Бульдозер на базе трактора т-500 модернизация рабочего оборудования




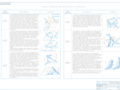
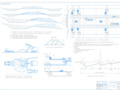
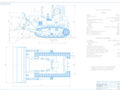
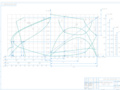
- Добавлен: 25.10.2022
- Размер: 16 MB
- Закачек: 1
Описание
Состав проекта
![]() |
![]() |
![]() ![]() ![]() ![]() |
![]() ![]() |
![]() ![]() ![]() ![]() |
![]() ![]() ![]() ![]() |
![]() ![]() ![]() |
![]() ![]() |
![]() ![]() ![]() ![]() |
![]() ![]() |
![]() ![]() ![]() ![]() |
![]() ![]() ![]() ![]() |
![]() ![]() ![]() ![]() |
![]() ![]() |
![]() ![]() |
![]() |
![]() ![]() |
![]() ![]() ![]() ![]() |
![]() ![]() |
![]() ![]() ![]() ![]() |
![]() ![]() |
![]() ![]() |
![]() ![]() ![]() ![]() |
![]() ![]() ![]() ![]() |
![]() ![]() |
![]() ![]() ![]() ![]() |
![]() ![]() |
![]() ![]() ![]() ![]() |
![]() ![]() |
![]() ![]() |
![]() |
![]() ![]() ![]() |
![]() ![]() ![]() |
![]() ![]() ![]() |
![]() ![]() ![]() |
![]() ![]() ![]() |
![]() ![]() ![]() |
![]() ![]() ![]() |
![]() ![]() ![]() |
![]() ![]() ![]() |
![]() ![]() ![]() |
![]() ![]() ![]() |
![]() |
![]() |
![]() |
![]() |
![]() |
![]() ![]() |
![]() |
![]() |
![]() ![]() |
![]() ![]() |
![]() |
![]() ![]() |
![]() ![]() |
![]() ![]() |
![]() |
![]() ![]() |
![]() ![]() |
![]() ![]() |
![]() |
![]() ![]() |
![]() |
![]() |
![]() ![]() |
![]() |
![]() ![]() |
![]() |
![]() ![]() |
Дополнительная информация
Лист 7 (Гидросхема).dwg

Гидроцилиндры блокировки подвески
Золотник трехпозиционный с электрогид-
предельной нагрузки в раскосе
Схема гидравлическая
СДМ-0.04.00.00.000 Г
Насос постоянной подачи 1 НШ-89
Распределитель секционный 1
Основные гидроцилиндры управления 2
вого механизма гусеничного движителя 2
Соединение разъемное 9
Дроссель с обратным клапаном 1
равлическим управлением 1
Клапан предохранительный 1 Р=10МПа
Дроссель с регулятором 1
Фильтр с переливным клапаном 1
Лист 5 (Деталировка 1).dwg

Сталь 45 Гост 1055-88
Лист 5 (Деталировка 3).dwg

Речь для диплома.docx
Вашему вниманию представляется дипломная работа на тему: «Модернизация рабочего оборудования бульдозера на базе трактора Т-500»
На 2-ом листе проекта представлен общий вид бульдозера с модернизированным рабочим оборудованием. Высота отвала может меняться с 2-х до 27 (м) за счет установленной внутри корпуса основного отвала дополнительной секции.модернизированного отвала увеличена на 20% и составляет 9800 (кг). Выдвижение внутренней секции осуществляется при помощи 2-х гидроцилиндров шаг которых составляет 07(м) а усилие развиваемое ими вполне достаточно для ее подъема. Для обеспечения плавности хода внутренняя секция установлена на боковых роликах. Для предотвращения заклинивания на лобовом листе основного отвала сделана фаска очищающая направляющую поверхность секции. На листе так же представлена техническая характеристика трактора и рабочего оборудования. Мощность двигателя составляет 382 кВт тип трансмиссии – гидромеханическая.
На 3-ем листе показан чертеж рабочего оборудования бульдозера состоящего из отвала толкающих брусьев и раскосов – предохранителей которые было решено поставить взамен стандартных раскосов с целью снижения динамических нагрузок на элементы рабочего оборудования возникающих в процессе работы в момент столкновения с непреодолимым препятствием.
На 4-ом листе проекта показан сборочный чертеж отвала в сложенном состоянии и когда внутренняя секция максимально выдвинута. Приведены габаритные и присоединительные размеры.
Также сборка дополнена сечением и разрезом которые раскрывают суть кинематики выдвижения. На разрезе показан отвал состоящий из внутренней секции корпуса основного отвала гидроцилиндров сменных ножей а также элементов крепления.
На 5-ом листе показаны сборочный чертеж раскоса – предохранителя и деталировка. Раскос – предохранитель состоит из корпусов–гильз штока пружины и крышек соединенных меж собой крепежными элементами. В его корпусе установлен контактный датчик посылающий сигнал золотнику с электрогидравлическим управлением в случае предельного сжатия пружины. Золотник переключается на выглубление отвала.
На 6-ом листе показана тяговая характеристика ЗТМ с ГДТ. Расчеты для ее построения представленные в ПЗ подтверждают что силы тяги развиваемой движителем достаточно для преодоления сопротивлений копания. У двигателя имеется достаточный запас по мощности для выхода на режим 100% буксования.
На 7-ом листе показана гидросхема бульдозера дополненная автоматикой выглубления отвала.
На 8-ом листе показаны схемы и последовательность работ бульдозера по возведению насыпи из боковых резервов маневры бульдозера на планировке площадки и работа бульдозера в копмлексе с экскаватором.
На 9-ом листе представлена технология изготовления детали. Таковой является ось соединяющая гидроцилиндры подъема - опускания внутренней секции и корпус основного отвала. Технология включает 5 операций таких как токарная токарно – чистовая шлифовальная слесарная и контроль.
На 10-ом последнем листе представлены основные технико-экономические показатели проекта. Годовой экономический эффект от внедрения новой техники составляет 1.826.000 руб. Диаграмма текущих затрат по НТ позволяет визуально оценить долю отдельных статей затрат в их общем объеме. График динамики дисконтированного эффекта показывает что срок окупаемости затрат на модернизацию БТ – менее года.
Лист 5 (Раскос).dwg

Проверить момент затяжки болтов;
Смазать смазкой "Литол-24" ГОСТ 21150-87
подвижные соединения.
Раскос-предохранитель
Лист 1 (Анализ вариантов технических решений).dwg

путем увеличения обзорности в транспортном положении. Указан-
ная цель достигается тем
что козырек соединен с отвалом шарнирно и
связан посредством шарнирных тяг с толкающими брусьями
кающие брусья и штанги соединены с базовой машиной перекрестно.
Бульдозер включает отвал 1
соединенный с отвалом шарни-
ром 3. Отвал шарнирно присоединен к раме базовой машины посредством
толкающих брусьев 4 и штанг 5
перекрещивающихся между собой.
Козырек 3 шарнирно соединен тягами 6 с толкающими брусьями. При подъ-
еме отвала козырек штангами 6 наклоняется к отвалу
вокруг шарнира 3. Подъем осуществляется при помощи гидроцилиндра 7.
Перекрестное расположение толкающих брусьев и штанг
нирное соединение козырька с отвалом позволяет сократить высоту ра-
бочего органа в транспортном положении
что улучшает условия труда
В авторском свидетельстве основная цель - повышение производитель-
ности бульдозера. Указаная цель достигается тем
отвал снабжен дополнительным гидроприводом и расположен вогнутостью
в одном направлении с основным отвалом. К базовой машине шарнирно при-
соединены толкафщие брусья 1 основного отвала 2. С основным отвалом
шарнирно соединены толкающие брусья 3 дополнительного отвала 4.
Управление основным и дополнительным отвалами осуществляется со-
ответственно гидроприводами 5 и 6.
Работа начинается при поднятом дополнительном отвале 4 и опущенном
равную толщине стружки
основном отвале 2. Перед основным
отвалом образуется призма волочения 7. После формирования этой призмы
дополнительный отвал 4 опускается на глубину
равную толщине стружки.
При дальнейшем движении бульдозера перед дополнительным отвалом так-
же образуется призма волочения 8. Таким образом
объем перемещаемого
материала включает объем призм - перед основным о дополнительным
Введение шарнирно соединенного отвала и независимого их управления
позволяет повысить производительность бульдозера за счет увеличения
объема перемещаемого материала.
Целью данного изобретения является повышение производительности.
Указанная цель достигается тем
что бульдозерное оборудование снабже-
но соединенными с козырьком гидроцилиндрами поворота отвальной части
и прикрепленной к тыльной стороне козырька дугообразной пластиной с
центром кривизны на оси поворота отвальной части
шарнирно соединена с ножом
а козырек жестко соединен с боковыми стен-
ками. На чертежах изображены вид бульдозерного оборудования и бульдо-
зерное оборудовании при транспортировании грунта.
Оборудование состоит из отвального листа 1
гидроцилиндров 6. Отвальный лист 1 с
боковыми стенками 2 соединен с помощью шарниров 7
с тыловой стороны к отвалу 1 прикреплены рычаги 8
но соединены штоки гидроцилиндров 9
корпуса которых установлены на
козырьке 4. С тыловой стороны козырька 4 установлена криволинейная
В процессе транспортирования
когда впереди отвала образовалась зна-
чительная призма волочения
отвал 1 под воздействием усилий
мых гидроцилиндрами 9
поворачивается на шарнирах 7 по часовой стрел-
ке на определенный угол.
Такая конструкция рабочего оборудования бульдозера обеспечивает сни-
жение энергоемкости процесса транспортирования за счет уменьшения
сопротивления перемещению призмы волочения
благодаря снижению сил
трения грунта по грунту и тем самым служит повышению производитель-
В изобретении предложена новая шарнирная установка колырька. Основ-
ная цель: уменьшение продольного габарита бульдозера в транспортном
положении и увеличение объема перемещаемой призмы волочения грунта
при транспортировании. Бульдозер включает базовую машину 1
толкающими брусьями 3. К отвалу 2 посредством шарнирного соединения 5
соединенный с базовой машиной 1 тягой 7. Подъем и
опускание отвала 2 осуществляется гидроцилиндрами 8
базовой машиной 1 и отвалом 2. При подъеме отвал 2 практически не зап-
так как имеет жесткую связь с толкающими брусь-
ями. Козырек 6 при подъеме отвала поворачивается тягой 7 вокруг шар-
нирного соединения 5 на небольшой угол. Этим и достигается улучшение
обзорности в транспортном положении.
Цель изобретения - повышение производительности работы бульдозер-
ного оборудования. Указанная цель достигается тем
снабжено отвальным скребком и гидроприводом его перемещения
посредством закрепленного на отвале двухступенчатого рычага соединен
с верхней частью скребка
при этом боковые стенки выполнены с направ-
а нижняя часть скребка имеет элементы скольжения
ленные в направляющих боковых стенок.
На отвале 1 подвешен сварной скребок 2
состоящий из лобового листа и
ребер жесткости. Верхняя часть скребка шарнирно соединена с одним
который через шарнир закреплен на отвале 1. Второй ко-
нец рычага 3 шарнирно соединен со штоком гидроцилиндра 4
торого шарнирно закреплен на отвале 1. На нижней части скребка укреп-
которые могут перемещаться в направляющих прорезах 6
выполненных в боковых стенках 7 отвала 1.
При разработке легких и разрыхленных грунтов скребок 2 поднимается в
верхнее положение и служит вспомогательным отвалом
чую площадь отвала 1
и объем перемещаемого грунта.
При разработке налипающих грунтов скребок 2
перемещаясь сверху вниз
срезает налипший грунт
очищая лобовой лист отвала 1.
Целью исследования является модернизация рабочего оборудования
целью его адаптации к рабочим условиям и как следствие увеличение про-
изводительности бульдозера. Отвал 1 меняет высоту с 2
достигается путем выдвижения дополнительной внутренней секции 2
при этом не затрагивается конструкция самого отвала
секция выдвигается в зоне козырька
что позволяет работать как со
так и с увеличенным по высоте отвалом.
На чертежах показаны рабочие положения отвала
когда подвижная секция
втянута в короб основного отвала и на второй проекции когда подвижная
секция максимально выдвинута. Выдвижение происходит при помощи двух
шаг которых составляет 0
м. К козырьку приварены
боковые стенки 3 исключающие просыпание грунта. Для предотвращения
заклинивания на торце переднего листа сделана фаска 4
равляющую поверхность подвижной секции. Для уменьшения сопротивлений
выдвижения подвижной секции внутри короба эта секция установлена на
Модернизация данного вида рабочего оборудования позволяет увеличить
производительность бульдозера
уменьшить себестоимость 1 м
получить положительный экономический эффект от его внедрения.
Модернизация рабочего оборудования
бульдозера на тракторе Т-500
Анализ вариантов технических решений
Описание изобретения
Лист 5 (Деталировка 2).dwg

поверхностей : отверстий +t
Лист 4 (Отвал СБ).dwg

Проверить надежность крепления ножей;
Проконтролировать свободный ход подвижных деталей;
Пальцы крепления гидроцилиндра смазать смазкой "Литол-24"
допускается применять смазку ЦИАТИМ 201
Лист 6 (Тяговая характеристика).dwg

Лист 5 (Деталировка 5).dwg

поверхностей : отверстий +t
Лист 2 (Общий вид).dwg

Тип трансмиссии гидромеханическая;
Максимальная скорость
Тип подвески полужесткая
Ширина звена гусеничной ленты
Масса конструктивная
Масса эксплуатационная
Бульдозерное оборудование
Максимальная высота подъема
отвала над опорной поверхностью
(при погруженных грунтозацепах)
Максимальная глубина опускания отвала
Основной угол резания
Объём призмы волочения
Проверить целостность шлангов гидривода;
Проверить наличие масла в гидросистеме;
Проверить натяжение гусеничной ленты.
Лист 9 (Схемы работ) .dwg

(цифрами показана последовательность мест разработки и отсыпки)
а) - при двухсторонних резервах с укладкой грунта грудами
б) - при двухсторонних резервах с укладкой грунта наклонными слоями
в) - при одностороннем резерве с укладкой грунта наклонными слоями
г) - при одностороннем резерве с укладкой грунта слоями и грудами
Работа бульдозера в комплексе с экскаватором
(стрелками показано направление рабочего хода)
Зарезание 5000-8000 мм
Возведение насыпи бульдозерами насыпи из боковых резервов
I - Разработка грунта в резерве с перемещением в нижний слой насыпи; разравнивание грунта в насыпи;
II - Уплотнение нижнего слоя насыпи;
III - Разработка грунта в резерве с перемещением в верхний слой насыпи и обочины; разравнивание грунта в насыпи;
IV - Уплотнение верхнего слоя насыпи; планировка насыпи
корыта и дна резерва; отделка откосов;
- Схемы движения бульдозера при возведении насыпи;
- Схемы движения катка при укатке;
Укладка грунта грудами вприжим
СДМ-0.04.00.00.000 СР
Маневры бульдозера на планировке площадки
Гребенчатый профиль зарезания
Лист 5 (Деталировка 4).dwg

Лист 3 (Рабочее оборудование СБ).dwg

Проконтролировать свободный ход раскос-предохранителя;
Смазать смазкой "Литол-24" ГОСТ 21150-87 все пальцевые соединения
допускается применение смазок марки ЦИАТИМ 201 ГОСТ 6267-74
ВНИИ НП-242 ГОСТ 20421-74 или других равноценных.
