца
где = 2 – количество прижимных вальцов;
= 05 – коэффициент сцепления вальца с деревом.
2 Определение потребной мощности гидромоторов
Усилие протаскивания комлевой части дерева:
Усилие протаскивания сучковой части дерева:
Необходимая мощность привода протаскивающего механизма (в Вт) определяется по значению сопротивления при обработке сучковой зоны:
где = 4 мс – расчётная скорость протаскивания;
=10 – КПД вальцового привода.
Выбираем нерегулируемый гидромотор серии 310 (аналог серии A2F Bosсh Rexroth)
рабочие объем = 160 см3; N = 252 кВт.
ПОВОРОТНАЯ ВАЛОЧНАЯ СКОБА
Харвестерная головка навешивается на конце рукояти или телескопической стрелы манипулятора через поворотный ротатор и связанную с ним скобу валочного устройства. Относительно скобы головка может поворачиваться из вертикального в горизонтальное положение с помощью гидроцилиндра.
Таким образом поворотная валочная скоба является важным конструктивным элементом который остаётся неподвижным относительно самой головки несёт собой крепёжную и ориентирующую функцию и через поворотный ротатор сообщается с самим рабочим органом.
СПИСОК ИСПОЛЬЗОВАННЫХ ИСТОЧНИКОВ
Сюнёв В.С. Рабочие органы харвестеров: проектирование и расчет: Учеб.пособие В.С. Сюнёв А.А. Селивёрстов. Петрозаводск: Изд–во ПетрГУ 2005. 204с.
Баринов К. Н. Проектирование лесопромышленного оборудования: Учебное пособие. К. Н. Баринов В. А. Александров. Л.: Издательство Ленинградского университета 1988. 240 с.
Сюнёв В.С. Справочные материалы и методические указания для курсового и дипломного проектирования В.С. Сюнёв А.В. Родионов. Петрозаводск: Издательство ПетрГУ 2001. 37с.
Рисунок 1 - Компоновочно-кинематическая схема захватного устройства
Рисунок 2 – Компоновочно-кинематическая схема срезающего устройства
Рекомендуемые чертежи
- 01.07.2014