Оборудование рабочее
4 Проектирование технологического процесса изготовления детали.docx
На основе анализа чертежей была выбрана деталь для разработки технологического процесса её изготовления. Этой деталью является палец.
Палец предназначен для подвижного соединения проушин гидроцилиндров подъема – опускания козырька с корпусом отвала бульдозера. Это деталь ступенчатой цилиндрической формы с максимальным диаметром 63 мм и длиной 1975 мм. Чтобы исключить продольное движение оси с одной стороны имеется шляпка диаметром 63 мм а с другой нарезана резьба для навинчивания гайки.
Для облегчения сборки с наружной стороны с торцов пальца сняты фаски размером 4x45° и 2.5х45°.
2 Определение размера партии деталей и типа производства
Если годовой объем выпуска деталей не известен то его рассчитывают. Объем с учетом поставок запасных частей ремонтных и эксплуатационным хозяйствам рассчитывается по формуле:
где m=4 - количество одинаковых деталей на одной машине;
М =35 - количество изготавливаемых за год машин;
- количество деталей изготавливаемых в качестве запасных частей в процентах (20-30%); принимаем =30%;
-процент возможного брака при обработке заготовок (=1-3%); принимаем =3%;
Размер партии деталей определяем из выражения
где t - количество рабочих дней на которое необходимо иметь запас деталей для бесперебойной работы сборочного цеха (для средних деталей t=7 дней);
Ф - число рабочих дней в году;
где Дк- число календарных дней в году Дк=365;
Дв- число выходных дней в году Дв=104;
Дп- число праздничных дней в году Дп=9;
Ф=365-104-9=252 дня.
Приближенно тип производства определяется по количеству деталей в партии.
Тип производства по табл.3.1 [7] – мелкосерийное.
Тип производства влияет не только на построение технологического процесса но и на выбор оборудования приспособлений режущего и измерительного инструментов уровень механизации и автоматизации. Из всего изложенного выше ясно что проектировать технологический процесс не зная типа производства нельзя.
3 Выбор способа получения заготовки
Выбор вида заготовки зависит от конструктивной формы детали ее назначения условий работы материала объема выпуска деталей.
Заготовки из проката (круглого) применяются для деталей по конфигурации приближающихся к какому-либо виду данного проката когда нет значительной разницы в поперечных сечениях детали и следовательно можно при получении окончательной ее формы избежать снятия большого количества металла.
Так как деталь у которой обрабатываются все поверхности выбирается наименее точный прокат как более дешевый. Выберем круглый прокат диаметром 100 мм
Всякая заготовка предназначенная для дальнейшей механической обработки изготавливается с припуском против размеров готовой детали. Припуск представляет собой слой материала удаляемый при обработке необходимый для получения детали заданных размеров и требуемой чистоты её поверхностей. Поверхности не подлежащие обработке припусков не имеют.
Определение величины минимального припуска на обработку симметричных наружных и внутренних поверхностей вращения производится по формуле:
при черновой обработке:
где - высота микронеровностей поверхности на предшествующем переходе для проката ;
- глубина дефектного поверхностного слоя полученного при изготовлении заготовки
- суммарное значение пространственных отклонений взаимосвязанных поверхностей оставшихся после выполнения предшествующего перехода (отклонение от параллельности перпендикулярности соосности симметричности):
где - длина детали мм; =1975 мм;
- погрешность установки при выполняемом переходе =400 мкм.
при чистовой обработке:
Общий припуск на обработку равен сумме промежуточных припусков по всем технологическим переходам процесса обработки - от заготовки до готовой детали.
Действительные припуски на обработку в партии заготовок колеблются в пределах от до .
где - максимальный припуск
- допуск по размеру на предшествующем переходе мм; (стр. 7-12 [8])
- допуск по размеру на выполняемом переходе мм; (стр. 7-12 [8])
Черновая обработка:
Чистовая обработка: ;
Общий припуск на обработку:
Правильность расчётов проверяем по формуле:
где - допуск на заготовку =16 мм;
- допуск на деталь =003 мм;
7=157 - условие выполняется.
При изготовлении детали из проката его минимальный диаметр определяют по формуле:
где - минимальный размер наибольшего диаметра ступени вала; =62.81 мм;
Поскольку прокат по диаметру тестирован то принимается ближайший по сортаменту принимаем диаметр заготовки dз=63 мм; при этом действительный припуск:
где - минимальный диаметр проката мм;
- минимальный размер шейки вала с наибольшим размером мм;
Минимальный припуск на обработку торца заготовки рассчитываем по формуле:
где - высота микронеровностей поверхности на предшествующем переходе для проката =100 мкм;
- глубина дефектного поверхностного слоя полученного при изготовлении заготовки =100 мкм;
- суммарное значение пространственных отклонений взаимосвязанных поверхностей оставшихся после выполнения предшествующего перехода (отклонение от параллельности перпендикулярности соосности симметричности) =20 мм;
- погрешность установки при выполняемом переходе =250мкм.
Максимальный припуск:
где - допуск по размеру на предшествующем переходемм;
- допуск по размеру на выполняемом переходе мм;
Исходя из расчёта припусков в качестве заготовки будем использовать прокат диаметром 63 мм длиной 200 мм.
при черновой обработке:
поверхность №1 - =5.1 мм; поверхность №3 -=13.35 мм;
при чистовой обработке:
поверхность №1 - =0.35 мм; поверхность №3 –=0.3 мм;
диаметр 52.45 мм -=0.45мм.
5 Выбор оборудования приспособлений и инструмента
Выбор станка прежде всего определяется исходя из вида и метода обработки в соответствии с конструкцией и размерами обрабатываемой заготовки.
В связи с тем что тип производства - мелкосерийное то наиболее целесообразно будет применение универсальных станков.
Для токарной обработки с учётом габаритов детали и способом её получения (из прутка) применяем токарно-винторезный станок 1К62.
В единичном и мелкосерийном производстве широко применяется обработка с приспособлениями универсального типа которые обычно являются принадлежностью станков.
Выбор инструмента и материала его режущей части зависит от следующих основных факторов: вид станка метода обработки режимов и условий работы материала обрабатываемой детали ее размера и конфигурации требуемых точности и чистоты обработки вида производства. Исходя из всех этих факторов выбираем резец с пластиной из твёрдого сплава - Т5К10.
Измерительный инструмент выбирается в зависимости от точности и формы измеряемой поверхности а также типа производства. При единичном и мелкосерийном производствах применяется измерительный инструмент общего назначения (штангенциркули микрометры и др.).
6 Определение режимов обработки заготовки
По основным видам станочных работ режимы устанавливают в такой последовательности:
-определяется глубина резания;
-исходя из глубины резания устанавливается подача;
-по глубине резания подаче и стойкости инструмента определяется скорость сила и мощность резания.
Подача при черновой обработке выбирается с учетом ограничивающих ее факторов: жесткость и прочность системы СПИД мощность привода станка [8].
Для поверхности №1 при диаметре заготовки 63 мм и глубине резания
tр=5.1мм подачу для черновой обработке выбираем из интервала S=06-12 ммоб размер державки резца от 20х25 диаметр детали от 60 до 100мм [8].
Принимается S=06ммоб.
Скорость резания рассчитывается по формуле [8]:
где Т - стойкость резца Т=60 мин.;
S - подача S =06 ммоб.
t - глубина резания t =5.1 мм.
Значение коэффициентов - Сv Kv и показателей степеней m x yv приведены в соответствующих таблицах [8 с.262-269].
Сv =350; Kv =0.742; yv =035; m=02.
По расчётной скорости определяем частоту вращения шпинделя:
где d - диаметр обрабатываемой поверхностиd=63мм;
Полученное значение частоты вращения для станков со ступенчатым его изменением необходимо скорректировать по станку выбирая ближайшее меньшее.
Ряд чисел оборотов определяется так же как и ряд подач.
к - число передач вращения шпинделя к=23.
n1=125; 15738; 19814; 24946; 31407; 39541; 49783; 62676; 7891; 99348; 125079; 157474; 19826; 24961; 314258; 395651; 498124; 627139; 789568; 994066; 1251529.
Принимаем n=498.124 обмин;
Для проверки возможности осуществления выбранных режимов обработки проводится проверка их по ограничивающим факторам. С этой целью прежде всего определяется сила резания.
Ее значение определяется по эмпирическим формулам значение показателей степени в которых для различных видов обработки приведены в таблицах [8].
где S - подача S =06ммоб.
t - глубина резания t =5.1 мм;
V-скорость резания V= 107.258 ммин;
Значение коэффициентов Ср Kр и показателей степеней np x р y р приведены в соответствующих таблицах [2 с.264-275]:
Ср =300; Kр =0.808; yр =075; np =-015.
При обработке резцами прочность проверяется расчетом на изгиб от действия :
где В Н - соответственно ширина и высота державки резца В=20 мм Н=25 мм;
l - вылет резца l=40 мм.
[] - допустимое напряжение для державки резца []=20 МПа
81.85 Н10219077 Н следовательно условие выполняется.
Мощность резания Nрез кВт рассчитывается по формуле [8]:
Расчетная мощность резания Nрез сравнивается с мощностью электродвигателя станка Nэ :
где - КПД станка ( = 0708).
условие выполняется.
Для поверхности №3 при диаметре заготовки 63 мм и глубине резания tр=13.35 мм принимаем для 1-ого прохода tр=8.35 мм; для 2-ого прохода tр=5 мм.
Подачу для глубины резания tр=8.35 мм выбираем из интервала S=06-12 ммоб размер державки резца от 20х25 диаметр детали от 60 до 100мм [8].
Скорость резания рассчитывается по формуле (4.15);
t - глубина резания t =8.35 мм.
Значение коэффициентов - Сv Kv и показателей степеней m x yv приведе ны в соответствующих таблицах [8 с.262-269].
По расчётной скорости определяем частоту вращения шпинделя по формуле (4.16):
Полученное значение частоты вращения для станков со ступенчатым его изменением скорректируем по станку выбирая ближайшее меньшее.
Из полученного ранее ряда чисел оборотов принимаем n=498.124обмин;
По формуле (4.18) определяем силу резания:
Производим проверку резца на прочность используя выражение (4.19):
В=20 мм Н=25 мм; []=20 МПа
29.584 Н10219077 Н следовательно условие выполняется.
Мощность резания Nрез кВт рассчитываем по формуле (4.20):
Расчетную мощность резания Nрез сравниваем с мощностью электродвигателя станка Nэ :
Подачу для глубины резания tр=5 мм выбираем из интервала S=04-10 ммоб размер державки резца от 20х25 диаметр детали от 60 до 100мм [9].
Принимается S=04ммоб.
S - подача S =04 ммоб.
t - глубина резания t =5 мм.
Значение коэффициентов - Сv Kv и показателей степеней m x yv приведены в соответствующих таблицах [9 с.262-269].
Из полученного ранее ряда чисел оборотов принимаем n=789.568 обмин;
56.735 Н10219077 Н следовательно условие выполняется.
7 Режим резания для шлифовальной обработки
По табл.55 [8] для предварительного шлифования диаметра 52.45 мм с припуском =03 мм принимаем:
-скорость вращательного движения заготовки мс;
-глубину шлифования t=0025 мм;
-скорость вращательного движения шлифовального круга мс;
Число проходов определяем из выражения:
Продольную подачу круга определяем по формуле:
где В-толщина круга мм; В=8 мм;
По табл.55 [8] для окончательного шлифования диаметра 52.15 мм с припуском =0.15 мм принимаем:
-глубину шлифования t=0.015 мм;
8 Определение нормы времени
Норма времени входит в число основных факторов технологического процесса. Она служит основой для расчета оплаты труда калькуляции себестоимости детали расчета длительности производственного цикла определения количества станков инструментов и исполнителей.
При выборе оптимальных вариантов технологического процесса норма времени является одним из основных критериев.
При определении нормы времени на механическую обработку одной детали определяем норму времени отдельно для каждой операции.
9 Определение нормы времени токарно-черновой операции
Норма штучного времени равна [7]:
где t0 - основное (технологическое) время мин.;
tB - вспомогательное время на операцию мин.;
Вспомогательное время затрачивается на выполнение вспомогательных переходов: установку переустановку и снятие заготовки пуск и остановку станка изменение режимов обработки в процессе выполнения операций измерения и контроль качества заготовки готовой детали и т.д.
t00 - время на операционно-техническое обслуживание и естественные надобности мин.
Величина t00 составляет 46% от tШТ..
Основное время при обработке заготовок на металлорежущих станках:
где L - расчетная длина обработки с учётом врезания и перебега инструмента мм:
S - подача мм на один оборот S = 06ммоб.;
п-частота вращения заготовки или инструмента обмин.;
L =135 + 2 + 2 = 139 мм.
где 038 мин - время на установку детали на токарном станке при массе 2.5 кг (табл. 71 стр. 132) [8];
6мин - время при грубой обработке в 1 проход (табл. 70 стр. 131) [8].
Сумма основного и вспомогательного (неперекрываемого) времени составляет оперативное время:
t=tо+tв=0.465+1.08=1.545 мин; (4.27)
Таким образом штучное время равно:
Подготовительно-заключительное время затрачиваемое на получение задания знакомство с работой наладку оборудования и приспособлений сдачу выполненной работы и т.д. определяется по нормативам в нашем случае:
Нормирование по штучному времени производится в массовом производстве. В серийном производстве определяется штучно-калькуляционное время:
где n - количество деталей в партии; n=10 шт.;
Квалификация рабочего устанавливается по тарифно-квалификационному справочнику -5-ый разряд.
3 Расчет на прочность элементов рабочего оборудования.docx
Расчет пальца соединяющего толкающий брус с отвалом производим по наибольшему действующему на него усилию которое определяется из максимальной тяговой мощности развиваемой бульдозером.
В качестве материалов для изготовления пальцев и осей в основном используют сталь 45 с НВ=170-217 (нормализированная) с т= 320 МПа; или сталь 45 с НВ=229-269 (улучшенная) с т=450 МПа.
Расчетная схема имеет следующий вид.
Рисунок 3.1 Схема сил действующих на палец и эпюры изгибающих моментов
В данной схеме RA=RB=3362=168 кН то есть половина тяговой нагрузки – нагрузка приходящуюся на одну проушину.
Наиболее опасное сечение пальца располагается на расстоянии
Изгибающий момент в наиболее опасном сечении определяем по следующей формуле:
Условие прочности имеет следующий вид :
где W - момент сопротивления изгибу м3;
Для круглого сплошного сечения W=
где d-диаметр пальца в рассматриваемом сечении; в нашем случае d=01 м;
- допускаемое нормальное напряжение при изгибе МПа;
Выберем для материала пальца - сталь 45 (нормализированная) с учетом его работы при переменной нагрузке используя данные [6] принимаем =320 МПа;
=3167 МПа []изг=320 МПа
следовательно условие прочности выполняется.
7 Заключение.docx
Бульдозер с данным видом рабочего оборудования может работать как со стандартным так и с увеличенным по высоте отвалом что делает процесс копания и перемещения адаптивным к рабочим условиям. Отвал снабженный дополнительной выдвижной внутренней секцией способствует увеличению производительности за счет увеличения высоты что в свою очередь ведет к увеличению призмы грунта волочения.
Данный вывод подтверждается расчетом технико-экономических показателей проекта. В ходе выполнения дипломного проекта мной были подробно изучены принцип и схемы работы бульдозера конструкции рабочего оборудования а так же устройств повышающих производительность.
Выполнение дипломного проекта способствовало закреплению навыков пользования программами ЭВМ технической литературой документацией а так же позволило реализовать свой творческий потенциал. Эта заключительная стадия обучения помогает в дальнейшей работе инженера-механика.
2 Расчет основных параметров бульдозера.docx
1 Расчет сопротивления грунта копанию
Расчет силы сопротивления грунта копанию производим для наиболее тяжелых условий работы бульдозера когда он осуществляет копание и перемещение грунта а призма волочения грунта достигает максимального объема при поднятом козырьке. Полученное значение сопротивления сравним с возможной максимальной силой тяги.
У бульдозера с неповоротным отвалом будут возникать следующие силы сопротивления движения [1]:
Ркоп = Ррез + Ртр + Рп +Рв (2.1)
где Ррез - сила сопротивления грунта резанию:
где кг – коэффициент удельного сопротивления грунта резанию для расчетов возьмем грунт 3 категории для которого кг = 6000÷12200 кгсм2 Возьмем 1000 кНм2 с учетом перевода из кгс в Н
В0– длина отвала В0=48 м;
hр – глубина резания hр =03 м.
Ррез = 10004803=1440 кН
Ртр – сила трения ножа о грунт
где 2 – коэффициент трения грунта по стали возьмем значение для среднего суглинка 2 = 05
Ртр = 05051440 = 360 кН
Рп – сила сопротивления перемещению призмы волочения грунта
Рп = 1Gпcosα H (2.4)
где - коэффициент трения грунта по грунту; =066 -для суглинка;
α – угол наклона к поверхности горизонта. Примем наклон поверхности α = 0 - работа на горизонтальной плоскости.
- вес призмы волочения грунта Н;
где - объемный вес грунта =1800 Нм3;
- длина отвала =48 м;
- высота отвала =27 м;
- угол естественного откоса грунта град; для глины =35;
- коэффициент разрыхления грунта; для глины =13;
Рп = 0663461 = 228 кН.
- сила трения грунта при движении вверх по отвалу Н;
Рв = 2Gпcos2 γ (2.6)
γ – угол резанья отвала γ =50
Рв = 05346041 = 70 кН.
Р коп = 1440+360+228+70 = 2098 кН
Сопротивление перемещению бульдозера [1]:
где G- сила тяжести машины. G=58300 кг.f-коэффициент сопротивления передвижению принимаем равным 01.
Суммарное сопротивление равно сумме Pf и Рдв [1]:
Pсум = 58+2098=2156 кН;
Сравним это значение с максимальной силой тяги которая определяется как [1]:
Tmax =084075300981=3363 кН
63 кН ≥ 2156 кН - условие выполняется.
Изменяя высоту отвала можно добиться оптимального соотношения скорости перемещения и объёма перемещаемой призмы грунта.
2 Расчет производительности бульдозера
Расчет производительности осуществляем для глины что соответствует грунтовым условиям используемым для построения тяговой характеристики – грунт связный плотный свежесрезанный.
Эксплуатационная производительность бульдозера при резании и перемещении грунта определяется по формуле [1]:
где - объем призмы грунта перемещаемого перед отвалом м3;
- коэффициент использования рабочего времени; принимаем =0.9;
- продолжительность рабочего цикла мин;
где - длина отвала м;
- высота отвала без учета козырька м;
- коэффициент разрыхления грунта; для глины =129;
Произведем расчет для двух случаев: для сложенного и выдвинутого положения дополнительного отвала.
Для сложенного положения отвала:
Для выдвинутого положения:
Продолжительность рабочего цикла определяется из выражения:
где и - соответственно пути резания грунта перемещения призмы волочения и холостого хода км; принимаем =01 км;
Путь резания грунта приближённо вычислим по формуле [1]:
где Sсг – площадь срезаемой стружки грунта Sсг=hl
и - средние действительные скорости движения бульдозера при резании грунта и перемещении призмы волочения кмч;
- средняя теоретическая скорость движения бульдозера на обратном холостом ходу.
и - время затрачиваемое на разворот бульдозера переключение передач а также подъем и опускание отвала мин; принимаем =03 мин =01 мин =004 мин;
Полагая что копание грунта осуществляется на первой рабочей передаче и режиме максимальной тяговой мощности т.е.
где - коэффициент использования силы тяги бульдозера учитывающий отклонение работы бульдозера от режима максимальной тяговой мощности определяемого силой ; ;
- наибольшая допустимая сила тяги при кратковременной работе кН; согласно тяговой характеристике (Лист 3 дипломного проекта) =435 кН; Ткоп=09435=3915 кН; и приближенно приняв что при перемещении грунта объем призмы волочения остается постоянным т.е. Тп =Рп=356 кН по тяговой характеристике бульдозера определяем значения
Среднюю теоретическую скорость движения бульдозера на обратном холостом ходу определяем по технической характеристике бульдозера Т-500 при его движении на задней 3-ей передаче =1091 кмч.
При объеме призмы =11.17 получим:
При объеме призмы =15.27 получим:
При объеме призмы =1938 получим:
То есть производительность при поднятом дополнительном козырьке больше приблизительно в 13 раза по сравнению с опущенным.
На основании полученных данных производительностей построим график зависимости производительности от величины высоты отвала (рисунок2.1).
Рисунок 2.1 - Зависимость производительности от высоты отвала
3 Тяговый расчет бульдозера
3.1. Исходные данные
Для выполнения тягового расчета бульдозера необходимы следующие исходные данные:
-номинальное число оборотов коленчатого вала обмин: 1600
-номинальная мощность кВт: 404
-номинальный крутящий момент Н·м: 2310
-часовой расход топлива при номинальной мощности кгч: 754
-удельный расход топлива при номинальной мощности гкВт·ч: 218
-максимальный крутящий момент Н·м: 2470
-часовой расход топлива соответствующий максимальному крутящему
-число оборотов коленчатого вала на холостом ходу обмин: 1840
-часовой расход топлива на холостом ходу кгч: 126
-тип: гидромеханическая;
Для построения тяговой характеристики бульдозера необходимы следующие исходные данные:
-механическая (регуляторная) характеристика двигателя ЯМЗ 850.10;
-вид грунта его состояние и влажность;
В качестве расчетных грунтовых условий принимаем связный плотный свежесрезанный грунт при отношении действительной влажности грунта к оптимальной влажности равном .
-коэффициент сопротивления качению гусеничного движителя ; для расчетных грунтовых условий =008;
-коэффициент сцепления гусеничного движителя с грунтом ; для расчетных грунтовых условий =09;
-вес бульдозера: G=58300 кг;
-радиус начальной окружности ведущей звездочки гусеничного движителя: =07 м.
3.2 Расчет и построение тяговой характеристики
Предварительно необходимо осуществить построение регуляторной характеристики двигателя (рисунок 2.2).
Координаты характерных точек характеристики и при заданных значениях и представляющих собой координаты точки будут:
Зависимость на регуляторной ветви характеристики двигателя (участок ) близка к линейной поэтому текущее значение при изменении в диапазоне от до 0 будет определяться выражением [2]:
Рисунок 2.2 - Регуляторная характеристика двигателя ЯМЗ 850.10
Зависимость на безрегуляторной ветви характеристики двигателя (участок ) может быть построена по формуле В.Н. Болтинского [3]:
где - коэффициент приспособляемости двигателя;
- коэффициент снижения частоты вращения коленчатого вала двигателя[3]:
Кривую можно заменить прямой . В этом случае текущее значение при изменении в диапазоне от до будет:
Если воспользоваться указанными допущениями то приближенно основная зависимость двигателя во всем рабочем диапазоне будет представлена двумя прямыми линиями и .
После этого строим производную зависимость используя выражение [3]:
Она будет выражаться прямыми и .
Построение тяговой характеристики бульдозера ЯМЗ 850.10 осуществляем в следующем порядке.
) Во втором квадранте размещаем регуляторную характеристику дизельного двигателя перестроенную в функции крутящего момента а в первом строим тяговую характеристику машины (лист №3 графической части курсового проекта).
) Строим основную зависимость - кривую коэффициента буксования гусеничного движителя в функции силы тяги применяя формулу д.т.н. проф. Н.А. Ульянова [3]:
где А В и n - постоянные коэффициенты зависящие от грунтовых условий; для указанных выше грунтовых условий А=0.05; В=1.76; n=12 [4].
Т - текущее значение силы тяги движителя при котором определяется коэффициент буксования Н;
R - нормальная реакция грунта на гусеничный движитель Н; принимается равной весу бульдозера G=58300 кг = 57134 кН.
Задаемся значениями относительной силы тяги .
При TR = 01; T = 01*G = 01*57134 = 5713 кН;
При TR = 02; T = 02*G = 02*57134 = 1142 кН;
При TR = 03; T = 03*G = 03*57134 = 1714 кН;
При TR = 04; T = 04*G = 04*57134 = 2285 кН;
При TR = 05; T = 05*G = 05*57134 = 2857 кН;
При TR = 06; T = 06*G = 06*57134 = 3428 кН;
При TR = 07; T = 07*G = 07*57134 = 4000 кН;
При TR = 08; T = 08*G = 08*57134 = 4571 кН;
При TR = 09; T = 09*G = 09*57134 = 5142 кН;
При TR = 095; T = 095*G = 095*57134 = 54285 кН;
) Рассчитываем силу сопротивления качению гусеничного движителя и откладываем ее значение влево от точки [4] [5].
где - коэффициент сопротивления качению гусеничного движителя; для расчетных грунтовых условий =0.08;
Pf = 008*57334 =457 кН.
) В первом квадранте для первой передачи строим график устанавливающий зависимость крутящего момента на коленчатом валу двигателя
() от окружной силы гусеничного движителя ().
Для этого отложив значение =100% и опустив из точки перпендикуляр на ось абсцисс (точка ) найдем максимальное значение силы тяги определяемое условием сцепления гусеничного движителя с грунтовой поверхностью. В нашем случае =4200 кН.
После этого определяем значение номинальной силы тяги для этого по оси ординат откладываем значение коэффициента буксования а затем из точки опускаем перпендикуляр на ось абсцисс и тем самым получаем значение =256 кН.
Проведя вертикаль из точки и горизонталь через точку получим точку их пересечения которую необходимо соединить с началом координат окружной силы гусеничного движителя – точкой . Тогда будет построен луч устанавливающий зависимость между крутящим моментом двигателя и окружной силой гусеничного движителя.
Передаточное число трансмиссии бульдозера на первой рабочей передаче определяем из выражения [4]:
где - радиус начальной окружности ведущей звездочки гусеничного движителя м; =065 м;
- кпд механической части трансмиссии; принимаем =086;
При копании грунта бульдозером часто возникают перегрузки которые могут вызвать либо полное буксование гусеничного движителя либо остановку двигателя если его мощности недостаточно. Остановка бульдозера при перегрузке из-за заглохания двигателя нежелательна так как с одной стороны усложняет управление машиной из-за необходимости быстрой реакции оператора а с другой - это приводит к весьма нежелательным частым перегрузкам двигателя и работе на безрегуляторной ветви характеристики. Если же имеется некоторый запас мощности двигателя обусловливающий возможность полного буксования то это упрощает управление бульдозером и создает более благоприятные условия работы двигателя. Поэтому необходимо определить значение силы тяги гусеничного движителя соответствующее части максимального значения крутящего момента двигателя используемого для привода ведущей звездочки - .
Для этого через точку проводим горизонталь до пересечения с лучом а затем из точки опускаем перпендикуляр на ось абсцисс. После этого устанавливаем величину =430 кН.
В соответствии с изображениями изложенными выше должно соблюдаться условие [4] [5].
где - коэффициент сцепления гусеничного движителя с грунтом; для расчетных грунтовых условий =09;
В нашем случае: Тmax = 430 кН ≥ T = 420 кН
Для исключения усложнения графических построений приведенные выше расчеты на листе №3 не отражены.
Далее необходимо произвести перерасчет передаточного числа первой рабочей передачи по формуле [4] [5].:
Для обеспечения запаса мощности двигателя обусловливающего возможность полного буксования колес указанная выше формула примет вид [4] [5]:
Согласно указанным выше соображениям величина максимальной силы тяги которая может быть получена на первой передаче при работе двигателя на режиме максимального крутящего момента будет определяться выражением:
Зависимость может быть получена путем соединения начала координат окружной силы гусеничного движителя с точкой полученной путем пересечения горизонтальной прямой проходящей через точку и вертикальной прямой проходящей через точку .
) Строим основную зависимость действительной скорости машины в функции силы тяги - .
Для этого задаемся некоторым значением силы тяги откладываем его на графике (отрезок ) а затем восстанавливаем перпендикуляр из точки до пересечения с лучом . Через полученную точку проводим горизонталь до пересечения с кривыми регуляторной характеристики двигателя (точки и ). Проектируя точку на ось абсцисс находим частоту вращения коленчатого вала соответствующую принятому значению силы тяги .
Определив значение (отрезок ) рассчитываем действительную скорость используя зависимость [3]:
и наносим полученное значение на график (точка ).
Выполнив указанные построения и расчеты и получив достаточное количество точек строим кривую . Крайние значения при построении кривой в данном случае можно определить следующим образом.
Максимальное значение будет на холостом ходу машины когда =0 и . Для определения частоты вращения коленчатого вала двигателя необходимо через точку провести горизонталь до пересечения с кривой а затем полученную точку спроектировать на ось абсцисс и определить частоту вращения коленчатого вала двигателя на холостом ходу машины . В нашем случае =1120 обмин. Тогда:
Величину откладываем на оси ординат (отрезок ).
Минимальное значение действительной скорости так как остановка машины при тяговой перегрузке происходит вследствие полного буксования гусеничного движителя.
Ввиду сложности точного определения значений коэффициента буксования из построений для их расчета необходимо воспользоваться приведенной ранее формулой.
Для =60 кН имеем:TR= 60462=013 из построений =1694 обмин;
Для =120 кН имеем: TR= 120462=0 26 кН; из построений =1678 обмин;
Для =180 кН имеем: TR= 180462= 0 39 кН; из построений =1662 обмин;
Для =240 кН имеем: TR= 240462=0 52 кН; из построений =1646 обмин;
Для =300 кН имеем: TR= 300462= 0 65 кН; из построений =1630 обмин;
Для =360 кН имеем: TR= 360462= 78 кН; из построений =1614 обмин;
Для =420 кН имеем: TR= 420462= 0 91 кН; из построений =1600 обмин; d= 10%
) Строим основную зависимость тяговой характеристики бульдозера кривую часового расхода топлива двигателем в функции силы тяги .
Часовой расход топлива при силе тяги может быть найден если отложить в первом квадранте (отрезок ). Получив таким образом достаточное количество точек строим кривую .
) Осуществляем построение производных зависимостей тяговой характеристики бульдозера: кривой тяговой мощности в функции силы тяги - ; кривой удельного расхода топлива в функции силы тяги -; кривой тягового кпд в функции силы тяги - .
Кривая тяговой мощности строится на основании расчетов по формуле [3]:
путем подстановки различных значений и соответствующих им величин .
При силе тяги значение определяется отрезком .
Из построений следует что:
При =0; =40278=1.11 кмч;
При =60 кН; мс; =303 * 0278= 084 мс
Nt = 084*60 = 50 кВт;
При =120 кН; мс;=298 * 0278 = 083
Nt =083*120 = 9941 кВт;
При =180 кН; мс; =293 * 0278 = 081
Nt = 081* 180 = 146 кВт;
При =240 кН; мс;=289*0278=08
Nt =08*240=1928 кВт;
При =300 кН; мс;=283*0278=0786
Nt =0786*300=2360 кВт;
При =360 кН; мс;=268*0278=0745
Nt =0745*360=2682 кВт;
При =420 кН; мс;=20*0278=055
Nt =055*420=233 кВт;
Кривая удельного расхода топлива строится с применением формулы [3]:
Для режима работы значение определяется отрезком а величина - отрезком . Их отношение представленное отрезком выражает удельный расход топлива при работе бульдозера на режиме .
При =60 кН; =46 кгч; =50 кВт;
При =120 кН; =52 кгч; =9941 кВт;
При =180 кН; =60 кгч; =1460 кВт;
При =240 кН; =75 кгч; =1928 кВт;
При =300 кН; =80 кгч; =2360 кВт;
При =360 кН; =90 кгч; =2682 кВт;
При =420 кН; =82 кгч; =233 кВт;
Кривую тягового кпд строим пользуясь зависимостью [3]:
В данном случае обозначено отрезком . Для указанного режима т.е. величина - отрезок в свою очередь величину определяем по регуляторной характеристике двигателя.
Из построений и расчетов получаем:
При =60 кН; =50 кВт; 382 кВт;
При =120 кН; =998 кВт; 385 кВт;
При =180 кН; =1460 кВт; 388 кВт;
При =240 кН; =1928 кВт; 392 кВт;
При =300 кН; =2360 кВт; 395 кВт;
При =360 кН; =268 кВт; 401 кВт;
При =420 кН; =233 кВт; 404 кВт;
Полученные при расчете данные используем для построения выходной характеристики системы ДВС-ГДТ и далее тяговой характеристики.
4 Описание гидравлической схемы бульдозера Т-500
Гидравлические схемы современных бульдозеров предусматривают агрегатирование на гусеничном или пневмоколесном тягаче различного навесного оборудования. Гидропривод бульдозеров должен обеспечивать подъем опускание изменение углов наклона и перекоса отвала а также позволять установку блока автоматического управления бульдозерным оборудованием.
Гидравлическая схема бульдозера Т-500 представлена на листе №8 графической части дипломного проекта и включает следующие элементы: бак 1 насос постоянной подачи 2 секционный распределитель 3 гидроцилиндры 4 подъема и опускания отвала бульдозера гидроцилиндры 5 подъема и опускания дополнительной секции отвала гидроцилиндры 6 блокировки подвески ходового механизма гусеничного движителя. Кроме того в гидравлическую схему входят: гидрозамок 7 разъемные соединения 8 дроссель с обратным клапаном 9 трехпозиционный золотник 10 с электрогидравлическим управлением двухпозиционный золотник 11 дроссель с регулятором 12 манометры 13 термометр 14 фильтр 15 с переливным клапаном.
Из бака 1 рабочая жидкость подается насосом 2 в напорную секцию распределителя 3. Четырехпозиционный золотник А направляет поток жидкости в гидроцилиндры 4 подъема и опускания отвала бульдозера. Трехпозиционные золотники Б и В управляют соответственно гидроцилиндрами 5 и 6 подъема и опускания дополнительной секции отвала и блокировки подвески ходовой части трактора.
В штоковой линии гидроцилиндров подъема и опускания отвала бульдозера установлен дроссель 9 с обратным клапаном который обеспечивает сплошность потока жидкости и замедление скорости опускания отвала. Присоединение гидроцилиндров к распределителю и соединение некоторых других гидролиний осуществляется с помощью быстроразъемных муфт 8 с обратными клапанами. Применение этих муфт уменьшает потери жидкости при выполнении монтажных работ и исключает попадание в гидросистему внешних загрязнений и влаги. Гидрозамок 7 предназначен для стабилизации положения отвала.
В гидравлической схеме предусмотрена возможность автоматического управлением отвалом бульдозера с помощью трехпозиционного электрогидравлического золотника 10 который в зависимости от электрического сигнала специальных датчиков соединяет поршневые или штоковые полости гидроцилиндров с напорной линией насоса. Автоматическое управление дает возможность поддерживать постоянную глубину резания грунта или выполнять планировочные работы.
Для автоматического регулирования рассоединяется муфта 17. Поток жидкости от распределителя 3 в бак направляется через предохранительный клапан 11 с переливным золотником. Этот клапан дистанционно управляется от электрогидравлического золотника 10. При включении золотника 10 клапан 11 закрывается и поток жидкости поступает от насоса в напорную линию золотника 10 который направляет этот поток в штоковую или поршневую полости гидроцилиндров 4. Для регулирования скорости перемещения потоков гидроцилиндров 4 при автоматическом управлении отвалом применен дроссель с регулятором 12 а давление в сливной и напорной линии замеряется манометрами 13. Рабочая жидкость очищается от механических примесей фильтром 15 с переливным клапаном. Гидравлическая схема бульдозера Т-500 показана на рисунке 2.5.
Рисунок 2.5 – Гидравлическая схема бульдозера Т-500
6 Охрана труда и окружающей среды при эксплуатации СДМ.docx
1 Классификация и источники вредных и опасных факторов
К вредным факторам согласно определению данному в Законе «Об основах охраны труда в Российской Федерации» от 23.06.1999 г. относят факторы которые становятся в определенных условиях причиной заболеваний или снижения работоспособности. При этом имеется в виду снижение работоспособности исчезающее после отдыха или перерыва в активной деятельности.
Опасными называются факторы которые приводят в определенных условиях к травмам или внезапным резким ухудшениям здоровья.
Источники опасных и вредных факторов.
По природе воздействия на человека опасные и вредные факторы подразделяются по ГОСТ 12.0.003-74 на следующие классы: физические химические биологические и психофизиологические факторы.
К физическим опасным и вредным факторам относятся:
острые и падающие предметы;
повышение и понижение температуры воздуха и окружающих поверхностей;
повышенная запыленность и загазованность;
повышенный уровень шума акустический колебаний вибрации;
недостаточное освещение пониженная контрастность освещения;
повышенная яркость блесткость пульсация светового потока;
рабочее место на высоте.
К химическим опасным и вредным факторам относятся вредные вещества используемые в технологических процессах промышленные яды используемые в сельском хозяйстве и в быту ядохимикаты лекарственные средства применяемые не по назначению боевые отравляющие вещества.
Биологическими опасными и вредными факторами являются:
патогенные микроорганизмы (бактерии вирусы особые виды микроорганизмов – спирохеты и грибы) и продукты жизнедеятельности;
растения и животные.
Психофизиологические опасные и вредные производственные факторы – это факторы обусловленные особенностями характера и организации труда параметров рабочего места и оборудования. Они могут оказывать неблагоприятное воздействие на функциональное состояние организма человека его самочувствие эмоциональные и интеллектуальные сферы и приводить к стойкому снижению работоспособности и нарушению состояния здоровья.
2 Действие вредных агрессивных и ядовитых веществ на организм человека и их предельно допустимые концентрацииметоды и средства
Степень и характер вызываемых веществом нарушений нормальной работы организма зависит от пути попадания в организм дозы времени воздействия концентрации вещества его растворимости состояния воспринимающей ткани и организма в целом атмосферного давления температуры и других характеристик окружающей среды.
Следствием действия вредных веществ на организм могут быть анатомические повреждения постоянные или временные расстройства и комбинированные последствия. Многие сильно действующие вредные вещества вызывают в организме расстройство нормальной физиологической деятельности без заметных анатомических повреждений воздействий на работу нервной и сердечнососудистой систем на общий обмен веществ и т.п.
Вредные вещества попадают в организм через органы дыхания желудочно-кишечный тракт и через кожный покров. Наиболее вероятно проникновение в организм веществ в виде газа пара и пыли через органы дыхания (около 95 % всех отравлений).
Сильно действующие ядовитые вещества - это обращающиеся в больших количествах в промышленности и на транспорте токсические химические вещества способные в случае разрушения ( аварий на объектах ) легко переходить в атмосферу и вызывать массовые поражения людей.
Согласно ГОСТ 12.1.007-76 по степени воздействия на организм вредные вещества подразделяются на 4 класса опасности:
Чрезвычайно опасные - ПДК менее 01 мгм (берилий ртуть сулема кварцевая пыль);
Высокоопасные - ПДК 01-10 мгм (окислы азота анилин бензол пыль гранита);
Умеренно опасные - ПДК 11-100 мгм (вольфрам борная кислота угольная пыль);
Малоопасные - ПДК более 100 мгм (аммиак ацетон пыль известняка).
Меры безопасности при работе на тракторах. Особенности безопасной работы на повышенных скоростях
- Перед пуском дизеля рычаг C должен находиться в положении «Н только после остановки» рычаг В и рычаги гидрораспределителя гидросистемы навесного устройства - в позиции Нейтральная" а стояночный тормоз затянут.
- Перед троганием с места убедитесь что путь свободен и между трактором и сельскохозяйственными орудиями а также в районе шарнирного устройства рамы нет людей. О начале движения предупредите сигналом.
- К работе с прицепами полуприцепами и другими транспортными средствами допускаются только лица знающие правила работы с ними.
- Прицепные орудия и прицепы должны иметь жесткие сцепки не позволяющие им набегать на трактор.
- Запрещается езда на необорудованных для этого прицепных орудиях навесных машинах и вне кабины трактора. В кабине трактора запрещается проезд более двух человек включая водителя.
- Кабину содержите в чистоте наличие в кабине посторонних предметов недопустимо.
- Категорически запрещается работать на тракторе при неисправных рулевом управлении тормозной системе электроосвещении и сигнализации.
- На полу кабины должны быть резиновые коврики.
- Тормоза трактора должны быть в исправном состоянии. При торможении рабочим тормозом трактора двигающегося по сухому и твердому грунту со скоростью 83 мс (30 кмч) тормозной путь должен быть не более 13 м; при скорости 55 мс (20 кмч) -65 м. Полностью выжатая педаль тормоза не должна упираться в пол кабины.
- При переездах через плотины гати и мосты убедитесь в возможности проезда и пользуйтесь только пониженными скоростями.
- Движение трактора с навесными машинами в транспортном положении осуществляйте с предварительным фиксированием навесного устройства посредством гидромеханических клапанов гидроцилиндров
- Переезд с навесными машинами через канавы бугры и другие препятствия производите под прямым углом на малой скорости избегая резких толчков и больших кренов трактора. - Габарит трактора с установленным насадком на выхлопную трубу - 44 м. При переезде под линиями электропередач и низкогабаритными проездами необходимо соблюдать осторожность. При наличии знака ограничивающего высоту проезда менее 44 м проезд трактора с установленным насадком выхлопной трубы запрещается насадок в этом случае должен сниматься.
- При поворотах выбирайте малую скорость.
- При движении под уклон запрещается использовать накат. При движении по прямой накатом без уклона установите рычаг С в положение Н только при движении".
- Подъезжайте к сельскохозяйственным машинам орудиям или прицепам на минимальной скорости с неполностью выжатой педалью слива.
- При появлении неисправности трактор должен быть немедленно остановлен до устранения неисправности.
- Допустимая скорость трактора на подъездных путях и проездах не более 10 кмч в производственных помещениях - не более 2 кмч.
- При погрузке (разгрузке) прицепа трактор должен быть надежно заторможен стояночный тормоз затянут.
- При агрегатировании с прицепами или полуприцепами присоедините их страховочные цепи к соединительным звеньям находящимся на рамах нижних тяг навесного устройства.
- При работе с тросами на буксирных крюках запрещается находиться в радиусной зоне тросов.
- Преодоление водной переправы вброд производите только после тщательной подготовки и проверки маршрута движения. Допускается преодоление брода глубиной до 1 м.
В кабине трактора должна быть установлена и закреплена аптечка первой помощи укомплектованная в соответствии с указаниями на ее крышке. [11 с. 36]
3 Микроклимат в кабинах самоходных машин
К самоходным машинам относят строительные и дорожные машины а также технологический транспорт на строительстве - грузовые автомобили и тракторы. Рабочая скорость этих машин не превышает 6 кмч а транспортная - 40 кмч. Самоходные машины работают во всех климатических зонах страны. Кабины имеют большую площадь остекленных поверхностей и составляют примерно 02 06 площади поверхности всех ограждений кабины. Как правило управляет машиной один человек.
Для обеспечения в кабинах микроклимата и предельно допустимых концентраций вредных веществ в воздухе в соответствии с нормами ГОСТ 12.1.005-96 12.1.007-96 12.2.019-96 и 12.2.023- 96 устраивают естественную вентиляцию (люки форточки опукающиеся стекла) и принудительную а также пылеулавливатели воздухоохладители кондиционеры и отопители.
Действующая система отопления кабин самоходных машин путем установки компактных нагревателей дающих сосредоточенную подачу теплового воздуха нарушает оптимальный теплообмен водителя машины. В этом случае температура внутренних ограждений кабины существенно ниже температуры воздуха и тело водителя вынуждено увеличивать теплоотдачу в окружающую среду.
Проводимые гигиенические исследования в этой области ставят задачу оценивать тепловое ощущение водителя по сочетанию температур воздуха в кабине и ее внутренних ограждений с учетом скорости движения теплого воздуха и его относительной влажности. С этой целью начинают применять в кабинах строительных и дорожных машин панельно-лучистое отопление. Принцип его заключается в том что на полу и по стенам кабины размещают нагревательные панели (они же являются и облицовочным материалом) в которых имеются нагревательные элементы. Они состоят из бумажно-слоистых пластин с расположенным внутри нагревательным слоем из электропроводной бумаги. При наличии в кабине жалюзей в полу и дефлектора в крыше внутри кабины создается гравитационный напор для конвективного тепловоздухообмена что создает для организма человека гигиенические и комфортные условия.
В условиях запыленности наружного воздуха например при земляных работах в кабинах устанавливают фильтровентиляционные установки или кондиционеры.
Фильтровентиляционная установка для кабин бульдозеров состоит из вентилятора двухступенчатого фильтра климатизера воздухораспределительного устройства и напорного воздуховода с нагревательными элементами и увлажнителем воздуха.
С помощью установки можно вентилировать кабину по рециркуляционной или прямоточной системе. Поступающий воздух очищается от пыли в две ступени. Холодный воздух подогревается электрокалорифером а теплый охлаждается и увлажняется водой.
В кабинах начинают применять кондиционирование воздуха с помощью кондиционеров. По принципу действия их делят на испарительные фреоновые и термоэлектрические. Во фреоновом кондиционере фреон (газ) при нормальной температуре сжимается в компрессоре и поступает в кондиционер или теплообменник для охлаждения. Сжатый фреон переходит в жидкое состояние и поступает в испаритель или воздухоохладитель где расширяясь испаряется и поглощает при этом большое количество теплоты из окружающего воздуха.
Термоэлектрический кондиционер основан на эффекте выделения или поглощения теплоты на спаях двух различных проводников в зависимости от направления электрического тока (эффект Пельтье).
Воздух охлаждается посредством термоэлементов состоящих из двух полупроводников последовательно соединенных пластинами. Воздух подаваемый вентилятором охлаждается на холодных спаях и поступает в кабину а воздух охлаждающий горячие спаи выводится в атмосферу.
При работе в холодный период года в блоке воздухоохладителя устанавливается теплообменник для подачи подогретого воздуха в кабину. Теплообменник подключается к системе охлаждения двигателя трактора.
4 Звуковые колебания. Защита от шума
4.1 Характеристики звуков и действие их на организм
Инфразвук возникает при работе дизельных и реактивных двигателей компрессоров и вентиляторов. При скорости движения автомобиля например более 70 кмч при открытых поворотных форточках в кабине и в салоне кузова инфразвуки возникают в результате удара потока воздуха о препятствия (например раму форточки). Это явление называют ветровым флаттером. С уменьшением объема кабины или салона инфразвук увеличивается.
В обычном понимании орган слуха человека не воспринимает инфразвуки. Особенностью действия инфразвука является высокая специфическая чувствительность органа слуха к низкочастотным колебаниям. Инфразвук с частотой 7 Гц совпадает с - ритмом биотоков мозга поэтому эта частота наиболее опасна. Кроме того инфразвуки воспринимаются поверхностью тела.
Шум (слышимый звук) возникает при работе экскаваторов компрессоров бульдозеров автомобилей-самосвалов тракторов автогрейдеров и других строительных машин.
Совокупность слышимых звуков сочетающая множество различных тонов и частот с беспорядочной интенсивностью и продолжительностью называют шумом. Но под шумом понимают также всякий нежелательный для человека звук мешающий восприятию необходимых звуков или нарушающий тишину.
Действие шума на организм человека проявляется в поражении органов слуха и нарушении систем (сердечно-сосудистой центральной нервной) а также ослаблении памяти изменении кожной чувствительности.
Ультразвук применяют для интенсификации технологических процессов (при механической обработке твердых и хрупких материалов сварке лужении травлении) в дефектоскопии иногда для мойки деталей при ремонте строительных машин.
Ультразвук порождает в тканях человека тепловой эффект. Энергия ультразвука поглощенная тканью переходит в теплоту и повышает температуру тела. Ультразвуковая волна вызывает в тканях высокое давление в связи с чем изменяются свойства клеток.
Систематическое воздействие ультразвуковых волн на организм человека вызывает быструю утомляемость боль в ушах голове нарушает равновесие развивает невроз и гипотонию. Вблизи оборудования генерирующего ультразвуковые колебания возникает шум до 120 дБ.
Шум классифицируют по следующим признакам:
По происхождению: механический шум (вследствие вибрации поверхностей машин и оборудования а также одиночных или периодических ударов в сочленениях деталей или конструкций в целом); аэродинамический (возникающий при движении газов например при истечении сжатого воздуха или газа из отверстий пульсации давления при движении потоков воздуха или газа в трубах и др.); электромагнитный (возникающий вследствие колебаний элементов электромеханических устройств под влиянием переменных магнитных сил например колебания статора и ротора); гидромеханический (при стационарных и нестационарных процессах в жидкостях например при гидравлических ударах).
По времени действия на организм: постоянный и непостоянный - колеблющийся во времени прерывистый и импульсный.
По спектральному составу: низкочастотный - с частотой колебаний не более 400 Гц; среднечастотный - от 400 до 1000 Гц; высокочастотный более 1000 Гц.
По ширине спектра: широкополосный (включающий почти все частоты звукового давления) и узкополосный.
Кроме того шум подразделяют на воздушный распространяющийся в воздушной среде от источника возникновения до места наблюдения и структурный излучаемый поверхностями колеблющихся конструкций стен перекрытий перегородок зданий в звуковом диапазоне частот.
4.2 Шумовые характеристики машин
Основными источниками шума внутри зданий и на строительных площадках промышленных предприятий являются технологическое оборудование строительные машины и средства транспорта. С целью обеспечения условий труда при которых шум воздействующий на работающих не должен превышать предельно допустимых уровней по ГОСТ 12.1.003-83 установлены допускаемые значения шумовых характеристик машин и оборудования. Такие характеристики позволяют рассчитывать ожидаемый шумовой режим в производственных помещениях и оценивать конструктивное качество изготовления машин с точки зрения безопасности труда. Допускаемые значения этих характеристик машин указывают в паспортах технических условиях и стандартах. Методы определения шумовых характеристик изложены в ГОСТ 12.1.023-80 12.1.024-81 12.1.025-81 и 12.1.028-80.
Согласно СН № 1102-93 утвержденным Минздравом РФ 18 мая 1993 г. внешний шум строительно-дорожных машин тракторов и грузовых автомобилей на расстоянии 75 м от оси движения машин должен соответствовать ГОСТ 19357-94.
В экскаваторах самоходных кранах погрузчиках машинах для строительства дорожных покрытий грузовых автомобилях основным источником шума является двигатель внутреннего сгорания. Уровень шума от рабочего и ходового оборудования а также от отдельных элементов строительных машин меньше уровня шума от двигателя.
Основными источниками шума бульдозера являются: вентилятор системы охлаждения система впуска система выпуска двигатель (механизм газораспределения процесс сгорания кривошипно-шатунный механизм) силовая передача.
4.3 Средства и методы защиты от шума
Классификация средств и методов защиты от шума установлена ГОСТ 12.1.029-80 «Средства и методы защиты от шума». Этот стандарт распространяется на рабочие места производственных и вспомогательных помещений а также на территории промышленных предприятий.
Общая классификация средств снижающих шум приведена ниже:
Снижение шума в источнике его возникновения (механического аэродинамического гидродинамического электромагнитного).
Снижение шума на пути его распространения (передача воздушного и структурного шумов).
Акустические средства защиты от шума: звукоизоляция (ограждения экраны кожуха кабины); звукопоглощение (облицовка поглотители звука); виброизоляция (опоры прокладки разрывы); демпфирование (с сухим трением вязким трением внутренним трением); глушители шума (абсорбционные реактивные комбинированные).
Средства индивидуальной защиты от шума (наушники вкладыши шлемы каски костюмы).
Существуют и методы защиты от шума: архитектурно-планировочные (рациональные акустические решения размещения рабочих мест оборудования и зданий зоны транспортных потоков шумозащитные зоны) и организационно-технические (применение малошумных машин и оборудования рациональные режимы труда и отдыха работающих).
Средства и методы снижения шума в источнике его возникновения должны реализовываться в процессе проектирования машины или технологического процесса.
4.4 Звукопоглощение виброизоляция демпфирование и средства
индивидуальной защиты от шума
Звукопоглощение. Для снижения уровня звукового давления на рабочих местах производственных помещений применяют конструкции в виде облицовки стен и потолков звукопоглощающими материалами и штучными звукопоглотителями.
Звукопоглощающие материалы характеризуются коэффициентом звукопоглощения . К таким материалам относят пористые неорганические органические и композиционные материалы и изделия (например вату минеральную и стеклянную маты в рулоне из штапельного волокна холсты из супертонкого стекловолокна).
Виброизоляция. При работе технологического оборудования (кузнечно-прессового дробилок вибростендов) возникают вибрации которые создают шум. Распространенным способом защиты от подобного шума является установка такого оборудования на виброизоляторы или упругие прокладки.
Эффективность виброизоляции оценивается коэффициентом передачи при виброизоляции.
Демпферы предназначают также для гашения колебаний машин. В отличие от виброизолятора демпфер не имеет упругих элементов и механическая энергия в нем не аккумулируется а преобразуется в тепловую рассеиваемую в пространстве. Демпферы с сухим или вязким трением устанавливают под оборудование. К демпферам с внутренним трением относят вибродемпфирующие материалы в виде мастик. При нанесении мастик на металлические листовые конструкции ослабляется их вибрация вследствие внутреннего трения в мастике.
Средства индивидуальной защиты от шума. В тех случаях когда невозможно снизить шум до установленных норм с помощью конструктивных мероприятий применяют средства индивидуальной защиты. Эти средства подразделяют на внутренние и наружные. В первом случае в ушные раковины наружного слухового прохода вкладывают тампоны из ваты или марли пропитанные жиром воском или другим составом. К наружным средствам защиты относят наушники или шлемофоны плотно закрывающие ушные раковины а также костюмы.
5 Действие вибрации на организм человека
Тело работающего человека условно рассматривают как своеобразную колеблющуюся систему поскольку под воздействием вибрации части тела человека перемещаются относительно друг друга с амплитудами в зависимости от источника колебаний и массы органов. Относительные перемещения частей тела приводят к напряжениям в связках между частями тела и взаимному соударению и надавливанию.
Продолжительные колебания человека с частотой f = 3 5 Гц вредно отражаются на вестибулярном аппарате сердечно-сосудистой системе и вызывают синдром укачивания. Колебания с частотой f = 5 11 Гц вызывают расстройства вследствие резонансных колебаний головы желудка кишечника в конечном счете всего тела. При колебании с частотой f = 11 45 Гц ухудшается зрение возникают тошнота рвота нарушается нормальная деятельность других органов. Колебания с частотой f≥45 Гц вызывают повреждение сосудов головного мозга; происходит расстройство циркуляции крови и высшей нервной деятельности с последующим развитием вибрационной болезни.
Тело человека рассматриваемое как вязкоупругая механическая система обладает собственными частотами и достаточно выраженными резонансными свойствами. Резонансные частоты (Гц) отдельных частей тела человека следующие: головы - 12 27 горла - 6 27 грудной клетки - 2 12 ног и рук - 2 8 поясничной части позвоночника- 4 14 живота - 4 12.
Степень вредного воздействия колебаний на организм человека зависит от частоты продолжительности и направления действия вибрации.
6 Общие требования безопасности труда
Требования безопасности труда в строительстве регламентируют СНиП Ш-4-90 а общие требования безопасности при эксплуатации строительных машин - ГОСТ 12.3.033-94.
К управлению техническому обслуживанию и ремонту машин допускаются лица прошедшие обучение и имеющие удостоверение на право выполнения работ соответствующей квалификации.
Основой безопасной эксплуатации машин является использование их в строгом соответствии с назначением выполнение работ по проектам производства работ и обеспечение высокого уровня работоспособности в соответствии с требованиями эксплуатационной и ремонтной документации.
До начала работы машинист обязан проверить техническое состояние машины устранить замеченные неисправности и провести ее техническое и технологическое обслуживание. К использованию допускаются машины в работоспособном состоянии. Технические данные машины допускаемой к использованию должны соответствовать параметрам технологического процесса и условиям работ.
Перед пуском двигателя необходимо убедиться в том что рабочие органы машины отключены. Не разрешается наматывать на руку свободный конец шнура при пуске пусковых двигателей а при их пуске пусковой рукояткой не следует брать ее в обхват.
Не разрешается посторонним лицам при движении машин сидеть или стоять на раме крыльях или прицепном устройстве соскакивать или садиться на них перебегать между тягачом и машиной с машины на тягач и др.
При работе и передвижении машины в ночное время место работы и путь следования должны быть освещены. Не допускаются к использованию в ночное время машины е неисправным освещением. Не разрешается использовать машины при отсутствии на них сигнала.
Спуск машин с уклона должен осуществляться на пониженной передаче и при малой частоте вращения коленчатого вала двигателя. Запрещается при спуске выключать сцепление и переключать передачи. Необходимо помнить что на крутых спусках поворот направо гусеничного тягача типа Т-35.01 производится выключением левой муфты поворота а налево - выключением правой муфты.
Запрещается заводить перегретый двигатель находиться под машиной при работающем двигателе и поднятым рабочим органом (отвалом ковшом заслонкой) удерживаемым гидроцилиндром или канатом. При выполнении работ под рабочим органом необходимо поставить надежный упор и заглушить двигатель.
Не допускаются к управлению машинами посторонние лица.
Необходимый инструмент и инвентарь должны храниться на машине в установленном месте. Нахождение на ней (в кабине под капотом на рабочем органе и др.) посторонних предметов запасных частей недопустимо так как они могут быт следствием аварии.
При выполнении работ машинами на строительной площадке следует руководствоваться знаками безопасности установленными ГОСТ 12.4026-86.
6.1 Требования безопасности труда при производстве работ бульдозерами
Перед началом работы машинист должен ознакомиться с участком на котором будет осуществляться разработка грунта и оценить его с позиций требований обеспечения безопасного ведения работ. С участка должны быть удалены крупные камни пни и другие предметы а места подземных сооружений обозначены предупредительными знаками. При наборе и перемещении грунта не допускаются повороты машины с заглубленным рабочим органом.
Во избежание сползания машины под откос движение ее вдоль насыпи из свежо отсыпанного грунта должно производиться на расстоянии не более 1 м от края ее бровки.
На крутых косогорах не допускаются резкие повороты так как они могут привести к сползанию или опрокидыванию машины. Не допускается работа машин с поперечным уклоном более 30°. Во избежание опрокидывания бульдозера запрещается перемещать грунт на подъем при уклоне 15° и на спуске при уклоне 30°.
При сбросе грунта под откос насыпи не разрешается выдвижение отвала бульдозера за бровку откоса.
При обнаружении в процессе разработки грунта непредусмотренных подземных сооружений необходимо прекратить работу и доложить об этом производителю работ.
Запрещается нахождение людей в радиусе 10 м относительно работающих машин и 50 м относительно бульдозеров используемых при валке деревьев.
Во время перерывов машина должна быть установлена на ровной площадке заторможена рабочий орган опущен на грунт рычаги управления установлены в нейтральное положение а кабина закрыта.
6.2 Требования безопасности труда при транспортировании и
При погрузке машины на прицеп и разгрузке с прицепа требуется следить за тем чтобы не находились люди в зоне возможного ее падения (сползания).
После погрузки машины на прицеп следует проверить надежность ее крепления.
При транспортировании машин по дорогам следует передвигаться по правой их стороне с соблюдением интервала между машинами или транспортными агрегатами не менее 20 м.
Железнодорожные пути следует переезжать только через переезды на пониженной передаче при открытом шлагбауме. При отсутствии на переезде шлагбаума и сигнализации необходимо остановиться перед ним и убедиться в отсутствии приближающегося к переезду поезда.
При подъезде к мосту плотинам необходимо убедиться в возможности проезда по ним.
Машины остановившиеся на дороге на длительное время необходимо огородить в дневное время красными флажками а в ночное время красными фонарями.
Запрещается транспортировать машины в ночное время без фар освещения и задних световых сигналов.
Площадки на которых ведется подготовка машин к хранению должны быть ровными хорошо освещенными не иметь посторонних предметов обеспечивать хороший доступ к машине и возможность использования грузоподъемных средств установки снятых с машины составных ее частей.
Гусеничные машины должны опираться на подкладки всей опорной поверхностью гусениц.
Снятые с машин сборочные единицы и детали необходимо укладывать на стеллажи: на нижние полки следует укладывать тяжелые детали а на верхние - легкие.
Рабочие выполняющие операции по нанесению защитных покрытий на детали машин допускаются к работе после проведения инструктажа и освоения правил пользования защитными приспособлениями с очками респираторами и др.
6.3 Требования безопасности труда при техническом обслуживании и ремонте машин
Площадка на которую устанавливают машину должна быть ровной сухой не загроможденной посторонними предметами и по возможности защищенной от ветра и пыли расположена вдали от источников загорания и линий электропередачи.
В стационарной мастерской машину следует устанавливать так чтобы был обеспечен свободный подход рабочее оборудование машин необходимо опустить на грунт пол или специальную подставку.
Перед выполнением технического обслуживания или ремонта машин следует заглушить двигатель за исключением тех случаев когда требуется проверить работу двигателя или других составных частей машины после их регулирования. На пусковых устройствах обслуживаемых машин рычагах кнопках для электростартерного пуска необходимо вывесить плакат «Не включать - работают люди!»
Мыть машину горячей водой следует в брезентовых рукавицах а для очистки ее и составных частей от пыли и грунта использовать скребки щетки специальные чистики и обтирочные материалы.
Во время работы использовать только исправный инструмент. Гаечные ключи должны соответствовать размерам гаек и головок болтов и не иметь смятых или сточенных граней; запрещается применять прокладки между гранями и торцами зева ключа а также наращивать гаечные ключи другими ключами и др. При подтягивании крепежных деталей ключ следует направлять «к себе».
Поверхность бойка слесарного молотка должна быть выпуклой без трещин и заусенцев. Рукоятки молотков и кувалд должны быть изготовлены из сухого прочного дерева и хорошо обработаны. Прочность крепления молотков и кувалд па рукоятках следует проверять перед началом работ.
В верхней части зубил не должно быть трещин забоин и заусенцев так как при ударе молотком по инструменту частицы металла могут отлетать в сторону.
Напильники и другие инструменты с заостренными нерабочими концами должны иметь рукоятки.
Крюки лапы и захваты приспособлений и съемников необходимо прочно закреплять па деталях.
Нельзя пользоваться съемниками и другими монтажными приспособлениями со смятой или сорванной резьбой погнутыми стержнями планками болтами.
Перед использованием подъемно-транспортных устройств следует проверять исправность подъемного устройства и схватки (цепи тросы канаты и др.). Поднимать и опускать груз следует вертикально; нельзя стоять под поднятым грузом; при транспортировании поднятого груза следует находиться сзади него. Запрещается ставить подкладки под груз при опускании (они должны быть установлены заблаговременно); запрещается оставлять груз в подвешенном состоянии если работа окончена или временно прекращена; нельзя устанавливать снятые сборочные единицы детали и инструмент на разбираемую машину.
Верстак от стружки опилок и осколков следует своевременно очищать щеткой веником метлой или обтирочным материалом. Пролитое на пол масло или топливо необходимо удалить а пол засыпать песком или опилками.
Перед промывкой деталей керосином или дизельным топливом руки необходимо смазывать вазелином.
Необходимо следить за вентиляционными отверстиями в пробках аккумуляторов так как при их засорении резко повышается давление газов внутри аккумуляторных батарей и возможен взрыв бака. Осматривать аккумуляторные батареи следует с помощью переносных ламп напряжением 36В. Запрещается пользоваться открытым пламенем при осмотре аккумуляторных батарей.
С кислотами следует работать в резиновых перчатках и очках. При смешивании кислоты с водой необходимо кислоту вводить в воду. Кислоту попавшую на одежду следует смыть нашатырным спиртом.
Запрещается мыть детали в этилированном бензине. Случайно пролитый этилированный бензин заливают дихлорамином или раствором хлорной извести (1 часть извести и 3-5 частей воды). Металлические детали машин загрязненные этилированным бензином промывают керосином или щелочным раствором.
Запрещается открывать крышку неохлажденного радиатора двигателя без рукавиц и наклонять лицо к заливной горловине радиатора.
Проверяя уровень масла в картерах машин следует остерегаться выброса горячего масла при повышении давления вследствие засорения сапуна.
Горячую воду из системы охлаждения двигателя и масло из картеров двигателей и машин необходимо сливать осторожно чтобы не получить ожогов.
Во время технического обслуживания машин не прикасаться к горячему выпускному коллектору во избежание ожогов.
При окраске машин необходимо пользоваться средствами индивидуальной защиты - респиратором очками перчатками и пастами для защиты рук.
6.4 Электробезопасность
Запрещается использование машин на разработке грунта под линиями электропередачи и вблизи электрокабелей находящихся под напряжением. Производство работ в зоне расположения электрокабелей допускается только с письменного разрешения организации ответственной за их эксплуатацию.
Переносные лампы используемые для осмотра машин при их техническом обслуживании и ремонте в темное время суток и затемненных местах должны иметь напряжение не более 36 В.
Перед началом работы ручным электрифицированным инструментом необходимо проверить исправность выключателя заземляющего провода и надежность питающих проводов. Подключать электроинструмент следует в резиновых перчатках стоя на резиновом коврике. Указанные защитные средства не должны иметь проколов трещин; хранить их следует в закрытых шкафах отдельно от инструмента. Их необходимо предохранять от воздействия масел бензина и других веществ разрушающих резину. Перед применением они должны быть осмотрены и очищены от пыли а при увлажнении поверхности высушены.
Перед использованием электрифицированного инструмента необходимо проверить его действие на холостом ходу. При работе необходимо следить за тем чтобы токопроводящий провод был защищен от случайного повреждения. Не допускается соприкосновение провода с горячими влажными и масляными поверхностями или предметами. При замене сверл и других рабочих частей электроинструмента необходимо отключать его от сети. Чтобы электроинструмент не перегревался следует переводить его на холостой ход. При внезапной остановке вследствие прекращения подачи электроэнергии а также при перерывах в работе электрический инструмент необходимо отключить от сети.
При работе с электрическим инструментом запрещается:
) использовать его на работах для которых он не предназначен;
) оставлять без надзора с работающим двигателем а также включенным в сеть;
) натягивать и перегибать кабель инструмента а также допускать его пересечение стальными канатами машин электрокабелями электросварочными проводами находящимися под напряжением со шлангами для подачи кислорода ацетилена и других газов;
) передавать инструмент другим рабочим не имеющим разрешения на его использование;
) эксплуатировать при повреждении штепсельного соединения кабеля или колпачка щеткодержателя и при нечетком действии выключателя;
) разбирать и производить ремонт инструмента проводов штепсельных разъемов;
) держаться за провод и касаться вращающихся деталей или рабочего органа;
) удалять руками стружку или опилки до полной остановки рабочего органа инструмента;
) работать при искрении щеток на коллекторе сопровождающемся появлением кругового огня на его поверхности вытекании смазки из редуктора или вентиляционных каналов появлении дыма или запаха характерного для горящей изоляции ненормального шума стука и вибрации поломке или появлении трещин в корпусе или рукоятке.
6.5 Пожарная безопасность
Не допускать утечек топлива масел и рабочих жидкостей; не хранить на машине использованные обтирочные материалы к запасу смазочных материалов и топлива; содержать в чистоте выпускную трубу. При осмотре топливных баков и системы питания двигателя машины следует пользоваться электрическим освещением.
Временные стоянки машин в летнее время на месте их использования должны быть очищены и расположены от складов лесоматериалов древесно-кустарниковых насаждений и построек на расстоянии не менее чем 10 м а от складов нефтепродуктов не менее чем на 20 м. В местах хранения машин должны быть огнетушители ящики с песком и противопожарный инвентарь. В случае воспламенения нефтепродуктов гасить пламя следует огнетушителем или песком землей или прикрывать брезентом и др. Категорически запрещается заливать пламя водой.
При работе обслуживании и ремонте машин запрещается открывать пробки бочек с бензином ударяя по ним металлическими предметами; пользоваться открытым огнем и курить в месте заправки машин и при проверке уровня топлива в баках; разводить огонь и курить вблизи места заправки и стоянки машин; оставлять машину после работы или заправки вблизи пункта заправки; подогревать двигатели открытым огнем при пуске машины; подходить к открытому огню в одежде пропитанной нефтепродуктами.
Каждая машина должна иметь огнетушитель.
7 Охрана окружающей среды
При эксплуатации машин необходимо строго соблюдать требования по охране окружающей среды. Так при строительстве различного рода земляных сооружений следует снимать плодородный слой почвы и укладывать его отдельно для дальнейшего использования. Если он не используется сразу то его необходимо укладывать в бурты.
Если в процессе выполнения строительных работ были разрушены сельскохозяйственные земли и лесные угодья то строители обязаны их восстановить (рекультивировать) в ходе строительства но не позднее чем в течение года после их окончания.
Деревья ценных пород растущие на месте будущей стройки необходимо пересадить на новые места а размещенные рядом со стройкой следует предохранять от повреждения.
Гусеничные машины при их транспортировании на собственном ходу должны передвигаться вдоль обочин дорог. Переезд через асфальтированные дороги следует осуществлять по временным настилам.
Не разрешается допускать к использованию машины у которых двигатели работают с дымностью превышающей установленные нормы. Снижение дымности достигается регулированием топливной аппаратуры двигателей.
Запрещается использовать машины при наличии у них утечек топлива масел рабочих жидкостей и смазок так как ТСМ отрицательно влияют на окружающую природу. По этим же причинам недопустим разлив и потери ТСМ при заправке машин замене масел рабочих жидкостей и смазывании их в процессе технического обслуживания и ремонта на месте использования.
Запрещается сливать отработавшие нефтепродукты на землю в водоемы и канализационную сеть. Нефтепродукты сливаемые из машин в виде отстоя топлива отработанные масла используемые на технологические нужды керосин бензин дизельное топливо растворители и другие нефтепродукты следует собирать и сдавать на базы нефтеснабжающих организаций или устранять методами согласованными с Госсанинспекцией.
8 Влияние машин на окружающую среду
Экологические проблемы вызываемые дорожными машинами могут быть разделены на три основные группы: локальные региональные и глобальные.
8.1 Локальное влияние
К данному виду влияния относятся:
Влияние на здоровье. Вызывается угарным газом (СО) углеводородами окислами азота твердыми составляющими выбросов транспорта (включая углерод сульфаты и свинец) вторичными фотохимическими токсинами.
Влияние на гигиенические условия. Воздействие шума и вибрации от процесса работы.
Разрушение конструкционных материалов транспортных средств и дорожных сооружений под действием серных и азотных составляющих выбросов машин а так же оксидов фотохимического происхождения.
8.2 Региональное влияние
Подкисление (ацилирование) почв происходящее под действием серных и азотных составляющих.
Насыщение воздуха азотом вызываемое азотными составляющими.
Увеличение концентрации тропосферного (низкоуровневого) озона и влияние на растительность. Этот эффект вызывается действием вторичных токсинов получающихся из углеводородов и окислов азота.
Разрушение конструкционных материалов под действием серных и азотных составляющих а также оксидов фотохимического происхождения.
8.3 Глобальное влияние
Парниковый эффект. Вызывается действием углекислого газа (СО2) метана (СН4) озона (О3) фреонов (CFC) и т.д. Истощение слоя стратосферного (высокоуровневого) озона. Вызывается действием фреонов (CFC) оксида азота (N2O).
Глобальные эффекты особенно парниковый эффект по расчетам экологов будут иметь долговременное развитие. Это значит что даже когда вредное воздействие вызывающее эти проблемы будет под контролем природные процессы уже вовлеченные в глобальные изменения будут продолжаться еще долгое время.
9 Оценка количества выбросов в окружающую среду
Участок по обкатке и испытанию двигателей оборудуется специальными стендами на которые устанавливается двигатель. При работе двигатель выделяет токсичные вещества: оксид углерода (CO) оксид азота (NOx) углеводороды (CH) соединения серы (SO2) сажа (C).
Обкатка двигателей производится как без нагрузки (холостой ход) так и под нагрузкой. На режиме холостого хода выброс загрязняющих веществ определяется в зависимости от рабочего объема испытываемого двигателя.
При обкатке под нагрузкой выброс загрязняющих веществ зависит от средней мощности развиваемой двигателем при обкатке.
Валовый выброс i-го загрязняющего вещества Mi определяется по формуле [12]:
где - валовый выброс
- валовый выброс i-го загрязняющего вещества при обкатке на нагрузочном режиме тгод.
Валовый выброс i-го загрязняющего вещества при обкатке на холостом ходу определяется по формуле [12]:
- время обкатки двигателя на холостом ходу (табл. 2.2 [12]) мин;
где - удельный выброс
- рабочий объем двигателя.
Валовый выброс i-го загрязняющего вещества при обкатке двигателя на нагрузочномом режиме определяется по формуле [12]:
где - выброс i-го загрязняющего вещества при обкатке двигателя под нагрузкой гс
- время обкатки двигателя под нагрузкой (табл. 2.2 [12]) мин;
- средняя мощность развиваемая при обкатке под нагрузкой двигателем (табл. 2.2 [12]) кВт.
Полученные данные могут служить основой для начисления налога на выбросы вредных веществ в окружающую среду. А так же для проектирования систем очистки включающих катализаторы на предприятиях занимающихся ремонтом данного типа двигателей.
Список использованных источников.docx
Волков Д.П. Крикун В.Я. Никулин П.И. Машины для земляных работ. - М.: Машиностроение 1992.- 448 с.
Никулин П.И. Гильмутдинов В.И. Литвинов В.С. Никулин А.П. Расчет и построение тяговой характеристики землеройно-транспортной машины с гидромеханической трансмиссией: Методические указания к курсовому и дипломному проектированию по дисциплине “ Машины для земляных работ”.- Воронеж: Воронежский государственный архитектурно-строительный университет 2005.- 36 с.
Ульянов Н.А. Ронинсон Э.Г. Соловьев В.Г. Самоходные колёсные землеройно-транспортные машины.- М.: Машиностроение 1976.- 359 с.
Ульянов Н.А. Теория самоходных колесных землеройно-транспортных машин.- М.: Машиностроение 1969.- 520 с.
Рейш А.К. Борисов С.М. Бандаков Б.Ф. Машины для земляных работ.- М.: Стройиздат 1981.- 352. с.
Гоберман Л.А. Степанян К.В. Яркин А.А. Заленский В.С. Теория конструкция и расчет строительных и дорожных машин.- М.: Машиностроение 1979.- 407 с.
Алексеева Т.В. Гидропривод и гидроавтоматика землеройно-транспортных машин.- М.: Машиностроение 1966.- 250 с.
Алексеева Т.В. Артемьев К.А. Бромберг А.А. Войцеховский Р.И. Ульянов Н.А. Машины для земляных работ. Теория и расчет.- М.: Машиностроение 1964.- 467 с.
Справочник технолога-машиностроителя Под ред. А.Г.Косиловой Р.К.Мещерякова.- М.: Машиностроение 1985.-Т.2 496 с.
Трухина Н.И. Методические указания по выполнению экономических расчетов в дипломных проектах для студентов специальности 170900 “Подъемно-транспортные строительные дорожные машины и оборудование”.- Воронеж: Воронеж. гос. арх.-строит. академия 1998.- 31 с.
Шамаев И.А. Курсовое проектирование по технологии машиностроения производству и ремонту ПТ и СДМ [Электронный ресурс]: Учеб.-метод. пособие.- Воронеж: Воронеж. гос. арх.-строит. ун-т 2005.- 90 с.
Дипломное проектирование по специальности 190205. Требования к составу и оформлению: учеб. –метод. пособие В.А. Жулай [и др.]; Воронеж. гос. арх.-строит. Ун-т. –Воронеж 2009.-62с.
1 Технико-экономическое обоснование темы дипломного проекта.docx
1 Анализ технической литературы и патентный поиск
Анализ технической информации о новых научных исследованиях технических предложениях конструктивных и патентных решениях в области бульдозеростроения позволяет выделить основные направления повышения эффективности рабочих органов бульдозеров.
Основными из них являются оптимизация линейных и угловых размеров увеличение габаритных размеров рабочего оборудования применение устройств снижающих потери грунта при наборе и перемещении придание рабочему органу свойств адаптации специализация и увеличение номенклатуры сменных рабочих органов; подвод части энергии непосредственно к рабочему органу минуя движитель применение принципиально новых методов воздействия на грунт.
Д.т.н. проф. П.И.Никулиным предложено решение повышения производительности путем увеличения высоты отвала. Этот метод более выгоден так как увеличение призмы волочения грунта прямо пропорционален квадрату высоты отвала. Другой положительной стороной является увеличение функциональных возможностей разработок грунта разных плотностей. Для более плотных грунтов уменьшение высоты отвала обеспечивает уменьшение величины буксования и тем самым увеличение скорости движения и уменьшения нагрузок на рабочий орган. Для менее плотных грунтов (снег рыхлый грунт мусор) регулируемая высота отвала позволяет легче приспособиться к максимальной скорости при максимальном объёме призмы волочения что обеспечивает максимальную производительность. Регулируемая высота отвала обеспечивает хорошую технику безопасности так как обеспечивает хорошую обзорность при движении вперед на транспортной скорости.
При изучении патентов выданных в СССР и Российской Федерации было обнаружено что эта область мало изучена. Прямых способов увеличения высоты отвала не найдено. Косвенно увеличивают высоту отвала при помощи шарнирно соединенного с отвалом скребка (авторское свидетельство №713956 кл. Е 02 F376) или при помощи шарнирно соединенного дополнительный отвал с его возможностью поворота в вертикальной плоскости (авторское свидетельство №846661 кл. E 02 F 376).
Известен отвал значительно расширяющий функциональные возможности рабочего органа бульдозера за счет шарнирной установки дополнительного отвала с лезвием выполненном из эластичного материала. При работе с большими объемами рыхлого грунта или с жестким грунтом дополнительный отвал устанавливается в верхнее положение. При этом наружная поверхность дополнительного отвала устанавливается таким образом что является продолжением рабочей поверхности основного отвала и значительно увеличивает объём перемещаемого грунта. При чистовой работе с рыхлыми материалами дополнительный отвал устанавливается в нижнее положение и его лезвие становится ниже лезвия основного отвала.
Предложен рабочий орган бульдозера позволяющий расширить технологические возможности за счет расширения сферы его использования. При полном выдвижении штока гидроцилиндра для управления скребком последний находится в крайнем верхнем положении. В этом положении производится очистка поверхностей расположенных вне досягаемости отвала бульдозера. При разработке легких и разрыхленных грунтов а так же снега отвальный скребок путем уменьшения вылета штока гидроцилиндра для управления скребком служит вспомогательным отвалом увеличивая рабочую поверхность отвала а следовательно и объем перемещаемого грунта.
В качестве многоцелевой предлагается конструкция отвала который можно использовать не только по прямому назначению но и в качестве отвала планировщика и ковша погрузчика. Профиль отвала отличается удлиненной частью присоединяемой к верхней криволинейной посредством приваренных планок и закладных штырей. Отвал можно рассматривать как адаптирующийся с изменяющимися размерами. В продольной плоскости он поворачивается двумя гидроцилиндрами. При максимальном опрокидывании вперед отвал используют для планировочных работ при опрокидывании назад - для погрузочных в среднем положении - как отвал бульдозера. На тыльной стороне нижней части отвала предусмотрены скобы для закладки рыхлящих зубьев. Отвал универсален не требует специального оборудования и усложнения системы управления.
Разработан отвал с ножом кожухом выдвижным ножом и силовыми цилиндрами. На его тыльной стороне и на выдвижном ноже имеются направляющие благодаря которым последний перемещается строго в плоскости параллельной плоскости основного ножа. На тыльной стороне отвала при помощи шарниров закреплены корпуса силовых цилиндров штоки которых шарнирно соединены с выдвижным ножом. При выдвижении ножа штоки силовых цилиндров перемещают его по направляющим. Ступенчатую режущую кромку получают не изменяя угла резания.
Данные о патентных исследованиях приведены в таблице №1 «Справка о патентном поиске».
2 Выбор темы дипломного проекта
Изучив патенты не был обнаружен способ увеличения высоты отвала посредством телескопирования. Способ телескопирования представляет собой выдвижение из основного отвала дополнительного при помощи гидроцилиндров телескопирования при этом высота рабочего органа увеличивается приблизительно на 33-35 %. Коробчатое сечение отвала позволяет центрировать выдвижную секцию по боковым поверхностям. Очистка рабочей поверхности дополнительного отвала производится путем трения первой по антифрикционному материалу и трению о заточенной кромке основного рабочего органа. Этот способ был выбран за основу дипломного проекта.
На рис.1 показан общий вид бульдозера с улучшенной конструкцией рабочего оборудования.
Рис. 1.1 - Общий вид бульдозера с улучшенной конструкцией рабочего
Отвал 1 изменяет высоту с 205 м до 27 м. Это достигается путем выдвижения дополнительной внутренней секции 2 при этом не затрагивается конструкция самого отвала а дополнительная секция выдвигается в зоне козырька что позволяет работать как со стандартным так и с увеличенным отвалом. Ширина отвала 4800 мм. Техническая характеристика гусеничного тягача: мощность N=382 кВт тип трансмиссии– гидромеханическая скорость движения на первой передаче от 0 до 35 кмч конструктивная масса 58300 кг.
Масса модернизированного отвала увеличена на 20% по отношению к стандартному и составляет 9850 кг основной угол резания 50 град. объем призмы волочения изменяется с 175 м3 до 30 м3 в зависимости от выдвижения внутренней секции.
На рис.2 показано рабочее состояние отвала когда подвижная секция выдвинута из корпуса основного отвала.
Рисунок 1.2 - Рабочее состояние отвала
Выдвижение происходит с помощью двух гидроцилиндров 1 шаг которых составляет 07м. Усилие развиваемое обоими гидроцилиндрами составляет 20 кН что вполне достаточно для подъема телескопической части отвала.подвижной секции 1600 кг. К козырьку приварены боковые стенки 2 предотвращающие просыпание грунта. Для предотвращения заклинивания на торце переднего листа сделана фаска 3 очищающая направляющую поверхность подвижной секции. Для уменьшения сопротивления выдвижения подвижной секции внутри короба эта секция установлена на боковых роликах.
Увеличение высоты отвала ведет к увеличению производительности. Таким образом не изменяя мощности двигателя мы добились увеличения производительности на 30%. Модернизация данного вида рабочего оборудования позволяет получить положительный экономический эффект от его внедрения. Снижается себестоимость 1м3 грунта. Проделанные расчеты показывают что с установкой модернизированного отвала двигатель имеет достаточный запас мощности для преодоления сопротивлений возникающих за счет увеличения призмы грунта.
0 введение середин.docx
Существует много различных способов повышения производительности но в этом курсовом проекте мы рассмотрим один из малоизученных и перспективных способов - увеличение высоты отвала. Расчет произведем на базе бульдозера Т-500
Бульдозер Т-500 – универсальная самоходная строительная машина. Бульдозеры этого семейства предназначены для разработки грунтов I-III категории без предварительного рыхления грунтов IV категории с предварительным рыхлением а также трещиноватых скальных пород и мерзлых грунтов планировки площадок отрывки котлованов засыпки траншей оврагов. Бульдозерная техника данного класса применяется также для расчистки дорог от снега. Они обладают высокой степенью надёжности и ремонтопригодности. При комплектации могут оборудоваться различными типами бульдозерных отвалов.
Бульдозер Т-500 может эксплуатироваться в условиях умеренного и холодного климата при температурах окружающего воздуха от + 40 до - 50 град. Цельсия.
5 Расчет технико-экономических показателей проекта.docx
1 Выбор базового варианта машины
В качестве базового варианта техники в дипломном проекте рассматривается бульдозер Т-500.
2 Назначение и область применения новой техники
Бульдозеры применяются в дорожном железнодорожном горнорудном мелиоративном и ирригационном строительстве. При помощи бульдозеров можно возводить насыпи разрабатывать выемки планировать и отделывать скаты откосы и поверхности площадок прокладывать и грубо профилировать дороги разрабатывать и засыпать рвы траншеи котлованы и каналы послойно разрабатывать легкие породы на открытых горных разрезах и удалять вскрышной слой грунта при добыче полезных ископаемых.
3 Выявление конструктивных и эксплуатационных преимуществ
Одним из главных экономических требований предъявляемых при проектировании землеройно-транспортных машин (ЗТМ) является снижение себестоимости одного кубометра разрабатываемого грунта.
Выполнение данного требования непосредственно связано с повышением производительности наибольшие резервы для повышения которой прежде всего могут быть найдены в увеличении призмы перемещения грунта.
Рассмотренное в дипломном проекте техническое решение позволяет увеличить объем призмы волочения грунта бульдозером при резании грунта за счет увеличения высоты отвала и тем самым увеличить производительность.
Продолжительность рабочего цикла определяется из выражения:
где и - соответственно пути резания грунта перемещения призмы волочения и холостого хода км; принимаем =002 км =008 км =01 км;
и - средние действительные скорости движения бульдозера при резании грунта и перемещении призмы волочения кмч;
- средняя теоретическая скорость движения бульдозера на обратном холостом ходу кмч;
и - время затрачиваемое на разворот бульдозера переключение передач а также подъем и опускание отвала мин;
принимаем =0.3 мин =0.1 мин =0.04 мин;
Требуемые для расчета значения рабочих скоростей получены из тяговой характеристики (п. 2) с учетом возможности полной реализации тягово-сцепных качеств бульдозера. Для различных видов грунтов значения рабочих скоростей отличаются незначительно поэтому расчеты технической производительности для базовой и новой техники справедливы для различных грунтовых условий.
Продолжительность рабочего цикла для базового бульдозера будет равняться:
Продолжительность рабочего цикла для модернизированного бульдозера определяется из выражения:
Техническая производительность определяется по формуле:
Где - объем призмы грунта перемещаемого перед отвалом согласно технической характеристике бульдозера Т-500 = 1117 м3;
- объем призмы грунта перемещаемого перед отвалом модернизированного бульдозера Т-500 = 1938 м3;
Техническая производительность базового бульдозера будет равняться:
Техническая производительность модернизированного бульдозера определяется из выражения:
4 Определение капитальных вложений по базовой (БТ) и новой (НТ) технике
Капитальные вложения на технику включают оптовую цену техники затраты на первоначальную доставку и монтаж а также сопутствующие капитальные вложения связанные с ее эксплуатацией.
Капитальные вложения рассчитываем по формуле:
где ЦБ – балансовая стоимость техники тыс. руб.;
КС – сопутствующие капитальные вложения потребителя связанные с эксплуатацией техники тыс. руб.;
Значение КС учитывают если имеются существенные различия в капитальных вложениях по сравниваемым вариантам. В нашем случае КС равняется нулю.
Балансовую стоимость определяем по формуле [10]:
КБ – коэффициент учитывающий затраты на первоначальную доставку техники и монтаж.
Значение коэффициента КБ принимаем по табл.2 [10] равным 109.
Рассчитываем балансовую стоимость базовой машины:
Балансовую стоимость новой машины принимаем равной:
5 Определение годовой эксплуатационной производительности
5.1 Определение годового фонда времени работы бульдозера
Продолжительность работы техники в течение года определяется по формуле [10]:
где - годовой фонд рабочего времени дни; принимаем =247 дней;
=82 ч – средняя продолжительность смены;
=1.5 - коэффициент сменности;
=2000 ч – продолжительность работы на одном объекте;
– простои при всех видах технического обслуживания (ТО) приходящиеся на 1 час работы днич;
где - число разновидностей ремонтов или технических обслуживаний за межремонтный цикл
- продолжительность пребывания техники в
- продолжительность ожидания ремонта доставки и ремонт и обратно дни;
- число технических обслуживаний и ремонтов за межремонтный цикл;
- межремонтный цикл ч; согласно рекомендациям по проведению ТО и ремонта бульдозера Т-500 =21360 ч;
Определяем число технических обслуживаний и ремонтов за межремонтный цикл по формуле [10]:
где - периодичность выполнения соответствующего вида технического обслуживания и ремонта; мото-час; 240 мото-час; мото-час;
- число всех видов технических обслуживаний и ремонтов с периодичностью большей периодичности того вида по которому ведется расчет;
- межремонтный цикл мото-час; в нашем случае =5760 мото-час;
Продолжительность пребывания в ТОиР:
dрТO1=02 дня; dрO2= 1 день; dрТP= 7 дней; dрКР= 14 дней.
Продолжительность ожидания ТОиР:
dпТO1=0 дней; dпТO2= 0 дней; dпТP= 4 дня; dпКР= 7 дней.
5.2 Определение годовой эксплуатационной производительности
Годовую эксплуатационную производительность сравниваемых вариантов техники определяем применительно к одним и тем же технологическим процессам. При определении экономического эффекта на этапах разработки новой техники годовую эксплуатационную производительность строительных машин рассчитываем по формуле [10]:
где - эксплуатационная среднечасовая производительность м3ч;
– коэффициент использования машины по времени который учитывает внутрисменные простои (по организационным причинам); не учтенные в среднечасовой эксплуатационной производительности;
Эксплуатационную среднечасовую производительность рассчитываем по формуле [10]:
где ПТ – часовая техническая производительность м3ч;
КТ – коэффициент перехода от технической производительности к эксплуатационной КТ=0.4.
Эксплуатационная среднечасовая производительность:
Годовая эксплуатационная производительность:
6 Определение годовых текущих затрат
Текущие затраты рассчитываются за год работы техники и включают амортизационные отчисления на полное восстановление зарплату машинистам занятых в технологическом процессе затраты на топливо затраты на сжатый воздух затраты на все виды ремонтов затраты на гидравлическую жидкость на смазочные материалы на замену быстроизнашивающихся частей затраты на перебазировку машин с одной строительной площадки на другую.
Таким образом текущие затраты рассчитываются по формуле [10]:
С= САМ + СЗП +СТОП+ СВОЗ+СРЕМ+СГЖ+ССМ+ССО+СПБ; (5.10)
6.1 Определение годового фонда заработной платы
В состав бригады включают рабочих участвующих непосредственно в технологическом процессе.
Состав звена принимают по инструкции эксплуатации машины (техники). Разряды рабочих принимают по единому тарифно-квалификационному справочнику. Заработная плата рабочих занятых управлением машины рассчитываем по формуле [10]:
где Кр – средний районный коэффициент;
Кр=107 – для средней зоны;
=13 – коэффициент учитывающий премии;
Б=1 – число рабочих занятых управлением машины в одну смену;
СТi – часовая тарифная ставка рабочего i-го разряда руб.ч.
Для рабочих обслуживающих машины повышенной единичной мощности установлен единый VI разряд и часовая ставка в размере 10015 руб.ч.
6.2 Определение амортизационных отчислений на полное
Показатель амортизационных отчислений на полное восстановление определяется по формуле [10]:
где ЦБ – балансовая стоимость тыс. руб.;
НА=206% - норма амортизационных отчислений на полное восстановление
6.3 Определение годовых затрат на все виды ремонтов машины
Затраты на все виды ремонтов включают в себя:
- затраты на капитальный ремонт ;
- затраты на техническое обслуживание и текущий ремонт ;
Размер амортизационных отчислений на капитальный ремонт составляет некоторую часть от балансовой стоимости машины:
где 10 % - норма амортизационных отчислений на капитальный ремонт в процентах;
Годовые затраты на техническое обслуживание и ремонт машины рассчитываем по формуле [10]:
где - стоимость ремонтных материалов и запчастей приходящаяся на один машино-час тыс. руб.;
- заработная плата ремонтных рабочих приходящаяся на один машино-час тыс. руб.;
Заработная плата ремонтных рабочих принимается исходя из часовой тарифной ставки ремонтных рабочих рассчитывается по формуле [10]:
где =1.3 – коэффициент премиальных доплат принимается по данным ремонтных предприятий;
- часовая тарифная ставка ремонтного рабочего
- количество ТО и ТР за межремонтный цикл;
- трудоемкость ТО и ТР чел.-час; =5 чел.-час =16 чел.-час =800 чел.-час =440 чел.-час.
Стоимость ремонтных материалов и запчастей рассчитываем с помощью переходного коэффициента Кпер от заработной платы к стоимости ремонтных материалов и запчастей.
Для расчета принимаем Кпер=2.0 следовательно:
Затраты на все виды ремонтов:
6.4 Определение затрат на дизельное топливо
Расчет затрат на топливо для техники с двигателем внутреннего сгорания производим по формуле [10]:
где = 17 руб. – стоимость одного кг топлива;
- часовой расход топлива;
Часовой расход топлива определяется из выражения [10]:
где - номинальная мощность двигателя кВт; =382 кВт;
- удельный расход топлива гл.с.·ч; =175 гл.с.·ч;
- коэффициент использования двигателя по времени за час рабочей смены =07;
- коэффициент использования двигателя по мощности за рабочий цикл =08;
- коэффициент учитывающий изменение расхода топлива в зависимости от степени использования двигателя по мощности; =094;
- коэффициент учитывающий снижение расхода топлива при работе двигателя на холостом ходу =025;
6.5 Определение затрат на гидравлическую жидкость
Расчет затрат на гидравлическую жидкость производим по формуле [10]:
где - вместимость гидросистемы дм3;
кгдм3 – плотность масла гидросистемы;
рубкг – оптовая цена масла;
- коэффициент доливок гидравлической жидкости;
машино-ч=3556 ч – периодичность смены масла в гидросистеме;
6.6 Определение затрат на смазочные и обтирочные материалы
Затраты на смазочные и обтирочные материалы приближенно определяем как 10% от затрат на дизельное топливо [10]:
где Е – коэффициент перехода от годовых затрат на топливо к затратам на смазочные материалы; Е=01;
6.7 Определение затрат на износ и ремонт сменной оснастки
К сменной оснастке относятся материалы и комплектующие изделия которые в процессе работы периодически заменяются и ремонтируются.
Затраты на сменную оснастку определяются по формуле [10]:
где - цена сменной оснастки тыс. руб.;
- число сменной оснастки в комплекте;
- срок службы машины лет;
- срок службы сменной оснастки лет;
При отсутствии данных о сменной оснастке ее стоимость приблизительно определяют как 1% от балансовой стоимости машины [10]:
6.8. Определение затрат на перебазировку машины
Затраты на перебазировку машин перевозимых без разборки в кузове бортового автомобиля на буксире или на большегрузном прицепе-тяжеловозе определяются по формуле [10]:
где - затраты на одну перебазировку включающие: зарплату экипажа перевозимой строительной техники ; зарплату такелажников ; затраты на эксплуатацию автопоезда (тягача) и вспомогательного крана .
где - среднее расстояние перебазировки км; =25 км;
- средняя скорость передвижения тягача кмч;
где - продолжительность работы крана ч; =2.9 ч;
n- количество такелажников в бригаде; n=2 чел;
- часовая тарифная ставка такелажника; =8129 руб.;
где - общее время работы тягача ч;
где - средняя продолжительность погрузки и разгрузки ч;
- плата за один автомобиле-час пользования; =0925 тыс. руб.;
- плата за один км пробега =30 руб.;
где - цена одного машино-часа работы вспомогательного крана тыс. руб.; = 15 тыс. руб.;
Затраты на одну перебазировку составляют:
Результаты расчетов текущих затрат по базовой и новой техники сведены в таблицу 4.
Таблица 4 – Результаты расчетов
Условные обозначения
Значение показателей
Техническое обслуживание и ремонт
Масло для гидросистемы
Ремонт сменной оснастки
Общие годовые текущие
7 Определение экономического эффекта
Экономический эффект за срок службы новой техники в расчете на годовой объем ее производства определяется по формуле [10]:
где - удельные приведенные затраты по сравниваемым вариантам тыс. руб. м3;
- количество единиц техники; принимаем =1;
Удельные приведенные затраты рассчитываем по формуле [10]:
тыс. руб. м3; (5.30)
где С – годовые текущие затраты связанные с выполнением технологического процесса тыс. руб.;
ЕН =015 – нормативный коэффициент эффективности капитальных вложений;
8 Определение основных удельных показателей
Удельные текущие затраты (себестоимость) на измеритель работы (И) рассчитывается по формуле [10]:
где И – измеритель работ; в нашем случае И=1 м3;
Удельные капитальные вложения на измеритель работ рассчитывают по формуле [10]:
тыс. руб. м3; (5.32)
9 Определение дисконтированного экономического эффекта за период срока службы объекта
Приведем общую сумму экономического эффекта от модернизации базовой техники к текущему периоду с учетом изменения стоимости денег с течением времени.
Дисконтирование является универсальной методикой приведения будущих денежных потоков (в нашем случае будущих экономических эффектов) к настоящему моменту основанной на понятиях сложных процентов. Формула суммарного дисконтированного экономического эффекта выглядит следующим образом [10]:
где ЭФтек – годовой экономический эффект;
r - ставка дисконтирования;
Ставка дисконтирования определялась как ставка рефинансирования Центрального банка Российской Федерации которая с 29.03.2010 года составляет 825 увеличенная на процент риска неполучения экономического эффекта в период срока эксплуатации техники который оценивается в 175%. Таким образом ставка дисконтирования будет составлять 10%.
Число периодов =12 – это число лет срока эксплуатации объекта.
10 Определение срока окупаемости использования новой техники
Срок окупаемости затрат на приобретение и эксплуатацию новой техники определяется следующим методом [10]:
Для расчета необходимы следующие данные:
) Ставка дисконтирования - r;
) Годовой экономический эффект от модернизации базовой техники в текущем году – ЭФтек;
) Затраты на модернизацию базовой техники Змод
а) Рассчитаем годовой экономический эффект приведенный к текущей стоимости:
ЭФ2 = 18265 (11)=16605;
ЭФ3 = 18265 (11)2=15095;
ЭФ4 = 18265 (11)3=1373;
ЭФ5 = 18265 (11)4=1251;
ЭФ6 = 18265 (11)5=11345;
ЭФ7 = 18265 (11)6=1032;
ЭФ8 = 18265 (11)7=937;
ЭФ9 = 18265 (11)8=853;
ЭФ10 = 18265 (11)9=774;
ЭФ11 = 18265 (11)10=705;
ЭФ12 = 18265 (11)11=641.
б) Определение периода окупаемости:
Так как сумма дисконтированного экономического эффекта за первый год больше затрат на модернизацию следовательно за этот период затраты на модернизацию базовой техники окупаются.
Змод=7561 тыс. руб. - затраты на модернизацию базовой техники
11 Рентабельность модернизации базовой техники
Рентабельность модернизации показывает во сколько раз суммарный дисконтированный экономический эффект от модернизации базовой техники за весь срок эксплуатации превышает затраты на модернизацию.
Рентабельность модернизации рассчитывается по следующей формуле [10]:
где PV – суммарный дисконтированный экономический эффект за весь срок эксплуатации техники
Содержание2.docx
6.7 Определение затрат на износ и ремонт сменной оснастки 56
6.8 Определение затрат на перебазировку машины ..56
7 Определение экономического эффекта ..58
8 Определение основных удельных показателей . 59
9 Определение дисконтированного экономического эффекта за
период срока службы объекта ..60
10 Определение срока окупаемости использования новой техники ..60
11 Рентабельность модернизации базовой техники . 61
Охрана труда и окружающей среды при эксплуатации строительных
и дорожных машин . .. .63
1 Классификация и источники вредных и опасных факторов .. 63
2 Действие вредных агрессивных и ядовитых веществ на организм
человека и их предельно допустимые концентрации методы
и средства оценки . 64
3 Микроклимат в кабинах самоходных машин ..66
4 Звуковые колебания. Защита от шума 67
4.1 Характеристики звуков и действие их на организм 67
4.2 Шумовые характеристики машин . 69
4.3 Средства и методы защиты от шума 69
4.4 Звукопоглощение виброизоляция демпфирование и средства
индивидуальной защиты от шума .. .70
5 Действие вибрации на организм человека . 71
6 Общие требования безопасности труда .. .72
6.1 Требования безопасности труда при производстве
работ бульдозерами . .73
6.2 Требования безопасности труда при транспортировании и
6.3 Требования безопасности труда при техническом обслуживании
и ремонте машин .. 74
6.4 Электробезопасность . ..76
6.5 Пожарная безопасность .77
7 Охрана окружающей среды . .78
8 Влияние машин на окружающую среду ..78
8.1 Локальное влияние .. 78
8.2 Региональное влияние . ..79
8.3 Глобальное влияние .79
9 Оценка количества выбросов в окружающую среду 79
Список использованных источников .. .84
Содержание1.docx
1 Анализ технической литературы и патентный поиск .. ..6
2 Выбор темы дипломного проекта .. 9
Расчет основных параметров бульдозера . ..13
1 Расчет сопротивления грунта копанию . 13
2 Расчет производительности бульдозера . 14
3 Тяговый расчет бульдозера .17
3.1. Исходные данные .. .17
3.2 Расчет и построение тяговой характеристики ..18
4 Описание гидравлической схемы бульдозера Т-500 ..30
Расчет на прочность элементов рабочего оборудования . .32
Проектирование технологического процесса изготовления детали .34
1 Анализ чертежей .34
2 Определение размера партии деталей и типа производства 34
3 Выбор способа получения заготовки . ..35
4 Расчет припусков .35
5 Выбор оборудования приспособлений и инструмента ..38
6 Определение режимов обработки заготовки .. ..39
7 Режим резания для шлифовальной обработки . .43
8 Определение нормы времени . .44
9 Определение нормы времени токарно-черновой операции 44
Расчет технико–экономических показателей проекта . .47
1 Выбор базового варианта машины .. .47
2 Назначение и область применения новой техники . .47
3 Выявление конструктивных и эксплуатационных преимуществ
4 Определение капитальных вложений по базовой (БТ) и
новой (НТ) технике 49
5 Определение годовой эксплуатационной производительности
5.1 Определение годового фонда времени работы бульдозера 49
5.2 Определение годовой эксплуатационной производительности ..51
6 Определение годовых текущих затрат 52
6.1 Определение годового фонда заработной платы 52
6.2 Определение амортизационных отчислений на полное
6.3 Определение годовых затрат на все виды ремонтов машины 53
6.4 Определение затрат на дизельное топливо 54
6.5 Определение затрат на гидравлическую жидкость 55